
9 minute read
Optimising revenues
The world’s first offshore wind farm was commissioned in 1991.
This Vindeby Offshore project, created by a group of Danish developers, consisted of eleven turbines that together generated 5MW. More than three decades later, a lot has changed.
The first offshore wind farms were constructed using technology with only slight adaptations compared to onshore wind turbines. In time, the turbines were designed, specifically for the harsh circumstances at sea. Also, at sea with no noise restrictions and plenty of room, operators started to look for larger turbines to reduce the cost of offshore power generation. At the beginning of the new century, the first 2MW offshore wind turbines were installed and increasingly more countries started to develop plans for the construction of offshore wind farms in order to reach their sustainability goals. Together with these plans, the industry continuously invested in further improving the efficiency and effectivity of the offshore turbines, resulting in turbines growing both in size as in power generation.
A handful
In Europe, currently the largest market except for China, the market for offshore turbines only knows a handful of companies that develop and produce offshore wind turbine generators. In the last few years, they together succeeded in further improving the power generation of offshore wind turbines. In February 2018, GE Renewable Energy announced their Haliade-X platform nameplated 12MW, and Vestas introduced the V164 10MW turbine. Soon after that, GE Renewable Energy and Siemens Gamesa launched their 14MW turbines, where the Siemens 14MW, making use of the Power Boost option, can even produce 15MW. Last year, Vestas introduced its 15MW prototype and the question arises where this race for power will end.
Pioneer
According to Morten Rasmussen, Offshore CTO at Siemens Gamesa, this company has been operating in the offshore wind market since the very beginning. “For us, like many other companies in the offshore wind industry, it all started onshore with the supply of turbines for onshore wind farms, but as the supplier for the Vindeby project, we established ourselves as the offshore wind pioneer. Today, we estimate that over 50% of all turbines installed offshore, excluding China, are made by us.” He continues, “One of the most important differences between onshore and offshore wind is that installation onshore is much easier and therefore less expensive, for example because you only need a relatively simple concrete foundation, and no long-distance cabling is necessary to connect the onshore turbines to the grid, as onshore wind farms are usually close to the existing grid. On the other hand, the size of onshore turbines can be limited due to infrastructure and logistics, whereas offshore turbines have more freedom to increase in size.”
These two aforementioned differences also play a role in the upscaling of offshore wind farms and turbines. “Constructing the offshore wind power plants of today,” Mr Rasmussen says, “is expensive as they are huge projects, providing electricity to hundreds of thousands of households. They provide industrial power generation at price levels that are fully competitive with fossil fuel-based power plants. The most obvious solution to reduce the cost of electricity provided from offshore wind farms is to build farms with large and more powerful turbines. We are driven to develop more and more powerful turbines both by demand from the market demanding larger turbines and by our goal to remain ahead of competition.”
No technical limitations
The question arises where this upscaling of turbines will end. There are currently installation vessels under construction that will be ready for the installation of 20MW turbines, so contractors apparently expect larger turbines to be developed soon. According to Mr Rasmussen, the upscaling will not be hindered by technical limitations. “No one really knows where things will end as technically, there are no restrictions”, he says. “However, I think that it is important to listen to the market instead
of just looking at what is technically feasible. What do operators need? Look for example at the aircraft industry and the long-term lack of commercial success of the Airbus A-380. Technically it is an absolute masterpiece, though in the end it was a commercial disappointment, as the market was not ready for such a large aircraft.”
“This is one of the reasons why, in the development for more power and larger turbines, Siemens Gamesa has chosen a sound, stepwise approach to growth by taking just small steps at a time”, Apart from creating larger power generation, the industry has also been seeking other improvements. “While sizes and capacity are exponentially larger, the core concept “of the offshore wind turbine today is the same as it was for the Vindeby turbine”, Mr Rasmussen explains. “Naturally, we have always been looking for improvements, for example in the field of aerodynamics to improve the efficiency of the rotor blades. And today, our turbines use our patented Direct Drive technology instead of geared solutions, which requires fewer components, and this saves money on construction and maintenance.”
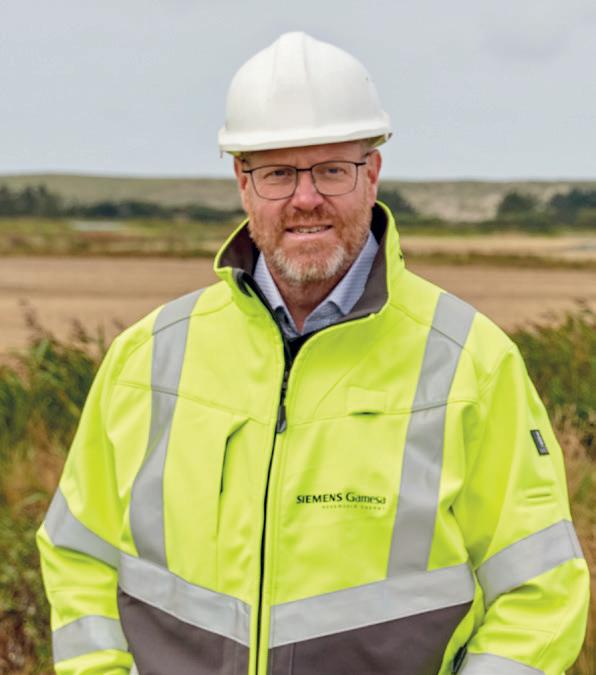
Morten Rasmussen, Offshore CTO at Siemens Gamesa. Image courtesy of Siemens Gamesa.
Catapulted
GE Renewable Energy entered the onshore wind business in 2002 and with the acquisition of the power and grid business of Alstom in 2015, the company also became involved in offshore wind. With this acquisition, the company immediately gained a position in a highly competitive market. However, according to Vincent Schellings, Chief Technology Officer of GE’s offshore wind business, more was needed to keep a strong position amongst the market leaders.

Vincent Schelling is Chief Technology Officer of GE’s offshore wind business. Image courtesy of GE Renewable Energy.
“When we took over the Alstom power business, their largest offshore wind turbine generated 6MW and although the acquisition catapulted us into the market, we were convinced that we had to come up with something unique to help our customers drive down the cost of electricity. The first question our engineers were asked was to develop a rotor with a diameter of at least 220m, which was at that time a world-leading size. As bigger blades only make sense with bigger power generators, their next challenge was to develop a bigger power generator, which resulted in the 12MW Haliade-X. With the bigger turbines, we could meet demand from the operators that were looking for ways to reduce the cost of electricity generated offshore. With bigger turbines, fewer turbines need to be installed per wind farm area, and fewer turbines also mean fewer subsea cables and less maintenance.” Rising costs Today, the Haliade-X turbine has been expanded to 14MW.
“Step by step,” Mr Schellings elaborates, “we increased the capacity of the Haliade-X prototype. It was certified in 2020 by DNV at 12MW and today it is also certified for up to 13.6MW, with the current prototype” running at 14MW and on its way to certification. The Haliade-X is therefore ready for the market, and we already have 7.4GW of customer commitments for this turbine. The first 14MW orders are noted, and production will start in 2023 for the Dogger Bank C offshore wind farm.” Mr Schellings admits that at some point the increase of power and turbine size might reach its limits. “Technically, larger turbines have no restrictions, and a decade ago I would not have thought that today’s offshore turbines would be possible. The aim of upscaling turbines is to reduce the cost of electricity.
However, without innovation at some point, the incremental cost of a larger turbine will exceed the incremental energy production, and hence drive the cost of electricity in the wrong direction. The cost here includes the turbine and the construction, as bigger turbines not only require more steel for the foundations and towers, but also bigger vessels for transport, larger cranes for installing, as well as larger marshalling yards. Logistical costs will increase, too. For this reason, GE Renewable Energy already has factories supporting its offshore business in port areas.”
Although upscaling might come to a halt someday, companies will keep on innovating to reduce costs. Mr Schellings explains, “One of the recent developments we think is worthwhile is 3D printing. Not necessary to produce components, but for example for the moulds needed to construct castings for turbine parts. The moulds presently require a lot of expensive manual labour, and a lot can be gained by 3D printing. Another aspect to mention in this matter is our Stay Ashore project with the Offshore Renewable Energy Catapult in the UK. This R&D project aims to find ways to reduce the time offshore for planned and unplanned maintenance. With this project, we focus on reliability of design, on how to make operations at sea more remote, and how to use robots in turbine maintenance.”

GE Renewable Energy’s Haliade-X prototype has a capacity of 14MW and is ready for commercialisation. Image courtesy of GE Renewable Energy.
Continue to improve
In its Global Offshore Wind Report 2021, the Global Wind Energy Council predicts a total added capacity of offshore wind between 2021 and 2030 of 102.6GW. This figure shows the potential of this renewable source of energy for the industry.
Throughout these years, companies will continue to improve the entire supply chain in order to make the construction, installation, operations, and maintenance more efficient and cost effective. With this in mind, for the time being, the upscaling of turbines will have no technical limitations, but from a financial point of view, it is good to face reality. And we should not forget that apart from upscaling, there are more options for optimising the revenues from offshore wind.
Source: Yellow & Finch Publishers
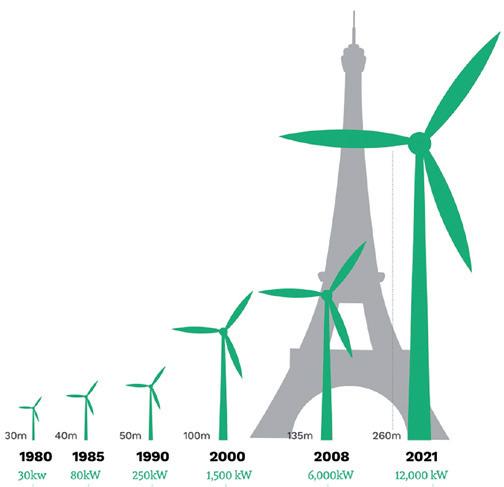
Three decades later, a lot has changed. Image courtesy of oneworld.nl.