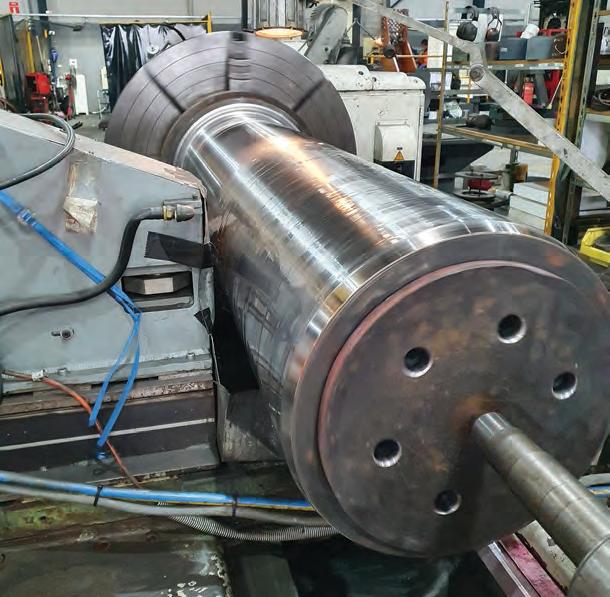
16 minute read
MINING SERVICES
SHINING OUT CHROME FROM MINING
LASERBOND’S E-CLAD SOLUTION SERVES AS A CAPABLE REPLACEMENT TO HARD CHROME PLATING THROUGH ITS ENVIRONMENTAL SUPERIORITY AND LONGER LIFESPAN.
Hard Chrome plating has long been the standard for protecting hydraulic cylinders against wear and corrosion attack in heavy industries such as mining.
Chrome plated hydraulic cylinder rods are used widely at mine sites, including on excavators, drills and haul trucks. Chrome is generally applied using highly toxic and energy intensive processes to provide a thin plating (0.025 millimetres to 0.25 millimetres) to protect components such as hydraulic rods from sliding wear.
For economic reasons, due to a very slow build-up of the plating, often only very thin layers are applied, which only provide minimum wear protection and which are prone to damage upon impact.
In addition, the inherent microcracks in chrome plating mean that such thin layers do not provide long lasting corrosion protection.
However, with miners being forced to abide to more stringent environmental, social and governance (ESG) demands, the days of chrome plating may soon be over.
Surface engineering company LaserBond recognises this and has developed E-Clad, an environmentally friendly and robust alternative to chrome plating.
E-Clad protects people and workplaces from the carcinogenic properties of hexavalent chromium (chrome), while reducing their carbon footprint with lower energy consumption in the process and extended wear life through higher abrasion, impact and corrosion resistance, meaning fewer changeouts.
LaserBond sales manager Mike Walker says E-Clad metallurgically bonds with the metal underneath to create a strong and more resistant product.
“We wanted E-Clad to replicate the functionality of chrome platings in an environmentally friendly way,” Walker tells Australian Mining.
“The E-Clad process creates a metallurgical bond by melting the chrome replacement layer into the parent material so that they are essentially one, whereas chrome just sits on the surface.”
According to Walker, regulations are being introduced across the globe to phase out chrome due to its environmental and workplace safety issues, with Australia likely to follow this trend.
This will push the mining industry to seek alternative products such as E-Clad. However, there is a strong incentive to switch to LaserBond’s solution sooner rather than later.
“If you have a cylinder and it is sliding in and out of a piston, and a rock falls and puts a crack into it, it will cut the seal in the hydraulic cylinder and oil will leak out,” Walker explains.
“The superior bonding between E-Clad and the actual component can prevent this from happening.”
Hard chrome plating has thickness limitations. The wear life of chrome plated components is determined by a reduction in the dimensions of the metal underneath the plating.
This can only be replaced two to three times before the chrome plated component needs to be thrown away, but E-Clad’s metallurgical bond ensures it can be taken off and cladded as many times as required.
E-Clad has a wear rate that is between three to 10 times lower than commercial chrome.
“It had to withstand impact thrown at it, it had to stay on even during vibration and be corrosion resistant,” LaserBond national production manager Steve Halloran tells Australian Mining.
“For example, if you had acidic conditions from minerals underground that contaminate steels it had to be resistant to that.
“We don’t have a thickness restriction so nothing is thrown out, there are massive savings on carbon emissions and we can keep that item in service a lot longer.”
LaserBond has developed E-Clad to use 25 per cent less energy than hard chroming, which also enhances its environmental benefits.
The science behind E-Clad has ensured it is stronger than chrome plating, which in turn prevents accidents from occurring on a mine site that lead to unplanned downtime and in a worst-case scenario, serious injury.
“We use E-Clad for suspension rods and trucks with great success,” Walker says. “If you’ve got a truck going down a haul road in a mine site and loses hydraulic pressure because chrome has bubbled up and cut seals it can lurch down and cause an accident.
“This is an unplanned and uncontrolled movement, but the chrome bubbling wouldn’t happen with E-Clad.”
The solution can also be applied in thin applications faster than hard chroming to reduce turnaround times for mining companies.
With E-Clad’s cutting-edge qualities for miners, LaserBond’s research and development team is already looking for ways to enhance its performance even further.
“We have two different grades of E-Clad at the moment so we will continue to expand that product range and continue to research the attributes that our customers are looking for, such as hardness, wear resistance, corrosion resistance and lowering porosity,” Walker says.
“The products that we develop are great products and opening up a huge potential for development in this space – there’s a lot more we can do as we further evolve E-Clad.”
The E-Clad solution is now available for application on wearing components for mine sites across Australia through LaserBond. AM
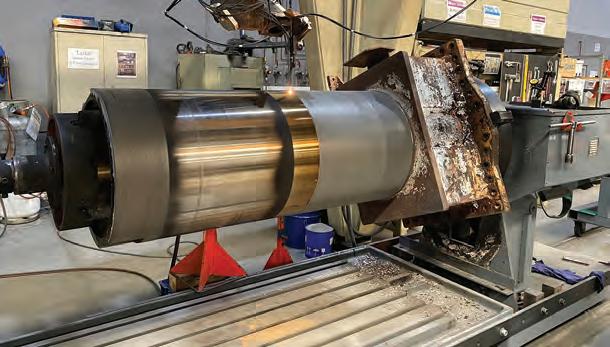
E-CLAD METALLURGICALLY BONDS WITH THE METAL UNDERNEATH HYDRAULIC CYLINDERS.
SANDY RIDGE IS 240 KILOMETRES NORTH-WEST OF KALGOORLIE BY ROAD.
TELLUS CONQUERS HAZARDOUS WASTE ONCE AND FOR ALL
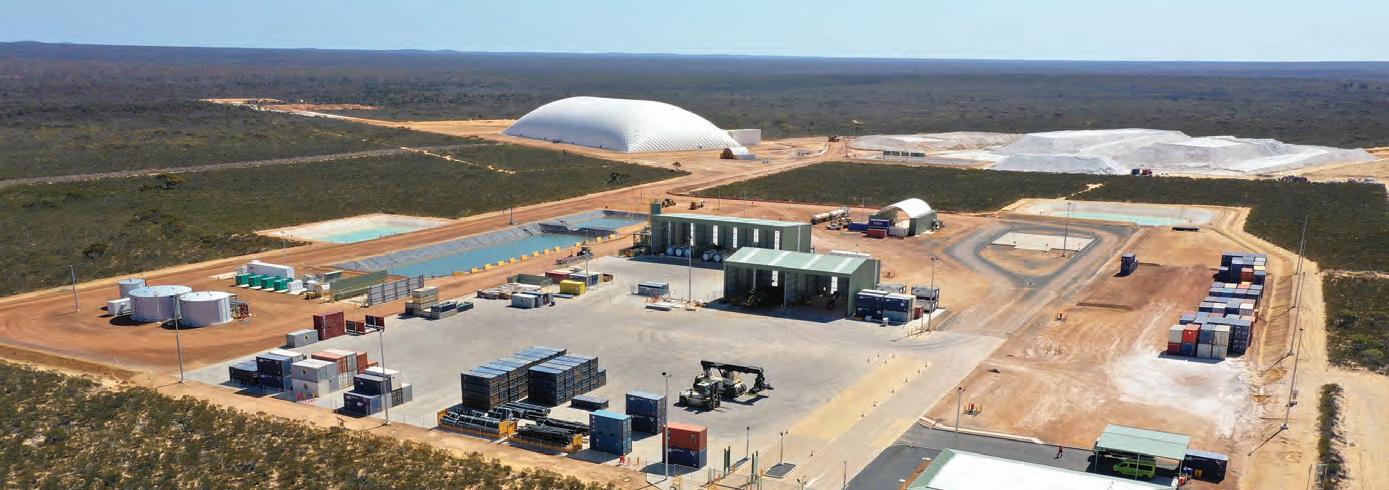
TELLUS’ AUSTRALIAN-FIRST COMMERCIAL HAZARDOUS WASTE GEOLOGICAL REPOSITORY IN WESTERN AUSTRALIA OFFERS MINING COMPANIES A SAFE, PERMANENT AND PROVEN OUTLET FOR THEIR HAZARDOUS WASTE DISPOSAL.
There’s more to the concept of waste disposal than the safe storage of by-products or surplus goods.
Waste management, and in particular hazardous waste management, is an art in itself and stands alone as an economic generator as much as it is an environmental preserver.
Hazardous waste innovator Tellus is relatively new on the waste management scene in Australia and understands the opportunities the Australian mining industry is embracing in recognising the importance of safe hazardous waste disposal. In fact, the company has built a proven business model on it.
When Tellus’ Australian-first Sandy Ridge hazardous waste geological repository was opened in March 2021, the company understood the momentousness of its venture.
Located 240 kilometres north-west of Kalgoorlie by road, among some of the world’s best geology for this purpose, Sandy Ridge doesn’t just permanently and sustainably dispose of nearly all types of hazardous waste, it enables industries such as mining to do away with the liabilities associated with their legacy hazardous waste disposal obligations.
For Tellus chief executive officer Nate Smith, one of the biggest strengths of Sandy Ridge is the costeffectiveness of the solution.
“We’re a new hazardous waste solution for the Australian mining industry to ensure they don’t have to compromise between mining development and environmental safety,” Smith says.
“The hard truth is that the issue of hazardous waste is not going away for the mining industry or Australia generally and that’s even with a renewed focus on renewables.
“With Sandy Ridge, Australia now has a world-class solution to ensure that hazardous waste of all types can be permanently dealt with and safely handled.”
It’s important to emphasise the perpetuity of Sandy Ridge – the harmful impacts of incoming hazardous waste are eliminated, not just from the environment but from the client’s balance sheet.
“Sandy Ridge coming online enables a seismic shift in how Australia deals with its hazardous waste, bringing a solution to this country that has been used for decades with success in North America and Europe,” Smith says.
“In the past, the lack of an economically viable and environmentally sustainable solution has led to utilising temporary storage systems in Australia, like landfill or in-situ storage, until a better solution comes along.
“Unlike such alternatives, the great part about us is that we can eliminate the dangerous impacts of hazardous waste and give positive assurance that disposal liability can be erased from a mining’s company’s balance sheet through the issuance of a Tellus Permanent Isolation Certificate.”
Sandy Ridge can expedite a mining company’s remediation process because it has pre-funded all its post-closure liabilities, while also having $100 million in pollution liability insurance.
There is next to no risk of liability coming back to haunt the waste owner once waste arrives on site.
The processes that underpin Sandy Ridge are intrinsically sustainable with its waste management techniques limiting its own burden on the environment.
“Alternatives for hazardous waste removal prior to Sandy Ridge opening could have been incineration, treatment or export of the most hazardous materials,” Smith says.
“However, those options have material downsides. They’re downsides because they’re volume-constrained, whereas we can initially accept up to 100,000 tonnes per annum, although our site could handle much larger volumes.
“They’re also energy-intensive, they create carbon dioxide and dioxin emissions, and a lot of the time they actually produce a more concentrated hazardous waste at the end.”
This is where Sandy Ridge comes to the fore. Smith says the operation is unique because of its world-class safety case, as well as the fact its backstopped by the Western Australia Government.
“The combination of our safety case and having the WA Government agree to monitor our site once it closes or if Tellus ever ceases to exist, actually allows us to give a positive assurance by issuing a Tellus Permanent Isolation Certificate, or Tellus PIC,” Smith says.
“The Tellus PIC is backed by ‘Big 4’ accounting advice that once we take risk and ownership of the waste, the former waste owner can totally wipe that liability off its balance sheet. That is meaningful and tangible value.”
Sandy Ridge can also accept nearly any type of waste in nearly any form. This includes everything from problematic mineral tailings to multi-contaminated soils, mercury, treated timbers, naturally occurring radioactive material (NORMs), surface contaminated equipment, lead and outof-date or unwanted reagents.
Even more, most incoming waste types typically don’t require treatment. Tellus can manage the entire hazardous waste management process end-toend. This means that once a mining company engages Tellus, it can focus solely on its core business, relieving it of any further responsibility for its hazardous waste.
Through Sandy Ridge, Tellus delivers the environmental, social and governance (ESG) outcomes to excite any miner eager to prove it is taking permanent steps to clean up Australia. AM
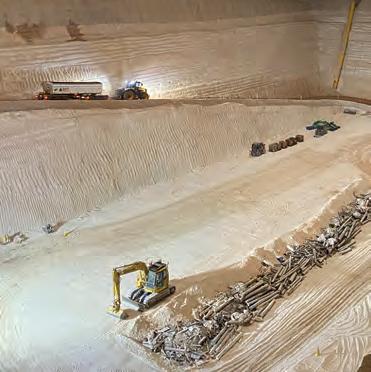
THERE’S NEXT TO NO RISK OF LIABILITY FOR THE WASTE OWNER.
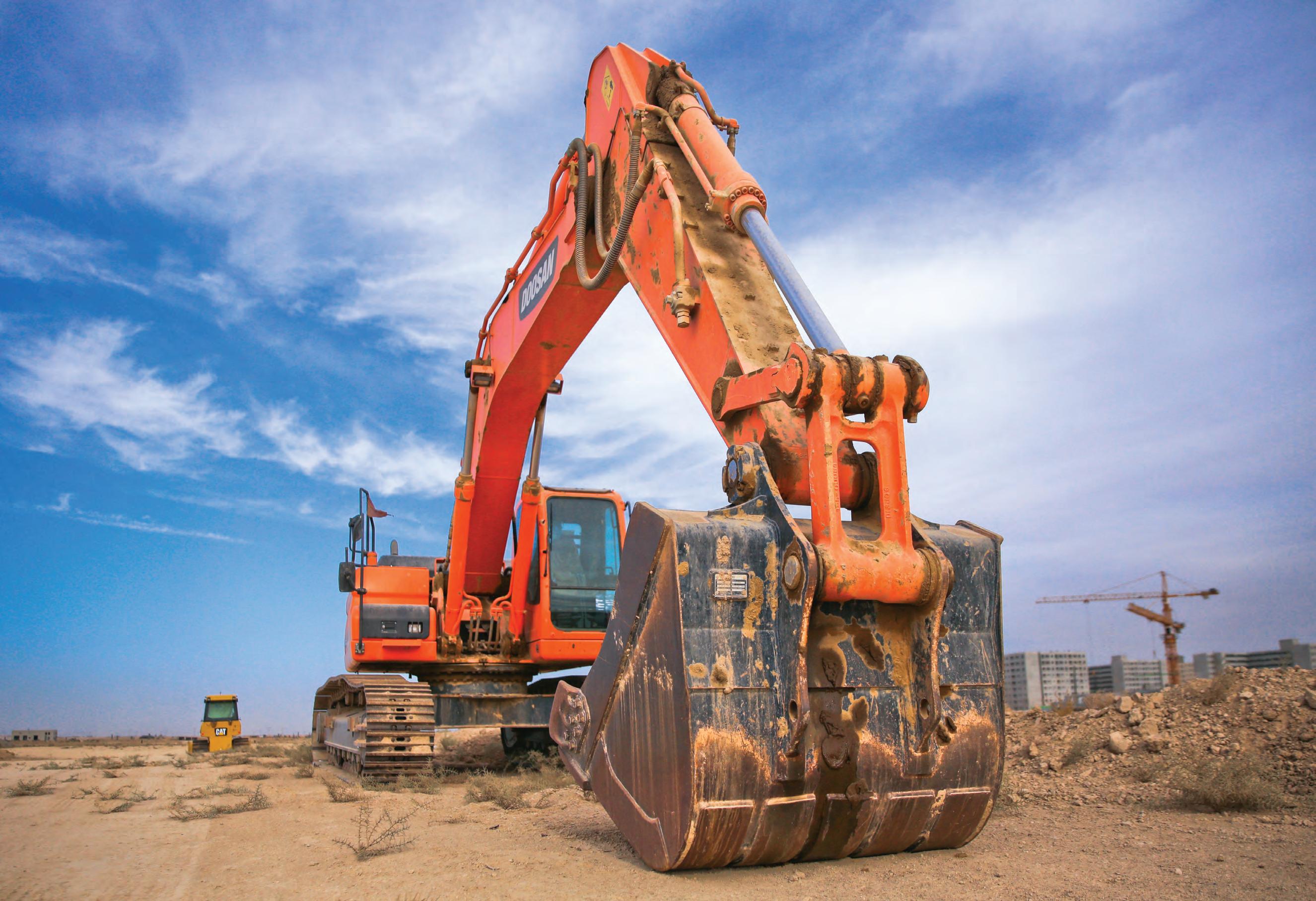
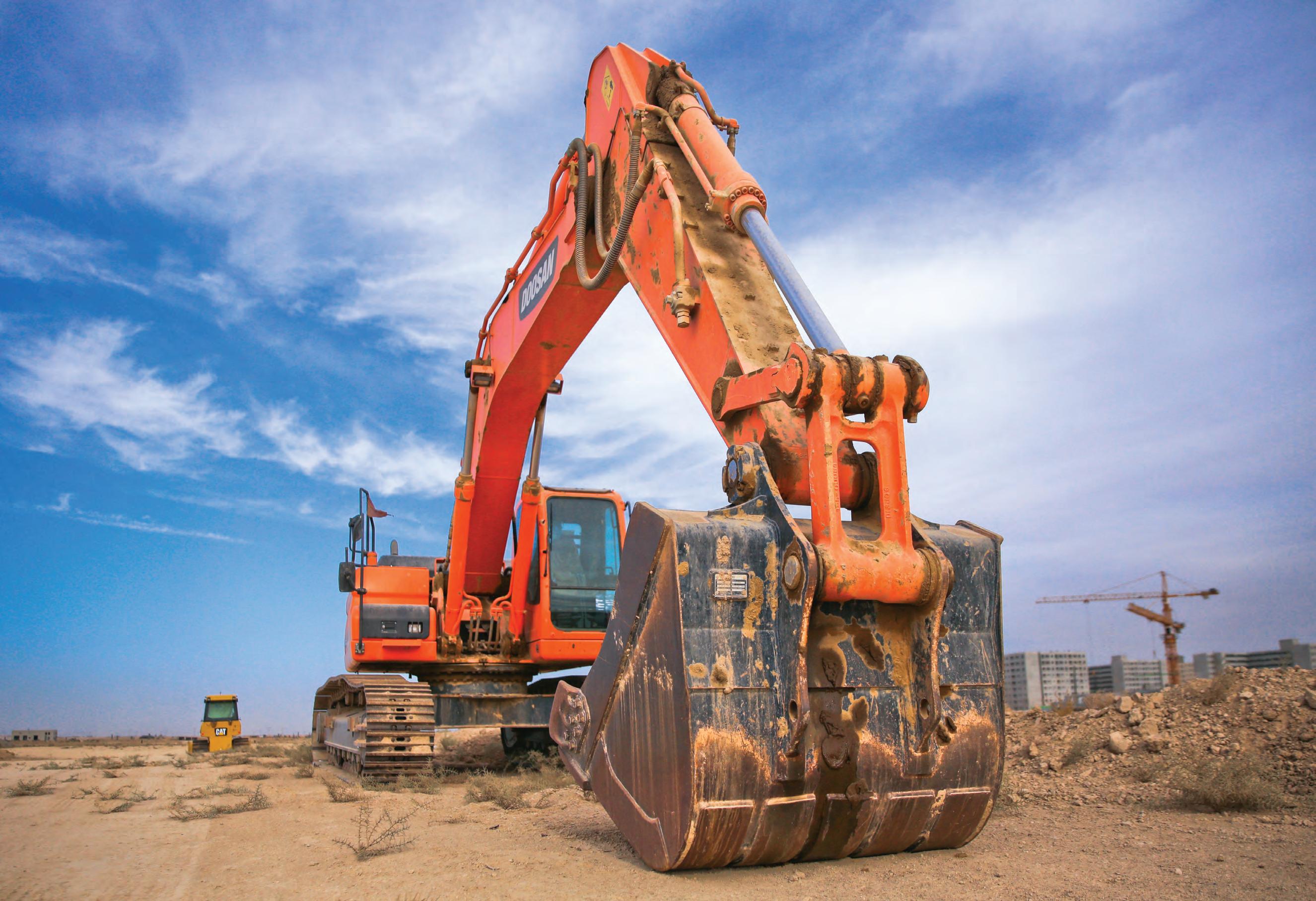
AIRING OUT THE MINE SITE
ATLAS COPCO COMPRESSORS IS PROVIDING SOLUTIONS FOR THE MINING INDUSTRY ACROSS THE GLOBE.
The high performance and efficiency of modern mining plant and equipment is something the industry places significant value on.
Yet the attention rarely focusses on the innovations behind powering many of the machines that make up the mining process.
Operations require heavy duty industrial air compressors and blowers for their plethora of applications.
Energy efficient solutions An effective air compressor must combine high performance and reliability with energy efficiency.
Atlas Copco will be one company to watch as the mining industry strives for a more sustainable future through more energy efficient solutions.
“Our compressors are known for their longevity and reliability, and we have machines that are still running after 20 years of operating in harsh mining environments,” Atlas Copco business development manager for the mining sector Tony Dias says.
Variable Speed Drive Compressors Atlas Copco’s variable speed drive (VSD) compressor range is designed specifically for challenging conditions such as those in Australia’s surface and underground mining operations.
The company was a pioneer of VSD technology in the early 1990s, which matches air production to demand, leading to substantial energy savings of up to 50 per cent and reduced carbon emissions.
“Approximately 10 per cent of the world’s energy today goes towards compressing air and if we can save one per cent of that by providing more efficient compressors, that could be a huge saving globally and will have a massive impact on global carbon emissions,” Dias says.
“Mining companies are driving demand for a more sustainable future through energy efficient solutions.
“It’s a major driver for all companies, not just mining as shareholders are demanding that companies reduce their carbon footprint.”

Fast and capable service By positioning itself on the doorstep of major mining regions in Australia, Atlas Copco offers fast and capable services to remote mining areas.
Dias says the company has begun offering compressed air as a utility as some customers do not want to invest in a fixed asset.
“It is a new solution for the industry and something we are now doing, albeit in a limited way. We are selling air by the cubic metre,” Dias says.
Customisation for mine sites Atlas Copco understands that no two mine sites are the same, which is why its local and international resources include dedicated engineering teams that help to formulate customised air compressor solutions. There is an increased demand for customisation of the company’s equipment.
Mining companies benefit from this service as it supports the diverse range of environments that their operations are located in.
“There is fairly high demand for customisation of our compressors, so they are suitable for harsh environments,” Dias says.
“Customers want to customise and almost cherry pick different elements of the compressor – they demand that we upgrade our standard compressors to suit custom requirements.”
The perfect plug-and-play solution The AIRCUBE allows companies that don’t have the time or space to add an indoor compressor room to quickly add compressed air capacity. It also solves a challenge many resource sector operations face: how do you get a dependable, high-quality air supply to some of the most remote places on this planet? Welcome to AIRCUBE.
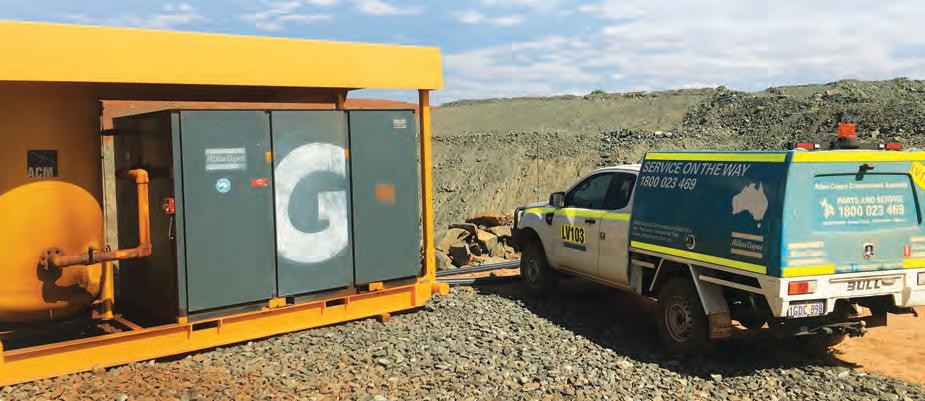
ATLAS COPCO CAN CUSTOMISE COMPRESSORS FOR EACH INDIVIDUAL MINE SITE.
Hydrogen to fuel the future for greener power With mining companies facing stringent environmental, social and governance (ESG) requirements, Atlas Copco is developing a 1000-bar compressor for hydrogen.
“Hydrogen is obviously touted as a clean fuel of the future and being able to utilise it as a fuel source is all about reducing the carbon footprint,” Dias says.
While development is in its early stages, hydrogen fuel is another step in the industry’s shift to greener power to cut carbon emissions.
Low pressure blowers Atlas Copco’s low-pressure blowers and compressors deliver a steady supply of high-quality, oil-free air with industry leading energy efficiency and reliability.
Its multi-stage centrifugal blowers guarantee a continuous supply of 100 per cent oil-free air and come in a flow range of zero to 68,000 cubic metres per hour, with pressures from 48 to 160 kilopascal gauge. Mining applications include leaching and flotation.
Nitrogen and oxygen generators A full range of on-site nitrogen and oxygen generators are part of Atlas Copco equipment offerings.
With a 150-year history, Atlas Copco has grown to become a globally renowned brand with technical and engineering teams based across Australia.
Atlas Copco’s service to the mining industry shows that it is capable of powering vital mining equipment through its wide range of air compressor technologies. AM
FANNING OUT THE BEST SOLUTIONS
WITH THE GOAL TO HAVE SOLUTIONS THAT HELP THE CUSTOMER EXTEND THE SERVICE LIFE, IMPROVE PERFORMANCE AND REDUCE THE TOTAL COST OF OWNERSHIP OF MACHINERY, SKF KNOWS TOO WELL THE HARSH ENVIRONMENTS MINING OPERATIONS FACE.
SKF rotating equipment performance specialist – Australia, Vishesh Arora, says fans are crucial components in many industrial applications and often the workhorses in production plants.
“If you look at a ventilation fan, which is commonly used in mine sites, imagine the whole mine being shut down because one fan stopped,” Arora says.
“A fan can be a simple application, but depending on where it is used, the impact to the business and people can be very significant.
“Just like a doctor would need blood test results for diagnosing, you first need to get reliability under control; minimising human interaction and most importantly, improving worker safety.”
This is where SKF’s smart fan program comes into play. The smart fan program is broken into three main steps – the positioning of the fan in terms of technicality; the current behaviours of monitoring fans; and finally, helping customers identify faults and reduce downtime.
SKF business development manager Asia, Senthil Vel, says the first step is to install pre-configured wireless sensors to connect to the fan.
The company can then detect any issues by interpreting the data using an automated machine monitoring system powered by cloud-based Internet of Things (IoT) solutions and AI driven analytics.
“Insights from the data are presented to clients in easy-to- understand dashboards, informing and advising when a problem arises – what it is, what the underlying cause might be and how to resolve it,” Vel says.
Through the application of sensors, technology and knowledge to identify what is happening with the fans, Vel says operators can see the data at every hour or even minute of the day, allowing them to proactively plan for changeouts and maintenance.
“We bring in the technology, expertise and software to simplify the process for the customer so they can take action immediately,” he says.
Boasting several advantages, Vel highlights two key benefits of the smart fan program. The first benefit of the program is the output.
“If a mine is producing coal then that doesn’t stop, allowing the client to get its product out to their customers on time,” Vel says.
The second benefit is the cost of maintenance. Vel says if a fan fails clients must replace the fan, fix it and bring in contractors, resulting in

SKF’S PROGRAM IS BROKEN INTO THREE STEPS WHICH HELP IDENTIFY FAULTS AND REDUCE DOWNTIME. SKF HAS OPTIMISED FAN PERFORMANCE FOR THE PAST 25 TO 30 YEARS.
significant maintenance costs.
“We feel by having the technology to understand what is going on, it will tell us what has to be done in terms of the diagnosis; how to avoid those failures and reduce the costs that would come along with that,” Vel says.
SKF has optimised fan performance for the past 25 to 30 years, designing and updating its solutions for mining companies around the world.
Traditionally, fans are inspected every three to six months. However, the company has identified over this period that during these intervals there is a chance that failure could occur with a large cost associated.
SKF application engineer Uwe Guist helped deploy a solution for a hot gas fan at a smelter facility in Western Australia, which increased the mean time between failures (MTBF) from less than 12 months to four years.
Guist says industrial process and hot gas fans operate with extremely high internal gas temperature (>300C). However, he says internal temperature is just the beginning of heatrelated problems.
Following a detailed assessment at the WA facility, Guist concluded that SKF technology needed to be deployed.
“From the condition data, we found clear evidence that the real roadblock was due to extreme heat, which was causing thermal expansion of the shaft,” he says.
“It’s virtually impossible to eliminate internal heat generated by the process.”
The company upgraded the appropriate bearing arrangements to accommodate the operating conditions; along with a review and change in the lubrication system.
The SKF service team in collaboration with its distribution partner, Applied Industrial Technologies, supervised the project, including the mounting of replacement bearings and associated components.
“The client was pleased that as a one-stop shop we were able to diagnose the problem and improve their performance with SKF engineering and application knowledge,” Guist says.
SKF mining segment manager Rod Allen says the company offers a unique combination of product supply and services with its rotating equipment performance solutions.
The company is not just a manufacturer of bearings, but also seals, lubrication systems, housings, power transmission products and condition monitoring equipment.
By leveraging its product and engineering expertise with deep understanding around rotating equipment, Allen believes SKF can provide a unique solution to its customer to maximise machine availability and increase reliability.
“With this solution, the customer needs to pay a monthly fee rather than the cost of the product and we get paid based on the performance we deliver. Essentially, we are moving from selling products to selling performance and uptime. We win when the customer wins,” Allen concludes. AM
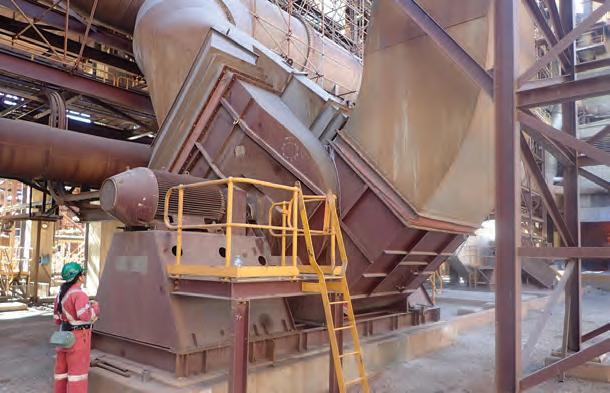