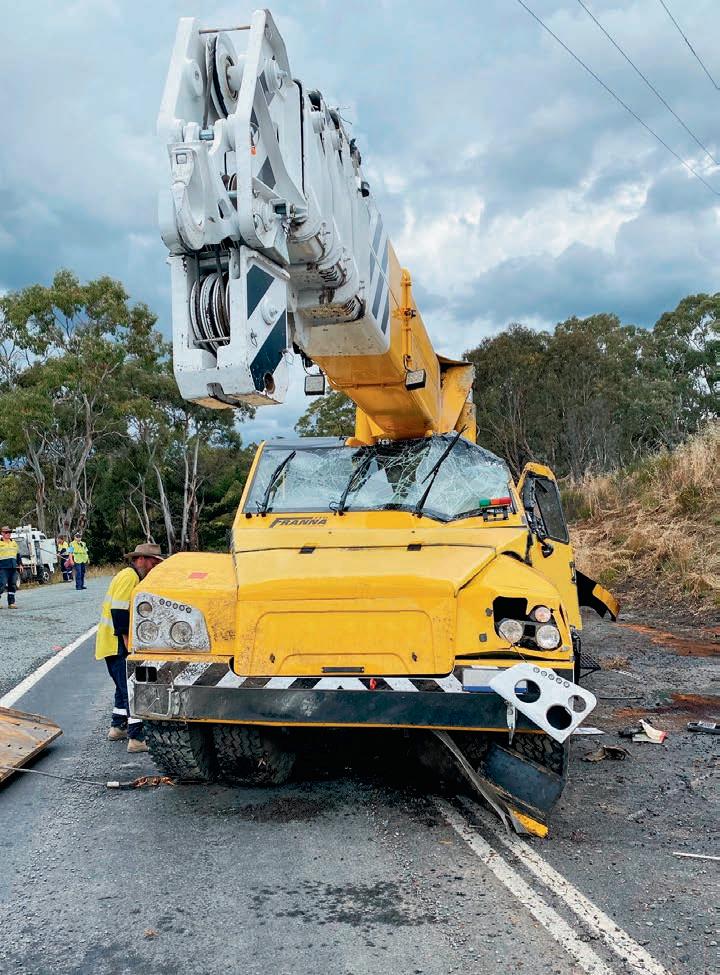
5 minute read
Ben Baden Services
WRITE OFF WRECK TO WORLD CLASS FINISH
Ben Baden and his crew at Ben Baden Services recently completed a major refurbishment of a ‘written off’ Franna AT40. It is the first time Baden and his team have been able to get this deeply involved with the latest model Franna.
The AT40 was an economical write off.
BEN BADEN TALKS ABOUT THE PROJECT
and what his team has learned.
“We purchased the wreck machine as it was an economical write off, meaning the insurance company made a financial decision not to repair it. We do this from time to time as a way of sustaining the workload in our workshop as well as treating it as a bit of a training exercise,” he explained.
“In this instance, the machine was quite badly damaged, so we set it up in the workshop and the first task was to fully strip the machine. The repairs included a new cabin and the majority of cosmetics including panelling and fibreglass finishes were required. We inspected the engine, gearbox, and transfer case, and they were all good.
“However, the boom required structural repairs to be carried out, which meant it needed to be removed. We found there was quite a lot of misalignment on significant points like the boom pivots and the centre articulation, and all of these items needed to be attended to and repaired.
“We have our own in-house line borer/machinist who is set up in a mobile truck. We service a lot of the earthmoving industry with this mobile truck, including the Caterpillar dealership, but it is a really handy trade to have on our books,” said Baden.
All of the work was conducted inhouse with hydraulic cylinders being the only elements outsourced for repair.
“The repair was completed over a period of 12 months. It took this amount of time because the workshop has been very busy and there were delays in receiving parts due to Covid and related supply chain issues.
“Obviously this is the first AT40 to go through this kind of repair process. In fact, it is the first 40-tonne Franna I’ve had in my workshop. One of the reasons to undertake the project was the educational opportunity it provided our team.
“Because we had to work on every aspect of a machine we hadn’t worked on before, the project provided the opportunity to learn about the machine ‘our way’. There were elements of the crane which we hadn’t
All of the work was conducted in house, with hydraulic cylinders being the only elements outsourced for repair.
seen before and it is ideal that the team have been learning about the AT40 on our own unit and not on a customer’s crane. When a customer’s AT40 does come in for repair, we will be ready.
“We literally know the machine from the inside out. We know where all the components are located and what they all do, right through to how to paint the crane. With painting, every time you get a new crane in the workshop, you need to know where to mask up and the segmentation of how to paint – it is different with every machine. Painting may not be a huge issue on its own, but because we now know the crane, we can save one or two days and get the customer’s crane back on the road quicker – all the better for the customer, because in today’s extremely busy environment, every day counts,” said Baden.
Baden goes on to explain how extensively damaged the Franna was through the centre articulation and at the boom pivot point.
“Over the years, we have repaired hundreds of pick and carry cranes and you get to know the most common issues relating to damage when there is an incident. With this AT40, we found the damage to be greater than we have experienced with other pick and carry models we have repaired in the past. This is probably as a result of the machine rolling at speed, where most other repairs have been on cranes which have rolled whilst conducting a lift.
“We are very pleased with the way the machine has turned out. The team are always happy to take on projects which present new challenges. Being the fi rst major incident involving this model Franna, there has been a lot of interest from the industry as a whole. Insurers and crane owners have all been interested in the how, the why and the what, and these sorts of questions have been asked around the project,” said Baden.
Baden talks about the capabilities of his business and how keen he is for interstate crane operators to look to
Ben Baden Services for major repairs.
“We have taken the wreck of a new model Franna AT40, we’ve pulled it right down to nothing, and rebuilt it, which is by no means an easy undertaking. The Sydney market is well aware of our capabilities and customers visit our workshop all the time and there is always something interesting going on. Hopefully, there might be some interstate operators reading this article who will also now better understand our capabilities and
The boom required structural repairs to be carried out, which meant it needed to be removed.
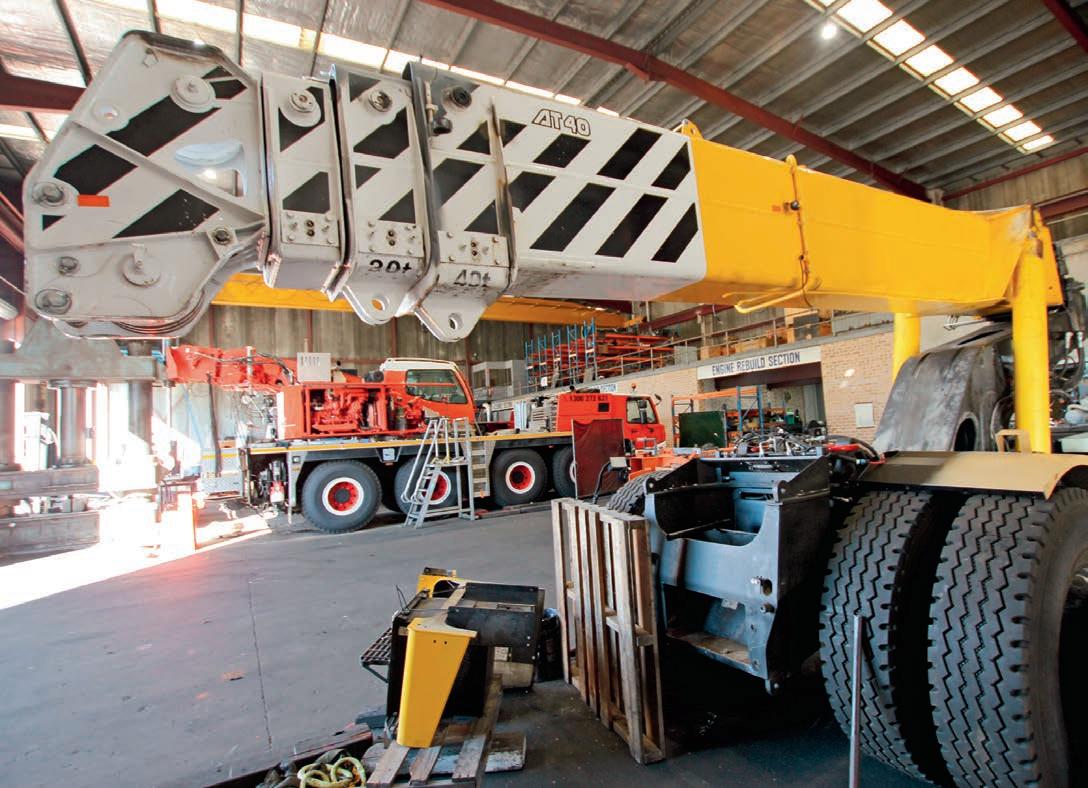
feel more comfortable contacting us in the future.
“I want them to know we welcome their work. Right now, we have a Franna in the workshop from Victoria and we also have one in from Tasmania. We recently finished a repair on the boom of a Tadano rough terrain from Western Australia. It was a 70t capacity crane and they’d damaged the base section. We also have a 100t Grove from the Northern Territory in the workshop. We have always received work from interstate and we’d like to see more of this type of work keep coming. I believe if we stick to trying to support the customer as best we can, particularly through reduced downtime, then we can prove ourselves as a logical and preferred choice for major crane repairs,” he said.
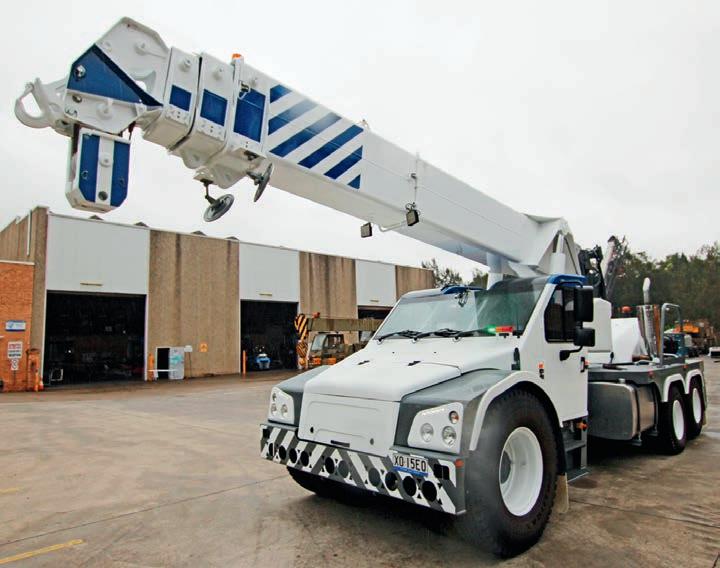
Being the first major incident involving this model Franna, there has been a lot of interest from the industry as a whole.
safer, faster, better.
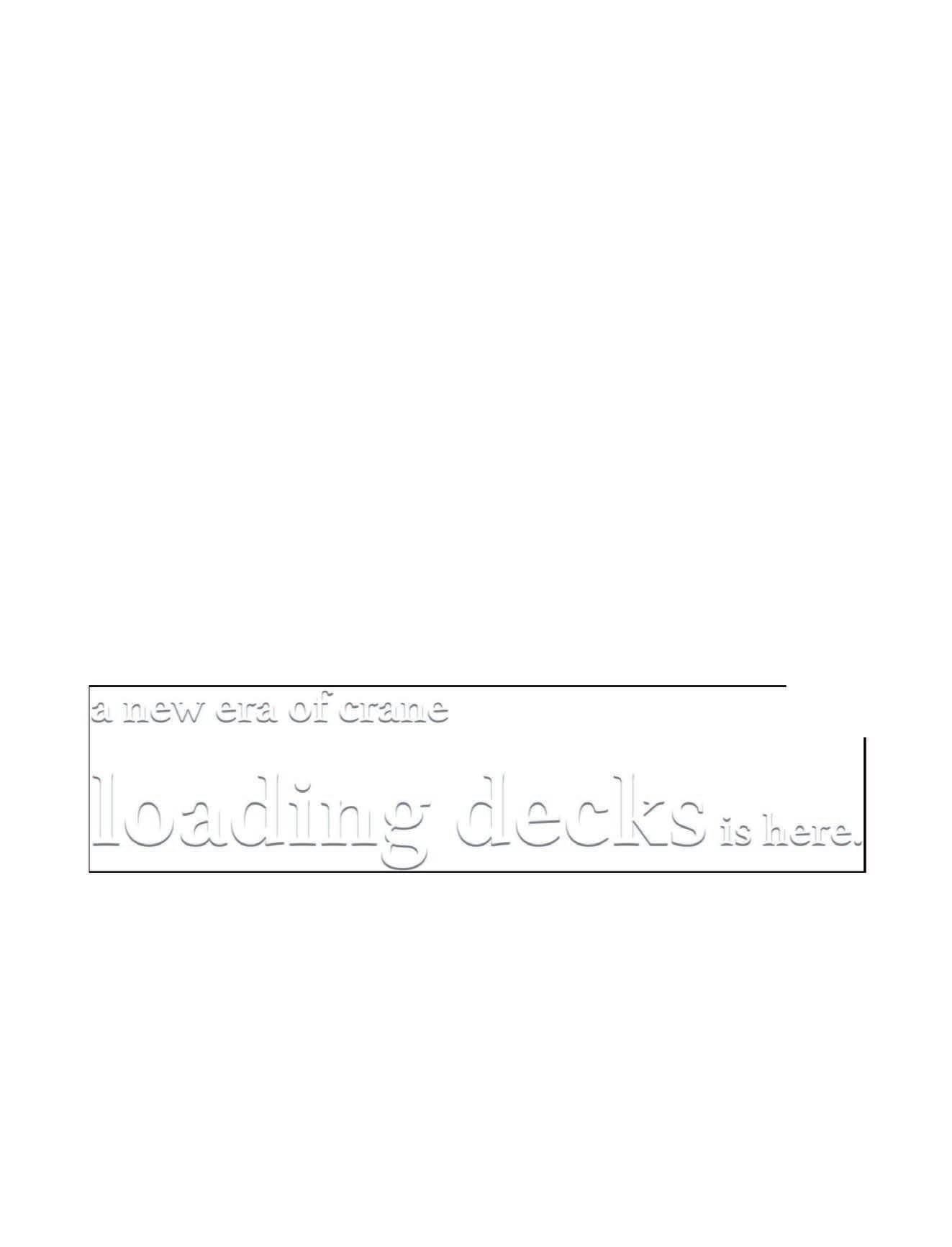
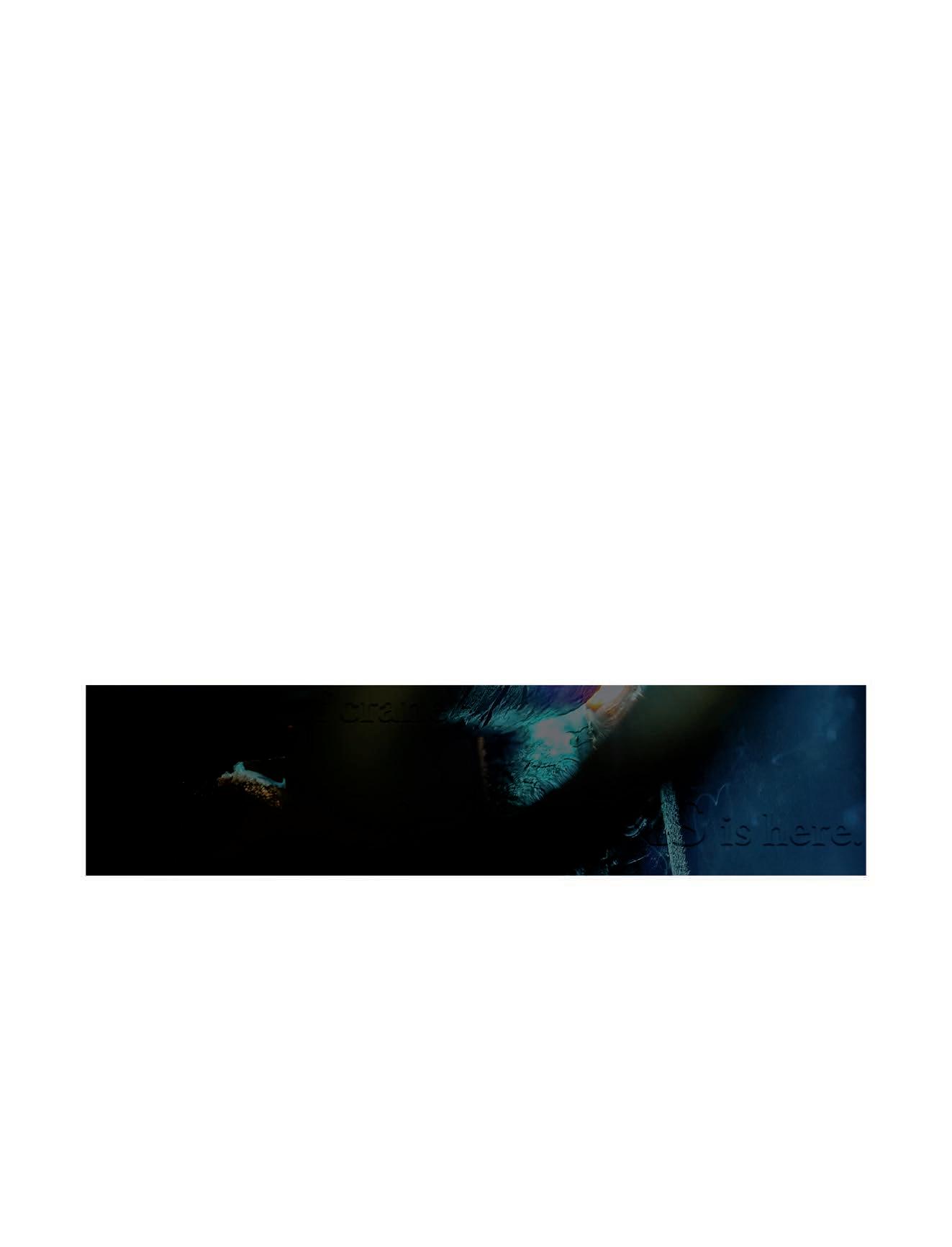
a new era of crane
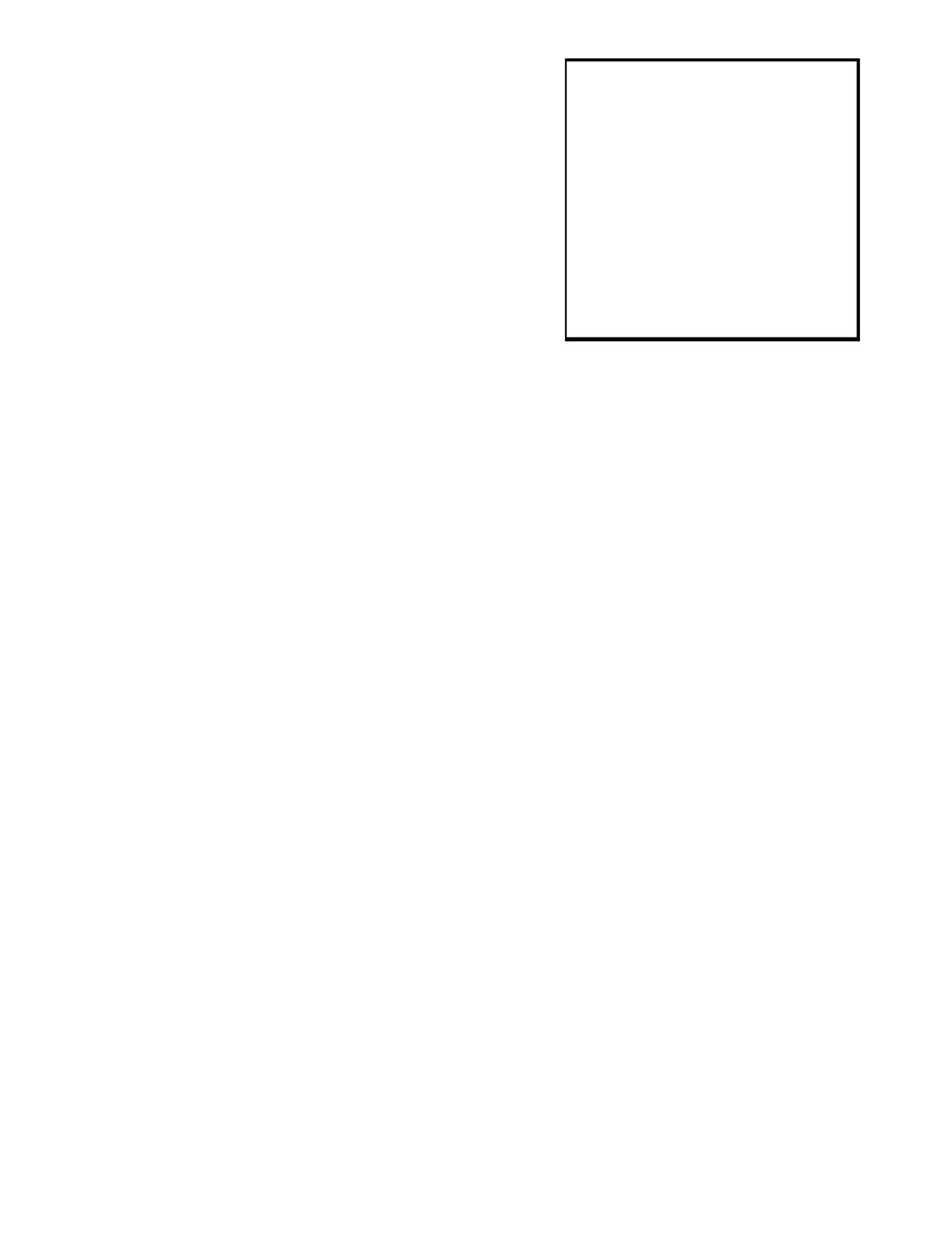
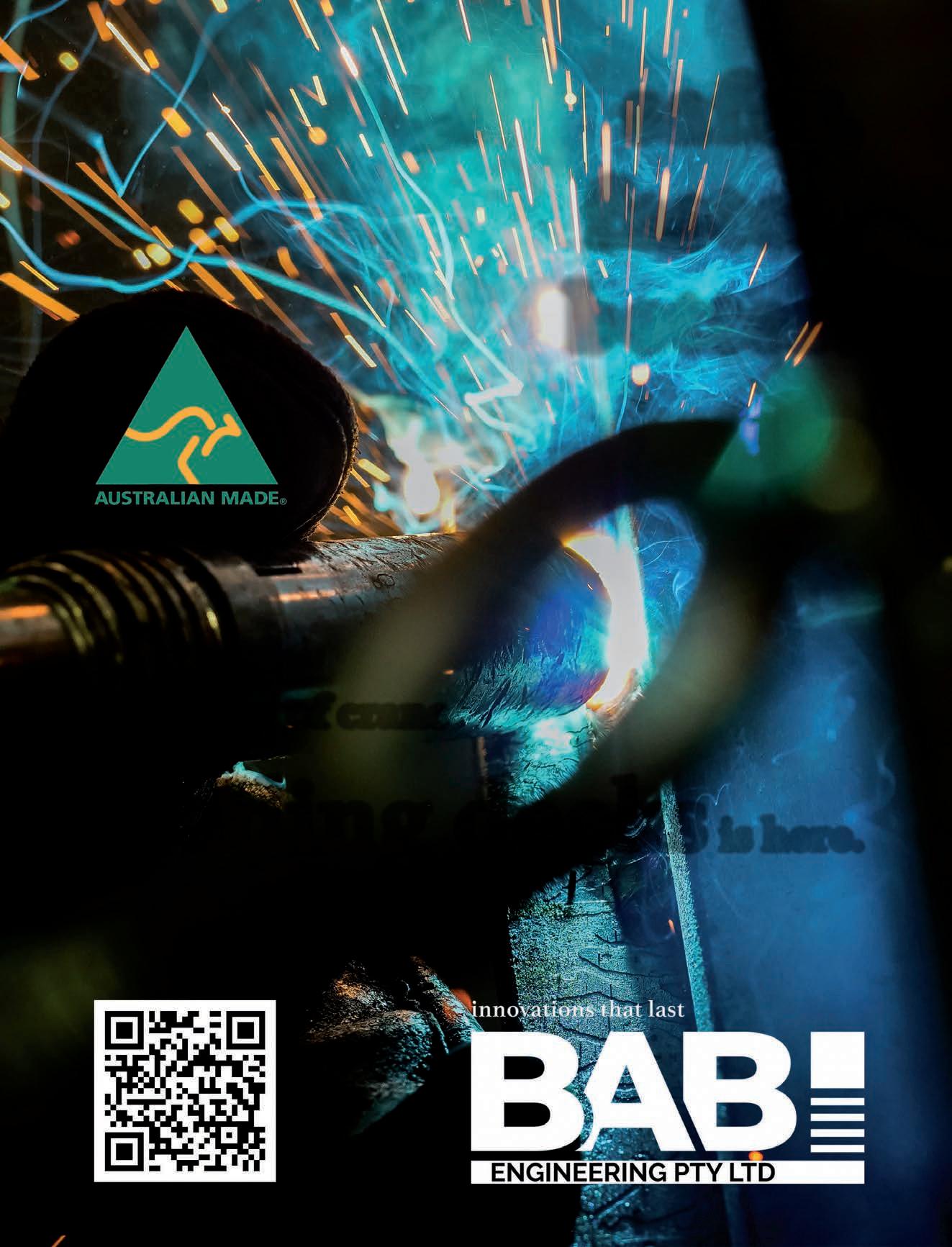