
9 minute read
Member News
by Pedemex BV
CPP advances with complex river-crossing pipeline project in
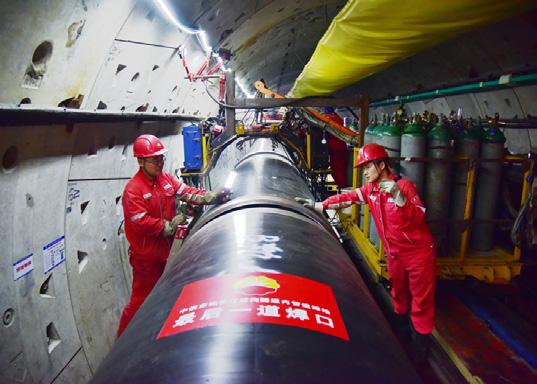
China Petroleum Pipeline Engineering Co., Ltd. (CPP) is constructing the Yangtze River crossing for the China-Russia East Route natural gas pipeline in China. Located 70 metres
beneath the Yangtze River, this project is the world’s most complex river-crossing pipeline installation due to its length, depth, and challenging conditions. CPP uses its proprietary CPP900 fully automatic welding equipment to lay three natural gas pipelines, each with a diameter of 56 inches and a wall thickness of 32.1 millimetres, made from X80M high-grade steel, in a “T” shape within a shield tunnel. The tunnel has an internal diameter of 6.8 metres and stretches horizontally for 10,226 metres. This marks the first use of fully automatic welding and foam concrete filling technology in a shield tunnel in China.
For this project, CPP has introduced innovations such as gantry cranes for tunnel use, a ground-based assembly line system, and high-precision pipe bending machines. Over 50 specialised pieces of equipment have been custom-made. Having completed the pipeline welding inside the tunnel, the team is now progressing with foam concrete filling and pipeline installation within the vertical shaft. The project is expected to be production-ready by the end of November
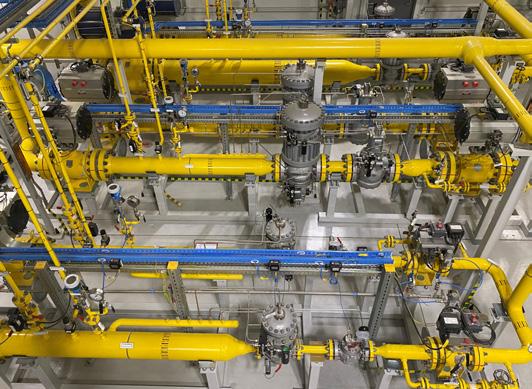
internal distribution pipelines for turbines and boilers, engineering and construction of a gas treatment station (52.000ncmh) and commissioning of the installation. The EU awarded subsidies for the project. The investor was Zespół Elektrociepłowni Wrocławskich Kogeneracja, owned by PGE Energia Ciepła of the PGE Group.
In March 2023, Gascontrol Polska completed a related project, the “Connection of the CHP Czechnica-2.” The scope of works included the construction of the DN500 MOP84 pipeline and gas distribution station with a capacity of 200.000ncmh. The investment was made by the Polish Gas Transmission Operator GAZ-SYSTEM S.A.
Goriziane unveils innovative Electric Beveling Machine
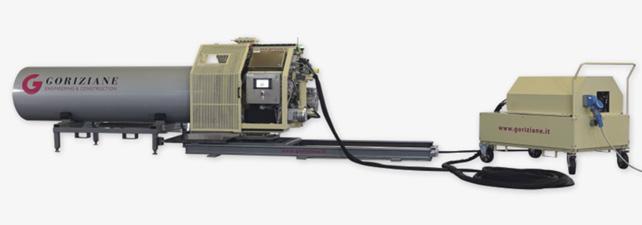
Goriziane E&C S.p.A., a leader in industrial machinery, has unveiled its innovative Electric Beveling Machine, designed to enhance efficiency and precision in metalworking tasks. This state-of-the-art equipment caters to the needs of industries requiring meticulous edge preparation for welding, such as pipeline manufacturing. The Electric Beveling Machine is equipped with a powerful motor and advanced control systems, allowing for smooth and consistent bevelling across various metal types and thicknesses.
One of its standout features is its versatility; it can handle straight, curved, and irregular surfaces, ensuring highquality bevels with minimal effort. Additionally, the machine offers adjustable bevel angles, providing flexibility to meet
specific project requirements. Ergonomically designed for user convenience, the machine ensures operator safety and comfort during prolonged use. Its robust construction guarantees durability and long-term reliability, reducing downtime and maintenance costs. The intuitive interface simplifies operation, making it accessible even for less experienced operators. Goriziane’s commitment to innovation and quality is evident in the Electric Beveling Machine, which not only enhances productivity but also maintains high standards of precision and safety. As industries continue to evolve, this machine represents a significant advancement in bevelling technology, underscoring Goriziane’s role as a key player in the industrial machinery market.
Hölscher Wasserbau’s key role in Germany’s energy transition
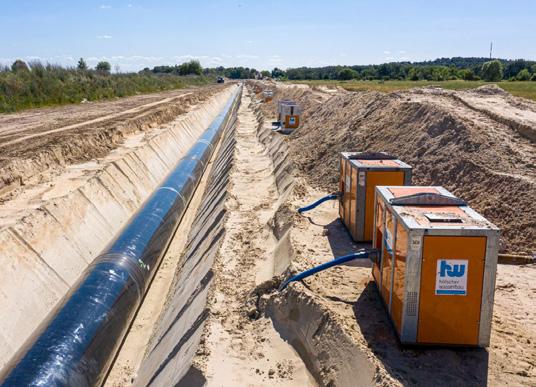
Germany is currently implementing numerous infrastructure projects as part of its energy transition to efficiently distribute renewable energy across the country. Key projects include the BalWin1 and BalWin2 high-voltage direct current (HVDC) lines, which connect offshore wind farms in the North Sea to the onshore transmission network. These projects are crucial for replacing conventional power plants and transporting wind power to grid connection points.
Hölscher Wasserbau is responsible for groundwater management in these projects, which is essential for the underground installation of the cables. By lowering the groundwater level, the soil remains dry and stable during construction. The extracted groundwater is treated and then returned to the natural environment in an environmentally friendly manner. Additionally, Hölscher Wasserbau manages the groundwater for the A-Nord HVDC project, which will transport two gigawatts of wind energy from the north to consumption centres in the west and south. This ensures the safe underground installation
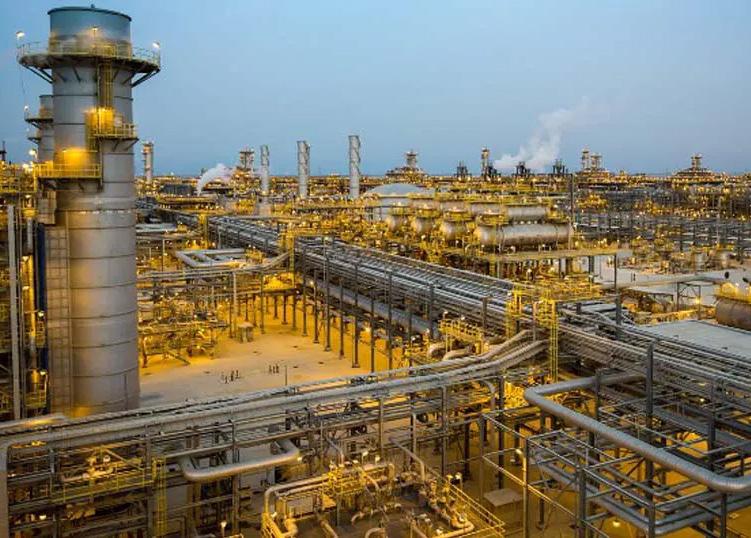
per day, in line with the company’s strategy to raise gas production by more than 60% by 2030, compared to 2021 levels. The expansion, which is expected to be completed by November 2027, is also expected to add an additional 2,300 metric tons per day to sulfur production.Nesma & Partners was awarded Package 6 for the upstream/downstream pipelines, which includes over 150 km of pipeline works.
Seal for Life Industries’ Covalence-Dirax coating system used in India
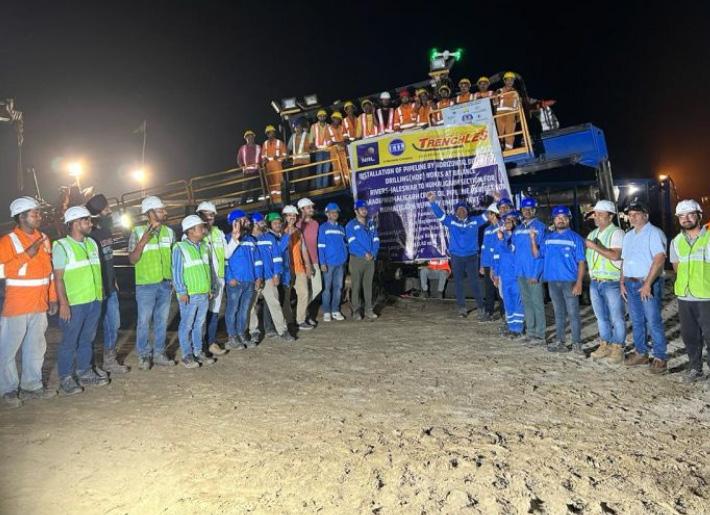
Seal For Life Industries recent project used the fiberglass reinforced Covalence-Dirax field joint coating system for the girth weld protection of 3LPE coated pipelines. The pipelines were laid by HDD (Horizontal Directional Drilling) methodology in the prestigious Ganga river crossing project.
The project is part of the Numaligarh Refinery Limited’s Crude Oil Pipeline project. Engineers India Limited (EIL) was hired as consultant. The Ganga river crossing, in the State of Bihar in India, has become the longest HDD in the country. The HDD project has been executed by Trenchless Engineering Services, one of the premiere HDD contractors in India. The entire project was accomplished within 76 days, 15 days ahead of the planned schedule.
The Covalence-Dirax field joint coating system has been protecting the girth weld from corrosion in India for HDD pipelines for more than 36 years.
Tekfen Construction appoints Serhat Pütürgeli as President
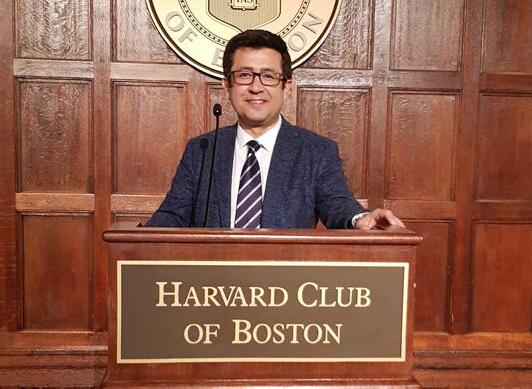
Serhat Pütürgeli, who has held various positions such as Project Manager, Regional Director, and Vice President at Tekfen Construction since 2003, was appointed as President as of 1 July 2024. Tekfen Construction, established in 1956, is an international contractor with major accomplishments in Turkey, the Middle East, North Africa, Caucasia, Central Asia, East-Central Europe. Its wide span of activities ranges from heavy civil works to refineries and petrochemical plants, including satellite towns, major industrial processing plants, pipelines and marine structures, power plants, electrical and communication works.
S.p.A. presents its new splash zone coating ENVIRAWRAP
The marine environment is known as a harsh and extremely corrosive environment due to continuous contact with highly aerated sea water and the erosive effects of spray, waves and tidal actions, which destroy any protective film that might be formed on the piles’ surface. In order to perform the best possible protection of marine infrastructures, TESI acquired the original ENVIRAWRAP brand from Strange Corrosion, LLC in 2023 and developed a new inducedtension polymer wrap, specifically designed to provide an easily installed retrofit encapsulation system for the cladding of vertical risers and piles in the splash zone.
ENVIRAWRAP’s unique features include easy and fast onepiece installation: no multi-layer or multi-phase procedure is required, and few tools are needed. Long term integrity: the wrap’s elastic memory properties create an inward force when mechanically tensioned around the pile. This

hoop tension force causes the organic corrosion inhibitor - factory blended into the thixotropic gel - to exude into the surface irregularities, providing both active and passive protection of the substrate. No ‘bare-metal’ preparation is required, only the removal of loose material and marine growth is needed. Easy substrate inspection: customers simply loosen bolts and partially open the one-piece wrap. After substrate inspection, users apply additional gel (if required) and reposition the wrap and tighten the bolts. The expected lifespan of the coating is over 20 years.
Vacuworx lifting systems used on pipeline project in Chile
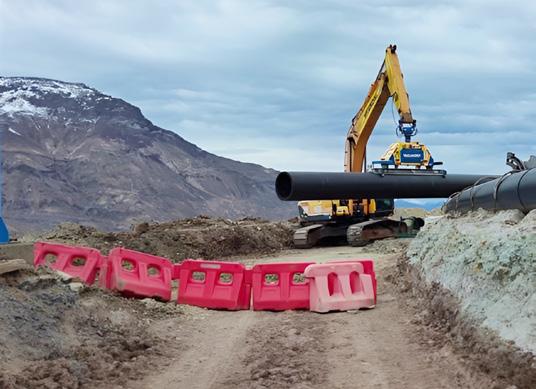
Recently, Vacuworx equipment was employed on a significant water and mine tailings pipeline project in the commune of Machalí, situated in the Libertador General Bernardo O’Higgins Region, approximately 50 km from Rancagua, Chile. This project required handling of 630 mm high-density polyethylene (HDPE) pipes, known for their durability and flexibility.
To manage these large pipes effectively, the project utilised a variety of Vacuworx vacuum lifting systems, including one RC10, one RC16, and three RC12 units,
which were paired with excavators. The vacuum lifting equipment was rented through MCI Thermofusion, a Vacuworx equipment dealer located in South America. The RC10 unit was primarily used for loading and unloading pipes in the storage yard, ensuring efficient and safe movement of materials. The RC12 and RC16 units were used for the installation phase, facilitating the precise placement of the HDPE pipes. The RC Series lifters operated without issue, even at the high elevation of the mountainous Chilean landscape.
Winn & Coales (Denso) Ltd. supplies innovative FJC system for offshore pipelay project
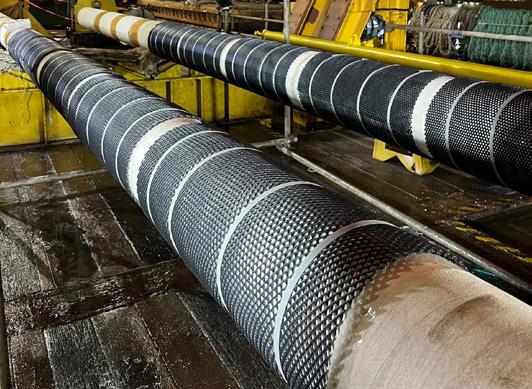
In June 2024, a Malaysia-based oil and gas company embarked on an ambitious offshore pipelay campaign aimed at developing three offshore gas fields in Southeast Asia. The project required the protection of 3,300 field joints on two new sour-rated carbon steel pipelines: an 18 km stretch of Ø10” and a 22 km stretch of Ø12”, both operating at temperatures of 109 °. The client’s objective was to find a high-temperature, cold-applied visco-elastic field joint coating system that complied with the international standard ISO 21809-3:2016. After a successful campaign featuring multiple rounds of rigorous testing and client approvals, the project marked the inaugural use of Denso’s Viscotaq™ Offshore Field Joint Coating (OFJC) system.
Exceeding all minimum requirements set by the ISO 21809-3 standard, the Viscotaq OFJC system was selected for its capacity to handle a maximum pipeline service temperature of 125°; enable application of the entire system in under 4 minutes; and achieve an average Shore 45D hardness within 5 minutes. This robust system, manufactured and supplied by Winn & Coales (Denso) Ltd, aided the contractor in finishing three days ahead of schedule and realising savings of over USD 1 million, showcasing the technical capabilities and extraordinary potential of cold-applied FJC systems in the offshore pipelay industry.