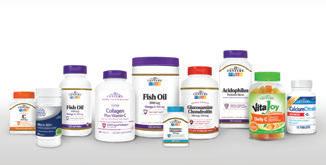
6 minute read
MEDICAL DEVICE PACKAGING
The beltorque BT-ICL Lite cappers at 21st Century also maximize production versatility and contribute to product quality. Compared to traditional cappers that use discs or spindles that can skew and scuff caps, beltorque features two pairs of belts that gently rotate and tighten caps by synchronizing the speed of the containers with
the rotating speed of the closures. “This technology doesn’t damage caps, and the precision of the cap placement and torque lead to accurate capping and better induction sealing. In general, child-resistant caps are the hardest to apply, but not with the beltorque,” says Horsefield. “Right after we installed our second beltorque, we ordered four more for other packaging lines.” 21st Century selected NJM’s Trotter 127 labeler for their new integrated line based on their experiences with their older Trotter labelers. This multi-functional pressure sensitive labeler can apply wraparound, front-and-back and 3-, 4- and 5-panel labels to round, square, rectangular, and oval bottles. “Applying a three-panel wraparound label along with a back label to a rectangular bottle, especially at the speeds we run, can be difficult—most manufacturers would shy away from that. Our success ↑ 21st Century packages close to 3000 different bulk tablets, capsules, and softgels in a variety of bottles, cap styles, and label configurations. This line offers about 25% more uptime than with this challenging application is pretty their other lines. incredible,” notes Horsefield.
1HHGKHOS" Automate!
-VSKSLHÅL[ZHUKPUZLY[ [OLTHSVUN^P[O[OL WYVK\J[PU[VJHY[VUZVU `V\YWHJRHNPUNSPUL
PRODUCT
GUKCartonac2005 Folder has a hinged feeding table for easy access to the fold plates and rollers. Simple upgrade from a Cartonac 91or 2000!
:H]LSHIVYJVZ[Z[PTLHUKSLHÅL[Z[VYHNLZWHJL
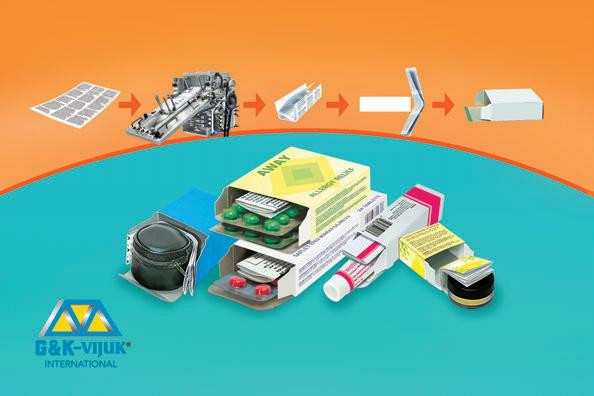
MEDICAL PACKAGING IS
ALL ABOUT FLEXIBILITY
Packaging can impact many facets of product design, including traceability, and a sterile barrier that’s guaranteed to hold up to rigorous testing and validation. Several packaging standards are in place today, but the type of regulations that apply will depend on the kind of packaging required, and our solutions meet them all, like ISO 11607, EN 868, ASTM D1585, ASTM F2097 and ASTM F3475-11. You can also expect to be in accordance with CFR 21 Part 11 for documentation. On top of that, we have in-process controls, process monitoring, and comprehensive calibration.
Frequently concentration is put on the device itself in efforts to address regulatory concerns. Is it safe, is it sterile, does it perform its function?
However, medical packaging is equally important to the device safety,
HI¿FDF\DQGSHUIRUPDQFH
Look to Harpak-ULMA, a packaging solution provider that knows how to leverage the latest packaging innovations and automation systems within the bounds of regulatory requirements, has the in-house capabilities to support such innovation, and can cost-effectively manage the phases of support such innovation, and can cost-effectively manage the phases of validation process. validation process. Learn more about our wide range of medical packaging and automation options.
Plus Product to Pallet Automation, including:
• Feeding • Loading • Robotics • Carton forming & closing • High-speed retail cartoning • Case packing • Palletizing • Stretch wrapping
Contact us today! HARPAK-ULMA.COM • 800-813-6644
Kilmer Innovations in Packaging Tackles ‘Wicked Problems’ in Med Device Sterility
KEREN SOOKNE, DIRECTOR OF EDITORIAL CONTENT

1. KiiP is an industry initiative ‘solving wicked problems in healthcare packaging’ comprised of volunteers. 2. They’re gathering passionate team members to tackle nebulous topics, ultimately improving patient safety. 3. Silos must be broken down, not just between suppliers, manufacturers, and healthcare providers, but often within company groups
TOP THREE TAKEAWAYS
Kilmer Innovations in Packaging (or KiiP) is a sterility assurance value chain collaborative effort focused on medical device packaging with the intent of fostering bold, unprecedented innovation. Their slogan is “solving wicked problems in healthcare packaging,” adopting a phrase originally coined by Dr. Laura Bix at a previous HealthPack conference; Dr. Bix brought it back into the conversation as KiiP was being formed. The idea behind KiiP and its slogan is that solutions to these wicked problems will lead to improved patient safety— while enhancing the experience of healthcare workers—among other benefits.
For a bit of background: The Kilmer Conference is put on by Johnson and Johnson once every three years, and the next is scheduled for 2022. It’s a prestigious, invitation-only event focused on sterility assurance.
Jennifer Benolken, MDM & Regulatory Specialist, Packaging Engineering at DuPont explained that a group of colleagues sat down at the last Kilmer Conference in 2019 and asked how they could get more people at the next conference who are passionate about packaging. What started out as a conversation about socializing the concept of the Kilmer Conference amongst packaging profession-
als has turned into an industry initiative in the spirit of the Kilmer Conference to collaborate to innovate. They’ve made a lot of progress in the last two and a half years, and it’s blossomed into a KiiP group on LinkedIn of over 300 members who have broken down value chain silos from medical device manufacturers through to the end user and healthcare professionals.
The four areas of focus for the programs within KiiP are: • The Last 100 Yards • Aseptic Handling • Speeding Things Up • Sustainability
Benolken, who leads The Last 100 Yards group, said that the interesting thing about KiiP’s efforts is they require a mindset shift for many participants. Generally, in the medical device industry, there’s a pretty clear target or end state (and process to get there). Whether it’s updating a standard, implementing a new package or machine, etc., there are defined processes, workflows, stage gates, and more.
Innovation in KiiP is far less straightforward, without a prescribed path to take. It requires participants to be open to questions, without a clear goal... until it emerges. In many ways, it is akin to the research phase of a new product development process—they need to find the problem that needs to be solved before determining how to solve
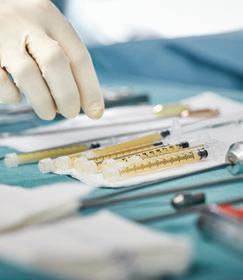
Q&A with KiiP
What’s an overarching concept being tackled across all groups?
KiiP is creating awareness about the importance of packaging. Packaging often goes unnoticed until something goes wrong. If we’re doing our jobs correctly, users are not necessarily tuned into the packaging because it seamlessly and efficiently did its job of protecting what’s inside. So that makes our job interesting—how do we get packaging to be recognized when our objective is not to be seen?
Is there involvement with regulatory folks, such as FDA or notified bodies in Europe?
KiiP has had some discussion with regulatory bodies, but they won’t be a major part of the conversation until we have identified potential solutions or paths to them. Not all of KiiP’s projects will be regulatory in nature.
What are some of the biggest hurdles?
+ It’s worrisome to potentially expose gaps or issues in established concepts. We’re asking tough questions in the name of innovation and patient safety and searching out either validation of existing or improvement to a better place. + KiiP wants these initiatives to be free enough for creativity, while still having some structure to move the needle forward. + There are also tangible hurdles like how KiiP processes money to fund projects. If we’re not formally established as an association or non-profit, how can we accept funds without conflicts of interest occurring? We’re working to find the right way to get this done. Also, some companies have expressed worry about IP when collaborating with others—we are quite focused on working on topics that there are currently no solutions for, in a way that collaborates a solution for all to help us get there more quickly than when we work on it individually. In many cases, KiiPsters are finding that the challenges are bigger than any one individual or company can tackle.
You’re asking big questions. Have you had any failures or innovations yet?
This is a huge learning process. We are grateful to be able to work on these important topics with our fellow KiiPsters—while no “failures” have occurred so far, we’ve had many pivotal moments and conversations about direction... Successes include the podcasts IAHCSMM has invited KiiP to participate in, and participation in events such as MD&M West and other venues to get people talking about what “could be” in going about solving these big, wicked problems the industry has been asking itself for years.