
2 minute read
POSITIONING SYSTEMS FOR PACKAGING MACHINES
Electronic, bus-compatible position indicators with target / actual value comparison and intuitive operation
Automated fieldbus-/Ethernet compact actuators: easy commissioning, fast amortization
Mechanically compatible: SIKO positioning systems are mechanically interchangeable
IO-Link in the most compact position indicator they can find jobs that will be Monday through Friday.
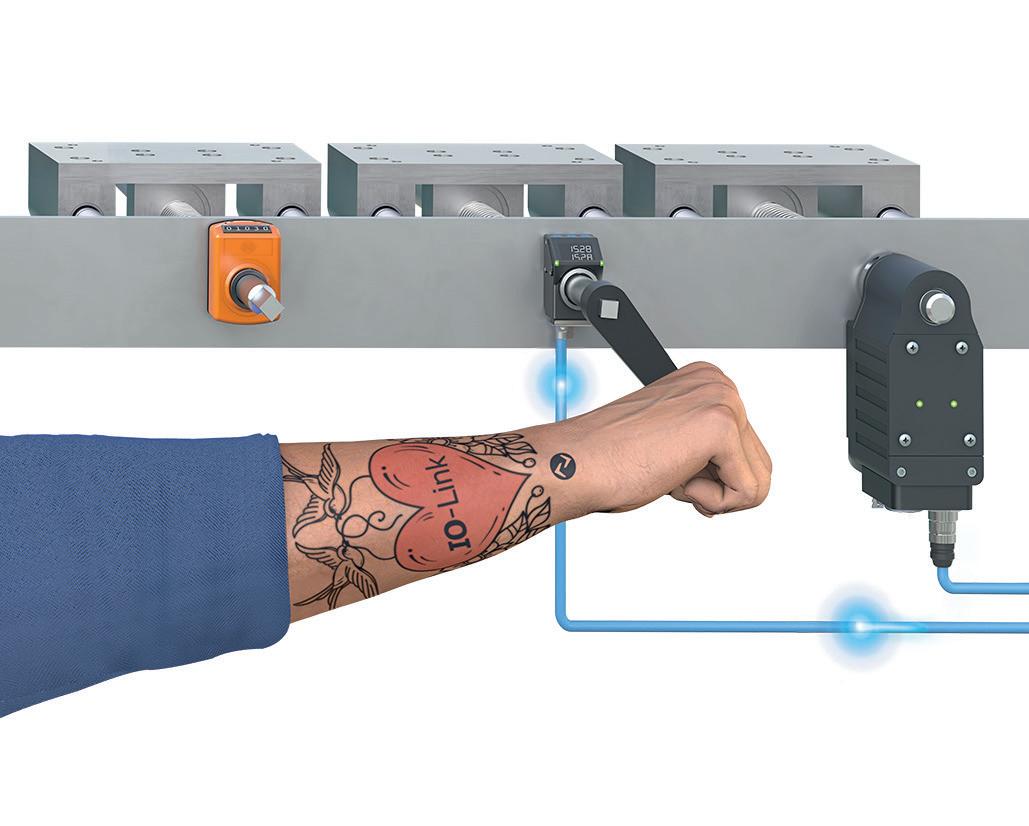
One of the roadblocks we run into in manufacturing is you typically run around the clock. At my previous job with SunOpta, we ran 24 hours a day, seven days a week, 365 days a year. For someone coming out of high school, a lot of the highly desirable jobs start on the back shift [late afternoon through midnight]; they don’t start Monday through Friday, 8 to 5. And so, getting someone to say, “Yeah, I’m willing to work that back shift,” has been a harder sell than probably the job itself, because you can’t have 12 people in a maintenance group on days and none on nights. You have to build positions that you need to be successful, which includes back shifts.
What strategies have you used to address these challenges?
One of the things we’ve focused on is how can we be competitive and still be family-friendly from a work schedule standpoint. So a lot of the decisions that we’ve made in the last six months to a year have really been focused around how do we stay on a four-day schedule, flexing to five, staying away from Saturday and Sunday—that’s family time— while at the same time being able to complete our production cycles and take on new growth over the course of the next one to five years.
We’ve done that with technology, through bigger, faster, more automated equipment that requires fewer people and that can increase our production 30%, 40%, 50%, without having to add a Saturday workday or a weekend shift. And in the last year, we’ve gone from producing probably an average of 350,000 units a day to, I think in the last three months we’ve averaged about 550,000. And we did that without really adding a lot of equipment; we’ve done that more with how well our equipment has run. We’ve added tools like Redzone [connected worker platform] to be able to watch our OEE and downtime and trend our performance. As a result, we’ve seen 10-point improvements across all of our lines in the last year just in OEE, which has been probably the biggest improvement we’ve seen because now we’re producing more with the same exact labor.
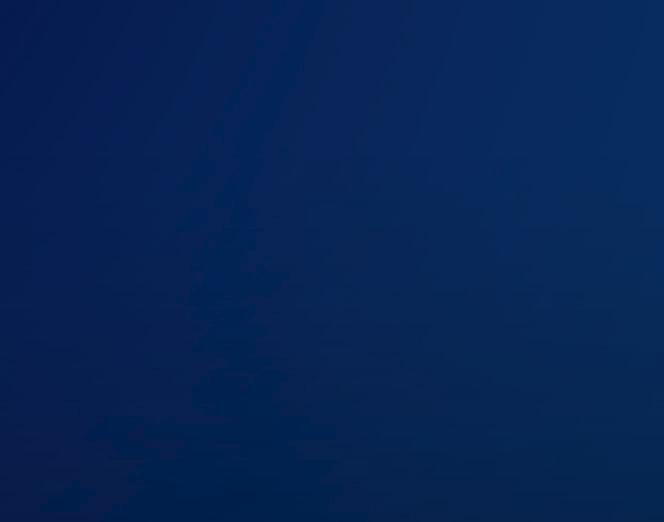
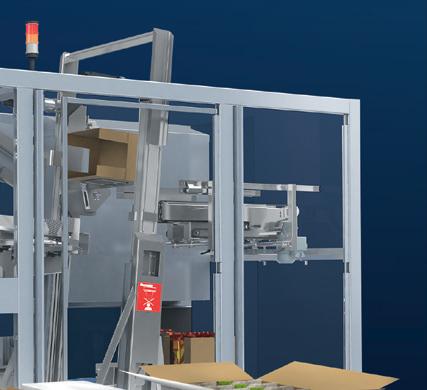

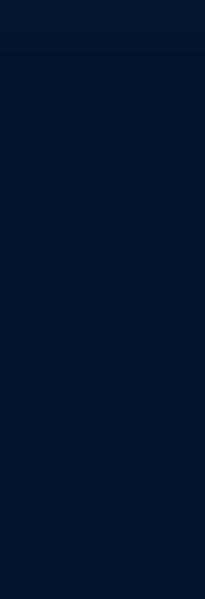
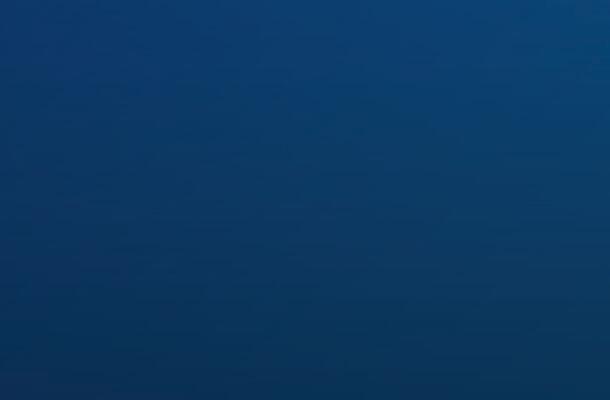
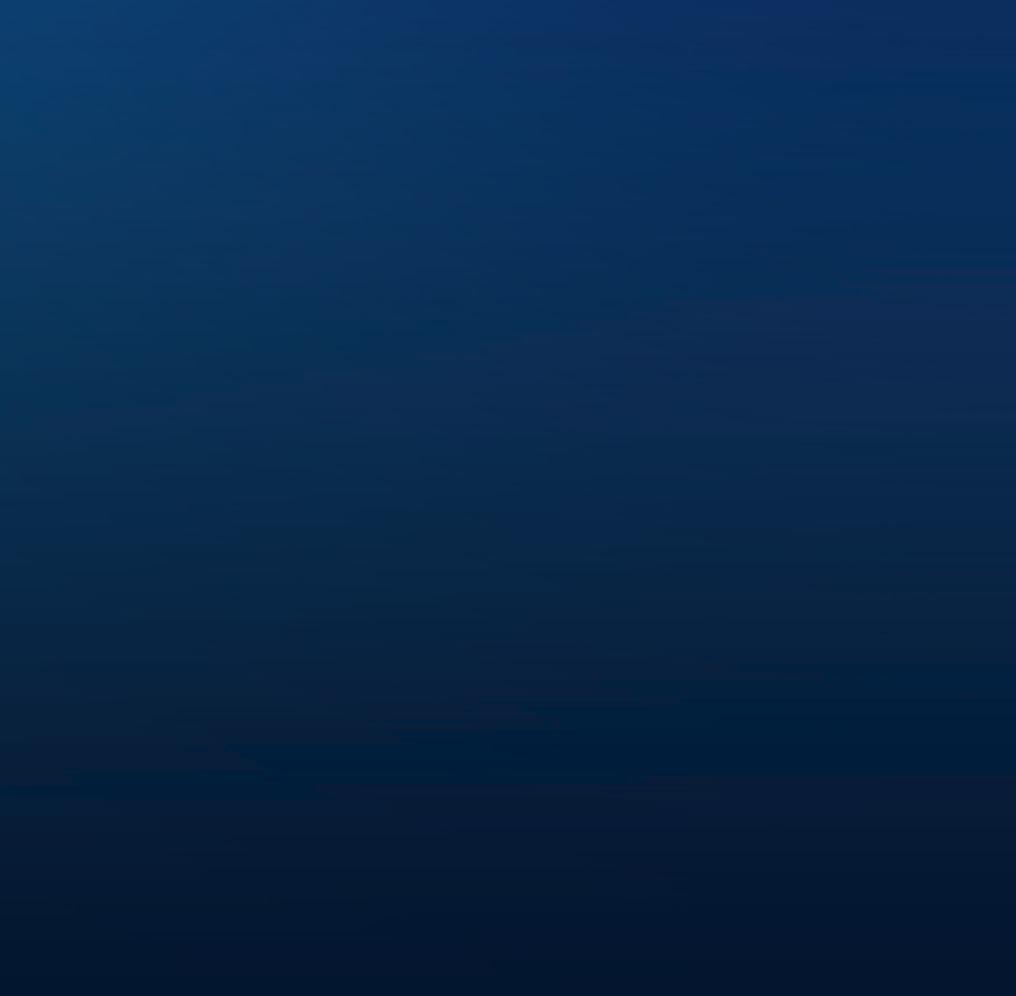
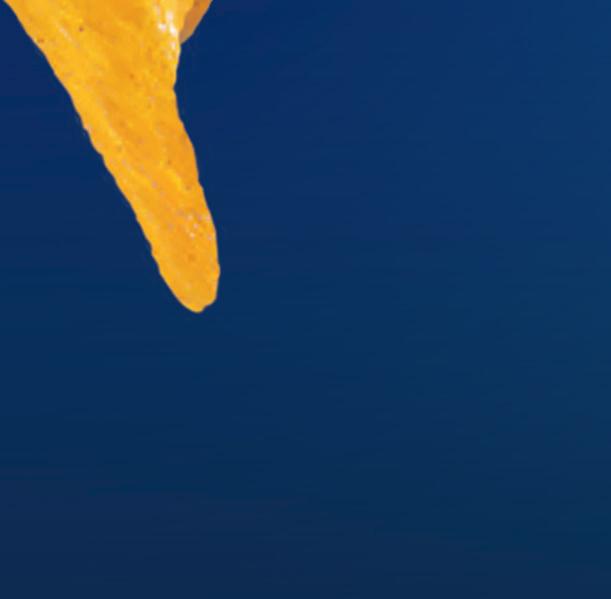
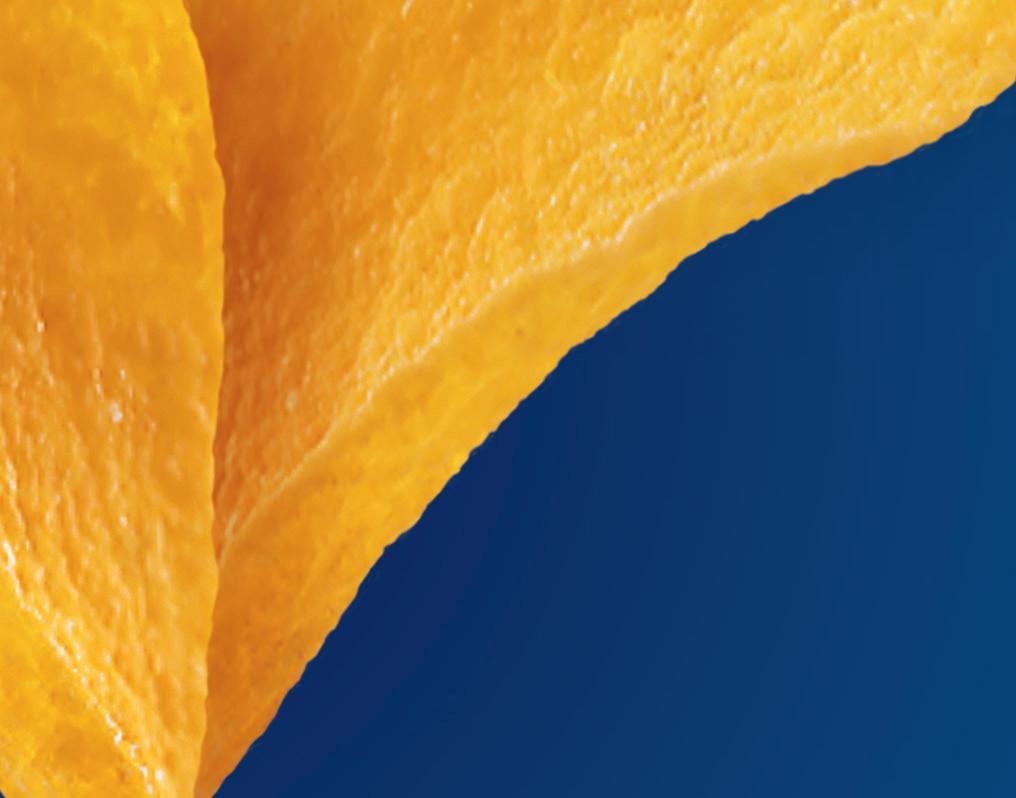
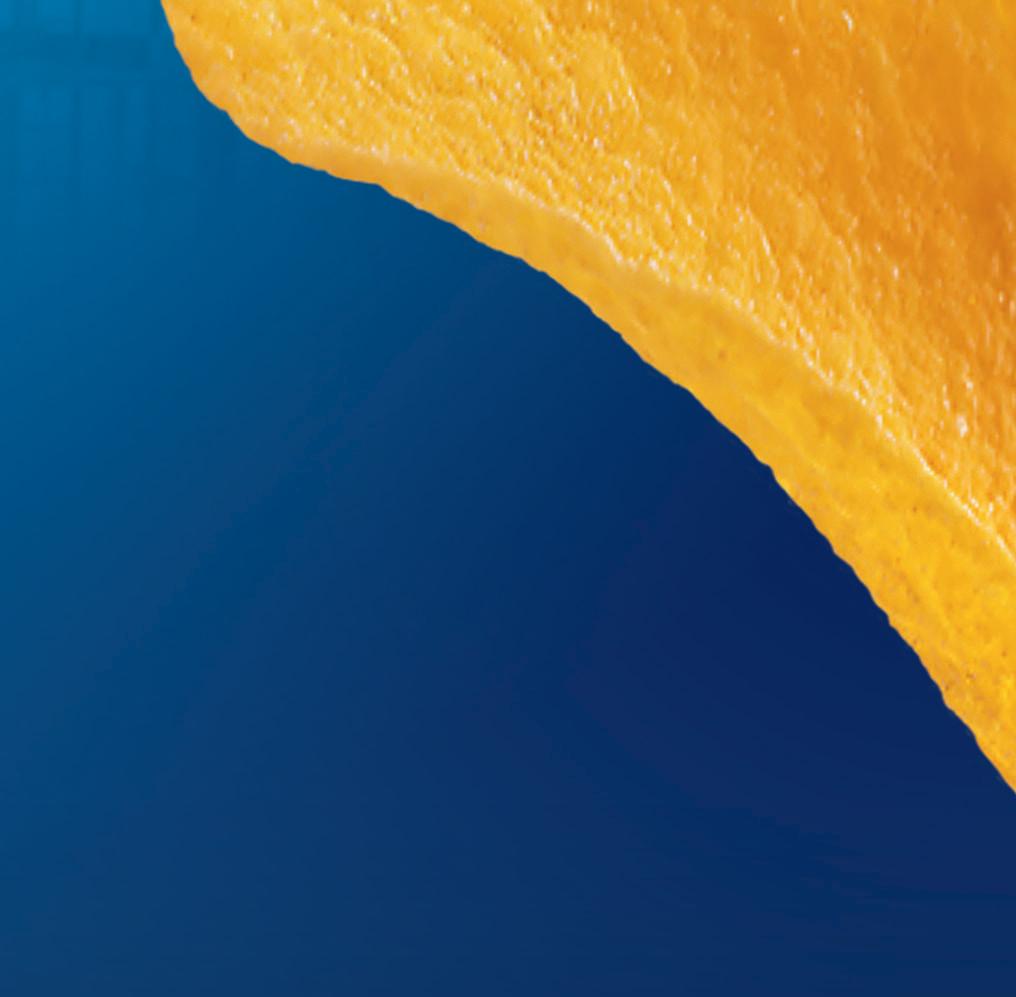
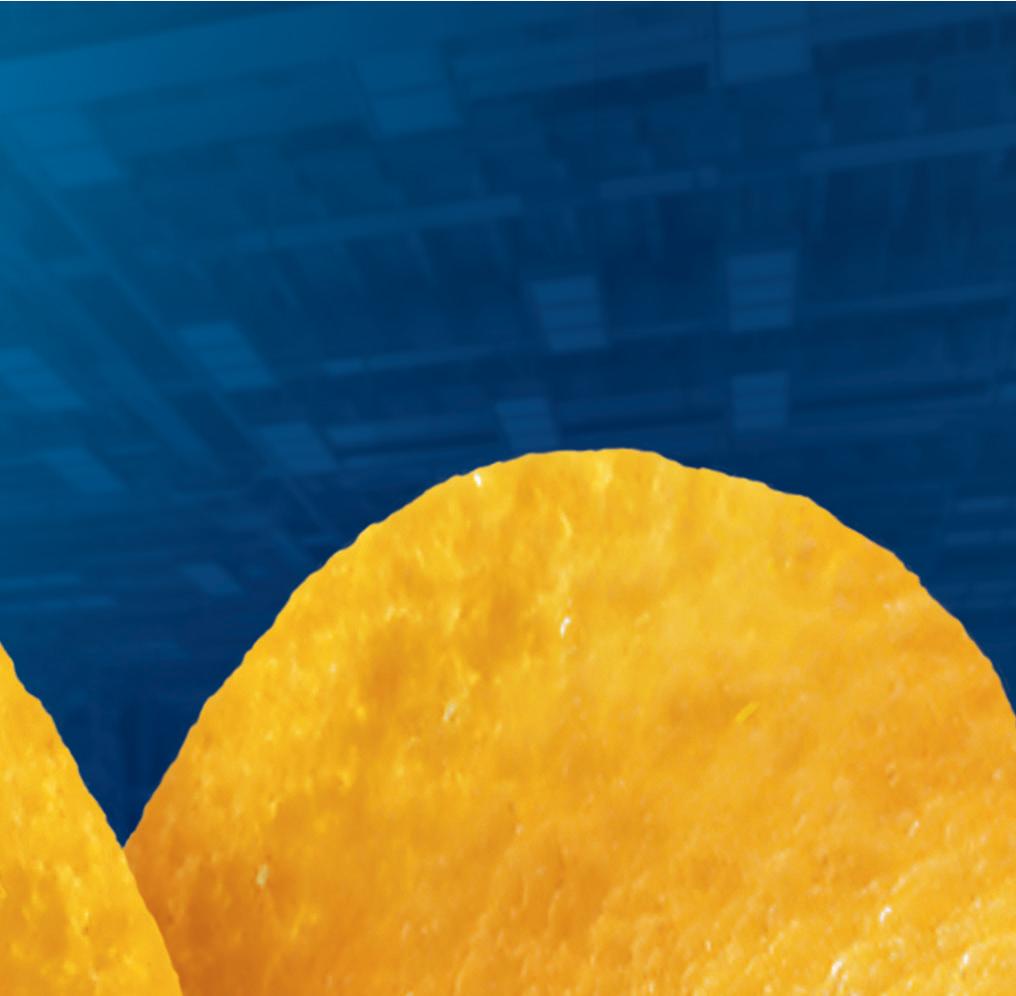
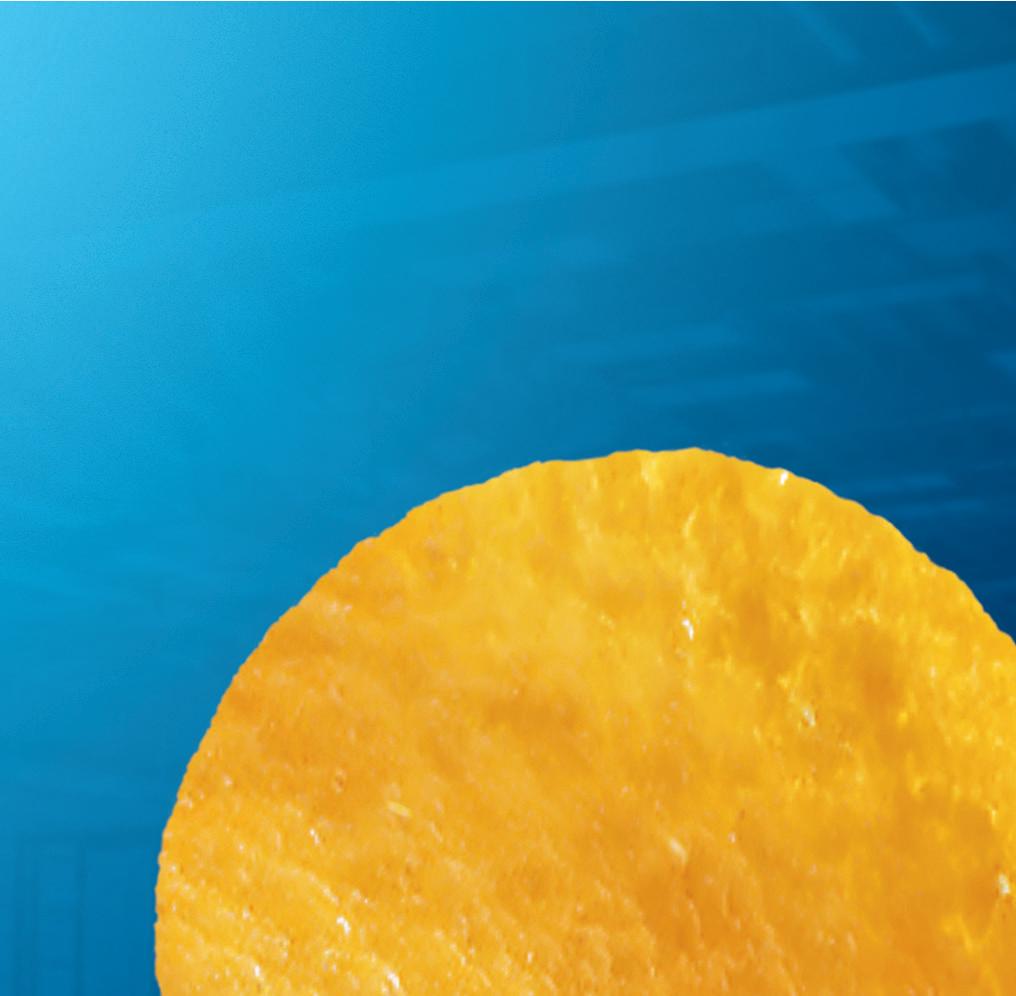
We also have a pretty good work environment as far as it’s not overly noisy and we keep the temperature around 70 degrees [Fahrenheit] in our packaging department because we have to control humidity, and the machines operate the best in a fairly standard environment. So it’s not a bad environment to be in. A lot of our competition within the community consists of meat plants, and that’s a very different environment to work in than ours. So we’ve tried to make our environment, our workdays, and our schedule better and more friendly for families.
The good news is, as we sit here today, we’re actually pretty good on labor—not without a lot of work and effort—but we’re sitting about where we need to be from a labor standpoint. We’d love to continue to increase our skillset, but that’s one of those areas where we know we’ll have some struggles, and we’re trying to be creative in how we go after and help promote more skilled labor as we go forward. —Anne Marie Mohan
By Sterling Anthony, CPP, Contributing Editor
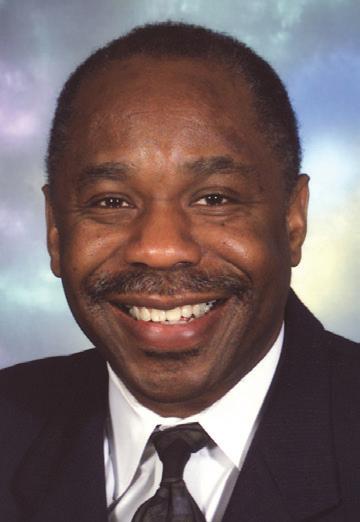