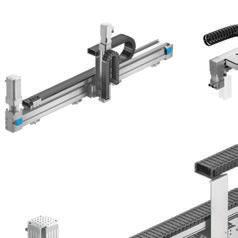
31 minute read
INDUSTRIAL INTERNET OF THINGS
from OEM Spring 2021
Understanding Robots and Their Role in IIoT
For a half century now, robots have been the centerpiece of Industry 3.0—the age of pre-digital automation. They will be just as critical, if not more so, as the world transitions to the digital automation age of Industry 4.0.
By Kevin Tardif, business development specialist - electric automation, Festo
The image of the large, six-axis articulated robot welding car and truck bodies became fixed in the popular imagination in the 1970s and 1980s. Since then, articulated robots have spread throughout and beyond heavy industry with many improvements to the robot itself, as well as the development of more end effectors (end of arm tooling) to address the wider need for flexible automation.
Articulated robots are used in sectors as diverse as healthcare, food and beverage, steelmaking, and warehousing—wherever there are repetitive or environmentally or ergonomically challenging tasks that can be accomplished faster, more reliably, and/or more cost-effectively.
Robot basics
Initially, this robot revolution provided major manufacturers like automakers with even greater economies of scale but offered nothing to most small- and medium-sized businesses. More recent developments in cartesian robotics (linear), SCARA and delta robots—along with collaborative robots— have made automation accessible to businesses of almost any size.
Each type of robot comes with benefits and limitations. For new adopters of robotics, it’s important to understand those possibilities and pitfalls.
Robots come with 1-7 axes, each axis providing a degree of freedom. A two-axis cartesian gantry typically plots on the X-Y or Y-Z axes. A three-axis robot has three degrees of freedom and performs its functions through the X-Y-Z axes. These small robots are rigid in form, and cannot tilt or rotate themselves, although they can have attached tooling that can swivel or rotate or adapt to the shape of a small payload. Four- and five-axis robots have additional flexibility to rotate and tilt. A six-axis articulated robot has six degrees of freedom—the flexibility to move objects in any directions or rotate them in any orientation. The latter type is generally chosen when an application requires complex manipulation of objects. The seventh axis allows extended reach in one axis; in other words, it allows displacement of the six-axis articulated robots.
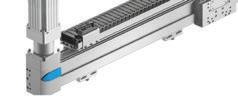
Cartesian Robots
Articulated robots
The popularity of six- and seven-axis articulated robots reflects the great flexibility that six degrees of freedom permit. They are easy to program, come with their own controller and movement sequences, and I/O activation can be programmed via a user-friendly teach pendant. On the hardware side, industrial articulated robots can be relatively small or massive. They can have substantial reach, over three meters with certain models.
The articulated robot also has issues which can restrict its utility or boost its cost profile. A small-sized articulated robot is easy to install; its base only need be bolted to a frame or floor. But it can only lift so much or reach so far.
Where the job requires a larger robot, civil engineering may be required to ensure the structure can handle the weight and torque caused by the load offset. The longer the reach, the greater the payload it can manage, the more space and engineering it requires, the more it costs.
An articulated robot also has singularities, i.e., locations and orientations in the surrounding space it cannot access. These spatial limitations require more complex safety precautions since the robot will often be used in zones where workers are present, even just occasionally. Expensive devices, such as zone scanners or safety mats are often necessary, and more advanced functionalities are then required, such as Safely Limited Speed (SLS), or Safe Speed Monitor (SSM). The fact it requires its own controller to handle the inverse kinematics can also represent a double dip from a hardware perspective since, in certain cases, the robot controller will need to communicate with a higher-level PLC on the production line.
Cartesian robots
A cartesian or linear robot consists of an assembly of linear actuators and sometimes a rotary actuator at the end of arm. The cartesian robot is fully adaptable; strokes and sizes of each axis can be customized to the application. Its reach and payload are independent of each other, not intertwined. The linear axis comes in a number of designs which further adapt it to the function it performs. For example, toothed belt actuators allow high velocities while ball screw actuators permit high precision and high feed force, with pick rates up to 100/min fairly typical.
The adaptability of these handling systems makes them price-optimized for a wide range of straightforward applications where the dexterity of an articulated robot isn’t required. That can involve extremely light to very heavy parts placement, sorting or boxloading, device inspection, and much more. Another major advantage and differentiator of the cartesian robot is its excellent space economy. It allows full access to the footprint it occupies. There is no dead space or singularities. Safety requirements are less stringent and hence less costly since the robot’s reach is limited to its small working zone.
Since the actuators are moving along the workspace coordinate system axis, interpolation of the motors position is not mandatory to determine the robot end-of-arm position in space. In other words, no calculation of inverse kinematics is needed. The system PLC can often be used to control each axis directly, without the addition of a second controller.
The cartesian robot’s main limitation is comparative inflexibility. It will easily accommodate linear movement in three axes, and a fourth, rotative axis. However, one has to add a motion controller to perform more complex synchronized tasks, such as CNC. Cartesian robots are rarely used in washdown environments, as they don’t provide sufficient protection against water ingress.
Finally, cartesian robots, if used without a separate motion controller, may require more programming time than other robot types. Teach pendants are less common, so programming of sequences must be done in the PLC, with each axis addressed and commissioned individually.
Collaborative Robot SCARA robots

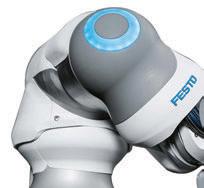
SCARA (Selective Compliance Articulated Robot Arm) robots have been designed and optimized for light applications. They are a streamlined version of articulated robots. They are very adept at functions like inserting components in spaces with tight tolerances while maintaining their rigidity in such movements, which makes them a cost-effective choice in pick-and-place applications as well as small parts handling. Programming and commissioning is relatively easy and fast, using the manufacturer-supplied teach pendant.
A SCARA robot requires a dedicated robot controller and is generally restricted to three axes. It may be the optimal solution where its full capability—three or four degrees of freedom—can be used. If the job only requires two (horizontal and vertical movement, for example), the SCARA robot cannot be reduced to a two-axis system, making it less attractive than a cartesian gantry-style robot from both the cost and performance standpoint. Like the articulated robot, the SCARA robot footprint also extends further than the working zone, resulting in a loss of functional space in and around the unit.
Delta robots
The delta robot is mainly renowned for its speed, with pick rates up to 300/min. Its mounting type puts it above its working zone, limiting the loss of footprint. It is often paired with a vision system to pick pieces randomly placed in more complex sorting and packing applications. Just like the articulated and SCARA robot, it will generally be provided with a teach pendant for easy programming.
The payload capacity of a delta robot is generally much lower than alternative technologies, and its inverse tripod design makes it less robust than the other robot options.
The delta robot has a limited working envelope, as its design does not allow long reaches. Like cartesian and SCARA robots, delta robots are generally limited to four axes and cannot provide the flexibility of an articulated robot.
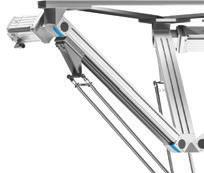

Delta Robot
Collaborative robots
integrated into industry. A cobot can be an articulated, cartesian, By allowing a direct collaboration between SCARA, or delta robot, although most would a worker and robot, collaborative robots be categorized as articulated. They come with (cobots) are adding a dimension to our payload capacity of 4-35 kg. The difference understanding of how automation can be understanding of how automation can be between cobots and other robots is their builtbetween cobots and other robots is their built-
SCARA Robot

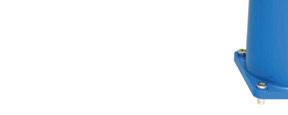
in safety features that allow direct interaction with humans without protective shielding, safety curtains, or other safety features.
Since they don’t need fixed external safety barriers, some cobots can be mounted on mobile platforms to go wherever they are needed. It is important to note that a safety evaluation of the application has to be done and, while the cobot itself might be safe, if the tool being used on its end of arm is sharp, an external safety barrier likely would be needed.
The greatest value of cobots is where they can free a skilled employee from the menial aspects of their job to concentrate exclusively on the high value aspects. For example, in complex device assembly requiring a deft human touch, a cobot can perform simple handling or manufacturing tasks in support of the worker, who can then focus exclusively on the part of the job that makes full use of their skills or knowledge.
The proliferation of various robot technologies has enabled businesses of all sizes to access the benefits of Industry 4.0 and digital automation. The best choice of robot usually comes down to the one that is the best fit— not just in terms of an application’s technical requirements, but also from the standpoint of related issues like productivity, plant safety, space utilization, cost, and more.
Growing New Business with Edge Computing
Industrial companies’ innovative approaches to market demands, enabled by industrial edge devices, illustrate how edge device technology is enabling manufacturers to be more adaptive and profi table.
By Josh Eastburn, director of technical marketing, Opto 22
As industrial edge devices become more common for building connected systems in the Industrial Internet of Things (IIoT) and automation, they are creating new business opportunities for system integrators and manufacturers. By simplifying the traditional architectures required to connect field assets to software systems, edge devices make many applications more affordable and practical.
Let’s look at a couple of real-world examples.
Easy EaaS
Equipment-as-a-service (EaaS) involves renting out or providing access to equipment and collecting payment periodically, rather than selling the equipment outright. This payment model enables end users to pay for costly or infrequently used equipment as an ongoing operating expense, which can open new markets for machine builders.
Martins Electrical Service, a Pennsylvaniabased system integrator, was hired to design a new EaaS option for an automated truck wash system. Shumaker Industries, the manufacturer of the wash system, wanted to add a remote monitoring option for customers interested in a rent-to-own arrangement. However, the programmable logic controller (PLC) they used didn’t have the ability to perform the database transactions needed to record monitor usage.
Initially, Martins experimented with a proprietary remote monitoring system—wireless sensors that pumped data into a cloud database through a local IoT gateway. The problem with this system was that it could only deliver updates every 10 minutes and the data was locked in the vendor’s private storage system.
Then Martins heard about Opto 22’s groov RIO edge I/O module and decided to tranther approach.
Rather than installing additional sensors, Martins used groov RIO’s 10 software-configurable I/O channels to capture existing sensor data in parallel with the wash system’s PLC. Using Node-Red—IBM’s open-source
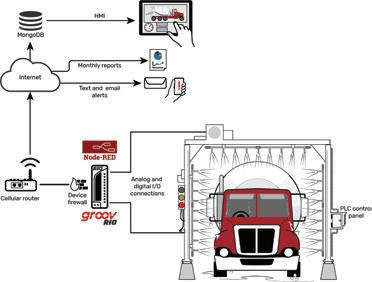
Martins’ monitoring system uses groov RIO to grab existing I/O signals, send them into cloud storage, and generate useful alerts and reports.
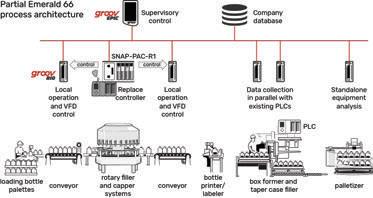
NACI used Opto 22’s groov edge devices and SNAP I/O to address a variety of integration scenarios.
IoT platform embedded in groov RIO—they organized the I/O data into timestamped sets associated with a vehicle number. They then connected a 4G cellular router to the groov RIO module and pushed the data structures into cloud-hosted storage rented from MongoDB.
This arrangement allowed them to deliver a scalable monitoring system without worrying about vendor lock-in or IT infrastructure maintenance. And by simply grabbing existing I/O signals, they avoided the need to communicate with or modify the manufacturer’s existing PLC controls.
To complete their EaaS design, Martins built a web-based dashboard that let Shumaker visualize the wash system in operation with one-second resolution. The system also generates email and text alerts in Node-Red, including a monthly report on the number of trucks processed by each system, which Shumaker uses to calculate billing.
“Since it’s an edge device, with security built in, groov RIO is perfect,” says Leslie Martin, an automation technician at Martins. “It’s a small add-on, so it’s easy to make an option for customers.”
From concrete to enterprise
Another example of rapid development with edge computing comes from system integrator equipment manufacturer Northeast Automation Company Inc. (NACI). Responding to increased demand for hand sanitizer in the early months of the COVID19 pandemic, NACI was hired by Emerald 66, a co-packaging and distribution company, to help them set up an automated bottling and packaging process.
With nothing but investor money and an empty denim processing plant, Emerald 66’s goal was to go as fast as possible. The company understood they were competing against low-paid, high-volume workforces operating manually and believed they could use technology to do more with a smaller, better-paid workforce.
The quickest way for Emerald 66 to build a new packaging process was by acquiring a variety of equipment at auction, leaving NACI the task of integrating it into a cohesive system.
NACI decided to make Opto 22’s groov products the focus of their strategy, so they could capitalize on the flexibility offered by edge devices. They used groov EPIC edge programmable industrial controllers to supervise the process lines, control equipment not already managed by a control system, and manage database transactions.
In addition, NACI used groov RIO edge I/O modules as a rapidly deployed remote I/O solution. As each new piece of equipment came online, NACI dropped in a powerover-Ethernet groov RIO module and used its software-configurable channels to identify the kinds of signals the unit provided. Next, the module was used to mirror the I/O signals in parallel with any existing PLCs and to integrate that data into the groov EPIC control system.
This integration required no modifications to the control systems already in place, allowing NACI to move very quickly. In three months, they had 15 pieces of equipment up and running.
From here, automation of applications grew from processing a high volume of one-gallon, single-formulation containers to working with a variety of sanitizer chemistries in different batch sizes and packaging form factors—from small two-, four-, six-, and eight-ounce containers, hand pumps, and spray bottles, to large jugs in excess of one gallon.
Fortunately, NACI’s decision to use a loosely coupled process line made it easy to modify individual segments without interrupting data collection and integration. In combination with on-site panel building and 3D printing capabilities, NACI’s investment in edge-oriented automation allowed them to retool very quickly. Emerald 66 was able to break even on their initial investment within six months.
As Emerald 66 continues to diversify its business, it has also found a valuable niche in original equipment development for overseas export. In one example, using groov EPIC and RIO, NACI took an inline mixer design from concept to implementation in about five days, including a mobile operator interface they built using the EPIC’s embedded groov View HMI server. By their estimate, they implemented the controls in about four hours for a system Emerald 66 will sell for $50,000.
“The fluidity and dynamics of modern manufacturing requires extremely fast response to changing market demands,” says Tom Coombs, principal engineer at NACI. “With groov EPIC and groov RIO, Opto 22 puts dynamic manufacturing data at the edge of the production line and into enterprise systems simultaneously in real-time.”
Keys to agility
The key to rapid automation development in both of these cases stems from the flexibility provided by industrial edge devices. With embedded general-purpose computing, networking, and storage, edge devices are able to assimilate automation functions traditionally requiring multiple devices and more

Opto 22’s groov EPIC and groov RIO industrial edge devices simplify traditional automation and speed up development of connected systems.
complex configuration.
Martins used groov RIO to process I/O data, open a secure connection with cloud services, execute database transactions, and generate reports. In an Industry 3.0 technology stack, all of this would typically require a local PC running multiple applications, meaning more complex and costly security, licensing, and maintenance procedures.
NACI used groov RIO and EPIC in combination to address a variety of integration needs while simultaneously building central data collection and process improvement capabilities. Because each component of the system is capable of handling sensing, control, data processing, and database transactions, the system could be expanded and reconfigured dynamically to keep up with the pace of change.
Given the economic pressures and increased pace of tech adoption that continue even as the world slowly exits the pandemic era, it is likely that designers will look more frequently to edge computing in search of this kind of competitive advantage.
6KRUWOHDGWLPHVIRUFXVWRP RURIIWKHVKHOIF\OLQGHUV
FABCO-AIR
A member of Festo Group
F Series
FXVKLRQV9LWRQ®VHDOVURGZLSHUV
DQGPRUH • 6XSSRUWIRUIRRGSDFNDJLQJRU
ZDVKGRZQHQYLURQPHQWV
Pancake II
• 5REXVWFRPSDFWDFWXDWRU • (LJKWERUHVL]HVWRÏDQGXSWR ÏVWURNHVWDQGDUG • &RPSRVLWHERG\HQDEOHVLPSDFW
ZHDUDQGLQFUHDVHGORDGFDSDFLW\
OEM NFPA
• &RVWRSWLPL]HG1)3$LQWHUFKDQJHDEOH
Find Yourself with a Real-Time Location System Real-Time Location System
Launched in 2020, omlox is the world’s fi rst interoperable standard for location technology in industrial environments.
By Michael Bowne, executive director, PI North America
Omlox is an open standard for a realtime location system (RTLS) in industry. The focus of omlox is to define open interfaces for an interoperable localization system. The standard enables interoperability and flexibility among different trackable providers within single or multiple tracking zones.
Until now, locating something in an industrial setting required proprietary hardware from a single vendor. That single vendor provided the transponders and infrastructure to provide location details for whatever was being tracked. Operability between providers was virtually nonexistent. Omlox changes all that.
The technology behind omlox consists of two parts: a hardware component and a software component. The hardware interface is known as the ‘omlox core zone’ and is built upon ultra-wide-band (UWB) technology. The UWB radio standard is often used for indoor locating tasks in factories, such as navigating automated guided vehicles, autonomous mobile robots or drones, and locating materials or orders. It is accurate to within inches, is relatively insensitive to interference, and consumes little power.
The software component is known as the ‘omlox hub’ and enables connection to the omlox core zone as well as other locating technologies such as RFID, 5G, Bluetooth, Wi-Fi, SLAM, and GPS. These connections are performed via an application programming interface (API). On the other side of the omlox hub, the API allows for connections to production control systems, goods tracking, or navigation orchestrators, for example.
The origins and first use-case for omlox came from the machine tool industry. Customers noted that the biggest bottleneck in production came not from the throughput of the machines themselves, but locating and getting parts to the tools for machining. Since then, the potential use cases have grown to include robots, access control, analytics, fleet management, augmented reality, intralogistics, supply chain, and even social distancing.
Meanwhile, UWB has found its way into the consumer realm, being integrated into the latest flagship phones of the world’s largest smartphone makers. Such adoption is driving down associated component costs and opening up possibilities for integration into more diverse industrial products.
Interested in getting in on the ground floor of omlox? A first version of the specification has been drafted and work continues towards broad publication later this year. Also, omlox has joined forces with Profibus & Profinet International (PI) to help with standards work and visibility. Learn more at us.profinet.com/ technology/omlox.
Have Questions About IIoT? We’ve Got Answers
Wago regularly receives questions from customers about a variety of technology topics. Those questions have really ramped up with the advance of IIoT (Industrial Internet of Things) and the onset of COVID-19. Here are answers to some of the questions we’ve seen most often.
By Charlie Norz, automation product manager, Wago
Q: How has the pandemic affected the IIoT world overall and specifically Wago?
A: Many manufacturing and process facilities have been evaluating the business advantages of using IIoT-based solutions. For some of these companies, they have accelerated their IIoT projects as more employees are now working remotely. Using cloud-based applications to monitor, control, and optimize plant floor manufacturing can be done from anywhere in the world.
Q: Do you see these effects being permanent? Why or why not?
A: IIoT is a long-term and permanent solution for the future of manufacturing. Companies that started with small test IIoT projects are now enjoying the business benefits from the technology. Most companies we work with plan to expand their IIoT application to multiple applications in the future. We offer great opportunities and solutions for every company. While there is no such thing as an all-in-one solution, smart products, methods, and partners will help advance digitalization in your business in ways that benefit all involved. Digitalization is something that we will see ramp up significantly over the course of the next two to five years.
Q: Why is it important that companies start moving forward towards digitalization now if they already haven’t?
A: It is all about data! In the past, the technical data from the field made it through to the control levels at best. That’s changed now. Thanks to modern information technology, the most important information from production is no longer restricted to the classical automation pyramid, but is now available at any time and place. However, the technical conditions must be right for this.
As the world becomes smaller, it becomes necessary to move to digitalization to increase production productivity while increasing quality and having flexibility to meet the changing demands of the market. IIoT is a key technology to enable manufactures to meet these business needs.
Q: What are some trends you see ahead for IIoT over the next year?
A: Cloud-based IIoT can be used for hundreds of different applications including machine learning, predictive maintenance, data mining, digital twins, OEE calculations, line comparison, dashboards, and many more. There are also many different ways to engineer these applications. For some, using tools from cloud service vendors are the way to go. However, this takes deep knowledge in specific algorithms. The other option is take advantage of pre-built solutions for these applications. In the next several years, companies will begin to utilize these prebuilt tools.
Q: What are some contributions Wago is making to IIoT?
A: At Wago, we provide PFC200 controllers with tools to seamlessly connect to popular IIoT and SCADA systems via MQTT, Sparkplug, and OPC UA. For example, these tools can help connect to Microsoft Azure, Amazon Web Services, IBM Cloud, and the SAP Cloud to name a few. Our new PFC200 features the ability to exchange data with two different clouds in parallel. For example, in applications where manufacturing data goes to one cloud and maintenance info to the other, the information can be aggregated and used for analysis. These capabilities create true added value for your company—whether for increasing the efficiency of in-house production, implementing energy management, or developing additional end-customer services.
In the coming year, we will be adding new IIoT related devices that include edge computers and edge controllers to our product line. These devices operate at the edge of the network for local control and data pre-processing and aggregation before it is sent to the cloud.
Also, a new on-machine IP67 platform—like Wago’s I/O System Field—with industrial fieldbus protocols and OPC UA for direct deviceto-cloud connection will be released. These high performance modules are designed for TimeSensitive Networking and are unshakeable in the harshest environmental conditions. Modern, decentralized production facilities require automation solutions that ensure the highest level of connectivity, which is what our I/O System Field provides.
Q: What do you see for the future of IIoT?
A: IIoT is the future and is here to stay. It will be a big part of industrial automation moving forward and we at Wago offer solutions specifically for this and look forward to helping companies with all of their digitalization needs.
The Best Way to Power Remote Wireless Communications
Why remote wireless sensors that communicate with the Industrial Interent of Things (IIoT) demand long-life, industrial grade lithium batteries.
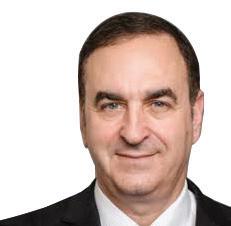
By Sol Jacobs, vice president and general manager, Tadiran Batteries
We are seeing a convergence of IIoTconnected devices, including rapid growth in two-way wireless communications. Common applications include asset tracking, supervisory control and data acquisition, environmental monitoring, artificial intelligence, machine to machine communications, and machine learning, to name a few.
As demand grows for battery-powered solutions in challenging environments and hard-to-access locations, industrial grade lithium batteries are gaining attention. Simple math tells you that the higher initial cost of an industrial grade battery is soon overtaken by the added value of higher reliability and a lower cost of ownership.
Low-power wireless devices
There are two main types of industrial grade low-power devices: 1) Those that draw an average current in microamps, typically requiring the use of an industrial grade primary (non-rechargeable) lithium battery; and 2) Devices that draw average current in milliamps, enough to prematurely exhaust a primary battery, typically requiring the use of an energy harvesting device in combination with an industrial grade rechargeable Lithium-ion (Li-ion) battery to store the harvested energy.
Specifying a battery involves numerous considerations, including: the amount of current consumed during active mode (including the size, duration, and frequency of pulses); energy consumed during stand-by mode (the base current); storage time (as normal selfdischarge during storage diminishes capacity); thermal environments (including storage and in-field operation); and equipment cut-off voltage, which drops as cell capacity is exhausted or during prolonged exposure to extreme temperatures. Criticaly important is the battery’s annual self-discharge rate, which often exceeds the energy consumed to operate the device.
The vast majority of remote wireless devices are powered by primary (nonrechargeable) chemistries, including iron disulfate (LiFeS2), lithium manganese dioxide (LiMNO2), lithium thionyl chloride (LiSOCl2), alkaline, and lithium metal oxide chemistry.
As the lightest non-gaseous metal, with a high intrinsic negative potential that exceeds all others, lithium offers the highest specific energy (energy per unit weight) and energy density (energy per unit volume) of all commercially available chemistries. Lithium cells operate within a normal operating current voltage range of 2.7 to 3.6V. This chemistry is non-aqueous, thus less likely to freeze in extremely cold temperatures.
When extended battery life is required, the preferred choice is lithium thionyl chloride (LiSOCl2) chemistry, which can be constructed in two ways: bobbin-type or spiral wound. Spiral wound cells provide higher energy flow while bobbin-type LiSOCl2 batteries are ideal for low-power applications, delivering high capacity, high energy density, and a wider temperature range (-80° to 125° C). Bobbin-type LiSOCl2 cells also feature exceptionally low self-discharge (less than 1% per year for certain cells), which permits up to 40-year battery life.
Understanding battery self-discharge
Self-discharge is common to all batteries, as chemical reactions rob energy even when the cell is unused or in storage. Self-discharge can be greatly reduced by harnessing the passivation effect.
Passivation is unique to LiSOCl2 batteries, resulting from a thin film of lithium chloride (LiCl) that forms on the surface of the lithium anode, separating the anode from the electrode, thus limiting the chemical reactions that cause self-discharge. When a load is placed on the cell, the passivation layer causes initial high resistance along with a temporary voltage dip until the discharge reaction slowly dissipates the passivation layer. This process keeps repeating every time the load is removed.
Numerous factors can influence cell passivation, including current discharge capacity, the length of storage and storage temperature, discharge temperature, and prior discharge conditions, as partially discharging a cell and then removing the load increases the amount of passivation relative to when the cell was new. While passivation serves to minimize battery self-discharge, too much of it can restrict energy flow.
Self-discharge is also affected by the cell’s current discharge potential, the method of manufacturing, and the quality of the raw
materials. For example, a superior quality bobbin-type LiSOCl2 cell can feature a self-discharge rate as low as 0.7% per year, retaining 70% of its original capacity after 40 years. By contrast, a lower quality bobbintype LiSOCl2 cell can experience a self-discharge rate of up to 3% per year, losing 30% of its initial capacity every 10 years, making 40-year battery life impossible.
Unfortunately, battery self-discharge can take several years to be fully measurable, and theoretical test data is often highly unreliable, so thorough due diligence is required when evaluating potential battery suppliers.
Two-way wireless connectivity demands high pulses
Increasingly, remote wireless devices require high pulses to power two-way wireless communications. To conserve energy, intelligently designed devices incorporate a low power communications protocol (e.g., WirelessHART, ZigBee, or LoRa), along with a low-power chipset, and proprietary energy-saving techniques.
Standard bobbin-type LiSOCl2 cells are not designed to deliver the high pulses required for two-way communications: a challenge overcome with the addition of a patented hybrid layer capacitor (HLC). The bobbin-type LiSOCl2 cell delivers background current during standby mode while the HLC works like a rechargeable battery to generate high pulses up to 15A. The HLC also features an end-of-life voltage plateau that can be interpreted to communicate ‘low battery’ status alerts for scheduled replacement.
Supercapacitors perform a similar function in consumer electronics but are rarely used in industrial applications due to inherent limitations, including: short-duration power; linear discharge qualities that do not permit full discharge of available energy; low capacity; low energy density; and a very high self-discharge rate of up to 60% per year. Supercapacitors linked in series require cell-balancing circuits that are bulky, expensive, and draw additional energy to further shorten their operating life.
Following are examples involving bobbintype LiSOCl2 batteries:
Oceantronics: To simplify the transport of scientific equipment across the Artic, Oceantronics redesigned the battery pack for its GPS/ice buoy by replacing a huge battery pack consisting of 380 alkaline D cells with a more compact, lighter, and cost-efficient solution using 32 bobbin-type LiSOCl2 cells and 4 HLCs. They achieved a 90% reduction in size and weight (54 kg down to 3.2 kg), enabling the GPS/ice buoy to be more easily transported by helicopter. Converting from alkaline to LiSOCl2 chemistry also multiplied the device’s operating life many fold.
Cryoegg: Researchers studying the relationship between climate change, rising sea levels, and deep water channels beneath glaciers in Greenland and Antarctica utilize Cryoegg, a remote wireless sensor that continuously monitors temperature, pressure, and electrical connectivity. Cryoegg eliminates the need for bulky and expensive cables that can be easily damaged by glacial movement. Bobbin-type LiSOCl2 cells were specified due to their high capacity, high energy density, wide temperature range, and high pulse capabilities.
Cryoegg utilizes the same 169 MHz Wireless M-Bus radio waves found in AMR/AMI water and gas utility meter transmitter units (MTUs). Bobbin-type LiSOCL2 batteries lower the cost of ownership of a water or gas MTU by preventing wide-scale battery failures that can disrupt billing systems and disable remote start-up/shut-off capabilities.
Southwire: Reducing size and weight is highly beneficial to utility line crews installing line/ connector sensors that monitor temperature, catenary, and line current on utility power lines to warn if a transmission line goes down. Use of bobbin-type LiSOCl2 cells enable a more compact and lightweight (3.5 lbs.) solution that can handle extreme temperatures (-40° to 50° C), providing months of back-up power if no line current is detected.
When energy harvesting is required
If an application draws milliamps of current, it could quickly exhaust a primary lithium battery. This may require the use of an energy harvesting device in tandem with an industrial grade rechargeable Lithiumion (Li-ion) battery.
One prime example is Cattlewatch, which combines small solar (PV) panels and Li-ion batteries to create mesh networks that track the location, health, and safety of animal herds. Solar/Li-ion hybrids also power smart parking meter fee collection systems that are equipped with AI-enabled sensors to identify open parking spots.
Low-cost, consumer-grade rechargeable Li-ion cells have a relatively short service life (5 years and 500 recharge cycles), a limited temperature range (0-40° C), and are unable to deliver high pulses. By contrast, industrial grade Li-ion batteries can operate up to 20 years and 5,000 full recharge cycles, along with an expanded temperature range (-40° to 85° C) and the capability to deliver high pulses to power two-way wireless communications.
If your battery needs to last as long as the device, then do your due diligence when evaluating potential battery suppliers. Start by requesting well-documented long-term test results, actual in-field performance data under similar environmental conditions, and numerous customer references. Specifying a more rugged battery often reduces your cost of ownership.
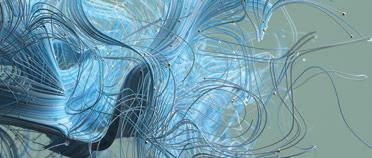
M16 connectors
The perfect solution for applications that need high pin counts
From its early beginnings in the audio industry more than 50 years ago—in fact the M16 connector was the first connector system binder manufactured— today’s M16 connector is very much a “go to” connector solution for a huge variety of indoor applications. Thanks mainly to continuous development and refinement, the M16 connector is now the ideal choice for specifiers looking for a cost effective, robust screw locking connector that can accommodate as many as 24 contacts—with or without EMI shielding.
M16 connectors were originally designed to meet the requirements of Deutsches Institut für Normung (German Institute for Standardisation) that defined the standard for circular connectors for analogue audio signals. These were used widely for many years and commonly known throughout the audio industry and to the consumer as DIN connectors.
High pin count and protection up to IP68
“Although still available in its original unshielded IP40 DIN formats, the latest M16 connectors are far removed from the early audio versions,” says Sascha Döbel, binder’s Product Manager for M16 connector systems. “Driven by market demands for lower contact resistance, higher pin count and improved levels of protection, today’s M16 connectors are capable of accommodating between two and 24 contacts. They are mainly housed in metal bodies, with or without shielding from electromechanical interference (EMI) and providing international protection up to IP67 or IP68 for certain versions,” adds Sascha Döbel.
Versatility of application is assured as a range of alternatives are available for cable mounting with straight or right-angled connectors terminated by soldering, with screws and crimp. Pre-moulded cables are available and the options are as equally comprehensive when it comes to the panel receptacles with front or rear fastening as standard for solder bucket versions and front-fastening for dip solder and pre-terminated flexible PCBs.
This connector style, along with the benefits of rugged design with good environmental resistance, have seen the M16 become widely used in instrumentation, measurement, and sensors for indoor use where there is a need for a higher pin count than is offered by M8 and M12 sensor connectors. Other applications include pneumatic controls, gas and pressure measurement, torque sensors, and motor speed regulators.
Suitable for 5G roll out
The latest applications for M16 connectors include the impending roll-out of 5G networks where binder’s ASIG-compliant connectors are designed to provide high international protection for selected outdoor installations. The AISG (Antenna Interface Standards Group) defines standards for the control and monitoring of antenna line devices in the wireless industry. binder’s Series 423 and 723 M16 connectors, for example, are available in 8-pin DIN variants, of which four to five contacts are used. The products are AISG C485 compliant and available as male and female shielded cable and panel mount connectors. The connectors, which can be used for all wireless networks, meet the requirements for protection class IP68 when connected, offering maximum reliability even under extreme external conditions.
Data transmission up to 10Gbits/s
One of the latest additions to binder’s M16 offering is an X–coded connector capable of handling the data speeds demanded by today’s sensor-based automated production facilities. Data transmission figures are up to an impressive 10Gbits/s.
The combination of a high pin count with the compact size of nominally 18.5mm diameter and 60mm in length means M16 connectors offer an excellent alternative to more expensive connector systems. Special short versions and right-angled versions with a height of only 37mm mean M16 can be used in applications where space is very tight.
M16 connectors accommodate cables ranging from 4.0 to 10mm diameter, are rated to 250V and can withstand an impulse voltage up to 1500V, with current handling of up to 7A (at 40ºC). With increasing requirements from equipment manufacturers for shielding against EMI, more applications now require shielded cable systems with the requirement for connectors with good shielding characteristics. For optimum results 360º shielding is required and this is achieved by integral shielding rings, providing a high attenuation over a large frequency band.
To sum up binder’s M16 product offering, Sascha Döbel comments, “At binder we have found that the flexibility provided by our comprehensive range of M16 connectors with the seemingly endless options at relatively low cost compared to other connector systems, has led to its popularity continually increasing and its application range has extended remarkably from the humble 1960s microphone to the latest communications and security systems that touch us all.”