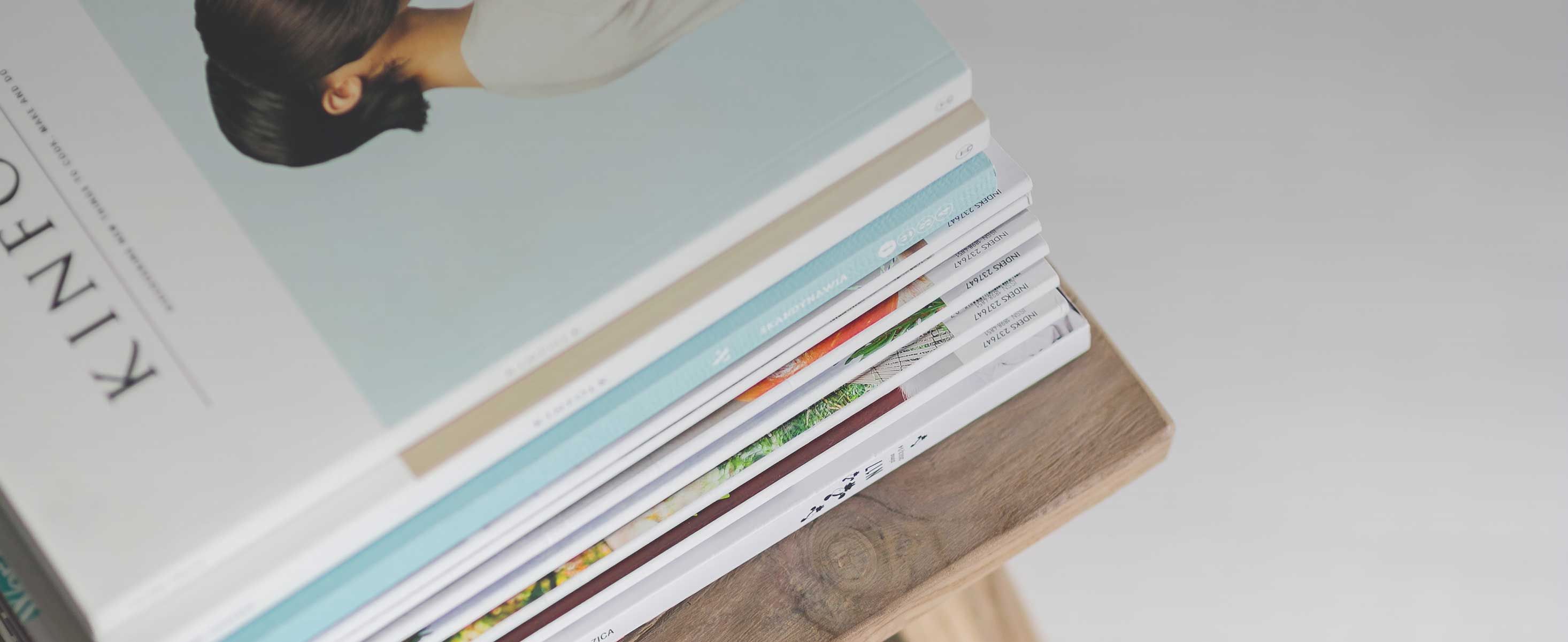
3 minute read
BATCH OF IDEAS
How to Make More Sense Out of Difficult Data
By Stephanie Neil
sneil@automationworld.com sneil@automationworld.com
Senior Editor
Most manufacturers take sustainability efforts seriously, but when the company makes paper, it is more than an honorable act for the environment, it’s a business imperative.
As the only paper mill in Denmark, Skjern Paper, which started production in 1967 with the idea of manufacturing paper exclusively from old newspaper, has had sustainability built-in to its production process from the beginning. Today, the company manufactures 75,000 tons of paper and board products each year from 100% recycled fiber.
The ability to provide high quality and just-in-time delivery to customers requires Skjern to use technology. Paper plants have hundreds of proportional-integral-derivative (PID) control loops that can cause process variations. In addition, quality assurance teams don’t have many real-time ways to measure paper quality, making real-time quality control difficult.
With the goal of reducing quality rejects, Skjern Paper turned to GE Digital’s Proficy CSense, an industrial advanced analytics software package that can predict future asset and process performance using artificial intelligence (AI) and machine learning (ML). What was compelling for Skjern is the software’s ability to do real-time closed loop control actions.
Another aspect that made the software so valuable to Skjern had nothing to do with the technology, but rather the training that GE Digital provided. Understanding that learning and using analytics isn’t easy, GE Digital offers its customers six hours of free consulting to get engineers up to speed on how to use the software.
Looking to reduce quality rejects by 5% as part of its exploration into adanced analytics, Skjern’s work with GE Digital experts enabled the paper mill to capture insights from the initial project and then build models to analyze data and discover quality variations. The company was also able to monitor the health of the PID control loops to reduce process variation and predict product quality in real-time.
“The interesting thing about GE’s consulting is that we make sure the customer doesn’t get stuck in simple things like installation,” said Cobus van Heerden, senior product manager for analytics and machine learning at GE Digital. “We also get to know their teams and what the software was bought for to understand the highest value use case.”
The Skjern team built a model in CSense around a quality parameter related to the paper strength and fiber bond. By examining that data, the paper company was able to discover possible causes of errors in the production line. For example, when producing paper, Skjern adds dewatering chemicals. With the help of CSense, they found that they were producing scrap by adding too much chemical to the pulp mix.
In the process of working with Skjern, GE Digital found out that it needed to add more functionality to CSense based on feedback from the users. This has resulted in the roll out of Proficy CSense 8.5, which adds the ability for manufacturers to improve equipment operations by up to 10% through mathematical algorithms that recommend the best tuning parameters or configuration settings to optimize real-time, closed-loop control actions. While CSense has always been able to monitor PID control loops, the new tuning assistant can calculate recommended PID loop tuning settings. In addition, there is a system identification assistant to estimate process transfer function models from historical data for process simulation or control optimization.
CSense 8.5 also adds support for the OPC UA interface to connect with other industrial systems. The software is also now available in Japanese, Chinese, Russian, and French.
It’s also easier to use, van Heerden said. “It provides an intuitive drag-and-drop environment. No programming skills needed.”
Skjern Paper has yet to upgrade to the new version of CSense, but the company is realizing a quick return on its initial investment. Erik Møller, Skjern Paper’s technical manager said, “The more we use the Proficy CSense software, the more ways we keep finding to apply it. And with AI, we can take production to the next level.”