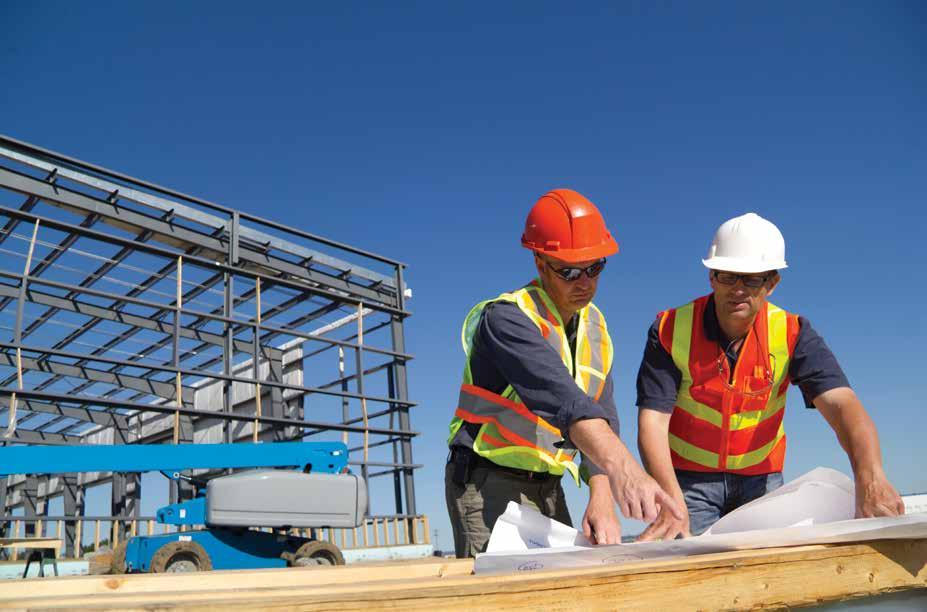
5 minute read
STANDARDS & REGULATIONS
Don’t let regulations bring you down
Capital investment when building or renovating a plant can be expensive. Even more so if you don’t follow council and building regulations. Food & Beverage Industry News explains.
Red tape, bureaucracy, standards and regulations – all can be a bugbear for any company thinking of building or expanding their food and beverage processing plant.
Food and beverage processing factories especially have a range of rules that dictate what they can and can’t do due to food safety issues.
Problems arise when the correct planning hasn’t been taken into account, or even ignorance of what is required when building a premises. However, the latter is never an excuse for putting up a building without consent, although that doesn’t stop it from happening.
It’s not lost on Total Construction’s design operations team, who has have seen their fair share of projects go pear-shaped due to naivety, poor planning, or disregard for building and council regulations. As the name
implies, Total Construction specialises in total builds – from the ground up and that includes getting all the right approvals.
Total cites a recent example with a client that wanted to expand its premises and had done so already without getting the correct building consents. They were told to dismantle the illegal structures. The company came to Total Construction for help.
“The client had put an awning structure out at the back of the property to protect their roller shutter opening when they were loading and unloading food products,” said Rob Blythman business development manager F&B. “And then they built another structure to store equipment that needed to be protected from bad weather. You can typically put up a small tool shed in your back yard, but when it comes to a commercial enterprise, you can’t do that without the correct approvals.
“We understood what the issues that were raised by council and by the owner – what they needed to achieve and what they wanted from a building point of view,” he said. “To do that, they needed to amend the building considerably and make about a 30 per cent increase in the building footprint.”
The client used its own architects, who managed to get the necessary approvals. However, the client soon realised that it still wasn’t big enough for what they actually needed. The Total Construction team helped to get the amended development approval through. If the client had done it correctly the first time, they might have saved themselves the best part of $25,000, according to Blythman.
But it just wasn’t the footprint of the upgraded facility that needed attention. There were other aspects
A company can save a lot of money if they get everything right at the planning stage of a build.
of the build that needed to be taken into consideration. For example, there needed to be enough room for trucks to turn around in while loading and unloading produce. That in itself holds a lesson for those looking at building or revamping a plant.
“The number of carpark spots that the original architect put onsite was over and above what the council minimum requirements were,” said Blythman. “Here’s a bit of advice – if the council says you only need 15 carparks, only provide 15. The reason being? If you provide 20 and you are going to do more works in the future, those 20 carparks can become your baseline. It is part of the development control plans that have been in play with any development project with councils.”
When a company decides to modify and carry out remedial works to buildings, they open themselves up to fire upgrades and compliance with current codes. The essential services for emergency requirements need to be upgraded as well. These are potential costs that clients may not be aware of that get triggered by council. Then there are the accessibility issues that able-bodied people forget about – planning authorities don’t.
“If there is an employee, employer or visitor in a wheelchair, you can’t discriminate against them according to the Disability Discrimination Act (DDA),” said Blythman. “If you walk down the street and you see a vacant shop, and you go, ‘that’s a nice shop. I might rent that shop out and make it a café’, and the front door requires you to step up, then you have considerations to think of. If you took on that lease, straight away the council would very likely invoke that you need to put accessible ramp in that building to allow accessibility for all persons wishing to enter that business.”
Not to be overlooked, but often can be, are the issues of acoustic requirements for the reduction of noise transferring out of the factory to adjoining properties. Some industrial properties cut across residential boundaries.
When such a factory has hours of operation that can potentially go on 24/7, the sensitive nature of the equipment and the noise needs to be able to be retained within the industrial boundary. It is not allowed to creep over and impact on the sleep of the nearby residents.
“If you can imagine the amount of mechanical plant that’s needed
Getting the correct permits can take time but are a necessary part of renovating or building a new processing plant.

to air-condition a large refrigerated space, then there is a lot of noise,” said Blythman. “There has to be acoustic screens specifically engineered by an acoustic engineer to make sure that the noise doesn’t leak out to disturb residents (i.e. sleep).
“Clients have to understand the legislation framework that goes around all projects.”
Blythman imparts a couple of pieces of advice to those that are thinking of upgrading or building a new facility. The very first port of call if they are unsure about anything, is to go and talk to the local authority on what is possible for the site and speak to the local planner for that council.
“You are a rate payer, so you are entitled to go and get help from your local authority,” he said. “Also, if you are unsure, or don’t know where to start, we can provide means to navigate you through all these issues. We can work in collaboration with a client’s architect or the clients can engage us directly and we can manage the process for them.” F
TOTAL FLOOR CARE SOLUTIONS
VALUE BEYOND MACHINE
INNOVATIVE TECHNOLOGY
EXPERT SERVICE
ASK US ABOUT OUR ECO-CRETE™ FOOD & BEVERAGE
FLOORING SOLUTIONS
