
10 minute read
Automating the tool change process
FEATURE ARTICLE - Automating the tool change process.
As the manufacturing industry is becoming more competitive than ever, fabrication workshops continue to seek ways to improve production speed and efficiency. While modern press brakes operate at higher speeds and with greater efficiency and accuracy over machines from a decade ago, bottlenecks in tooling setup and configuration continue to hamper machine output and productivity.
For many facilities that change tooling setups several times each day, a significant amount of production time can potentially be lost between bending jobs due to the time it can take for machine operators to manually unload press brake tooling, locate and load the next set of tools, plus configure tool placement and alignment in the machine before the next job can commence. In addition, there is the potential risk of injury for operators manually handling heavy tools as well as the risk of damaging expensive tooling through mishandling or an incorrect setup.
The amount of time required for each manual tool changeover can vary greatly based on several factors that include the experience and speed of the machine operator, the amount of tooling to be removed and loaded, returning tools to storage, locating and loading the next set of tools and the complexity of the new tooling setup.
Effective tool storage and management creates challenges for most workshops. Quite often, production delays can occur through the additional time required to locate the tooling for a bend job. In many cases, press brake punches and dies are stored on shelves or racking in the workshop and shared amongst two or more machines. An efficient production facility relies on diligent operators to manually manage the storage and placement of tools; however, this is not always the case.
Just consider how much production time is currently being lost as machine operators spend time searching for tools or maybe just trying to locate one final piece to complete a setup. Or perhaps the required tooling is already in use on another machine. For facilities that process many different parts each day and on tight production schedules, having all the tools available and readily accessible for each machine is essential.
Press brake manufacturers are addressing these issues with intelligent mechanical systems that completely automate the tool change process.
Automatic Tool Changer (or ATC) press brakes are making machine setup and tool changeover faster, more reliable and a lot more efficient compared to a manual tool change process. These systems also free up time for operators to perform other tasks or get material blanks ready for bending so production can start as soon as the tool change process is complete.
Offered as an option from the press brake manufacturer, an ATC is either incorporated into the design of the machine or as a separate integrated module. While designs and functionality vary and are unique to individual manufacturers, ATC press brakes generally comprise the same basic elements. This begins with a tool storage area, either contained within the machine footprint or attached externally, a motorised system that transfers the tools between the storage area and the machine tool holders and finally, a mechanism that sets the position and spacing of the tools along the length of the machine.
The automatic tool change process is managed by the CNC system in conjunction with the bend program. The ATC first removes any punches and dies that are not needed for the next setup and returns them to the storage area. The ATC then identifies the next set of tools that are defined in the bend program and retrieves the required punches and dies from the storage area and inserts them into the tool holders, which would generally encompass a hydraulic or pneumatic tool clamping system. The horizontal placement of the punches and dies along the length of the machine is adjusted, including any necessary spacing between tools that is needed for part production such as box bending, where the correct tool gaps are required to accommodate part side flanges.
Also, in cases where multi-stage bending is required, these intelligent systems can effectively manage complex setups and with different tool profiles.
TRUMPF, LVD, Prima Power, Salvagnini and Warcom are among several press brake manufacturers that have developed their own unique solutions to automate and streamline the tool change process.
TRUMPF ToolMaster
TRUMPF ToolMaster boosts productivity by automatically switching between bending tools. The new generation ToolMaster can accommodate three times the tool metres as the previous model and changes a tool in just a few seconds. Users can insert both standard tools as well as ACB sensor tools and customer-specific special tools.
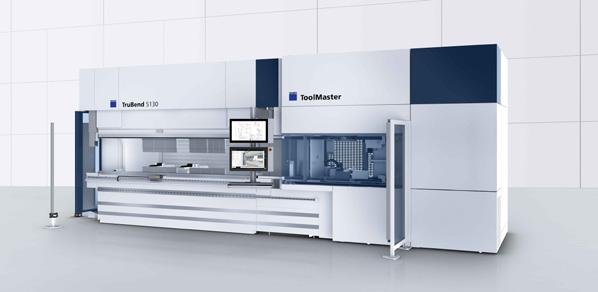
The TRUMPF ToolMaster
TRUMPF
On the end of the tool cabinet, a multi-shelf racking system stores the punches and dies with a storage capacity of around 85 metres of tools (depending on the selected tooling) that are well protected against corrosion. TRUMPF has developed a unique three stage solution that achieves optimal efficiency for faster tool changes.
In the first stage, there are two independent tool transfer arms - one for the punches and one for the dies. Each transfer arm comprises a multiaxis system that moves vertically and horizontally to access the multiple racks and shelves and a tool gripper that pulls the tools out from each shelf.
Once the tools are removed from the shelf, the transfer arms load the tools into two separate upper and lower turntables. Each turntable independently rotates 90 degrees, so that the tools are aligned with the press brake upper and lower tool holders. The upper turntable can also rotate in the opposite direction so that goose neck tools can be loaded in the inverted position.
In the final stage, two separate shuttles are used to load the punches and dies into position along the press brake.
Another interesting feature of the ToolMaster is the ability to easily load additional punches and dies into tool storage. The operator manually inserts the new tools into the upper and lower tool holders, then using a 2D handheld scanner, scans the Data Matrix Code codes that are printed on the front of the tools. After scanning and confirming the entry at the machine control, the ToolMaster automatically transfers the tools to the storage cabinet. >>
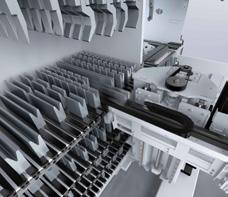
ToolMaster storage cabinet and transfer arms
TRUMPF
Salvagnini B3.AU-TO
The Salvagnini B3.AU-TO press brake stores the punches and dies in a covered tool magazine that is located within the rear of the press brake and can stock up to 24 metres of tooling.
The patented AU-TO system allows the transfer of tools between the tool magazine and the tool holders. Once the tools are in place, the B3 uses two additional levels of automation using the ATA and ATA.L devices to adjust the upper and lower tool length and spacing.
The ATA (Automatic Tool Adjuster) device is used to change and automatically adjust the upper bending tool length, saving time and increasing production efficiency. Changeover is fast, taking just a few seconds, and programming is simple and intuitive.
The ATA.L device, for the lower tools, is the ideal solution for kit production, as it allows parts of different thicknesses to be bent in sequence.
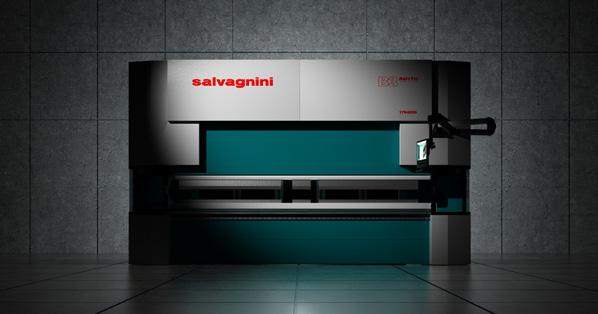
Salvagnini B3:AU-TO press brake
Salvagnini
LVD ToolCell
LVD prides itself on remaining close to customers and the challenges of modern-day manufacturing. In the last 10 to15 years they have seen a dramatic drive towards a ‘Small batch – Short Lead time’ culture. In addition, many manufacturers are reducing stock levels (for better use of working capital) and putting pressure on the supply chain. So, for LVD there was a clear need for a dramatic increase in throughput when processing small batches of parts.
In response to these manufacturing challenges, LVD was an early adopter of an Automatic Tool Change process with the introduction of their ToolCell press brake and was the first manufacturer to integrate tool storage within the existing machine footprint.
ToolCell ends the search for tooling with unique stadium style storage of top and bottom tooling that is located under the machine’s back-gauge, taking advantage of the available space. The tooling stadium holds up to two complete lengths of punches and five complete lengths of dies for flexibility and space-saving all in one compact design. The ToolCell tool storage system offers a flexible tooling configuration to suit specific application requirements.
Innovative grippers built into the machine’s back gauge fingers serve as the tool changer mechanism to transfer punches and dies. While the operator is preparing parts for the next job, the machine unloads the previous tool setup and loads the next setup, all without manual intervention.
The ToolCell comes equipped with LVD’s patented Easy-Form® Laser (EFL) adaptive bending system. EFL ensures the first bend is accurate every time. The EFL system transmits the digital information in real time to the CNC control unit, which processes it and immediately adjusts the position of the ram/punch to achieve the correct angle. The bending process is not interrupted, and no production time is lost.
LVD also offers ToolCell XT, the latest generation of its ToolCell automatic tool changing press brake with extended capacity to hold 50 percent more tooling than the original design.

LVD ToolCell XT
LVD
The large capacity of tools housed within the press brake provides the flexibility to handle a wider range of bending jobs, including complex layouts. With its extended tooling capacity, ToolCell XT offers the versatility to handle varying material types, organise tooling by material type, easily switch between stainless steel and mild steel applications. >>
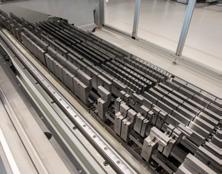
ToolCell stadium style tool storage
LVD
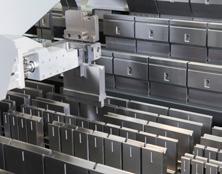
Grippers in the backgauge are used to transfer the tools
LVD
Prima Power eP Genius
Making its world premiere at Blechexpo will be Prima Power’s new bending solution, the eP Genius 1030, consisting in the integration of a servoelectric press brake eP-1030 with an automatic tool change storage.
The tool storage, which is the main innovation of this product, can accommodate a total of 32 metres of tools to be placed on 8 tool holder supports that move on 3 axes. It allows to handle tools (Wila style) with a minimum length of 20 mm up to 515 mm. Furthermore, a rotating turret rotates the tools taken from the storage to grant multiple processing possibilities. The latest-gen user interface allows the programming of the piece in a simple and intuitive way, both on the machine and off-line, as well as the automatic management of the machine set-up.
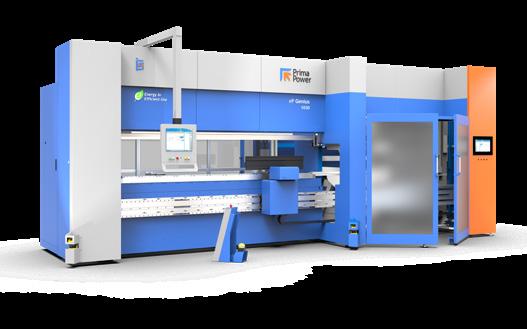
The Prima Power eP Genius will debut at Blechexpo 2019
Prima Power
Warcom BEND-MASTER
Italian press brake manufacturer Warcom has developed the BENDMASTER automatic tool change system to complement its entire bending system for greater flexibility, speed and reliability.
BEND-MASTER features a six-axis drive system that includes a dual axis racking system, single axis rotary bridge and a three-axis loading and unloading shuttle. The tool storage room includes the option of 32 metres or 52 metres of tooling capacity that can accommodate a range of selected PROMECAM and WILA punches and dies. The storage room can be installed on either the left or right side of the press brake and comprises a series of racks and drawers that hold up to 4.5 metres of tooling per rack. Optionally, two press brakes can be served by the same BEND-MASTER.
During automatic tool change, the rack that contains the tooling defined in the bend program is moved to the front of the storage room. The shuttle shifts across to the storage room and slides out the required punch or die and moves the tool to the correct location in the upper or lower tool holders. While this is happening, the storage room moves the tool rack up and down or brings forward another tool rack, so that the next punch or die is ready for loading. This saves time since the shuttle is never sitting idle while waiting for the next tool to be ready for collection.
When a punch needs to be installed in an inverted position (for example an inverted goose neck tool), the system employs a rotary bridge that sits in between the tool racks and the machine bed. The shuttle slides the punch from the tooling rack across to the rotary bridge and the rotary bridge turns the punch 180 degrees so that it faces the opposite direction. The shuttle then continues to slide the punch into position on the press brake.
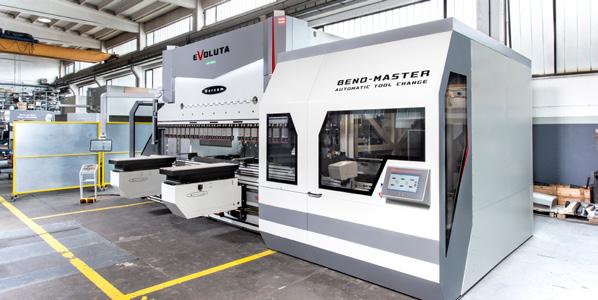
The Warcom Evoluta press brake with integrated BEND-MASTER
Warcom
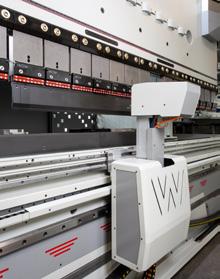
The BEND-MASTER tool shuttle loading the upper punches
Warcom
Automated workflow
Automated workflow also plays a significant part in streamlining production processes with networked machines that are more effectively managed from the office to further eliminate operator intervention in the workshop. A complete working shift of scheduled bend programs and tooling setups can be remotely transferred to the machine in advance so the next automatic tool change can commence as soon as the current job is finished.
Press brake users are also looking to automatic tool change as a solution for reducing operator fatigue and improving safety to minimise the risk of both short and long-term injuries. Many machines use heavy sections of tooling that require manual lifting by the operator or the use of lifting aids such as hoists to transfer tools to and from the machine. Injuries can result from lifting strain or the tools being dropped and there are possible longterm health implications from repeated lifting of heavy tooling over the course of many years.
Thanks to these modern automation systems, tool setups are becoming faster, safer and far more efficient. ATC press brakes are an ideal solution for managing multiple daily tool changes, complex punch and die setups and the effective storage and protection of tooling.