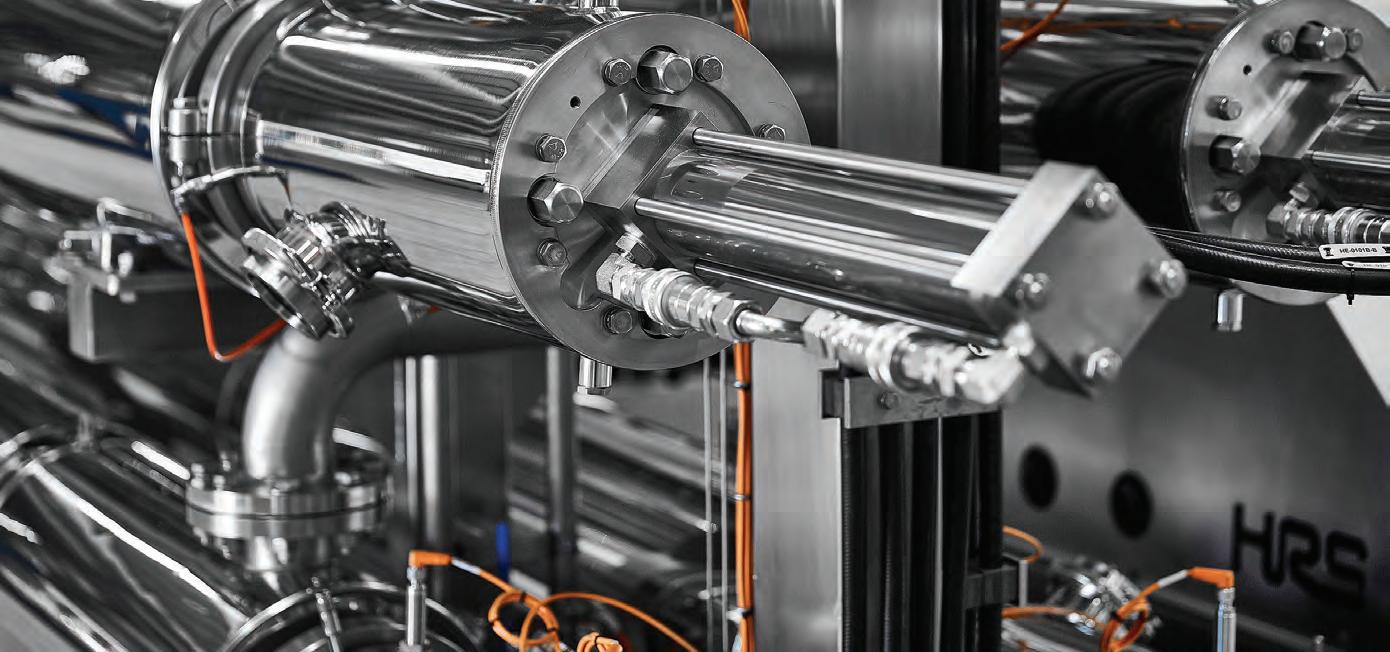
5 minute read
THERMAL TECHNOLOGY
The range of heat exchangers from HRS offer innovations that raise the quality of heat transfer.
HRS’unique scraped surface heat exchangers deliver superior heat transfer
Food & Beverage Industry News looks at some of the key features of the HRS heat exchangers and how they can save on production costs.
The UNICUS and R Series of heat exchangers from HRS, a thermal technology company, promise features not found in alternative designs, according to Chris Little, director, HRS Heat Exchangers ANZ.
Key reasons for using scraped surface heat exchangers (SSHEs) are to prevent product build up on the surface of the tubes inside the machines, which if left reduces thermal transfer, and to improve mixing within the product or material being treated.
As a result, SSHEs are commonly used for viscous food products such as pastes, creams and sauces, and for high fouling waste products such as slurries.
“HRS currently has two model types on offer, the first of which is the UNICUS, which has been around for about 20 years now. And that is a unique solution compared to traditional scraped surfacing technology because it uses reciprocating technology,” said Little.
The design is based on a traditional shell and tube heat exchanger with scraping elements inside each interior tube.
The reciprocating movement of the hydraulically operated scrapers mixes the fluid and cleans the heat exchanger surface. This keeps heat transfer high and reduces downtime because timing in between clean in place (CIP) can be extended.
“The whole point of these products is that they are self-cleaning during production, which is one of the most desirable features for heating applications,” said Little.
“Fouling and scaling are enemies for any heat exchanger and would otherwise reduce the thermal performance, and most importantly for the food and beverage sector, product quality, and this technology counteracts that.
“With an HRS scraped-surface heat exchanger the operational uptime is potentially limitless, and the requirement for CIP is really determined by product quality and not thermal performance.”
The other model of SSHE is the HRS R Series, a more traditional rotating design that includes a patented helical blade scraper bar, an innovative gearbox, and multi-tube options. These combine to reduce footprint, energy consumption and operating costs. A unique sealing system allows the removal of individual tubes. Another critical selling point for the HRS R Series is the low cost per square metre of treatment surface.
“It’s also low shear and very gentle when processing products, which is often relevant for food stuffs,” said Little. “We also developed the R Series in response to existing technologies in the marketplace for scrape surface variants. We asked ourselves how to do things differently.”
The HRS R Series also presents a more compact solution, with the versatility to meet different requirements for different clients.
“A key area for us was looking at the solution from the owner’s perspective, as well as the operator’s and maintainer’s, and making sure the equipment is easy to operate and maintain, ideally with the lowest cost of ownership,” said Little.
Another innovative feature of the HRS R Series is a uniquely designed helix on the scraping bars, allowing it to process highly viscous substrates with lower operating pressures. This has a positive impact on operating costs and energy consumption.
This design provides increased efficiency in the heat transfer, resulting in a smaller carbon
Chris Little said the heat exchangers have the potential for limitless uptime.
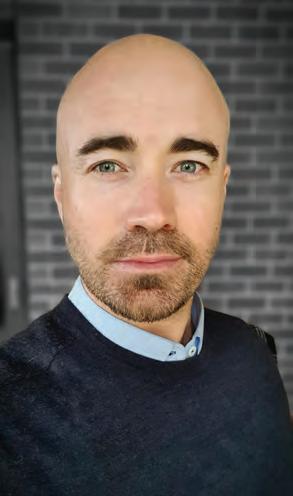
footprint than many alternative offerings. It also offers three important benefits.
First, pressure is reduced along the heat exchanger, and second, the gap increases turbulence at the tube wall, reducing fouling and improving product mixing. Third, the helix can also be used to recover product, either by running it through the system or running the helix in reverse. Depending on the product and configuration of the heat exchanger, up to 90 per cent of product can be recovered.
But perhaps the biggest feature to the R Series design is the ability to extend the life of the machine. The inner tubes in the heat transfer area are removable, which means after long operational life cycles, or being under aggressive conditions, the heat exchanger can be refurbished to brand new at a relatively low cost.
“The features are quite unique to this rotating technology. Usually, if the client needs more heat exchange area, then the cost of scale-up is substantially lower than with alternatives,” said Little.
The HRS R Series is available in both single- and multi-tube versions, with three and six tubes per unit.
“Meaning we can put up to six units in one, keeping the footprint compact, with one set of process
and service connections, one drive assembly, resulting in lower capex, which based on feedback has been well received by our clients,” said Little.
HRS has 40 years’ experience in the thermal technology sector and is often faced with new issues to solve, which is a large driver for innovation.
“Our first objective when we meet a new client is to undertake extensive consultation to gain a greater understanding of the product and process requirements,” said Little.
“We have equipment for clients to trial, which can be deployed to obtain data and use with product samples so they can de-risk a project and supply us with the necessary information to provide them process guarantees.”
Once the initial consultation is completed, HRS puts together a detailed technical commercial proposal for the client within days. If HRS is given the green light, it can have the product manufactured and shipped within eight weeks, depending on the size and complexity of the project.
Trial units are available for testing and evaluation around the world, and the product development team at HRS continues to develop and adapt the R Series for new applications and processes.
“The process trials we carry out, and which we have done on countless occasions, really do extend a long way to the success of any project and gives the client the confidence to proceed,” said Little. F
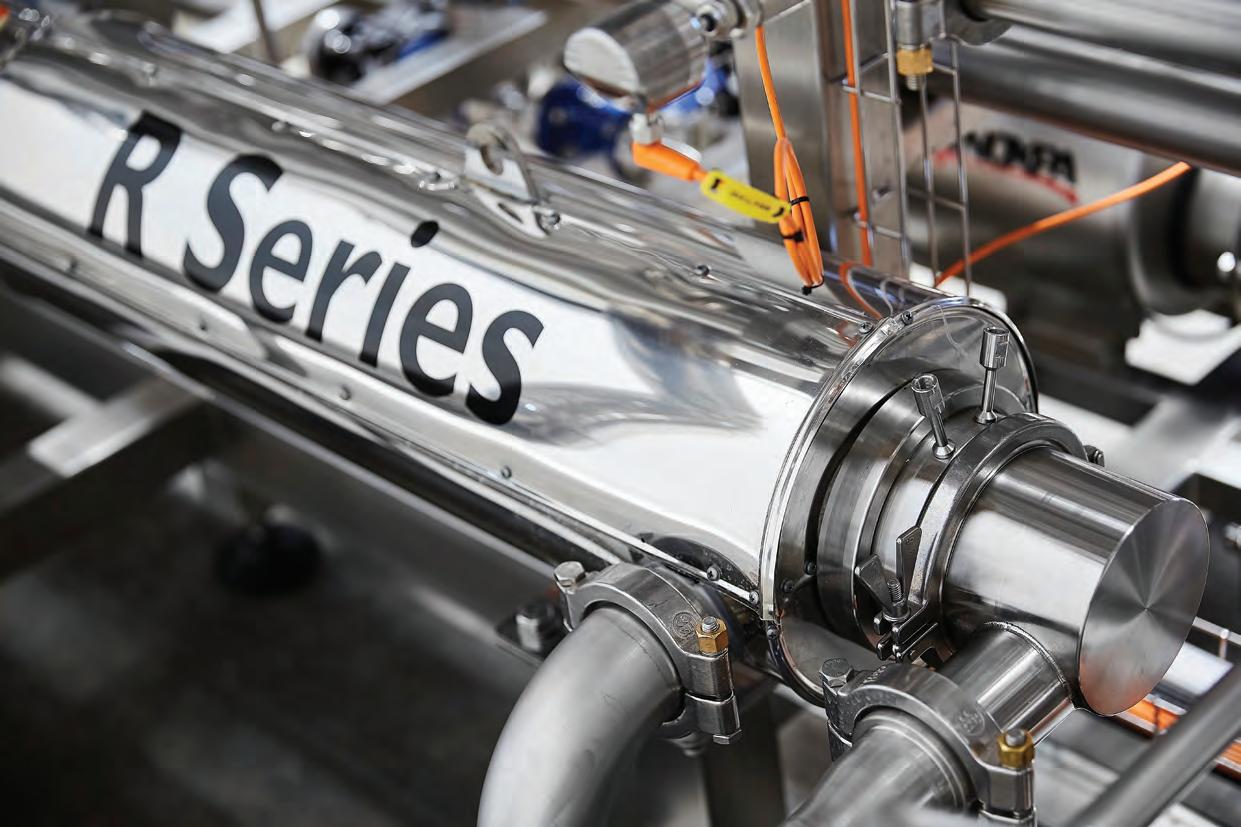