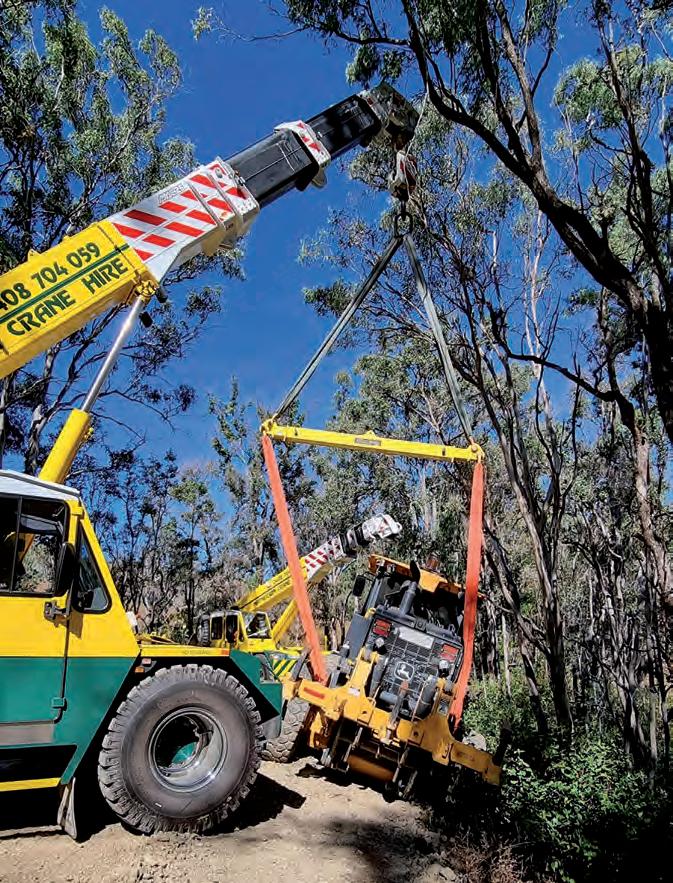
7 minute read
Frannas in grader rescue
DUAL FRANNAS PERFORM IN MOTOR GRADER RECOVERY
When a 22t motor grader got into trouble in the Bundaberg Region of Queensland, Matherson Crane Hire sent two Franna MAC 25 SuperLifts to the rescue.
TO ACCESS THE SITE, THE FRANNAS HAD
to navigate the Boolboonda Tunnel which is an abandoned heritagelisted railway tunnel at Tunnel Road, Boolboonda, in the Bundaberg Region. The tunnel is 192 metres in length making it the longest unsupported manmade tunnel in Queensland.
On arrival, the Matherson Crew carefully planned the lift to ensure the motor grader couldn’t move in an uncontrolled manner and that no damage was done during the recovery.
To manage the 22t grader, the rear crane had a weight 13t and the rigging included a 30t Maxirig bar and 8t 6m slings which were doubled on the top of the grader and 10t x 3m slings on the bottom. The spreader was utilised to minimise/stop the far sling from damaging the engine covers.
The front crane had a weight of 9t with 2 x 10t 1m slings attached to the lifting lugs at the top of the chassis, above the front axle, to maintain a high centre of gravity on the lift to maximise control.
The team and the Frannas executed the recovery perfectly, says Wayne Matherson, Matherson Crane Hire.
“The team did a great job and executed the lift perfectly. The motor grader was in a fairly precarious position by the time they got there, so they had to carefully prepare the rigging and the position of the Frannas for the lift to go smoothly.
“Our business originally grew on Pick and Carry cranes and we have been running 25t Frannas for over 10 years. The addition of extra lifting capacity by adding SUPER LIFT to our current Franna MAC 25’s has only extended the capability of an already great machine. As usual, the Frannas performed perfectly with this lift and the client was happy to have his grader back on stable ground with no damage. The crew also enjoyed the journey through the Boolboonda Tunnel which doesn’t happen every day,” said Matherson.
To manage the 22t grader, the rear crane had a weight 13t and the rigging included a 30t Maxirig bar and 8t 6m slings which were doubled on the top of the grader and 10t x 3m slings on the bottom.
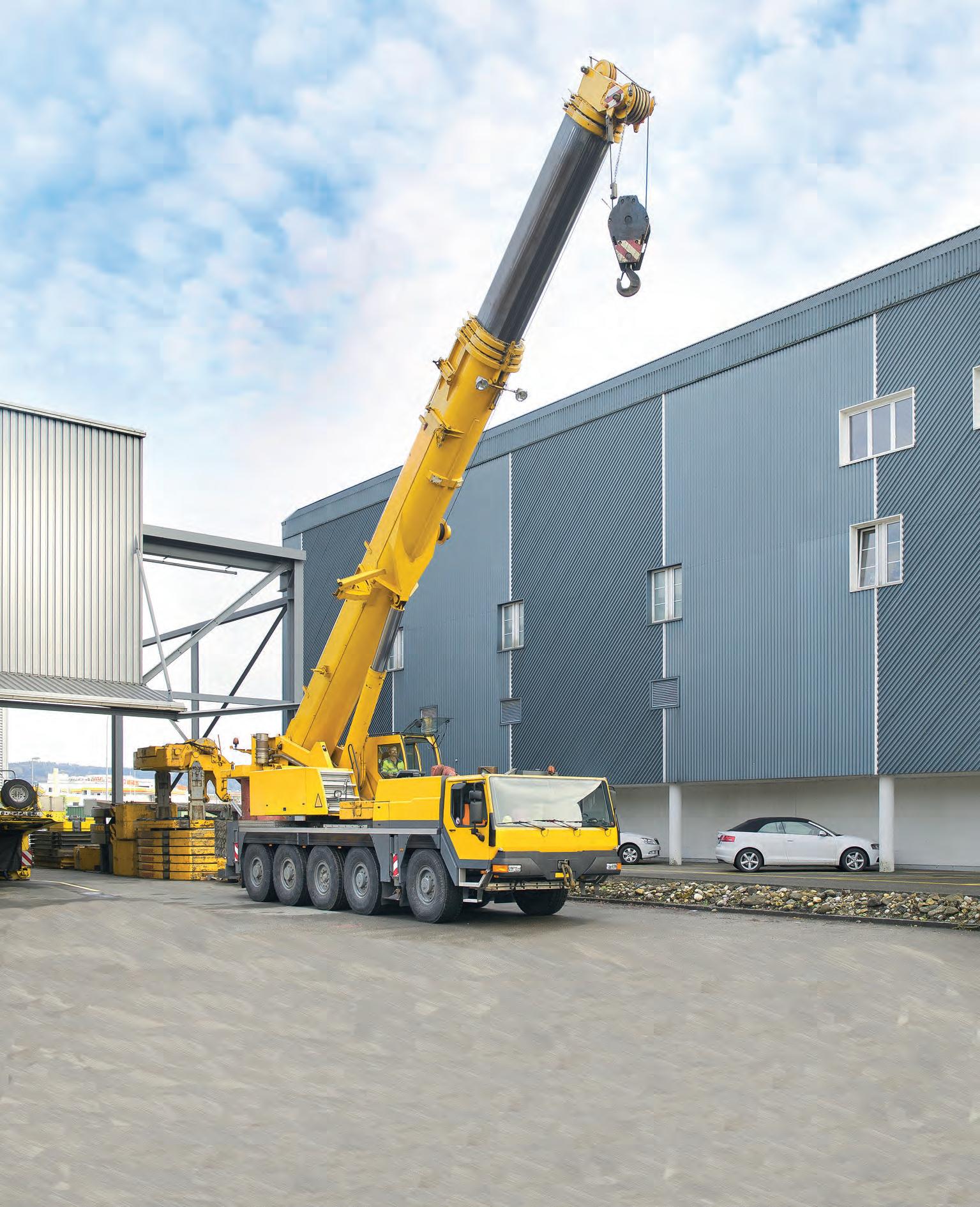
GROVE ROUGH TERRAINS BIGGER, BETTER STRONGER
In 2016, Manitowoc launched the new range of Grove Rough Terrains (GRTs) which have proven to be popular on jobsites around the world. Federico Lovera is the Product Manager for GRTs in Europe, the Middle East, Africa and the Asia-Pacific. He discusses the features and benefits of the range and explains why the various models will suit the Australian market.
“THE GRT RANGE OF ROUGH TERRAINS
was first introduced in 2016 with the GRT880 and the GRT8100 models. These replaced the previous models the RT880E and the RT890E. The GRT880 and the GRT8100 models were the result of an extensive re-design and testing process conducted in both the Niella Tanaro factory, in Italy and the Shady Grove factory, in Pennsylvania in the US. More recently, we added the Grove GRT655 and GRT655L models to the range.
“We undertook a complete review process of the rough terrain range. We listened to feedback from customers noting likes and dislikes about the products and we collected information and data on the performance of the machines. We then conducted an extensive internal analysis review process which included the engineering and after sales teams,” he said.
“The main purpose of the review process was to design and manufacture more reliable machines. With the new GRT range we have focused on the reliability of the cranes. We changed the design, but we also carefully chose the suppliers for the componentry contained within the crane. In fact, we validated every crane component at the Product Verification Centre in Shady Grove,” said Lovera.
The centre features hot and cold weather chambers and the components were subjected to all types of testing including pressure, water resistance and humidity testing says Lovera.
“We conducted all types of testing using hydraulic test benches and hot and cold weather chambers. In terms of scope, we conducted accelerated lift cycle testing on every new component including cylinders, pumps and sensors. When a component was successful and free of defect, and this is after 10 years of the accelerated lift cycle testing, it was seen as being of the right quality to be included in the machine.
“For example, we had cylinders operating continually, 24 hours a day, seven days a week on a hydraulic testing bench testing the sensor of the outrigger spread or the boom extension cylinder. The cylinder for the GRT880 outrigger totalled 80kms travelling back and forth. This testing was designed to validate every component and the results came together with the GRT880 and the GRT8100. We are now confident with the reliability of these models, so much so that we provide customers with a standard two-year warranty,” he said.
Federico Lovera, product manager, Grove Rough Terrains Europe, Middle East, Africa and Asia-Pacific.
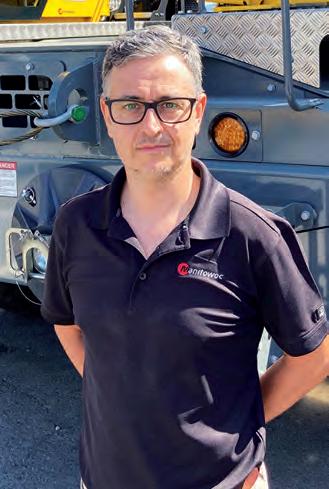
Manitowoc offers a 50t rough-terrain crane with two boom versions. The options include the GRT655 with a 34.8m boom for heavy duty applications and the GRT655L with a 43m boom.
A new boom extension stowage system for both cranes’ hydraulic and off-settable jib options decreases erection and stowage time by 60 per cent when compared with previous generation Grove cranes. This enables operators to set up and disassemble the cranes in less time, saving money and increasing return on investment.
The 100t Grove GRT8100 has exceptional reach with its 47m boom that has a maximum tip height of 49m. With a full complement of boom extension and insert options, the crane also has an outstanding reach of 77 m. The boom is lighter and longer than its predecessor, but has the ability to lift heavier loads throughout the load chart. Capability such as this will allow customers to get unparalleled usage out of a 100t rough-terrain crane.
The 80t GRT880 features a shorter 41 m boom that is also lighter than the GRT8100 boom. Customers will find this boom especially useful for the mining sector, equipment maintenance and infrastructure projects.
With increased capacity at mid range and maximum radii, the GRT8100 and GRT880 are more versatile than competitors’ cranes – they boast up to 16 per cent greater capacity at full radius, 13 per cent greater capacity in mid-range applications and 27 per cent greater capacity at close radii. With off-settable boom and fly extensions, the cranes enable customers to lift heavier loads to greater heights, helping companies compete for - and win - bids for projects they may not have been able to previously.
The GRT8100 is the only crane in its class to offer a hydraulic luffing jib that can be configured at lengths between 10m and 17 m. Other optional boom extensions for the cranes include a 10-17 m manual off-settable bi-fold boom extension with fixed offsets at 0, 20 and 40° as well as a heavy-duty 3 m jib that is off-settable to 40°.
A new boom extension stowage system for both cranes’ hydraulic and off-settable jib options decreases erection and stowage time by 60 per cent when compared with previous generation Grove cranes. This enables operators to set up and disassemble the cranes in less time, saving money and increasing return on investment.
The GRT8100 and GRT880 also have best-in-class line pulls at 7,883 kg on both the main and the auxiliary hoists. The stronger pull results in fewer parts of line being needed to lift loads, which will lead to increased productivity on the job site and faster customer payback.
Manitowoc also offers a 50t roughterrain crane with two boom versions for different applications. The options include the GRT655 with 34.8 m boom for heavy duty applications and the GRT655L with 43 m long boom for those applications where reach is a must.
At 43 m, the Grove GRT655L has the longest boom in its class. With this long boom, the rough-terrain crane has the advantage that no additional jib is needed for long reach jobs. And when working with a jib, operators can reach more than 56 m and nearly 60 m at maximum tip height. The shorter boom version, GRT655, has the strongest load charts in its class and is the preferred choice when extra capacity is needed. Both models share a light and compact carrier, weighing only around 35 t and measuring less than 3 m in width. Therefore, crane operators can drive into narrow spaces such as refineries, power plants and densely populated areas and access a greater variety of jobsites.
The narrow dimensions of either model – the most compact in their class – make the GRT655 and GRT655L easy to transport on a trailer and they can be shipped in one complete load. In addition, when manoeuvring around a jobsite, operators benefit from all-wheel steering with a choice of four steering modes – two-wheel front, two-wheel rear, four-wheel crab and four-wheel coordinated. In coordinated mode, the crane has a turning radius of just 6.4 m, allowing it to access even the most congested sites.
The Manitowoc Crane Control System (CCS) makes it intuitive to set up, control and command the crane. This system is in common with all-terrain cranes, as well as truck-mounted and