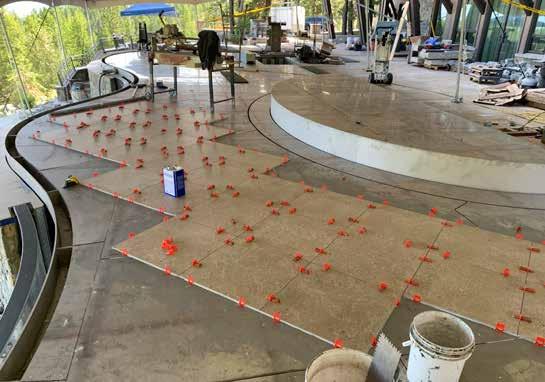
3 minute read
What Were The Builders Thinking ON THIS MOVABLE FLOOR?
BY PAOLO BENEDETTI
It started with a phone call from the owner’s personal assistant. They had movable pool floors in the pool and spa that didn’t operate properly. They wondered if I’d fly up to Whitefish, MT, and have a look-see at their problems.
Upon my arrival, I was met with an odd home-brew moving floor system. In an attempt to reinvent the wheel, the pool builder tried to create his own moving floor systems. The premise was that ballast tanks would be filled with water to lower the floor and be filled with air to raise it. In theory, it may have worked, but as with any unproved and untested design, there are always kinks. Testing theories on a wealthy client and working out the kinks on a multi-million dollar pool project, is never the place to learn.
To begin with, the structure was fabricated out of aluminum. Anyone who’s spent time around chlorinated swimming pools knows that aluminum rapidly decays in salt or chlorinated water. The ballast tanks did not have any bulkheads, so the water sloshed from end to end. This caused the floor to list to one side or end, binding it within the pool walls. You can imagine a multi-ton structure wedged within the pool walls. The deck of the floors were finished in Ipe, a hard exotic hardwood. However, after submersion in water, the wood becomes gray, slimy, and slippery.
To make matters worse, the builder failed to recess the incandescent lights and wall fittings. So the shifting floor structure would sheer off the glass lenses and fittings. In a futile attempt to keep the multiton structure aligned, the builder cut guide tracks into the walls and installed roller wheels. The forces at play here grossly exceeded the bolt-on wheel assemblies.



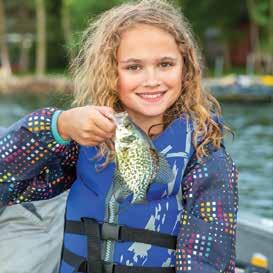


The moving floor in the spa was another disaster. The mechanism was a scissors lift, driven by a hydraulic ram. The builder sourced his hydraulic ram from a local tractor supply store. Over a few quick months, the leaking ram created an oil slick atop the spa. Needless to say, the cast iron ram began to corrode within the chlorinated water.
Once I began to evaluate the hydraulics, electrical, and moving floor systems, it became apparent that the entire project would require a substantial renovation in order to be safe, functional, and code compliant.
I partnered with a local contractor, Shawn Hossack of Panorama Builders. Together we came up with a plan to remove the dangerous floor system and install a new fully proven and engineered system. Though we obtained bids from a number of manufacturers, we settled on systems from Hydrofloors - Twinscape Group. Their technical support and proven track record made the client’s choice simple.
The interior of the pool & spa was determined to be not completely plumb and true. The only means to correct these deviations would be to render them with mortar and tile them. First, the failing Eco-Finish would have to be removed from the walls, the walls roughened, and prepared for waterproofing
To get the exact contours from which Twinscape could begin fabrication, the crews at Panorama tiled the top 3 feet of the pool in order to generate a 3-D model of the interior.
Since the walls are supposed to be perfectly vertical, these 3 feet would be a representation of the entire pool depth. From this model, Twinscape was able to begin fabrication, while progress was being made on tiling the pool.
The spa wasn’t quite deep enough to accommodate a properly designed scissors lift. We remedied this by raising the spa walls 18 inches and replumbing the jets. Once the concrete had cured, the tiling of the spa began in parallel with the pool.
During demolition, we discovered many electrical and bonding deficiencies. The incandescent lighting was converted to strip lights from Hydrolume and proper j-boxes and conduits were installed.
The hydraulics and mechanical systems were corrected to the best possible conditions. Some pumps were eliminated and their pipes repurposed in order to reduce the line velocities on the remaining pumps. Some drains were converted to returns and unblockable drains and sump were installed.
To eliminate the fall hazard over the vanishing edge, we partnered with Reynolds Polymers to fabricate and install an acrylic railing system. The panels were set into a channel within the floor. So, regardless of the height of the floor within the pool, there will always be a railing of sufficient height to protect pedestrians and bathers.
All in all, the repairs to the project took almost 20 months. The ensuing lawsuit resulted in a jury trial and a judgment of $4,750,000 – to date, the nation’s largest judgment in a residential pool construction defect case.
Read the entire article...