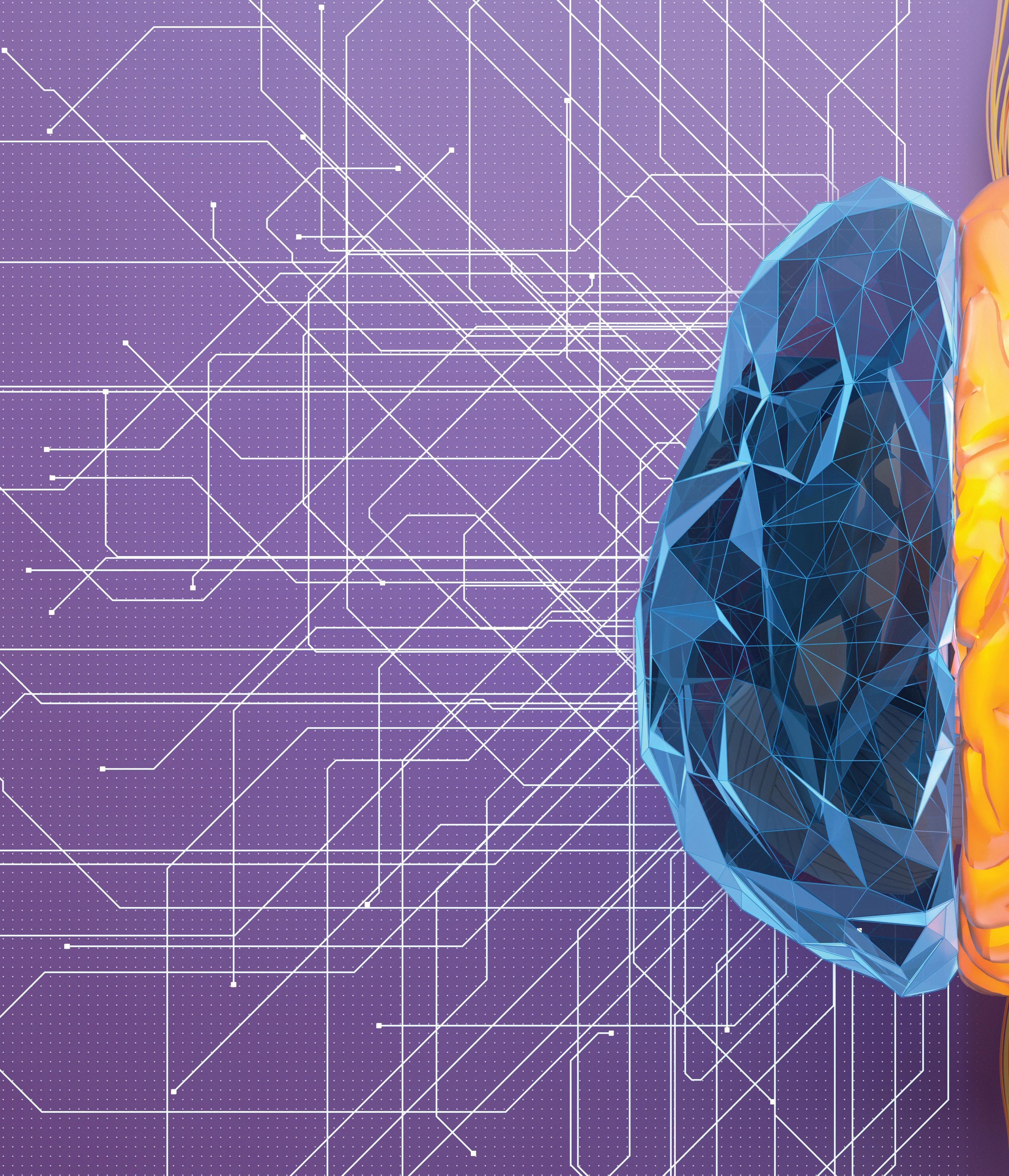
13 minute read
PLCs Gain Esteem as the Brains Behind the Machine
New PLCs Gain Esteem as the Brains Behind the Machine


Next-generation controllers o er multifunctional automation with more intelligence and connectivity, opening the door to new opportunitiees for machine builders and integrators.


Stephanie Neil, Senior Editor at Automation World






Modern industrial machines must be able to adapt to new configurations, new materials, and shorter runs to accommodate an ever-changing product landscape dictated by consumer and end user demands. To accomplish this, machines are increasingly designed to be modular while allowing for integration into production lines.
And, with the Internet of Things (IoT) making its way into machines and onto the plant floor, there are even more aspects to manage and control. Though this can require machine redesigning, it also presents an opportunity for OEMs, integrators, and end users.
“Next-generation machine builders want to differentiate themselves,” said Vibhoosh Gupta, senior portfolio product manager for Emerson’s machine automation solutions business. And the technology available now can provide that critical differentiation, as long as OEMs start to think differently. Specifically, he said to rip a page from the Tesla playbook. “Tesla is teaching us that the relationship between OEM and customer is not a one-time transaction. If a machine is smart, you can make it a multi-touch transaction by providing [new] capabilities and service to the customer.”
The big question is: How have the machine controls—the programmable logic controllers (PLCs)—evolved to accommodate the need for more flexibility, connectivity, and functionality? In fact, machine control technology has progressed tremendously over the years as suppliers add machine learning, artificial intelligence (AI), analytics, cloud connectivity, simpler programmability, and even virtual operating systems.
PLCs and programmable automation controllers (PACs)—which are similar in functionality to PLCs but use different programming interfaces—have long been thought of as specialized computers designed to collect data from inputs and then execute an action. But now that these controllers are being designed with more capabilities, they are increasingly being seen as multifunctional mechanisms that are the real brains of the operation.
Of course, when it comes to brains it’s all about processing power—and maybe a little bit more.
Thanks to Moore’s Law, which simply states that processor speeds for computers will double every two years, industrial suppliers are now using faster, multi-core CPUs in their automation controllers. A multicore processor is a single integrated circuit that contains two or more processing units, each of which can read and execute program instructions, thereby offering parallel computing and better overall performance. And by coupling multi-core technology with virtualization technology, the PLC platform can run multiple operating systems (OS) on the same processor, including the realtime operating system (RTOS) required for deterministic control.
Emerson, for example, recently introduced an edge controller, which is basically a PLC with embedded IoT capability that uses real-time virtualization to add analytics and cloud connectivity at the control level. Within this controller’s quad-core CPU, two cores are dedicated to traditional highspeed deterministic control, and two cores are dedicated to another OS, like Linux, to run different applications in a safe and cooperative manner, making sure that deterministic control is not impacted by anything that happens on the Linux side.
Edge controllers like this will feed the brains of the machine with IoT information that adds to the overall intelligence and scalability. And, referring back to Gupta’s original comment, will enable that Tesla-like multi-touch experience between the OEM and the end user.
Adding an edge controller—along with many smart sensors and instrumentation— will also usher in a new way to make machines. “In the future, instead of replacing machines, you can upgrade them over time with IoT,” said Rich Carpenter, general manager of product management for Emerson’s machine automation solutions business.
Pondering next-gen PLCs
For the most part, machine builders have settled in to their tried-and-true PLCs, rarely attempting to change to a new control system or upgrade the technology because, if it’s not broke, don’t fix it, right? That may have worked in the past, but now is the time for OEMs to adopt more advanced control technology that will not only provide a competitive advantage, but also position them for a digital transformation.
“To achieve the next level of machine performance, the control platform is going to have to be much more capable than the legacy PLC,” said John Kowal, marketing director for B&R Industrial Automation. Manufacturers will not be buying the same machines that they did several years ago, simply because e-commerce and mass customization has changed the way products are designed and made. And that means the way the machine is designed and made must change as well. “It is going to require a change in mindset. You’re going to have to make your machines more adaptive, and


Emerson PACSystems RX3i CPL410 programmable automation controller features a universal programming environment to provide application portability across multiple hardware platforms.

that starts with the capability of the control platform.” (Editor’s note: John Kowal passed away after this interview was conducted. More information about John’s passing can be found at http://awgo.to/NwYUv)
Kowal pointed to the ability to engineer multiple machine applications within a single unified control environment.
In late 2019, B&R announced the integration of ABB robots into its automation portfolio. Blending robotics with machine control into one unified architecture will help execute smaller lot sizes for mass customization. In addition, B&R integrates a vision system into the machine controller so that it works on the same real-time network as the machine in order to respond faster.
Omron Automation Americas’ Sysmac AI Controller is said to help manufacturers reduce the risk of equipment damage and downtime by detecting issues early on, prompting immediate action to reslove them.


By merging robotics and vision with machine control, there is more precise synchronization. “That same PLC has the power to control all aspects of the machine, process our integrated vision data, control our track systems, integrate networked safety including collaborative robotics, run digital twins, you name it,” Kowal said.
Today’s controllers are multi-tasking machines—just like the systems they automate.
Take the Mitsubishi Electric controllers. The MELSEC iQ-R Series is designed specifically for advanced applications around productivity, engineering, maintenance, quality, connectivity, security, and compatibility. The iQ-F, on the other hand, is designed for machine builders. It is a compact PLC that still has some of the characteristics of the more advanced version. It is an all-in-one power supply, CPU, and I/O with built in features for high-speed counters, positioning outputs, Ethernet, and SD card slot, a safety extension module can be connected, as well as various communication modules including a CC-Link IE Field Network intelligent device station module.
“It is designed to be an all-in-one unit with everything you’d need from a controller,” said Lee Cheung, product marketing engineer for Mitsubishi Electric Automation. In addition, the latest generation of the controller enables machine-to-machine communication between iQ-F CPUs without

any programming.
“If you want to connect PLCs or devices, [typically] the programmer would have to write a program just to do the communication and handle data transfers and handshaking to make sure the data passes back and forth,” Cheung said. “But with this functionality built in to the CPU, all the programmer has to do is use a wizard-based drop-down menu to select what data is to be transferred.”
Mitsubishi Electric has also made it easier for the user to see the status of the machine via a built-in web server on the PLC. “And we’ve made it possible to create custom web pages,” Cheung said. “So OEMs can create their own web page that shows all of the information as it relates to the machine.”
The next-generation controller will have even easier usability, more flexible connectivity and communications, and some of the advanced functionality that is affiliated with Mitsubishi Electric’s higher performance PLCs, including even more coordinated motion control. “Packaging machines, for example, rely on high speed and high accuracy, and all of the axes have to be coordinated. And this is one of the key features of iQ-F and one of the reasons that a lot of our packaging customers use this product,” Cheung said.
Beckhoff Automation also has an integrated offering as part of its TwinCAT 3 automation software for PC-based control. The company’s TwinCAT Vision software adds image processing to a universal control platform that incorporates PLC, motion control, robotics, high-end measurement, IoT, and human-machine interface.
“When you have an external vision system it grabs an image, communicates over fieldbus to the controller and, after processing, the controller may issue resulting commands to a robot,” explained Mark Ruberg, packaging industry market manager for Beckhoff USA. “So there is latency in the communication from the camera to the processor. Beckhoff’s TwinCAT Vision has removed all communication latency by embedding the vision algorithms into our real-time kernel. Thus, control loops around vision can be in microseconds as opposed to milliseconds, an order of magnitude faster.”
With its introduction of the ctrlX Automation platform, Bosch Rexroth claims to have done away with traditional boundaries between machine control systems, information technology (IT), and the IoT. It’s a more flexible and scalable platform, providing both centralized and decentralized automation topologies with the help of a Linux RTOS, open standards, app programming capabilities, web-based engineering, and a comprehensive IoT connection. According to Bosch Rexroth, the ctrlX Automation platform combines the latest engineering software tech-
Bosch Rexroth’s ctrlX Automation platform features open software architecture, a wide choice of programming language options, and app-based functionality.
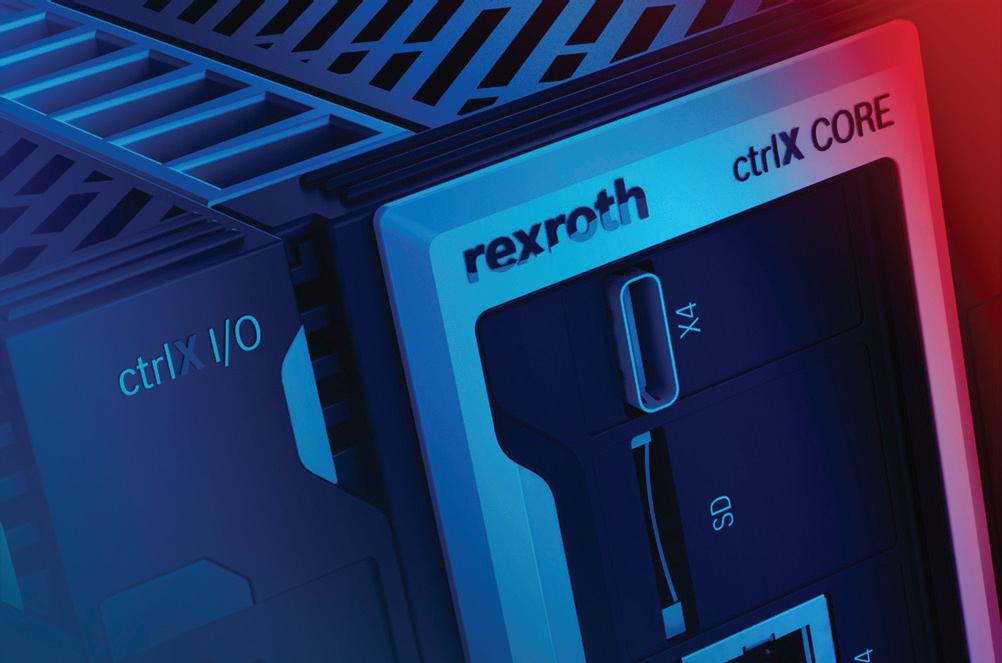
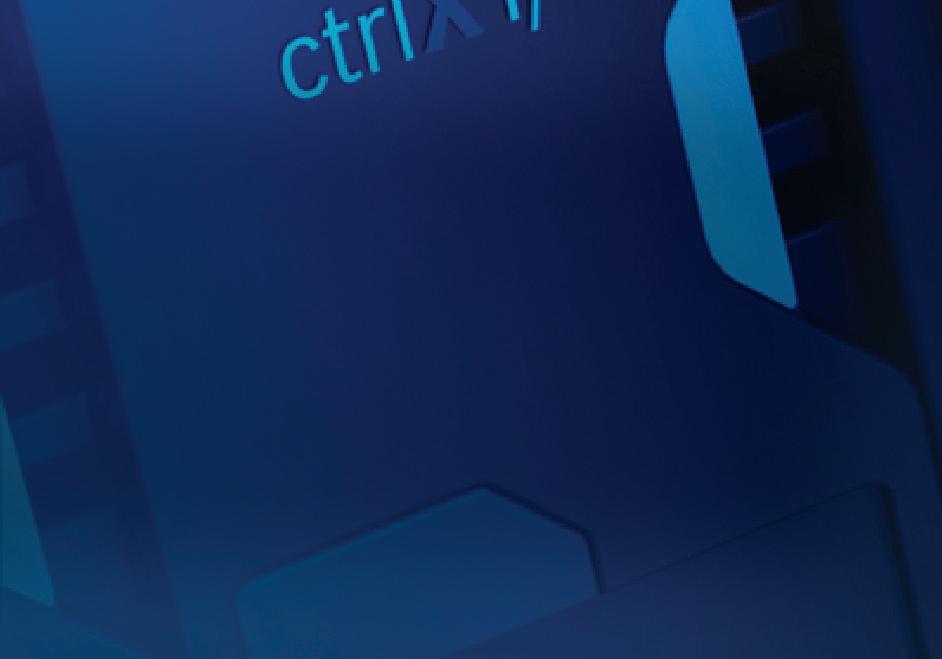
nologies with all PLC and motion tasks. Software functions are combinable in any number of ways with ready-made, customized and customizable apps—which could be created by Bosch Rexroth, its customers, or thirdparty suppliers in a variety of programming languages such as C++ or IEC 61131, script languages such as Python, or new graphical languages such as Blockly.
The network and the need for speed
Speed in the fieldbus network is also important because all of this processing power doesn’t matter if the data gets stuck in traffic. Beckhoff’s EtherCAT, which was developed in 2003 and has an independent technology group with over 5,600 members, is 100% deterministic. In 2018 EtherCAT G was announced, offering Ethernet transmission rates of 1Gbit/second. EtherCAT G10, currently in development, delivers 10 Gbit/ second data rates.
“EtherCAT is still the fastest industrial fieldbus available, but data transmission needs are constantly increasing for vision, analytics, machine learning, and communication to the cloud, driving greater bandwidth requirements,” says Ruberg. “EtherCAT G and G10 are there to fill this developing need, before it becomes a bottleneck.”
Carrie Lee, product manager of controllers at Omron Automation Americas, echoed Ruberg when she said, “EtherCAT has great network performance. It is super fast, and moving into the future it streamlines what we are trying to do.”
What Omron is trying to do is create a data sharing environment that a controls engineer can easily understand without having to become an IT expert. Through its Sysmac Studio and Integrated Development Environment (IDE), Omron provides a single operating environment to setup, program, debug, and maintain an entire machine system. It’s one software suite for configuration, logic, motion, vision, safety, drives, networks, and I/O. Last year, the company announced the Sysmac Artificial Intelligence controller that integrates machine learning into an edge-level industrial controller. It runs in parallel with the standard controller, sharing a backplane to leverage machine learning and AI to monitor what is happening in the machine and to detect something out of the ordinary in order to react to it programmatically. “It means when it detects that something happened, rather than shutting down the line or wasting product, the machine will detect the anomaly and go to an alternate run mode to protect the product and processes,” Omron’s Lee said.
B&R has its own answer to network speed. First, it starts with I/O slices with their own processing power inside. “It’s like the PLC distributed down to the I/O slice with fast response time [because] it’s not going up to the CPU to make a decision, it’s doing it right there,” Kowal said.
B&R, like many other automation suppliers, is also adding OPC Unified Architecture (UA) over Time-Sensitive Networking (TSN) to its
automation portfolio. OPC UA is a platform independent serviceoriented architecture that provides the security and the semantics for multi-vendor machine-to-machine communication. TSN is an IEEE 802.1 defined standard technology that provides deterministic messaging on standard Ethernet. And OPC UA over TSN enables high-performance motion control traffic and bandwidthintensive IT traffic on a single cable without interference between them. (For more information on TSN, see: http://awgo.to/yQhpQ)
For Rockwell Automation, OPC UA over TSN is not adding speed and determinism to its own EtherNet/IP reference architecture, which company officials say is designed to ensure the network is not overloaded. But it could solve a couple of problems inherent to the automation community.
“One is communication from controller to controller when supplied by different vendors,” said Paul Brooks, Rockwell Automation’s manager of technology business development. “As an industry we’ve never agreed on a single mechanism for controllers to talk to each other. The second thing is, as a community none of us have a good solution to communicate from a device to software applications. Communication from the controller to software apps is a well-solved problem, we have no problem getting information out of the Logix controller into a software app and into the cloud. But if you have a Kinetix drive it is a more difficult problem. The OPC community is working to solve the communication from an automation device to software applications…making it easier to get information out of those devices.”
And the bigger opportunity is the ability to seamlessly move machine information to the cloud, which can increase a recurring revenue stream for an OEM. “That means they can take a much greater degree of responsibility for ongoing maintenance support,” Brooks said.
There are other ways to collect that information now, of course. Mitsubishi Electric’s iQ-F controllers, for example, integrate with the company’s IoT gateway, so that the PLC can have connectivity to the Internet and push data to an online portal that allows the OEM to manage all of the machines in the field through a centralized point. “OEMs can see all of the different usage information about each machine as well as OEE stats at each location so they can give recommendations when they see that a machine is underutilized or overutilized. It also allows them to do remote maintenance through a tunneling functionality,” said Cheung.
Not your father’s PLC
And that brings us back to the theme of multi-touch service based on more capability embedded within the PLC. It’s what Emerson calls a “true” edge controller, and it truly changes the definition of what a PLC can do these days.
In fact, with so much power, intelligence, and speed built-in to automation controllers, B&R’s Kowal said the name “programmable logic controller” a bit obsolete these days. “I guess the term PLC today is kind of like my parents calling the refrigerator the ice box,” he said.
