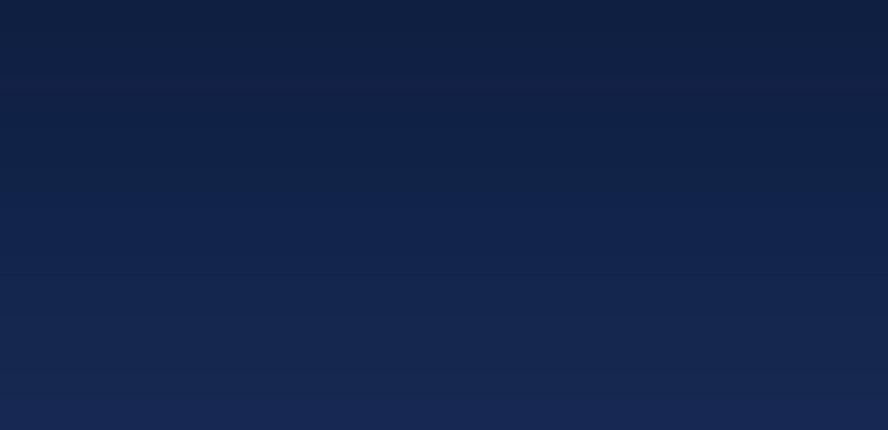
2 minute read
Tankers go hydraulic
WITH a drought on the horizon, based on El Nino conditions, we look like we are in for a dry and dusty summer, especially for the eastern states.
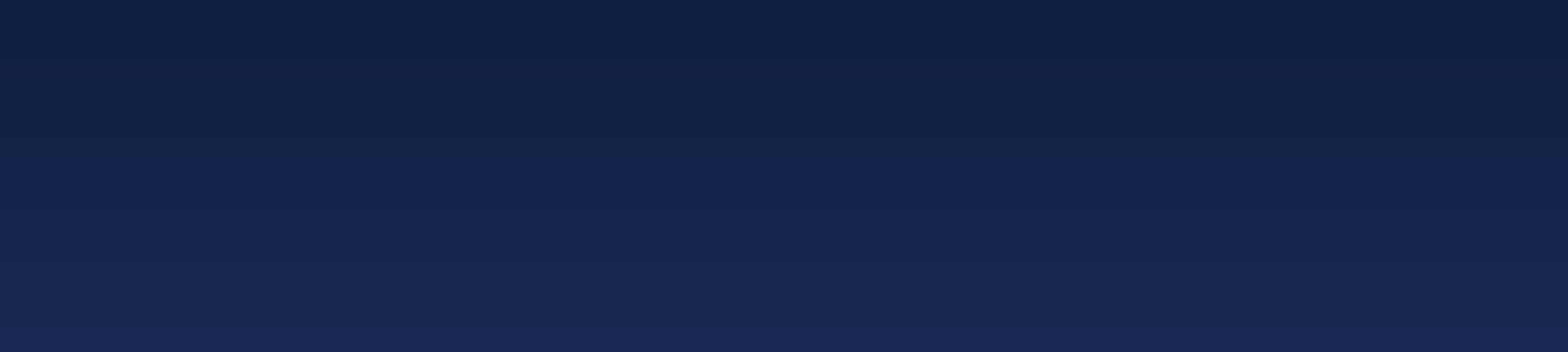
Tanker bulk liquid transport operators, whether handling water, molasses, or even liquid fertiliser, face a real challenge.
In drought water carts, anything from 5000 litres to 50,000 litres become premium property. During the last sixyear drought, water carts kept country towns running by trucking in huge loads daily. It seems governments are not responding to the need for increased water storage.
So those water carts that have been doing very little work over the last three summers are going to be very busy!
Aussie tanker pumps
When Aussie Pumps got started 30 years ago their super reliable and highly efficient engine drive self-priming pumps were a big hit. The range went from 2” all the way through to 6” pumps and delivered flows of up to 2900 litres per minute. Those pumps were powered by Honda engines, Yanmar or Kubota diesels.

Most were perched on the back-end of water carts and were used for dust suppression on construction and roadwork sites and for hauling water in those tough drought conditions. The weakness in the whole system wasn’t the pump but rather the engine that drove it. Aussie Pumps repeatedly got complaints from customers with engine failures, due to ‘dusting’ or sometimes simply poor engine maintenance.
“We found that the tanker operator always checks the truck engine to make sure the oil levels are right, and maintenance is okay. They often forgot about the engine at the back-end that runs the pump,” said Aussie Pumps chief engineer John Hales.
“Truckies wanted a more reliable drive system and more versatile pump performance.”
Aussie’s hydraulic drive solution
Australian Pump introduced the GMP pump to replace traditional lightweight aluminium Honda drive units with bigger 3” cast iron pumps that were designed around ‘semi trash’ configuration. That includes a big open impeller, a stainless steel wear plate mounted inside the body and silicon carbide mechanical seals (for long life and abrasion resistance). Most importantly, a front clean-out port that enables the pump to be cleared of blockages in the impeller chamber, without dismantling pipe work, is now a standard feature.
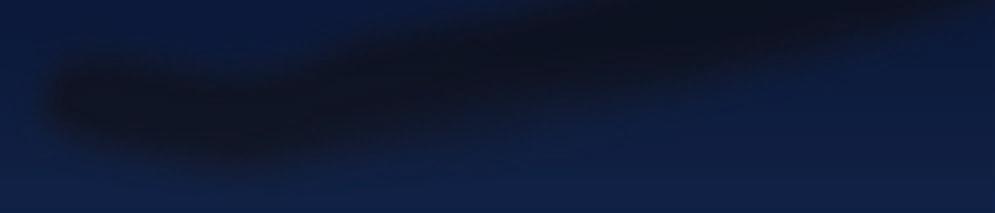
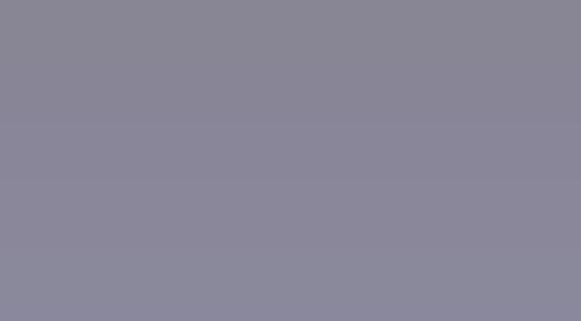
Going hydraulic
Aussie pioneered the use of hydraulic drive systems in engine drives. The hydraulic circuit is completely sealed from dust. Lubrication is another massive advantage. The hydraulic motor is lubricated by the closed circuit system. There are no daily engine oil checks, it’s all just driven off the prime mover’s PTO hydraulic pump.
So hydraulic drives are taking over. Local government bodies, probably Australia’s biggest fleet owners of water carts, have already discovered that hydraulic drive is the way to go.
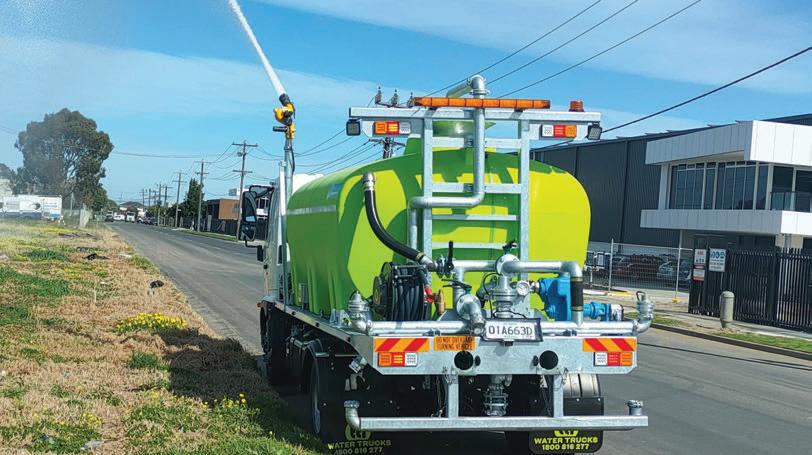
Imagine having no issues with available power because the hydraulic drive has the prime mover engine to draw off.
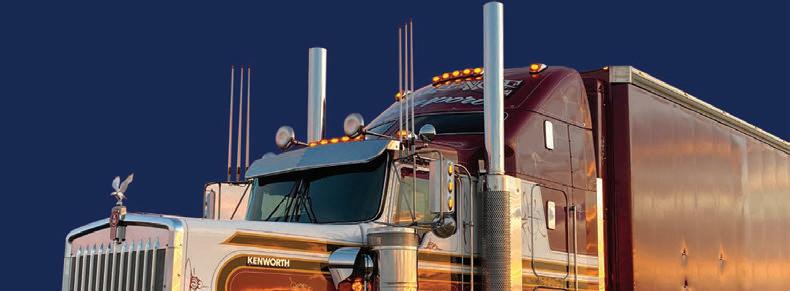
“We are seeing more and more tanker manufacturers swapping over to our hydraulic drives. We also are noting many conversions of earthmoving contractors and even farmers swapping over to hydraulic where the truck transmission is suitable.
Replacement program
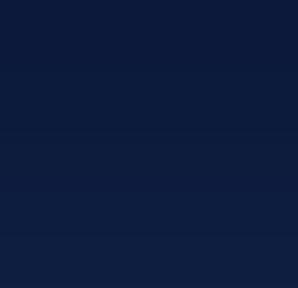
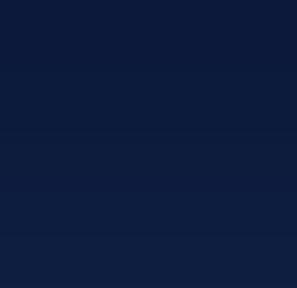
“The company is also seeing some level of disenchantment with third world hydraulic drive pumps. Parts support seems to be non-existent, and customers tell us that they constantly face problems with premature seal failures. We don’t have any of those problems,” said Hales.

Further information on the complete range of hydraulic and engine drive pumps is readily available from Australian Pumps. “Truckies get the best deals,” said Hales.