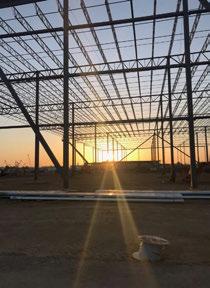
8 minute read
OpX Intel
funding to o set these escalating costs.”
Weber says: “Our projects are typically designed without a lot of bells and whistles to keep costs down already, so there are not a lot of items owners are interested in cutting for the overall quality of construction to o set rising prices.”
Design/builders and owners need to have open conversations about pricing expectations. “This situation is really out of the builder’s control,” says Weber. But it helps when we can show owners documentation from vendors showing price increases and shipping delays.”
But he points out that there is a breakeven point when considering schedule impact versus increased cost. “We have had a few customers willing to pay the additional structural steel costs to get construction started two to three months earlier and save on the overall project duration. But there is a point of diminishing returns with this, depending particularly on the size and scope of the project.” If you are even considering a project in the near future, Weber recommends completing these tasks as early as possible:
•Begin construction documents while estimated costs are being obtained. •Get geotechnical exploration work completed early, even if the project won’t start until the following year. •Plan contingencies into capital expenditure requests for escalating costs. •Award subcontracts early to get submittal, and shop drawing review completed right away to prevent vendor procurement holdups on long lead items.
“Most importantly, be patient with the contractor and understand that this is a global issue and there are very few things that can be done to o set the e ects of this unprecedented situation,” he says.
FEATURED PROJECT
ESI NAVIGATES RISING COSTS FOR PFG EXPANSION
Performance Food Group (PFG) selected ESI to design and construct a 152,623-foot expansion to its Reinhart facility in Mount Pleasant, PA. This includes freezer space, cooler space, refrigerated dock, dry warehouse, a truck maintenance facility, and related site improvements. The expansion will also include a 50-foot high Multi-Shuttle Automated Storage & Retrieval System (AS/RS), and a two-story o ce expansion will boast flexible configurations.
PFG, the parent company to Performance Foodservice, Vistar, and PFG Customized, delivers more than 150,000 food and related products to customers across the United States. This project is expected to take 14 months to complete, and while ESI is optimistic this schedule is attainable, Jason Weber, project manager, ESI Group USA, says material availability could have an impact.
Also impacting the project is the cost of those materials. In some cases, vendors, and suppliers to ESI’s subcontractors are not willing to uphold the pricing provided in their proposals. “This is because these folks have been hit with price increases as well,” he says. “This situation is really unheard of, but we are trying to navigate this situation with subcontractors and the owner.”
Some suggestions Weber and his team have made to o set cost and availability issues are using di erent wall panels, di erent types and thickness of roof insulation, concrete floor thickness options, and the level of o ce finishes.
“ESI has a long-standing partnership with PFG and will work on their behalf
ESI GROUP USA
to ensure a quality facility is constructed for the best value that will perform for their needs today and in the future,” says Weber.
s
• Availability: By reducing both planned and unplanned downtime, there is a commensurate increase in the uptime opportunity. • Output Improvement: The equipment e ciencies to achieve the uptime opportunity can also positively impact reliable output performance, e.g., more units/cycle produced at required quality. • Cost management: E ectively managing the cost of maintenance labor through better utilization of existing sta , combined with better inventory control of the maintenance, repair, and operations (MRO) costs and supply.
The Asset Reliability Opportunity Calculator is an excellent tool to assess the “size of the prize” quickly and e ectively by achieving improvements to uptime performance. This tool uses your company’s actual performance data on unplanned downtime, units produced, cost of goods sold, and your desired improvement goal for the next year. The result is the value of added uptime for that line.
It is important to gain leadership support and
buy-in by proving what can be achieved. Be sure to identify and engage with the critical stakeholders from project inception and throughout. To validate the concept, it is important to be thorough in defi ning the scope of the project, objectives, and expectIMAGE COURTESY OF PMMI’S ed outcomes. At the conclusion, OPX LEADERSHIP NETWORK document the results and include lessons learned. Financial validation is confi rmed by tying back to the Asset Reliability Opportunity Calculator preliminary fi ndings. Untapping the hidden potential from your asset base could have a profound impact on your company, associates, and customers. The upside is impressive in the near term by controlling unit costs (and even reducing them), improving your operational e ectiveness as a dependable supply chain partner, and fi nding that hidden plant within your operations that can defer major capital expenditures.
Download your free copy of the “Asset Reliability Roadmap for the Consumer Products Industry” at www.opxleadershipnetwork.org/maintenance/ download/asset-reliability-roadmap.
CASE IN POINT
Uncovering the Opportunity
The FSO survey provides an industry overview, directional in nature. Consider your organization within the context of these functions: general maturity level (the leadership, cultural, and procedural commitment within the organization) and reactive maintenance sta (nearly 70% of companies are still reactive). Some areas to consider for maintenance improvement are having operators engaged with more basic maintenance functions to free up the sta to tackle more di cult problems, and more targeted utilization of the computerized maintenance management system (CMMS) for better-informed prioritizations.
Production readiness and capability is the consistency of performance in the organization to meet customer requirements. Uptime improvement is new capacity without the expense. Performance can be improved substantially, according to 93% of survey respondents. What would 10% uptime improvement look like for your plant? The Asset Reliability Opportunity Calculator might uncover the opportunities in changeovers, fi rst hour full power, or even in your legacy maintenance practices.
Equipment readiness and capability includes the fl exibility and reliability of the existing asset base to meet the current and future demands of your organization. It enables technologies to better inform the fl oor. For example, greater than 56% of companies state their companies’ lines are not capable of notifying those who can provide needed attention to fi x a
PHILIP WEYER RICHARD LARSEN JEFF SMELTZER
problem. Consider evaluating your equipment technology and capability to meet future business needs, including modifications that will reduce changeover time more e ectively and enable use of predictive analytics.
FSO Institute interviewed three industry executives to get their feedback on asset reliability: Philip Weyer, director of manufacturing operations at Shipley Do-Nuts; Richard Larsen, former vice president at Honeyville and FSO Institute coach; and Je Smeltzer, reliability engineer at Land O’Lakes.
FSO INSTITUTE: What challenges are you facing in launching or expanding asset reliability into a highly valued operational methodology in your company?
WEYER: The primary challenge we face currently is bridging from a culture of reactive maintenance to a predictive model that will allow for increased uptime. Proper training, equipment monitoring, and improved technology are all tools we are employing to improve our operator knowledge level and understanding of the equipment. This will allow us to properly identify issues ahead of time, prevent forced deterioration, and ensure equipment runs at optimal performance. By doing this, we expect to improve uptime and increase throughput to help support demand growth.
FSO INSTITUTE: Where do you see the signi cant opportunities to enhance a company’s production readiness and capabilities?
LARSEN: As a co-author of the OpX Asset Reliability Roadmap, I have come to recognize that asset reliability is an ongoing process that requires an e ective production readiness program to achieve the desired result in throughput and expected profitability.
In order to have an e ective production readiness program, there are a number of important key factors that need to be addressed: • Historical data: To move forward, you need to know where you have been and where you are today. • Production objectives: Understanding where you want to (or can) be. This begins with a realistic assessment of the production line capabilities (design and in-plant reality) to identify throughput goals. • Asset Reliability Calculator: With past, current, and expected data, you are ready to apply the
OpX Asset Reliability Calculator to be able to see
“the size of the prize,” which is what additional production yield and production cost savings can be achieved by minimizing unplanned downtime. • Production readiness: Sustaining your achievements requires an ongoing commitment to training of the maintenance and operations teams and the discipline of a preventive maintenance program.
FSO INSTITUTE: Where do you see the signi cant opportunities to enhance your company’s equipment asset base to meet your future business requirements?
SMELTZER: Throughout our many and diverse manufacturing plants, there are three key focus areas that we can consistently employ to enhance our existing asset base to meet future business requirements: 1. Strategy: Right care strategies for all our critical equipment assets are in place and being implemented. Embedded in these strategies is the focus on uptime inspection preventive maintenance. 2. People: Standard work methods engage the operators to participate and take ownership in certain daily functions that can help them recognize their importance to the team’s success and improve uptime performance. 3. Technology: Real-time feedback from the equipment enables the team to constantly monitor equipment health. Consider the value of monitoring components over time using predictive tools and software to better inform the floor of equipment not running at optimal rate and a potential component failure.
ABOUT THE OPX INTEL SERIES OF ARTICLES
PMMI’s OpX Leadership Network has produced more than 20 manufacturing process-improvement documents for CPGs and OEMs. The FSO Institute has facilitated the adoption and implementation of these documents, especially for food and beverage manufacturers. This series of articles shows how CPGs are using OpX and FSO documents to improve their overall manufacturing health and collaboration with OEMs and other suppliers. Learn more at www.opxleadershipnetwork.org and