
1 minute read
Fix Your Mix.
Is your current in-tank mixer not producing the quality mix you need?
Eliminate lumps, clumps and fish eyes; wasted ingredients; and clogged filters. Fristam’s FS Series Shear Blender for inline mixing is the perfect solution when existing in-tank mixers are not able to produce the quality mix you need.
Rather than replacing your in-tank system, simply supplement it affordably with an FS Shear Blender. The FS Shear Blender, placed after a mix tank, disperses particles into liquid in just one pass and produces consistent product time after time.
Watch short video at www.fristam.com/fs
•
Deep Neural Network technology—to randomly pick oriented objects that are known to the system during setup and/or engineering.
Thus, the key di erentiator with the developing Siemens technology is its ability to pick unknown objects.
According to Siemens, this new software will enable users to move from using robotic systems with static pick points to AI-driven piece-picking robots in less than an hour. Setup for the system is accomplished in four steps: Set the robot arm and related end-of-arm tooling to move safely to static pick-and-place points; mount the 3D camera; install the Siemens software for piece picking on the target runtime hardware of choice; and follow the guided setup via the user interface for calibration.
With these steps implemented, calculated pick points are then continuously provided to the robot motion program, enabling the robot to grasp any object. “The setup takes only 30 minutes through an easy and straightforward calibration process,” Solowjow says. “The user interface is very simple and clear.”
Target applications for this technology include order fulfillment operations with a high number of
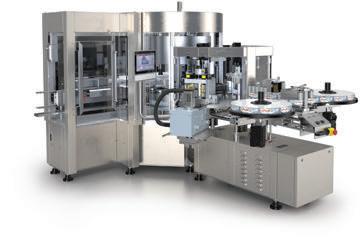
SKUs requiring 500 to 1,200 picks per hour, such as goods-to-person tote picking, conveyor induction and sortation in e-commerce, e-grocery warehouse automation, and food and beverage packaging.
Inputs to the Siemens pre-trained, AI-powered vision software in the PLC come from the 3D camera’s point cloud, with the output being the grasp pose for any object at runtime. A Siemens HMI is used to interface with the PLC and software; and Siemens TIA Portal can be used to program the entire system—Siemens PLC and HMI as well as the robots, vision system, and gripper.
The Siemens AI-driven piece-picking system also provides for collision avoidance for all actions in the robot workspace, enables robots to master challenges such as handling tightly packed boxes using low-cost 3D cameras, and reduces errors through features such as automatic bin detection.
“We pretrain the AI skill for grasping using simulation,” says Solowjow. “Similar to a human, the AI learns how to grasp in general—as opposed to specific objects—so that grasping of unknown or previously unseen objects is possible.”
The Siemens AI picking software is robot and end-of-arm tooling agnostic. In its exhibit at PACK