
2 minute read
How volumetric manufactured buildings meet Part L requirements
Developers face significant changes, with major steps taking place in the government’s drive to become carbon neutral. Richard Hipkiss, development director of the Modular and Portable Building Association (MPBA) considers the significant role volumetric modular technology can play in achieving new building regulations.
[PAVING THE ROAD to net zero targets and the nationwide commitment to create a cleaner and greener built environment, the new updates to Part L of the Building Regulations will have a big impact on the construction industry. The new regulations came into place in England on 15 June last year in the biggest change to building regulations since 2006, while Scotland can expect to see similar changes implemented.
There are now higher performance targets, CO2 emissions are reduced by 31% for dwellings and 27% for other buildings, and a new emphasis has been placed on low-carbon heating systems. Part L sets out the rules that homebuilders must abide by, while also setting out guidelines for the efficient use of fuel and power in new buildings, outlining what materials can be specified and the correct procedures.
Homebuilders will face a range of changes, including how a property is insulated as well as in relation to heat pumps and solar panels. The regulation changes also apply to non-domestic developments.
The changes continue to broadly follow a ‘fabric first’ approach, requiring lower U-values than previous versions of the regulations, while also incorporating renewable technology. In all new domestic builds the new U-value for walls will be 0.18 W/m2, 1.4 for windows and rooflights and 1.4 for doors. In non-domestic builds there is a lowered U-value of 0.26 for walls and the majority of windows and curtain walling must achieve 1.6 W/m2 .
Since the government amended the Climate Change Act in 2019 to commit the UK to achieving net zero carbon emissions by 2050, the construction industry has been confronted with the need to decarbonise. As an industry association it is our mission to demonstrate how the route to 2050 could follow a number of different paths. We intend to achieve this by extolling the virtues of volumetric manufactured buildings, as well as removing the complexity surrounding so-called modern methods of construction by diluting the myths and embracing reality.
Volumetric modular buildings are less susceptible to poorly specified products as time can be taken upfront to validate the correct specification of materials. Designs are digitally constructed and virtually tested before they move onto the manufacturing phase. That process eliminates waste and achieves highly-accurate and airtight building envelopes designed and built to higher sustainability standards. That allows clients to have confidence in the quality and performance that they can expect from their new building.
Unlike factory manufactured buildings, there is significant evidence that traditional construction methods do not produce structures that perform as well as design expectations and there is a void between anticipated and actual in-use performance. Findings from studies such as PROBE (Post Occupancy Review of Buildings and their Engineering) reveal that actual energy consumption in traditionally conceived buildings is often as much as twice that predicted at the design stage.
Not only is the actual construction of the building ‘greener’, but
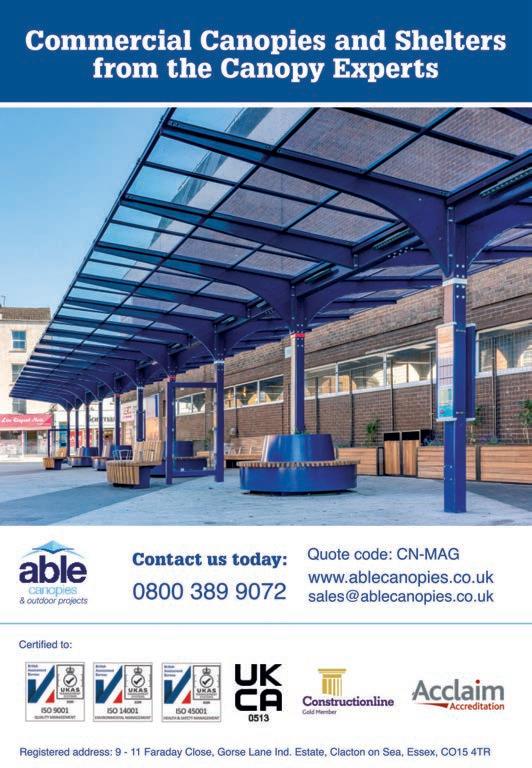