
4 minute read
Endress + Hauser helped the Archie Rose distillery upscale its manufacturing capabilities.
from FBIN MARCH 2022
by Prime Group
Endress+Hauser helped the Archie Rose distillery upscale its manufacturing capabilities.
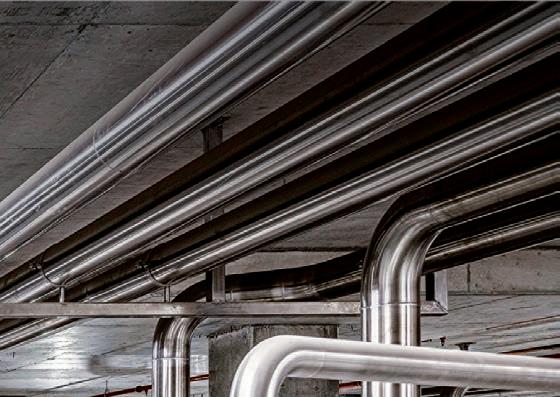
Modernising traditional processes for future success
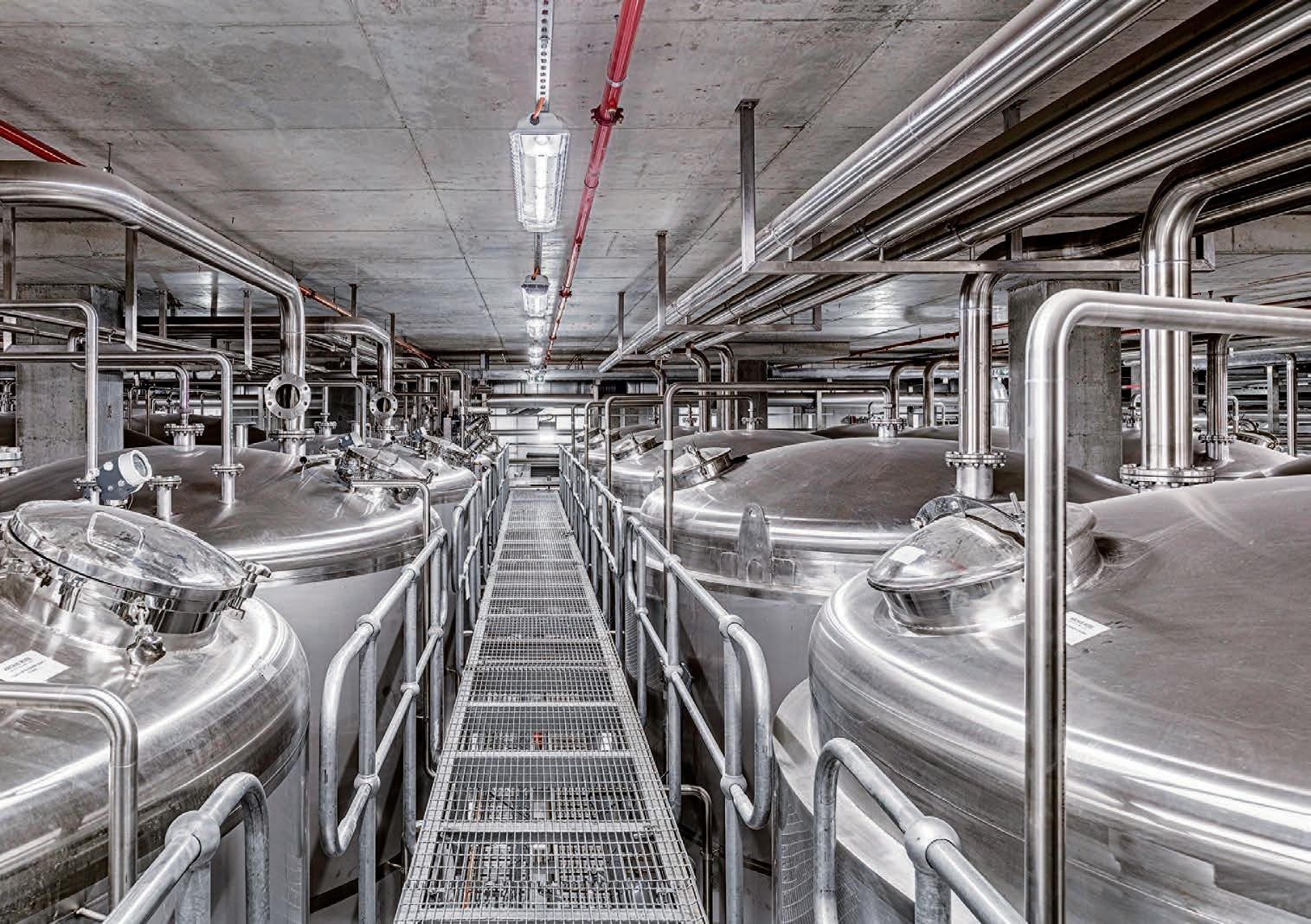
Endress+Hauser helped the Archie Rose distillery upscale manufacturing after the company experienced rapid growth in its first years. Food & Beverage Industry News reports.
After hitting the market in 2014, Australian distillery Archie Rose experienced rapid growth when its products became popular with consumers. As a result, the company had to scale up its manufacturing capability and turned to Endress+Hauser for its instrumentation requirements.
The project to help modernise the craft distillery kicked off in 2019 with a key challenge being centred on retaining the heritage of a centuryold method of whiskey production while also overhauling the method of gin distilling, too.
Modernisation at scale comes with many challenges. Ensuring the distillery is running safely and within specification is critical, but it is also important that resources are being used efficiently to extract the most from each process step.
From a process control perspective, instrumentation plays an important role in guaranteeing optimal conditions for each step.
Gustavo Queiroz, industry manager at Endress+Hauser, said the company helps manufacturers of all sizes to enhance, overhaul and upscale processes.
The core of the process is distillation, where temperature is carefully controlled to ensure operational safety and an effective cut of heads, hearts and tails in the downstream. This step is crucial for a high-quality and consistent product.
Meanwhile, blending and storage areas require instrumentation for accurate transfer of products and consumables as well as inventory control of final products. This makes production planning more effective.
Both process steps were looked at by experts from Endress+Hauser who developed a multipronged solution.
“We worked together with an engineering company and supplied all the instrumentation they needed from a monitoring and control perspective,” said Queiroz.
“They needed to upscale from the handmade production of spirits, to an automated system that created a reliable way to protect the brand and ensure product quality.”
The resources offered by Endress+Hauser also had to meet resource requirements for a successful expansion.
“Our instrumentation is present

from the beginning to the end of the manufacturing process,” said Queiroz.
The solution put forward by Endress+Hauser was designed to meet Archie Rose’s requirements; to improve process control, energy efficiency, product consistency and ensure employee safety. To achieve this, various levels of instrumentation were supplied.
First, the company supplied instrumentation to ensure operational safety for the pumps and tanks using level switches to avoid overfills and prevent pumps running dry. This is an integral part in ensuring the safety of employees.
Second, flow meters were provided to ensure an effective monitoring and control across multiple process steps.
Endress+Hauser also supplied inline quality parameters such as density measurement for a real-time monitoring of distillation streams, allowing to quantify the ethanol content and have a clear picture of the distillation process.
“This supports the distiller to understand which stage of the process the product is in, supporting the decision making process,” said Queiroz.
“Once through the distillation process, the product goes to storage tanks where level measurement and overfill prevention solutions are installed.”
And finally, full compliance of instruments with hygienic and hazardous approval, which certify both the quality of the product to the consumer and the safety of distillery workers, as required by industry standards.
“From the beginning to the end of the process different safety devices have been installed due to the flammable nature of the alcohol,” said Queiroz.
“Endress+Hauser have a broad range of offerings that cover everything from basic instrumentation, for monitoring, right up to advanced solutions for process and control optimisation.”
Queiroz said the trickiest part of scaling up from manual to automated processes was engineering the correct solution for the desired outcome.
Archie Rose had already employed the services of an engineering firm to help complete all the process engineering design. “One of the key challenges when it comes to instrumentation is finding the right piece. Tailoring the right instrument for the application is key for successful performance; this is especially true in food and beverage where the measurement instrument usually needs to be in contact with the product,” said Queiroz.
Automation also allows for future growth and scaling up of processes and the team from Endress+Hauser is available for site visits to make sure everything continues to work as it should.
“We are able to sit down with them and ask them what they specifically need,” said Queiroz.
“Then we can bundle up a solution and deliver not only instrumentation, but we can support other applications like cloud computing solutions, for example.” F
Process control was a key area of the partnership so instruments such as absolute gauges and pressure transmitters were used.

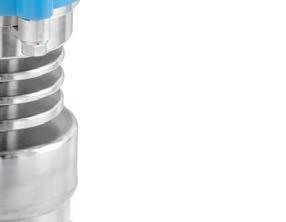

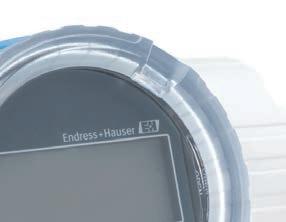



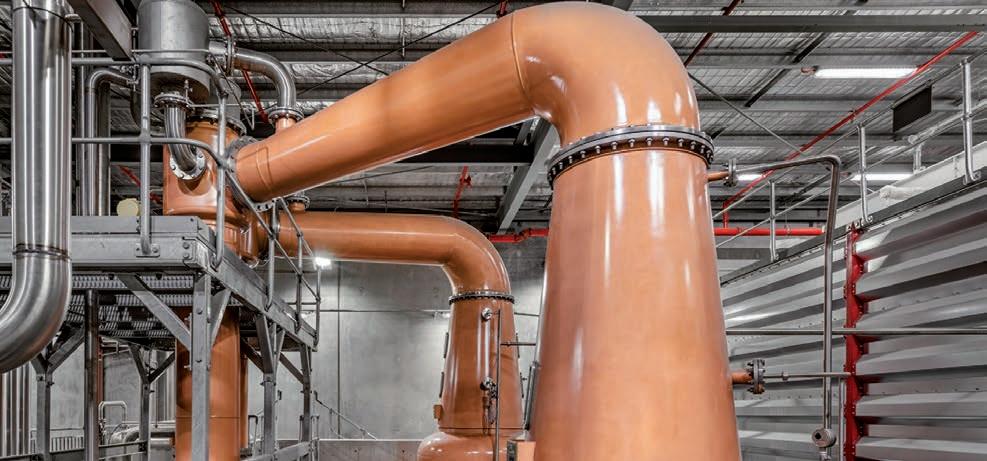
