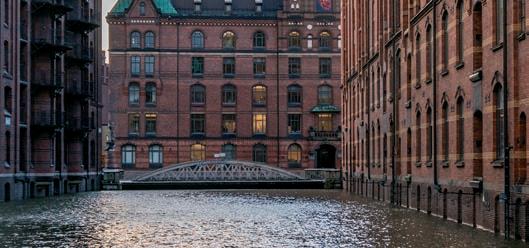
8 minute read
Where do you go for expert opinion on flooded equipment?
By Mamoon Alyah PE CEng IRMCert and Rose Campbell IRMCert
[AROUND THE WORLD we have witnessed an increase in contamination losses due to flooding in manufacturing plants, data centres, office buildings and other industrial and commercial properties. Previously unforeseeable rain and flooding has been reported in many parts of the world and we can only expect that there will be more natural catastrophes such as occurred in Germany, UK, USA and throughout the Middle East during the past few years.
We can expect an increase in disputes related to the reliability and cost of reinstatement of mechanical, electrical, data and communication systems following contamination, and whether a full replacement of affected equipment is necessary.
Risk of damage from contamination
The question of actual damage to contaminated equipment is complex and extends beyond whether or not the equipment appears to be functional immediately following exposure. Risk of damage varies depending on numerous factors, including type and level of exposure to contaminants – water, chemicals etc – and the type of equipment in question. Some types of damage include: • Mechanical binding, where mechanical components such as relays and circuit breakers become clogged due to the settlement of the residue of dissolved salts in floodwater. That is very dangerous, especially in electrical equipment. Although the equipment affected may still work, it might not respond properly and fail to trip when necessary. • Obscuration from debris affects the interfaces and reduces the overall quality of signal transmission. • Galvanic shorts, where surface water is bridged by conductive debris and acts as a circuit bridge. That is less of a concern if the water that has come in contact with a piece of equipment is clear, fresh water that has no contaminants. In flooding conditions, however, it is extremely likely that the water will be contaminated. • Increased contact resistance, where electrical contacts are coated with contaminants – increasing the contact resistance and leading to hot spots which may cause fires. • Corrosion, which occurs when contaminants react with water to form acids that corrode non-protected metal. That can set in on different pieces of equipment, resulting in irreversible damage. • Overheating, which occurs when, after the water dries out, layers of contaminants blanket the surfaces of electronic components, preventing them from dissipating heat during operation. Prolonged operation while overheated can lead to premature failure of electronics.
Investigating damage
To investigate flooding damage to different types of equipment, a number of challenges must be recognised and overcome: starting with the need to identify the correct expert who can assist with the damage assessment and evaluation of different reinstatement options. The right expert must possess enough knowledge about the contaminated equipment and – more importantly – how the contamination, regardless of its type, can affect the equipment in the long term.
It may not be possible for experts to examine the property and equipment straightaway. In that case, they must have access to detailed information, including photographs of the affected property, equipment and the circumstances that led to the contamination. Experts can only carry out their investigation after the water has receded or the fire has been put out. At that time, the property must be secured and made safe to access. It is important to mitigate the damage to the equipment, to prevent irreversible corrosion from setting in and to prevent overheating and electrical shorts. Experts can create a plan to preserve equipment and prevent further damage from settling in. Where possible, all power should be disconnected and controls should be in place for temperature and humidity.
Before any testing can be carried out, equipment must be dried. That can be accomplished via a number of options, depending on the type of equipment and the environment, including: • Baking, where heat is applied in a controlled manner to the equipment • Ventilation, where air flow is increased until the equipment is dry • Drying current, where a low voltage of electricity is applied to the machinery to evaporate water
Assessing the damage
The assessment of damage involves the inspection and examination of equipment to establish how far contaminants have penetrated the equipment and what parts were affected. Contamination damage to equipment raises a lot of technical complications that make it difficult to identify the true extent of the damage. Many factors must be considered including:
Type of contamination
Floodwater is rarely fresh, clean water and will almost always have dissolved contaminants in it. The type of contaminants will vary depending on the surrounding area from black water – the category of water that includes floods – containing pathogenic agents, to domestic drinking water which will have low levels of different chemicals.
The level of contamination
This is one of the most critical variables that will determine the effect contaminants will have on a piece of equipment. The higher the concentration of contaminants, the higher the risk of formation of acids that can lead to corrosion and electrical shorts.
Type of facility
The extent of damage will differ depending on the type of facility. Industrial properties often rely on many different types of equipment and machinery to function and damage could result in stoppage of all business until the equipment can be repaired or replaced. That becomes a particular concern when a plant is manufacturing highly-regulated products such as food or medication.
While commercial and residential buildings do not rely on the same machinery as manufacturing plants to stay in business, many pieces of equipment are critical to maintain continuous operation, such as IT and communication servers necessary to transact.
Location of equipment
The location of equipment within a facility is going to influence the extent of exposure that equipment will have endured. For example, equipment housed in the basement will be more likely to be completely submerged in the event of a serious flood, compared to equipment housed on upper levels.
Can equipment be restored to pre-loss condition? Yes: by looking at the results and comparing them against global standards, experts can determine whether equipment can be considered clean – and therefore liable to work again – whether it can be restored or decontaminated with good results, or whether the extent of contamination is so severe that restoration is not recommended.
There are some situations where replacement is the better option, such as if the equipment has suffered serious damage from corrosion, as that cannot be reversed or repaired.
When there are short-circuits and corroded surfaces, reinstatement is also unlikely to be viable. Transformers may be reinstated; however, because they often use paper insulation, there might be the possibility of irreversible damage and further testing will have to be done.
In other situations, the answer will be more straightforward: wiring designed to be submerged can be reinstated, while cables that are meant to remain dry cannot. Similarly, any submerged wiring device such as wiring sockets must be replaced.
For those situations where it is unsure whether equipment is damaged beyond all repair, additional testing can be carried out. With electrical equipment, the insulation, current and voltage should be tested. Sometimes a ‘hi-pot’ test will be carried out, which stresses the equipment to higher levels to ensure reliability has not been affected. Mechanical components will often see the trip mechanisms checked to ensure that they are working properly and have not been damaged.
Chemical testing can be used to understand the full extent of the contamination. One method that is often utilised is the use of wipe samples, which will identify the type and extent of chemicals on the equipment.
There are many tests that can be carried out, but it is important to decide which are necessary, feasible, and will yield the information that will make the testing worth the expense. When choosing which tests to carry out, it is important that all tests should answer the question of the extent of contamination, and therefore whether the equipment has been affected or not.
Testing protocols must be prepared and agreed upon. While there are many tests that can be carried out on flooded equipment, those tests are expensive and may not provide valuable information.
Reliability concerns
An important question following a flood is whether the exposure will affect the long-term reliability of the equipment. The supplier or OEM may no longer want to cover the equipment by an existing warranty or service contract, based on concerns that the damage sustained affects the reliability of the equipment.
Once equipment has been tested, a combination of restoration, repair and replacement will often be used to return a property to a pre-loss condition. Do not assume that the correct answer for what to do about one piece of equipment will apply to all others, as the extent of damage is dependent on many different factors – including the amount of exposure to contamination and the type of equipment being exposed. q • Mamoon Alyah PE CEng IRMCert is the managing director and principal engineer at CEERISK Consulting Ltd, a global engineering consultancy headquartered in London, which provides expert witness services in matters involving damage and failure of electrical and mechanical equipment. Mamoon has been instructed as an expert witness in jurisdictions around the world, including the USA, UK, UAE and Australia. He has worked on large and complex losses, including flooding to large electrical systems following hurricanes in the USA and flooding in the UK. Contact Mamoon by email at mamoon.alyah@ceerisk.com. • Rose Campbell IRMCert is a risk analyst and services manager at CEERISK Consulting. She specialises in the assessment of risk of failure of electrical and mechanical equipment in different types of commercial and industrial properties in different sectors. She has been involved in developing contingency plans and business recovery programmes for medium and large industrial facilities throughout the Middle East. Contact Rose by email at rcampbell@ceerisk.com.
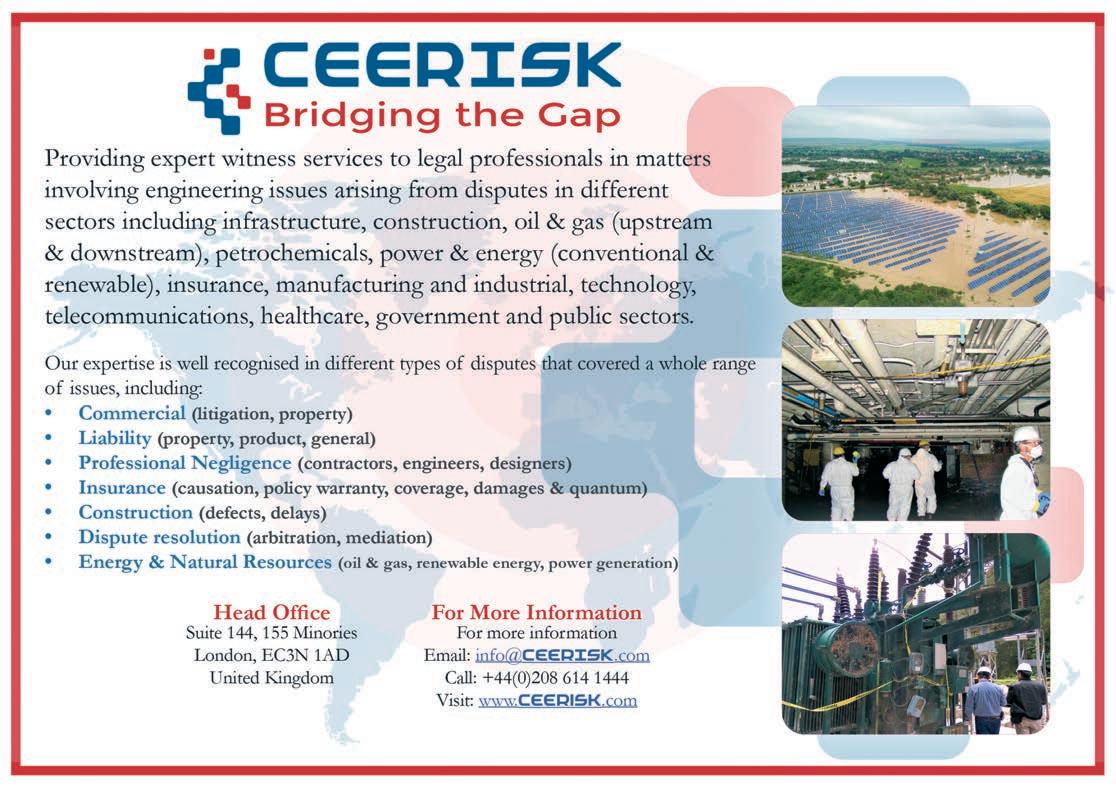