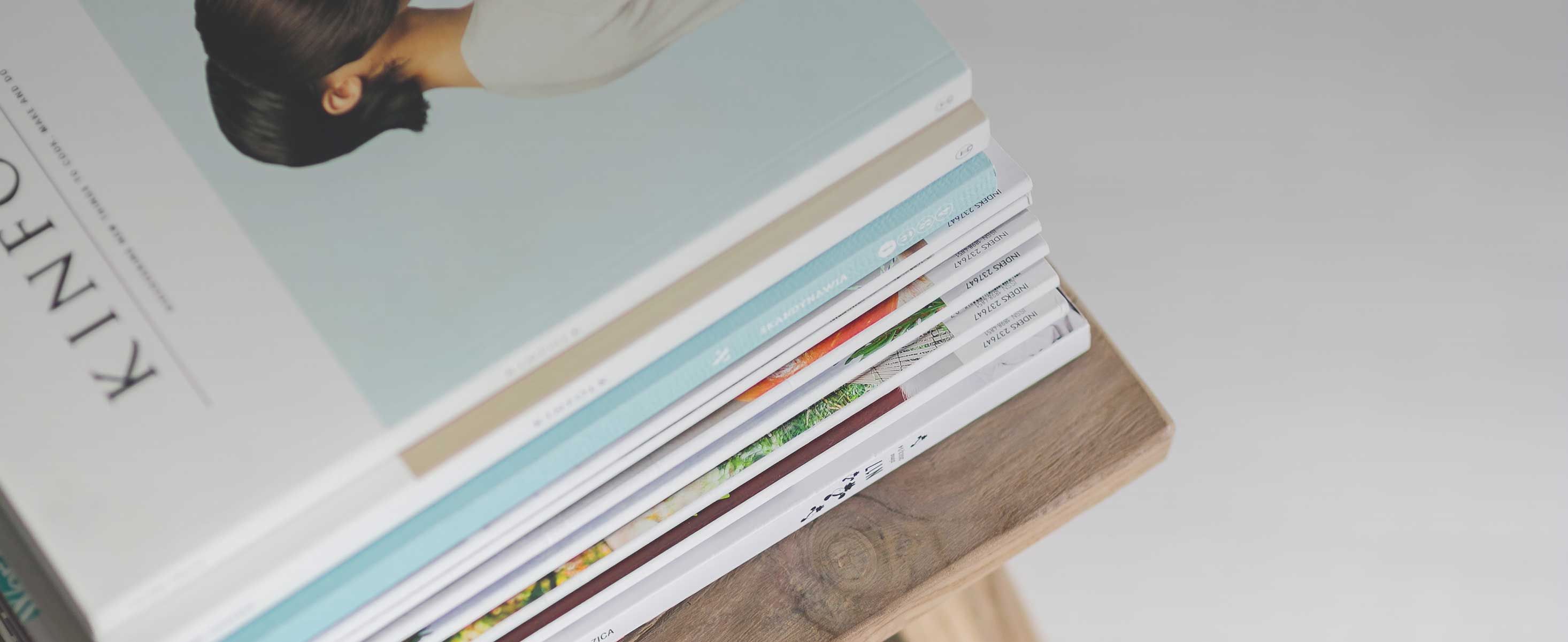
10 minute read
THE LATEST NEWS FOR PMMI MEMBERS
from OEM Summer 2020
ASSOCIATION NEWS
Sean Riley Senior Director, Media & Industry Communications
A champion of growing and developing women and the next generation in the workplace, PMMI board member and CEO of Morrison Container Handling Solutions Nancy Wilson was selected as a 2020 STEP Ahead honoree. Convened by The Manufacturing Institute, the annual STEP Ahead Awards recognizes women in science, technology, engineering and production careers who exemplify leadership within their companies. Wilson’s outstanding work as a manufacturer and leader in her community earned her recognition as a 2020 honoree. “Nancy is known in the industry for her unwavering commitment to growing and developing the roles of women and the next generation in today’s workforce,” says Tracy Stout, vice president, marketing and communications, PMMI. “PMMI is honored to have Nancy extensively involved in our organization and we look forward to celebrating her achievements during the STEP Ahead Awards.” An active PMMI member for more than a decade, Wilson helps drive the strategic plan for the industry as an elected member of the Board of Directors. As Chairperson of the Future Workforce Committee, she led the group in establishing $500,000 in matching funds to help members work locally to build the future manufacturing workforce.
Organizations with Eff ective Leaders Outpace Competitors
The PMMI U Leadership Development Program was designed to assist PMMI member companies develop the future leaders and managers in their organizations. The program features a personalized leadership development plan for each participant, based on a multi-dimensional assessment measuring behavior, motivation, and leadership attributes. Help your future leader(s) stand out from the crowd and nominate them for PMMI’s upcoming Leadership Development program, starting virtually on June 12. To learn more about the Leadership Development Program and how to register, visit: oemgo.to/
leadershipdevelopment
Nominate Rising Young Professionals
Do you have a young professional in your company displaying extraordinary leadership qualities? Recognize this individual's achievements by nominating them for PMMI's On the Rise Awards. Winners will receive complimentary airfare, registration, and hotel stay for PMMI’s Annual Meeting, Oct. 5-7. • Candidates must be 35 years old or younger by July 31, 2020 • Entry-level young professional(s) employed by a PMMI member company for at least one year • Demonstrates leadership qualities and achievements in their role, and shows potential to lead the future of packaging and processing • Individual displays a desire to advance their career in packaging and processing • Only one employee can win per member company • Prior winners are excluded from consideration Submit a nomination at: oemgo.
to/ontheriseawards
PACK EXPO Green for a More Sustainable World
Launching at PACK EXPO International and Healthcare Packaging EXPO 2020 (Nov. 8-11; McCormick Place, Chicago) the PACK EXPO Green Program will highlight the commitment of PACK EXPO and all of its partners, vendors, and exhibitors working together to create a more sustainable world. Exhibitors providing sustainable solutions, either via new materials or technology such as biodegradable packaging or new packaging reduction processes, can highlight these efforts to reduce the carbon footprint with the new PACK EXPO Green Icon. Log into the Exhibitor Dashboard at oemgo.to/packexpo and click the PACK EXPO Green tile to get started or contact the PMMI Show Department at expo@pmmi.org.
Risk Assessment: What Do You Really Want to Know? By Devon Colianni, Industry Services Coordinator at PMMI
PMMI has been coordinating risk assessment workshops for years, both as part of the PACK EXPO Portfolio of Trade Shows and more frequently onsite at individual member locations. The umbrella of risk assessment is so large that people often get lost in a sea of terminology and processes. Risk assessment touches technical, legal, and procedural aspects, plus many national and international industry safety standards. For attendees to get the most out of a training program, Bruce Main from Design Safety Engineering, Inc. and Fred Hayes from PMMI, begin by asking what attendees most want to learn. What topics need addressing so that each attendee, upon completion of the training, believes they are better prepared to handle a risk assessment. By starting to train this way, they steer the agenda for each person and company to have a personalized portion dedicated to their topic of choice. Collected throughout fi ve risk assessment trainings, the following are the most requested discussion topics from PMMI members. The most common topic was understanding the risk assessment process and how to do a risk assessment. This topic often comes from people wanting to learn more and familiarize themselves with the content before getting lost in the weeds. Having a workshop that clearly lays out the steps of risk assessment and engages individuals with in-depth walkthroughs provides attendees with an ideal educational setting for optimal retention. This interest is mentioned in almost every training session because understanding what risk assessment is and how to apply it to your company remains one of the most challenging topics of discussion. Another question frequently noted during the workshops is related to international machinery compared to U.S. safety practices. Applicable to a lot of companies who either buy or sell machinery overseas, there needs to be a level of comprehension on this topic so that participating companies can effectively compete with other businesses internationally. Knowing the requirements and applying them effectively leads to better, safer, and more effi cient machinery. The third reoccurring topic is how to lead a company in deploying risk assessments. Stepping into a catalytic role in your company about changing its culture of safety is not easy. What are the steps needed to create change in the company’s current machinery safety program? Direct guidance and professional counsel are key components to approaching inquiries like this. These workshops best prepare attendees on how to handle these diffi cult processes with their own staff. These are just a few examples of the many different discussion topics requested at risk assessment training. Companies have their personnel attend these training workshops to identify better fact-based answers to pressing questions, in a manner that is much stronger than an online search. Participating in training sessions at your facility provides an open line of communication between industry experts and your company, which is incredibly benefi cial to improving a machinery safety program. Live advice, feedback, and face to face assistance and guidance is what makes a difference in teaching someone about risk assessment and addressing their specifi c concerns. Call PMMI to set up a training session at your facility or register for the next open class training at pmmi.org. Learn about the PMMI U Skills Fund for matching funds that support member training opportunities by visiting: oemgo.to/
skillsfund
New One Voice Ready Assessments Available
Three new One Voice Ready assessments are now available from The OpX Leadership Network. Based on knowledge of the following OpX solutions, these assessments can have a positive impact on operations, with particular relevance during the COVID-19 pandemic. • One Voice for Hygienic Equipment Design for Low-
Moisture Foods • Workforce Engagement • Worker Safety Readiness for the CPG
Industry Visit the One Voice Ready webpage to access the tests at: oemgo.to/opxln. Early adopters receive half-off pricing through PACK EXPO International.
NAM Health Care for Select Members
PMMI is excited to announce an association healthcare plan for its members, extending affordable health care to small and medium-sized manufacturing companies in approved states. The National Association of Manufacturers (NAM ) Health Care plan meets the unique healthcare needs of manufacturers. In states where these plans are available, businesses with two to 99 employees will be able to choose from a variety of health plans. Learn more by visiting: oemgo.
to/nam
Syntegon Unveils Sustainable, Intelligent Machine Design at Virtual Show service programs. The new machine design is also easier to clean, which further improves hygiene. The health of industry Grosse kicked off the virtual show by providing a glimpse into the company’s own health, noting for its 2019 fiscal year it generated annual sales of 1.33 billion euros, which was slightly above the previous annual figure. Stephanie Neil Editor-in-Chief Of course, a lot has happened since the end of 2019, speThe processing and packaging industries—and the world—are experiencing enormous changes as a result of megatrends like the coronavirus pandemic cifically, the pandemic, which has impacted Syntegon’s customer base. “Our customers are experiencing particularly high demand during the corona crisis,” said Grosse. “To support them, Syntegon has expanded its customer service and a sustainability call-to-action that puts pressure on activities. These include increased spare parts deliveries corporations to do their part to protect the environment. and providing customer service via digital solutions. We
In times like these it requires business agility and opera- have been conducting key meetings within the scope of tional flexibility, and Syntegon Technology is becoming an customer projects virtually, including model presentations expert at both. and factory acceptance tests.”
The company has recently gone through its own mega In pharma, variations and dosage forms are becoming transformation when, in January, it announced the global more versatile and specialized drugs are being produced in launch of a new brand. Syntegon Technol- smaller quantities. Pharma is playing a critiogy, formerly Bosch Packaging Technology, a cal role in combating the COVID-19 crisis in division of Bosch Group, was acquired by CVC the form of finding vaccines. Capital Partners at the end of 2019, becom- “Syntegon is aligning itself with these ing an independent company headquartered developments,” said Uwe Harbauer, a memin Waiblingen, Germany. Shortly thereafter, ber of the company’s executive board. “Using in March, Dr. Michael Grosse was appointed our highly flexible systems, which can enter as the new CEO. Grosse was most recently a production without long lead times, our cusmember of the management board of Tetra tomers quickly bring new products to market. Pak. Our modular systems with fast delivery times
Syntegon is an OEM that caters to the and efficient start-up processes also allow food and pharmaceutical industries, provid- companies to adapt dosage forms, product ing a variety of processing and packaging formats, speed, and volumes at short notice.” machines, as well as robotics and advanced In the food segment the company has technologies ranging from track and trace to noticed an increase in product variety in the Industry 4.0 to hygienic design, and more. At Michael Grosse, Syntegon CEO double-digit percentage range, noted Clemthe center of it all is a commitment to sustain- ens Berger, an executive board member. “And ability, which was a major theme at the company’s virtual e-commerce is growing rapidly. As a result, demand for show that ran from May 7-13. The online exhibit served as smaller quantities is increasing within the context of small a platform to showcase the company’s latest innovations— orders. Existing shortage of skilled workers and rising including the unveiling of a new machine design—which labor costs are leading to increasing automation. We expect was scheduled to be on display at interpack 2020. that the market demand for robot solutions to more than
“Syntegon stands for synergy, technology, and a focus double in the coming years.” on the future,” said Grosse. “The new corporate color green underscores the importance of sustainability and health. The future is bright These aspects are also reflected in our new machine de- Grosse said the company draws on experience in sign.” developing and integrating software, and uses connected
An important feature of the new design is a user-friendly components enhanced with artificial intelligence. “Our interaction zone highlighted in white. It creates a clear user machines not only look good, they also embody intelligent interface and generally makes the machine easy to operate. and sustainable technology. Our focus will continue to be The new design includes an optimized HMI, the logo, which on this in the future.” is seamlessly integrated into the surface, the type designation, and a status indicator. In the future, it will integrate To learn more about the products introduced additional components, such as a wireless charging sta- at the Syntegon virtual show go to: tion for tablets that can be used to run augmented reality oemgo.to/syntegon