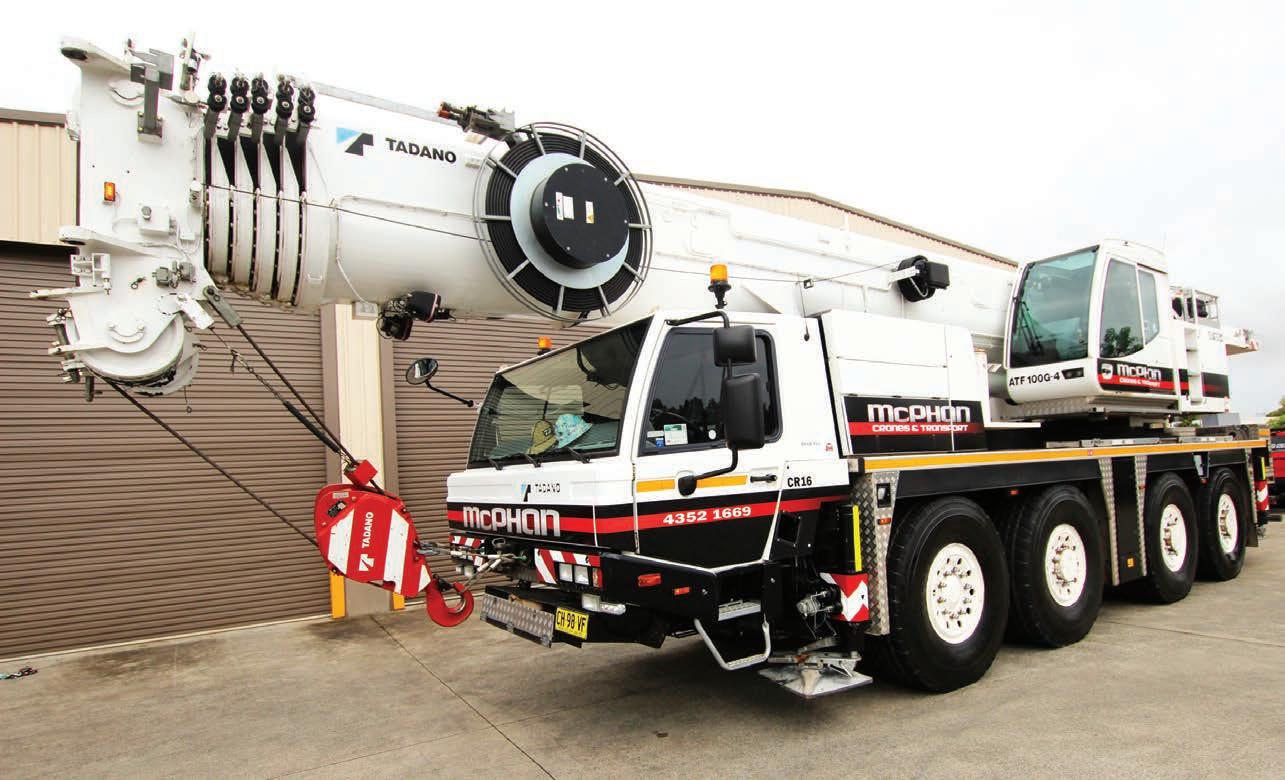
5 minute read
McPhan Cranes and Transport and The Crane Connection
CRANE CONNECTION DELIVERS AGAIN
McPhan Cranes and Transport recently took delivery of a Liebherr LTM 1090-4.2, which had been sourced from Germany by used cranes experts The Baden Davis Crane Connection.
The new Liebherr LTM 1040-4.1 will partner McPhan’s Tadano ATF 100G-4.1.
MCPHAN CRANES AND TRANSPORT HAS
had a long association with The Baden Davis Crane Connection and Anthony Davis, explained Tony McPhan.
“We’ve worked with Anthony, Ben, and Gerhard over many years. We bought our first all terrain, a 35t Liebherr, from the guys almost 19 years ago. The Liebherr LTM 1090-4.2 will be the fourth Liebherr in our fleet and the third we have purchased directly from Anthony,” he said.
“Why do we use The Baden Davis Crane Connection to source our cranes? I regard Anthony as a consummate professional, a personal friend, and key fleet advisor for our company. Ben is our ‘go to’ guy for all significant repairs and he provides an excellent service. It is a pleasure dealing with a family-oriented business with synergies to ours.
“Anthony’s ‘superpower’ is the honest advice he provides to his customers, even when he isn’t selling the product he is recommending. Through regular contact with him and his global contacts, Anthony matched our needs with an ideal machine, which he sourced from Germany.
“Anthony and the team at The Crane Connection have never let us down and their small family business structure offers a personalised experience. The team at The Crane Connection genuinely care about what they do and the customers they have,” said McPhan.
The four axle Liebherr LTM 10904.2 provides a lifting capacity of 100t with 60m of main boom, a maximum lifting height of 76m, and radius of 62m. It also features outstanding mobility, power, and economy. The LTM 1090-4.2 can be driven all over
the world at low cost as it can be configured with a whole series of different axle loads for driving on roads and sites. ECOdrive and ECOmode reduce its fuel consumption and noise emissions making it better for drivers and the environment. The Liebherr VarioBallast and VarioBase innovations enhance its capacity, safety, and flexibility.
McPhan Cranes and Transport was founded in October 2002 by Tony and his father, David, when they purchased the Davies Bros Cranes business.
“I was working away remotely in the mining industry and wanted to be with my newborn son every night. When the opportunity to buy the Davies Bros Cranes business, my father and I grabbed it. We run a family business in every sense of the word, with our employee’s wives and children frequently part of our workplace culture,” said McPhan.
“We have been operating out of our 8,000m2 yard in North Wyong on the Central Coast of New South Wales since June 2007, with plans to potentially relocate as the business continues to grow.
“We have a wide and varied customer base including Tier 1 contractors in the power and infrastructure sectors through to clients in mining, councils, and private customers installing pools, spas, and everything in between. We don’t touch arborist work, we leave that to the specialists,” he said.
McPhan discusses the shape of the McPhan Cranes and Transport crane fleet.
“We operate a mixed fleet of cranes and vehicles, which includes Frannas and all terrain mobile cranes. We also operate rigid trucks with vehicle- mounted cranes and a tilt tray.
With the Frannas, we have four in the fleet – one with a 15t capacity, two with 20t capacity, and one 25t Franna. With the all terrains, we range from 40t, 55t, 90t, and 100t capacities. Our brands include Terex Franna, Tadano, and Liebherr,” he said.
“We continually re-invest in our equipment to ensure the fleet is efficient and relevant and we work hard to maintain our reputation for delivering a prompt, professional, and personalised service. We focus on maintaining long-term relationships and I am delighted to say many our customers have been with us for the 20 years we have been in business.
“We operate throughout the Central Coast and into the Lake Macquarie and Hunter Valley regions. We place a major emphasis on customer service and satisfaction, which helps to develop long-term relationships with our regular customer base, which is paramount. Repeat business with individuals and companies alike is the cornerstone to why we exist,” said McPhan.
Safety and lift planning are integral to the way McPhan Cranes and Transport operates. Mcphan explains measures are in place to ensure lifts are conducted safely.
“Safety is the main priority with everything we do. We regularly conduct
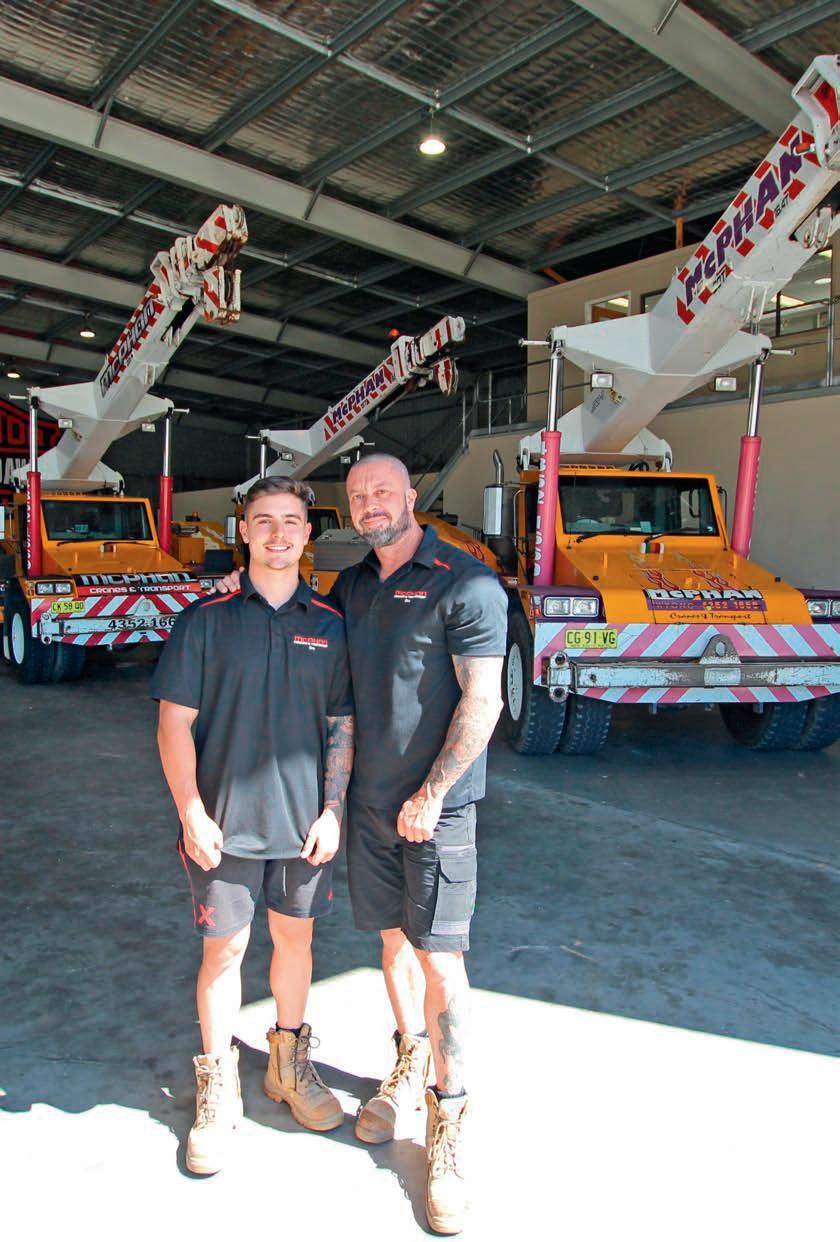
McPhan’s father and son team, Dré and Tony McPhan.
McPhan Cranes and Transport also operates a fleet of Frannas.
site inspections overlaid with the latest lift study software to equip our staff with all the information and tools to perform the service safely and efficiently. We like to visit a site before the lift and we will conduct an initial site consultation with the customer and then provide a documented lift study utilising current software where required,” he said.
McPhan goes on to discuss the experience he has within his team.
“My father, David, retired recently after a career as a structural engineer, which spanned 45 years. I have a number of titles, which include director, operations manager, janitor, and complaints department. I spent 10 years in the mining sectors and I’m now in my 20th year with cranes. I have a Diploma in Engineering, and I’m currently completing a Batchelor of Social Science in Psychology.
“My sin Dré McPhan looks after our allocation and compliance and he is currently studying a double degree Law and Commerce. Britt runs our accounts department, and she has 11 years’ construction trade and customer service experience. All our operators have open tickets and possess diverse experience working in all aspects of the Australian crane hire and rigging landscape.
“Our lift team not only facilitate services to the customer but provide management with invaluable back up and know-how. The experience in our team is the reason we can offer a personalised service which is the reason our customer’s keep asking us back to help with their lifts,” said McPhan.
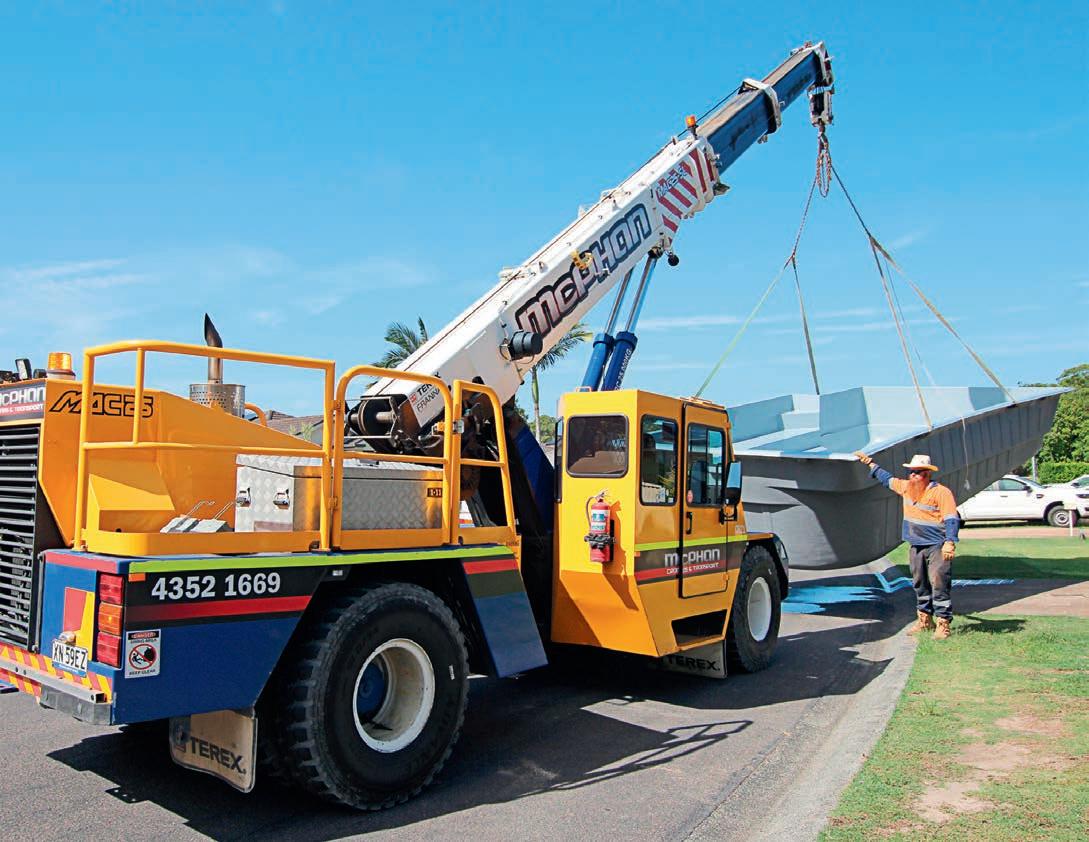