
6 minute read
World’s longest running construction project speeds up Potain cranes help fast-track completion of Barcelona’s Basilica Sagrada Familia
BRINGING A VISION TO LIFE
Potain cranes help realise Gaudi’s130 year old vision with the imminent completion of Barcelona’s Basilica Sagrada Familia.
ONE OF EUROPE’S MOST FAMOUS construction sites, Barcelona’s Basilica Sagrada Familia, is the focus of unprecedented construction activity in a bid to complete the vision of the original architect, Antoni Gaudi.
More than 130 years after the first stone was laid, the end is within sight for Barcelona’s Basilica Sagrada Familia. Thanks to an influx of funding, striking innovations, old fashioned craftsmanship and four Potain tower cranes, the famously unfinished church is now on schedule to be completed in 2026. This coincides with the 100th anniversary of the death of its architect, Antoni Gaudi.
Millions of travellers visit Barcelona each year and this has meant salvation for the Sagrada Familia foundation. The church currently sees roughly four million tourists a year, each paying an entry fee ranging from $24 to $64, meaning the foundation, which is overseeing the basilica, has enough money to finish the main nave, a soaring expanse of treelike pillars and multicoloured stainedglass. The nave was consecrated by Pope Benedict in 2010.
Today, more than two dozen architects are working on the project - most of them local Catalans - and 200 workers in total are involved in the construction.
A construction site as unique and monumental as the Basilica of the Sagrada Família requires a carefully selected range of cranes to help complete the construction process.
Potain tower cranes have been on site since 1998, and before that the only crane on the job site was a Richier crane, part of
Construction of the unfinished church is now on schedule to be completed in 2026, coinciding with the 100th anniversary of the death of its architect, Antoni Gaudi
the Potain Group through the BoileauPotain-Richier (BPR) brand. This crane had been on site since the late 60’s.
Currently, there are four Potain cranes operating on the construction site: MD 175B – MD 238 – MD 125B and the MD 560 B. The construction site team call the MD 560 B the ‘Mother of All Cranes’ because it feeds work to the other cranes.
The cranes only play a part in accelerating the construction process; changes to the way key components are manufactured is also key.
As the know-how and financing fell into place, the Sagrada Familia foundation began to study what it would take to actually finish the church. Enter British structural engineer Tristram Carfrae, the deputy chairman of Arup, the design and engineering firm that built the Sydney Opera House. He found himself walking out of a meeting in 2014 with the foundation thinking, “Did that really happen? Do we really have the opportunity to work on the most fantastic project in the world?”
The challenge was how to speed up the rate of construction by a factor of 10 and complete the project by 2026.
Part of the answer lies at Galera, a sprawling work site 90 minutes north of Barcelona. Here a small crane is used to slide multi kilo ‘anchor blocks’ onto an interlocking row of granite stones that will be fixed to a steel plate and bound together into panels. Because the anchor has holes through which steel rods will be inserted, there is a tiny margin for error. The panels are Arup’s solution to the complex problem of building the Sagrada Familia’s towers. To make them light enough, the engineers could have built a steel frame and clad its surface with stone.
“That didn’t fit with our notion of quality – from the inside it would have looked like a Hollywood set,” says
Carfrae. Instead, they make the panels entirely of stone-albeit blocks only 300mm thick, rather than a cathedral’s more typical one to 2 m.
Carfrae and the Arup construction team were also faced with the challenge of building 10 more towers, among them the 172m Jesus tower which will be the tallest structure in town. Questions needing answers included, “How do we account for the fact that as you complete the church, the available area on site for assembling things diminishes? And how do we do all this with the quality the church and Gaudi’s vision demands?”
In 2012 there were five cranes involved in building the Sagrada Familia. When faced with beginning construction on the tallest towers (the central towers of the evangelists, the Virgin Mary and Jesus Christ), it was necessary to reconsider which cranes should continue serving the Temple and which would have to be acquired to meet future needs.
The method using the pre-assembled pieces designed to build these towers required a much larger crane with enough power to lift these heavy new pieces. In addition to the needs of this approach, there was also the possibility of having a machine that could be used for maintenance tasks on the other cranes. With these two premises in mind, the conclusion was reached that the best solution would be to have a new crane that was much larger.
So, in 2012, the site acquired a Potain MD 560 B, a 25t crane in the company’s successful MD tower crane range. The Potain MD 560 B has a 550 tonne-meter rating and is available in 25t or 40t versions.
The MD 560 B has been installed over the crossing of the Basilica at 67m above ground level. The jib can cover almost all of the diameter of the Temple, lift up to 25t (more than twice the previous load) and reach 180m. This crane has the latest technology, including a camera that controls the difficult movements between the towers, millimetre by millimetre.
In late 2019, the jib is expected to move up to its top height of 180m to build the tallest tower, the tower of
The MD 560 B can cover almost all of the diameter of the Temple, lift up to 25t and reach 180m.
Jesus Christ, which should stand at 172.5m in 2022. When fully extended at 177.72 meters, it will be higher than Montjuïc Castle, the highest peak of Barcelona’s skyline.
The MD 560 B was chosen for its attributes in terms of practical utility. The main one is that it is controlled remotely and has sensors that help compensate for the difficulties crane operators experience in accurately visualising the movements of their load. These sensors help operators put the pre-assembled pieces in place and fit them together precisely. Other highly useful features include a black box which monitors every movement of the crane and a toilet in the operating cabin, which is highly practical for the operator.
Potain also made a number of modifications to the MD 560 B which included changes to the cable drum. The original model has less than 1 km of cable and for the Sagrada Familia, a longer cable was needed which meant the cable drum was also made larger. A more powerful motor was also installed because the lifting and placement of the heavy prefabricated pieces required more horse power.
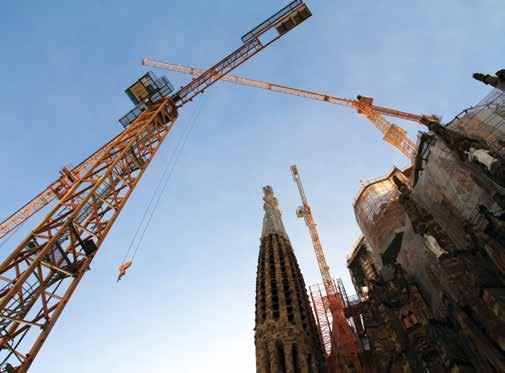
The MD 560 B is strategically located and if it stays in place until the Temple is completed, its current location ensures that there will be no danger of hitting the towers or damaging any other part of the building. Plus, the length of the jib makes it capable of suppling the other cranes being used at the Temple, so no additional, external cranes are necessary for maintenance and the ultimate dismantle of the three cranes. The role of feeding the other tower cranes led to the MD 560 B being named the ‘Mother of All Cranes”.
Using this crane, and introducing the pre-assembly method, has made construction of the Sagrada Família a faster, more effective and simpler process. For example, it only takes six and a half hours of work to assemble an eight-faced level on the towers of the evangelists, much less than with other less innovative methods.
The MD 560 B saves time and has made a method normally used for other large, tall buildings a viable option for Gaudí’s emblematic building.