
20 minute read
COVER STORY
Colgate Toothpaste in PET Ushers in a ‘Frictionless Future’
A recyclable, clear PET toothpaste bottle is enabled through the use of a slippery coating on the inside of the container that allows the viscous product to be dispensed easily and completely.
Reduced product waste Recyclable toothpaste packaging
By Anne Marie Mohan, Senior Editor
Colgate-Palmolive is inviting European consumers to make toothbrushing part of their beauty ritual, with its new Elixir line of three toothpaste formulas in a striking PET package that breaks from category norms in every way. Says Colgate-Palmolive Co. Worldwide Director of Oral Care Packaging Liz Mellone, “Colgate Elixir is toothpaste reimagined—breathtaking design with beautyinspired ingredients in a unique packaging technology that is recyclable and designed to let people enjoy the toothpaste to the last drop.”
According to Mellone, the three innovative toothpaste formulas—White Restore, Cool Detox, and Gum Booster—were co-developed in tandem with the package, a clear, inverted, 80-mL (2.7-oz) PET bottle with a clear overcap. The sleek and stylish container is a significant departure from, and a more eco-friendly alternative to, traditional toothpaste tubes, which are made from a multilayer construction of plastic and aluminum that renders them non-recyclable.
What makes the use of PET possible in the Elixir application is a breakthrough coating technology from LiquiGlide that eliminates the friction between the inside of the package and the product, allowing the toothpaste to flow freely from the container, evacuating the toothpaste completely. Explains LiquiGlide CEO Dave Smith, “The reason toothpaste isn’t in PET packages, other than Elixir, is because it sticks and won’t come out easily. The LiquiGlide coating enables PET squeeze bottles to work for standard toothpaste.”
An MIT innovation
The frictionless coating technology was co-invented by Smith and Professor Kripa Varanasi at the Varanasi Lab at MIT. In 2012, the two co-founded LiquiGlide with what they say was “a vision to eliminate the no-slip boundary condition to minimize material, water, and energy waste and enable new and better products, processes, and technologies across industries.”
Explains Smith, “We’re not inventing new materials, we’re combining them in a way to create this stable, slippery effect, and the right choice of materials depends on the product properties. The platform is flexible enough that we’re able to make coatings from safe, common materials that won’t alter or compromise the product.” For example, for food applications, LiquiGlide develops coatings from FDA-approved food ingredients; for skincare products, like lotions and creams, coatings are formulated from common, dermatologically safe skincare product ingredients. The thickness of the coating varies depending on the needs of the application and can range anywhere from a micron to tens of microns.
In 2012, LiquiGlide released a video of ketchup being dispensed from a bottle coated with its super-slippery lubricant. Despite an overwhelmingly positive reaction to the technology, it has taken a while for it to become commercialized. “Breakthrough innovation can be challenging for CPG and health and beauty, which are traditionally conservative and slower-moving industries,” says Smith. “However, brands like Colgate and others recognize the importance of creating value, differentiating from the competition, and taking serious steps to achieve their sustainability goals. These are the types of brands that are ready for a frictionless future.”
PET plus LiquiGlide a natural choice
According to Mellone, LiquiGlide came to the attention of Colgate-Palmolive when its Strategic Innovation Group was searching for next-generation technology and dispensing. “Together with the MIT Industrial Liaison Program, we conducted a summit, which ultimately led to the connection with LiquiGlide and this partnership,” she shares.

“Previously PET was not suited for viscous products such as toothpaste. The PET bottle married with the LiquiGlide technology is unique and enabled us to use PET with more viscous toothpastes. The clarity and recyclability of PET as well as its great barrier properties for toothpaste made it the natural choice.” The bottle design, led by Colgate-Palmolive’s Global Packaging & Design Team, was developed from a human-centric perspective, Mellone explains. “Functionally, it’s quite important for the bottle to intuitively work as a toothpaste package in terms of form, squeezability, and nozzle design,” she says. “Aesthetically, clarity was critical to both showcase how the product dispenses and to highlight the toothpaste aesthetics. Moving into a rigid format enabled us to achieve a ‘counter-worthy’ appearance throughout the entire usage cycle of the product.” The cap was designed with an opening that allows the viscous product to dispense onto a toothbrush while also allowing air into the bottle for a smooth outflow of the toothpaste. The cap is made from a thickwalled PETE, which ensures the entire package is recyclable.
While Colgate-Palmolive does produce its own packaging in many instances, for the Elixir project, the company partnered with an unnamed external supplier for the bottle and cap. The bottle is produced through a single-state ISBM (injection/stretch blow-molding) process and is assembled with an injection-molded polypropylene shoulder shroud.
The coating, which is added to the inside of the bottle before filling, is applied by Colgate-Palmolive using new equipment from Sprimag. According to Smith, the coating formula developed by LiquiGlide and licensed by Colgate-Palmolive comprises a natural, plant-based oil and common toothpaste ingredients.
Adding to the container’s premium appearance, it uses a combination pressure-sensitive label printed in four colors, with dual matte and gloss varnishes as well as two cold-foil applications, with a reverse-printed back label.
The Colgate-Elixir line was launched in April 2021 in several European countries, including the U.K. and Germany, and will be rolled out in other European countries throughout the year in various retail environments, with a focus on e-commerce.
Says Mellone, “We are quite excited about this technology and what it enables from a user experience standpoint, and we are looking at other ways to apply it.” PW
Watch a video of LiquiGlide technology, from its debut at PACK EXPO Las Vegas 2015: pwgo.to/7061
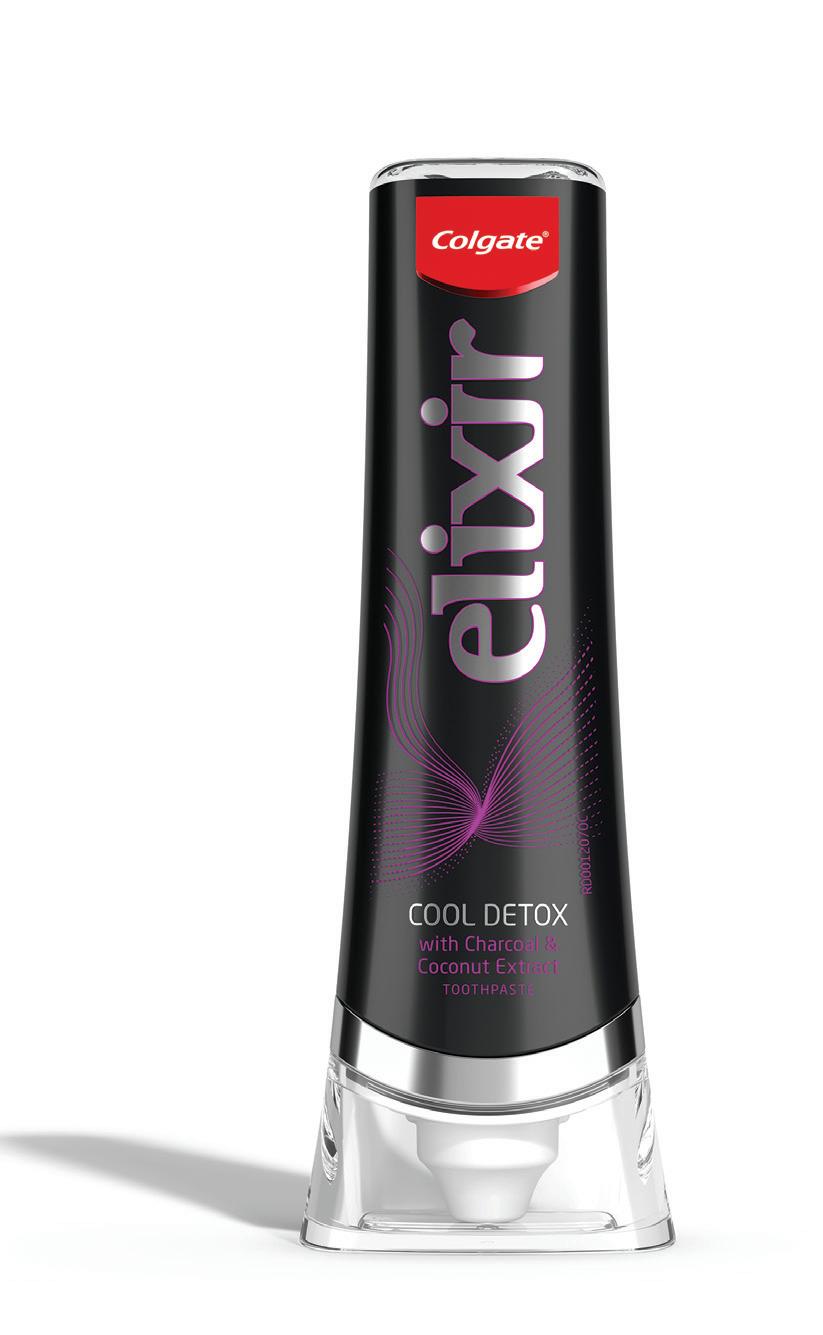
Fabco-Made NFPA
Versatile, rugged cylinders—when you need them
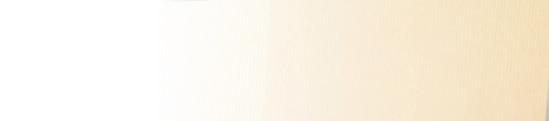
FABCO-AIR
A member of Festo Group
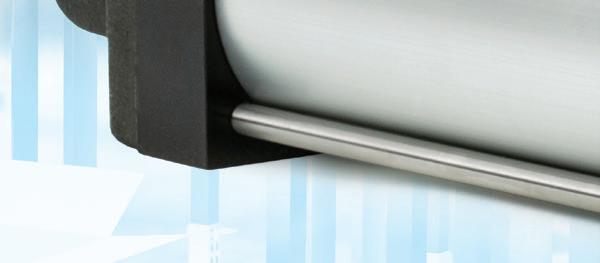
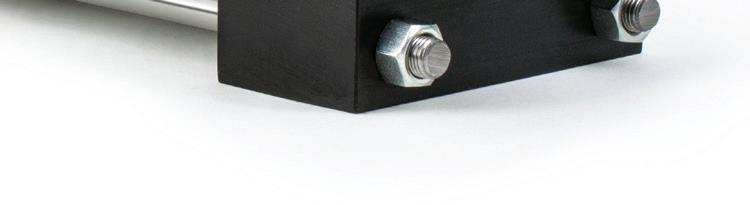
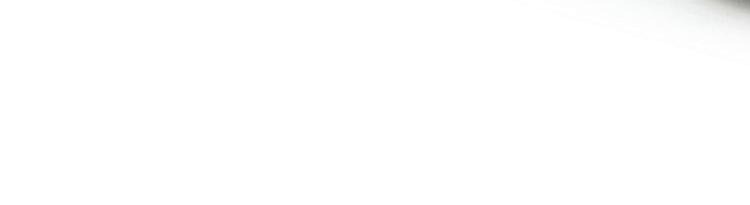

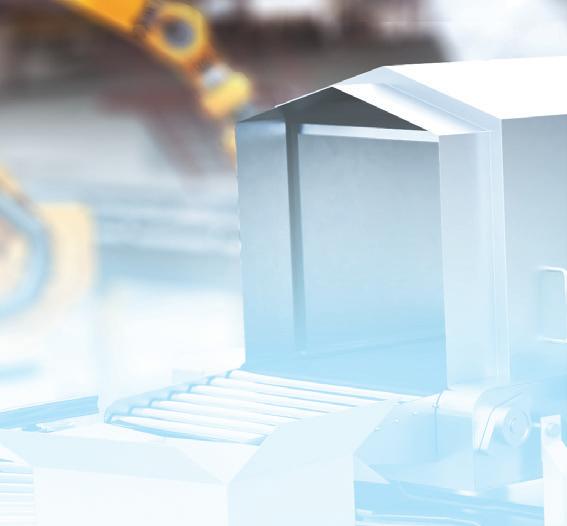

Our NFPA interchangeable pneumatic cylinders take the guesswork out of cylinder selection.
We design and manufacture our NFPA cylinders in Gainesville, Florida—so expect fast delivery, supply chain resilience and local support no matter your application. Built tough, our NFPA actuators feature anodized aluminum heads and barrels and stainless steel hardware for corrosion resistance. They also incorporate high-strength composite rod bears and PTFE piston wear bands for superior load handling and long service life. Choose from 19 standard mounting options and hundreds of standard confi gurable options to meet the requirements of almost any application. Standard catalog not enough? Tell us about your application and let us design a custom solution optimized for your environment. • Standard bore sizes: 1.5–6 inches • Standard strokes to 99 inches • Pressure rating: 250 PSI
MADE IN GAINESVILLE FLORIDA

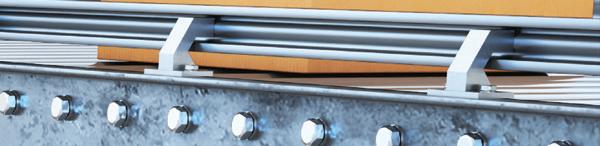
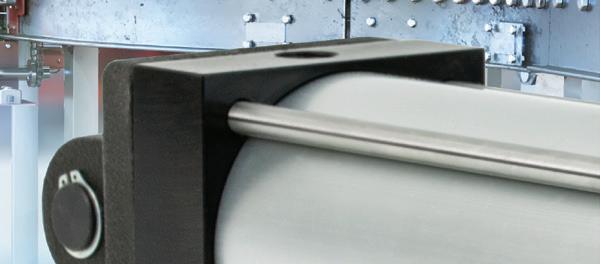
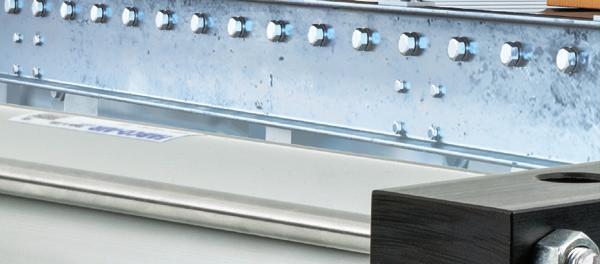
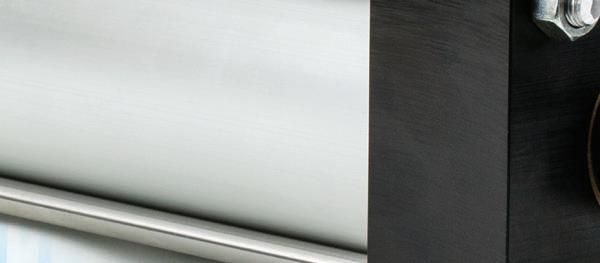

Digital Printing Upgrade and a Second Digital Laser Cutter
This Wisconsin producer of both in-mold and pressure-sensitive labels upped its game in 2020 with systems that have enabled the firm to get into the flexible films market.
Short-run, quick-turn production Advanced laminating methods
By Pat Reynolds, VP Editor Emeritus
B
A
The stainless steel belt of the LasX digital laser system (A) delivers cut parts to the Dorner vacuum conveyor belt (B), which in turn deposits them on the Dorner discharge conveyor belt (C). Immediately upstream is the LasX system (right).
C
Founded as a digital-press-only producer of pressure-sensitive as well as in-mold labels, InkWorks Printing opened its doors 12 years ago with the installation of a narrow-web HP Indigo 4500 digital press. Later the rm graduated to an HP 6900 digital press, which has a 13-in. web width, and later still a second 6900 was added.
As capacity requirements continued to grow, some thought was given to a third 6900. But instead the Plymouth, Wis., converter opted to go wide web with an HP Indigo 25K digital press, which offers a 30-in. web width. Based on the well-established HP Indigo 20000 system for digital printing of roll-fed exibles, the new 25K is designed to deliver a 25% increase in short-run productivity and less waste through improvements in color automation, sustainability, and work ow automation. The new press has been running at InkWorks since December of 2020.
To complement the new press, InkWorks also installed a Combi Pack Ready Laminator from Karlville, which offers both thermal and solventless lamination. “We had been running solventless lamination on a narrow-web machine,” says President Bob Travis. “But it was not very sophisticated, and in fact it was kind of a home-grown solution. Plus it was for 13-in. wide web, and with the 30-in. 25 K we needed a 30-in. wide laminator. (See sidebar on page 64 for more on the Karlville laminator.) “Among other things,” Travis continues, “these new capabilities allowed us to get into the exible packaging market. Not to mention letting us of oad some of the larger labels that previously we could only run one across on the 6900s. Now we can run those in multiples across the web. So it really came down to a decision to eliminate some of the bottlenecks we had in our operations.” Travis says that when laminating thin lms, a thermal process involving heat can too easily make the material curl. “The thermal laminating we do tends to be for pouch materials,” he points out. “In-mold labels are done via solventless technology, usually at speeds in the range of 600 feet per minute. Thermal lamination is more like 150 ft/min.”
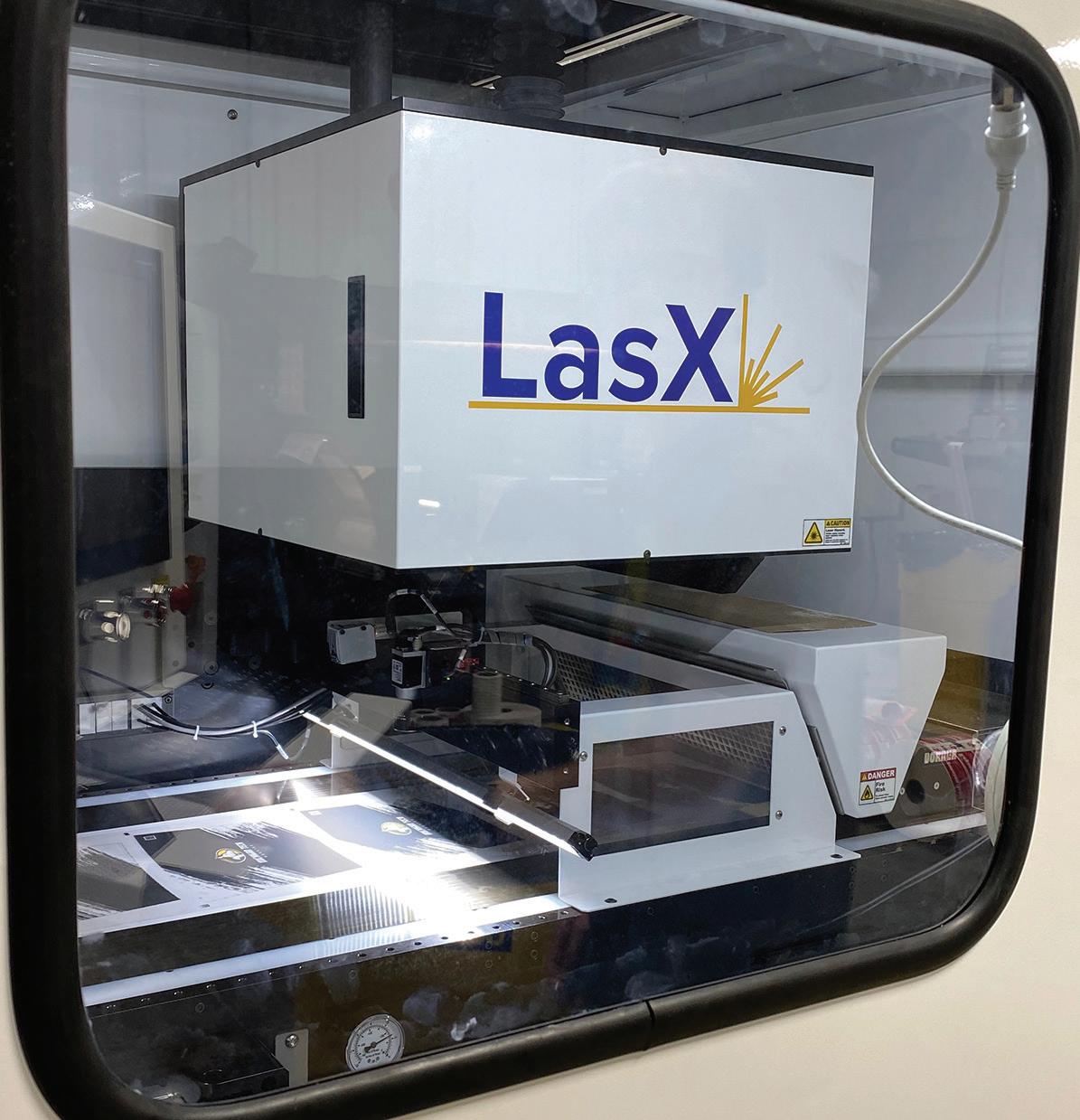
Digital finishing, too
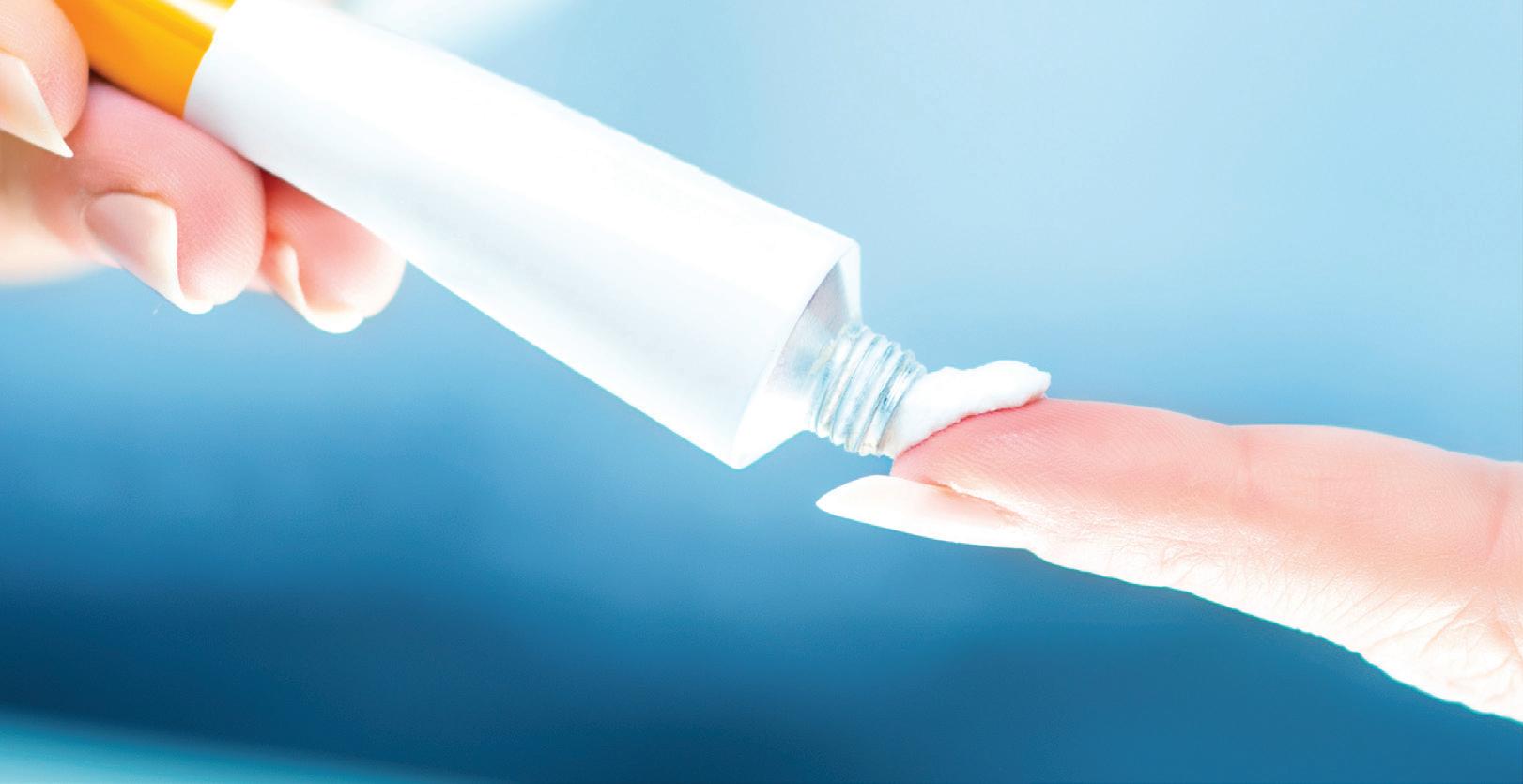
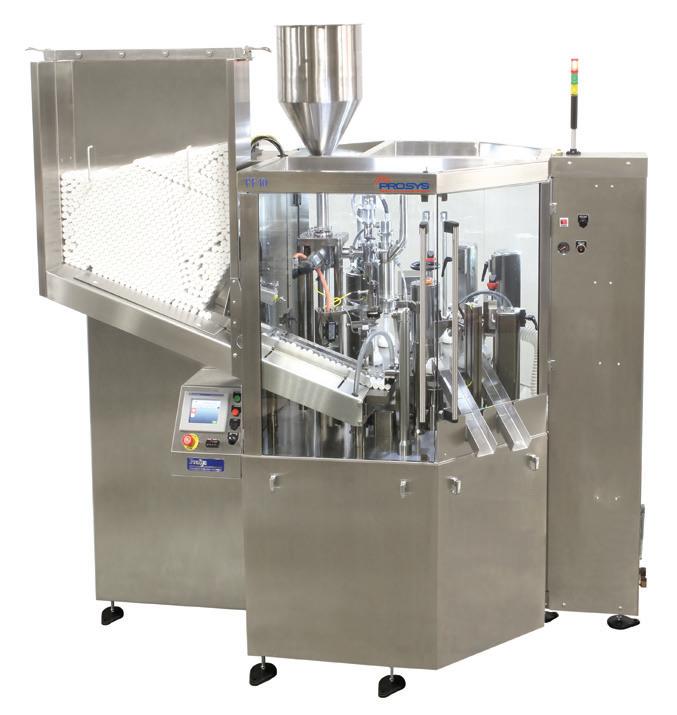
Bold as it was, the leap to a new press and laminating system was just the beginning. It coincided with the installation of a second LasX digital laser cutting system. Travis says his experience with InkWorks’ first LasX machine was an eye-opener. “Once we no longer had to rely on conventional die-cutting tooling and could set up jobs digitally, we had the ability to cut any size or shape and go from one to another in rapid succession. When you put that capability in front of designers and brand owners who suddenly realize they no longer have to stick to the same size or shape of a label or package, it just opens up a lot of really interesting possibilities.”
InkWorks can use either of its 15-in.-wide LasX systems for either roll-to-roll or roll-to-sheet operations. The roll-to-sheet capability comes in mighty handy with two types of labels produced by InkWorks. One is where the customer’s volume requirements are relatively low. “Some of the smaller food manufacturers, or maybe a craft brewer, find it easier to pull pressuresensitive labels from a sheet and manually apply them to containers than to bother with a roll of labels,” says Travis. “We make labels for pouches, for example, where the customer needs 1,000 of one label, 10,000 of another and 5,000 of a third. Customers find the sheet format easier to handle.”
When these sheets of pressure-sensitive labels are in production, the laser kiss-cuts the labels on the release liner and then it cuts a deeper cut to separate individual sheets from the roll. Number of labels per sheet
All Your Package Printing Answers in One Place
The PACKage Printing Pavilion returns as a highlighted feature in the North Hall at PACK EXPO Las Vegas 2021, to be held Sept. 27-29. This pavilion will shine a spotlight on digital’s advantages for shortrun, on-demand, cost-effective, variable data, and personalized packaging as well as labeling, coding and marking solutions.
If you’re dealing with any of the following, this is a spot for you to visit: • SKU proliferation • Micro marketing efforts • Sustainability • Traceability
As consumers look for smarter packaging options, advancements in digital printing are more critical than ever, making this pavilion a must-see for all show attendees. Visit www.packexpolasvegas.com to learn more and register to attend. PW

First Combi Pack Ready Laminator installed
The Combi Pack Ready Laminator at InkWorks represents the first commercial installation of this newly available combo laminating system, which offers either thermal or solventless adhesive lamination. When Karlville debuted the original Pack Ready concept at drupa 2016, it was strictly for thermal lamination. The technology was notable then and remains notable now because it lets converters go from laminating directly into slitting and pouch-making with no time required for curing of adhesives. Here’s how it works.
InkWorks surface prints a roll of biaxially oriented polypropylene (BOPP) supplied by a firm like Nobelus. Also supplied by Nobelus is a roll of clear polyester that InkWorks laminates to the surface-printed BOPP as a way of protecting the inks. Both the polyester and the BOPP arrive from Nobelus with an extrusion coating of EVA. So all InkWorks need do is introduce heat to bond the two together—thus the term “thermal laminating.” Because no adhesive is applied, there’s no time required for curing before the material goes to InkWorks’ slitting operation. “This capability has opened up new markets and allowed us to partner with makers of standup pouches, side-gusseted pouches, and bags,” says Travis.
While InkWorks relies on thermal laminating for the pressure-sensitive label side of its business, it switches to solventless adhesive lamination for its in-mold labels. This is not only because the substrates being married are very thin and thus subject to curling when subjected to heat. It’s also because in-mold labels are usually laminations of clear BOPP to surface-printed BOPP. Thermal lamination involves EVA, which would interfere with the monolayer quality you’re after when injection molding PP containers, thus complicating ease of recycling.
Solventless laminating involves the application of an adhesive. You feed in two rolls of BOPP and one of them goes through a trough of adhesive. Then comes a doctoring roll, then a transfer roll, and then a nip roll to bond the two layers together. PW
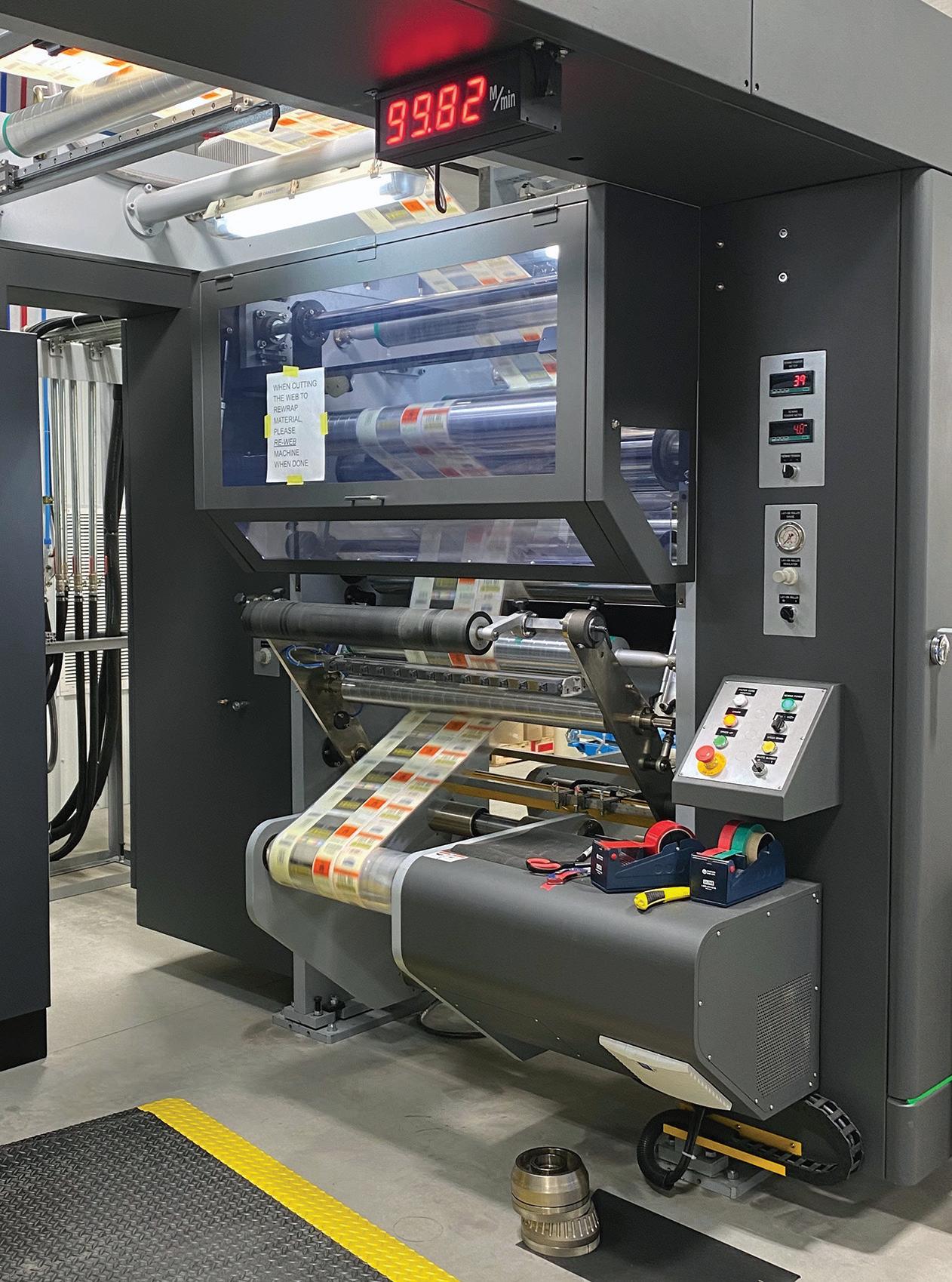
The Combi Pack Ready Laminator offers both solventless adhesive or thermal lamination.
Metal Detection with Automatic Rejection
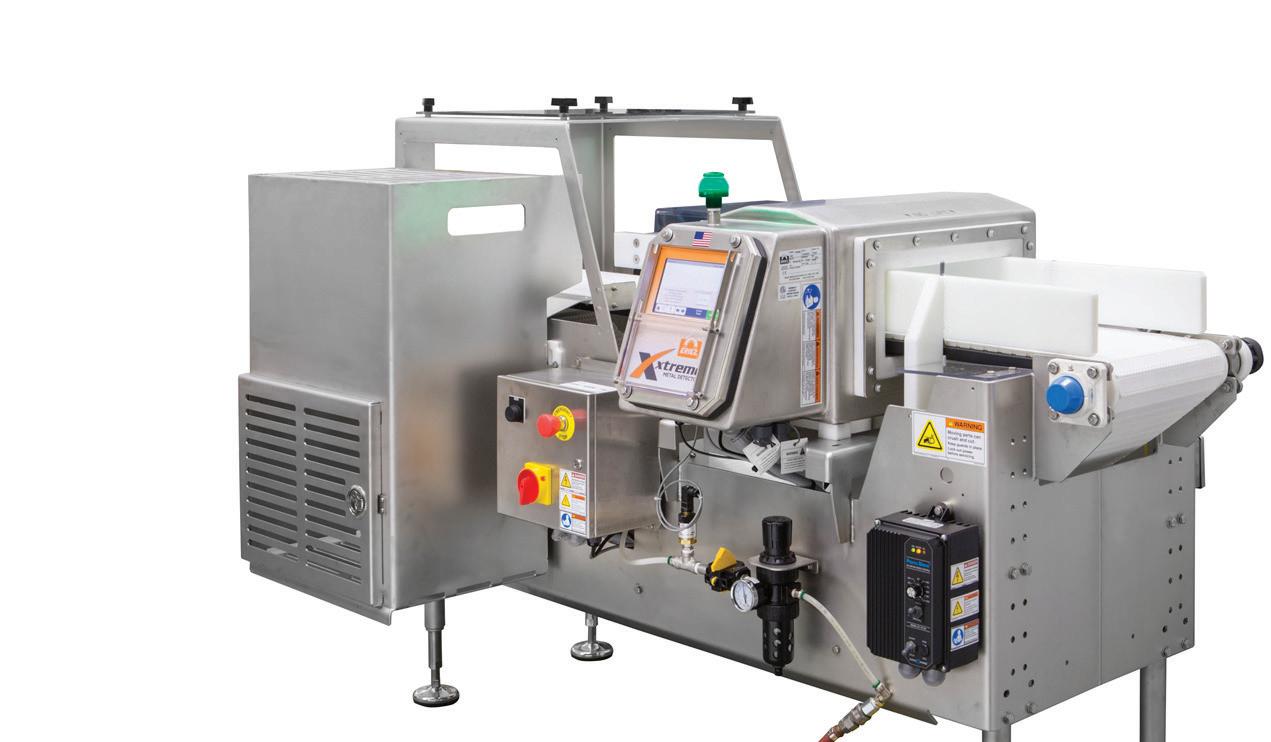
In In
X® • • • E - - • 6”, 12” 18” z • N • •
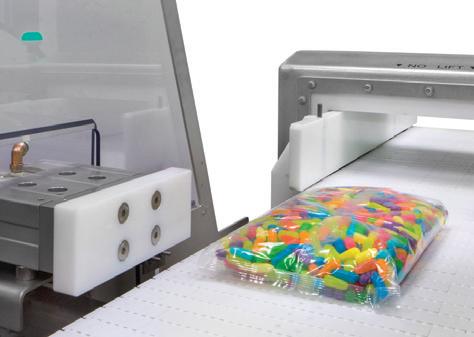
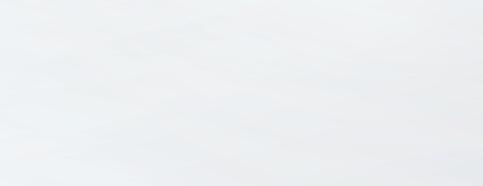
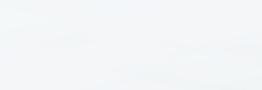


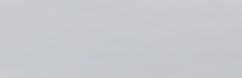















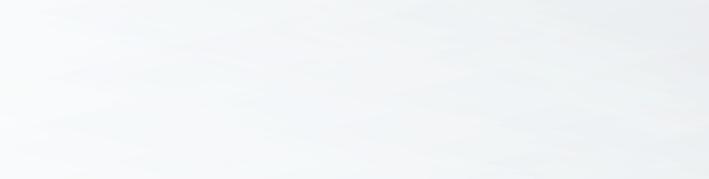



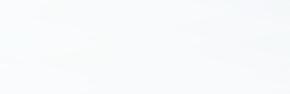


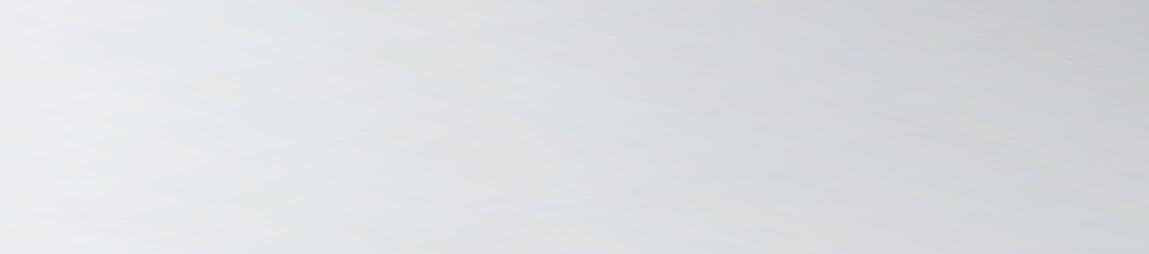

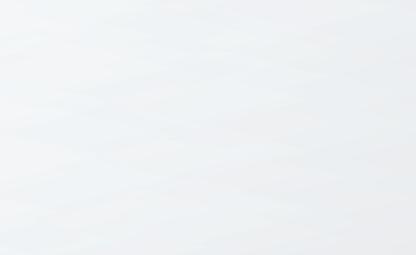
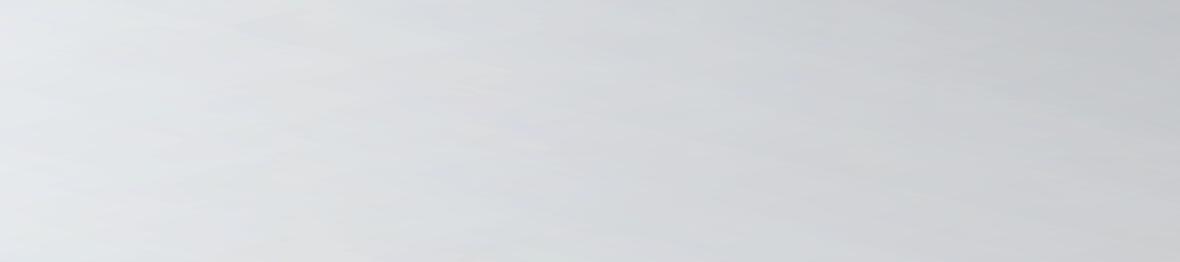
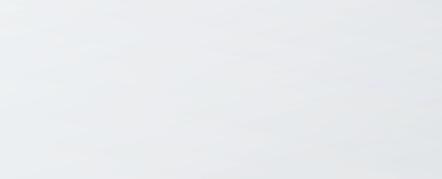
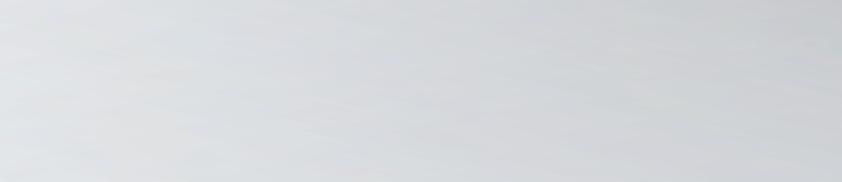

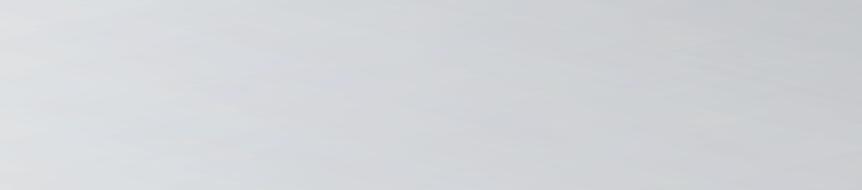








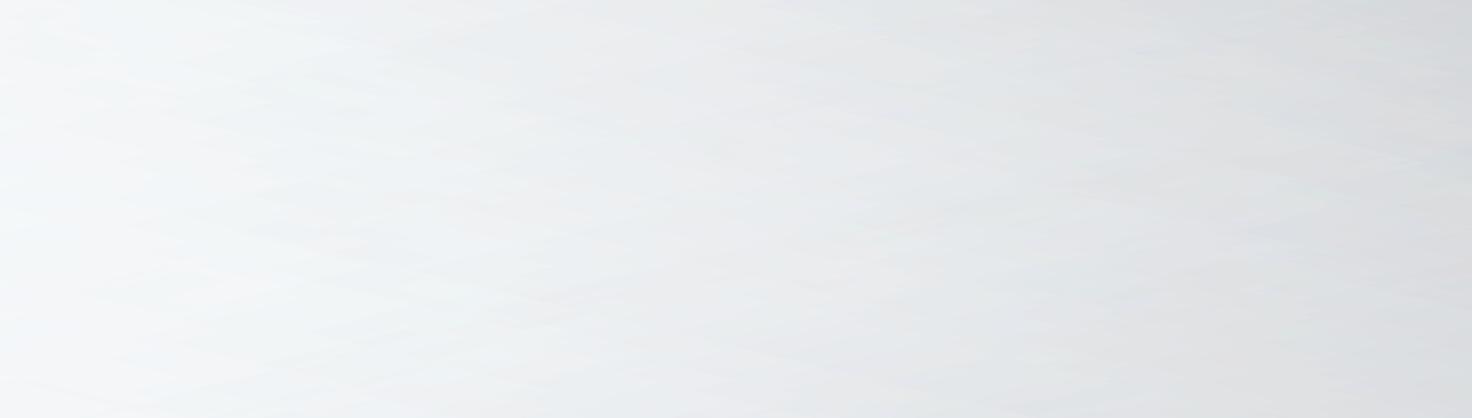
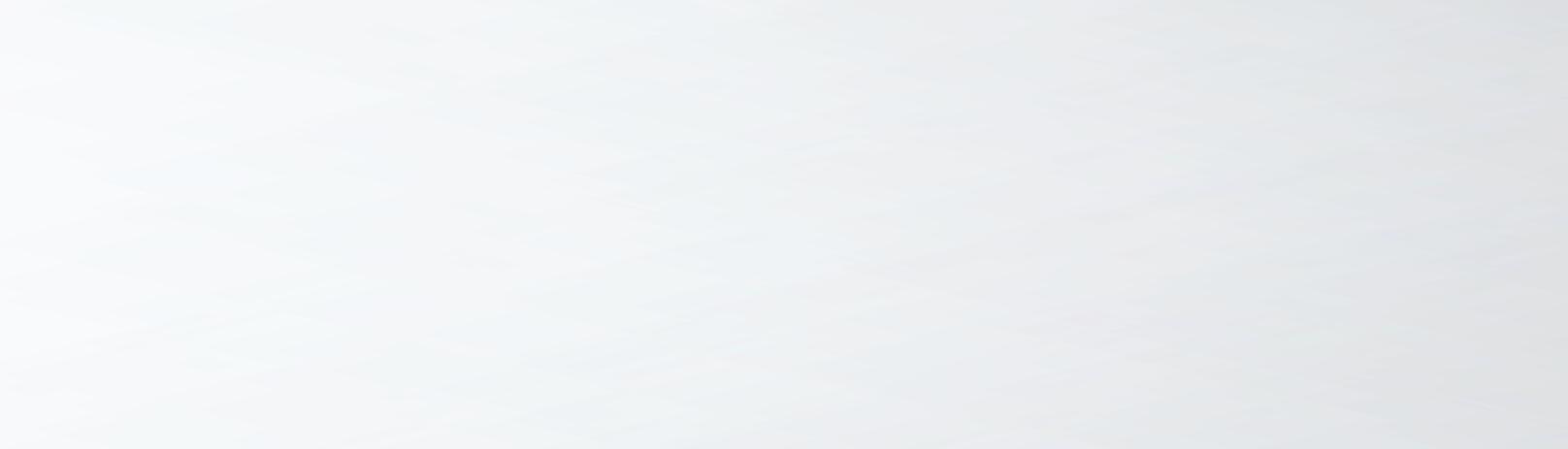






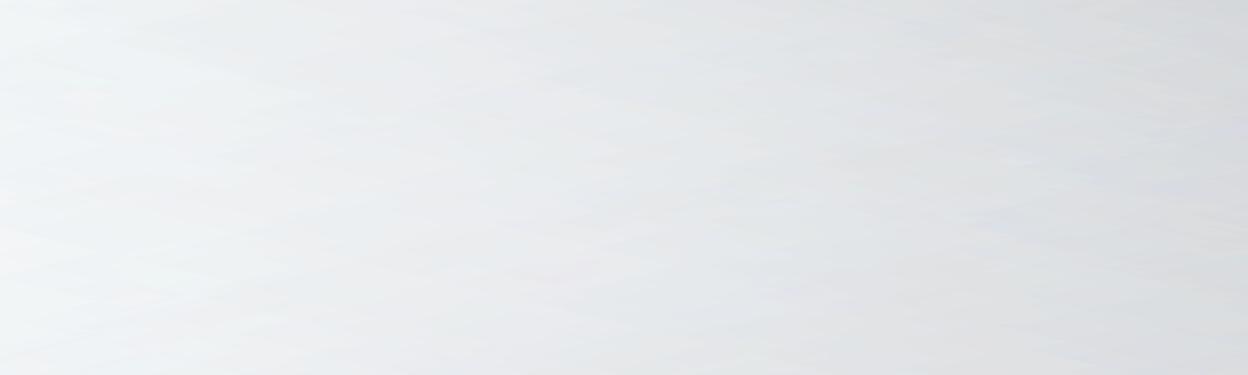









depends entirely on the customer’s requirements.
The other application where roll-to-sheet is in demand is where in-mold labels are concerned because it makes it possible to cut and stack individual labels that customers can conveniently load into the magazine feed of their injection-molding machines. Such labels are typically a two-layer lamination of 0.5-mil and 2.6-mil polypropylene (PP). The digitally printed 2.6-mil substrate fuses with the bottle sidewall in the mold, and the clear .5-mil layer traps the inks so they can’t be scratched off.
Both LasX systems operate in fundamentally the same way. When a 2D bar code printed along the edge of the roll gets scanned, it sends that identifying information to the LasX software, which then pulls the digital file needed to cause the laser to cut the appropriate shape. “It’s non-stop,” says Travis. “A circle, a square, a rectangle, a triangle, or whatever shape we need to cut. And every time a new shape is called for, the digital system immediately picks that up and changes its cutting mode with no need whatsoever to change cutting tools of any kind.”
One significant capability in the second LasX system operating at InkWorks revolves around how the laser-cut units are handled in roll-to-part production. It involves the integration of LasX’s patented stainless steel vacuum processing belt with two Dorner conveyors. The stainless steel belt makes it possible for the laser to accurately register the digitally printed web on the fly and through-cut the web, thus creating each part. The fully cut parts are then delivered from the laser area to the first downstream Dorner unit, which is an inverted vacuum conveyor. The vacuum conveyor carries the parts from the stainless steel conveyor onto the secondary Dorner belt conveyor. The servo driven rewind shaft collects the webbed scrap matrix. The speed of the second Dorner conveyor is variable and can shingle or space the parts. Counting of the parts is done automatically so the secondary conveyor accelerates to create a space to indicate to the operator the stack count has been reached. All that remains is for an operator to bag the parts into cartons for shipment to the customer.
“It’s much more fluid than how we’re doing it on the first LasX system,” says Travis. “On that system the machine extracts parts from the web by redirecting the web path after cutting and allowing the cut-through labels or sheets to be captured by a nip that feeds the parts onto a conveyor. If the labels are very small or extremely thin, they wrap up on the nip rollers or they get jammed up. The new vacuum conveyor system completely eliminates these issues. We learned a lot with that first machine. Then, by working closely with LasX, they were able to design just what we needed this time around. It’s just an amazing machine.” PW The latest addition to the world of multipacking is Standard-Knapp’s new TriWraptor™ TSUP (Tray/Shrink/Unsupported/Pad) Packer.
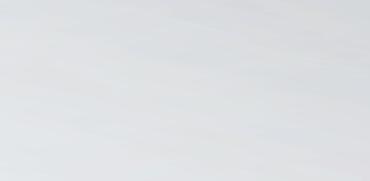
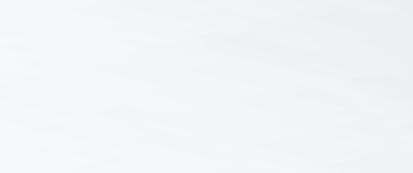

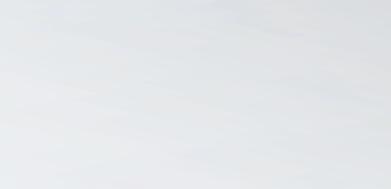
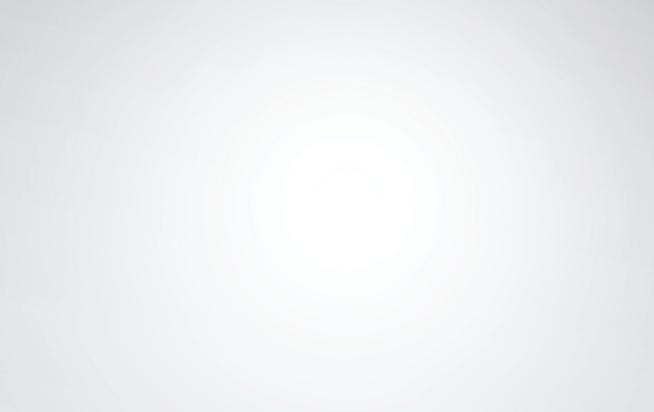
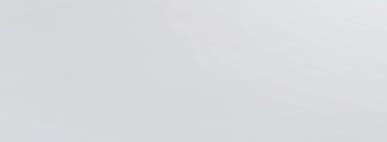
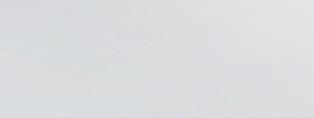

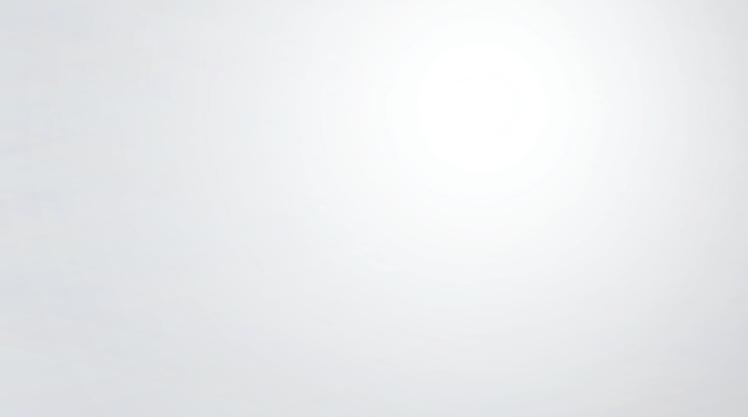
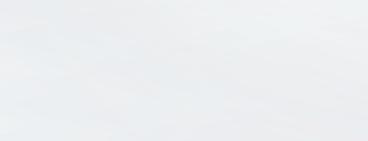
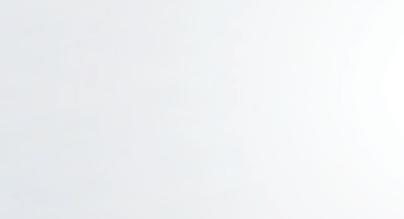
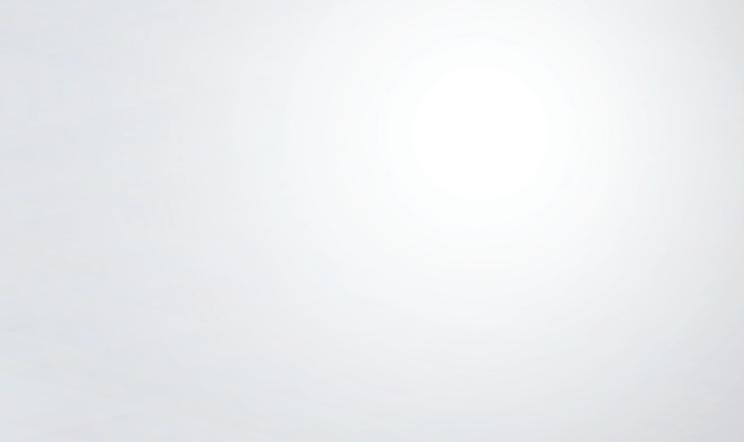
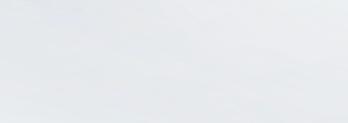
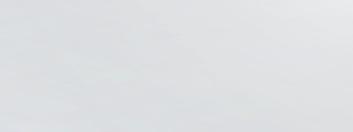

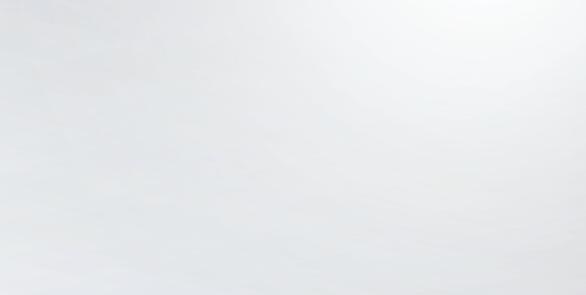

Within the TriWraptor TSUP’s footprint lies the ability to package PET, glass, HDPE, steel, aluminum and fiberboard into tray, film, U-board, pad and unsupported configurations. Added to this flexibility are the high reliability, robust construction and simple operation that make Standard-Knapp a leader in packaging machinery.
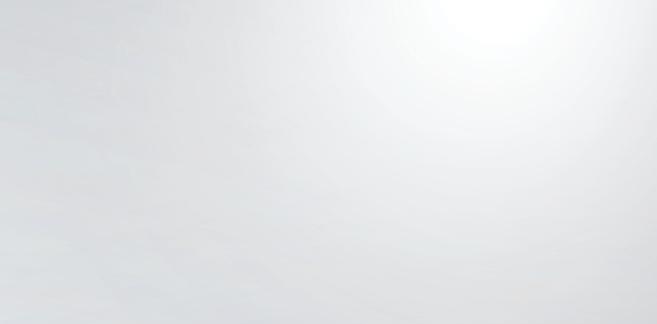
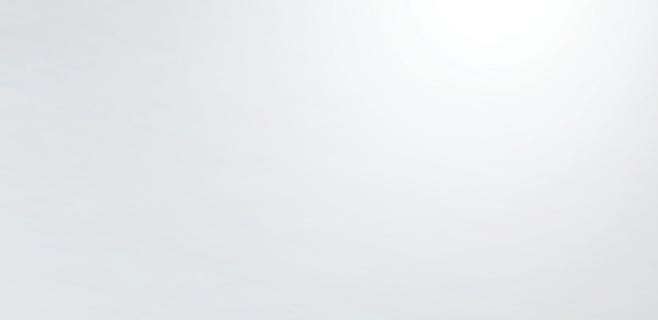
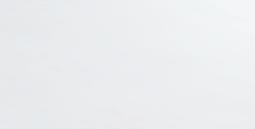
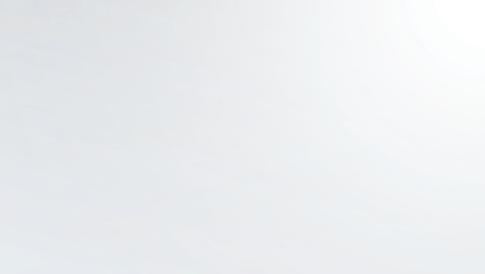

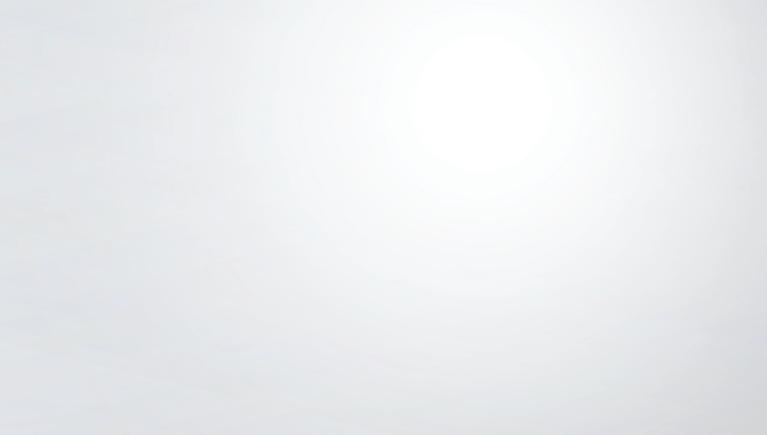


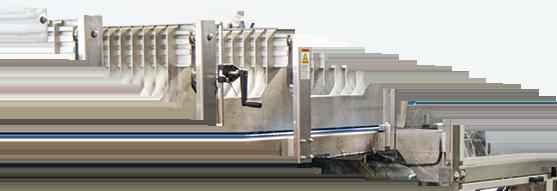

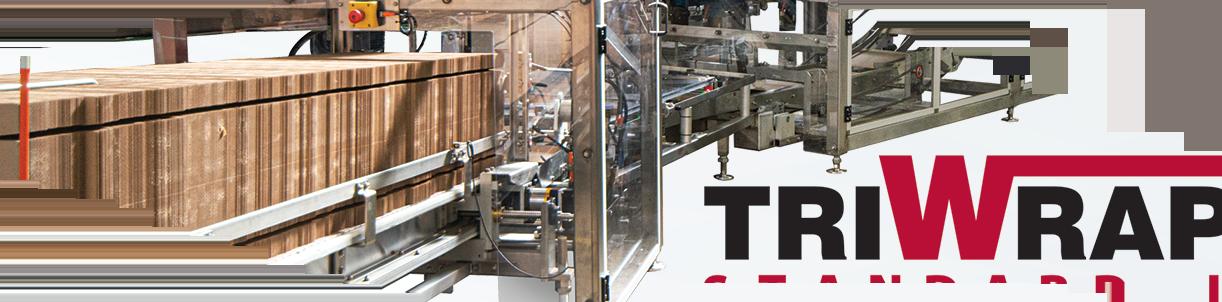


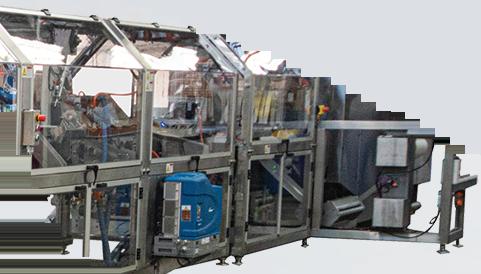
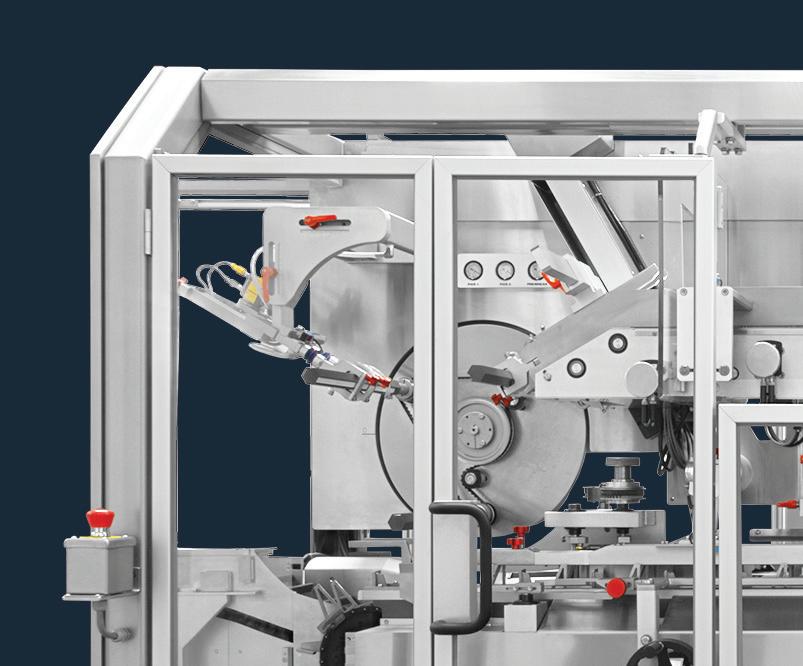
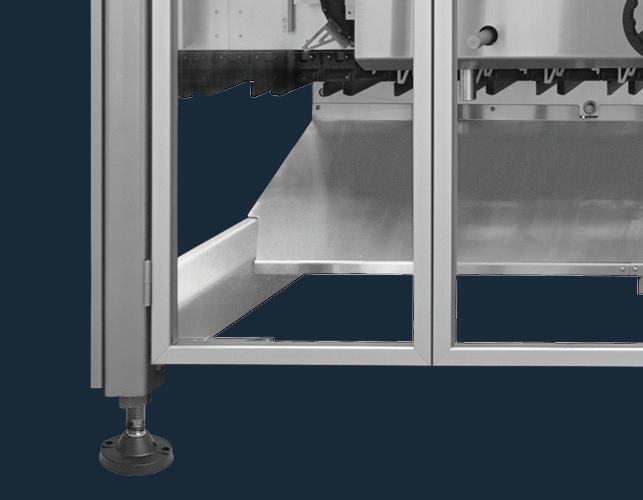
Trade Shows have returned! See us in September:
September 9-12, 2021 Colorado Convention Center Denver, CO Booth #5156 September 27-29, 2021 Las Vegas Convention Center Las Vegas, NV Booth #C-3800

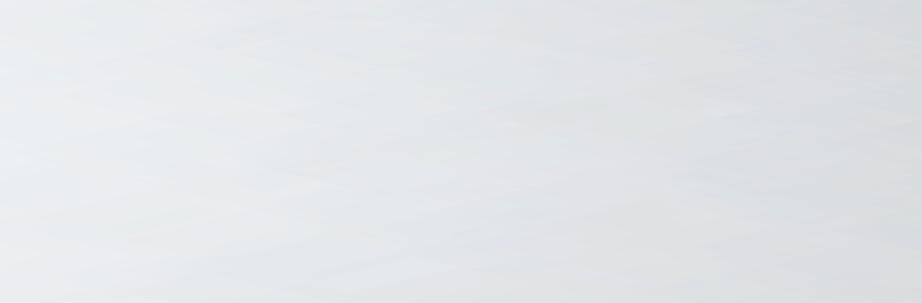