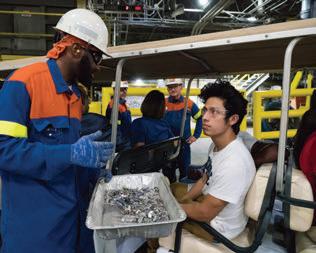
13 minute read
The Workforce Undergoes a Digital Transformation
from OEM Summer 2022
plus million impressions collected on the MFG Day website, and 15 states made written proclamations declaring the event on the first Friday of October, bringing weight and validity to the institute’s goals.
Novelis, the world’s largest aluminum recycler and leading provider of flat-rolled aluminum products, is (and has been) one of the companies participating in MFG Day.
“We have participated in MFG Day for several years by opening our doors to students, teachers, and community leaders and giving them a firsthand glimpse into cuttingedge manufacturing careers and operations,” says Dev Ahuja, executive vice president and CFO at Novelis. “In 2019, we held a kick-off event at our Greensboro, Georgia, recycling facility, where I joined Manufacturing Institute president Carolyn Lee and our Greensboro team in welcoming 50 students to the plant. While visiting, the students learned about career advancement, safety, environmental sustainability, and STEM-related applications.”
While the events help students to learn about careers in manufacturing, as well as the technology being applied at the facilities, the event can be beneficial to participating companies as well. Miller Fabrication Solutions, one of the top metal fabricators in the U.S., is an active participant in MFG Day, and has benefitted from past events.
“MFG Day has undoubtedly helped with our recruitment and marketing efforts, “says Eric D. Miller, president of Miller Fabrication Solutions. “The event gives people a behind-the-scenes look at how we help produce the types of heavy equipment you see on construction jobs, railroads, mining sites, and other industrial applications. It’s a great way to showcase the many rewarding career opportunities at Miller and convince the workforce of tomorrow to consider a career here.”
In the last few years, due to the COVID-19 pandemic, MFG Day events went virtual through virtual factory tours and demonstrations. This year, MFG Day is expected to be a mix of in-person and virtual events held throughout the country.
Ge ing involved
So, you may ask yourself, “How can first-time participants get involved?” You’ll find everything you need to get started at mfgday.com. There you will be able to see relevant information regarding how to participate and ways to host an event. This can include hosting a virtual event, a factory tour, or product demonstration. You’ll then register for the event, which will publish the event and its details on the site, allowing attendees looking to participate in MFG Day to see it.
After that, promote the event as you see fit. The Manufacturing Institute’s Grant says that a good practice is to reach out to local high schools (and sometimes middle schools), and talk to staff, explaining your participation in MFG Day, with the ultimate goal of inspiring the next-generation workforce to consider manufacturing as a career.
“As we all compete for workers in a tight labor market, it’s more important than ever to highlight our industry and connect with prospective employees. I would tell organizations participating for the first time—or the 10th time—to ensure their approach is creative, inspiring, and true to their brands,” says Miller.
While there is no cost to participate in Manufacturing Day, you may incur costs as you work to create a memorable event, such as providing refreshments, catering lunch, and even providing student transportation. The good news is that there is help for you if your company wants to participate in Manufacturing Day and is looking for a little bit of cost assistance. The PMMI U Skills Fund is available to member companies looking to participate. It is a matching program that helps company dollars go further, according to Kate Fiorianti, senior manager of workforce development at PMMI. For example, if a PMMI member company wanted to get a bus to bring students into their facility for the day and it costs $1,000, PMMI would match $500.
Find out how PMMI can assist your MFG Day here: https://www.pmmi.org/skills-fund
Best Practices for a Successful Manufacturing Day
Consider participating in Manufacturing Day to heighten interest in the industry. Here’s how to get started:
• Visit www.mfgday.com and sign up your company. • Create a simple profile with a warm welcome message. • Create a description of what people can expect on your tour, describe your company, what you make, and entice people to visit. • When a endees sign up for your event, you’ll receive their contact information. Reach out to a endees and arrange the visit. • For more participation, contact local schools and organizations. • If you’d like financial assistance, reach out to the
PMMU U Skills Fund. • On the day of the event, give students and other a endees a tour and insights into working at the facility. Let them hear from business leaders. • Consider refreshments or other hospitality e orts to make the day more memorable.
Building the workforce
The goal is clear: To get future generations interested in manufacturing and excited about the industry. It’s also to showcase innovative automation and robotics technology behind modern manufacturing, proving it to be an exciting career path for just about anyone.
“At Novelis, we are excited about the future. We recently introduced ambitious sustainability commitments – including being carbon neutral by 2050 or sooner and reducing our carbon footprint by 30% by 2026 – and announced several capital investments, many of them to increase our recycling capacity that are enhancing the sustainability of our products and preparing us for an exciting period of growth ahead. We know that the future is bright, which is why we love to use opportunities like MFG Day to share our excitement with the communities where we live and work,” says Ahuja.
As more companies open their doors to the next generation workforce, the idea of modern manufacturing won’t be so foreign. And as more people and students gain knowledge and excitement surrounding the industry, the hope is that the skilled labor gap will begin to close, and eventually close for good.
Easily share this article with your peers:
oemgo.to/MfgDay2022
At the Novelis kick-off event at its Greensboro, Georgia, recycling facility, 50 students learn about career advancement, safety, environmental sustainability, and STEM-related applications. Photo courtesy of Novelis
with Digital Speed Controller ELECYLINDERº Can Be Set on the Unit Itself, Just Like an Air Cylinder
Look, Look, you adjust you adjust the Air Cylinder the Air Cylinder speed this way. speed this way. I think it's time for us to I think it's time for us to replace Air Cylinders replace Air Cylinders withElectric cylinders. withElectric cylinders.
If we use Electric, If we use Electric, we need a we need a teaching pendant teaching pendant every time every time we adjust the speed! we adjust the speed!
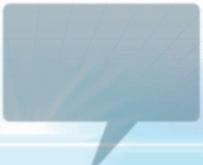
Also, it takes time to learn Also, it takes time to learn Also, it takes time to learn how to use a new one. how to use a new one. how to use a new one.
With Air Cylinder, we can With Air Cylinder, we can adjust the speed with the adjust the speed with the speed controller on the speed controller on the main body right away! main body right away!

is the key to on-site is the key to on-site operation! operation!

We don't have to worry We don't have to worry about that with about that with Digital Speed Controller. Digital Speed Controller.
What? What?
Digital Speed Controller!? Digital Speed Controller!?
You don' t You don't understand. understand. understand.
Programming not required Programming not required
The speed can be set digitally by entering numbers directly as opposed to an analog adjustment by turning a knob.
Speed controller
adjustment
Digital Speed Controller
A: Acceleration V: Speed D: Deceleration F: Forward B: Backward
ELEC YLINDER with D igital Sp eed Controller EC-DS6
e Workforce Undergoes its Own Digital Transformation
Tools that will help manufacturers tap into and transfer knowledge across the organization.
Stephanie Neil, Editor-in-Chief
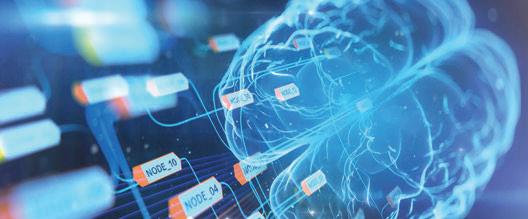
THERE ’ SABITOFATWISTINTHEUSEOFTECHNOLOGY on the plant floor as of late. While the focus to date has been on the digital transformation of equipment and other assets, manufacturers are now turning their attention to automating the flow of information in order to improve processes— with the ultimate goal of helping people.
For example, Pretium Packaging, a designer and manufacturer of packaging products for food and beverage, personal care, and medical and consumer industries, has manufacturing facilities across the U.S., Canada, Mexico, and Europe. Many of these plants were acquired, and therefore, Pretium didn’t have a standardized way to share process improvement best practices.
Similarly, Covestro, a manufacturer of high-tech polymer materials, needed a way to seamlessly implement processes in each plant across the globe, even though each facility may use a different system to track variations. A key factor of the disconnect in getting new processes effectively implemented across all its plants was an inability to transfer updated information during shift changeovers.
Meanwhile, J.M. Smucker Company was looking for a way to improve its operations’ accuracy and efficiency by effectively combining data from multiple production systems.
Though each example differs slightly, they are all trying to solve the same “people problem” as it relates to the workforce. Between the great resignation brought on by the pandemic and a skillset shortage, there is a need to equip people with tools that will drive operational efficiency and improve the employee experience.
“We had a customer that spent millions on equipment and now they are saying it’s time to invest in people,” says Allen Hackman, general manager and global head of the manufacturing industry vertical at ServiceNow, a cloudbased digital workflow platform. “Our customers are striving to improve capacity and productivity and retention. They are dealing with turnover and an aging workforce and they have a lot of manual processes on the shop floor, which means that many procedures are baked into Excel.”
Hackman says he hears three things from ServiceNow customers. First, they want to remove paper processes from the factory floor. Second, they want to build knowledge into those processes, especially as people need to manage multiple jobs. And third, they want to onboard new
people faster by capturing and transferring the knowledge of the retirees. “The key thing is that they’re losing people and they need to retain that knowledge.”
Lauren Dunford, co-founder and CEO of Guidewheel, agrees. “People have so much valuable information and knowledge and there is an important role [emerging] for getting information from their heads into a consistent and dependable system that can transition into a scalable system rather than ad hoc, one-off solving.”
To do that, manufacturers will need a plan, which is why the OpX Leadership Network is working on a roadmap for the Industry 4.0 digital transformation that addresses a range of tools—from wearables to QR codes to Andon displays—that will first and “We had a customer that spent millions on foremost get the right information to the right people at the right time. equipment and now OpX doesn’t recommend specific toolsets, rather, the group is focused on best practices. “That could include they are saying it’s time to invest in checklists to ensure that operators are doing the right things at the right people.”—Allen Hacktime,” says Bryan Griffen, senior director of Industry Services at PMMI, who leads the OpX effort. “These man, ServiceNow’s general manager and checklists could be integrated directly into the control of the process and the global head of the machine.” Griffen said the group is still in the very early stages of developing this manufacturing industry vertical. specific work product, with a second one kicking off this summer that will address hiring, onboarding, and retaining critical staff, including operators, maintenance and quality technicians, and control system engineers. “A big part of this has to be the move to digital tools to aid employees in their jobs in order to help them feel like they are working in a modern facility and not something out of the dark ages,” Griffen explains.
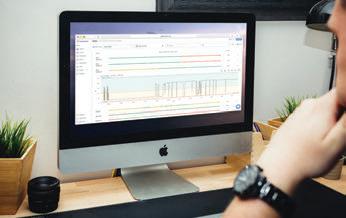
Learn more about the OpX Leadership Network here: h p://oemgo.to/aboutopx
Digital power to the people
For its part, Guidewheel’s FactoryOps platform delivers intuitive, out-of-the box workflows. It starts with a simple sensor that clips around the power cord of any type of equipment on the plant floor—regardless of the control system or the age of the machine—in order to pull information into the cloud in real time. “It’s like a Fitbit for the machine,” Dunford says, explaining that it measures the power draw to easily spot microstops and differences in changeover or process time. As an always-on source of truth, the system is constantly working in the background to alert the right teammates immediately if there is a problem. “It is the heartbeat of the machine that you can then layer critical information on.” That critical information—delivered in real time and in context— could include reasons for downtime, quality issues, actions taken on machine components, labor issues, etc. End users can customized the drop down menu to their own downtime codes. And using the FactoryOps web interface, which has a mobile component, a plant manager could wake up in the morning and pull up the status of a line to see if a machine is down and adjust the production schedule accordingly.
Pretium Packaging is using Guidewheel to replace that “gut feeling” people have used to determine what caused machine downtime with actual data-driven information
Read how ABB is delivering digital work instructions on demand to engineers in the field. h ps://www. oemmagazine.org/technology/ automation/article/21295660/ delivering-digital-work-instructionson-demand
that provides easy-to-understand information and escalates alerts to the proper people based on the problem the machine is having.
“Before Guidewheel we had to physically go to every machine to figure out why it was down and document it,” says Steve Hernandez, a maintenance manager at Pretium. “Now we are able to react in a more timely manner…and our lives at Pretium have changed as we are now able to get alerts on our phones and react whether we are at home or at work.” In addition, the team can use the Guidewheel charts to see operating trends and take ownership of the machines. “Our team is more engaged and are generally concerned as to why [machines] are down,” he says.
Indeed, having the ability to manage incidents is an important part of empowering operators in this digital-first world. ServiceNow recently released its Manufacturing Connected Workforce platform which provides maps and visual guides of a facility’s systems and processes, standard operating procedures to help ensure efficiency and compliance, and the ability to capture institutional knowledge on how to deliver best practices. “This was our entry into the factory floor,” Hackman says, “leveraging data models to give workers context to challenges.” The ServiceNow platform covers four areas. The first is the standard work that happens every day, which is digitized into checklists of things that need to get done. If a worker doesn’t know how to complete the task on the checklist they can click on an instructional video to build knowledge into the procedure. The second piece is exception management, which gives operators the ability to record an incident that drove a specification. Third, if something is wrong, such as an out-ofplace safety guard, a worker could trigger an alert that requests some action be taken. Finally, once tasks and workflows are recorded, users can plot trends that help determine why a failure on a machine happened at the time it did. “The ultimate goal is to improve productivity in the factory; an impediment [to this] has been a lack of knowledge,” says Hackman. “We have a system of action. There are [other systems] that store data, and we sit across the top to be the system of engagement that workers interact with…to drive action. We make sure the task gets to the right person, ensure it gets done, and then learn from it.”
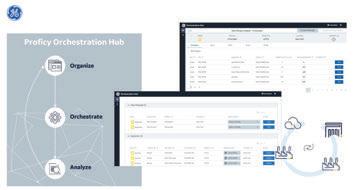
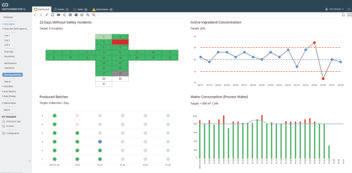
