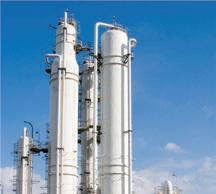
17 minute read
NEWS
Artificial Intelligence Autonomously Controls JSR Chemical Plant
By David Greenfield
Director of Content, Automation World
In a field test to determine the viability of artificial intelligence (AI) to control a chemical plant, automation technology supplier Yokogawa Electric Corporation and chemical manufacturer JSR Corporation successfully operated a distillation column at the JSR plant autonomously with AI for 35 days. The test ran from January 17 to February 21, 2022, for a total of 840 hours of operation.
Yokogawa and JSR say the test confirmed that reinforcement learning AI can control operations beyond automated PID and Advanced Process Control (APC) applications that typically require the judgement of plant personnel and manual operation of control valves.
The specific AI technology used at the JSR plant—the Factorial Kernel Dynamic Policy Programming (FKDPP) protocol—was developed by Yokogawa and the Nara Institute of Science and Technology in 2018. IEEE recognized this technology as being the first reinforcement learning-based AI suitable for use in plant management. In addition to the FKDPP protocol’s ability to handle tasks beyond PID and APC, Yokogawa says specific strengths of this AI technology include an ability to deal with conflicting targets, such as handling the dual needs of maintaining high quality and achieving energy savings.
Other Yokogawa automation technologies used in the test included: • OmegaLand plant simulator; • Centum VP integrated production control system; • Exaopc OPC interface package (OPCcompliant software that enables management of databases used in the processing industries); and • GA10 data logging software.
According to Yokogawa and JSR, specific achievements of the AI technology during its 35 days of autonomously operating the plant include: • Ensuring product quality while eliminating excess fuel, labor, and time costs associated with the production of off-spec products. • Maintaining liquids in the distillation column at an appropriate level while making maximum possible use of waste heat as a heat source. • During inclement weather conditions that could disrupt the control state due to temperature changes, products produced during those periods still met the plant’s standards.
Though the test proved that complex chemical plant operations can be successfully controlled autonomously, Yokogawa and JSR point out that “there are still many situations where veteran operators must step in and exercise control.”
The two companies plan to continue exploring the application of the FKDPP protocol to other processes and plants to improve productivity.
“We have heard comments [from operators in the field] that not only has the burden on operators been reduced [with this AI technology], but the very fact that we have taken on the challenge of [using] this new technology and succeeded is motivation for moving forward with digital transformation,” said Masataka Masutani, general manager of production technology at JSR.
Kenji Hasegawa, vice president at Yokogawa Electric, added that the success of this test suggests that AI can significantly contribute to autonomous production operations, maximization of ROI (return on investment), and environmental sustainability around the world. “With our gaze fixed firmly on a world of autonomous operation that forms the model for the future of industries, we are now promoting the concept of IA2IA (Industrial Automation to Industrial Autonomy), which considers the impact of differences in humans, machines, materials, and methods in industry,” he said.
Distillation column at JSR plant.
22_001941_Automation_World_SEP Mod: August 15, 2022 5:08 PM Print: 08/15/22 5:08:29 PM page 1 v7 π
SHIPPING SUPPL SPECIALISTS D NEEMA® TOUGH GLOVES WAREHOUSE
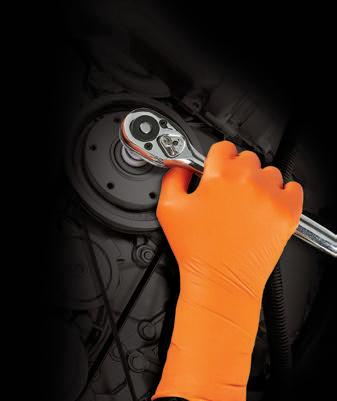

LATEX
NITRILE
Google Cloud and Litmus Co-Develop Data Connectivity Platform
By David Greenfield
Director of Content, Automation World
If there’s one thing industry’s embrace of cloud and edge computing technologies has shown us, it’s that hybrid systems—using both cloud and edge computing to handle data storage and analytics—are the preferred approach. As revealed in a 2019 Automation World study, digital transformation initiatives tend to follow a typical rollout pattern: Phase one is usually centered around the cloud to host core enterprise analytics applications to evaluate plant performance or for asset optimization to reduce production downtime. From there, manufacturers tend to invest in edge computing technologies for detailed onsite analytics delivered in near real time. The cloud also figures in as a means of providing additional storage and compute scalability.
This hybrid reality of cloud and edge computing can be seen in the development of the Manufacturing Connect platform by Google Cloud and Litmus (a supplier of industrial edge computing technologies). The idea behind the Manufacturing Connect platform is to simplify the process of collecting data from disparate factory devices and exposing it to Google Cloud data and artificial intelligence (AI) applications.
According to Litmus, Manufacturing Connect is a factory edge platform designed to support more than 250 machine communication protocols. Data is structured and stored locally and then sent to Google Cloud for analysis. The platform can also reportedly deploy and manage AI and machine learning models at the edge for closed loop AI applications.
Features of the Manufacturing Connect platform include data collection and engineering, data visualizations and KPI (key performance indicator) dashboards, containerized application deployment, and machine learning model runtime. It also includes out-of-the-box integration with several analytics packages, such as Looker for BI and analytics, and Vertex AI for machine learning and AI.”
Explaining how Litmus Edge prepares data for Google Cloud analytics, Vatsal Shah, Litmus CEO, says, “Using Litmus technology, we collect data from industrial systems, normalize that data, and add all of the OT (operations technology) data variables for context locally. We push that data into the Google Cloud environment using publish/ subscribe while Google can add more contextualized data on top at the enterprise level, such as from MES or ERP systems. The structured final data point is ready to use for analytics. All of this happens automatically but it is configurable if the user would like to change anything.”
Charlie Sheridan, technical director of industry solutions for manufacturing at Google Cloud, adds, “Manufacturing Connect provides data interoperability for all devices—regardless of type or brand—by generating a standardized JSON payload format for all data streams. In addition, Manufacturing Connect and Manufacturing Data Engine (the Google technology that provides for the common data model) share a common metadata model that supports integrated data contextualization at the edge and in the cloud.”
Sheridan points out that Manufacturing Connect can be used across the discrete and process manufacturing verticals, such as automotive, aviation, electronics, semiconductors, medical devices, pharmaceuticals, chemicals, plastics, food and beverage, and packaging and processing.
Describing how end users can apply Manufacturing Connect, Sheridan says, “Once data is centralized and harmonized by the Manufacturing Data Engine and Manufacturing Connect, it can then be used to create custom dashboards to visualize key data—from factory KPIs (key performance indicators) such as overall equipment effectiveness (OEE), to individual machine sensor data, allowing them to uncover new insights and opportunities throughout the factory. These insights can then be shared across the enterprise and with partners.”
Two specific types of applications noted by Sheridan are: • Machine-level anomaly detection via Manufacturing Connects’ use of Google Cloud’s
Time Series Insights, which analyzes real-time machine and sensor data such as noise, vibration, or temperature. • Predictive maintenance to reduce downtime and maintenance cost. Manufacturers can use
ML (machine learing) models and high-accuracy AI optimizations that are “deployable in weeks,” says Sheridan.
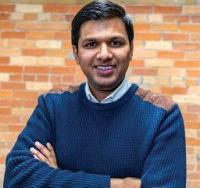
Vatsal Shah, CEO of Litmus
This video covers the initial work to align Litmus edge and Google Cloud technologies.
Learn more about the publish/subscribe method of network communications.
Connect Legacy Systems with Edge-as-a-Service
Advantech and Hivecell technologies connect legacy systems to IoT devices for scalable data collection and management.

By David Greenfield
Director of Content, Automation World
One of the biggest challenges of the digital transformation for existing manufacturing operations is accessing data from legacy production technologies and connecting them for greater analytic insights. To help address this, Advantech is working with Hivecell, a supplier of edge-as-a-service (EaaS) technology, as part of Advantech’s Artificial Intelligence of Things (AIoT) development. The combination of Advantech’s industrial hardware and Hivecell’s EaaS platform is meant to ease the process of connecting legacy systems to IoT devices for scalable data collection and management.
According to Advantech, the enormous amounts of data generated by connecting production systems can “be an obstacle to efficient operations if end users depend on cloud-only processing. While the cloud has value as a storage space, it cannot enable the day-to-day operational and safety improvements that EaaS makes possible for critical and real-time decision-making.”
Jerry O’Gorman, vice president of the Industrial IoT Division at Advantech, says, “The continuous growth of connected smart devices and machines is driving a need for cloud-native architectures to be built on the edge, addressing increasing computing, throughput, and privacy needs closer to source.”
“Hivecell provides the industry’s first edge-asa-service platform enabling cloud-like compute power deployed on premises,” says Jeffrey Ricker, CEO of Hivecell. “By combining forces, Advantech and Hivecell jointly provide customers with a complete edge solution at the data source.”
Hivecell’s EaaS reportedly connects legacy systems to gateways, edge computers, 5G routers, and other IoT devices for scalable data management. By collecting and processing data at the edge, Hivecell says data flow can be improved because useless data is efficiently discarded on site. “Only relevant data is sent back to headquarters and/or the cloud. The result is deployment and management with on-premises computing power for hundreds, or even thousands, of locations,” says Ricker.
IoT gateways act as the bridge between devices and the network, converting physical information into digital data for transmission from the edge. Raw data flows through a gateway at the edge where it is processed by machine learning and other analytics. In the end, only business-relevant data is sent to the cloud.
Advantech products recommended for use with Hivecell’s EaaS, include: • UNO-238: Compact IoT edge computer with
Intel Core i Processor; • UNO-148: High-performance DIN-rail control computer with Intel 11th Gen Tiger Lake
Core i7/i5/i3 CPU; • SKY-640V2: 4U rackmount Intel Xeon scalable GPU server; • MIC-770 V2: Compact fanless system with 10th Gen Intel Xeon/Core i CPU socket.
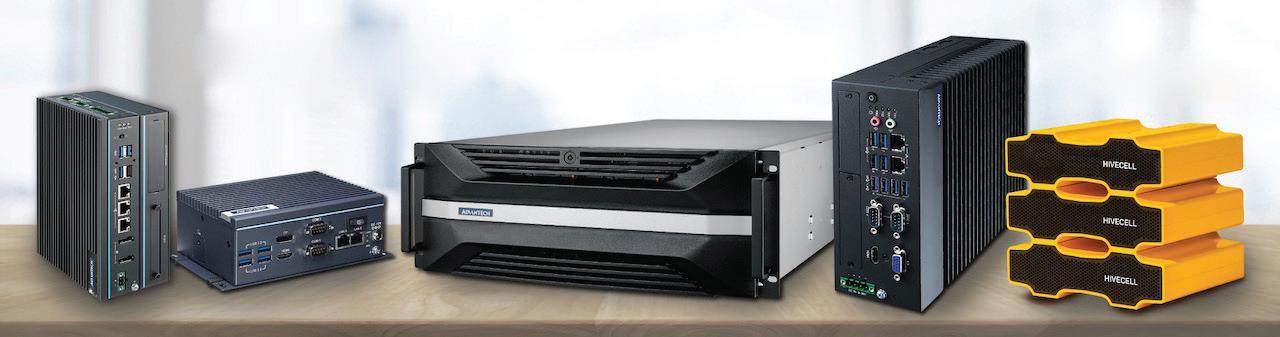
GE Digital Amps Up Asset Performance Management
By Stephanie Neil
Senior Editor, Automation World
The energy industry is well on its way to digital transformation, and GE Digital is positioning itself as a technology supplier that can help accelerate an oil and gas manufacturer’s digital journey as well as their time to value for new applications.
To that end, GE Digital has made three announcements around: a partnership with a 3D digital twin software provider; the new Accelerator product line designed to quickly configure its Asset Performance Management (APM) software; and that GE Digital has achieved Amazon Web Services (AWS) Energy Competency status, which recognizes GE Digital’s ability to help the energy industry prepare for a lower carbon future.
First, GE Digital has formed a partnership with 3D digital twin provider Visionaize that brings high accuracy visualization capabilities to operational use cases as a way to save time, reduce cost, and improve safety, the company said. Visionaize’s V-Suite Starter can be incorporated into GE Digital’s APM Mechanical Integrity software designed to streamline maintenance activities and improve worker efficiency across asset intensive industries.
While industrial companies can choose to review data and information in any number of formats including plant blueprints, piping and instrumentation diagrams (P&ID), and isometrics through CAD/CAM software, V-Suite Starter allows users to view real-time and historical asset data on the 3D model to deliver timely and valuable insights at the point of action. The 3D visualizations of key asset information combine “see it, model it, and understand future behavior.”
Visionaize integrates 3D plant models with APM Mechanical Integrity to provide data-driven visualization of key attributes by color coding the model to filter out noise and focus on what matters most. It dynamically visualizes and contextualizes data for operations and maintenance activities to help assetintensive companies solve challenges associated with downtime, quicker time to resolution, maintenance costs, and workforce productivity, the company said.
In a separate announcement, GE Digital announced the launch of its Accelerator tools which will fast track the time it takes to leverage predictive analytics, asset health and reliability processes, asset strategy optimization, and change management workflows without custom development.
GE Digital’s first set of Accelerators includes an extensive library of predictive analytics, asset management strategies, and standard health and reliability processes. Using advanced prebuilt product configurations, companies can set up enterprise-level asset reliability and performance programs, embedding prioritized actionable information into daily work. In addition, they are designed to scale the power of APM with health monitors, analytics, asset maintenance strategies, and business process workflows.
In addition to GE Digital’s own asset library, the company has partnered with Stork, an asset performance improvement provider, to offer their Asset Strategy Library (ASL,) delivering a collection of pre-defined strategy templates for known failure modes and prescribed mitigating actions for a wide variety of asset types including Balance of Plant (BoP).
“Energy companies have used asset management practices for decades, but today’s operating environment requires that they extend that to even more assets in the plant,” said Tracy Swartzendruber, GE Digital’s VP of marketing for power generation and oil & gas during a press conference. “Accelerators help energy companies expand processes without consuming more time and more resources required on custom configurations.”
Swartzendruber went on to liken Accelerators to the game Minecraft, where players can build and create anything. Over time, to avoid custom coding, the game began to productize different textures and sounds, for example, that could be easily applied. “That’s Accelerators. GE Digital deploys so many APM instances and we keep seeing the same things that people need…why not package these things up? They can still customize it, but we give them the head start.”
Lastly, GE Digital’s AWS Competency status was a result of a rigorous technical validation process, including a customer reference audit, resulting in a demonstration of GE Digital’s deep expertise of AWS to build, implement, and integrate technology—using its APM software for power generation and oil & gas—that transforms complex business and operational systems in a way that can accelerate energy and digital transitions.
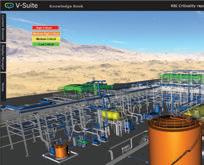

GE Digital's partnership with Visionaize adds 3D digital twin technology to its asset performance portfolio. Source: GE Digital
Read more GE Digital News: Profi cy Operations Hub 2022.
CPG Cobot Use Expected to At Least Double in Next Five Years
By Sean Riley
Senior News Director, PMMI Media Group
According to the “PMMI Business Intelligence Report 2022 Robots and Cobots: An Automated Future,” 84% of consumer packaged goods companies now use robots somewhere on their production lines, and this number is expected to rise to 93% in the next five years. Deployment of collaborative robots, also known as cobots, is also expected to see strong growth, with use more than doubling from 27% this year to 57% in 2027. Respondents to the PMMI research say improvements in robot functionality, such as vision, self-learning, and artificial intelligence are spurring manufacturers to purchase and use more robots in processing and packaging applications.
Processing operations
Cobots have seen their role in processing steadily expand as inclusion of the IP69k harsh environment standard, artificial intelligence, and enhanced robot vision systems become more common and affordable. Adoption in processing has also accelerated with COVID-19 restrictions, particularly in the food industry.
Primary packaging
Robotic capabilities in primary packaging have expanded significantly recently. With the advent of tactile sensors, AI-supported vision, and innovative end of arm tool designs, cobots are finding new roles in primary packaging and expanding their reach into new manufacturing markets.
Secondary packaging
Cobots are playing a key role in improving the efficiency of secondary packaging operations. From secondary packaging material handling to visual inspection, robots are driving new levels of efficiency and speed that help manufacturers manage production costs and increase throughput.
Access the PMMI report on robots and cobots
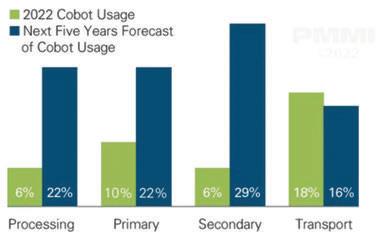
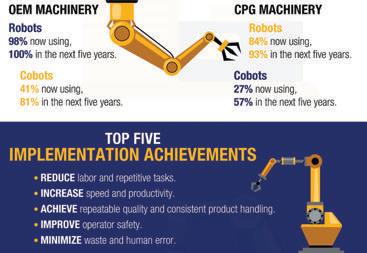
Delphon Puts Robotsas-a-Service to Work
By David Greenfield
Director of Content, Automation World
Through its TouchMark business, Delphon (a Hayward, CA-based manufacturer) provides high quality, precision pad printing services to the medical device and electronics industries. Pad printing is a printing process that can transfer a 2D image onto a 3D object. The company’s cleanroom manufacturing facility enables it to handle prototypes ranging from small clinical trials and engineering lots to large production volumes.
Like most manufacturers today, Delphon has been finding it difficult to find machine operators for its production operations.
“Recruiting operators has been next to impossible. It only got harder once the pandemic hit,” said James Garner, director of TouchMark’s manufacturing operations.
In response, Delphon has been looking to automate various aspects of its production operations for some time now. The problems Delphon encountered in its mission to automate were multiple: the robotics systems the company investigated all cost too much, took too long to install, or delivered too little value.
“TouchMark had considered robotic automation in the past, but the ROI never made sense,” Garner said. “Other cobots (collaborative robots) worked at the same rate as a human operator, needed constant supervision, and came with a big sticker price. Choosing one of these cobots would mean that TouchMark’s labor costs and throughput would have stayed the same, while its capex would have increased.”
Despite its lack of success finding suitable robotic automation technologies for its operations, Delphon continued its search and found the Rapid Machine Operator (RMO) from Rapid Robotics to be different. A key factor for Delphon is that RMOs with built-in computer vision and pre-trained artificial intelligence to operate the kinds of machines TouchMark used could be hired for $2,100 per month.
Garner noted that the RMOs took only a few days at most to set up and needed
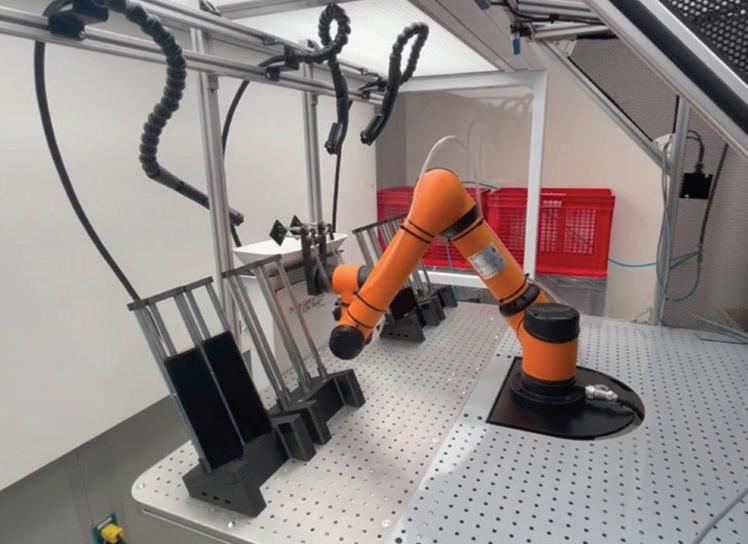

only light supervision from an operator who could work another machine at the same time.
TouchMark put the RMO to work on a task it had been running the same way for 30 years—applying pressure-sensitive adhesive to semiconductor packaging. With the RMO successfully automating this procedure, TouchMark brought in another RMO to work a pad printer alongside the first RMO.
“Production became less expensive and more consistent,” said Garner. “TouchMark’s RMOs worked at the same rate, hour by hour, day by day. That steady pace proved invaluable during the pandemic when other manufacturers were struggling to staff their machines.”
Prior to the RMO deployments, an operator was assigned to each pad printing machine. Now, one employee can supervise both RMOs while operating a third machine at the same time. The other two operators were redeployed elsewhere in TouchMark’s operations . With the two RMOs in place, TouchMark was saving $15,640 per month.
Based on the success of the RMO at TouchMark, Delphon began using the RMO at its Gel-Pak facility, which manufactures containers and films to protect electronic materials and components. Gel-Pak uses the RMO to clean molded parts with an ionized air knife prior to assembly. With two RMOs doing the work of five Gel-Pak operators, the company is saving $20,400 per month, and the operators were redeployed to other activities.
Speaking to the value that robots-as-a-service has brought to Delphon’s operations across two of its divisions, Philip Haseltine, vice president of Delphon’s manufacturing operations, said, “If you don’t have a massive engineering staff and you want to start saving immediately, this is the business model for you.”
Garner added, “We don’t have a ton of engineering resources. We don’t have any robotics engineers or software engineers. For us, the RMO was an easy, quick, and incredibly rewarding entry into the world of robotics.”
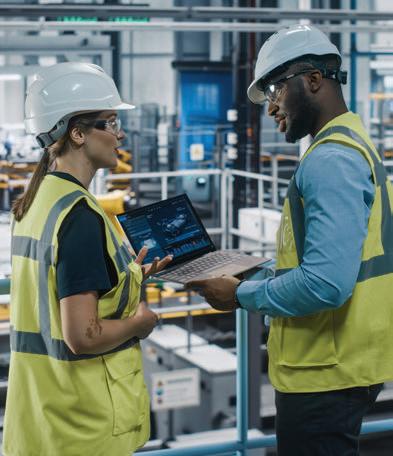
Read more about the robots-as-a-service trend.
We see
new insights into energy consumption supporting environmental sustainability goals.
Manufacturing plants typically lose 30% of compressed air due to pneumatic system leakages. This impacts energy efficiency and environmental sustainability goals. Emerson’s Industrial Internet of Things (IIoT) solutions and analytics software provide actionable insights to reduce waste and optimize the energy consumption of your machines.
Discover how digitally transforming your operations can help meet your sustainability goals:
Visit us at Pack Expo North Hall – Booth N4736