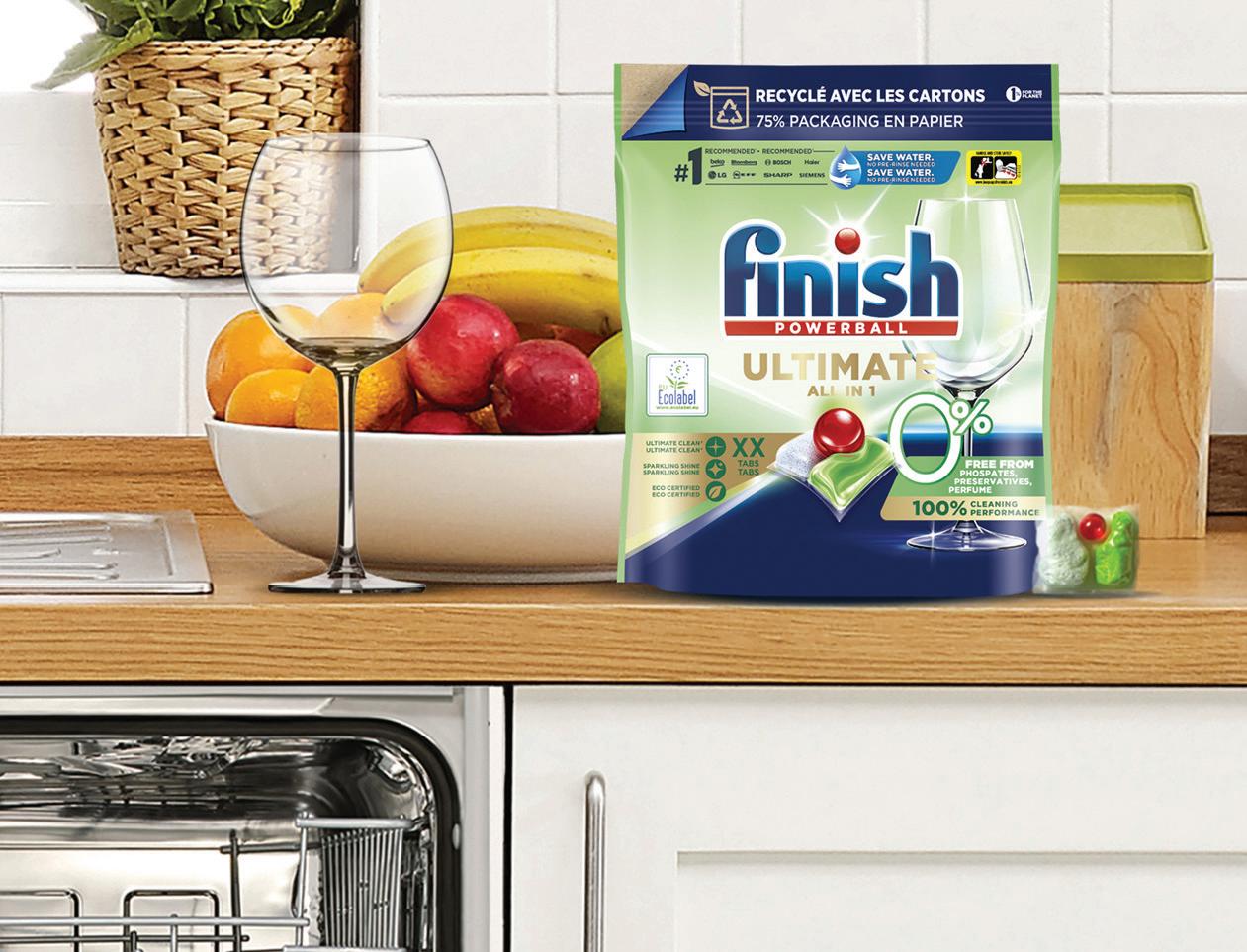
5 minute read
Paper Packaging Expands to Reckitt’s Dishwasher Tablets
Innovation that enables a switch from plastic to paper packaging for a range of Consumer Packaged Goods products having challenging barrier requirements has been on a tear of late. This includes paper bottles for liquids, flow wraps for confectionery, and cups for yogurt. Among the latest is a new stand-up pouch for multinational Reckitt’s Finish dishwasher tablets, a particularly difficult application given the product’s water-soluble nature.
Introduced in Carrefour retail stores in France in the fall of last year, the paper-based pouch is the culmination of a multi-step process by Reckitt to “achieve the ultimate pack in terms of sustainability.” That’s according to Krzysztof Krajewski, director of packaging sustainability hygiene at Reckitt, who says the innovation around the Finish package first gained momentum in 2018, when the company developed a long-term plan to reach its goal.
“In 2019, Finish replaced the non-recyclable plastic laminate from its stand-up pouch with a recyclable film,” he says. “Later in 2021, we incorporated a minimum of 30% recycled plastic into its recycled pouch and rigid packaging, eventually leading to the paper-based packaging that launched in November 2022.”
Top 5 Robot Trends for 2023
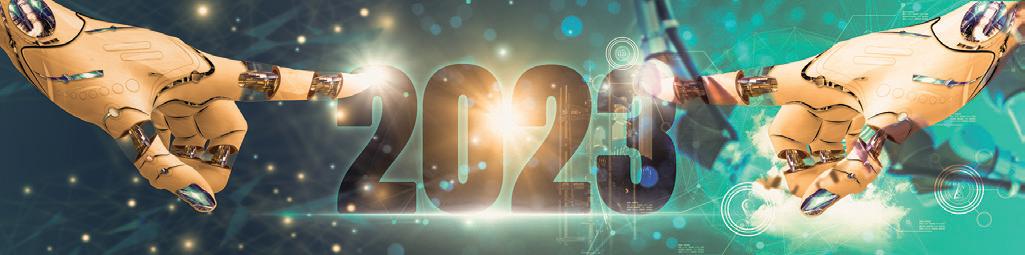
New data from the International Federation of Robotics shows that in 2022, the stock of operational robots around the globe hit a new record of about 3.5 million units, while the value of installations reached an estimated $15.7 billion. Looking to 2023, IFR has identified five trends that will shape automation and robotics in the coming year. These include:
The new pouch was developed by Reckitt and longstanding supplier Mondi, whose tactic is to “use paper where possible, plastic when useful,” says Olivier Seux, head of global key accounts at Mondi. Seux explains that Mondi used its EcoSolutions approach, whereby it jointly evaluated the requirements of the product packaging—sealability, durability, and water-resistance—along with Reckitt’s sustainability goals to design and manufacture the new pouch.
“The paper-based packaging is replacing 75% of plastic with responsibly sourced paper and works towards Reckitt’s sustainability target of
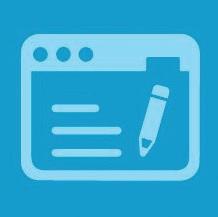
1.Energy efficiency: Energy efficiency is key to improving companies’ competitiveness amid rising energy costs; the adoption of robotics can in many ways help lower energy consumption in manufacturing. Compared to traditional assembly lines, significant energy savings can be achieved through reduced heating, while at the same time, the high speed of robots increases production rates, making manufacturing more time- and energyefficient.
Today’s robots are also designed to consume less energy, which leads to lower operating costs. To meet sustainability targets for their production, companies are using industrial robots equipped with energy-saving technology such as robot controls that can convert kinetic energy into electricity, feeding it back into the power grid, and smart power-saving mode technology that controls the robot’s energy supply on-demand throughout the workday. Since industrial facilities need to monitor their energy consumption, such connected power sensors are likely to become an industry standard for robotic solutions.
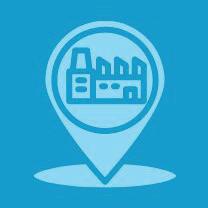
2. Reshoring: Resilience has become an important driver for reshoring in various industries. For example, car manufacturers are investing heavily in short supply lines to bring processes closer to their customers. These manufacturers use robot automation to manufacture powerful batteries cost-effectively and in large quantities to support their electric vehicle projects, making the shipment of heavy batteries redundant.
Relocating microchip production back to the U.S. and Europe is another example of a reshoring trend. Since most industrial products nowadays require a semiconductor chip to function, their supply close to the customer is crucial. Robots play a vital role in chip manufacturing, as they meet the requirements for extreme precision. Specially designed robots can now automate silicon wafer fabrication, perform cleaning and cleansing tasks, or test integrated circuits.
3. Ease of use: The emergence of new automation platforms is making it easier for nonexperts to program industrial robots, as OEMs work with low-code or no-code technology partners to enable users of all skill levels to program robots. New, easy-to-use software with intuitive user experiences is replacing extensive robotics programming and opening up new robotics automation opportunities. For example, a traditional heavyweight industrial robot can now be equipped with sensors halving the amount of virgin plastic used by 2030,” Seux explains. “At the same time, the sealable packaging provides excellent barrier properties, protecting the dishwasher tabs from moisture, making the packaging sustainable by design.”
According to Krajewski, Reckitt chose to focus its sustainable packaging efforts on the Finish package due to the plastic-reduction potential of the product—the world’s largest automatic dishwashing brand. While the new bag is currently only available in Carrefour in France, Reckitt plans to launch the new packaging across Europe once it has made adaptations to the structure to make it recyclable in those markets as well. When the launch is complete, Reckitt estimates the new paper-based pouch will help eliminate more than 2,000 metric tons of plastic annually as well have a notable impact on CO2 emissions.
As Krajewski explains, Reckitt used the company’s Sustainable Innovation Calculator (SIC), which measures the sustainability of plastic and packaging inputs of every new product, in the development of the paper pouch. “Using the SIC and an external Life Cycle Assessment, we were able to understand the innovation’s impact across countries with different recycling regulations and facilities,” he says. “It also allowed us to get a detailed understanding of its impact on CO2 emissions. We expect this packaging will generate 15% less CO2 emissions across the packaging lifecycle versus previous versions.”
The technical details on the pouch construction are proprietary, but Seux shares that a polyethylene zipper is used for the package. The pouch is gravure-printed in up to 10 colors, depending on the product variety. According to Krajewski, the new construction did require some adjustments to Reckitt’s packaging equipment, with changes ranging from relatively small to larger improvements in the process.
As for the cost of the new package, Krajewski says that Reckitt always ensures that its innovations are cost-effective for the company and for its customers. He adds, “As we continue to scale up production of the new packaging, we expect to see its cost reduce.” —Anne
Marie Mohan
and software that allow for collaborative setup operation. This makes it easy for workers to adjust heavy machinery to different tasks.
Easy-to-use programming interfaces that allow customers to set up the robots themselves are also driving a new segment of low-cost robotics. Many manufacturing customers reacted to the pandemic in 2020 by experimenting with robotic solutions. Robot suppliers acknowledged this demand, making improvements to their equipment for easy setup and installation, with preconfigured software to handle grippers, sensors, or controllers that support lower-cost robot deployment.
4. Artificial Intelligence (AI) and digital automation: Connected robots are transforming manufacturing. Robots will increasingly operate as part of a connected digital ecosystem, with cloud computing, big data analytics, or 5G mobile networks providing the technological base for optimized performance.
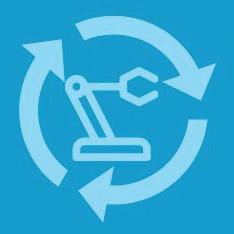
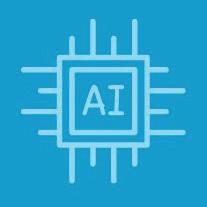
AI also holds great potential for robotics, enabling a range of benefits in manufacturing. The main aim of AI in robotics is to better manage variability and unpredictability in the external environment, either in real time or offline. AI-supported machine learning will thus play an increasing role in areas such as optimizing processes and predictive maintenance. This technology will also help manufacturers, logistics providers, and retailers deal with frequently changing products, orders, and stock. The greater the variability and unpredictability of the environment, the more likely AI algorithms will provide a costeffective and fast solution.
5. Second life for industrial robots: Since an industrial robot has a service lifetime of up to 30 years, new technology is giving old robots a second life. Industrial robot manufacturers are now running specialized repair centers close to their customers to refurbish or upgrade used units in a resource-efficient way. This prepare-to-repair strategy for robot manufacturers and their customers also saves costs and resources. Offering long-term repair to customers is an important contribution to the circular economy.
—Anne Marie Mohan
• Process Flexibility: Modular conveyor systems with standard designs
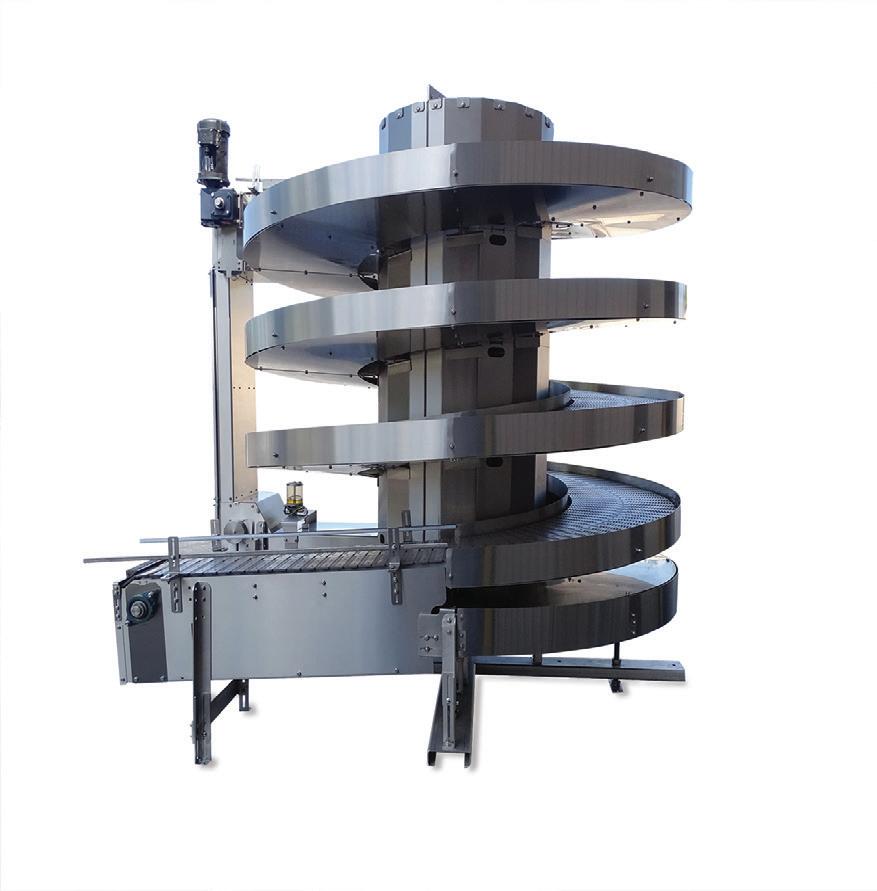
• Cost Flexibility: Quote solutions with options for every project blueprint
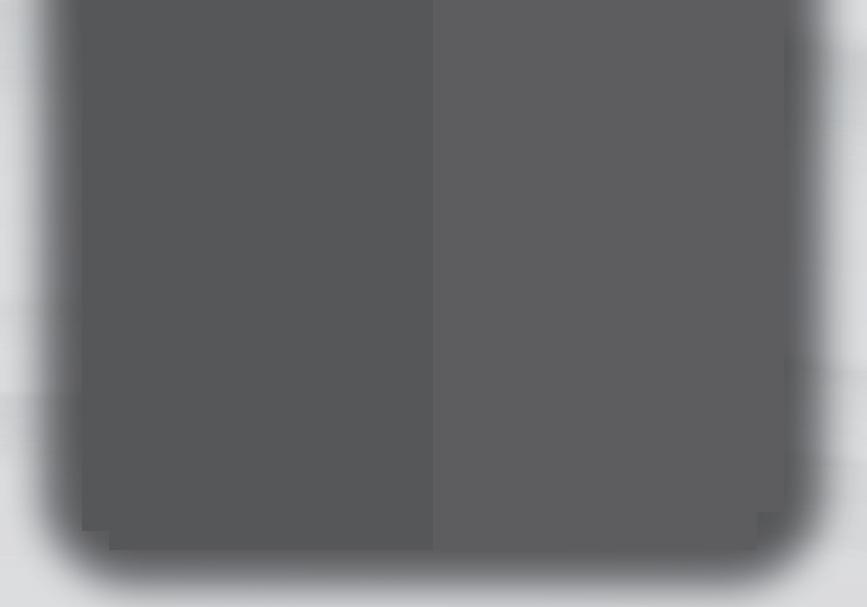