FLAME
CONTROL
SAFETY PRODUCTS THAT PROTECT EQUIPMENT, LIVES & THE ENVIRONMENT
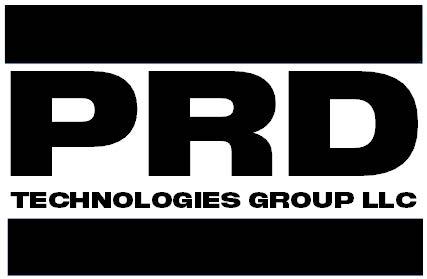

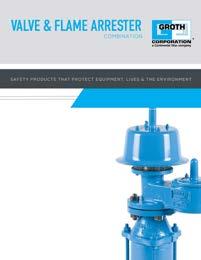
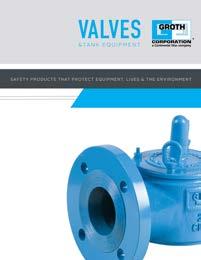
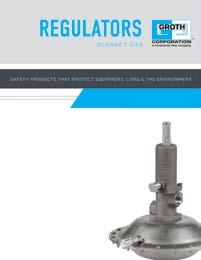
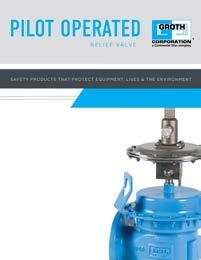
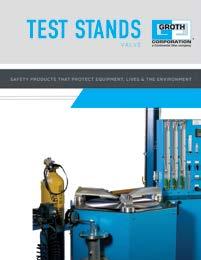
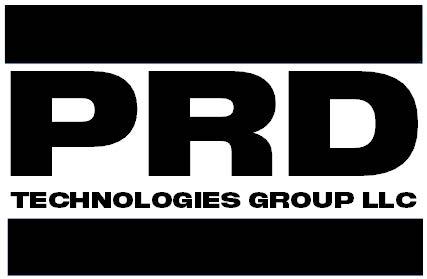
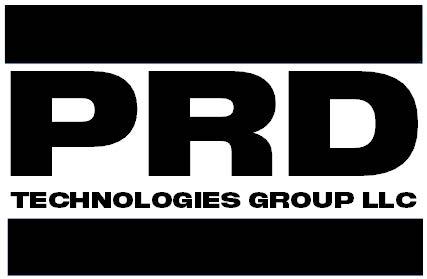
• Sizes 0.5" through 2"
• Housing standard material: carbon steel or stainless steel
• Flame element standard material: stainless steel
• Operational Temperature Range -4 to 140 ºF (-20 to 60 ºC)
• Good for IEC gas group IIB3 (MESG > 0.65 mm)
• Pre-Ingition system pressure up to 23.2 psia (1.60 bara)
• Certified to ATEX Directive in compliance with EN ISO 16852:2010
Certificate #: IBExU14ATEX2076 X
Model 7622B is designed to prevent flashback in small lines carrying flammable gases. They are often used in small pilot lines and are intended for use where the gas flow can be shut off. The units are union type fittings with FNPT connections.
FEATURES & BENEFITS
• Flame element has sufficient openings to provide a minimum pressure drop and still prevent flashback in the line
• Flame element consists of mesh and chemically etched plates
• Modular design allows easy access for inspection and maintenance
OPTIONS
• Special options available
• FNPT threaded connections
0.50"*1.87"2.77"1 (13 mm)(48 mm)(70 mm)(0.5 kg)
0.75"1.87"1.84"1 (19 mm)(48 mm)(47 mm)(0.5 kg)
1"2.12"2.34"3 (25 mm)(54 mm)(59 mm)(1.4 kg)
1.50"2.50"2.59"4 (38 mm)(64 mm)(66 mm)(1.8 kg)
Specifications subject to change without notice. Certified dimensions available upon request.
*0.5" size utilizes a 0.75" flame check with 0.75" x 0.5" reducers.
Note: Maximum working pressure 25 psig
Include model number and setting when ordering.
For special options, consult factory
1.
1. Flow facility and equipment comply with API 2000.
2.Flow measurement accuracy verified by an independent research organization.
3. Flow capacity is based on actual tests and certified by Groth Corporation.
4.Flow data are for tank mounting or end of line and includes flame arrester entrance loss, exit loss and internal losses.
• Flange sizes 2” through 12”
• Housing standard material: carbon steel, stainless steel, aluminum
• Designed for quick and easy maintenance
• Unique recessed seating for superior protection
• Proven spiral-wound, crimped-ribbon flame element (316SS or aluminum)
• Operating Temperature <= 140°F(60°C)
• Vertical installation only
The 7618 model is designed to inhibit flame propagation in gas piping systems and to protect low pressure tanks containing flammable liquids. Arresters protect low flash point liquids from external sources of ignition. This provides increased fire protection and safety.
Weather Hood Outlet
• Gas Group: NEC D, IEC IIA
• Operating Temperature <= 140°F(60°C)
• Pre-Ignition Pressure = Atmosphere
Flanged Outlet with or without Discharge Piping
• Gas Group: NEC D, IEC IIA
• Operating Temperature <= 140°F (60°C)
• Pre-Ignition Pressure = Atmosphere
• Discharge Piping Length <= 10 pipe diameters
• Gas Group: IEC IIA1, Methane (includes most Biogas applications)
• Operating Temperature <= 140°F (60°C)
• Pre-Ignition Pressure <= 1 psig
• Run-up Length <= 50 pipe diameters (2”)
• Run-up Length <= 20 pipe diameters (3”)
• Run-up Length <= 10 pipe diameters (4” – 12”)
• Flame arrester element geometry maximizes flame quenching capability while minimizing pressure drop
• Proven spiral-wound, crimped-ribbon flame element provides reliable flame protection
• Modular design allows easy and cost-effective flame bank maintenance
• Exterior painting or coating available
• Weatherhood (replaces flanged outlet)
• DIN or ASME/ANSI drilling available
• Tapped drain and instrumentation ports available
2"8.75"14" 50psig100psig 18 (50mm)(221mm)(356mm)(345kPa)(690kPa) (8kg)
3"9.50"16" 50psig100psig25 (80mm) (241mm)(406mm)(345kPa)(690kPa)(11kg)
4"12.25"18.25" 50psig100psig40 (100mm)(311mm)(464mm)(345kPa)(690kPa) (18kg)
6"16.50"21" 50psig100psig 70 (150mm)(419mm)(533mm)(345kPa)(690kPa)(32kg)
8"21"25" 50psig100psig135 (200mm)(533mm)(635mm)(345kPa)(690kPa)(61kg)
10"24.75"30" 50psig100psig235 (250mm)(629mm) (762mm) (345kPa)(690kPa) (107kg)
12"28.62"32.50" 50psig100psig345 (300mm) (727mm)(826mm) (345kPa)(690kPa)(156kg)
* Larger sizes available on special application.
†150# ANSI drilling compatibility, F.F. on aluminum and R.F. on carbon steel and stainless steel alloys. ◊Pneumatic tested to 15 psig as standard.
1. Flow facility and equipment comply with API 2000.
2.Flow measurement accuracy verified by an independent research organization.
3. Flow capacity is based on actual tests and certified by Groth Corporation.
4.Flow data are for tank mounting or end of line and includes flame arrester entrance loss, exit loss and internal losses.
1. Flow facility and equipment comply with API 2000.
2.Flow measurement accuracy verified by an independent research organization.
3. Flow capacity is based on actual tests and certified by Groth Corporation.
4.Flow data are for tank mounting or end of line and includes flame arrester entrance loss, exit loss and internal losses.
• Flange sizes 2” through 12”
• Housing standard material: carbon steel, stainless steel, aluminum
• Designed for quick and easy maintenance
• Unique recessed seating for superior protection
• Proven spiral-wound, crimped-ribbon flame element (316SS or aluminum)
• Operating Temperature <= 140°F(60°C)
• Horizontal installation only
The 7628 model is designed to inhibit flame propagation in gas piping systems and to protect low pressure tanks containing flammable liquids. Arresters protect low flash point liquids from external sources of ignition. This provides increased fire protection and safety.
END-OF-LINE IN-LINE
Flanged Outlet with or without Discharge Piping
• Gas Group: NEC D, IEC IIA
• Operating Temperature <= 140°F (60°C)
• Pre-Ignition Pressure = Atmosphere
• Discharge Piping Length <= 10 pipe diameters
FEATURES & BENEFITS
• Gas Group: IEC IIA1, Methane (includes most Biogas applications)
• Operating Temperature <= 140°F (60°C)
• Pre-Ignition Pressure <= 1 psig
• Run-up Length <= 50 pipe diameters (2”)
• Run-up Length <= 20 pipe diameters (3”)
• Run-up Length <= 10 pipe diameters (4” – 12”)
• Flame arrester element geometry maximizes flame quenching capability while minimizing pressure drop
• Proven spiral-wound, crimped-ribbon flame element provides reliable flame protection
• Modular design allows easy and cost-effective flame bank maintenance
OPTIONS
• Exterior painting or coating available
• DIN or ASME/ANSI drilling available
• Tapped drain and instrumentation ports available
2"15"9.50" 150psig350psig 18 (50mm) (381mm) (241mm)(1035kPa)(2415kPa) (8kg)
3"17"11" 140psig325psig25 (80mm) (431mm) (279mm) (966kPa)(2242kPa)(11kg)
4"18.75"12.50" 140psig325psig40 (100mm) (476mm)(318mm) (966kPa)(2242kPa) (18kg)
6"21"16.50" 140psig325psig 70 (150mm)(533mm)(419mm)(966kPa)(2242kPa)(32kg)
8"26"20.50" 90psig200psig135 (200mm)(660mm)(521mm)(621kPa) (1380kPa) (61kg) 10"30"24.50"75psig 150psig235 (250mm) (762mm) (622mm) (517kPa) (1035kPa) (107kg)
12"32.50"28.50"75psig 150psig345 (300mm) (826mm)(724mm)(517kPa) (1035kPa)(156kg)
* Larger sizes available on special application.
†150# ANSI drilling compatibility, F.F. on
◊Pneumatic
R.F.
1. Flow facility and equipment comply with API 2000.
2.Flow measurement accuracy verified by an independent research organization.
3.
4.Flow
1. Flow facility and equipment comply with API 2000.
3. Flow capacity is based on actual tests and certified by Groth Corporation.
4.Flow data are for tank mounting or end of line and includes flame arrester entrance loss, exit loss and internal losses.
• Sizes 2" through 12"
• Housing standard material: carbon steel, stainless steel, aluminum
• Flame element standard material: 316L stainless steel
• Other materials available upon request
• Maximim Operational pressure 15.7 psia (1.08 bara)*
• Operational Temperature Range -4 to 140 ºF (-20 to 60 ºC)
• Burn Time tBT 5 minutes*
• IEC gas group IIA1 (MESG > 1.14 mm)
• Certified to ATEX Directive in compliance with EN ISO 16852:2010
Certificate #: IBExU12ATEX2018 X
• Thermocouple is required for flame detection per the ATEX code
The 7588 model is a In-Line Vertical Deflagration Flame Arrester designed to inhibit flame propagation in gas piping systems and to protect low pressure tanks containing flammable liquids. Arresters protect low flash point liquids from external sources of ignition. This provides increased fire protection and safety.
FEATURES & BENEFITS
• Flame arrester element geometry maximizes flame quenching capability while minimizing pressure drop
• Proven spiral-wound, crimped-ribbon flame element provides reliable flame protection
• Modular design allows easy and cost-effective flame bank maintenance
OPTIONS
• Exterior painting or coating available
• DIN or ASME/ANSI drilling available
• Drains and instrument ports available
• Factory installed thermocouples for flame sensing
*Testing parameters based on EN ISO 16852:2010
Specifications subject to change without notice. Certified dimensions available upon request.
2"8.75"14" 50 18 40 (50mm)(221mm)(356mm) (8kg)(18kg)
3"9.50"16" 20 27 60 (80mm) (241mm)(406mm)(12kg) (27kg)
4"11.50"18.25" (100104291 mm)(292mm)(464mm)(19kg)(41kg)
6"16.50"21" 1092 184 (150mm)(419mm)(533mm)(42kg) (83kg)
8"21"25" (20010146309 mm)(533mm)(635mm)(66kg)(140kg)
10"24.75"30" 10 237498 (250mm)(629mm) (762mm)(108kg) (226kg)
12"28.62"32.50" (30010306694 mm) (727mm)(826mm) (139kg)(314kg)
*Testing parameters based on EN ISO 16852:2010
1. Flow facility and equipment comply with API 2000.
2.Flow measurement accuracy verified by an independent research organization.
3. Flow capacity is based on actual tests and certified by Groth Corporation.
4.Flow data are for tank mounting or end of line and includes flame arrester entrance loss, exit loss and internal losses.
• Sizes 2" through 12"
• Housing standard material: carbon steel, stainless steel, aluminum
• Flame element standard material: 316L stainless steel
• Other materials available upon request
• Maximim Operational pressure 15.7 psia (1.08 bara)*
• Operational Temperature Range -4 to 140 ºF (-20 to 60 ºC)
• Burn Time tBT 5 minutes*
• Good for IEC gas group IIA1 (MESG > 1.14 mm)
• Certified to ATEX Directive in compliance with EN ISO 16852:2010
Certificate #: IBExU12ATEX2017 X
• Thermocouple is required for flame detection per the ATEX code
The 7598 model is a In-Line Horizontal Deflagration Flame Arrester designed to inhibit flame propagation in gas piping systems and to protect low pressure tanks containing flammable liquids. Arresters protect low flash point liquids from external sources of ignition. This provides increased fire protection and safety.
FEATURES & BENEFITS
• Eccentric design allows for horizontal installation by preventing liquid accumulation
• Flame arrester element geometry maximizes flame quenching capability while minimizing pressure drop
• Proven spiral-wound, crimped-ribbon flame element provides reliable flame protection
• Modular design allows easy and cost-effective flame bank maintenance
OPTIONS
• Exterior painting or coating available
• DIN or ASME/ANSI drilling available
• Drains and instrument ports available
• Factory installed thermocouples for flame sensing
*Testing parameters based on EN ISO 16852:2010
Specifications subject to change without notice. Certified dimensions available upon request.
2"13.75"9.50" (50503169 mm)(349mm)(241mm)(14kg)(31kg)
3"15.75"11" 2040 85 (80mm) (400mm) (279mm)(18kg)(38kg)
4"18"12.50" (1001053112 mm) (457mm)(318mm) (24kg)(51kg)
6"21"16.50" (15010111216 mm)(533mm)(419mm)(50kg) (98kg)
8"25"20.50" (20010213413 mm)(635mm)(521mm) (97kg)(187kg)
10"30"24.50" (25010306622 mm) (762mm) (622mm)(139kg) (282kg)
12"32.50"28.50" 10 378 693 (300mm) (826mm)(724mm)(171kg) (314kg)
*Testing parameters based on EN ISO 16852:2010
1. Flow facility and equipment comply with API 2000.
2.Flow measurement accuracy verified by an independent research organization.
3. Flow capacity is based on actual tests and certified by Groth Corporation.
4.Flow data are for tank mounting or end of line and includes flame arrester entrance loss, exit loss and internal losses.
• Sizes 2" through 12"
• Housing standard material: carbon steel, stainless steel, aluminum
• Flame element standard material: 316L stainless steel
• Other materials available upon request
• Maximim Run Up (L/D) 50*
• Operational Temperature Range -4 to 140 ºF (-20 to 60 ºC)
• Burn Time tBT 2 minutes (sizes 8”, 10” and 12”)*
• Burn Time tBT 10 minutes (sizes 2”, 3”, 4” and 6”)*
• IEC gas group IIA (MESG > 0.90 mm)
• Certified to ATEX Directive in compliance with EN ISO 16852:2010 Certificate #: IBExU12ATEX2016 X
• Thermocouple is required for flame detection per the ATEX code
The 7688 model is a In-Line Vertical Deflagration Flame Arrester designed to inhibit flame propagation in gas piping systems and to protect low pressure tanks containing flammable liquids. Arresters protect low flash point liquids from external sources of ignition. This provides increased fire protection and safety.
FEATURES & BENEFITS
• Flame arrester element geometry maximizes flame quenching capability while minimizing pressure drop
• Proven spiral-wound, crimped-ribbon flame element provides reliable flame protection
• Modular design allows easy and cost-effective flame bank maintenance
OPTIONS
• Exterior painting or coating available
• DIN or ASME/ANSI drilling available
• Drains and instrument ports available
• Factory installed thermocouples for flame sensing *Testing
Specifications subject to change without notice. Certified dimensions available upon request.
2"8.75"14" (5023.2101941 mm)(221mm)(356mm)(1.60)(9kg) (18kg)
3"9.50"16" 23.210 28 61 (80mm) (241mm)(406mm)(1.60)(13kg) (28kg)
4"11.50"18.25"17.4 (100104493 mm)(292mm)(464mm)(1.20)(20kg)(42kg)
6"16.50"21"17.4 10 98189 (150mm)(419mm)(533mm)(1.20)(44kg) (86kg)
8"21"25"17.4 2155 317 (200mm)(533mm)(635mm)(1.20) (70kg) (144kg)
10"24.75"30"17.4 (2502250512 mm)(629mm) (762mm) (1.20)(113kg)(232kg)
12"28.62"32.50"17.4 2324 712 (300mm) (727mm)(826mm) (1.20) (147kg) (323kg)
*Testing parameters based on EN ISO 16852:2010
1. Flow facility and equipment comply with API 2000.
2.Flow measurement accuracy verified by an independent research organization.
3. Flow capacity is based on actual tests and certified by Groth Corporation.
4.Flow data are for tank mounting or end of line and includes flame arrester entrance loss, exit loss and internal losses.
• Sizes 2" through 12"
• Housing standard material: carbon steel, stainless steel, aluminum
• Flame element standard material: 316L stainless steel
• Other materials available upon request
• Operational Temperature Range -4 to 140 ºF (-20 to 60 ºC)
• Good for IEC gas group IIA (MESG > 0.90 mm)
• Certified to ATEX Directive in compliance with EN ISO 16852:2010 Certificate #: IBExU12ATEX2015 X
• Thermocouple is required for flame detection per the ATEX code
The 7698 model is a In-Line Horizontal Deflagration Flame Arrester designed to inhibit flame propagation in gas piping systems and to protect low pressure tanks containing flammable liquids. Arresters protect low flash point liquids from external sources of ignition. This provides increased fire protection and safety.
• Eccentric design allows for horizontal installation by preventing liquid accumulation
• Flame arrester element geometry maximizes flame quenching capability while minimizing pressure drop
• Proven spiral-wound, crimped ribbon, flame element provides reliable flame protection
• Modular design allows easy and cost-effective flame bank maintenance
OPTIONS
• Exterior painting or coating available
• DIN or ASME/ANSI drilling available
• Drains and instrument ports available
• Factory installed thermocouples for flame sensing
Specifications subject to change without notice. Certified dimensions available upon request.
2"13.75"9.50" 23.2501032 70 (50mm)(349mm)(241mm)(1.60)(14kg)(32kg)
3"15.75"11" 23.2501041 86 (80mm) (400mm) (279mm) (1.60)(19kg)(39kg)
4"18"12.50"17.4 (100201055114 mm) (457mm)(318mm) (1.20)(25kg)(52kg)
6"21"16.50"17.4 (1502010116222 mm)(533mm)(419mm)(1.20)(53kg)(101kg)
8"25"20.50"17.4 (200202221422 mm)(635mm)(521mm)(1.20)(100kg)(191kg)
10"30"24.50"17.4 (250202320635 mm) (762mm) (622mm)(1.20)(145kg) (288kg)
12"32.50"28.50"17.4
202 397836 (300mm) (826mm)(724mm) (1.20) (180kg)(379kg)
*Testing parameters based on EN ISO 16852:2010
1. Flow facility and equipment comply with API 2000.
2.Flow measurement accuracy verified by an independent research organization.
3. Flow capacity is based on actual tests and certified by Groth Corporation.
4.Flow data are for tank mounting or end of line and includes flame arrester entrance loss, exit loss and internal losses.
• Sizes 2" through 12"
• Housing standard material: carbon steel, stainless steel, aluminum
• Flame element standard material: 316L stainless steel
• Other materials available upon request
• Operational Temperature Range -4 to 140 ºF (-20 to 60 ºC)
• Burn Time tBT 2 minutes*
• IEC gas group IIA (MESG > 0.90 mm)
• Certified to ATEX Directive in compliance with EN ISO 16852:2010
Certificate #: IBExU12ATEX2019 X
• Thermocouple is required for flame detection per the ATEX code
The 7678 model is an End-Of-Line Vertical Deflagration Flame Arrester designed to inhibit flame propagation in gas piping systems and to protect low pressure tanks containing flammable liquids. Arresters protect low flash point liquids from external sources of ignition. This provides increased fire protection and safety.
• Flame arrester element geometry maximizes flame quenching capability while minimizing pressure drop
• Proven spiral-wound, crimped-ribbon flame element provides reliable flame protection
• Modular design allows easy and cost-effective flame bank maintenance
OPTIONS
• Exterior painting or coating available
• DIN or ASME/ANSI drilling available
• Drains and instrument ports available
• Factory installed thermocouples for flame sensing
*Testing parameters based on EN ISO 16852:2010
2"13"18" 22 37 (50mm)(330mm) (457mm) (10kg) (17kg)
3"17"18.7" 3565 (80mm) (432mm) (475mm) (16kg)(29kg)
4"19.5"21.1" 4990 (100mm)(495mm)(536mm)(22kg)(41kg)
6"23.50"24.2" 105 168 (150mm) (597mm) (615mm) (48kg)(76kg)
8"28.3"32" 160 280 (200mm) (719mm)(813mm)(73kg)(127kg)
10"32.25"36" 244 417 (250mm) (819mm) (914mm)(111kg) (189kg)
12"40"39" 314 567 (300mm)(1016mm)(991mm)(142kg) (257kg)
1. Flow facility and equipment comply with API 2000.
2.Flow measurement accuracy verified by an independent research organization.
3. Flow capacity is based on actual tests and certified by Groth Corporation.
4.Flow data are for tank mounting or end of line and includes flame arrester entrance loss, exit loss and internal losses.
• Sizes 2"x5" through 6"x12"
• Vertical or horizontal installation
• In-line or end-of-line deflagrations
• Unstable detonations
• Pre-ignition system pressure up to 15.7 psia (1.08 bara)
• Pre-ignition system temperatures -4 to 140°F (-20 to 60°C)
• Burn Time tBT 10 minutes
• Bi-directional with respect to flow and ignition source
• Standard materials of construction are carbon steel or stainless steel
• Stainless Steel element is standard
• Low pressure drop with multiple element sizes available for each flange size
• Certified to ATEX Directive in compliance with EN ISO 16852:2010
Certificate #: IBExU12ATEX2160 X
• Certified to USCG per 33 CFR Part 154 App. A Type II
Certificate #: CSA LO 4000-5704
• Thermocouple is required for flame detection per the ATEX & USCG codes
The Groth Model 7658A Deflagration & Detonation Flame Arrester inhibits flame propagation in gas piping systems. The design of the Model 7658A Flame Arrester makes it ideal to protect liquid storage tanks containing NEC Group D (IEC Class IIA) gases with a Maximum Experimental Safe Gap (MESG) equal to or greater than 0.90 mm.
Housings are available in carbon steel , stainless steel or Alloy C276 and elements in stainless steel, Alloy C276 or other corrosion resistant alloys.
These arresters are compact with high flow capacity and low pressure drop. Elements are easily removed in-line for cleaning and maintenance and are economical to replace if necessary.
• Other materials available
• Sensor ports
• Large inspection and cleaning ports
• Swing bolts for fast element removal
• Factory installed thermocouples for flame sensing
Specifications subject to change without notice. Certified dimensions available upon request.
5"18"9"75 (125mm) (457mm) (229mm)(34kg)
6"20.31"11" 100 (150mm)(516mm) (279mm) (45kg)
8"22.43"13.5"175 (200mm) (570mm) (343mm) (79kg)
12"25.94"19" 350 (300mm)(659mm) (483mm) (159kg)
* Larger sizes available on special applications. All units with ANSI 150 RF flanges standard (other flange drillings available).
1. Flow facility and equipment comply with API 2000.
2.Flow measurement accuracy verified by an independent research organization.
3. Flow capacity is based on actual tests and certified by Groth Corporation.
4.Flow data are for tank mounting or end of line and includes flame arrester entrance loss, exit loss and internal losses.
Note: Consult factory for flow on other sizes.
1. Flow facility and equipment comply with API 2000.
2.Flow measurement accuracy verified by an independent research organization.
3. Flow capacity is based on actual tests and certified by Groth Corporation.
4.Flow data are for tank mounting or end of line and includes flame arrester entrance loss, exit loss and internal losses.
• Sizes 4"x16" through 12"x30"
• Vertical or horizontal installation
• In-line or end-of-line deflagrations
• Unstable detonations
• Pre-ignition system pressure up to 15.7 psia (1.08 bara)
• Pre-ignition system temperatures -4 to 140°F (-20 to 60°C)
• Burn Time tBT 20 minutes
• Bi-directional with respect to flow and ignition source
• Standard materials of construction are carbon steel or stainless steel
• Stainless Steel element is standard
• Low pressure drop with multiple element sizes available for each flange size
• Certified to ATEX Directive in compliance with EN ISO 16852:2010
Certificate #: IBExU15ATEX2060 X (Element Sizes 16”, 20” and 24”)
• Certified to USCG per 33CFR Part 154 App. A Type II
Certificate #: IBExU IB-16-8-115, IBExU IB-16-8-031 (Element Sizes 16”, 20”, 24” and 30”)
• Thermocouple is required for flame detection per the ATEX & USCG codes
The Groth Model 7661 Deflagration & Detonation Flame Arrester inhibits flame propagation in gas piping systems. The design of the Model 7661 Flame Arrester makes it ideal to protect liquid storage tanks containing NEC Group D (IEC Class IIA) gases with a Maximum Experimental Safe Gap (MESG) equal to or greater than 0.90 mm.
Housings are available in carbon steel , stainless steel or Alloy C276 and elements in stainless steel, Alloy C276 or other corrosion resistant alloys.
These arresters are compact with high flow capacity and low pressure drop. Elements are easily removed in-line for cleaning and maintenance and are economical to replace if necessary.
• Other materials available
• Sensor ports
• Large inspection and cleaning ports
• Swing bolts for fast element removal
• Factory installed thermocouples for flame sensing
Specifications subject to change without notice. Certified dimensions available upon request.
16"29.63"23.50" 550 (400mm) (753mm)(597mm) (249kg)
20"32.43"27.50"850 (500mm) (824mm) (699mm) (386kg)
24"38.75"32.00" 1200 (600mm) (984mm)(813mm) (544kg)
30"42.88"38.75" 1900 (750mm)(1089mm)(984mm)(862kg)
* Larger sizes available on special applications. All units with ANSI 150 RF flanges standard (other flange drillings available).
1.
2.Flow
3.
4.Flow
1.
4.Flow
• Sizes 2"x4" through 12"x30"
• Vertical or horizontal installation
• In-line or end-of-line deflagrations
• Stable detonations
• Unstable detonations (element sizes <=12”)
• Pre-ignition system pressure up to 19.7 psia (1.36 bara)
(see specifications table)
• Pre-ignition system temperatures -4 to 140°F (-20 to 60°C)
• Bi-directional with respect to flow and ignition source
• Available in carbon steel, stainless steel, Alloy C276, and other materials
• Wafer mesh element is standard
• Low pressure drop with multiple element sizes available for each flange size
• Certified to ATEX Directive in compliance with EN ISO 16852:2010
Certificate #: IBExU12ATEX2170 X (Element Sizes 4”, 6”, 8” and 12” Unstable detonations)
• Certified to ATEX Directive in compliance with EN ISO 16852:2010
Certificate #: IBExU12ATEX2171 X (Element Sizes 20”, 26” and 30” Stable detonations)
• Thermocouple is required for flame detection per the ATEX code
The Groth Model 7758A Deflagration & Detonation Flame Arrester inhibits flame propagation in gas piping systems. The design makes it ideal to protect liquid storage tanks containing both NEC Group D and Group C vapors (IEC Class IIA and IIB1 through IIB3 vapors) with a Maximum Experimental Safe Gap (MESG) equal to or greater than 0.026" [0.65 mm].
Housings are available in carbon steel, stainless steel, and Alloy C276 and elements in stainless steel, Alloy C276 and other corrosion resistant alloys.
These arresters are compact with high flow capacity and low pressure drop. Wafer mesh elements are easily removed in-line for cleaning and maintenance and are economical to replace if necessary. Contact the factory for additional features and options.
• Other materials available
• Sensor ports
• Large inspection and cleaning ports
• Swing bolts for fast element removal
• Factory installed thermocouples for flame sensing
2”4”12”11”30
(50mm)(100mm)(305mm) (279mm)
(50mm)(150mm)(324mm) (279mm)
(50mm)(200mm)(394mm)(394mm)(1.36)(1.36)(1.36)(52kg)
3”6”
(80mm) (150mm)(324mm) (279mm)
3”
(80mm) (200mm)(406mm) (381mm) (1.36)(1.36)(1.36) (57kg)
3”12”
(80mm) (300mm)(465mm) (483mm)
4” 8”16.75”
(100mm)(203mm)(425mm)
4”12”19”19”5
(100mm)(300mm) (483mm)(483mm) (1.24)(1.24)(1.24)(125kg)
4”20”23.69”
(100mm)(500mm)(602mm)(699mm)
(150mm)(300mm)(465mm) (483mm) (1.24)(1.24)(1.24)(130kg)
6”20”23.69”
(150mm)(500mm)(602mm)(699mm) (1.188)(1.188) (299kg)
6”26”29.06”34.25”30
(150mm)(650mm) (738mm)(870mm)(1.188)(1.188)(483kg)
6”30”32.31”
(150mm) (750mm)(821mm)(984mm)(1.188)(1.188) (640kg)
(200mm)(500mm)(602mm)(699mm)
(200mm)(650mm) (738mm)(870mm)(1.188)(1.188)
(300mm)
* Consult factory for larger sizes.
1. Flow facility and equipment comply with API 2000.
2.Flow measurement accuracy verified by an independent research organization.
3. Flow capacity is based on actual tests and certified by Groth Corporation.
4.Flow data are for tank mounting or end of line and includes flame arrester entrance loss, exit loss and internal losses.
1. Flow facility and equipment comply with API 2000.
2.Flow measurement accuracy verified by an independent research organization.
3. Flow capacity is based on actual tests and certified by Groth Corporation.
4.Flow data are for tank mounting or end of line and includes flame arrester entrance loss, exit loss and internal losses.
For easy ordering, select proper model numbers
• Include model number when ordering.
• For special options, consult factory
• See dimension and capacity tables for available flange/element combinations.
* Customer specified size
= No Options Z = Consult Factory
= No Options I = Instrument Connections*
= Integrated Thermocouple (includes Thermowell)
= Integrated Thermowell A = 150# R.F. ANSI Flange B = DIN PN10 Flange
= DIN PN16 Flange
2680 New Butler Rd. New Castle, PA 16101
Tel: 724-368-8725
Email: sales@portersvillerd.com
700 Southlake Blvd. North Chesterfield VA 23236
Tel: 804-593-2384
Email: sales@portersvillerd.com
www.portersvilleprd.com
143 S.Thomas Rd. Tallmadge, OH 44278
Tel: 330-253-4800
Email: sales@portersvilleprd.com
1551 Shipley Ferry Road Blountville, TN 37617
Tel: 423.482.0496
Email: sales@portersvillerd.com
1500 E. Burnett St. Signal Hill, CA 90755
Tel: 562-424-8108
Email: Sales@BV-BM.com
www.bv-bm.com
403 Technology Dr South Point, OH 45680
Tel: 740-377-0012
Email: sales@portersvilleprd.com
3800 Fruitvale Avenue Bakersfield, CA 93308
Tel: 661-589-6801
Email: Sales@BV-BM.com
3195 Park Road, Benicia, CA 94510
Tel: 707-590-6688
Email: Sales@BV-BM.com