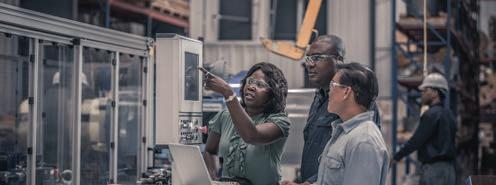
9 minute read
Operator Safety
Safety First: All Things Risk Assessment
KIM OVERSTREET, DIRECTOR, EMERGING BRANDS ALLIANCE, WITH SEAN RILEY
1. Machine suppliers and end users must identify hazards and reduce risks. 2. The methodology in the B155.1 standard is recommended for its ease of use. 3. Though methodologies/approaches can differ, there are fi ve key steps to risk assessment.
TOP THREE TAKEAWAYS
In this Q&A, Bruce Main, PMMI Technical Advisor and President of design safety engineering, inc. (pictured), and Sean Riley, Senior News Director, PMMI Media Group, discuss risk assessment for packaging and processing machines.
Sean Riley: We hear “risk assessment” a lot. What exactly is it in layman’s terms?
Bruce Main: It’s basically a safety assessment. It’s a type of analysis where you look to identify hazards associated with machinery or equipment. It guides you through a process to develop risk reduction measures to make sure that you achieve acceptable risk.
Sean Riley: When did this become a topic for machinery in particular? When did PMMI fi rst integrate risk assessment into the B155.1 standard?
Bruce Main: Let’s start with the last part fi rst. The B155.1 fi rst integrated risk assessment in the 2000 edition of that standard. The reason that it was done then was because of where it came from. The risk assessment process really got legs in the 1995-1996 timeframe when the European Union issued the Machinery Directive, which is a law in Europe that requires that machine suppliers or builders do risk assessments. Because of that, and because many PMMI members were shipping machines to the EU, we needed a methodology to do this. That’s where this really came from.
Sean Riley: Is that something I can do on my own or do I need to bring someone in to do one?
Bruce Main: Well, it’s intended to be something you can do yourself. As a builder of a machine or a supplier of the machine, the Machinery Directive is intended that you can self-certify. Who’s required to do this under the Machinery Directive? The law in Europe says the machine supplier is required to do it.
Now, under B155.1, we operate in a bit of a diff erent legal environment, so there’s requirements in the B155.1 standard that both the supplier of the machine is required to do a risk assessment and the user of the machine is also supposed to do a risk assessment. The machine supplier looks at the machine as they build it and its intended use, and the user of the machine looks at how that machine is used within a facility and the hazards that might be associated with the facility.
Sean Riley: Do they bring that to each other to make sure they
mesh or is that something that’s done independently?
Bruce Main: If it’s an off-the-shelf type of machine, a labeler, there may be very little collaboration, whereas if your supplier is building you an integrated bottling line, then quite a bit of collaboration will go on and that risk assessment may be done collaboratively for both the machine as well as the installation.
Sean Riley: Besides one being from the supplier and one being from the purchaser, are there different ways to do a risk assessment?
Bruce Main: Yes, there are many different ways to do risk assessments. That’s one of the great things about risk assessment is there’s lots of flexibility. The key thing is that you need to identify hazards and reduce risks to an acceptable level. Those are the very fundamental pieces and there’s lots of different ways to do it in different industries. The semiconductor industry has a methodology, the robot industry has a methodology, the machinery methodology is available—the B155.1 follows the machinery methodology as well. There’s a whole bunch of different approaches to risk assessment and there’s flexibility in how you can do it.
Sean Riley: Okay, so if I’m a packaging company, does PMMI have one that they suggest, the method that I should follow?
Bruce Main: The methodology that’s illustrated in the B155.1 standard is the one that we recommend. We do that because it’s easy to use and easy to learn. It provides enough structure and granularity to help you identify hazards without getting down a rabbit hole and getting lost. When I say there’s lots of different ways to do it, there’s also lots of different ways to overdo it, if you will.
Sean Riley: Okay. Could you give me some key steps on how I would do a risk-assessment process?
Bruce Main: Yes. There are five key steps. When we look about at the different methodologies and the different approaches to risk assessment across several industries, and I’ve had the opportunity to do that because I’ve written a couple books on this topic of risk assessment, what you see is the commonalities: the first step is you need to identify hazards, second is to assess the risks, third is reduce the risks to an acceptable level, fourth is to document your results, and fifth is to follow-up to make sure you’ve done what you said you’re going to do.
Of those five steps, the first one, identify hazards and the third one, reduce risks to an acceptable level, are the most important parts because if you don’t identify hazards, you can’t achieve acceptable risks, you’re going to potentially miss something and if you don’t reduce risk to an acceptable level, you’re missing the point.
What is most interesting is the second step, assessing risk. There are great efforts made by engineers all over the world trying to get away from the subjectivity of it. That’s one of the challenges of risk assessment is that fundamentally, you want to keep your Operator Safety on the goal and identify hazards and reduce risk to an acceptable level. The scoring of risk is really not that important and it’s sometimes overemphasized.
It’s different for the application. If we’re making cotton balls, we have one level. If you’re making steel, it’s entirely different level. The hazards are different, the risks are different. It’d be great if somewhere in industry from above we said, “Okay, you need to get to be a seven. If you get seven, you’re good, and if you’re more than seven, you’re not,” but it really depends on the application.
Sean Riley: How do I get started? How do I integrate risk assessment into my process?
Bruce Main: Well, you need to form a team. That’s usually the best way. Get the resources to understand what’s going on. B155.1 is certainly a great place to start. There are tools available. The PackSafe software is a tool that we have developed and is offered for sale for companies to use. It guides them through the process, lets you know what to do next, and how to make decisions about what you need to do. It’s not an expert system, it doesn’t tell you what to do, but it tells you what to think about. That’s one of those tools that will help you work through this process. The standard is something that is a very good resource.
PMMI offers risk-assessment training—Fred Hayes and I have done the risk-assessment training for many years. This is a two-day session where we talk about the different topics of risk assessment, products, liability aspects, aspects related to control systems, and even OSHA enforcement. We spend a fair amount of time working with the PackSafe software, getting people to do risk assessments in the training session. There’s a lot of resources available.
Introduction to Standards Development is a free program developed by PMMI to benefit businesses by providing insights related to standards participation. With knowledge of standards development, machinery can be designed, operated, and maintained in accordance with applicable requirements. Machinery export marketers also gain a tremendous benefit related to meeting requirements in effect at global destinations.
This program is designed to increase awareness of how standards can assist in meeting business objectives. In addition, the ability to participate in standards development supports a competitive solution for the global marketplace.
The course is not industry-specific; it raises the importance and value of standards work within all industries. It features examples related directly to packaging and processing machinery.
Visit the free program at: pmmi-standardstraining.com/
Sean Riley: What are the legal implications of doing a risk assessment, whether it’s in Europe or the U.S.?
Bruce Main: Well, let’s start with Europe because there’s a law. The Machinery Directive is the law that requires that you do risk assessments. If an OEM is shipping a machine into Europe, you have to do risk assessment as required by the law. That’s just what you have to do.
TRANSFER LOADS FROM ONE TYPE OF PALLET TO ANOTHER.

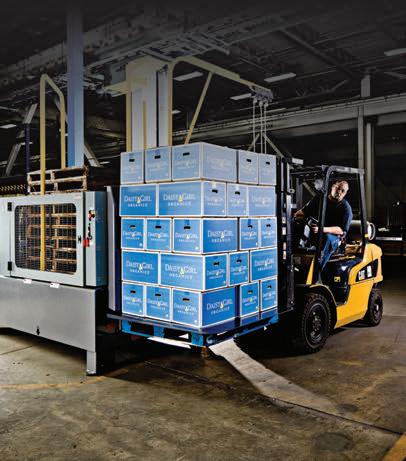

Safer, cleaner and faster than other load transfer devices Enhance safety for warehouse personnel Category 3 safety compliant Helps meet FSMA, HACCP and GMP compliance Helps reduce contamination from entering production areas 1 800 628 4065
In the U.S., we have the standard, the B155.1 standard. That’s not a law, it’s just a consensus standard. It’s a situation where you don’t have to do it by law, but the standard’s going to be what is used to measure your performance in the court of law if somebody were to get hurt, so you really need to be doing risk assessments. It’s going to be hard to defend a company if they’re not doing it, primarily because it’s been required now for almost 20 years.
Sean Riley: Are there other reasons for people to do risk assessments that would help in the design of their machinery that isn’t just eliminating hazards?
Bruce Main: We have seen situations, and I want to say almost every project that I work on, where what comes out of the risk assessment is one of two things: You either have hit a home run and you’ve identified all the hazards and you’ve got it solid and you’ve got a great machine and now the confidence in your design goes up, or we’re able to identify small changes that can actually improve the productivity, the throughput, the ease of use, the speeds, you’re just making better machines. One of our customers commented, “When engineers’ confidence goes up, costs go down.”
Let me give you an example. If you need to change a pump or a motor on a machine and the design of the machine is such that it’s buried inside the middle of the machine and in order to get to it, you have to dismantle the machine, that can really impact your downtime, but if you identify that task—and there’s safety implications to all this—but if you make it so that you can actually get to the pump or the motor, get in and get out and make that change and do it relatively quickly, that impacts [the end user’s] ability to produce.