
4 minute read
Technology Advancements in Injection Moulding Machines

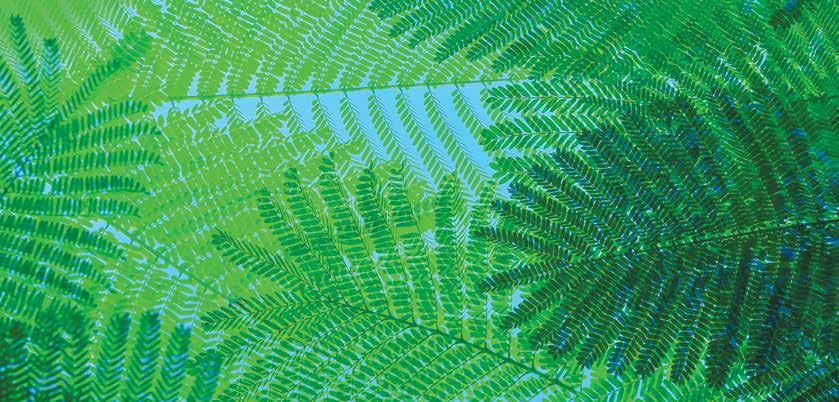
Advertisement
Technology Advancements
in Injection Moulding Machines
Plastics are here to stay and so is the injection moulding technology. With plastics being the most comfortable and convenient material to use for mankind and with large strides being made in the science of plastics, coupled with the advances in injection moulding machines, we can safely assume enhanced processor delight.
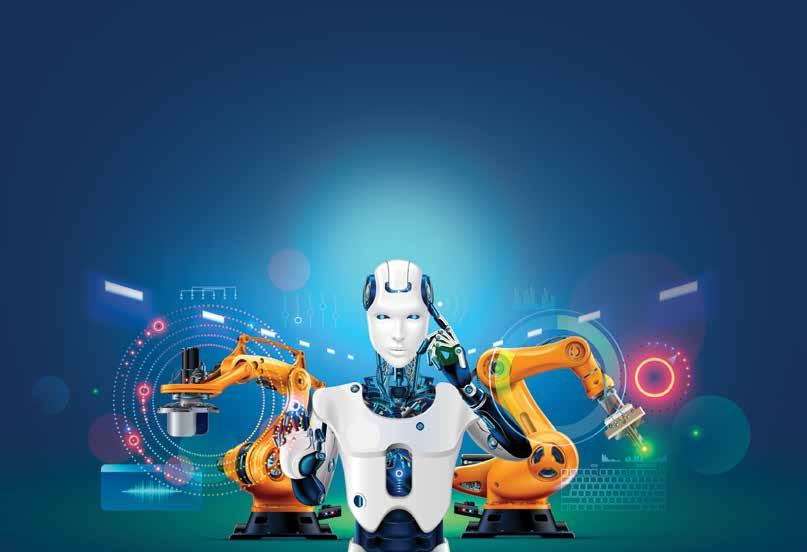
P Kailas
(Retd.) Managing Director, Shibaura Machine, Chennai Injection moulding is a process used for manufacturing various mechanical components. The versatility of this method enables the high quality, low cost and rapid manufacturing of plastic parts. Although injection moulding machines are a mature industry today all over the world, including India, they are expected to grow at an impressive average annual growth rate of 8% to 15% till 2030. However, new manufacturing technologies emerging, like 3D printing, could be a threat to injection moulding machines and may hinder its growth if 3D printing is successful in the future for cost-effectiveness in mass production.
In particular, now that keywords such as SDGs, CO2 reduction and carbon neutral Plastic injection moulding process are being called for, I think that dates back to the dedicated moulding machines for late 19th century. environment-friendly materials (biodegradable plastics) are expected. The 1870’s gave birth to the practice of plastic injection moulding. Better plastics and better processes offered manufacturers a new level of customisation and accuracy, allowing them to produce parts to tight specifications for a wide variety of applications. Manufacturing was forever changed in 1946, when an American inventor James Watson Hendry built the first screw injection machine. This design provided much greater control over the speed of the plastics injection. It also significantly improved the quality of finished parts. James Watson Hendry’s machine allowed materials to be mixed prior to being injected, like blending coloured, regrind and virgin plastics. It is important to note that almost all injection moulding machines of today are screw injection moulding machines.
A Healthy Industry
No technology is static in injection moulding machines. Constant improvements are being made to guarantee that injection moulding remains a viable production technique. The injection moulding industry has never been healthier despite competition from new technologies. New changes will ensure that injection moulding remains a viable and productive industry for years to come. The future of plastic injection moulding is bright and thanks to the advances in machine technology and development of better materials, important shifts within the plastics industry are already occurring and shaping the future of plastic parts manufacturing.
Let’s Analyse...
l Development of an all-electric machine is being projected as a technologically advanced solution over the hydraulic machine. However, at present, it is cost-prohibitive for customers to shift to an all-electric machine, owing to larger sized parts. Therefore, all-electric machines cannot replace hydraulic machines for all applications. Hydraulic machines contribute to nearly 90% of the market demand in India.
l Development of improved, lightweight materials and automated systems are reducing costs and streamlining processes.
l Development of customisation features is allowing manufacturers to use precision technology to create quality pieces to exact specifications.
l Increased awareness of climate change and other environmental factors will continue to drive demand for more eco-friendly materials, such as recycled, reclaimed and renewable plastics.
The Future Will Be Focused on High Productivity
Today, all companies are strongly focusing on higher productivity from injection machines. By using multi-cavity moulds, it is now possible to make many products within a few seconds. Productivity will further progress with system engineering and IoT solutions. System engineering here refers to the concept of a ‘total solution provider’ approach and we can make the automatic product processes for inspection, assembly, painting, stocking in box etc.
By connecting all the processes through IoT, it will be possible to achieve flexible production control, self-tuning for zero defect and self-diagnosis for zero downtime. Manufacturers are attempting to offer articulated robots and SCARA robots that can be entrusted with the post-processes such as finishing, assembly and more.
In future, customers will be looking for internetbased solutions, like IoT, which are necessary to warn in advance about production disturbances and solutions that support them, bringing them more confidence. This technology significantly reduces downtime by combining the self-diagnosis function and failure prediction function. The ultimate goal is to aim for full automation and unmanned factories.
Computerising the Injection Moulding Process
One of the most important improvements to the injection moulding industry is the advent of the computerised injection mould. This allows the moulding process to be fully automated. The injection machine has sensors that allow
To know more, please subscribe to Polymers Communiqué at subscriptions@polymerscommunique.com

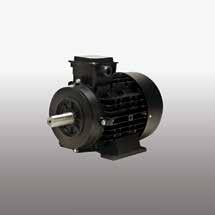
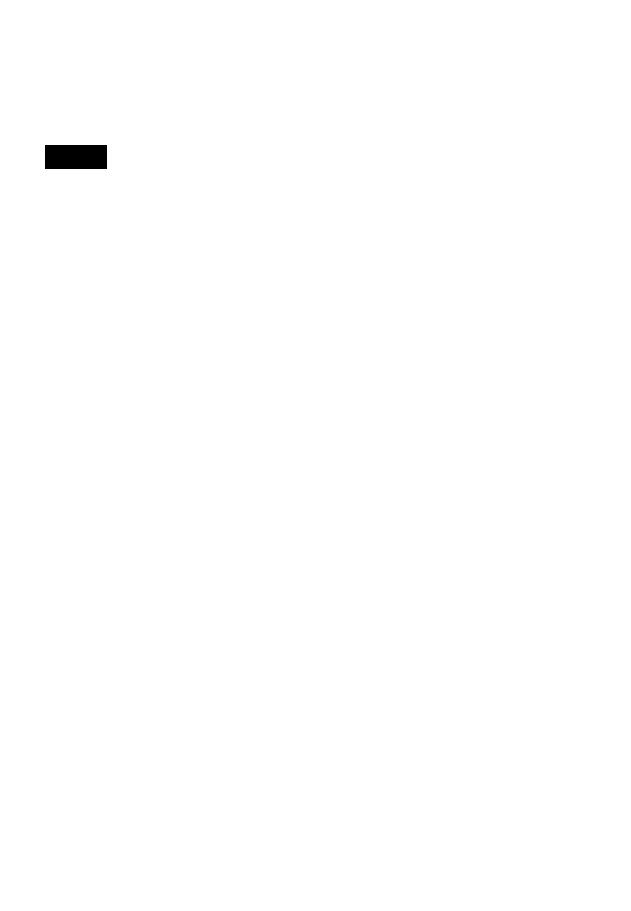
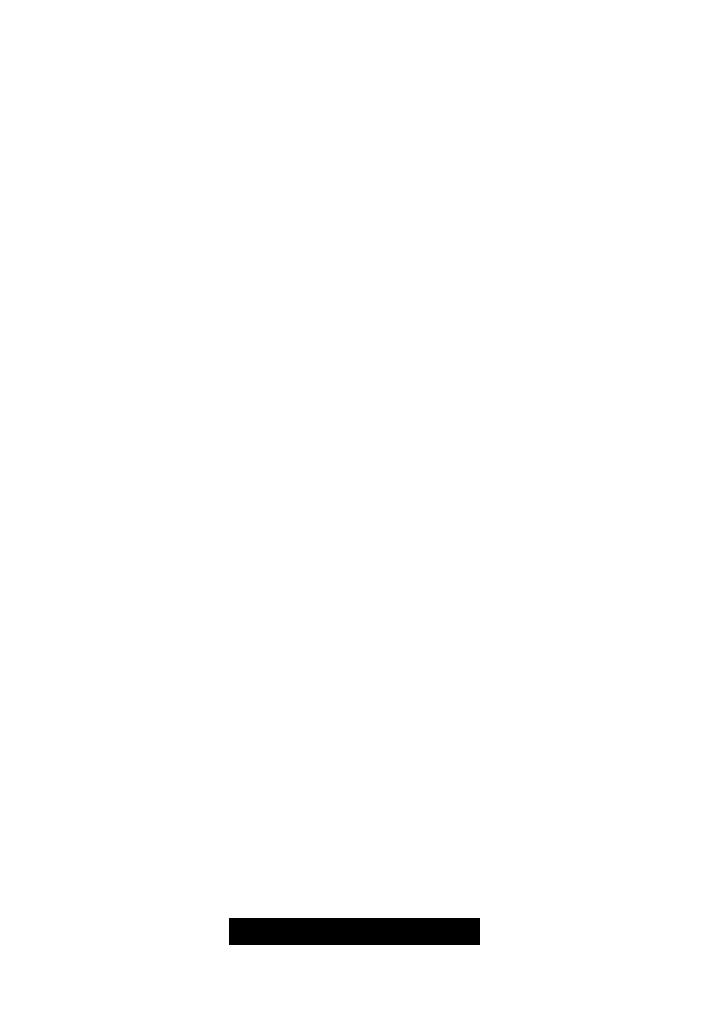
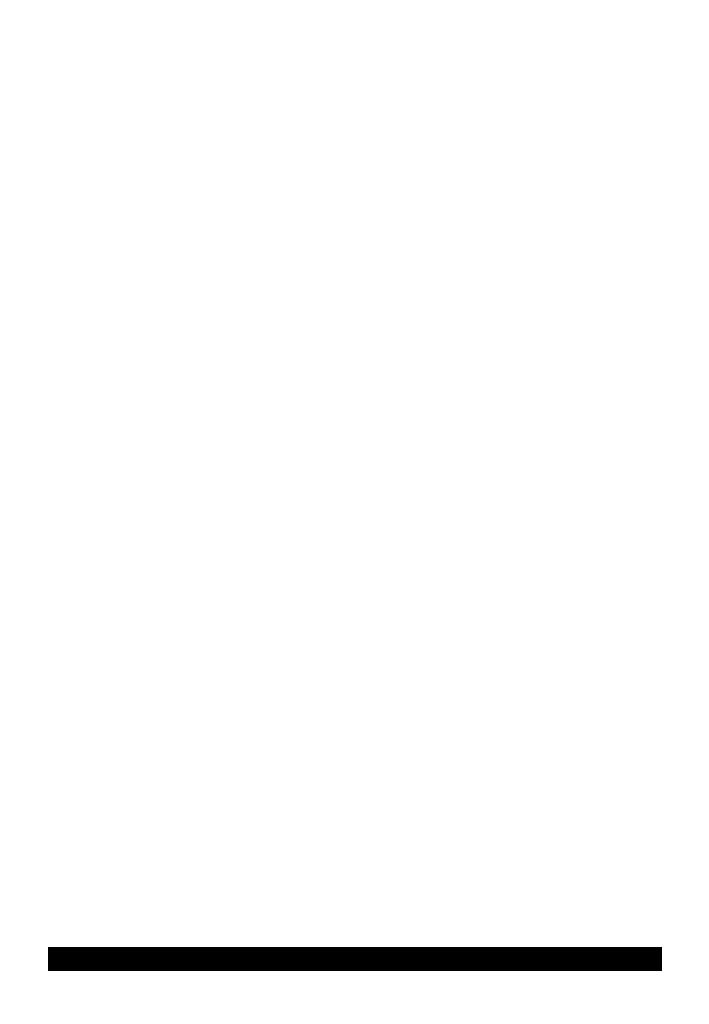
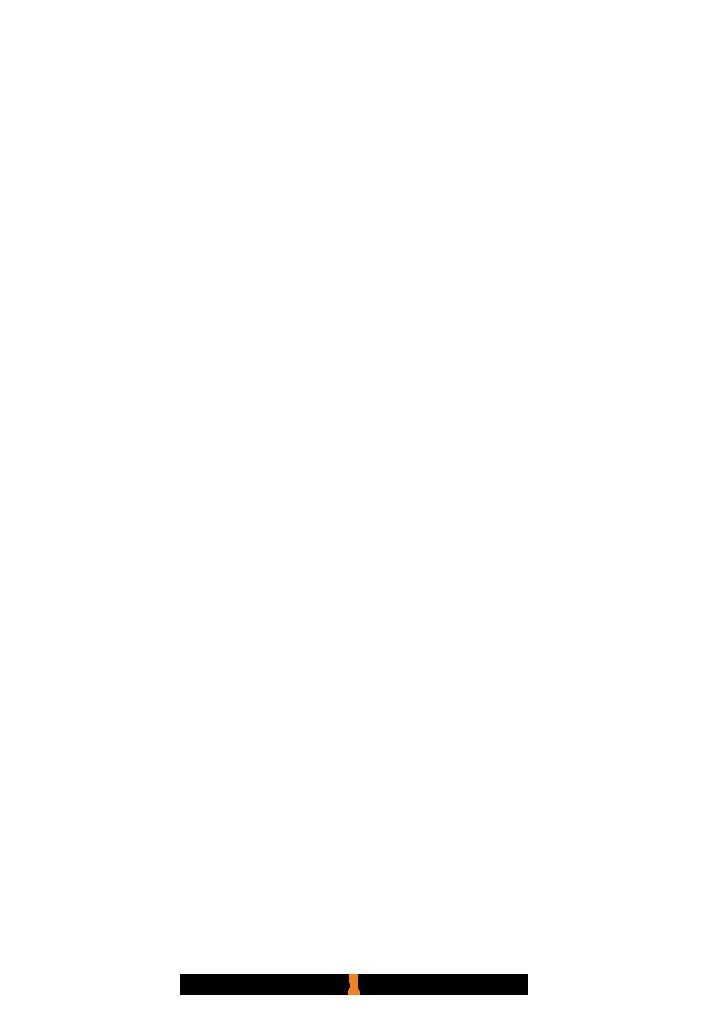