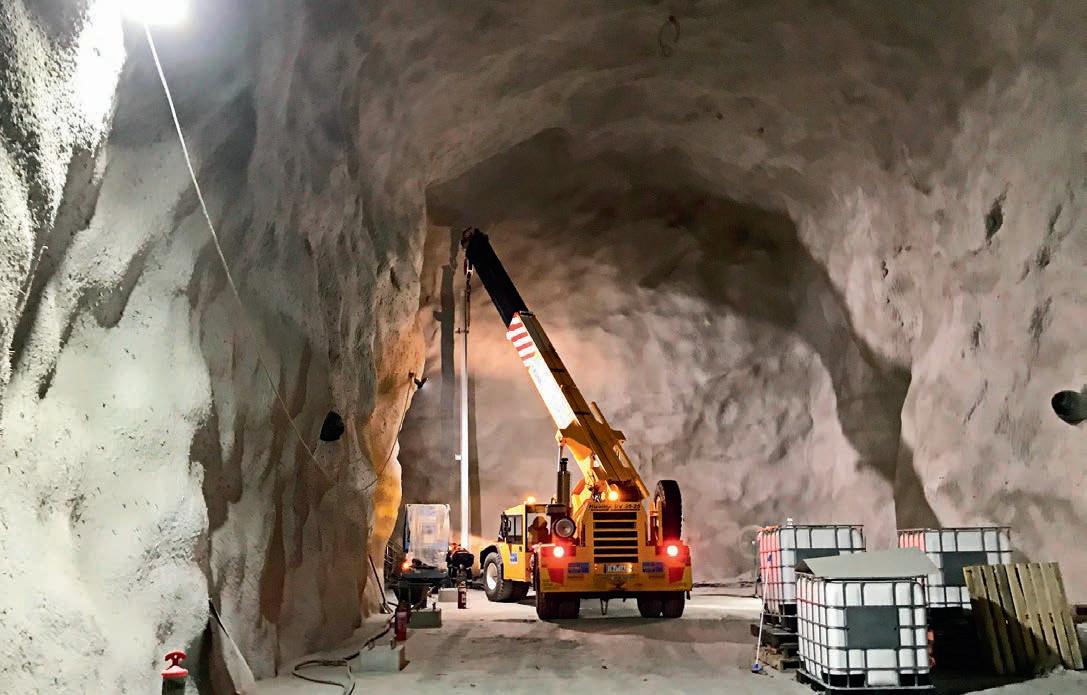
6 minute read
DRA Engineering and Humma pick and carry
Mining companies are insisting all vehicles required to work underground must have the failsafe wet brake.
HUMMA 35 RELEASES THE WET BRAKE
You may ask what is a wet brake?. The layman’s answer is it is the brake of last resort, used when conventional hydraulic or pneumatic brake systems fail to safely bring the vehicle to a stop. DRA Engineering’s Peter Dalla Riva explained the background to this safety innovation for Humma articulated pick and carries.
PICK AND CARRY CRANES WORKING
underground or in open cut mining where they are required to travel down a decline can sometimes result in the brake system overheating, with loss of braking efficiency, which causes the driver to lose control of the crane. If the crane is carrying a load the braking system is required to not only stop or slow the rate of decline of the crane but has the added task of contending with the load, which could double the design capability of the crane braking system.
“Working in this environment it is not uncommon for Pick & Carry Cranes to lose braking systems on long declines necessitating the driver to take evasive action which can result in endangering the life of the driver and surrounding personnel with potential damage to the crane and other machinery in the area.
“Driving procedures do exist when driving down declines but, with the increased amount of underground mining, wet brakes are being specified by mining companies, which are insisting all vehicles required to work underground must have the failsafe wet brake. Where a vehicle manufacture cannot fit a wet brake easily for genuine mechanical reasons, miners are forced to give a dispensation for a limited time, allowing the manufacturer to carry out the design and testing of a wet brake system capable of being incorporated in a new model if it cannot be retro fitted to the existing model pick and carry,” he said.
Like most research and development for Humma, the wet brake project was as a result of a request from a mining company, said Dalla Riva.
“It is interesting to illustrate what happened. The safety department at BHP Olympic Dam, one of the world’s leading miners, contacted us to see if a wet brake could be fitted to a Humma.
“They explained the problem with their Frannas working underground [was that they] did not meet the safety requirement of being fitted with a wet brake.
“BHP had given Franna time to come up with a solution and, after two years, BHP were advised that the wet brake could not be fitted to Frannas and they would have to allow them

The boom rear mounting allows a second winch to be fi tted to operate under the boom.
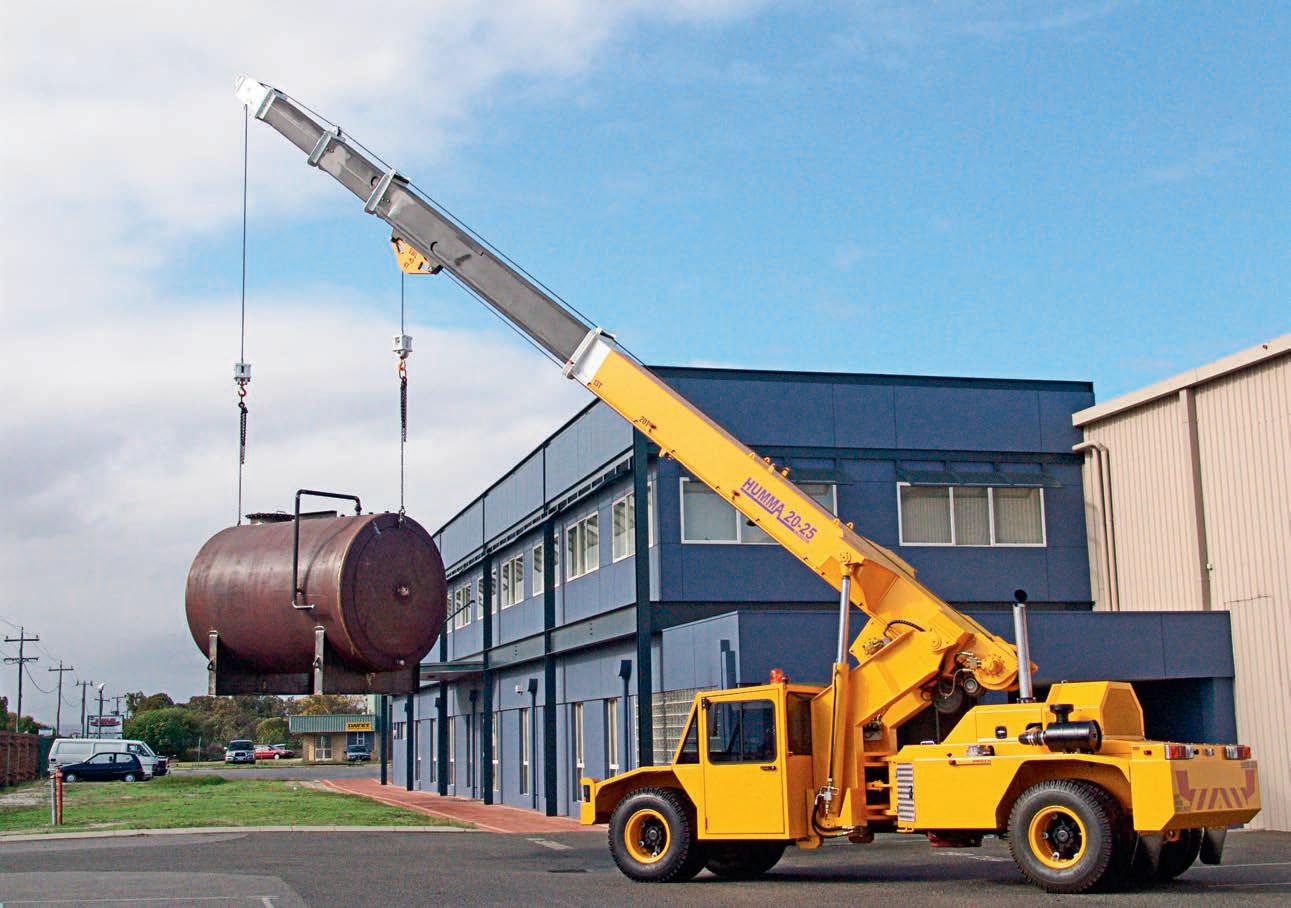
to continue to operate underground as a non-conforming crane.
“BHP Safety considered the position taken by Franna [to be] totally unacceptable, especially since the site had over 15 Frannas working above and underground. DRA was then asked if a wet brake could be fi tted to a MAC25.
“Obviously, we had no interest in designing a brake for our competitor. However, we did an investigative evaluation of the MAC chassis and driveline. Our conclusion was that it could be done but required considerable redesign time and cost possibly necessitate changes to the chassis.
“BHP then asked if a wet brake could be fi tted to Humma 35 [same width as a MAC25]. We informed them that the Humma chassis design had the capability to absorb the energy from deacceleration caused by the wet brake being applied without structural damage and we needed to establish the size of the wet brake capable of handling the weight of the crane and load, and then seeing if it could be installed within the Humma’s existing driveline. Wet brake systems can be fi tted elsewhere on a pick and carry – the Humma wet brake can be fi tted as an extra to the new model Humma 35MK3, where it is bolted into position.
“Within an eight-week project period, the Humma 35 wet brake was developed with designs allowing manufacture to proceed. As part of the
project, BHP requested a 500kg manbasket with overhead protection for underground service, which was also completed. This fulfi lled BHP Olympic Dam safety criteria of having a Humma 35 fi tted with failsafe braking operating with the large capacity overhead protection man-cage.
“The Humma 35 wet brake system provides braking at full load on a 1:5 gradient whilst still retaining the ability to travel at highway speeds in crane travel mode,” said Dalla Riva.
Having solved BHP’s underground pick and carry crane safety issues, DRA also solved it for all underground miners worldwide where pick and carry cranes operate. The speed with which the solution was found was not based on smart 2020 engineering; the ability to solve the problem dates back to 1996
when the design and specifi cation for Humma was prepared.
“Having started in the 1950s, the Linmac business ceased trading in 1996. Franna was the remaining manufacturer of pick and carry cranes, having launched in the 1980s. Both used design and technology that was either out of date or quickly becoming outdated.
“Air-spring suspension had arrived,
with Mack trucks being the early users, leaf springs were on the way out.
The crane hire market was growing, so pick and carry design needed to have the prime mover capable of being driven at highway speed safely with the gearing allowing good acceleration, the chassis had to be rigid not only for use as a crane but capable of being used as a prime mover suitable for fi tting other attachments,” said Dalla Riva.
“The Humma development was two-pronged involving the prime mover and the boom system. The Humma 35 chassis is capable of being multifunctional. In 2001, it was fi tted with a 14T capacity fork for Heinz Foods and used for moving 10t bins of tomatoes in the paddock whilst harvesting. The Humma prime mover can be fi tted with a tyre attachment for handling of a large mine site tyre assembly and a telehandler attachment.
“The boom rear mounting allows a second winch to be fi tted to operate under the boom. A Humma 25 with the dual winch was built for a client in South Australia, who fabricated stainless steel fl at bottom tanks up to three metres in diameter. A Humma 25 dual winch allowed the tanks to be lifted horizontally, loaded onto a semitrailer, delivered to site then unload horizontally and installed vertically, where the support was on the centre of the tank roof.
“The rear chassis confi guration allows suffi cient space to allow modifi cations that may be required when fi tting attachments. The 1996 chassis design made the wet brake installation economically and mechanically possible,” he said.
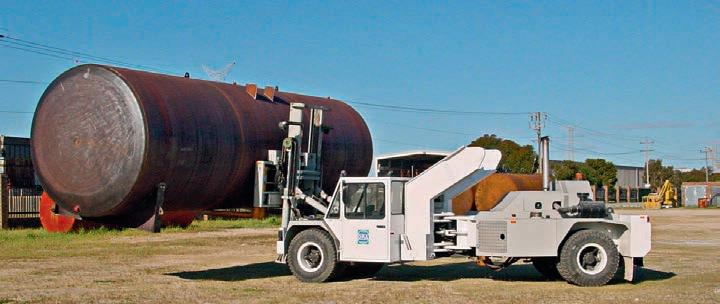
The Humma range of pick and carry cranes are very multi-functional.
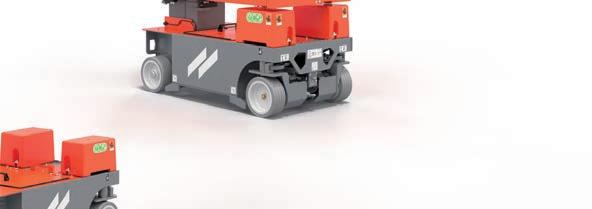
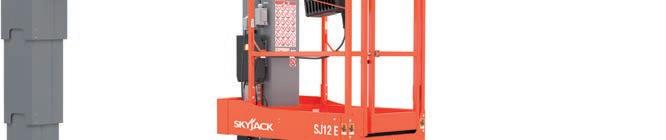
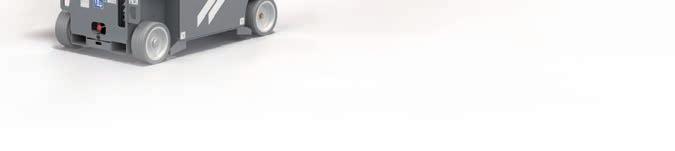
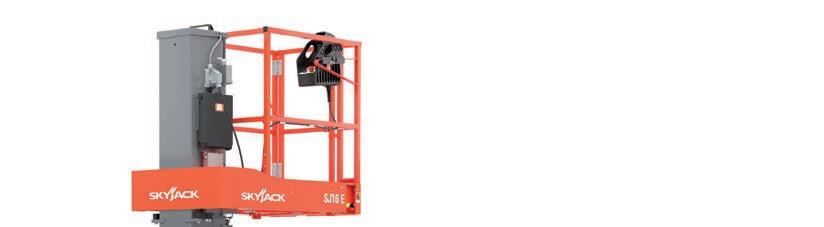
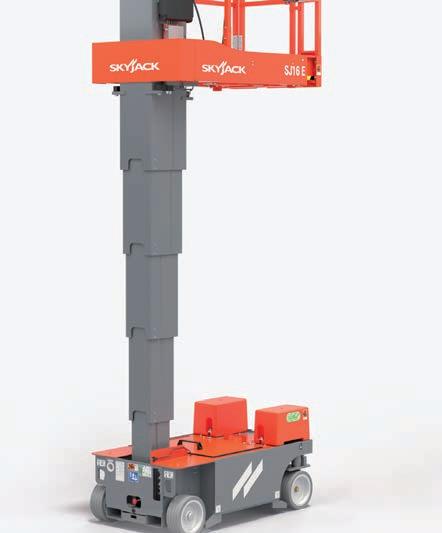
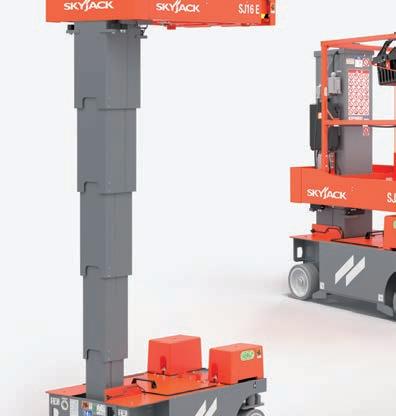
SIMPLY
TRANSFORMED
Skyjack’s Next Generation Vertical Mast Lifts provide a quiet and versatile package with zero emissions. a quiet and versatile package with zero emissions. They deliver benefits in environmental performance and long-term sustainability. and long-term sustainability.
With a new mast design, direct AC electric drive, drivable at full height, and less hydraulic drivable at full height, and less hydraulic connection points, the SJ12 E and SJ16 E boast connection points, the increased duty cycle expectations. increased duty cycle expectations.