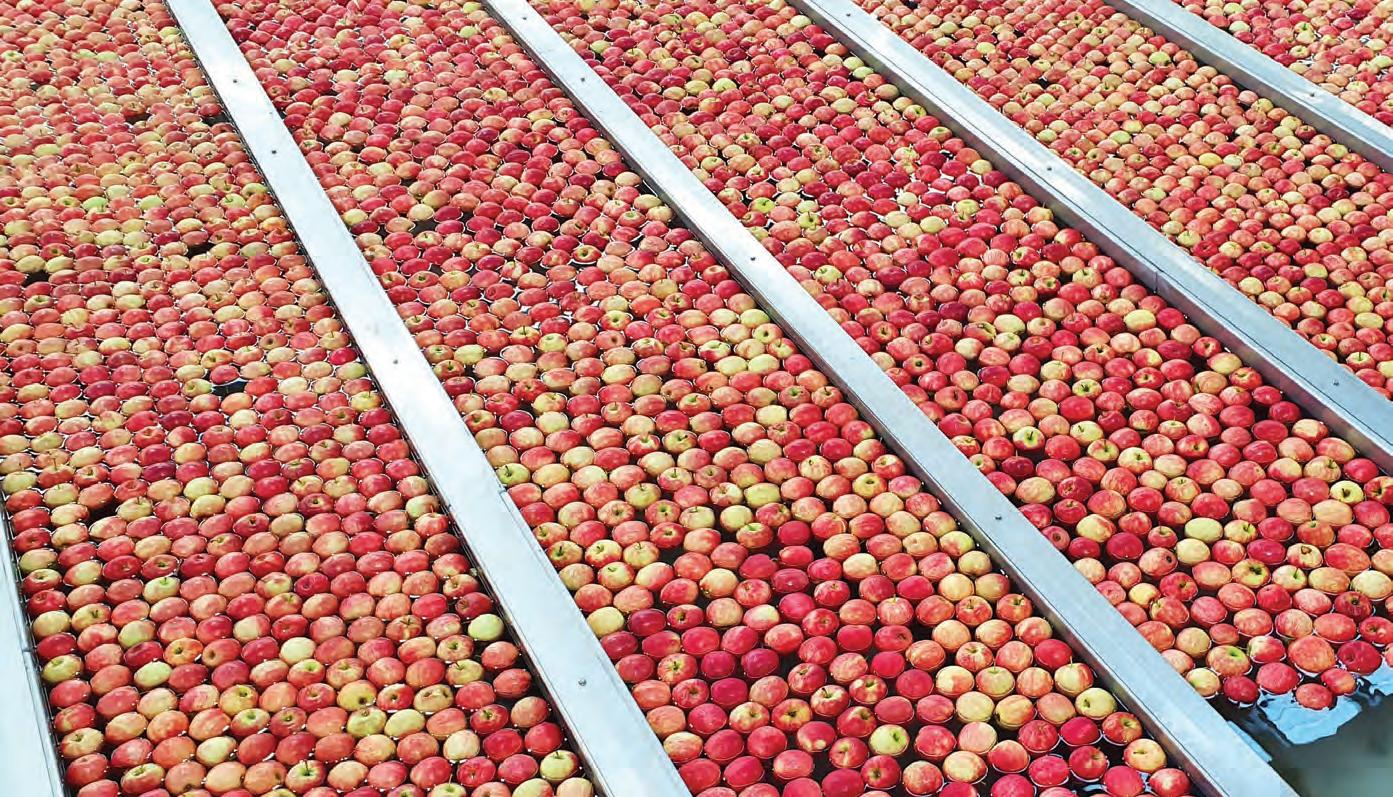
5 minute read
AUTOMATION
ThreeSixty designing today’s solutions to optimise tomorrow’s performance
A partnership between the ThreeSixty Supply Chain Group and fresh food producer Montague helped create efficient systems for Montague’s new Victorian facility, while demonstrating the expertise provided by ThreeSixty. Adam McCleery writes.
ThreeSixty used expert consultation to develop new system designs for Montague’s apple processing business.
Australian fresh food producer and logistics company, Montague, initially engaged ThreeSixty Supply Chain Group (ThreeSixty) to review manufacturing, distribution and warehouse automation to be installed in the former’s greenfield 18,000 square metre, $54 million automated packaging and export manufacturing processing centre in Victoria. .
Montague subsequently extended ThreeSixty’s engagement to include the development, systems design, and the integration of six different software systems to ensure the new highly automated manufacturing Distribution Centre (DC) worked holistically.
Montague engaged ThreeSixty to embark on a discovery and transformation journey in early 2019.
This included the complete review of the Automated Storage and Retrieval Systems (AS/RS), and the operational review of the existing apple grading and sorting system. Analysing the data, volumes, throughputs and forecasts was necessary in order calculate system storage requirements. This allowed ThreeSixty to complete an AS/RS best-fit solution assessment, engage with potential suppliers and provide Montague with an industryleading solution.
ThreeSixty’s approach was one of its market differentiators. It was crucial to gain an in-depth understanding of the customers business requirements. Strategising and evaluating every aspect of the supply chain, allowed ThreeSixty to develop a tailored solution to meet the customers current and future needs. The customer journey didn’t end there; the team at ThreeSixty worked with customers on an ongoing basis to continuously review and optimise the solutions.
Rowan Little, Montague’s chief innovation officer, said ThreeSixty’s partnership approach working through its complex requirements, gave it a deep understanding of what its business
Rowan Little (left) and Derek Tan (right) worked together to develop the new Montague systems.
was seeking in a highly automated production centre solution. In addition, ThreeSixty’s coordination of crucial technical design workshops ensured all the different software vendors were aligned.
ThreeSixty’s director of project services, Derek Tan, told Food & Beverage Industry News the solution design process was challenging. “This was especially so when you had to adapt to the COVID-19 world. When you try to design a complex solution that incorporates six systems and vendors to make it work, it can be a big undertaking,” said Tan.
Montague originally planned to send key staff overseas for firsthand experience with systems and best practices commonly used in Europe and North America, which the company aimed to adopt in Australia, but the COVID-19 pandemic created a roadblock.
Montague’s goal in adopting a business model that was a first in the Australian produce industry was imperative in order to remain competitive and increase productivity. The expertise provided by ThreeSixty helped achieve that goal, said Little.
ThreeSixty worked to enhance Montague’s performance through sizing, solution design and build, system integration testing, user acceptance testing through to commissioning and most recently, optimisation of the automated facility. Though the equipment and automation was new to Australia, ThreeSixty’s expertise in delivering similar projects for the food and beverage, manufacturing and retail industries ensured the successful outcome
“We developed a tailored solution that focused on service, simplicity and cost benefits. This was presented back to Montague, which included expected
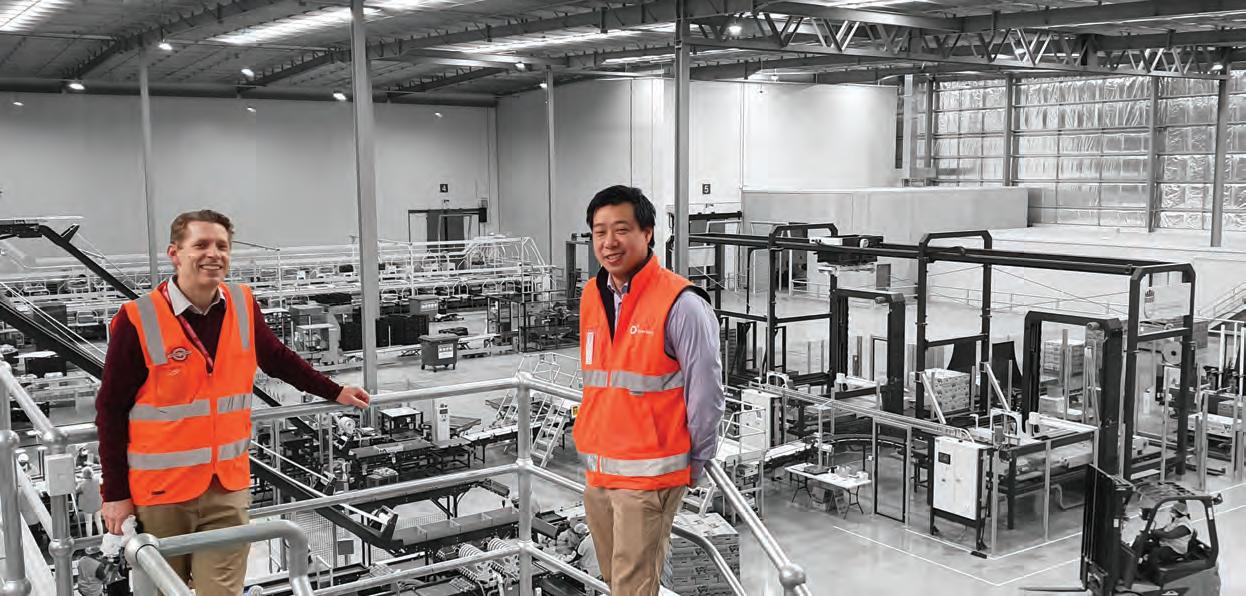
"One of the unique things when you go to a new building and new processes, is you don’t have people within your team who are protective of the way things were done. The fact that there were no systems and no history meant people were much more open to ThreeSixty being able to help develop new disciplines and business rules."
outcomes and benefits,” said Tan.
Some of the software recommendations made by ThreeSixty included enterprise resource planning software (ERP), warehouse management software (WMS), warehouse control system (WCS), fruit tracking and the production control system software. Other areas the solution design focused on were operation and mechanical perspectives, as well as a functional interface and documentation of hardware specs, to help support the build phase. The detailed solution design presented by ThreeSixty was a critical element in Montague confidently adopting new systems and business processes.
When fully operational, the new systems will increase Montague’s apple packing capacity by 75 per cent, to approximately 38,000 tonnes per year, with the ability to process 20 tonnes per hour.
Montague’s AS/RS integrated production centre is also the first of
its kind in Australia and demonstrates ThreeSixty’s ability to solve complex issues for clients by thinking outside the industry box.
The new design also caters for an additional 30,000 bins, bringing capacity to three million 12kg cartons, which equates to 227 million apples each year.
To address the increase in output, the Montague facility was designed with new features, including an Aporo Produce Packer and a 21-metre-tall automated AS/RS cool room.
“The only way to be efficient and competitive globally was to find a way to process twice as much fruit within our new facility without increasing total man hours,” said Little.
“One of the unique things when you go to a new building and new processes, is you don’t have people within your team who are protective of the way things were done,” said Little.
“The fact that there were no systems and no history meant people were much more open to ThreeSixty being able to help develop new disciplines and business rules.”
Tan agreed the process was made much easier by the willingness of Montague and its workforce to adopt the new business model.
Currently, the ongoing partnership between ThreeSixty and Montague is focused on the optimisation phase of the solution design, which will be more comprehensive once the limitations of COVID-19 lockdowns pass. This will involve collecting business case numbers to identify the operational opportunities, system enhancements and change management the group needed to adopt to maximise throughput and gain the operational benefits in the new facility.
Although Covid-19 has created significant manufacturing and supply chain disruptions for many industries globally, it has also presented a unique opportunity for businesses to re-evaluate their operations. The team at ThreeSixty is passionate about working with their customers to turn their supply chain into their competitive advantage. F