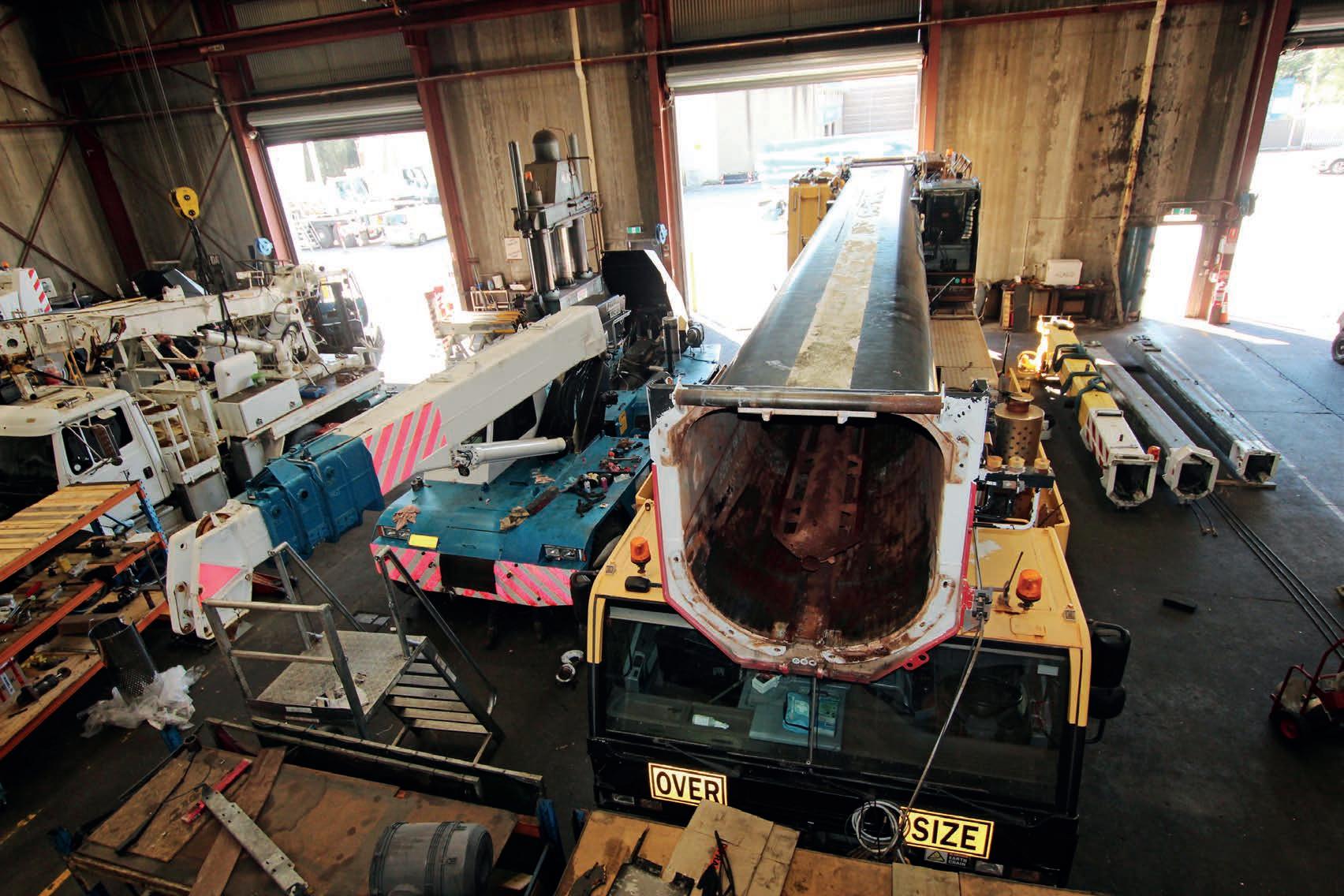
7 minute read
Major inspections: Experience can’t be bought
Ben Baden Services understands the crane’s downtime costs the owner far more than the major inspection itself.
MAJOR INSPECTIONS: EXPERIENCE CAN’T
BE BOUGHT “WHEN IT COMES TO MAJOR INSPECTIONS, we have tried to find the best of the middle ground,” said Baden. Major inspections have long “The quality and depth of major inspections can vary widely. They can been a topic for discussion start with a half day check, which in the crane industry. generates a single page report as a certificate, through to an inspection Ben Baden Services has process which takes many months and been conducting major inspections for many years. includes a highly elaborate strip down of the machine.” He goes on to discuss how the ‘middle Ben Baden discusses the ground’ approach works for Ben Baden options crane owners face Services and its clients. “Our middle ground approach and some of the pitfalls they includes the inspection of components can avoid. that are critical to the crane, and we inspect these to a point that satisfies us that they are in good working condition

without conducting inspection processes which don’t really need to be done and can be costly and add to repair timeframes,” he said.
“We look to inspect the crane in situ and by using the crane itself. For example, hydraulic cylinders can easily be inspected in situ, and we can see if they are ‘creeping’ or leaking oil externally. All the cylinders on the crane can be inspected within hours of the crane’s arrival and, if they are all OK, then that’s great.
“This approach has enabled us to find a niche in the market for customers who want to complete a major inspection in the right manner but without going overboard.
“Our middle ground approach has allowed us to keep the costs of the major inspection to a reasonable number but, more importantly, our approach is designed to minimise the downtime of the crane. We understand the crane’s downtime costs the owner far more than the major inspection itself,” said Baden.
Ben Baden Services is conducting major inspections on cranes from right around the country.
“Cranes from the Sydney metropolitan are obviously driven straight into our yard and cranes from regional areas or interstate get floated. Quite often we will tie in a major inspection if a crane has been involved in an incident and it requires extensive repairs.
“Again, we are optimising on the downtime because the machine is down anyway. Why not have the major inspection as part of the repair process, have it repaired and repainted and ready to go?” he said.
Ben Baden Services boasts a highly experienced team that is capable of the initial assessment of the machine with third-party engineers and third-party crack testing organisations engaged when required.
“Our staff are highly qualified and make the initial assessment of the machine, but we always use third party engineers and third-party crack testing organisations when required.
“If anything is found during the inspection process and the issue requires repairs, we will have a third-party engineer inspect the crane and the engineer will always witness the final load testing of the machine before issuing a final report,” said Baden.
As a result of this ‘middle ground’ approach, and because Ben Baden Services is focused on keeping costs down and time frames reasonable, Baden has seen an increase in the number of major inspections from regional areas and interstate.
“We have been conducting major inspections on machines which were coming to us for major or structural repairs, and we are currently working on
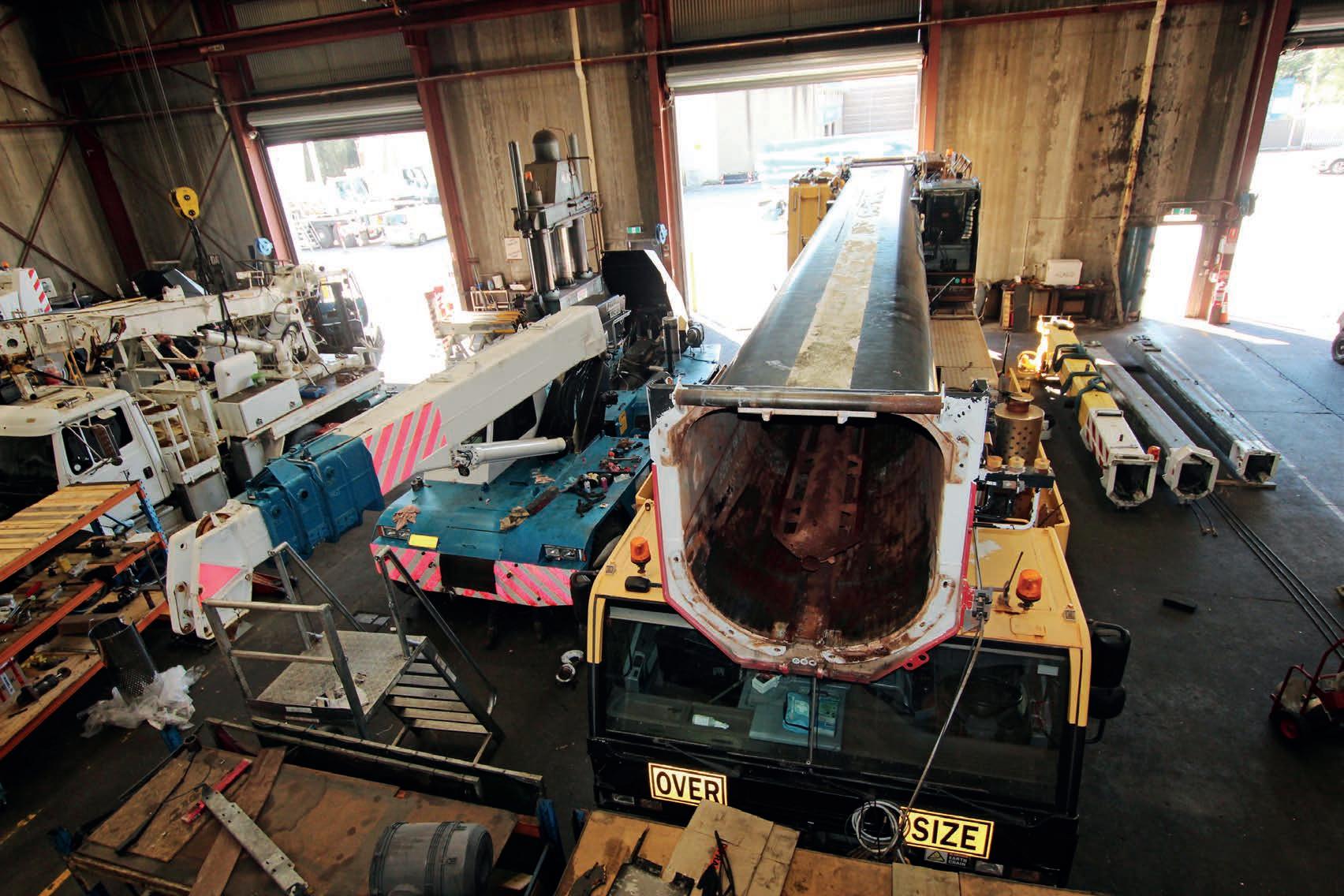
The ‘middle ground’ from Ben Baden Services keeps the costs of major inspections to a reasonable number and is designed to minimise the downtime of the crane.

cranes damaged during the recent floods, but we are now seeing cranes arrive from interstate for major inspections,” he said.
“Our facility is set up with a mechanic shop, which includes sub assembly bays, transmission bays and engine bays. We have a fabrication shop, which includes our own inhouse fitter machinist and we also have our own large wash bay and paint shop facilities. All of our specialists are employed inhouse.
“All of this provides our customers with the advantage of a ‘one stop shop’, which is focused on minimising the downtime of the crane. As I have said, we understand the cost of the repair is not the biggest cost to the crane owner.”
In mid-April, Ben Baden Services had a number of cranes in the yard that had arrived from all over the country. One crane was from the Northern Territory, there was an accident machine from Tasmania and one from South Australia, and an accident-damaged crane was recently fixed and delivered back to Queensland.
Recently, a boom base section from a 70-tonne capacity rough terrain crane was shipped from Western Australia. It had received impact damage and the section was no longer available from the original equipment manufacturer, so there was no option but to repair the boom, paint it and truck it back.
Ben Baden Services provides customers with a generic scope of works for each major inspection and a set price depending on the make and model. If the machine is in good condition and if it has been serviced, maintained, and has a thorough record of annual inspections, generally speaking the quoted price will stand, says Baden.
“Minor issues might be found, but problems that can really blow out costs are leaking telescope cylinders or leaking luffing cylinders and, in these instances, we would expect the customer to know this is a problem before the crane arrives in our yard.
“When the customer has received and considered our scope of works, we discuss the best timeframe for them, and we try to be as flexible as possible to work
around what might be a quiet period for them. Shortly after the arrival of the crane, we make a start on assessing the crane to ensure our timeframe is close to as humanly possible the promised timeframe,” he said.
Following a Ben Baden Services major inspection the customer will receive a detailed engineers report, including a scope of works and details of the works completed. It will also include an independent crack test report, which includes coloured images of everything that has been dismantled and inspected.
“This document is quite extensive in detail and will normally run to 30-plus pages. It presents excellent documentary evidence so there is no ambiguity as to what was and wasn’t required,” he said.
With major inspections being a significant part of the Ben Baden Services business activities, and with countless years of experience in the business, Baden provides some insights as to what a crane business should be looking for when choosing a business for a major inspection.
“When a crane owner is looking to have a major inspection completed, they should certainly do their research. Most importantly and regardless of who does it, they should examine the company’s experience in the crane industry. Are they new to the industry or have they been in it for a long time? This is important because experience can’t be bought.
“The crane owner should research what the company is offering in terms of facilities because this will influence the time it takes to repair the crane. The last thing a crane owner can afford is for a repairer to say it is going to be four to six weeks and it ends up being three to four months.
“The easiest way for the crane owner to ascertain the answers to these questions will be to pick up the phone and chat to the person in charge to get a feeling from them and determine if they are genuine or not,” said Baden.
“My phone is always on, I always answer it and if I don’t because I am busy, leave a message and I always call back.
“If there are crane owners considering major inspections call and talk to me about them. I will be straight up and down. I’ll explain what we do and what we offer. I don’t over promise and under deliver and I like to be as close to the time frame and the money as is humanely practical,” he said.
Ben Baden Services provides customers with a generic scope of works for each major inspection and a set price depending on the make and model. “All of this provides our customers with the advantage of a ‘one stop shop’, which is focused on minimising the downtime of the crane. As I have said, we understand the cost of the repair is not the biggest cost to the crane owner.”
