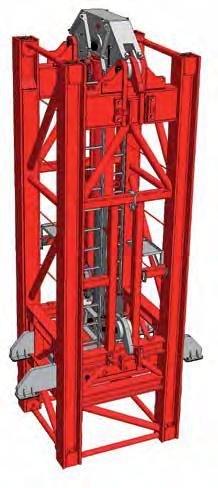
6 minute read
Cosmo’s internal climbing system First in Australia and only the second in the world
INTERNAL STACKER CRANE: AN AUSTRALIAN FIRST
Cosmo Cranes has installed a Terex Internal Climbing System HD12 (for use with a CTL 340-24 luffing jib tower crane) which is a first for the Australian crane industry and only the second time it’s been employed in the world.
THE PROJECT IS THE LENNOX, CHURCH Street, Parramatta. It’s a 48-storey building, 176m in height. The crane system started in the lift pit below basement level eight and it is providing all the hook work for the job. It’s the sole crane on the project and operating six days a week, so the builder is getting good use from it.
Damian Hibbert is a civil structural engineer specialising in construction engineering including temporary works, materials handling equipment, as well as equipment that’s found on a construction site to assist in the construction of the building including staging installation works and other structural works outside the scope of the building engineer. He designed the tower crane climbing system’s support structures.
“One of my clients is Cosmo Cranes and this project is using an internal climbing system HD19 from Terex. It hasn’t been used in Australia before,” he said.
“It is a project that required a tower crane using an internal climbing system to erect the tower inside the building and we looked at a few different options. With the size of the job it was only really a one-crane job. To install a tower crane with an external climbing system up the building was considered too expensive and would delay finishes. There are too many towers, too many ties and we were fairly limited with where we could secure the crane on the outside,” said Hibbert.
“The obvious solution was to use a tower crane with an internal climbing system and recover it with a roof-top crane at the end of the project. This would be more cost effective than running with a tower crane using an external climbing system,” he said.
“We are quite limited with space in the core with this project. It’s fairly tight, so a lot of the typical internal climbers couldn’t fit so we looked at a few options with Cosmo Cranes and different manufacturers with the
Internal climbers are governed by deflection and how much clearance there is.
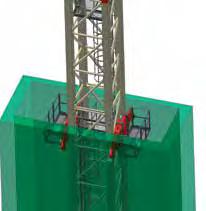
climbing system itself.”
It was always intended to put the Terex CTL 340-24 luffing jib tower crane on top, it was just whether the project required a Terex Comedil internal or external climbing system. After researching the options and looking at the way the system works, it was decided the internal climbing system HD19 would be perfect. It’s quite quick to stage the tower-crane climbing system’s support structure, which is adaptable for future jobs, so there is longevity in the support structure.
In essence, the internal climbing is a ladder climber, unlike the majority of systems in Australia, which are beam climbers. With a ladder climber, two ladders are hung each side of a tower section. These are hung from just underneath the internal climbing system’s support structure. They are hung down each side of the tower section and the crane will use them to “climb” itself up the ladder. It’s a hanging ladder
system and the crane climbs up the ladder. Once the tower achieves the selected height, support brackets are extended to support the structure. Once supported, the internal climbing system lifts up the tower and the next section is inserted. When the crane is ready to climb again, the process is repeated.
“You are governed by the staging of the building and the core,” said Mr Hibbert.
“The core has certain ‘jump points’ underneath the crane. When the crane sway is close to the hitting the core, that is the point when we need to jump the crane. We’ll jump that as high as we can to stick the ladder underneath the formwork system and we jump it right to the other side of the ladder system,” he said.
Once in place, it can sit there until the core does another two or three jumps and then the process is repeated. It’s efficient, it’s quick and the system used to stabilise the crane inside the core is a frame bolted to the tower with rollers which roll up the tower as it jumps. There is little preparation work for the riggers to jump the crane.
This is the first time a system like this has been seen in Australia and only the second time in the world.
“When we started on the project, Terex sent us details of a project in London where they had used the internal climbing system for the first time and we were able to get an idea of how it worked,” said Hibbert.
“Engineers for the London project used a slightly different way of stabilising the internal climbing system because the jobsite requirements vary from project to project. That project used a skid system whereas I wanted to use rollers, so it’s a different type of support frame to accommodate the rollers. The London project went well, and photos of the project reinforced our decision to go with this system,” he said.
All systems and their supporting structures have their strengths and it depends on the projects as to which system and supporting structure will work most efficiently.
The design of this system with the supporting structure, means it is quicker to climb as there is no need to install horizontal beams. However, challenges can arise if the core extends at some stage of the project.
“With this project, the builder installed concrete nibs to act as rails, so the rolling frame of the support structure didn’t need to be extended,’ said Hibbert.
The challenge with this project was getting the chocking system into the core due to a small access point of 1m x 1m. Everything designed to be put into the core had to drop through the hole so it could rigged to get it horizontal, in place and bolted to the tower.
“We made sure we positioned the casting legs of the crane where they needed to go and surveyed to check that and that it was level. In essence, when
The Lennox project in Parramatta, Western Sydney.

we came to put this system in, it ran smoothly,” said Mr Hibbert. “In terms of the system functioning as an internal climber, it is going exceedingly well. The tower is a fairly small foot print so the crane is the right size for the job.”
Internal climbers are governed by deflection and how much clearance there is. The art of staging an internal climber is to marry it with how the support structure is working so it’s repetitive. It’s a typical set out for the formwork jump heights and the builder is not altering pocket positions in the form work. It takes time, experience and skill to stage an internal climber.
Done well, the number of times the crane has to jump is limited. If it isn’t planned well. the crane could be jumping 20 per cent to 30 per cent and that can be costly.