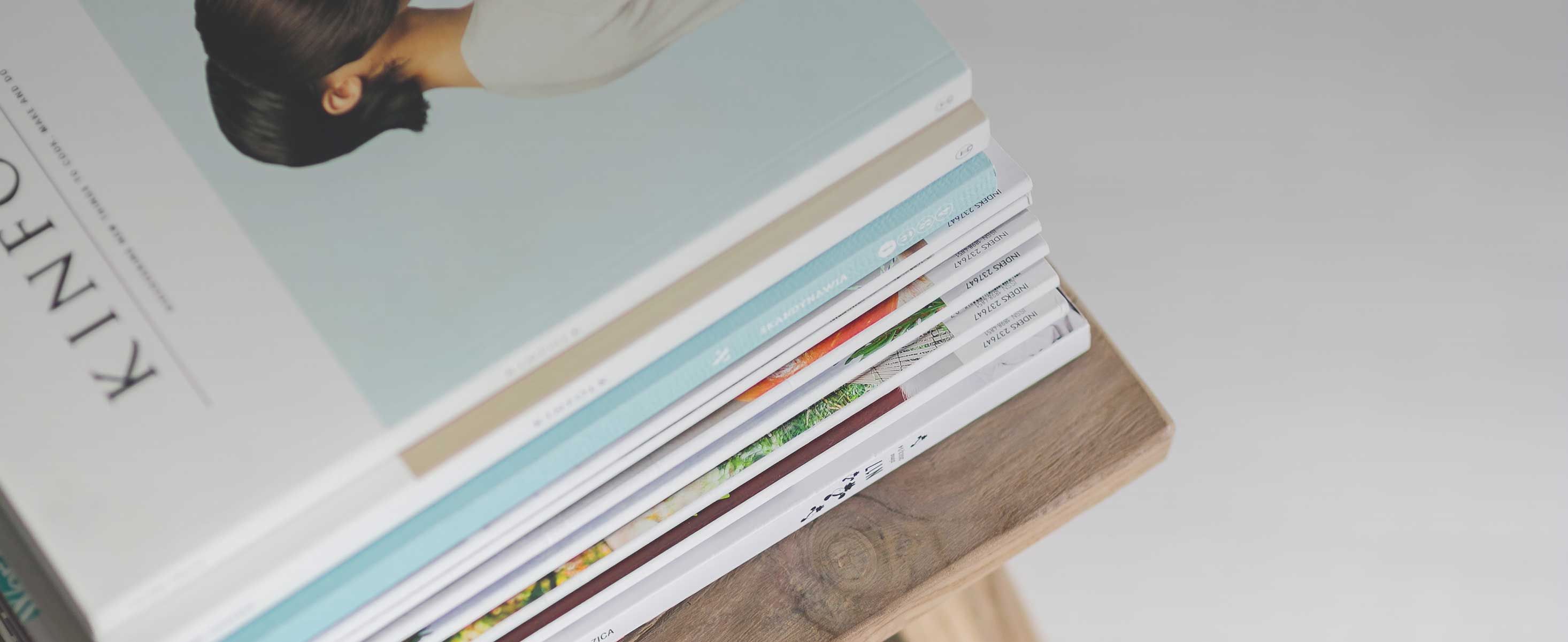
2 minute read
Controls
The eXtended Transport System (XTS) was a highlight of the Beckho booth at PACK EXPO International. The unique technology features movers that can move independently or be synchronized in groups for material handling in a variety of applications, such as consumer packaged goods (CPG) packaging applications. The XTS features built-in collision avoidance, and tooling on the XTS movers can be used to open and close bags, cap bottles, or move parts down the line.
“XTS is not just a substitute for lower-cost solutions like chain-driven systems with lugs and buckets, it’s a fundamentally di erent way to approach material handling transport processes,” says Je Johnson, mechatronics product manager at Beckho Automation.
The news at PACK EXPO was that Beckho has updated its XTS ( 1) with its No-Cable Technology (NCT) for contactless, continuous power supply and synchronous real-time data transmission to the XTS movers. To enable this, the XTS modular system has been expanded to include a special motor module and electronics mounted on the mover. With this addition, no further connections or supply lines are required, meaning that processing steps and quality control can be accomplished directly on the mover while a process is running.
“Traditionally, if you wanted to grip something on linear transport systems, you’d have to have two movers mechanically linked to do the gripping,” says Johnson. “Now that we’ve integrated power and data on the movers, you can mount things like vacuum generators on the movers to do vacuum pickup of materials. You can even use mechanical actuators—really any end-of-arm robot tooling can be mounted on the movers to pick and place product.”
A few XTS with NCT application examples include the ability to divide and reunite product flows using mechatronic transfers between two movers; sort products using an integrated pusher on the mover; pick and place products for product sorting using vacuum suction units; and pick up individual products from unsorted and irregular product flows and be able to sort them into good and bad parts or place them correctly for final packaging.
Explaining how XTS with NCT can increase production output, Johnson says with energy being wirelessly transferred to the mover with NCT, this energy is available to realize di erent motion sequences directly on the mover with the help of motors. The system’s CNC-based motion synchronizes positioning of the movers in real time, and the central software approach in TwinCAT allows synchronization with external processing stations. These features enable the movers to become an active part of the manufacturing process as a mobile processing station. For example, the mover can be used to manipulate a product to position a carton or screw on a cap.
With this level of synchronization, process times for feeding and removal at alternative processing stations are eliminated and the product flow no longer need be interrupted. As a result, the e ciency of the machine increases, as does the production output.
Throughput can be increased by adding movers. Each mover can perform multi-axis movements, allowing for product alignment along the X, Y, and Z axes. Additional degrees of freedom can be achieved by rotary movements using TwinCAT to control the interaction of the axes via CNC functions.
Magnetic levitating shuttles
High-margin CPG industries like spirits, confectionery, and cosmetics are early adopters of a trend toward heightened personalization, both in what’s placed in packaging by automation and on the packaging itself. In these highly personalized environments, often referred to as “batch size one,” we see packaging applications emerging on the bleeding edge.
One such technology that plays in this space, demonstrated by B&R at PACK EXPO International, is called Acopos 6D (six degrees of freedom) (2).