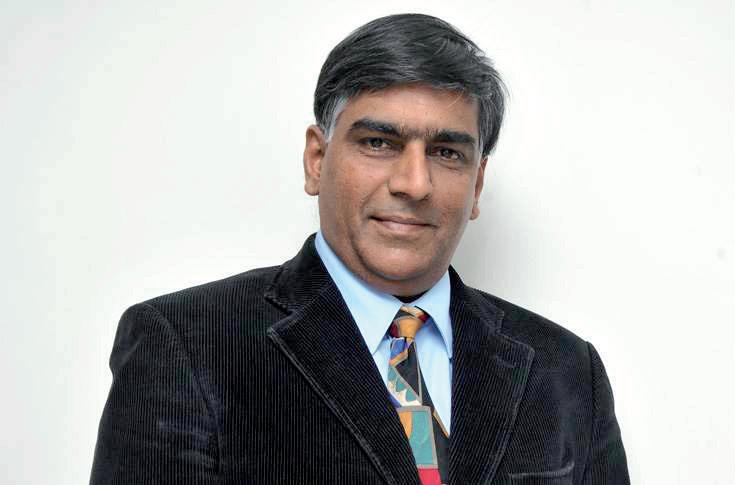
11 minute read
Minosha’s core business offering
digital printing
Minosha India: Core business off ering focuses Ricoh brand
Advertisement
> Ensuring continued supply of consumables & spares with entire range of products during the past 3 years with Ricoh support. > The new organization is managed by a new
Board assisted by a team of confident and energetic professionals eager to serve the customers. > To bring all the latest products from Ricoh to the Indian market on an ongoing basis. Minosha India Limited (Formerly Ricoh India Limited) is present in India for over 27 years and operates through a robust pan-India network of 8 offices, 100 + engineers, and over 250 + business partners. What sets Minosha India apart is that it delivers not only a wide array of products and solutions but
From Printing & Document Solutions to Cloud services to Communication Systems, Minosha has created offerings that cater to the ever-evolving and diverse needs of customers under a holistic umbrella.
Key Notes :
consistent service levels across the country. With the Insolvency Resolution Plan for Ricoh India Ltd. having been approved by the Hon. NCLT vide its Order dated 28 November 2019, Minosha India will continue as a “Ricoh Partner”. Commenting on the development, Balaji Rajagopalan, CEO Core Business, Minosha India says, “I would like to take this opportunity to thank all our partners and customers who continued to trust us and continuing the relationship. We shall strive to improve Ricoh’s legacy of providing best in class products, solutions, and service to customers.”
While the offerings from Minosha will remain the same as they were from Ricoh India, Balaji adds that all the latest products from Ricoh will be brought to the Indian market on an ongoing basis.
“However, what is more important,” he says “is that we ensured the continued supply of consumables & spares to all our customers with our entire range of products during the past 3 years with Ricoh support.”
Minosha has a long experience in the digital printing space in India. Its team both internally and the partner community will continue to serve the Ricoh brand. “We will continue to make all the offerings as available from the brand with our highly skilled workforce in order to bring in efficient document management environment at our customer place,” asserts Balaji.
Speaking about the management, he says, “The new organization is managed by a new Board assisted by a team of confident and energetic professionals eager to serve our customers. Post the implementation of the Resolution Plan, the New Promoters, a consortium of highly respected and experienced Financial Investors have facilitated our transformation to a well-capitalized and debt-free Minosha India Ltd. Minosha works with its existing robust network pan India.
From Printing & Document Solutions to Cloud services to Communication Systems, Minosha has created offerings that cater to the ever-evolving
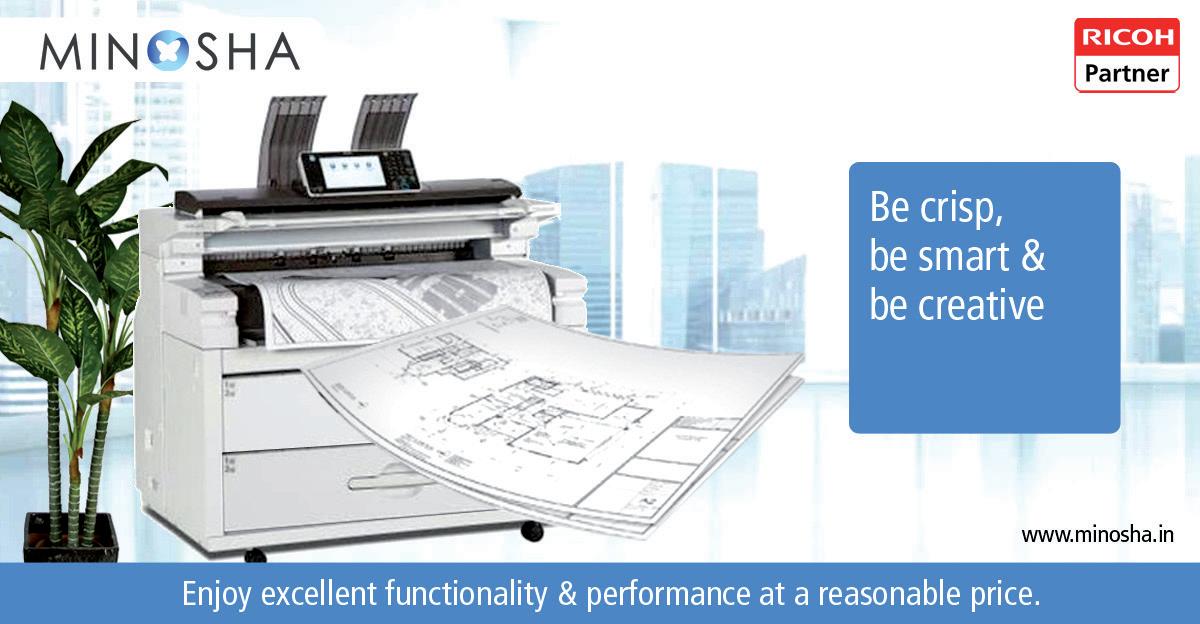
and diverse needs of customers under a holistic umbrella. “Minosha India believes that business development is compatible and integrated with social sustainability,” emphasizes Balaji.
Minosha’s TGOs offering Minosha’s TGOS model offering embraces 6 key strategies which are: Consultancy, Paper reduction, Energy efficiency, Green product design, Legislative compliance & Life cycle solutions.
Minosha’s consulting services include auditing and analyzing the customers’ current device usage, energy consumption, and paper use. “Based on this information, we create an optimization scenario that not only reduces the customers’ TCO but also limits their energy use, paper cost, and carbon dioxide (CO2) impact—a significant improvement to our customers’ business processes—which makes our customers leaner and greener,” informs Balaji.
Minosha’s’ Total Green Office Solution (TGOs) helps customers to achieve their targets by visualizing, analyzing, and minimizing their environmental impact by optimizing their office infrastructure and workflows.

The remote device management tool Remote device management tools are part of Minosha’s portfolio of Software & Device features which help in remotely managing customer devices. The key features are: • automated supplies and consumables management • automated service alerts and call registration • accurate meter counts are sent on-time with automated meter reading • dashboard and reporting for IT managers and service provider on fleet health and performance
Benefits for customer and Minosha include: • maximize machine uptime • improve customer satisfaction • reduce the need for the technician dispatch • reduce business resources to save time and cost
The remote management tool proved especially beneficial in the present tough COVID-19 related situation. It helped Minosha to monitor everything remotely from a networked engine. “It enables automatic toner ordering and in event of a breakdown examining the situation and even notifying the service partner. It can improve the efficiencies for the customers’ day to day operations,” explains Balaji.
Minosha – with offices in all metro cities + 14 warehouses +more than 250 + channel partners, 100 + engineers – covers the remotest parts of the country. Enabled by such strong system, it ensured all its customers both in MFP and Production space received excellent service and full access/availability of parts and consumables with the support of principal. It also ensured that no customer face any challenge during the transition period. “The team did a great job and in fact this effort is helping us to retain our customers including repeat business,” declares Balaji.
“We are one of the organizations offering truly the entire range of products from Multifunction to Production. We are planning to launch the new product offerings in Oct to Dec time frame,” he concludes.
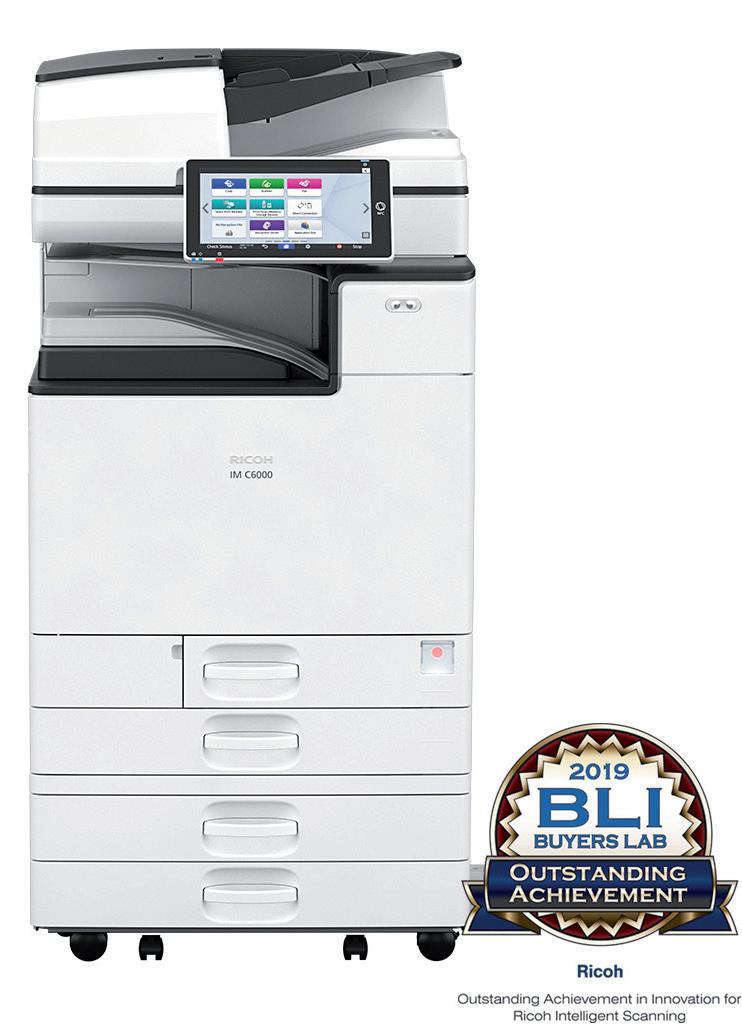
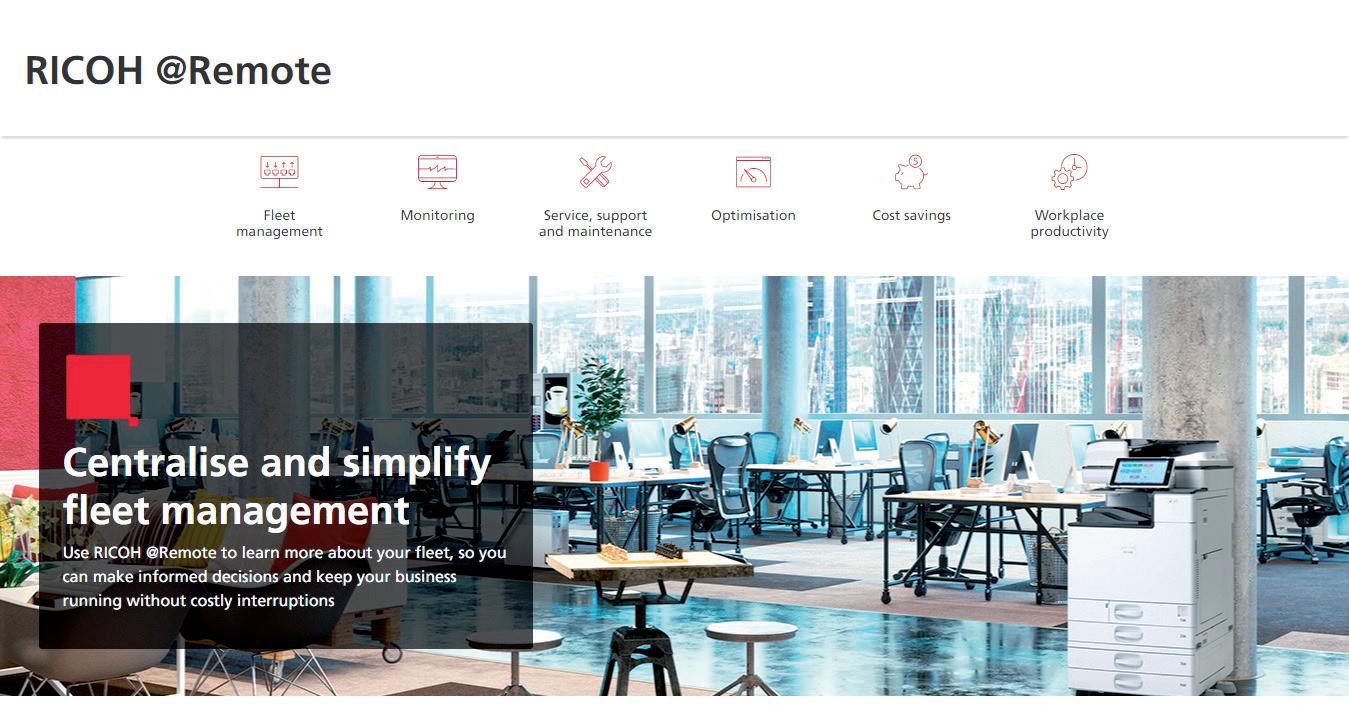
Kodak and Uteco ship third Sapphire EVO M Press
- the shipment of the third Sapphire EVO M Press for digital fl exible packaging printing heads for N. America.
The third UTECO Sapphire EVO M Press for the production of flexible packaging began its journey to the customer a few days after passing the factory acceptance test. This inkjet web press is destined for a company in North America, where it will be used for applications requiring large quantities of short run jobs. Other Sapphire EVO M Presses are already up and running very successfully at flexible packaging printers in Italy and Japan.
The Sapphire EVO M Press was developed jointly by the Uteco Group and Kodak. The mid web digital press lets flexible packaging printers migrate jobs from traditional printing processes to digital and achieve high quality results along with tremendous time, makeready and cost savings. Utilizing KODAK Stream Continuous Inkjet Technology and low-cost water-based pigment inks from Kodak, the digital press delivers excellent CMYK print quality on a variety of plastic film materials and papers. Sapphire EVO M supports a maximum web width of 650 mm and a print width of 620 mm. With production speeds of over 150 meters per minute, it Scodix, global digital enhancement solutions provider for the graphic arts industry, has launched a new productivity workflow package, Scodix Studio Station. The new workflow solution boosts press utilisation and production flexibility and can process jobs up to 60 percent faster for Ultra Digital Enhancement Press users. “This new solution allows printers to prepare more jobs, faster, handle large volume
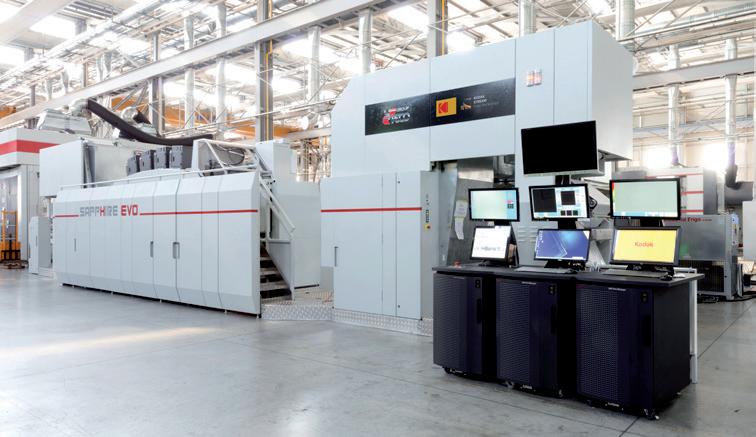
is faster than any other digital solution for flexible substrates.
The new customer chose the Sapphire EVO M Press because it offers the best duty cycle of any mid web digital press and enables more cost-effective production of volumes up to 20,000 sqm compared to analog processes. Another key benefit of the Sapphire EVO M from the customer’s point of view is that it improves their time to market enormously. Whereas production using conventional analog processes typically takes two weeks or more, it is estimated that jobs will be turned around on the new inkjet
Scodix launches Studio Station
press in as little as two days.
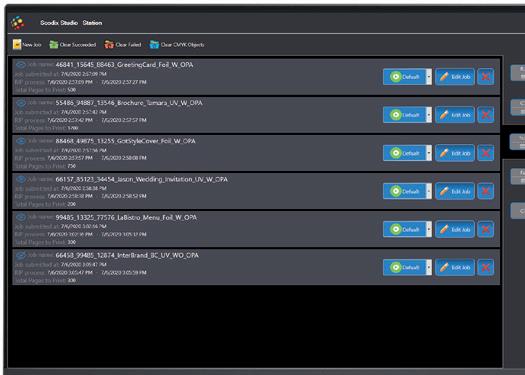

variable-data jobs and process jobs from various sources more efficiently,” says Amit Shvartz, Scodix CMO. “As every digital printer knows, uptime is imperative to profitability, and Scodix Studio Station will help printers maximize the efficiency and productivity of their digital enhancement operations.”
Scodix Studio Station is an enhancement digital front end (EDFE) with Scodix software running on dedicated Scodix hardware. The system has an external RIP server, making RIPs faster and automatic, with an easyto-use interface, and incorporates two new registration methods.
“Scodix has always provided best-in-class registration. Until now that has been achieved by detecting four OPA dots. With Scodix ARP (Automatic Registration Process), Scodix Studio Station can achieve registration down to 100µm, using corner detection or CMYK
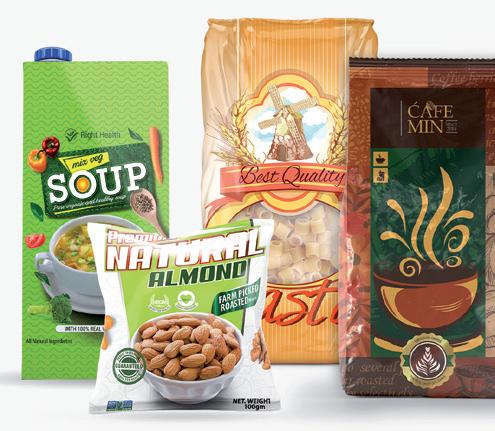
“This latest sales success is clear evidence that Sapphire EVO Presses featuring Kodak’s high-speed continuous inkjet and water-based ink technology are all set to become one of the leading solutions worldwide for digital flexible packaging printing,” said Randy Vandagriff, Senior Vice President, Print, Eastman Kodak Company.
Aldo Peretti, President and CEO of the Uteco Group added: “We’re delighted that our Sapphire EVO M Press will soon be in action in different flexible packaging applications on three continents. It provides an efficient way for packaging printers and converters to meet brand owners’ increasing need for fast, costeffective and high-quality production of short and medium runs.”
objects detection. For trade printers and PSPs receiving jobs from lots of different sources, this will simplify the process and allow them to access the full power of Scodix Digital Enhancement,” says Shvartz.
Scodix Studio Station was developed for the Scodix Ultra family of Digital Enhancement Presses and joins Scodix Studio W2P and Scodix Studio W2P Customized in the company’s workflow solutions portfolio.
“Scodix digital enhancement provides a perfect solution for businesses looking to distinguish themselves from the competition. With over 350 installations in more than 65 countries, Scodix is constantly developing new ways to add value for its diverse customer-base,” asserts Shvartz. “As with all our products, we look to provide maximum value, productivity and ROI – the new Scodix Studio Station does just that.”
Customer’s Canvas by Aurigma
Customer’s Canvas streamlines the creation of web-to-print for Shopify-based storefronts. The web-to-print software vendor announces a new service that helps printers add product personalization functionality to Shopifybased storefronts. The service is tailored to help those who want to offer online product personalization navigate the maze of web-toprint technology.
“From our experience, small and mediumsized vendors often lack the technical expertise and resources to launch a web-to-print project,” states Dmitry Sevostyanov, CEO at Customer’s Canvas. “This is a serious burden that prevents many companies from initiating them.”
The new offering includes the following steps: • Discuss the goals of the project and the outcome. During this step, company’s engineers collect the client’s project requirements and define the project scope. • Build a proof-of-concept to validate the feasibility of the project and demonstrate it to the client. • Deploy the web-to-print integration and set up the online storefront. • Train the client’s employees on Fujifilm India has contributed to healthcare during Coronavirus crisis by supplying around 200 PPE kits to medical professionals of Holy Spirit Hospital in Mumbai. These preventive healthcare utility kits for doctors
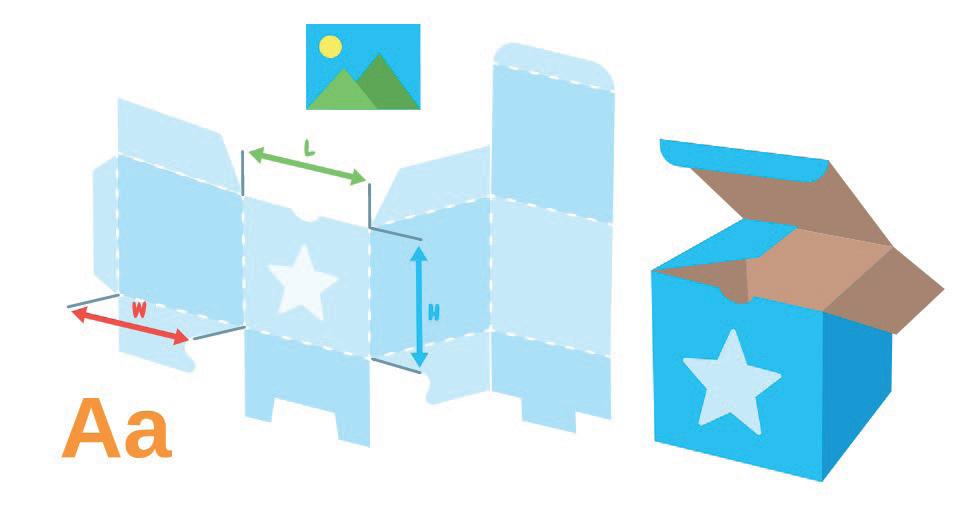
managing the storefront. Provide support and updates.
The main distinction from other solutions is that customers don’t need to have programming resources or infrastructure. Customer’s Canvas provides the complete development cycle, which is based on its own comprehensive web-to-print technology stack and vast experience in implementing web-to-print projects of any complexity.
From a technological perspective, the service is based on two main assets: a web-to-print editor and the brand-new technology called BackOffice that simplifies the workflows for managing a web-to-print integration so that even non-technical staff can handle it.
“We decided to offer a service for Shopifybased storefronts because this e-commerce include Surgeon Gown, Face Mask, Gloves, Preventive Eye wear, Hood Cap and Shoe Cover. Commenting on this, Mr. Haruto Iwata, Managing Director, Fujifilm India said, “We all are witnessing an unprecedented and difficult time of our lives due to COVID-19 global pandemic. As Mumbai battles the highest number of coronavirus cases in India, we wanted to show our support to the healthcare professionals and salute these health warriors for stepping up for the country selflessly. Committed to work together with the people of India in this hour of difficulty, we have introduced these measures to ensure adequate protective equipment and masks
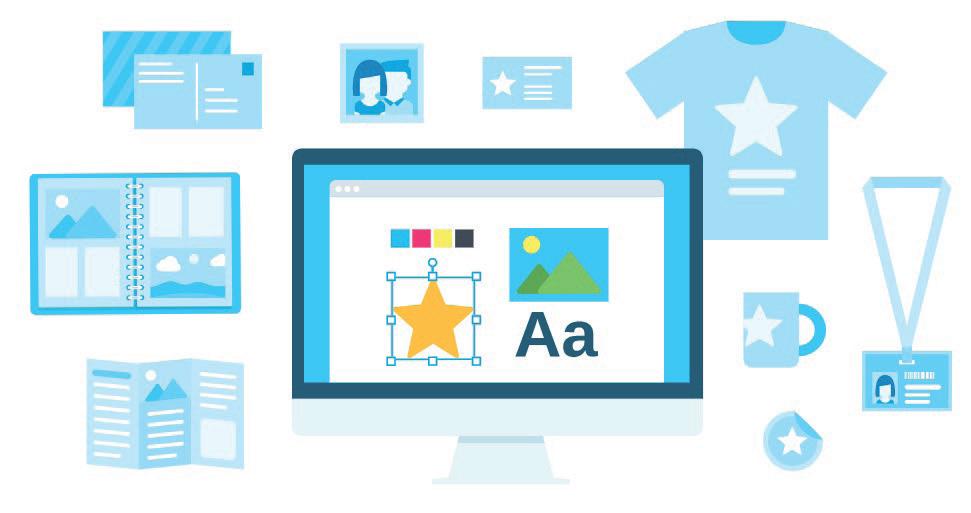
platform is easy to set up and use, yet powerful – both things that have made this platform so popular these days,” Dmitry continues. “Much like our service, Shopify helps users focus on their core business and gets rid of the headache of setup and maintenance while providing a comprehensive web-to-print solution.”
Customer’s Canvas by Aurigma is a vendor of image composition, design personalization, and prepress automation software for print service providers and marketing companies. Their flagship product – Customer’s Canvas Web-to-print SDK – is designed to streamline the creation of personalized designs online. This solution integrates into any existing or new website, allowing companies to build ordering workflows for varied print and packaging
Fujifilm India extends support in the fight against Covid-19
- supplies around 200 PPE Kits to healthcare professionals at Holy Spirit Hospital in Mumbai.
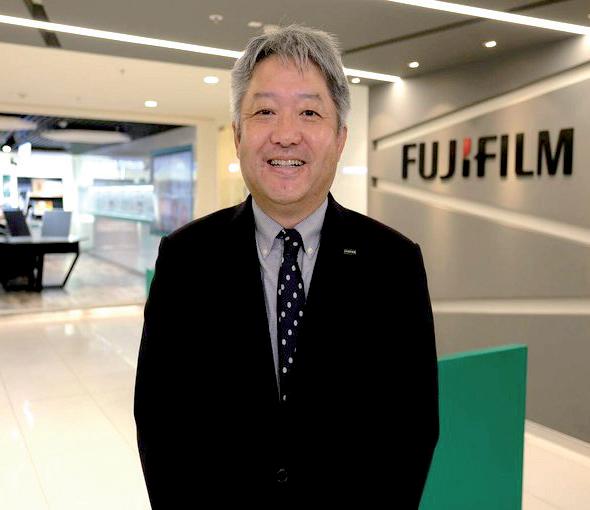
products. are available for healthcare specialists and associated workforce present on the front lines. At Fujifilm, we believe it’s time for all of us to come together and protect the humanity by acting responsibly and by doing what we can do to prevent further spread of COVID-19.”
In addition, the company is installing Computed Radiology, Digital Radiology systems and imagers across isolation wards at hospitals to ensure effective monitoring and controlling the disease outbreaks. These technologies will empower clinicians to improve efficiency and expedite the early diagnosis of the disease.