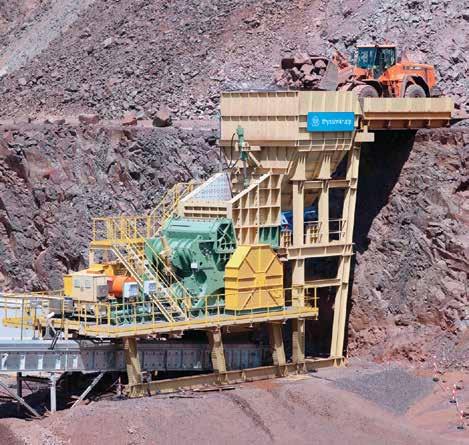
36 minute read
ECCENTRIC SOLUTION FOR SURFACE EXTRACTION
from Quarry Apr 2019
by Prime Group
A thyssenkrupp ERC 25-25 test plant at a hard rock quarry in Germany.
AN ECCENTRIC SOLUTION TO THE PRIMARY CRUSHING CONCEPT
Designed initially as a smaller option for miners in underground primary crushing operations, the eccentric roll crusher can be adapted to the quarrying application as a workable primary crusher in mobile operations above ground.
Compact but powerful, ultra-productive with excellent crushing performance, highly energy efficient and well balanced.” These are attributes featured in promotional literature describing the new eccentric roll crusher (ERC) from thyssenkrupp Industrial Solutions.
The supplier says the ERC redefines the concept of primary crushing hard rock. As such, it is suited not only for use in underground operations but also in open pit mines and quarries, where its qualities are particularly useful in semi- or fully mobile operations.
For decades, gyratory and jaw crushers have proved their worth in crushing hard rock. However, their application is limited by their high headroom, requiring capital-intensive construction of large-scale, costly caverns when used in underground operations. Moreover, in open pit operations they are only partially suitable for mobile use because of design-related residual imbalance-induced forces.
Although low-headroom crushers such as double roll crushers and sizers have become established as primary crushers in the industry, design constraints mean they are not considered capable of efficiently and economically processing hard rock.
The new ERC, with its patented design of pre-screening and crushing features, combines a compact design and the ability to crush hard rock with high throughputs in an energy-efficient manner.
OPERATIONAL BENEFITS The ERC offers significant operational benefits. Its installation height is between 20 and 55 per cent lower than similar-performing gyratory or jaw crusher options, in an overall lighter package.
At the same time, the ERC is highly productive and energy-efficient. Its kinematics with a constantly large stroke promote a more profound crushing intensity and higher throughput rates.
High inertia moments in the roll and flywheels enhance the ERC’s energy efficiency. Its integrated pre-screening device allows for efficient bypassing of fines to significantly reduce power consumption, compaction risk and the wear rate of crushing tools.
The steady rotation of the freely rotatable crushing roll, when exposed to feed material, results in exceptionally uniform wear and high utilisation of crushing tools.
The symmetrical arrangement of the eccentrically moved crushing roll allows for easy balancing, so foundation forces and vibrations are reduced to a minimum. As a result, the ERC is particularly suitable for use in semi- or fully mobile applications. Smart control is another decisive advantage. Thyssenkrupp’s patented hydraulic gap setting/retraction system allows for safe and simple automatic adjustment of the gap, liner wear compensation and release of tramp metal or other non-crushable material content.
Further, the ERC is equipped for Industry 4.0, incorporating a comprehensive monitoring system that allows for local or remote control and the automation of equipment parameters from the crusher’s display. In addition, an optional thyssenkrupp data acquisition system offers reliable recording and storage of relevant operational data for trouble-shooting, condition monitoring and preventative maintenance.
OPERATING PRINCIPLE Material is fed into the crusher by an apron feeder, push feeder or the like. Fine particles in the feed are screened out by the integrated
Figure 1. An illustration of accumulated energy in the eccentric roll crusher.
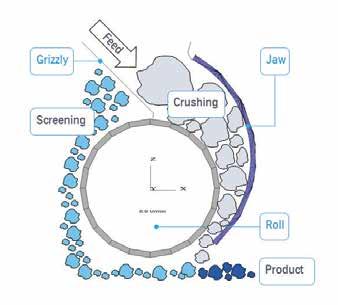
static grizzly and bypassed through the crusher housing.
Coarse particles are transferred into the crushing chamber. A rotating eccentric shaft, axially guided by two sets of roller bearings mounted in the crusher housing, generates an oscillating movement in the freely rotatable, horizontally arranged crusher roll. Consequently, the crushing gap between the crusher roll and the jaw in the crusher housing changes continuously, which means the feed material is crushed by compressive forces as it falls by gravity, until the product exits the crushing chamber at the bottom. The eccentric shaft is driven by a V-belt drive, with the inertia of two flywheels mounted onto the shaft accumulating crushing energy (see Figure 1).
The kinematic principle applied in the ERC ensures the stroke remains the same throughout the entire crushing chamber. This unique feature significantly increases the comminution intensity compared with commonly used crushers. The jaw itself does not move during the crushing process but is supported by a fully hydraulic gap setting/retraction system with a patented safety device.
This system allows for automatic adjustment of the gap, compensation of liner wear and release of tramp metal or otherwise uncrushable feed material content.
After the detailed design of this roll crusher, a prototype of the machine was built and extensively field-tested in a six-month campaign at a hard rock quarry in Germany.
The crusher model ERC 25-25 selected for this purpose has a crushing roll of 2500mm in diameter and width. The feed opening to the crushing chamber is 2500mm wide and 1230mm high.
Both the coarse and fine run of mine feed were processed, plus selected lumps of up to five tonnes. The equipment parameters were varied with regards to eccentric shaft speed and gap closed side setting (CSS). The corresponding operating data was collected with and without the integrated grizzly.
PILOT PLANT During this pilot operation, average capacities of 2000 to 3000 tonnes per hour (tph) were recorded.
The desired product size of 0-200/x mm was achieved at various settings, with P 80 at CSS of 140mm recorded with about 130mm. The integrated grizzly effectively bypassed fines and contributed between 30 and 40 per cent of the total equipment capacity. The power consumption at nominal capacity ranged between
200kW and 500kW, depending on crusher settings. However, the high energy efficiency of the ERC was confirmed by the power consumption of 0.1 to 0.2kWh/t.
The ERC from thyssenkrupp offers new standards in the primary crushing of hard rock thanks to features not found in conventional crushers.
This opens up numerous new application areas in the processing of mineral raw materials. The ERC roll crusher series comprises four units, ranging from the ERC 18-14 entry model to the top-end ERC 25-34 model, with throughputs between 600 and 10,000 tph.
The first ERC for commercial operation – the ERC 25-25, capable of generating an output of 8000 tph – has already been sold and will be on show at the bauma 2019 trade exhibition in Munich, Germany in April.
“We are constantly seeking new solutions for our customers that improve crusher availability and efficiency and reduce installation and operating costs,” said Detlef
Figure 2. The main components of the ERC 25-25 crusher.
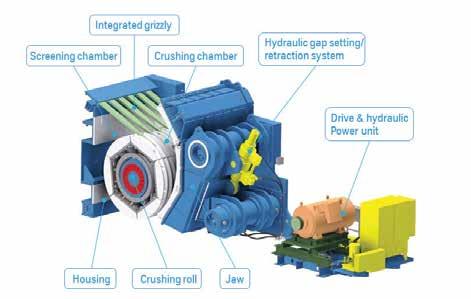
Papajewski, the head of mineral processing at thyssenkrupp Industrial Solutions’ mining technologies business unit.
“With the new ERC we have developed a technology that is the first of its kind. Its innovative design combines the advantages of conventional primary crushers with solutions to their typical disadvantages, such as large height. As a result, the ERC can be used in underground and surface mining operations and in quarries to process ore and hard rock more effectively.” •

Source: thyssenkrupp Industrial Solutions
MORE INFORMATION & FURTHER READING Szczelina P, Drescher F, Silberman F. Compact, robust and high performance: New ERC 25-25 eccentric roll crusher revolutionises primary crushing in underground mines. A thyssenkrupp reprint from AT Mineral Processing Europe 05; 2017. thyssenkrupp-industrial-solutions.com/media/ products_services/mineral_processing/crushers/ sonderdruck_thyssenkrupp_screen_300617_final.pdf
LARGE, HIGH PRODUCTION JAW CRUSHER DEBUTS IN AUSTRALIA
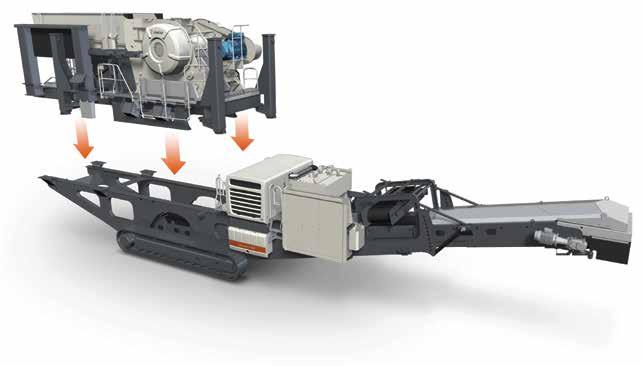
Tutt Bryant Equipment (TBE), the national distributor of Metso mobile plant and equipment, will launch a new primary crushing solution – in the form of the Metso Lokotrack LT130E mobile jaw crushing plant – in Australia this month.
The new Lokotrack’s heavy-duty design offers a reliable, high capacity solution, even with the hardest feed materials. For optimised energy efficiency for crushing operations, the mobile jaw crusher can run on an external electrical drive or, in locations where this is not possible, an integrated Caterpillar C15 engine and 500 kVA generator power package. The LT130E incorporates a Nordberg C130 jaw crusher for large-scale quarrying applications. A deeper 1000mm (40”) feed opening can handle coarser feed material and greatly reduces the need for blasting. A small nip angle and kinematics ensure aggressive crushing along the whole length of the crushing cavity and for all rock conditions.
The tracked jaw crusher is easy to adapt to existing processes. You only need to adjust the height of the main conveyor hydraulically and start the process with an advanced Metso IC (intelligent crusher automation) control system. It connects the unit to the existing Lokotrack crushing and screening plants with a wireless Metso ICr remote monitoring system or an interlocking cable. All maintenance locations are easily accessible, making daily routines easier and safer.
The LT130E can be optimised to move smoothly between different sites. All the electric and hydraulic connections have quick couplings for easy disassembly. Optimised lifting points, along with user-friendly and safe hydraulic features, reduce downtime, while a new easy split feature makes portability and set-up much easier. For contracting purposes, the plant can be set up within a matter of hours.
The easy split advantage utilises hydraulic
The new, large Lokotrack LT130E is built for optimised energy efficiency in crushing operations.
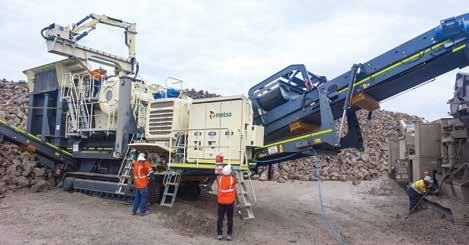
SPECIFICATIONS: LOKOTRACK LT130E* FEATURES TYPE/CAPACITIES Transportation dimensions (depending on specification) 21.5m (length) x 3.5m (width) x 3.85m (height), 132 tonnes (weight) Crusher Nordberg C130, with feed opening of 1.3m x 1m (51” x 39”) Engine Caterpillar C15 Acert engine (403kW, 500 kVA generator) – external power source option. Feed hopper volume 11m³ Feeder B13-50-3V Main conveyor H14-16E (with adjustable height) Process control Metso IC900
*Remote monitoring system and optional extras available
cylinders to lift the crusher and feeder above the chassis for transfer to a standard trailer (illustrated above). The chassis of the LT130E can be driven to the trailer by using a remote controller – just as with all Lokotrack mobile plants.
TBE is the largest multi-franchised equipment distributor in Australia, with more than 80 years of experience supplying a quality range of equipment and services to mining, quarrying, construction, recycling and other Australian industries. It has been Metso’s exclusive distributor of Lokotracks in Australia since 2012 and more recently had the territory extended into Papua New Guinea.
TBE provides national coverage with service centres and equipment distribution. •

KIMBERLEY PRODUCER TOPS UP ITS HIRE FLEET WITH MOBILE JAWS
The Kimberley and Pilbara regions of Western Australia and the Northern Territory are some of the hottest, most remote areas of Australia, where the faint hearted do not venture, let alone maintain a professional, diverse contracting business for nearly 20 years. The Kimberley Quarries team thrives in this hostile, competitive environment.
Since 2000, Kimberley Quarries has become a successful company with extensive experience supplying products and services to the mining and construction industries. The company operates the Nillibubbica Quarry, 100km east of Broome and contracts out quarrying, mobile crushing and screening, drill and blast and equipment hire in the Kimberley, Pilbara, and mid-west regions, and the Northern Territory.
Kimberley Quarries promotes a quality service and continually produces high specification products for clients with a focus on repeat business. It is a quality assured company, maintaining an excellent safety record, good customer relations and consistent supply of quality products.
The company has many years of material supply to a regional customer base that includes Mineral Resources Western Australia, numerous shires and private contractors developing highly specified infrastructure projects like airports.
Some of Kimberley Quarries’ large repeat business clients include the major construction materials houses of Boral, Holcim and Adelaide Brighton, which have all utilised the contract quarrying and crushing services for the numerous quarries in the region. They have also engaged Kimberley Quarries on major infrastructure projects at Wheatstone, Cape Preston, Cape Lambert, Gorgon Projects and Tindal Airbase, with highly specified products supplied and challenging quarantine requirements met. Kimberley Quarries has 12 quarry managers, eight of whom have in excess of 20 years’ quarrying experience. The management team recognises the importance and benefits of a well trained work force and believes training increases productivity, improves quality, promotes a better safety culture and fosters more job satisfaction. As a result, there has been a very low turnover of employees that has lead
Quality assured alternative wear parts for all crushing equipment


• Manganese & alloy steel wear parts • Bowl, mantle and jaw liners • Concave segments • Blow bars & hammers • Auxillary wear parts • Mining & Quarrying spares • Mill liners • AUD $5 million manganese in stock
lift jaw & cone liners with MANGASAFE ™
Quality Assurance Standard AS/NZS ISO 9001:2008 covered wear parts for all popular crushers in stock Assuring you of our careful attention at all times
MELBOURNE 6 Dib Court Tullamarine VIC 3043 F 03 9338 0680 P 03 9338 0200
PERTH 88 Barberry Way Bibra Lake WA 6163 F 08 9434 5515 P 08 9434 5552
BRISBANE Unit 2/23-31 Meakin Road Meadowbrrok QLD 4131 F 07 3382 0098 P 07 3801 8153
CHILE Santiago
to the continuity of an experienced team.
After many years of working its equipment hard in an extremely challenging environment, the company considered replacement options for its ageing primary jaw crushers. Its research lead to Tutt Bryant Equipment (TBE), the national distributor of Metso’s Lokotracks. With a few local references to draw from, the Kimberley Quarries management decided to purchase the Lokotrack LT120 jaw crusher.
“The key points that lead to this decision was the machine’s safety, high power crushing, ease of maintenance and its transportability,” Kimberley Quarries’ Pilbara area manager Dave Young said.
Metso’s uncompromised safety approach to the LT120 has led to feed hopper side wedges being hydraulically secured from the ground. The Metso IC control unit provides a safe and easy operation. All conveyors have lanyards attached on the sides, with the ability to be switched for isolating the unit during maintenance. Proper stairs and access platforms create a safe working environment. A reliable, efficient mobile crushing plant is a sum of several factors working together smoothly. The new Metso C120 jaw crusher, with its 1200mm x 870mm (47 x 34”) feed opening, provides more capacity in the toughest applications. The hydraulic drive encourages trouble-free operation and enables the crusher direction to be changed in case of blockage. The Caterpillar C13 Acert engine module provides optimal power to the high inertia flywheels.
Quick, easy maintenance was a major driver in the Lokotrack LT120’s design. The jaw die bolts are easily accessible, and the composite covers protecting the flywheels can be safely and easily opened. Good access and proper platforms make a difference in daily operational safety.
Thanks to compact dimensions combined with agile tracks, the Lokotrack LT120 is a very portable unit. The chassis design with good clearance at both ends enables simple loading onto a trailer. The feed hopper sides equipped with a patented securing system allow the unit to be ready for crushing only moments after arriving on-site. The side conveyor stockpiling capacity can be easily installed on either side of the unit.
TBE’s Metso technical support team delivered and commissioned the first LT120 unit to Kimberley Quarries in January 2018. Within a few weeks of operation, Kimberley Quarries placed the order for another unit, which arrived in Perth in March 2018. TBE’s WA branch service team performed a quick turn-around, preparing the unit for immediate dispatch to an awaiting Kimberley Quarries project. Both units have since exceeded more than 1000 hours of operation each.
TBE continues to support Kimberley Quarries with parts and service support as required, much to Young’s satisfaction. “The Tutts guys have really looked after us and the machines are performing better than expected,” he said. •
Source: Tutt Bryant Equipment
WHEN WORN OUT BECOMES NEW AGAIN
SANDVIK REBORN SOLUTION - CONE CRUSHERS
In these cost-conscious times for our industry, replacing a complete crushing system is often not feasible or even necessary.

Our Sandvik REBORN solution rebuilds your crusher system by exchanging your worn out Sandvik crusher for a new one, and reutilizing your crusher auxiliaries and infrastructure. Your new crusher is backed by our three-year extended warranty*, and includes on-site services to help you maximize productivity.
A brief introduction to Komatsu’s expanded crushing product line

In the wake of Komatsu’s acquisition of Joy Global in 2017 to form Komatsu Mining Corporation, the company has significantly expanded its Joy crushing product line. The company now offers a complete range of feeder breakers, reclaim feeders and sizers – suitable for a wide range of quarrying and processing applications.
n FEEDER-BREAKERS Joy feeder-breakers are derived from a product line that Joy Global acquired from Stamler Corporation in 2006. More than 4200 feeder-breaker installations have been supplied to quarrying and processing operations around the world. Joy feeder-breakers consist of dual-strand conveyor chain which drags raw material under a breaker shaft fitted with picks. The advantage of a feeder-breaker is that the material flows horizontally through the machine, so the overall installation height can be significantly lower than other crusher types of comparable capacities.
n RECLAIM FEEDERS Joy reclaim feeders are similar to feeder-breakers except there is no breaker shaft; instead the feeder typically has a pile of material which it reclaims on to a conveyor belt. Reclaim feeders can be fed with a dozer, excavator or belt conveyor.
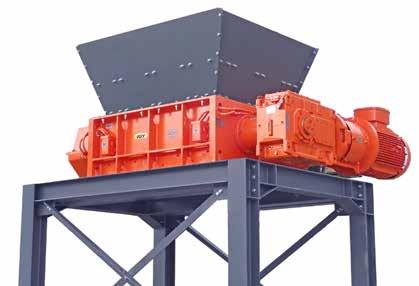
n SIZERS Komatsu also now offers both primary and secondary sizers. Joy primary sizers feature pick technology developed for Joy feeder-breakers, shearers and continuous miners. A sizer drives a pick into the mineral, which breaks the rock in tension, taking advantage of the fact that the tensile strength of most minerals is 10-15% of their compressive strength. Joy sizer picks have been designed to minimise labour requirements, so no torch, welding or special tools are required to remove and replace picks. Joy picks as standard have a tungsten carbide insert, with a chromium carbide overlay available as an option for abrasive applications. Joy primary sizers can produce a product size of between 150-250 mm. Our secondary sizers can be configured to output product sizes of -100 mm, -50 mm, -38 mm or -25 mm. Joy secondary sizers feature bolt-in wear castings, with weld on white iron or alloy teeth depending on application.
n SIZER APPLICATIONS Sizers are a good crusher choice for operations that have to handle sticky materials. Primary sizers have cleaners which scrape the sticky material off the rolls, while secondary sizers have teeth that mesh together to displace material. Sizers are also a good choice if fines generation is a concern. Essentially, a sizer acts like a screen, letting undersize material pass through unaltered, but crushing the large lumps. This allows sizers to achieve very high capacities in a compact package, making them particularly suitable for mobile applications.
The Sandvik Reborn solution enables old crushers to be rebuilt from the ground up, aided by the latest advancements in technology.

BUY NEW OR REBUILD: DOES A ‘REBOOT’ OFFER A NEW LEASE ON LIFE?
Is your crushing plant ready for an upgrade or complete replacement? Turkka Kulmala says a new alternative to the conventional crusher overhaul, with innovative thinking, is a rebuild solution.
Conventional wisdom in crusher maintenance involves two basic approaches: regular replacement investments in new crushers, or overhauls specified for the conditions at hand. It’s not unlike buying a new car at regular intervals as opposed to making a continuous effort to keep an old car in a good state of repair.
Both approaches, naturally, have their merits and disadvantages. Investing in regular replacements increases capital spending, but helps to minimise maintenance costs. Extended ownership with regular overhauls can be financially more attractive, but the owner may have to accept longer downtimes.
Some suppliers to the industry offer a third way, such as Sandvik’s Reborn rebuild solution, which could be compared to upgrading a used car with a new engine. Reborn combines a 100 per cent new, factory-built Sandvik crusher with a systematic service package, where usable auxiliaries and surrounding process infrastructures are reutilised.
A part of the Sandvik 365 service concept, the Reborn rebuild solution is combined with a three-year extended warranty that applies to all major components, including onsite service. ‘BORN AGAIN’ Reborn essentially standardises the rebuild process into a systematic, six-stage service product: pre-feasibility assessment, budgetary quotation, crusher auxiliary audit, new crusher installation under Sandvik supervision, on-site training, and regular condition (see boxout).
The exact scope of each Reborn package is defined during the pre-feasibility study, depending on the specific crusher model. The standard scope in all cases includes a replaced crusher and hopper, a bottom shell liner upgrade with a hard, highly wearresistant steel grade and a new offline filter. The hydroset cylinder protection is also included as a default for all models.
The most commonly usable auxiliaries and infrastructure surrounding the crusher include the main motor, drive system, lubrication and hydraulic systems, coolers, control, automation and electrical components, foundation, feeders and conveyors.
The pre-feasibility assessment reveals whether the auxiliaries can be reused with normal spare parts exchange and modifications. If so, this results in a quote at a fixed cost and scope.
This can be followed by a Reborn auxiliary audit – a full inspection of all auxiliaries to list the actions to be taken prior to, or in combination with, the Reborn installation.
INSPECTIONS, TRAINING
Inspection: Three to four inspections are planned and conducted annually by certified engineers. Generally, they coincide with liner changes, to avoid downtime. They take one to two days, and the data gathered helps diagnose maintenance issues. From there, corrective action can be enacted immediately. This is a proactive, predictive and preventative maintenance philosophy, saving the producer time and money in the long term. A three-year extended warranty is included in the offering, which helps maximise equipment uptime and addresses ongoing issues.
Training: Sandvik not only supervises installation but provides on-site training to equipment operators. It helps new and veteran workers get to grips with the machinery quickly, ensuring they respond effectively to maintenance challenges. The two and a half days of training consists of theoretical operations, plus maintenance training, equipping operators with the knowledge to keep equipment performing at its peak. It also prepares employees for the tasks they will face when operating the unit in its real-life environment.
The installation under Sandvik supervision is followed by on-site training to lay a solid foundation for effective operations and crew safety. Periodic condition inspections verify that the specifications and targets are met and that preconditions for continuous improvement exist.
LIFE CYCLE ASPECT Reborn replaces the complete crusher, to upgrade its performance and restore availability rates close to those of a new unit at a lower operating cost, yet with significantly lower capital expense compared with purchasing an entirely new crusher system. A key feature of the Reborn solution is a pronounced and integrated life cycle aspect, leveraging the expertise advantage of the original equipment manufacturer compared with third-party overhaul firms. The extended three-year warranty covers 85 per cent of the list price of the specified components, typically including top and bottom shell, main shaft and head centre, gear and pinion,
CAPITAL AGGREGATES/DELTA MATERIALS, MARBLE FALLS, TEXAS, USA
The US aggregates producer had a Sandvik CS440 cone crusher installed about 15 years ago for secondary crushing of competent sandstone.
The feed material is from a primary jaw crusher, while the crusher itself feeds a tertiary crusher further downstream.
After 15 years of operation, the CS440 had started to suffer mechanical issues. However, the ASRi 2.0 setting control system was recently updated.
As the lubrication system was also in good repair, only the crusher required refurbishment.
The Sandvik Reborn solution offered a cost-effective alternative to a complete overhaul by replacing only the worn-out components, with minimal downtime. Reliability benefits were achieved by solving the mechanical problems, compared with the potential problems after an off-site weld and machining repair.
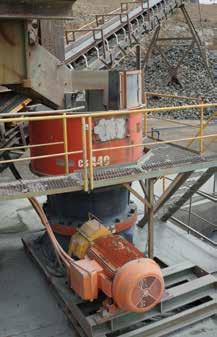
sales@precisionscreen.com.au precisionscreen.com.au 1800 727 991 (Free call AUS)
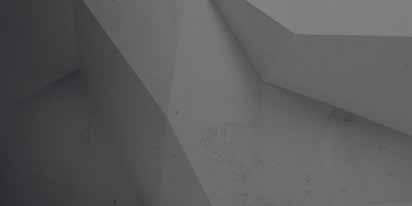
« MOBILE CRUSHERS « MOBILE SCREENS & SCALPERS « CONVEYORS & STOCKPILERS « WASHING PLANTS & PUGMILLS « HAMMERS & ATTACHMENTS DRY HIRE AVAILABLE PARTS & SERVICE SUPPORT


hydroset cylinder and cylinder cover, piston, hub, dust collar and eccentric.
On-site training responds to needs arising from matters such as changes in personnel, which can also create maintenance challenges. A two and a half day theoretical operation and maintenance training course gives the operators a comprehensive introduction to maintaining and operating the unit properly in its real life environment, giving them the practical skills to maintain optimal performance.
Three to four annual condition inspections by certified engineers are planned to coincide with liner changes, to avoid extra downtime. Measurements are carried out and reported according to a set protocol designed by Sandvik. The one to two days of inspections provide data to diagnose any progressing maintenance issues and to propose corrective actions as required.
The aim is a proactive, predictive and preventative maintenance philosophy: the owner can draw from accurate data-based predictions and prevent any issues in a
Sandvik Reborn offers a completely new crusher, but makes use of the existing infrastructure.
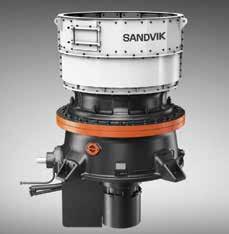
controlled manner before they become acute. For example, the status report can include a quote for an imminent bearing change that should advisably be scheduled for the next maintenance stop.
End users most likely to benefit from the Reborn service are mines and aggregate
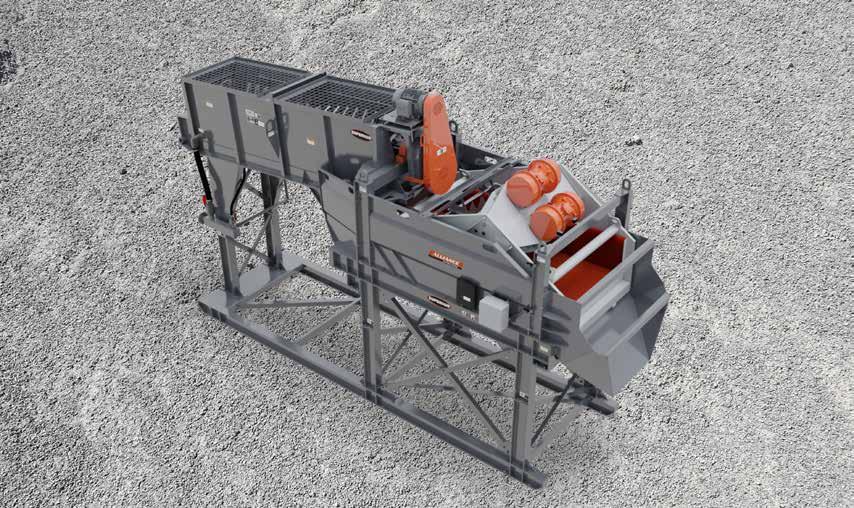
producers processing hard types of rock and thus experiencing greater than average wear and tear.
DOWNTIME SOLUTION Another area where the solution offers high potential includes any operation with low downtime tolerance.
The well defined service concept with clear component interfaces serves to eliminate uncertainties resulting in downtime. It eliminates the risk of omissions in orders of spare parts, typical with regular overhauls. In essence, the Sandvik Reborn solution keeps the crusher continuously updated with the latest design upgrades. It offers full reliability and performance levels comparable with a new crusher, plus additional value – the extended warranty and service offering – at a very competitive cost compared with a complete overhaul. •
Text by Turkka Kulmala. Originally published in Solid Ground magazine, a Sandvik Rock & Technology publication. Visit solidground.sandvik
Industries P/L
ALLIANCE Low Water Washer - the most efficient way to wash Man Sand
Load it right

First time Every time
TRADE APPROVED

Simple, accurate on-board weighing solutions Save time, increase productivity, reduce fuel and machine wear with RDS weighing solutions for loaders, excavators and telehandlers.

Leading solutions from the world’s technology innovators, backed by Position Partners’ unrivalled national support and expertise.
1300 867 266 info@positionpartners.com.au www.positionpartners.com.au Australia • New Zealand • SE Asia Get in touch today:
TERTIARY CONE DELIVERS MORE PRODUCT, LESS REPEAT LOADS
A US-based quarry producer and a supplier have successfully collaborated on the installation of a tertiary cone crushing plant with the aim to minimise recirculating loads.
Maintaining optimum yield from any cone crushing circuit is achieved by combining the latest cone crushing technology with solid application expertise and highly responsive equipment life cycle management.
The latter is essential when fine-tuning a crushing circuit for peak performance – and this is best driven by a producer/equipment manufacturer “partnership” that ensures the highest production capacities and the lowest percentage of recirculating loads.
Circuits with high recirculating loads eat up more capacity and wattage in the crusher while also increasing wear, and unnecessary recirculating loads send saleable material back to the crusher rather than to the finished product stockpile.
Minimising recirculating loads is an imperative for producers such as the RiverStone Group, which operates 15 quarries throughout the US states of Iowa and Illinois.
As a family owned business since the late 19th century, the company “prides itself on pushing the envelope in productivity and innovation”.
RiverStone is known for its abundance of Class A quality stone products, which meet stringent US quality assurance standards. At its Colona, Illinois-based Cleveland Quarry, the company recently upgraded its plant with higher capacity primary and secondary crushers. For optimum yield of finished product at its tertiary circuit, it installed a new P500HD Patriot cone crusher manufactured by Superior Industries.
The result has been greater plant uptime, long-term efficiency, reduced wear costs, minimal recirculation load and increased production capacities at lower costs per tonne. Delivering a speedy return on investment, the site has nearly doubled its tonnes per hour output since the installation of the new crushers.
Cleveland Quarry’s plant superintendent Scott Skerston calculated the circulating load
RiverStone’s plant superintendent Scott Skerston calculated the favourable circulating load ratios of the P500HD Patriot cone crusher.
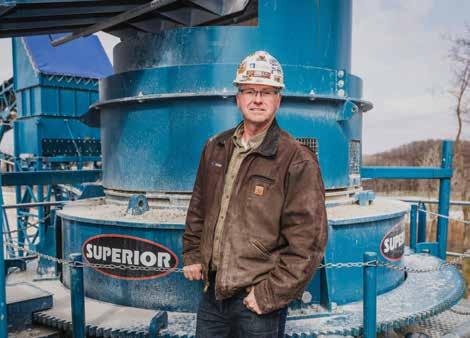
ratios of the Patriot cone crusher. He found that at a closed side setting (CSS) of 25mm, the cone processes finished product at a 78 per cent throughput; and at a 12.7mm CSS, the throughput percentage reaches a high of 83 per cent.
“We’re getting maximum efficiency, and very little recirculating load, while averaging 80 per cent of our crushed material going directly out to the finished, saleable product stockpile,” Skerston said.
In part, he attributes this to the cone’s spiral tooth bevel gearing system, which “engages more gradually, giving an efficient transfer of horsepower to the rock, rather than to the structure of the machine”.
As a result, the cone is proven to perform at higher speeds with less noise and vibration.
“With its uptime and availability at more than 97 per cent, the Patriot cone maximises our production of Class A quality concrete, stone and asphalt chips,” Skerston said. “Before we added all the new crushers, we ran at just over 400 tonnes per hour. Now we’re running steady at 800 tonnes per hour due to our crushing advancements.”
NEXT LEVEL CRUSHER TECHNOLOGY Skerston said the design improvements on the Patriot cone crusher made it far more durable, reliable and user-friendly than olderstyle cones.
Unlike most crusher models, he said, the Patriot cone crusher’s counter-shaft spins in a counter-clockwise rotation, which causes the crusher to open if clamping pressure is lost, reducing the risk of catastrophic failure. “This feature literally saved us last production season when a simple solenoid valve failed and would not reset the clamp pressure,” Skerston said. “The counterclockwise rotation allowed the cone to open, preventing any damage to internal
components. When older-style cones lose clamp pressure, the bowl tightens down, often snapping the shaft and leading to machine failure.”
Another feature that prevents costly damage to the new cone’s crushing chamber is the tramp relief system.
“First, it’s designed with fewer accumulators for minimised maintenance, but most important is the inclusion of a secondary pressure relief valve that ensures the crusher will open if a tramp event occurs,” said Superior Industries’ crushing product manager Michael Schultz, who has more than two decades of crushing industry experience. “This means that even if an accumulator fails, the secondary relief valve will provide immediate pressure relief, allowing the crusher to open.”
In addition, Schultz points to the inverted design of the tramp release cylinders, where the hydraulic cylinder rod seal is not exposed during operation, greatly reducing the potential of contamination and failure.
The P500HD Patriot cone crusher has undergone significant design improvements.

He said the Patriot cone crusher was more robust than the typical cone, because “it’s beefed up to increase the strength of the unit with a heavier duty adjustment ring, base frame, eccentric and clamp ring, and bowl castings. We’ve made sure it will withstand the toughest applications.”
AUTOMATION PACKAGE Schultz said Vantage Automation, an inhouse cone crusher automation package, was the latest addition to the Patriot series. “It’s completely built in-house by the Superior Industries team, with no third parties involved, allowing one-call service and support, and offering a complete automation package that is far more affordable than competitive systems.”
Vantage Automation monitors all the crusher’s vital functions.
“An automation package should be simple and easy to use. Importantly, it acts as a warning system that alerts operators to conditions such as bowl float, excessive amperage or temperatures, and lubrication or low-flow oil issues,” Schultz said.
“Our mission is sharing hands-on expertise and partnering with producers throughout the
RADIAL AND SUPER STACKERS - CRUSHING AND SCREENING - WASHING AND CLASSIFYING
M O D U L A R - B R E A K E R S A N D B O O M S Y S T E M S M A T E R I A L S H A N D L I N G
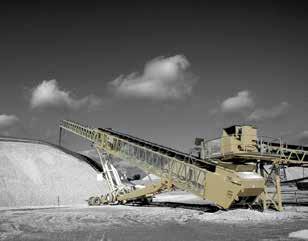

F I X E D
M O D U L A R

B O O M S Y S T E M S T R A C K
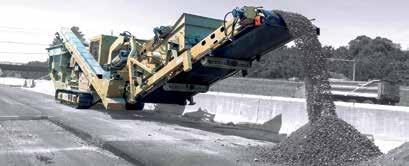
R E N T A L
life cycle of the plant and its components.” As the RiverStone Group upgraded its crushing circuits, Skerston worked closely with Chris Wade, a customer service and technical support technician for Superior Industries, which operates a 21,336m 2 crushing equipment and parts distribution centre in Pekin, Illinois.
“Chris, along with the service and parts support team, have specialised in cone crushing for many years. They know how to analyse our application to make us more efficient,” Skerston said.
“It’s such an advantage to rely upon the knowledge of the equipment manufacturer. The product and parts support is excellent, and the Patriot cone does just what it’s designed to do.”
In Australia, the distributor of Superior Industries’ crushing, screening and washing equipment is 888 Crushing & Screening Equipment. •
Source: Superior Industries
WHAT IS VANTAGE AUTOMATION?
Superior Industries’ Vantage Automation software monitors and controls crusher parameters, automatically adjusting unit settings or shutting down the machine when harmful conditions occur. Designed for simple, straightforward operation, the software maintains optimum crusher production without operator interruption. It is applicable for the Patriot range of P200, P300, P400 and P500HD crushers. The software is available on a HMI touchscreen, which comes as part of the package, along with a 10-metre tether cord for remote locating. The touchscreen virtually eliminates the need for electrical push buttons and operator intervention, meaning motor starts and stops can be safely controlled from the pad itself.
The software monitors CSS, amperage draw in real time, liner wear conditions, and the counter-shaft RPM sensor, and can
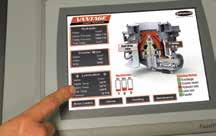
generate performance analysis reports. It will also alert users to potentially harmful conditions, such as lube oil temperature and pressure, lube filter condition, hydraulic clamp and tramp releases, ring bounce/ bowl float, lube oil and hydraulic tank levels, and the eccentric bushing temperature.
Vantage Automation also provides access to Superior’s in-house engineering team, allowing users to directly ask questions of the source developers.
JZi\\e`e^D\[`XJfclk`fej
N\f]]\iXelegi\Z\[\ek\[c\m\cf] jlggfik]fifliZc`\ekj`eZcl[`e^1
JZi\\e`e^d\[`Xj\c\Zk`fe JZi\\eljX^\XeXcpk`Zj KiX`e`e^ GifZ\jj`dgifm\d\ek DX`ek\eXeZ\jlggfik
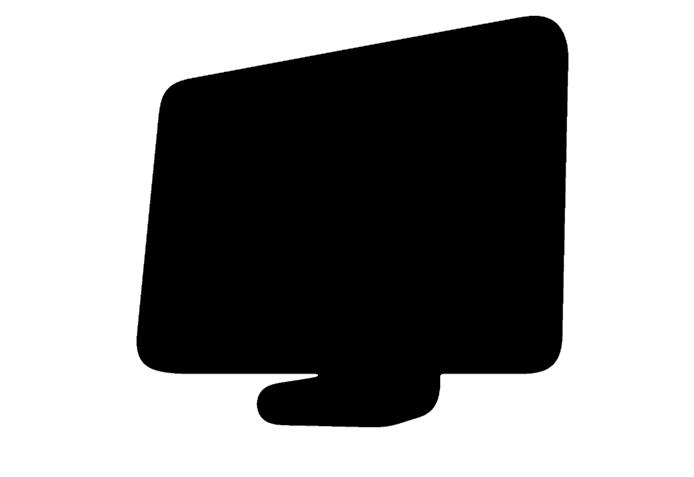
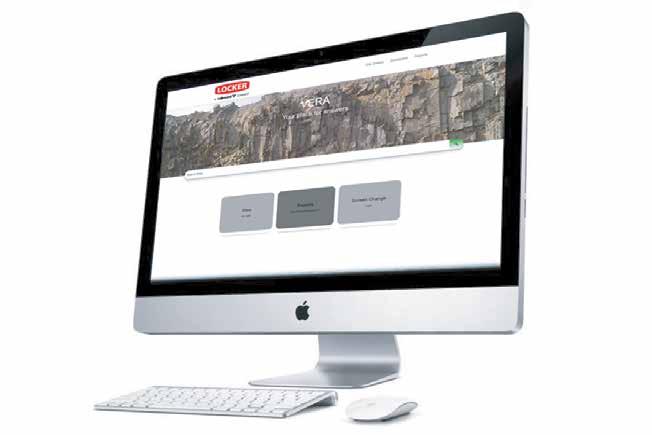
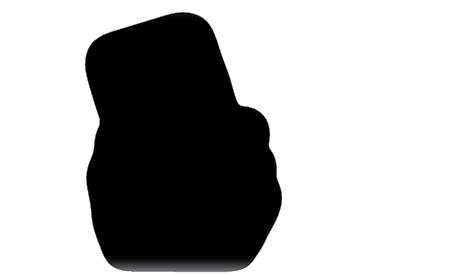
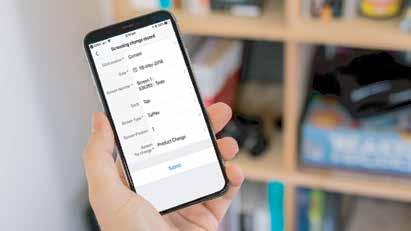
:fekXZkpflicfZXcjZi\\e`e^ \og\ikkf[`jZljjpflij`k\
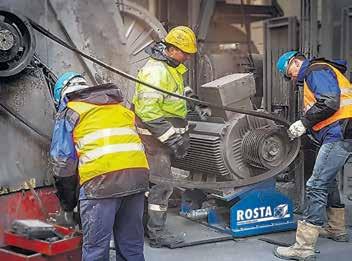

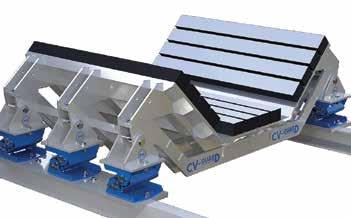

‘ACES IT’ WITH UPSIZED SCALPER FAMILY BUSINESS
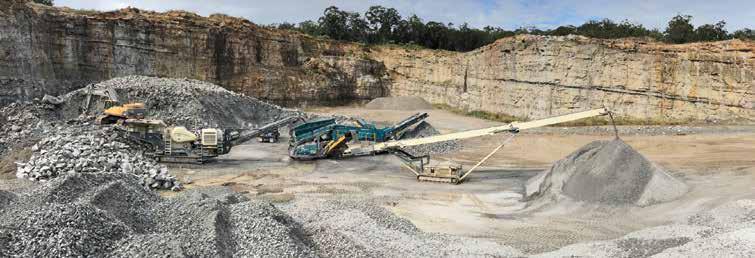
A family quarrying business has never been busier, thanks to local and national infrastructure project demands. The task of meeting the hunger for construction materials has been made easier by the acquisition of an enlarged scalper to the company’s mobile fleet.
Quarrying runs through the Lewis family’s veins; its involvement in the industry dates back to the early 1980s. The family business started as a small road construction business, winning materials with a dozer and loader.
Brian Lewis, the owner of Lewis Quarry, recalls that crushing rock began with a jaw crusher comprising a feed of 76cm x 38cm (30” x 15”). Since then, the business’ operations have continued to expand and the equipment has been upgraded to meet changing needs.
“When we were starting out we grew slowly and never had any big equipment, but every time we did have to buy something new, it was always the next size up,” Lewis said. “Over a period of a few decades, we’ve got to where we are now.”
For the past 23 years, Lewis Quarry has operated its own site in the Clarence Valley, in the Northern Rivers region of New South Wales. It is a hard sandstone quarry, which has to be drilled and blasted, with a footprint of about 15ha to 17ha. Under the current development application, its output per annum is capped at 246,000 tonnes.
“[In 2017], with the equipment we have at the moment, we crushed our quota in six months,” Lewis said.
The quarry services the local community and provides material for everything from riverbank protection rock to roadbases.
In recent years, construction materials demand has increased with the advent of the Pacific Highway project and, as a result, Lewis Quarry has had to upgrade its equipment once again. It formed a relationship with Lincom
The Warrior’s feed log regulates the material flow; once the material exceeds a certain weight, it slows down or stops.
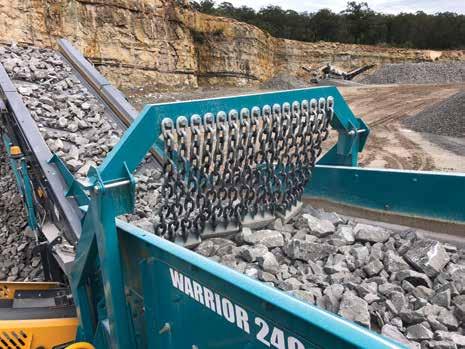
Equipment “quite a few years back” and has owned and operated various stackers and crushers previously.
“Then they came up with the Powerscreen Warrior 2400, which was exactly what we needed,” Lewis said. The Warrior 2400 has played a major role in enhancing the efficiency of the site’s operations.
TRIPLE-SHAFT TECHNOLOGY The Warrior 2400 has been specially designed for large-scale operators in the quarrying and mining sectors, and is capable of handling larger feed sizes and throughputs.
It features a heavy-duty incline screen with a high amplitude triple-shaft drive mechanism, lending it to screening, scalping, two- or three-way splitting and stockpiling materials. “The Warrior 2400 is different to everything else on the market,” said David McDermott, the area sales manager for Lincom on the east coast of Australia.
“It’s the only scalper with triple-shaft
technology, which means we can make it more aggressive. You can also adjust it to fit any application.”
It’s a sentiment shared by Lewis. “There’s no comparison with other equipment. When we had two screens in the system we had to be very careful because we could overload them and we’d have to spend an hour trying to dig them out. But the Warrior won’t really let you do that,” he said.
“Basically, the feed log regulates the flow and once the material gets above a certain weight, it just slows down or stops. In screening that’s crucial. Because it’s such a big screen, I’d hate to have to dig it out. The mere fact that the system can actually control the feed is invaluable.”
RESPONSIVE SERVICE One of the other major selling points for Lewis Quarry was Lincom’s after-market service.
Because of their existing relationship, Lewis knew what to expect, and he hasn’t been let down. “You never have to worry about whether there’ll be back-up if something goes wrong.”
Lincom’s service is personalised, which makes it more responsive to calls for help, according to Lewis. He compares it with previous experiences he’s had with large multinational companies: they were less engaged with his business’ needs and, as a result, it was difficult to get quick resolution when something went wrong.
“If you’re in trouble, Lincom get you out of trouble,” Lewis said. “The back-up is brilliant – we can’t complain at all.
“And they [Lincom] keep a hell of a lot of parts, whereas some other manufacturers want to charge you freight from overseas.” The Warrior’s capacity has improved productivity, which has led to more efficient crushing capabilities and, ultimately, reduced Lewis Quarry’s costs.
“In the past, we needed two scalpers to keep up with the jaw. Now we have the Warrior, we can manage to do with one screen what used to take two screens to handle. So it’s an efficiency thing with regards to both fuel and wear and tear,” Lewis said.
Lincom worked closely with Lewis Quarry to understand its specific requirements and provide the best solutions.
“Lewis Quarry needed big tonnage for the Pacific Highway project and the Warrior is the biggest scalper on the market,” McDermott said. “It is 6m x 1.8m on both decks, top and bottom.”
Lewis Quarry’s mobile plant and equipment has been processing up to 7000 tonnes of aggregate daily.

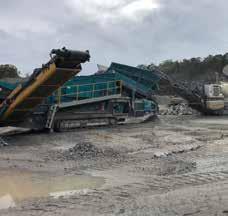
According to Brian Lewis, the Warrior 2400 (left) has helped enhance the efficiency of the site’s operations.
SPECIFICATIONS – WARRIOR 2400
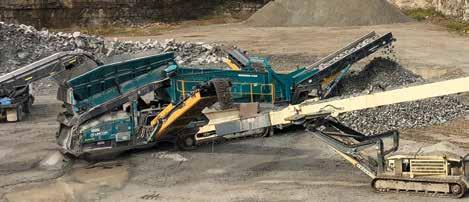
TOTAL WEIGHT Transport Length Width Height Working Length Width Height Screen unit
Length Output Max feed size Hopper size Power unit Plant colour THREE-WAY SPLIT TWO-WAY SPLIT 45 tonnes* 43 tonnes* 17.3m 17.2m 3.0m 3.0m 3.6m 3.6m 18.5m 18.3m 15.3m 9.6m 5.2m 4.9m
6.1m x 1.93m 6.1m x 1.93m
800 tph 800 tph 750mm 750mm
10m 3
10m 3
Diesel/hydraulic Diesel/hydraulic
RAL 5021 RAL 5021
* Weight will vary depending on machine specification.
Running the bigger equipment has also allowed Lewis Quarry to reduce its number of on-site operators.
“We only have four full-time employees in the quarry and we often utilise our fourth employee on truck driving or some other job,” said Lewis.
As of mid-2018, Lewis Quarry was processing about 7000 tonnes of material per day. Once the Pacific Highway is finished in another two years, “then we’ll revert back to a quiet life,” Lewis said.
“And the Warrior will be able to cope with anything that comes along.”
As for the Lewis family, the plan is to continue quarrying for many years. Brian’s sons already work in the business and, with the quarry still on its original cut, he predicts there’s a lot of life left in the site. •