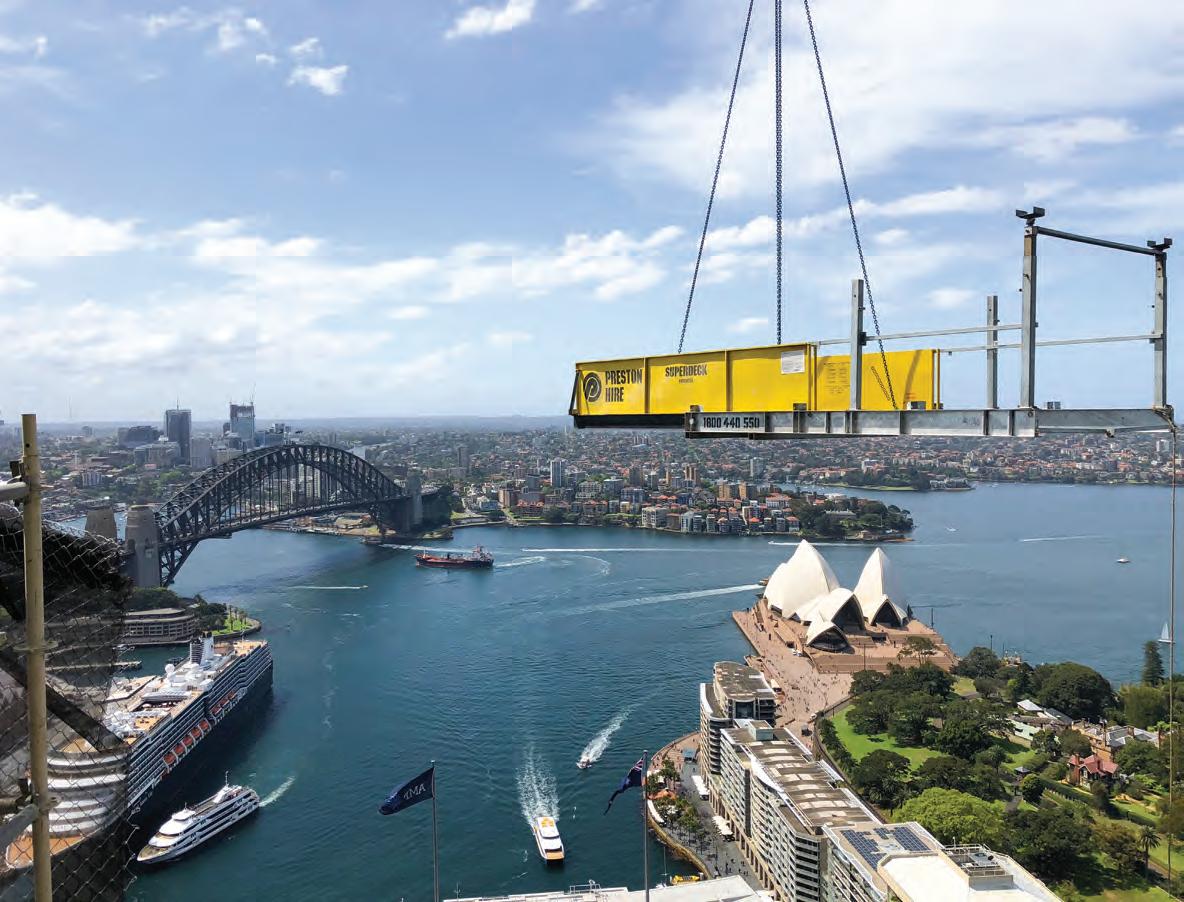
9 minute read
Preston Hire’s SuperDeck sets industry standard
MAINTAINING THE STRENGTH AND POSITION OF A LEADING BRAND
The SuperDeck service and ongoing maintenance program is a key reason customers can rely on the product.
Loading platforms are a standard fixture on most multi-storey or high-rise projects requiring crane access and Preston Hire has been manufacturing retractable loading platforms for over 20 years under the well-known product name, SuperDeck. Anthony Walsh, Preston Hire’s head of SuperDecks explains more.
LOADING PLATFORMS ARE DESIGNED TO
increase site safety and productivity by providing a platform for the loading and unloading of construction material for the site. Preston Hire has been manufacturing retractable loading platforms for over 20 years under the well-known product name, SuperDeck. Anthony Walsh was recently appointed as Preston Hire’s Head of SuperDecks and explains how the business intends to maintain its position as the sector’s leading innovator and manufacturer.
Walsh began his career as a lift mechanic with a focus on maintenance and repairs. He then moved to various roles where his interest in providing solution-based sales for customers grew.
“I’ve been fortunate to work for a number of leading companies in various industry sectors. Success was largely as a result of finding solutions to difficult projects, offering in-depth knowledge of both local and international standards as well as building great relationships with new and existing suppliers. I joined the Preston Hire team in 2020 as a business development manager for the New South Wales Branch.
“I was focused on customers outside
of Greater Sydney with a specific focus on Canberra and Newcastle. This was my first appointment working directly for a hire company, however my previous roles had provided an overlap in skills and a thorough understanding of the responsibilities needed to deliver in this sector. I was thrilled to accept the newly created position of Head of SuperDecks in July of this year,” he said.
Walsh explains what attracted him to Preston Hire.
“Preston Hire is a solutions-based business with great products and even better people. I was immediately impressed with the SuperDeck; its design and the benefits it delivers. I have always been attracted to SME privately owned businesses because I have felt it is important to have a voice. Within SME businesses, there is generally more opportunity to have exposure to the overall business rather than be pigeonholed to the one task. Preston Hire has maintained the ability for staff to be both accountable and noticed, to have access to the owner and the senior management team, whilst continuing to grow the business within our industry sectors.”
According to Walsh there are many advantages to the SuperDeck product.
“While the list of advantages is extensive, I can clearly identify five reasons why the SuperDeck has been so successful over many years.
“Experience: Preston Hire has been able to develop the SuperDeck system over many years. This has allowed us to create an adaptable product capable of fitting almost any site without compromising safety, quality, strength or durability.
“Simplicity of use: We don’t need a power supply, there are no switches or wiring to malfunction or oil leaks to manage, you simply unlock and push it out. It is that simple.
“Consistency: As a truly national, and international business, we have customers who work across multiple regions. These customers can use the same plans and methods from state to state and country to country. Teams and individuals don’t need to start from scratch when it comes to loading platforms, the same system operating in NSW can operate anywhere in the world,” he said.
“Strength: Our SuperDecks are arguably some of the toughest loading platforms on the market. When you think about where they are located and the role they play in the construction process, customers have peace of mind knowing the SuperDeck is up to the task. It is built to withstand rough treatment and as a result, there is less down time on the construction site.
“Design: The design of our SuperDeck allows us to implement our two-prop methodology. This methodology applies almost half the downward force to a slab edge when compared to a traditional four prop installation method. This can also be achieved via our bolt down option should props not be possible,” said Walsh.
Walsh provides more detail regarding the evolution of the SuperDeck and how Preston Hire’s design and construction processes have helped make it an industry leading product.
“The first step in the evolution towards an improved loading platform was in 1994. We recognised the significant risks that fixed, non-retractable platforms which were largely made of scrap steel, were extremely unsafe putting staff and workers at risk. The Transformer Platform was designed and introduced as the first commercially successful, easy to use, vertically stacked retractable platform available on the market. The Transformer Platform offered many improvements compared with previously used platforms, however we held a belief that a safer and more effective loading platform was still achievable.
“Significant reviews and analysis of the Transformer Platform ensued over the following years. After a great deal of investment in design, engineering, manufacturing and testing, the Preston SuperDeck was successfully launched in Australia in 1998. It was subsequently launched in the United States, New Zealand, Europe and Canada. In line with our mantra to always be improving and setting the industry benchmark, we continue to review and make subtle changes to the SuperDeck design to improve the customer on-site experience and overall capabilities,” he said.
“All SuperDecks have certified engineering and are quality and safety checked before dispatch. This aligns with our ISO-9001:2015 certification that Preston Hire works incredibly hard to maintain. We have held ISO accreditation for six consecutive years following successful annual audits of our processes and standards. ISO 9001:2015 is an international standard dedicated to Quality Management Systems (QMS).
“It outlines a framework for improving quality and a vocabulary of understanding for any organisation looking to provide products and services that consistently meet the requirements and expectations of customers and other relevant interested parties in the most efficient manner possible. We take this very seriously as it
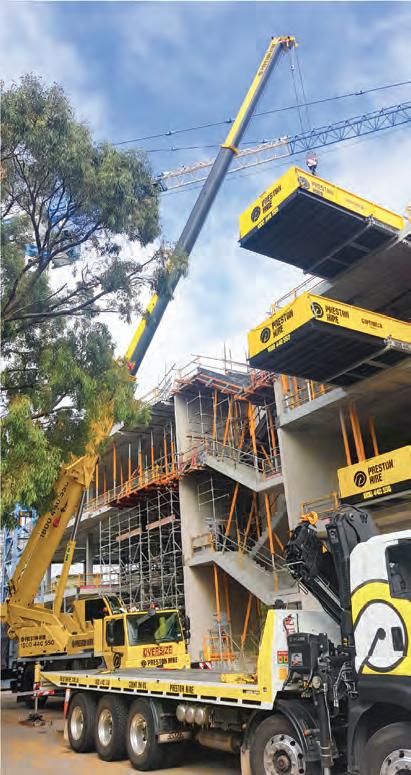
Preston Hire is a solutions-based business that prides itself with great products and reliable staff.
SuperDecks are now being used in a number of unique scenarios including major tunnelling projects in Sydney and Melbourne.
reflects our commitment to delivering the best,” said Walsh.
Walsh goes on to explain what he sees as the major challenges for the SuperDeck.
“I see the non-regulation of our industry as the biggest challenge. This has led to a vastly increased number of suppliers on the market. Many of these suppliers are sourcing and offering what seems to be the cheapest product, and in many instances, they are using these as a ‘loss leader’ to drive their core product range onto jobs. The SuperDeck is our core product range and as such our standards are high. Our concern is that without industry regulation and management of quality control in the wider industry, it is inevitable that standards will fall and with this comes grave concerns around the safety of loading platforms and their ability to withstand the rigours of the construction process,” he said.
“Although loading platforms have become something of a commodity with numerous options now available to builders, we will continue to position our SuperDeck as a premium product for safety and reliability. When other providers lower their standards, cut quality and tender for projects based on price alone, we will continue to raise our standards of design, engineering and manufacturing. We are never satisfied and believe there is always room for improvement.
Walsh explains what he sees as the major implications and risks for a builder who is prepared to hire loading platform on price alone?
“Besides the obvious risk of catastrophic failure resulting in injury or worse, a builder needs to factor in other considerations than the price. For example, there can be considerable cost implications if additional propping is required. How much does lost productivity cost a construction site if a loading platform is not fit for purpose and needs replacing? How much does it cost a builder if the loading platform doesn’t meet the design of the building and changes are required?
“Hiring the cheapest product often leads to false economy. Basing a decision solely on the quote price and not considering the usability or the additional ongoing costs related to that “cheap” initial price nor do we consider it ‘best business practice’. For example, the ability to stack our SuperDecks as opposed to staggering them, has huge cost benefits in building design and crane operator’s time, and it can lead to a building being delivered much quicker. Many loading platforms suppliers avoid these conversations.
“SuperDecks are a quality product at a fair price and builders receive many advantages from our product when compared to others on the market. Peace of mind would be top of this list. Builders have enough to worry about, the last thing they need be concerned about is loading platforms slowing down deliveries or worse, becoming a hazard to their site,” said Walsh.
The SuperDeck service and ongoing maintenance program is a key reason customers can rely on the product says Walsh.
“Maintenance of our fleet is extremely important, and this is managed by our factory trained staff, onsite boiler makers and fabrication teams. All equipment is quality controlled with an extensive pre-hire and de-hire process which ensure all damages are repaired before the next hire. We respect the appearance and quality of both our own products and our customer’s sites. Before delivery to a new site, we ensure every SuperDeck is fully functioning, freshly painted and looking brand new,” he said.
SuperDecks are now being used in a number of unique scenarios including major tunnelling project in Sydney and Melbourne says Walsh.
“Preston Hire works with a number of customers to provide custom made solutions for their projects. Each job is assessed individually, and appropriate recommendations are made. Recently, we provided a Lend Lease project at Pitt Street North Sydney, with a custom-made solution to provide a platform with a 10t loading weight. This was achieved through a detailed engineering review by Preston Hire, the design and manufacture of a custom bracket and appropriate propping to ensure safety was maintained at all times,” he said.
“We also provided a modified 2.2 SuperDeck for the Metro Tunnel at La Trobe Street in Melbourne and West Connex 3A Project in Sydney. SuperDecks provide the same benefits for tunnelling projects as they do in vertical high-rise construction. They are a safe means to get materials in and out of the project. In these instances, the platform required a vertical install from ground level down into the plant room. With very limited options for getting machinery and gear into the tunnel, our SuperDeck was the ideal solution,” explained Walsh.
“We are 100 per cent committed to continuing to provide the industry with a service that is so much more than just product supply. I have been charged with the responsibility of ensuring every Preston Hire SuperDeck®️ experience is the best in the business. I look forward to further demonstrating why the industry can count on us for their loading platform needs,” he said.
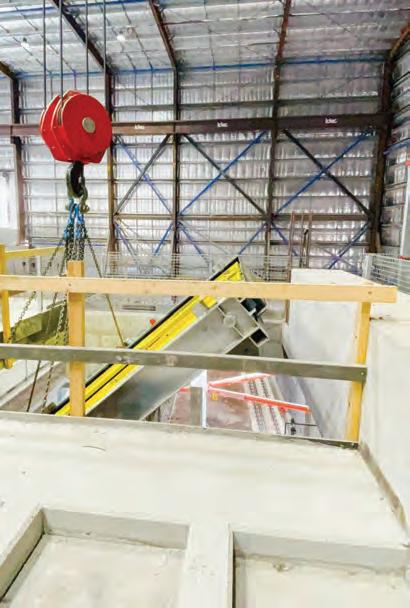