
58 minute read
The 10 Commandments of Cybersecurity
e 10 ommandments of y ersecurity
By David Miller
Senior Technical Writer, Automation World
Industry 4.0 and the Industrial Internet of Things (IIoT) have opened up vast horizons of new production efficiencies for manufacturers of all stripes through data acquisition and analysis. However, the adoption of these technologies can be a double-edged sword if not implemented properly. As software and devices all the way down to the sensor level are increasingly transformed into potential network gateways, previously unseen cybersecurity vulnerabilities may arrive in tow.
More and more companies are connecting previously isolated industrial control systems (ICS) to the enterprise level to enable everything from higher-level data analytics and remote access to digital twin simulations. With COVID-19 expanding the need for remote connection, this trend is expected to accelerate.
These increasing connections are part of the reason the past decade has seen an explosion of cybersecurity concerns, with the world witnessing threats to every imaginable sector of industry—from oil and gas and general manufacturing to critical electrical infrastructure.
The attackers behind these incursions range from organized criminals attempting to steal intellectual property or personal information for the purpose of extortion; hacktivists who aim to knock out critical assets and cause chaos to garner public attention; disgruntled current and former employees; and even state-backed foreign actors engaged in espionage activities for political purposes. And while attacks on critical infrastructure such as the electric grid or wastewater treatment facilities are more common, the threat to manufacturers is real as well.
Even though industry leaders such as Kellogg’s are investing more resources into securing their network and assets and sharing their insights, much uncertainty still remains. According to a 2019 Deloitte poll of more than 4,200 professionals, when asked how confident they were that their organization’s connected products, devices, or other “things” were secure, only 18% said that they felt very confident, while 51% said that they were somewhat confident, 23% said that they were uncertain, and 8% said they were not confident at all.
For those organizations that fall into the latter categories, Ilan Shaya, CEO of ICS Security, a company that develops security measures for industrial control systems, recently shared his “10 commandments” of cybersecurity during Inductive Automation’s Ignition Community Conference.
Commandment 1: Shaya recommended, first and foremost, that operators should identify all connections to their supervisory control and data acquisition (SCADA) network and run a thorough risk analysis of each. This includes internal local networks and wide-area networks such as business networks, connections to the internet, wireless network devices, satellite uplinks, and even modem and dial-up connections where they are still in use.
Commandment 2: In addition to ascertaining the level of risk each connection presents and taking steps to protect it, Shaya advised that operators ask themselves whether or not each connection is really necessary to minimize potential vulnerabilities wherever possible. Because every connection also creates an accompanying security risk, SCADA networks should be isolated from the enterprise level as much as possible. In cases where there is a genu-
Ilan Shaya’s “10 commandments” of cybersecurity come at a time when increasing remote access, sensor proliferation, and plant-to-enterprise networking are creating unprecedented concerns over the safety of companies’ assets.
ine need for ICSs to be integrated with the enterprise network, a demilitarized zone (DMZ) or data warehouse should be used. Moreover, remaining connections should be subjected to penetration testing and vulnerability analysis.
Commandment 3: Because systems can be exposed to attack by default network services, Shaya stressed that, in addition to limiting access points, unnecessary network services should also be removed or disabled where possible. “SCADA servers and clients do not need any applications or software, but the human-machine interface (HMI) and its drivers and structured query language (SQL) databases,” he said. “So, there is no need for any service to run but the HMI service.”
Commandment 4: Relying on proprietary protocols or factory defaults may also be unsafe, Shaya said. For example, while Modbus is often used to connect programmable logic controllers (PLCs) from different vendors, doing so may increase security risks. Instead, Shaya recommended using open protocols such as Profinet or OPC UA. In addition, he noted that end-users should demand their vendor disclose any backdoors that may allow their equipment to interface with the SCADA system.
Commandment 5: Rather than taking security for granted, SCADA system owners must insist that their system vendor implement security features in the form of product patches or upgrades. Shaya has observed that many systems do not have any security measures by default. However, as some newer SCADA devices now include basic security features, endusers should ask their vendor if they can purchase a device or license with additional security features.
Commandment 6: Strong controls and authentication measures must be established over any medium that may function as a backdoor into a SCADA network. With more mobile devices being used to monitor plant processes, wireless access points are increasing. According to Shaya, if these wireless devices are to be used, extra security precautions must be taken. In fact, he recommended not using a wireless network unless it is absolutely needed. If a wireless network is required, inbound access should be disabled where possible, as not all industrial control networks and devices require both inbound and outbound tra c.
Commandment 7: Full audits should be conducted on all SCADA networks to eliminate the paths of least resistance for hackers and other malevolent actors. Once issues are identified via an audit, the entire system should be retested to ensure they are solved. Shaya also advised carefully documenting every single point of failure via documents such as Microsoft Excel spreadsheets and Microsoft Visio diagrams for ease of display, organization, and accessibility to all stakeholders.
Commandment 8: Because any SCADA system may present a target for hackers, security assessments of physical and remote sites must also be conducted. With remote access spanning increasingly larger areas, it’s possible that even a single, small unmanaged switch at a distant site could be exploited to gain access to a system. Shaya’s advice: Perform a physical security survey in addition to network audits, create an inventory of all access points, and eliminate single points of failure. Live network access points at remote, unguarded sites should never be allowed simply for convenience.
Commandment 9: Clear and e ective configuration management processes must be established by management for both hardware and software. “Changes to the hardware or software can easily introduce vulnerabilities that undermine network security,” Shaya said.
Commandment 10: While the goal is always to prevent security breaches, in the case that one does occur, it is essential that companies have prepared plans in advance to handle it. System backups should exist and disaster recovery plans should include the potentiality of a cyberattack. According to Shaya, much of an organization’s approach to this may be dependent on how long its system can remain o ine. For example, if some downtime is acceptable, keeping spare parts and servers on hand may be a workable solution. However, in the instance that a system cannot be shut down for even a brief moment, redundant servers that can function locally should already be in place so that operators can respond immediately to a crisis without any idling.
Ready to Step-Up Your Automation?
By Kim Overstreet
Content Strategist, Alignment, PMMI Media Group
Three key elements of automation— speed, precision, and payload—also come with trade-o s, said Scott Marsic, senior product manager at Epson Robots, during his Automation 201 presentation at the PACK EXPO Connects Innovation Stage.
When evaluating these requirements in order to develop an automation system, you are unlikely to get everything you need due to inevitable trade-o s, said Marsic, and if you don’t know the ins and outs of your current process—and where your bottlenecks are—you won’t be able to determine where to invest for the best return. “This is why,” said Marsic, “It’s critical to understand up front what your goals are and clearly define your expectations.”
For those who may be thinking, “Wait, where do I even start an automation project?” Epson o ers a white paper called “Automation 201”. Marsic said the white paper is a great place for automation beginners, and provides an easy-to-use framework with five simple steps: 1. Why does your organization need to automate? What are your goals? 2. Define and document your current process. 3. Identify your requirements. 4. Identify the automation components you need. 5. Who will do the work?
“Automation 201” focuses on the third step of identifying requirements.
Speed, though being one of the main three requirements of automation, is also “one of the most important justifications in a business case for a robotics implementation,” Marsic said. But, he asks, what does improving speed mean to you? What part of the manufacturing process needs to be set up to achieve that time and what are you willing to give up to achieve those changes? A simulation of the application will assist with understanding what is possible. Marsic also noted that the robotics manufacturer specification of a cycle time should not be equated to the cycle time of your own project.
Throughput is another aspect of the speed requirement, and it is the quantity of output produced within a specific period of time. This takes into consideration, said Marsic, “How peripheral components interact with the robot, how parts are picked up, delays with PLCs, and the robot vision.” That’s why it is important to know if you are trying to improve cycle time or throughput in your process. Introducing independent parallel processing can also provide big gains in overall throughput, said Marsic, instead of using sequential processing.
Layout also a ects speed, as it can impact reach and cycle times. Marsic said to consider if the layout is fixed or can be adjusted. For example, moving the payload and end of arm tooling, or optimizing weight of the payload.
Peripheral interaction is the final element of speed considerations, and Marsic said there are some low cost, high benefit wins with small component adjustments. This could mean optimizing code, improv-

ing tool activation, or bringing valves, vacuum generators, etc. closer to the system to improve cycle time.
Marsic’s final note on speed is to “document your process, look for the low-hanging fruit, and plan ahead.”
The second requirement is precision, or the robot’s ability to return to the same position and orientation repeatedly (repeatability). “The entire system is often referred to as the stack, and each element of the stack has its own precision and respective tolerance,” said Marsic. “So, in addition to the robot, make sure to evaluate the elements attached to the robot, such as the end of arm tooling, cabling, its rigidity, your vision system, and its field of view, as well as peripheral equipment. Things like manufactured parts, conveyors, and pallets. Like musicians in a symphony, all the components in an automation system need to work in harmony to arrive at a desired output. The overall tolerance of the stack will have an impact on your ability to achieve a desired precision.”
Marsic also o ered additional pointers: • Evaluate your robot type. Are you using the right robot for the job? Only use what you need. • Localize your workspace to maintain precision. “The further out the arm extends, the more precision degradation you may experience. Get a robot that optimally moves within the designated workspace.” • Look at fixtures and tooling. Pneumatics or air will potentially not deliver the same precision as a mechanical gripper.
A molded vacuum tool formed to the shape of the part can improve speed and precision, but the trade-o is incremental cost. • Peripheral feedback. The addition of peripheral feedback, such as a vision system or force feedback, can help improve the precision of the system.
The last requirement is payload, and Marsic said there can be more than meets the eye with this topic. “When selecting a robot, look at the entire payload that will be moved by the arm. This includes not just the weight of the product being picked up, but also the end of arm tooling. And this can include mounting plates, grippers, air valves, cameras, etc. Make sure to consider all payload weights up front. They all get added together as part of the payload.”
Also, consider inertial e ects, or the resistance to velocity change, on the robot. “Too much inertia dramatically e ects robot cycle times,” he said, “And this has the potential to decrease your overall system throughput.”
Knowing these three requirements will enable you to optimize your automation. Know your current process. Know your trade-o s. “Not everything you implement is going to have a big trade-o , said Marsic, “Do your homework, buy the appropriate tools, get input from professionals and rely on vendors and integrators for support. All too often people buy the wrong equipment, spend too much or too little, and they miss the target.”
To see this Innovation Stage presentation in its entirety (available through March 31, 2021), visit awgo.to/1126.
ONE source.
Simply easy!
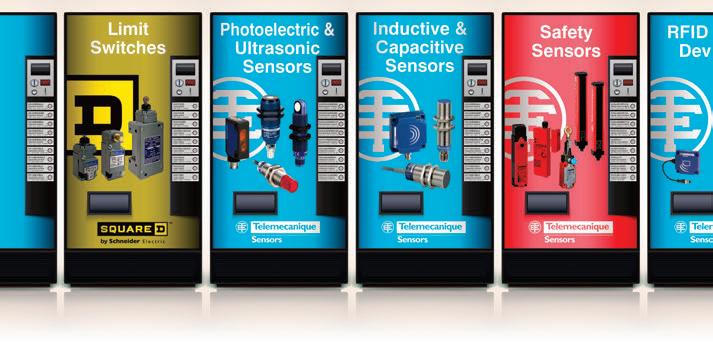
Improving Process Accessibility with Wireless Metering
By David Miller
Senior Technical Writer, Automation World
Digital transformation initiatives have been creeping into oil and gas for several years now with new technology deployments ranging from outfitting front line workers with augmented reality headsets to using remote monitoring and big data algorithms to increase equipment utilization rates and optimize overall performance. And this trend is only accelerating as COVID-19 pushes many once optional technologies to become essential.
Metering has not been overlooked in the digital transformation process. It is a vital part of the process industries, particularly in fields like oil and gas where the materials being moved are of high value, meaning that even a minor measuring inaccuracy could cost thousands of dollars in revenue. Coriolis flow meters, which measure the twisting motions caused by the inertia of fluid or gas flowing through an oscillating tube to derive mass flow, density, and other variables, have become especially popular for oil and gas applications. A major reason for their popularity is their high accuracy and ability to provide numerous output parameters without the need for additional devices.
Though for all the benefits they o er, accessing Coriolis meters in the field can still be di cult. “One of the things we struggle with a lot is that equipment is not always [accessible]. Sometimes you have to climb up ladders, or reach across hot tanks,” said Tonya Wyatt, Emerson’s global product line manager during a presentation at the Emerson Exchange virtual event series. “It’s not always beautiful weather. Sometimes in Texas it’s so hot you can’t stand it, or it might be pouring rain or some other kind of nasty weather that makes it tricky to find a device and hook up to it or remove power. Not to mention the fact that you have to get a hot work permit—not a fun situation.”
However, wireless technology that allows for remote access is helping to alleviate this issue.
Emerson’s new 5700 Coriolis transmitter, which o ers a Wi-Fi configuration option, is a prime example of how wireless technology can address specific industrial operation issues. The 5700 can be used with ProLink III for Windows, iOS, and Android to connect

to, configure, troubleshoot, and download historical files from Emerson Coriolis meters from a range of up to 115 feet. In the case of historical files being downloaded from the device, ProcessViz software can be used to visualize the data and make decisions on how to improve process performance.
Once a user has accessed their meter through ProLink, an assortment of current and past alerts can be viewed, such as when power resets and other configuration changes have occurred. A visual dashboard also provides read-outs for mass flow rate, volume flow rate, and other metrics, such as the amount of energy being used by the device. Requisite configuration changes to inputs and outputs can be made remotely via the software.
In addition, data from ProLink can be exported into ProcessViz where it can be converted into a spreadsheet format and printed as a report, making Emerson’s wireless metering pipeline convenient not only for engaging in asset monitoring and making on-the-fly adjustments in hazardous or hard-to-navigate environments, but for easing the administrative burden of mandatory reporting to regulatory agencies for compliance purposes.
Still, some threats do abound, and wireless access via the 5700 does not come without its trade-o s. With oil and gas operations having been a target of hackers in the past, cybersecurity concerns must be taken into consideration. Although remote access has great utility, it’s important for operators to keep in mind that with each added point of connection comes an expanded surface for potential cyber attacks.
Emerson is well aware of such risks and has outfitted its 5700 transmitters with the appropriate safeguards. For example, access control allows for two separate sets of log-in credentials—one for administrators and one for operators. This means that while operators can access data and make some moderate changes to configuration without administrative permission, more consequential actions are restricted. Also, the 5700 cannot be connected to via web browser or external web servers. Only Emerson’s proprietary software can be used to limit potential vulnerabilities. Similarly, devices cannot be connected to automatically, but require an assortment of security credentials.
“I typically like to think of security and usability as a trade-o . You want to keep the product as easy and straightforward to use as possible, but you also want to minimize any vulnerabilities,” Wyatt said. “The Wi-Fi option is just that—an option. For people who have extreme security concerns, rest assured that if you order the 5700 without the Wi-Fi option, it doesn’t even include the hardware to make the device wireless, so there’s absolutely no additional security risk there at all. On the other hand, if you are interested in the Wi-Fi option, but you have security concerns, we have built in several levels of security, so you can customize it to get the best solution for your needs.”
ERT ®
NEW BELTLESS CONVEYOR
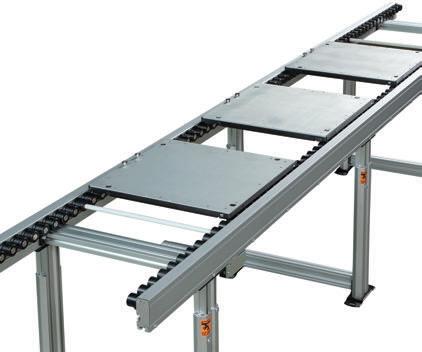
Dorner’s new ERT250 utilizes Edge Roller Technology to provide low back pressure accumulation, non-contact zoning, and conventional transport, all without a belt! Patent Pending Linear Gearbox
SOLUTIONS FOR MEDICAL
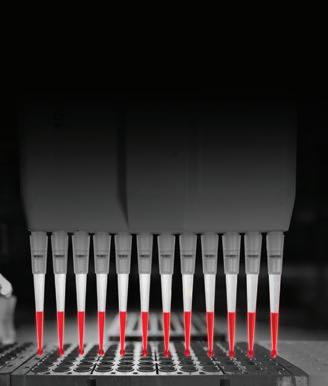
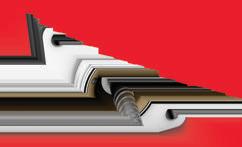
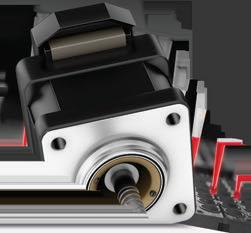
NSK MBSA Motorized Ball Screw Actuator for Compact, Precision Linear Motion
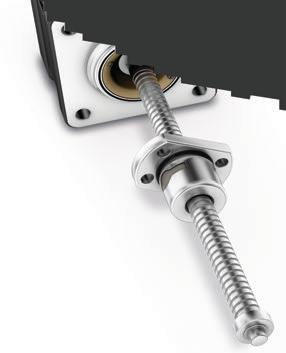
Compact, high-accuracy y positioning through seamless less mechatronic integration.
For life-critical medical, imaging and laboratory applications, NSK integrates a high-resolution motor with our precision-machined ball screw to create the MBSA Motorized Ball Screw
Actuator. The result: smooth, nearsilent, extremely reliable and ultraaccurate motion, improving efficiency and throughput while lowering costs.
CONTINUED FROM PAGE 15
Better quality in automotive. TSN’s determinism, especially when combined with gigabit bandwidth, can help manufacturing facilities speed up production processes. This is particularly useful for automotive assembly plants due to their production of a variety of models, each characterized by di erent trim levels. “That’s why it’s mandatory for manufacturing systems in the automotive industry to handle large amounts of data generated in real time during the assembly of various car parts,” said Burke. “Only in this way can manufacturers ensure that the di erent combinations of possible model variations do not slow down cycle times and the allocated parts are fitted correctly on the right models, at the right time, in a traceable manner. Automotive companies can use TSN to build production lines that ensure short cycle times because the technology combines advanced synchronization with tra c prioritization capabilities.”
These prioritization capabilities allow the network to deliver time-critical tra c while also allowing less critical tra c to coexist on the network. “Consequently, total cost of ownership can be reduced, since multiple types of network can now be combined onto a single hierarchy,” said Burke. “The end result is higher performance, lowered costs and simplified maintenance, all of which translates into better quality vehicles.”
Simplified machine design and higher performance for the
converting sector. When TSN is adopted in networks used in the converting industry, “plants can achieve accurate synchronization between multiple axes on a machine” because of TSN’s deterministic nature, said Burke. “By being able to control the motion of many di erent axes simultaneously over one network, facilities can optimize product quality and production processes as well as increasing the flexibility of their architectures and machines, while simplifying the mechanical set up. The end result is reduced time for retooling and maximized product yield.”
Higher levels of integration for semiconductor manufactur-
ing. Burke explained that synchronicity and traffic prioritization are also key to combining different types of process control on one network and effectively handling different recipes and activities across multiple machines and stations. “The numerous processing stages of the semiconductor industry—which require process, discrete, and motion control, along with integration of robots and IT systems—can be handled by TSN-based networks because of TSN’s ability to mix time-critical data for high-performance, high-speed motion control with slower, less time-dependent traffic,” he said.
The CLPA’s o ering for TSN applications is the organization’s CC-Link IE TSN. Burke said, “This is the first open Ethernet technology to merge gigabit bandwidth and key TSN functionalities, time synchronization, and tra c prioritization. By relying on this cutting-edge network technology, manufacturers from any sector can find a key solution to boost their processes.”
Powertrain Manufacturer Deploys New High-Payload Cobot
By David Miller
Senior Technical Writer, Automation World
Collaborative robots (cobots) have been a fixture of the manufacturing landscape for some time now, with the very first cobot sold to Danish plastic and rubber supplier Linatex back in 2008. At the time, cobots were largely relegated to simple, repetitive tasks capable of being performed by small, low-payload robots, such as machine tending for computer numeric control (CNC) applications. However, as technology has evolved, cobots have increasingly been integrated with more sophisticated sensors, vision systems, and control software, allowing their reach, speed, and payload capacities to improve.
As this trend continues, accelerating adoption is expected. PMMI’s 2019 business intelligence report “Robotics: Innovation 2 Implementation,” predicts that while cobots only accounted for 3% of all robot sales in North America in 2017, that number will swell to 34% by 2025.
Not only does this growth in the cobot space represent an exciting shift for those interested in the technology, it sounds a positive note for those who may fear that automation could displace human workers. Because humans work alongside cobots rather than seeing their roles eliminated entirely, cobots are often seen as a friendly face for the rapid expansion of robotics in industry.
FPT Powertrain Technologies’ industrial driveline plant in Turin, Italy, recently expanded its collaborative manufacturing capabilities with the adoption of Comau’s Advanced Use Robotic Arm (AURA). This robotic arm was designed in coordination with the human-centered manufacturing system (HuManS) project, launched in the Piedmont region of Italy by FPT, Comau, and 17 other companies.
Standing nearly three meters high and weighing in at three tons, AURA has a payload capacity of 170 kg (~375 lbs)—one of the highest of any cobot on the market. In addition to eliminating the need for fencing
Comau, which provided FPT Powertrain Technologies’ AURA robots, is focused on delivering advanced industrial automation products and systems for electric, hybrid, and traditional vehicle manufacturing, as well as industrial robots, and collaborative and wearable robotics technologies.
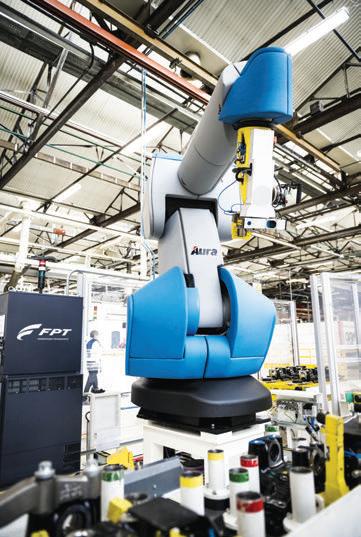
Connecting Sensors to the Cloud
By David Greenfield
Editor-In-Chief/Director of Content, Automation World
Industry 4.0 and Industrial Internet of Things (IIoT) architecture strategies have largely centered on sending data from controllers, edge devices, or software systems (such as manufacturing execution systems and supervisory control and data acquisition systems) to the cloud for aggregation and analysis. It was generally understood that sensor data would not be sent to the cloud directly; it would first travel through one of these higher-level systems.
However, advances in sensor connectivity and partnerships between companies on the OT (operations technology) and IT (information technology) sides of industry are changing that conception.
One partnership that exemplifies this change is the one between ifm and CloudRail. According to the companies, the integration of ifm’s sensors and CloudRail’s CloudRail.Box technology mean that users only need to connect an ifm sensor, select the cloud system they want to connect to (such as AWS, Microsoft Azure, or Alibaba), and the data from that sensor will then be processed and transferred to the cloud.
Felix Kollmar, CEO of CloudRail, said the simplicity of this plug-and-play sensor-tocloud connection is enabled by CloudRail.Box
By Aaron Hand
Executive Editor, ProFood World
Restrictions on travel have created one of the biggest pandemic challenges as suppliers struggle to provide services to their customers. “In order to uphold a standard of safety for our customers and onsite food safety sanitors, approval procedures were put in place to restrict travel within the organization,” notes Candy Lucas, senior food safety director for PSSI.
Suppliers are incorporating new technologies to better service their customers remotely. features that make it possible to remotely monitor and configure devices and deliver updates. CloudRail.Box supports several edge computing connection technologies as well as OPC UA. These capabilities enable direct sensor-to-cloud connections to be rolled out across large manufacturing facilities or by OEMs, according to Kollmar.
The CloudRail system is available worldwide via ifm, which offers several starter kits containing all components required to implement an IIoT project. One of these kits contains ifm’s new VVB001 vibration sensor. “Within a few minutes, the vibration of a machine can be detected and evaluated in any cloud,” said Michael Strauss, head of product management, industrial communication, at ifm.
Explaining the partnership between the two companies, Strauss said, "CloudRail offers us market access to big digitization projects. Our salesforce has been explaining the advantages of clouds to automation specialists, now we are cooperating with leading cloud providers and consulting companies on interdisciplinary projects to contribute our sensor expertise. CloudRail is one of few companies worldwide with extensive expertise both in IT and OT.”
Kollmar added that "the challenges of digitization are simply too big for individual companies. They require close cooperation between OT and IT, of which the partnership between ifm and CloudRail is a good “The increase of Microsoft Teams meetings, Zoom meetings, FaceTime calls, conference calls, and remote desk audits are now part of our new normal,” Lucas says.
Sani-Matic has developed a software as a service (SaaS) called the SaniTrend Cloud Online Data Acquisition & Management System that provides customers with visibility into their cleaning equipment from anywhere. It is available with any new PLC-controlled, automated cleaning system from Sani-Matic and can also be retrofitted with any existing Sani-Matic automated cleaning system that has an AllenBradley CompactLogix or higher PLC processor.
The software provides automated, secure
example. While ifm can look back at more than 50 years of experience in industrial automation, CloudRail's specialty is bridging the gap towards the IT world and thoroughly understanding the corresponding target group. ifm already has several cloud solutions in its portfolio; however, these have primarily been developed for the OT target group. With CloudRail.Box and the corresponding Device Management Cloud, our product bridges the gap between OT and IT.”
Cloud services supported by CloudRail include: AWS IoT Core, AWS IoT SiteWise, AWS IoT Greengrass, Microsoft Azure IoT Hub, Microsoft Azure IoT Central, Google IoT Core, SAP Cloud Platform Internet of Things, Alibaba Cloud IoT Platform, IBM Watson IoT Platform,
Remote Access Technologies Help Keep Food Sanitation Workers Safe
and Aveva Insight. data acquisition and reporting of critical cleaning cycle information for any automated cleaning system. Dashboards, OEE trends, event history, and alerts also provide actionable insights into cleaning system operation.
The equipment maker was already working on its release pre-COVID, but the timing of its release was fortuitous with so many workers needing to work from home because of the pandemic. “The technology to see information outside of the main plant has existed, but the food industry has been very reluctant to allow data outside the firewall. That’s prohibited a lot of this technology,” says Bryan Downer, vice president of sales and marketing at Sani-Matic.
“What we’ve seen more and more is that customers are recognizing it’s inevitable. Their IT departments have begun providing a means by which things like this can be done.”
Augmented reality (AR) and virtual reality (VR) technologies might have seemed relatively futuristic just months ago even. But with the restraints that COVID-19 is putting on facility access, they are becoming a more essential part of the toolbox. “Digital tools are boosting efficiency and avoiding downtime, which is always critical, but particularly so during COVID-19, when so many people are relying on a robust food supply,” says David Goforth, vice president of field sales for Ecolab’s Food and Beverage division in North America.
Ecolab, which provides cleaning and sanitation products and services, is leveraging Microsoft’s mixed-reality technology to enable social distancing and gain access to facilities that have closed or restricted access during the COVID-19 pandemic, helping them to keep operating, Goforth notes.
“Ecolab’s sales and technical representatives in the field can wear Microsoft HoloLens devices, which allows them to virtually connect to Ecolab’s scientists, engineers, and cross-functional teams for support,” he says. “This allows Ecolab to remotely diagnose and troubleshoot issues around contamination, our engineers to oversee chemistry usage, guide the installation of new equipment, monitor water quality, help train new employees and, ultimately, implement solutions. Response times are quicker and multiple experts can collaborate to diagnose and troubleshoot customer problems without having to travel to the site.”
Ecolab has pilot programs in place at dozens of its customer facilities across six regions. They’re using mixed reality to identify and fix tank leaks, cross-contamination, and site surveys, for example, and have also recognized and eliminated equipment malfunctions and corrected wastewater flow rates, Goforth says. “For one beverage producer, we instructed a new employee how to perform an acid wash and the trainer was completely remote,” he notes. “Very few people were needed to achieve these successful outcomes. The mixed-reality program can also save hours or days in response time, it may eliminate travel expenses, and it keeps our customers and associates safer.”
With customers across a range of industries, Ecolab is also using experience from those sectors to apply lessons learned back to food and beverage customers, Goforth adds.
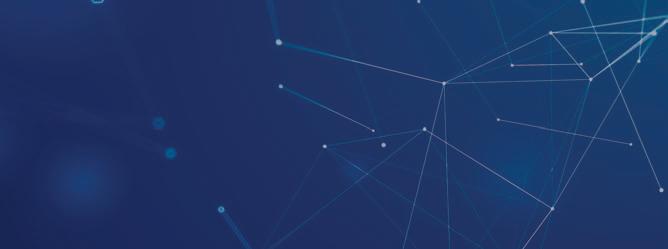
Ecolab is using augmented reality from Microsoft to help service its customers remotely, particularly in light of pandemic restrictions on access.
CONTINUED FROM PAGE 23
and barrier requirements, AURA is capable of being manually guided by human workers.
AURA’s hand-guiding capabilities are enabled by a touch-sensitive skin that covers its surface, which allows it to slow its speed and force when it comes into contact with a human operator. Moreover, 3D vision-enabled cameras are used to scan equipment and supply crates being retrieved by AURA to maximize its accuracy. Finally, a laser scanning system continuously monitors AURA’s workspace for speed and separation monitoring purposes.
“The synergy between two leading companies in the technological field, such as FPT Industrial and Comau, has led to an innovative solution focused on the collaborative AURA robot,” said Pietro Ottavis, chief technology officer for Comau. “Cobots and digital instruments are just some of the main technologies that Comau has developed following its own approach to Industry 4.0, called HuManufacturing, to create safe collaboration in production operations between humans and machines, called on to support humans in operations that require greater speed, strength, and repeatability, as well as dangerous operations.”
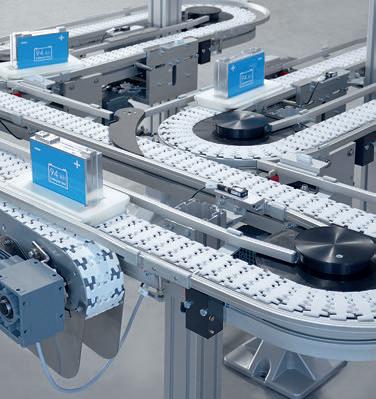
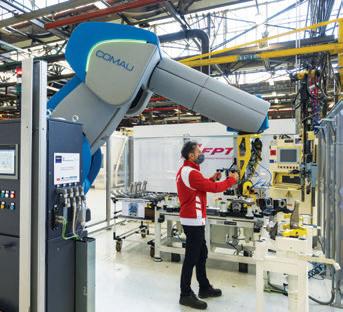
Versatile. Flexible. Modular. Flat Top Chain Conveyors
The perfect solution for complex layouts: • Pallet or product handling • Inclines, curves and loops • Diverters and merges
(860) 769-5500 | info@mknorthamerica.com better products. better solutions.
PACK EXPO Connects Engages CPGs Through March 31
By Sean Riley, Senior Director, Media and Industry Communications, PMMI
After bringing the industry together during its launch week Nov. 9-13, PACK EXPO Connects continues convening consumer packaged goods companies and brand owners with more than 700 exhibitors at packexpoconnects.com.
“This event continues to connect the industry, which was our number one goal in a year when professionals cannot attend physical trade events,” says Jim Pittas, president and CEO, PMMI. “And our exhibitors were remarkable in their ability to react and deliver effective demonstrations despite the technical challenges entirely outside of their control.”
Despite exhibitor preparedness, technical issues kept the live demonstrations from launching as intended on Monday, Nov. 9, but the PACK EXPO Connects exhibitors adapted, and demos returned for attendees looking to see technology in action the remainder of the live event.
Exhibitor Engage Technologies Corporation and its family of companies, including Squid Ink, Eastey, and AFM, attained nearly 1,000 new contacts during the live launch portion of PACK EXPO Connects, according to marketing manager Josh Nelson.
“We were successful in providing live demonstrations of our equipment after switching over to the Zoom platform after [a few] technical difficulties on Monday morning,” Nelson said. “We formed a plan as a team to put our demonstration agenda into an easily emailable format.”
Nelson was pleased with the feedback he received regarding their virtual showroom. Customers were particularly pleased with the interactions and detailed information his team could provide in the chat as the demonstrations were live.
Spee-Dee Packaging Machinery serves as a prime example of an exhibitor who pivoted on the fly to mine substantial success from PACK EXPO Connects.
“Spee-Dee was fortunate to have a successful demo on Monday via the PACK EXPO Connects platform, and then we jumped over to Facebook Live for our remaining demos,” says Dave Navin, president and CEO, Spee-Dee. “We plan to use the recorded content posted on the PACK EXPO Connects platform as a way to continue to build our brand and engage our customers. We have all found new ways to connect with our customers, which provides one more tool for us.”
In addition to demos, educational offerings—many debuting for the first time at PACK EXPO Connects—produced engagement that has been surpassing expectations. More than 800 attendees tuned in live to the keynote address by Kim Houchens, director, Customer Packaging Experience at Amazon, which remains available on-demand at packexpoconnects.com. The daily Jumpstart sessions each averaged 400 viewers seeking insights into key trends and technologies. And every day, more than a dozen Innovation Stages, afternoon Trend Chats, and Daily Downloads with PMMI Media Group editors attracted high daily participation. The Solutions Room wrapped up the week on Friday with targeted interactions from the OpX Leadership Network, Organization for Machine Automation and Control (OMAC), the Institute of Packaging Professionals, and the Contract Packaging Association.
“PACK EXPO Connects offered a unique opportunity to report on industry developments via a new digital format,” commented Jim Chrzan, vice president, content and brand development, PMMI Media Group. “I’m incredibly proud of our team and grateful to Amazon, General Mills, Bush Brothers, and many industry experts who presented. Engagement from the packaging and processing community was exciting to see, and the experience has expanded our vision of the many ways we can deliver content.”
Engagement will continue through March 31, 2021, with on-demand demos, educational sessions and showrooms remaining available as resources for industry professionals in the coming months.
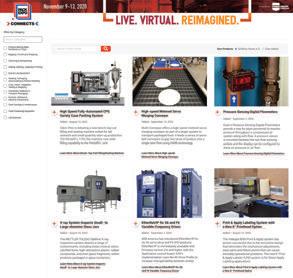
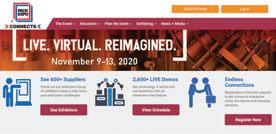
Picking, Placing, and Packing Robot Portfolio Expands
The focus on pick-and-pack robots at ABB’s PACK EXPO Connects exhibit re ected changes in direct-to-consumer and direct-to-store shipping trends, as well as hygiene-sensitive pick-and-place applications.
In response to the growth of omnichannel retailing and its requirements for manufacturers to handle both pallets and packaging destined for retail shelves—while also picking and packing highly varied items for shipping direct to individual consumers—ABB highlighted its new FlexPacker robot and PickMaster Twin software at PACK EXPO Connects.
The IRB 390 FlexPacker robot, with its 35% faster pick speed and 45% increase in payload of up to 15 kg (compared to ABB’s IRB 360-8/1130 FlexPicker), is available as a four- and five-axis variant delta robot.
Marc Segura, ABB’s managing director of consumer segments and service robotics, said ABB developed the IRB 390 FlexPacker with the food and beverage, logistics, pharmaceutical, and consumer packaged goods industries in mind. He added that the IRB 390 is designed for secondary packaging and higher payload applications, with the speed and flexibility to support shelf-ready packaging and retail-ready packaging. It features NSF H1 food grade lubricants and is built using an FDA-compliant material, suitable for use in hygienic environments.
In its exhibit, ABB demonstrated how the PickMaster Twin, ABB’s digital twin robotic software for vision-guided random flow picking-and-packing applications, enables the simulation of packing stations to optimize the picking process before the stations are physically constructed. This ability is said to dramatically shorten commissioning times from days to hours and reduce changeover times from hours to minutes, while maximizing overall line efficiency. The software also features a color vision system that can support up to 10 cameras for accurate position guidance and inspection.
Just prior to PACK EXPO Connects, ABB announced its acquisition of Codian Robotics, a well-known supplier of delta robots for high-precision pick-and-place applications. Codian’s robots are also recognized for their use in hygiene-sensitive industries, including food and beverage and pharmaceuticals.
Johannes Faden, strategic development manager at ABB for the company’s machine and factory automation business unit, explained that Codian’s portfolio of robots for hygienic food and beverage processing are built with FDAapproved materials, meet the IP69K waterproof standard, and can be cleaned with high pressure water and detergents.
“There is a strong need for pick-and-place robots that ensure high hygienic standards, which has been accelerated by the COVID19 pandemic. Our food and beverage, pharmaceutical, and logistics customers are particularly interested in the potential of automation, enabling supply chains to continue to function, while protecting employee welfare,” said Sami Atiya, president of ABB Robotics and Discrete Automation.
Faden noted that ABB’s interest in acquiring Codian was driven by the growing use of delta robots in pick-and-place applications in the food and beverage, pharmaceutical, and logistics industries. “Codian’s robot arms will be integrated into ABB’s IRC5/Omnicore control platform, RobotStudio simulation tools, and PickMaster picking software to expand our total solution platform for endcustomers and system integrators,” he said.
Check out the many packaging and automation technologies featured by ABB at their PACK EXPO Connects Virtual Showroom, Found at awgo.to/1118 and awgo.to/1119.
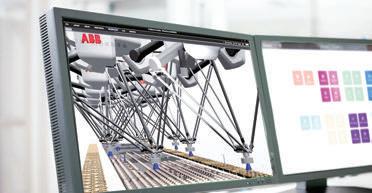
IIoT-Enabled Packaging with Multi-Purpose Servo
The new i950 servo drive from Lenze features three operation modes, providing exibility to OEMs to use the drive in multiple and custom-con gured packaging machine applications.
One of the clearest trends in modern automation technology is flexibility—the built-in capability of a device to perform more than one function or be used in more than one way. And flexibility of application is evident in Lenze’s new i950 servo drive. In its demo at PACK EXPO Connects, Lenze highlighted a key aspect of the i950’s flexibility via its three modes.
Dan Barrera, applications engineering manager at Lenze, explained the i950’s drive-based motion, which includes two of the servo drive’s modes. Those modes are: 1) drive parameterization using Lenze’s preconfigured FAST software application, which allows personnel who are not engineers or programmers to commission the drive and its application; and 2) custom configuration of the FAST applications, enabling OEMs and system integrators to access the code behind the applications using IEC 61131-3 programming languages to customize the pre-developed FAST software code for unique uses. Fieldbus protocols, like Profinet, EtherCAT, and EtherNet/IP, can be used to connect a Lenze controller or any third-party controller to the i950 in these two servo drive modes.
The i950’s third mode is control-based motion. “Using control-based motion, the i950 can be set up in CiA402 mode to receive commands from a main control motion system,” Barrera said. He noted that, for motioncentric applications, any third-party controller used with the i950 drive should support motion over EtherCAT.
The i950 can be used in packaging machinery for registration and synchronization, table positioning, camming, electrical gearing, and winding applications.
With respect to the drive’s IIoT enablement, Barrera pointed out the i950 supports MQTT communications to deliver the drive’s operational data to plant and enterprise systems.
The compact i950 servo is available with a power spectrum ranging from 0.55 kW–110 kW and features modular interfaces for fieldbus and feedback connections.
In addition to its operation and programming characteristics, six technology applications have been implemented in the i950 to save OEMs time and money when developing machine tasks.
These applications are: • Speed control, which can operate with and without feedback, to deliver high control performance with speed stability for conveyor and traveling drives. It also includes start-up and deceleration profiles, as well as process and torque control. • Electronic gearbox to enable precise speed- and position-synchronized drives in a network for the continuous transport of continuous materials such as paper, films, or textiles. • Table positioning enables management
of profile data sets and sequence profile control for discontinuously running conveying, lifting, and handling drives. This application provides profile generation and position at target and has an override function. • Synchronism with mark correction for the transport of continuous and archshaped materials or piece goods. • Winder with dancer control and winder with tension control enable speed-controlled drives for the storage or dispensing of continuous materials such as paper, film, or textiles and tension-controlled (open loop) drives for the storage or dispensing of continuous materials such as paper, film, or textiles, respectively.
Check out the many packaging and automation technologies featured by Lenze at their PACK EXPO Connects Virtual Showroom, found at awgo.to/1122.
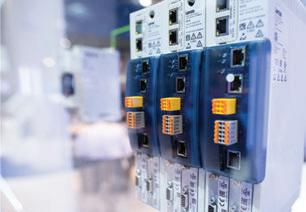
Material Handling by Levitation and Hygienic Linear Transport
Beckhoff’s XPlanar oating material handling system made its U.S. debut at PACK EXPO Connects. The company also introduced a stainless steel, hygienic version of it XTS material handling system.
First introduced in Europe in 2018, Beckhoff’s XPlanar technology—which enables “flying motion” for materials handling—made its North American debut at PACK EXPO Connects. The XPlanar system uses planar motor tiles as a base to levitate passive movers at speeds of four meters per second with acceleration rates up to 20 meters per sec2 .
The XPlanar tiles levitate by use of traveling magnetic fields generated in the planar tiles to precisely move objects in any kind of pattern through different tracks, enabling batch-of-one applications and flexibility in product handling. The tiles can be programmed to move as needed for an application by automatically lifting, lowering, tilting, or rotating while traveling.
Because the material handling tiles of the XPlanar system float above the surface, Beckhoff said XPlanar offers maintenancefree motion control for complex packaging, inspection, and material handling applications.
Collision avoidance for the tiles is put into effect once the user programs the XPlanar using TwinCAT 3 software, said Jeff Johnson, mechatronics product manager at Beckhoff. “The software includes all of the configuration tools, motion function blocks, and collision avoidance functionality. Because the movers travel on programmed tracks, users can prioritize cross-over tracks,” he said.
A particularly interesting feature of the XPlanar system is its anti-sloshing functionality, based in the TwinCAT 3 software, for use in applications involving movement of liquids. According to Johnson, the XPlanar anti-sloshing ability is enabled by the six axes of coordinated motion used on each mover. “Beckhoff has developed motion algorithms that create very smooth acceleration and deceleration profiles,” he said. “Think of it as a very soft ‘S’

curve for acceleration/deceleration.”
Johnson added that XPlanar’s planar motor tiles can be coated with stainless steel, glass or any another surface to “ensure XPlanar is a sanitary, wash-down-capable solution.” He added that Beckhoff supplies the motor tiles and movers, while the machine builder is “responsible for building the machine base and the tile coverings. In some cases, coverings will be unnecessary, and in others they will be critical. This offers the machine builder and end user flexibility in the design and implementation of XPlanar to suit their specific application.”
In terms of how XPlanar coordinates or connects with other systems for placement and removal of materials on the tiles, Johnson explained that products can be loaded onto XPlanar tiles via pick-and-place robots, the eXtended Transport System (XTS) from Beckhoff, manually, or via any other system the user chooses to integrate with XPlanar. “Most robot manufacturers offer high-speed EtherCAT interfaces which enable very fast and synchronized communications between XPlanar and the robot,” he added. “This creates a faster cycle time versus using an asynchronous Ethernet protocol.”
Hygienic handling
Also featured by Beckhoff at its PACK EXPO Connects exhibit was the XTS Hygienic—a stainless steel, IP69K version of the XTS system featured at PACK EXPO 2019. This new hygienic version is designed for wash-down production environments in packaging, pharmaceuticals, and food and beverage.
Beckhoff’s XTS material handling system combines rotary and linear drive principles into a linear transport system for packaging machines. The system features customizable motor modules, mechanical guide rails, wireless movers, power electronics, EtherCAT communication, and position measurement in a compact form factor that Beckhoff says reduces the machine footprint up to 50%. The XTS movers can move as fast as four meters per second and achieve acceleration exceeding 100 meters per second2. The XTS’s flexibility allows it to be designed in circles, clothoids, S-curves, or in straight segments. The tracks can operate horizontally, vertically, or at angles, and can handle parts with single or multiple movers.
In the new XTS Hygienic version showcased at PACK EXPO Connects, the system’s new Track Management functionality was also highlighted. This allows individual movers to transfer between multiple XTS systems, enabling further customization, quality inspection, and automatic defect ejection.
Explaining which components of the XTS Hygienic version are stainless steel, Johnson said, “The motor modules and rails are stainless, while the movers have stainless and aluminum options. There is also a NiTuff coating option for the aluminum machine base. Since it is rated IP69K, we went to great lengths to design it for easy cleaning by including food-safe seals and ensuring that the surface can withstand harsh chemicals in washdown environments.”
The XTS also has the ability for its carriers to be tilted—like the tiles on the XPlanar system—even though the XTS has just one axis of linear motion.
Check out the many packaging and automation technologies featured by Beckhoff at their PACK EXPO Connects Virtual Showroom, found at awgo.to/1120.
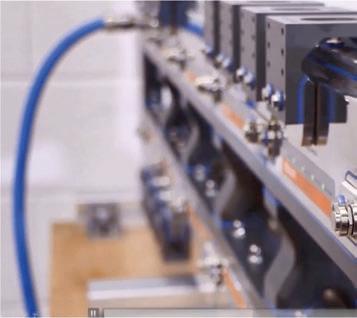
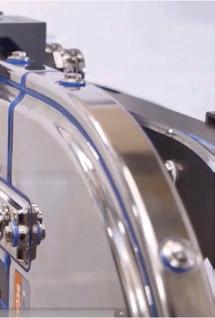
All-in-One Feeder Systems and a Lightweight 6-Axis Robot
Epson Robots highlighted new additions to its IntelliFlex series of exible feeding systems and its highest payload, highest reach robot for packaging, kitting, machine tending, or palletizing.
Epson Robots debuted the two newest additions to its IntelliFlex flexible feeder system line-up at PACK EXPO Connects. The new additions are the IntelliFlex 80 for handling small parts (3mm to 15mm) and the IntelliFlex 380 for large parts (15mm to 60mm). These systems join the IntelliFlex 240 (for part sizes 5mm to 40mm) and the IntelliFlex 530 (for part sizes of 30mm to 150mm). These flexible feeder systems are used to feed consumer goods for packaging in kits, as well as sorting of electronics and medical device parts for packaging.
A key aspect of Epson Robots’ approach to flexible feeding systems is its all-in-one system delivery. Stacey Tieu, product manager at Epson Robots, explained that common flexible feeder systems are composed of separate feeder communication protocols; feeder tuning requirements; vision system calibration and programming; and system programming and optimization to coordinate the robot, feeder, and vision system. Epson Robots’ approach is to combine all these components into one system that integrates the vision programming, part tuning, and parts control adjustment. This allows for the Epson IntelliFlex system to be set up and running in one day, rather than the weeks it typically takes to set up a flexible feeder system, according to Tieu.
“IntelliFlex is a great alternative to bowl feeders,” said Tieu. “With bowl feeders, if you happen to change a part, you have to go out and buy a new bowl feeder or modify your existing one to handle the new part. “With IntelliFlex, you don't have to retool the system, it can accommodate different part sizes as well as different part and material types.”
This inherent adaptability of IntelliFlex is made possible by Epson’s RC+ integrated software environment, which is used to program and control all aspects of the flexible feeder system. “It’s also what enables
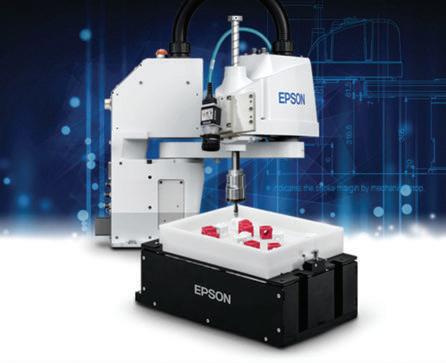
the IntelliFlex to be set up so quickly,” Tieu added. “We have built-in command sets for parts feeding so that engineers don't have to figure this out themselves. The user interface provides a point-and-click way to program the feeder.
The software environment’s use of artificial intelligence enables autotuning of the IntelliFlex system. Aaron Donlon, Epson product manager, explained that, in the RC+ environment, “if you set up the system for one part and then need to move to the next part for a different product, setting up that new part in the system is very easy with all the built-in wizards. You literally just drop 10 parts on the feeder and it uses the built-in algorithm to determine the right set of vibrations or frequency to spread those parts out for optimized feeding. There’s no trial and error with this process, you just let the machine do the automated tuning calibration for you.”
Donlon noted that the longest he’s seen the system take to self-adjust to new parts is five minutes, but that the process typically takes about two minutes.
Lightweight 6-axis robot
Though Epson Robots is well known for its SCARA robots, the company has been producing 6-axis robots for 25 years. The newest addition to the company’s C series of 6-axis robots is the C12XL—Epson Robots’ highest payload and highest reach robot released to date. It features a 12kg payload capacity and a reach of 1400mm.
As with Epson’s other 6-axis robots, the C12XL has a slim, lightweight design due to its use of Epson’s QMEMS (quartz micro electro-mechanical system) technology in the robot’s gyro sensors, which are part of the servo system. This technology dramatically reduces the weight of the robot, allows for low residual vibration, and minimizes overshoot with smooth end-of-arm motion, according to Epson.
“Many robots on the market use a lot of mass to dampen out the vibration,” said Aaron Donlon, Epson Robots product manager. “We use the QMEMS technology to cancel out the vibration and that allows us to have a lighter weight, faster, and higherperforming robot. That's how we get a 65kg robot and a smaller controller with that level of payload capacity.”
According to Epson, the C12XL features high acceleration/deceleration rates and high-speed cycle times to optimize parts throughput. Its compact wrist pitch enables access to hard-to-reach areas. ISO 4 Cleanroom models of the C12XL are also available. In the cleanroom version, protective covers are used to avoid static buildup and a vacuum port in base pulls particles in.
Usable as a stand-alone robot or as part of line, Donlon noted the C12XL will excel in end-of-line applications such as packaging, kitting, material handling, or palletizing.
An integrated vision option is also available for the C12XL.
Check out the many packaging and automation technologies featured by Epson Robots at their PACK EXPO Connects Virtual Showroom, found at awgo.to/1121.

New Material Handling and Traceability Systems
In its exhibit at PACK EXPO Connects, Omron introduced a new mobile robot, highlighted new vision and picking capabilities for collaborative robots, and demonstrated a new data communication product for managing Industrial Internet of Things data transfer.
Robot technologies have been gaining ground across the packaging and processing industries over the past few years based on their increasing ease of deployment, programming, and use. The effects of the pandemic across industry have also increased the growing interest in robotics due to their ability to help address social distancing requirements and industry’s ongoing workforce development issues.
At PACK EXPO Connects, Omron Automation highlighted three of its robot products designed to address specific packaging and processing applications.
One of these robots is Omron’s new HD-1500—an autonomous, intelligent mobile robot that can handle payloads of up to 1500kg. Omron’s demo of this robot showcased the robot’s use of lasers to provide 360 degrees of safety coverage as well as its sensor, which allows for precise pickup and drop-off of materials. The HD-1500 uses Omron’s Fleet Manager software, which enables the robot to calculate the best route for material transport while navigating safely around people and obstacles without the use of magnetic floor tapes or other guides. Omron’s Fleet Manager can control up to 100 mobile robots of different sizes, configurations and payload capacities, such as Omron’s other mobile robots—the LD-60/90 and LD-250. “The HD-1500 is specifically designed for industrial environments and allows for the movement of large payloads while reducing the need for forklifts,” said Kate Cramer, automation engineer at Omron Automation. “Typical applications include high-payload transporting of materials or finished products such as wrapped pallets, modular equipment, and subassemblies to and from the warehouse or from one location to the next.”
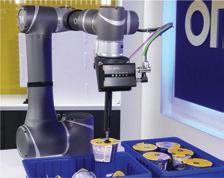
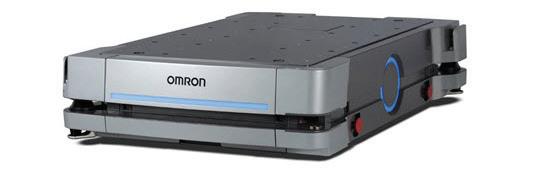
Bin picking
Omron also gave PACK EXPO Connects attendees a preview of its forthcoming FH-3D Vision Sensor, which will be available for purchase in April 2021. To demonstrate this new sensor, Omron showed how it works with the company’s TM collaborative robot.
Danielle Belskis, automation engineer at Omron Automation, said Omron developed the FH Series 3D camera to solve robotic bin picking applications. “Our collaborative robot, when equipped with our new 3D vision camera, is able to pick up known objects with random overlapping positions out of a bin. Traditionally, this was difficult to automate due to varying weights, shapes, and orientations of objects that require 3D location and different forces during picking. The FH Series 3D camera locates the various objects in the bin and sends their coordinates to the robot, while the cobot’s software makes the advanced calculations required for optimized trajectory and force to pick up objects.”
Traceability
In Omron’s Traceability 4.0 demo, Brian Jeppesen, automation engineering supervisor at Omron Automation’s Technology Center, used an Omron NX102 automation controller, a mechanical stage with a concentric ring, Omron’s G5 servo system, and Omron’s FH vision system. He explained that, in this setup, the NX102 automation control-
ler sends motion commands to the G5 servo system. The servo system then sends position data back to the automation controller, which then determines the correct time to trigger the camera and send triggers to the FH-5050 vision system.
“The vision system triggers the camera and the strobe light and the camera passes the image back to the vision system,” Jeppesen explained. “The FH-5050 processes the image and decodes the 2D code. The code value is sent back to the NX102, which sends the decoded data to the cloud using the MQTT protocol. And all of these processes can be programmed and monitored using the Omron’s Sysmac Studio software.”
With the controller’s ability to send data to the cloud via MQTT, Jeppesen said “one of the major benefits of this Traceability 4.0 solution is having the ability to get information scanned at the point of origin and then become immediately available for analysis using cloud services.”
The ability to quickly access and analyze this kind of granular production data is critical to industries such as the food and beverage packaging industry so that contaminated products can be traced to a specific serial number or a lot number. With this level of detail, it means that “all products with a specific part number need not be discarded, only the products with that specific lot number or serial number range would need to be discarded,” Jeppesen said.
Check out the many packaging and automation technologies featured by Omron Automation at their PACK EXPO Connects Virtual Showroom, found at awgo.to/1123.

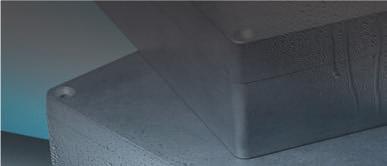

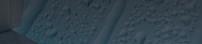
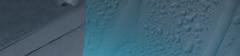
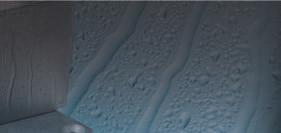
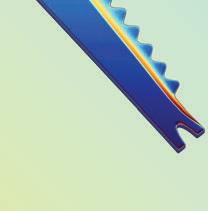


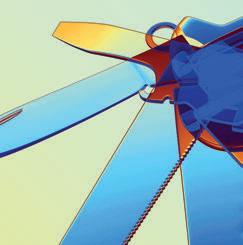
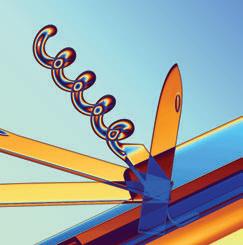
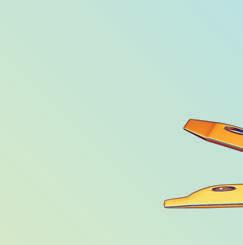
Sensor Fusion: The Swiss The Swiss Army Knife of Army Knife of Digitalization Digitalization
With the proper communication protocols and network architecture in place, smart sensor network architecture in place, smart sensor technology and the data it provides can be the technology and the data it provides can be the bulwark on which digital transformation is built. bulwark on which digital transformation is built.
If industrial control systems are the brains of a plant, then sensors are its brains of a plant, then sensors are its eyes and ears. Simply put, without eyes and ears. Simply put, without sensors there would be nothing for sensors there would be nothing for SCADA, DCS, or PLCs to respond to. SCADA, DCS, or PLCs to respond to. That’s why increasingly intelligent or “smart” That’s why increasingly intelligent or “smart” sensors packing more onboard processing sensors packing more onboard processing power, the ability to monitor new variables, power, the ability to monitor new variables, and digital communication capabilities are and digital communication capabilities are playing such an important role in helping playing such an important role in helping plant operators and enterprise level planners plant operators and enterprise level planners alike to see better and respond to problems alike to see better and respond to problems with more finesse. with more finesse.
In the past, sensors were largely relegated In the past, sensors were largely relegated to the status of mere on-off switches. When to the status of mere on-off switches. When inputs such as temperature, flow, or proximinputs such as temperature, flow, or proximity pass a certain threshold, an analog sensor ity pass a certain threshold, an analog sensor sends out a current or voltage signal to set a sends out a current or voltage signal to set a simple control loop into action. For instance, simple control loop into action. For instance, fans could speed up or slow down, control fans could speed up or slow down, control valves might change position, or bumpers on valves might change position, or bumpers on a conveyor may be actuated.
Today’s smart sensors, however, are different in a number of ways, says Manikandan Nambiar, vice president of product management for Plantweb and reliability solutions at Emerson Automation Solutions. Most importantly, many contain micro electro-mechanical systems (MEMS) along with onboard microcontrollers, which allow them to collect and process more information in real-time.
The use of this technology in modern sensors reflects two major trends at play: The first is “sensor fusion,” or the ability for a single sensor to monitor multiple input types, leading not only to more granular insights, but cost efficiencies as well. In essence, more data can be attained without needing to invest in multiple devices. Secondly, the capacity to track how inputs are changing over time may allow maintenance personnel and others to move from engaging in a merely reactive approach—that is, responding to a problem when an on-off switch is tripped—to truly understanding the root cause of a failure and moving to prevent it from happening again.
“There’s a lot of different ways to define a smart sensor, depending on the type you’re talking about; but in my mind, where the smarts really come in is with these MEMS along with the microcontrollers,” says Christopher Koch, senior application engineer for connected devices and solutions at Bosch Rexroth. “When you add these components, you can have sensors that have accelerometers, gyroscopes, and magnetometers all combined into one; or environmental sensors that have temperature, pressure, and humidity all together. Then you have the ability to communicate that data into upstream analytics sites. That’s really what a smart sensing device is.”
Communication protocols and network architecture
The evolution of smart sensing technology to its current state has been a long time coming. The edge computing power present in modern sensors is largely the result of Moore’s Law (the observation that the number of transistors in an integrated circuit doubles every two years), yielding exponential growth in processing power and fueling the endless array of ever-smaller devices we continue to make use of.
However, smart sensors didn’t develop in a vacuum, and their value can’t be fully tapped in one either. According to Balluff marketing manager Shishir Rege, numerous communication protocols and network architecture complexities have often hampered their deployment. Just as sense organs are of little use without the neural pathways that carry the information they gather to the brain, smart sensors with no effective means of communication are little more than expensive hunks of circuitry. Solving these problems over the past decade has greatly accelerated new sensor adoption and will continue to do so.
The TDL110 Bosch Rexroth Transport Data Logger senses and records relevant temperature, humidity, tilt, and shock events.
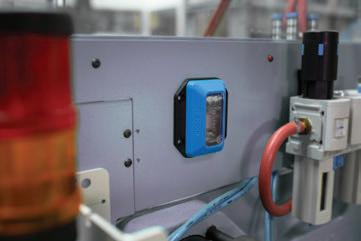
According to Ballu Marketing Manager Shishir Rege, IO-Link has been a major enabling technology for the proliferation of smart sensors.
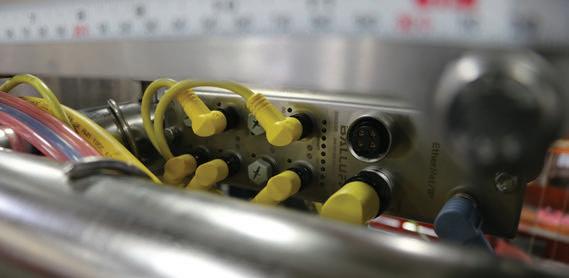
While digital network protocols, such as HART, have been of some utility in this regard, Rege notes that the real breakthrough has been in device-to-device communication technology such as IO-Link. First developed by a consortium of industry stakeholders and automation suppliers in 2006, IOLink is a fieldbus agnostic point-to-point networking standard that allows sensors and actuators to send and receive data from higher-level controllers with standard cabling.
For example, numerous smart sensors outfitted with IOLink chips can communicate with a single IO-Link master via standard three or five pin connectors and IO-Link can pass that data to a control system over any other Fieldbus protocol. Users can then “rinse and repeat” in either direction.
The most obvious advantage this arrangement confers is that, by being able to employ low-cost standard cabling, both compatibility and economic efficiency are ensured. Yet there are other gains to be had as well. For instance, Rege observes that, by eliminating the need to assign individual IP addresses to each sensor on a network, a great deal of programming and other configuration tasks can be replaced with a simple plug-and-play model.
“With IO-Link, you can use a standard cable that used to plug into an analog sensor; so you can basically just unscrew the old one wholesale and put the new one in,” says Jack Moermond, engineering partner manager at Balluff. “We now have the ability to do with one sensor what it used to take multiple technologies to achieve because IO-Link makes configuration so much easier. Years ago, you had to use an analog network module if you wanted to do a simple distance measuring sensor. Now, you can put IO-Link right out there next to the device, run a standard four connector cable as far as you want, and you’re getting additional digital value right away.”
Endless applications
Once the proper communication and network infrastructure are in place, the true power of the dizzying array of smart sensors available on the market can be fully brought to bear on production. Potential applications are almost endless, spanning predictive maintenance, supply chain optimization, and even enterprise level planning. In many cases, successful deployments rely as much on the ingenuity of operators as the capacities of the hardware itself.
According to Koch, predictive maintenance in particular rises to the fore. Consider a mining operation where large pumps are used to move hard rock slurries through pipelines. Rubber encasements are placed along the interior of the pumps to prevent them from being punctured or eroded, and maintenance is scheduled to ensure the integrity of the housings every three to six months. These inspections require that the entire line be shut down, often for a full day, even if no changeover is required. By employing an intelligent accelerometer sensor instead, the changing rate at which the slurry moves through the pump can be used to deduce when maintenance is actually necessary, saving precious time and labor.
Also, it’s important to note that the value to be tapped from these sensors need not be limited to the confines of a single operation. Often, by aggregating plant level data across numerous sites, along with external variables such
H o w Y o u W a n t T h e m , W h e n Y o u W a n t T h e m Short lead times for custom or off-the-shelf cylinders
FABCO-AIR
A member of Festo Group
F S e r i e s
Confi gurable general purpose cylinder Twelve bore sizes (5/16 to 3”) and standard strokes to 32” Options include adjustable air cushions, Viton® seals, rod wipers and more Support for food packaging or washdown environments
P a n c a k e I I
Robust compact actuator Eight bore sizes (1/2 to 4”) and up to 9” stroke standard Composite body enables impact resistant, self-lubricating operation Composite rod bearing for reduced wear and increased load capacity
O E M N F P A
Cost-optimized NFPA interchangeable pneumatic cylinder Five bore sizes (1-1/2 to 4”) and strokes up to 48” standard Adjustable air cushions and magnet for position sensing standard Variety of NFPA mounting options
as weather conditions or GPS coordinates, even more advanced efficiencies can be attained, says Mike Hamoy, product manager at Omron Automation.
As an example, imagine a company running two plants that perform the same tasks in different parts of the world where the seasons differ. If the first plant were to optimize its winter operations to adjust for changing demand or environmental effects on equipment performance while it is still summer time for the second plant, the data gathered from the initiative could later be used to model a similar repeat transition and maintain a more consistent product output across locations.
Self-learning
Such data aggregation trends speak to a world where plant data is increasingly shipped upward to the enterprise level to be mined for new aggregate insights—a prospect that would be impossible without sensor level data. With much of industry moving into a landscape of tightening margins, cutting costs and squeezing new efficiencies out of production may be the new normal. As a result, smart sensors capable of providing richer data will almost certainly continue to play a role in the transition to Industry 4.0.
Moving forward, artificial intelligence (AI) and machine learning could be the next major frontier. Data is the key to enabling the algorithms that drive these breakthroughs, and more is never enough. Hence, as sensors become more ubiquitous, multimodal, and precise, the storehouses of data needed to nourish burgeoning AI applications will only grow.
“Right now, we implement sensors and then data analysts have to look through all of the data gathered, determine what it means, and then program the system so that it knows what to do,” Koch says. “As we move toward [greater use of] artificial intelligence, we’ll start to see self-learning algorithms that help us to move away from that long learning stage. You’ll buy a sensor, plug it in, and it will learn what the processes are, learn what is good and bad, all on its own.”
As for the hurdles that remain, growing quantities of available data may turn out to be a double-edged sword. While this surplus of information can enable unprecedented coordination and efficiency, dealing with it may prove overwhelming for many. With hundreds of sensors providing new readings every millisecond, terabytes of data could be created in mere days. Sorting, analyzing, and finding ways to use this data will be a tall order indeed.
Still, the emergence and accelerating deployment of smart sensor technology is just one more promising step along the road to the full realization of Industry 4.0.
Omron’s E3NX and E3NC sensors with E3NW communications modules streamline batch changes and support more thorough data collection.
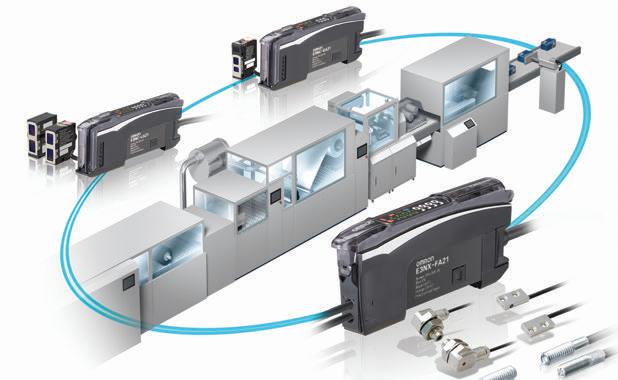