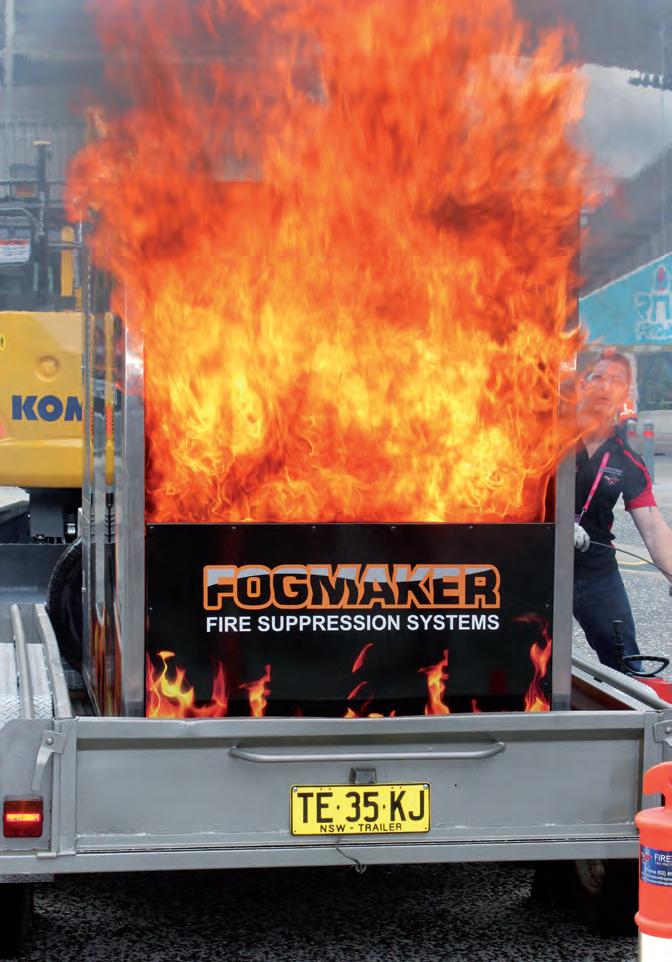
5 minute read
How effective are your fire suppressant systems? There is a perception that once a crane fire get started nothing can be done to stop them. Firestorm’s Kieran McHatton explains this isn’t the case
HOW EFFECTIVE ARE YOUR FIRE SUPPRESSANT SYSTEMS?
Crane accidents, especially crane fires can be making news headlines almost immediately in today’s digital age. There is a perception that once these fires get started nothing can be done to stop them. Firestorm’s Kieran McHatton explains this isn’t the case.
IN MANY CASES, the risks and related control measures around crane operations are well known, but in terms of risk assessment, a crane fire isn’t necessarily front of mind.
The ‘worst case scenario’ happened in Sydney six years ago, when a fire started on the machine deck of a diesel/ hydraulic luffing crane which caused the luff rope to fail allowing the jib to collapse onto the worksite below. Fortunately, there were no injuries as the worksite had been evacuated and the jib fell into the evacuated worksite rather than a populated area. Safety reports at the time confirmed that the same fire potential for fire applied to electric tower cranes.
Providing protection against fire on mobile and transportable equipment is governed by Australian Standard (AS) 5062 -2016 and the objective of the standard is to formalise current good practice in reducing the incidence and severity of fires and to provide a consistent approach to fire risk reduction in order to safeguard life, property and the environment against fire associated with mobile and transportable equipment.
Firestorm Fire Protection designs, installs and services fire suppression systems throughout Australia.
The Firestorm Fire Protection Group comprises an integrated network of fire suppression solutions for a wide range of applications including cranes, mining and heavy industry, bus, construction, recycling, trucks, tunnelling and forestry sectors.
Firestorm has been distributing the Swedish manufactured Fogmaker Water Mist Fire Protection System since 2010.
According to Kieran McHatton, General Manager of Fogmaker Australia, the system is AS 5062-2016 approved and industry response to the system was quick and positive. “In the first 12 months of taking on the product we installed 600 systems,” he said. “We started in mining, and then moved to the public transport sector. Today, we have installed 9000 systems across Australia and NZ and 180,000 systems internationally.”
McHatton comments that AS 5062- 2016 is a risk based methodology and has certain fire testing component criteria. Not all systems comply to the standard.
“There are two ways to look at the standard. Firstly, suppressant manufacturers have to put their systems through AS5062 to get approval and compliance. Secondly, the end user needs to follow the AS5062 risk based methodology to be part of that approval process,” he said. “So, the user owns the risk assessment and determines whether a fire system goes on the machines or not. There is a chain of responsibility on the machine owner, and they should be ensuring that a fire suppressant system is fit for purpose prior to purchase.”
The Fogmaker system is a piston accumulator system using high-pressure water mist.
“Compared to conventional foam systems we are a more compact unit and use 1/10th of the agent to provide the same or better outcomes. Essentially, we fill the engine compartment with water mist and one litre of water creates 1,700 litres of steam,” he said. “Steam is an inert gas, and that extinguishes the fire and the evaporation process turns the water mist into steam and that’s the cooling effect. If there’s a fire in the engine compartment we cool it from 850C down to 75C within 15 seconds. That’s a drop in temperature of over 700C within 15 seconds – nothing cools like water mist.
The system automatically detects a fire, so if the temperature in the engine compartment reaches 180C the system the system will automatically function. There’s no need for electrical power as the system functions without it. The Fogmaker system also provides pressure switches on the cylinders so we can advise the operator on a fault or an alarm condition.
It can also provide ancillary controls which include shutting the engine down and providing voice announcements to instruct the operator in case of an evacuation.
The Fogmaker system has been fitted to see a number of frannas and large harbour cranes. All the new Liebherr harbour cranes for Qube Ports in
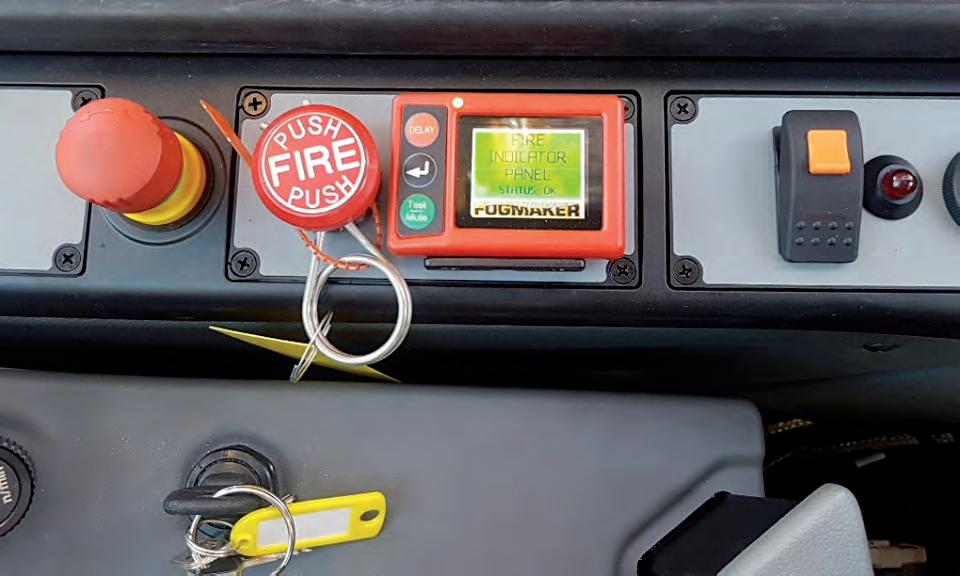
The system has an easy-to-use panel. Kieran McHatton from Firestorm.
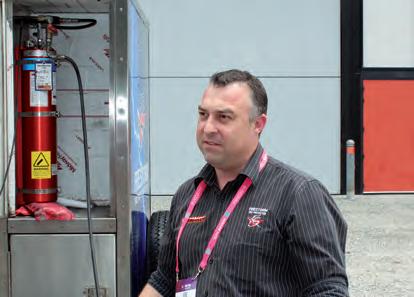
Australia come with the Fogmaker system fitted as standard. Liebherr run all the cabling and Fogmaker manage the final fit at the assembly stage.
“Firstly, we fill our detection tube with a liquid so we don’t get any leaks, this has been proven in the bus industry where we’ve installed more than 8000 systems. There’s no doubt that the system is robust and we don’t get faults, if it is activated, it’s because there’s been a thermal incident.
“Secondly, our system is compact and because it’s a piston accumulator it can be installed at any angle. Thirdly, because there are so many different cylinder sizes in the range, we can fit our system to the smallest and largest crane. Construction equipment is getting more compact and the larger conventional systems no longer fit on these machines, that’s why there’s such a big move to Fogmaker,” he said.
McHatton makes an interesting observation about environmental legislation and engine emissions.
“Tier 4 engines now feature higher pressures and are running hotter to reduce emissions. They also feature diesel particulate filters, which add more heat to the engine compartment. More heat equals more pressure, equals more fire risk,” he said.
“Previously, engines featured low pressure diesel and it’s hard to light a pool of diesel, but today’s engines atomise diesel so finely, we can ignite diesel at less than 100C. So there’s a lot more chance of fires starting and I don’t think anyone can really say ‘my machine doesn’t need a fire suppression system’.”