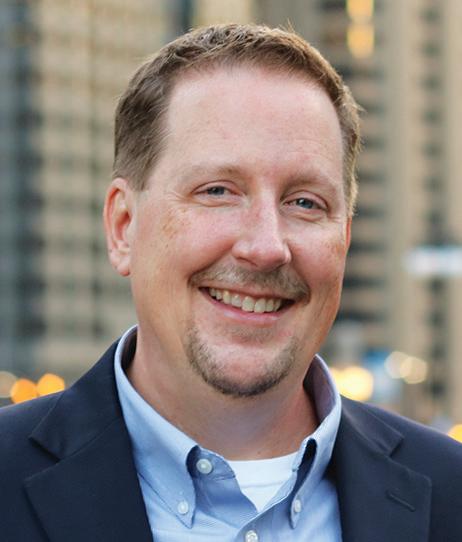
2 minute read
Technology’s Not Worth Much If They Can’t Use It
Lots of innovative technologies were launched at PACK EXPO Las Vegas in September. Perhaps most impressive were the technologies that were easy to use.
As we go to press, we are freshly back from PACK EXPO Las Vegas—although “fresh” is probably not the right word for what we’re feeling after a week at a record-breaking trade show in a city where there’s no shortage of things to do after hours.
The show was abuzz with new product launches for the food and beverage industry—new inspection systems, new sorters, new conveyors, motors, robotic systems… As editors, we not only write up these individual news items (and shoot videos), but we also try to keep an eye out for trends among all those one-off releases.
If there’s one trend that really caught my attention at this year’s event, it was the latest efforts to make the new technologies not only advanced in capabilities, but easier to access and to use.
The fact that manufacturing faces a major labor shortage— one that is not likely to end any time soon, if ever—is not lost on anybody. Check out this issue’s cover story (“Labor’s Long Reach Creates Challenges Beyond Processing,” page 24) for our annual global food and beverage industry report, where Senior Editor Michael Costa details the many ways that the ongoing labor crunch is affecting the industry.
The machine builders are keenly aware of this trend and know that the user interfaces of old might not work so well going forward. It does no good releasing the latest and greatest technology if an employee is heading out the door by the time they’ve finally learned how to use it. Suppliers are realizing, instead, if the machine cannot be learned easily, in a short amount of time, then it’s impossible to deliver on the automation promise. Simplifying the machine is often an incredibly complex undertaking. But OEMs know that they’d better do it or risk becoming obsolete.
Looking for our coverage from the show? Check out www.profoodworld.com/PACKEXPO.
EDITORIAL ADVISORY BOARD
CHRISTINE BENSE
CHIEF SUPPLY CHAIN OFFICER
Turkey Hill
GREG FLICKINGER
CHIEF OPERATING OFFICER
Nobell Foods
JOHN HILKER
SENIOR VP, OPERATIONS
Kite Hill
VINCE NASTI
VP, OPERATIONS
Nation Pizza & Foods
JIM PRUNESTI
VP, ENGINEERING
Conagra Brands
LISA RATHBURN
VP, ENGINEERING
T. Marzetti
MARK SHAYE
VP, ENGINEERING
Ken’s Foods
TONY VANDENOEVER
CONSULTANT, FOOD MANUFACTURING ENGINEERING
Waterfall Ventures
DIANE WOLF
FORMER VP, ENGINEERING AND OPERATIONS
Kraft Foods
BROOKE WYNN
SENIOR DIRECTOR, SUSTAINABILITY
Smithfield Foods ahand@pmmimediagroup.com
RIBBON/PADDLE/PLOW BLENDERS HANDLE POWDERS TO PASTES
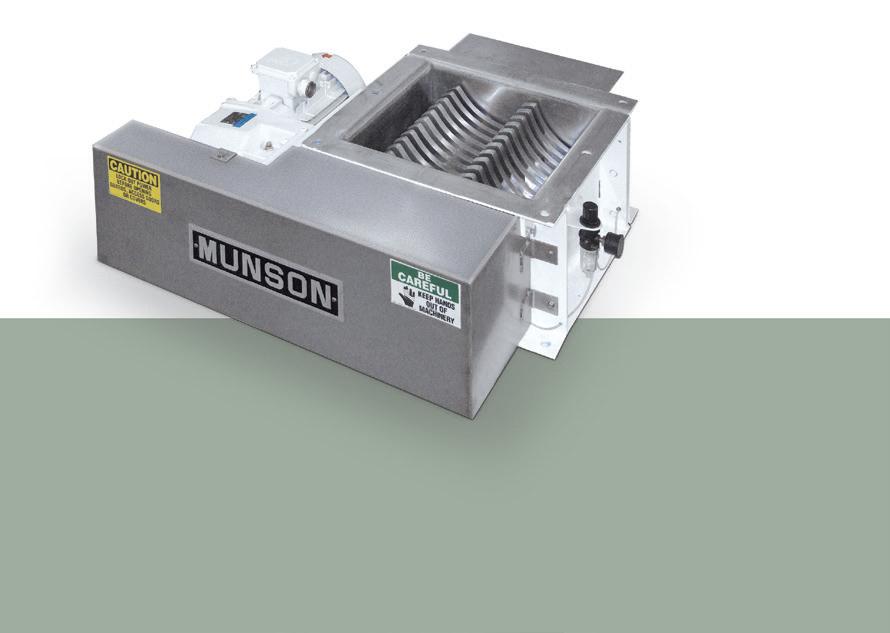
Agitators forced through stationary materials impart shear needed to reduce agglomerates and blend pastes and slurries. Basic industrial units to state-of-the-art sanitary designs with heating/cooling jackets, liquid spray additions, and high-speed choppers/intensifiers. Capacities from 1 to 1,150 cu ft (.03 to 32 m3).
VEE-CONE BLENDERS SANITIZE ULTRA-FAST, THOROUGHLY
Smooth internal surfaces free of baffles, shafts and bearings allow unobstructed material flow, plus complete discharge through a gate valve for rapid cleaning or sanitizing of the easy-access interior. Uniform blends are typically achieved in as little as 15 minutes with equal efficiency at fill volumes from 100% to 25% of capacity. Ideal for dry and granular materials.