
11 minute read
Hustler’s new Combi RX218 feed wagon is big bold, and very capable at what it does
With the ability to feed pretty much anything you want, Hustler’s Combi RX218 feed wagon is big and bold, and very capable at what it does
Words Jaiden Drought Images Oliver Brunton
Ultimate all-rounder
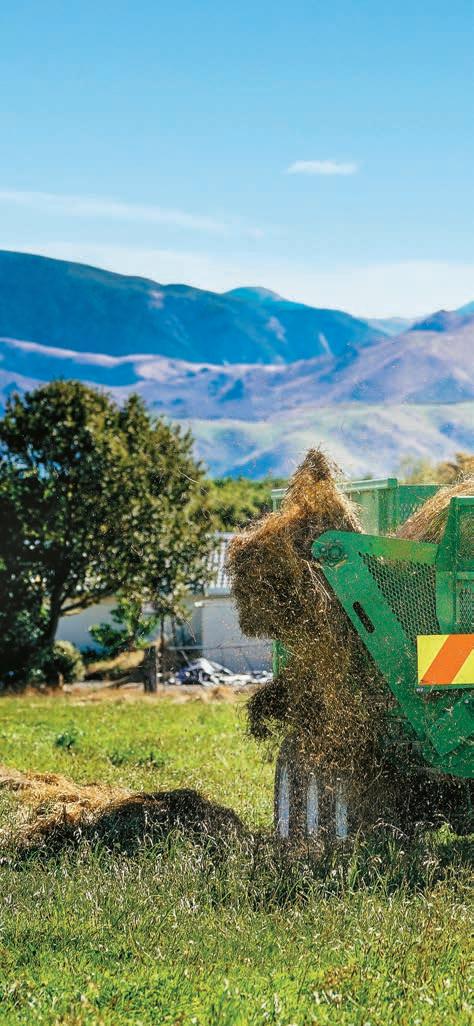
For 60 years now, Hustler has been redesigning its machinery line-up into sleek-looking, ‘outside the box’ designs, incorporating the ideas and on the ground opinions of the very people who purchase and use the machinery. This, along with the recent ‘MiNT Edition’ colour scheme change, has farmers highly invested in the launch of the new Hustler RX wagon range, moreso the big daddy: the RX218.
I’ve spent some considerable time with this wagon, which is the result of six years of thoughtful research, development and refinement. In true Hustler style, the company opted to do something more creative than the norm to release this machine – investing in a roadshow around New Zealand, taking the RX218 to farms from the bottom of the South Island to the top of the North Island.
So, what makes the RX218 so special? The beauty of the RX is that it will feed almost anything or a combination thereof.
That’s what makes it so popular; particularly for South Island farmers who feed bales, grass/ whole crop silage, maize, root crops, or any other concentrated feeds in large quantities to mobs all over the district.
Customers want a hardworking, simple and bulk capacity machine. Hustler is upfront in saying that if you want to blend several feeds plus trace minerals and chop bales, then buy a mixer. If you want to feed a large variety of feeds in the paddock at all times of the year, and sometimes on the feed pad, with a simple reliable feeder that’s easy to use and isn’t going to need a digger if you get stuck, then the RX is a more sensible option.
CONCEPT
The Combi RX218 delivers two wagon concepts in one. The front right-hand chain elevator and side chain feed keeps forage moving to the elevator. Once this feed is exhausted, the rear pusher brings forward another chunk to be side shifted to the elevator. The machine delivers a huge 26 cubic metre heaped load capacity.
A standout of the system is that the bulk of the weight isn’t moved all at once (saving chains) and the rear compartment (where the bulk of the feed is) is moved by two internally-ported rams. This means fewer hoses, no grease and no moving parts.
Hydraulics beat chains all day in my opinion. The flat floor runs seamlessly between the rear bed and the cross conveyor. The bin allows two four-foot silage bales to easily be stacked across the width of the machine. This delivers the ability to keep a short overall length and low loading height, which Hustler is traditionally popular for.
The only small problem with the rear pusher is the slot in the floor where the door slides. This means you can’t put concentrates like PK straight on the bottom to be mixed and maize silage will lose a small amount (which can be easily picked up in less than a shovel full), whereas silage presents no problems. If you do want to add feeds like PK, simply add maize or some other silage onto the bottom first, then the PK in the middle. As it goes through the chain elevator, the feed mixes very well. RX218. The large elevator tilts over enough to allow significant clearance off he wall of the bin, while still enabling you to feed in the middle of the trough. Feeding bales on the pad keeps you on your toes as with all wagons. Fortunately, this is covered by a smart controller (more on that later).
The elevator has a single ram for tilting. This prevents twisting of the elevator from a twin ram design (if one ram was damaged, had a leaking seal or wasn’t phased properly, and the two rams were out of sync, twisting could occur). On the RX, however, the pivot ram is tucked neatly away, as are the gearboxes, hydraulic motors, and hoses – all conveniently out of harm’s way.
CONSTRUCTION
The elevator and side feed chains use 12,000lb (5,443kg) roller chains with Bis-Alloy sprockets (this is Harden metal, more often used on digger and loader bucket cutting edges). The shafts use self-aligning bearings and are well covered away from acidic feed.
The feed bars use two bolts on either side to connect right through the chain, so if bent or broken, do not require a chain link. Four bolts and the bar can simply be removed, and you can carry on feeding. This doesn’t impact the structural integrity of the chain and, more importantly, enables a quick fix. The chains all have adjustable tensioners, so as they wear, you can simply take up the slack again to prolong their life.
The floor of the wagon is a real piece of ingenuity. Made from a durable plastic called Puck board, this hard-wearing plastic composite is made from the
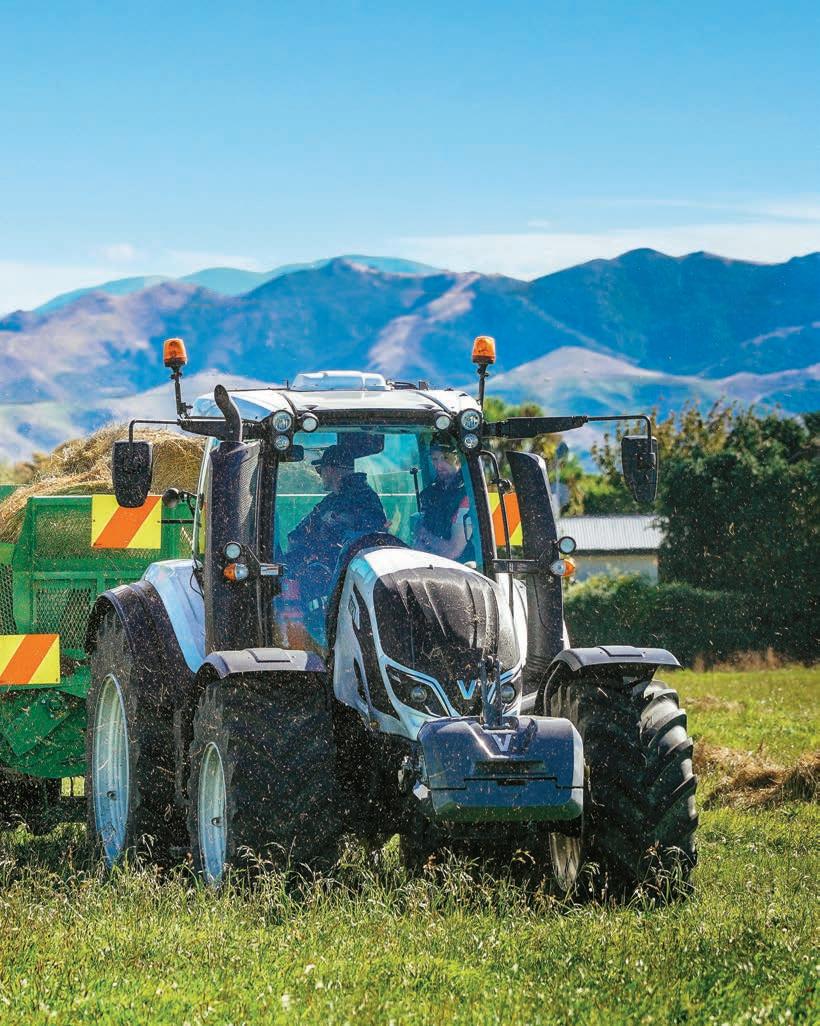
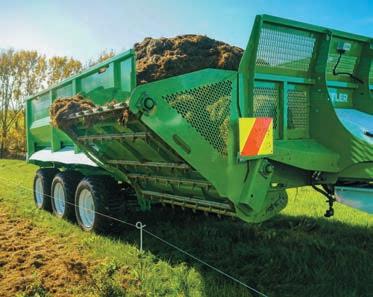
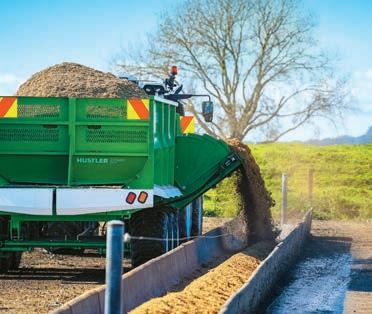
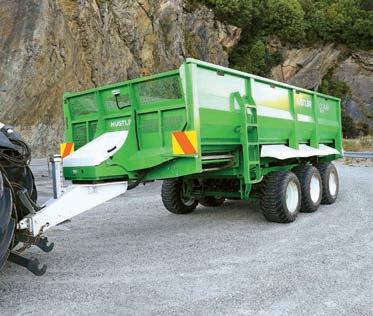
same material they used to make ice hockey rinks (hence they can withstand the impact of hockey pucks even while frozen).
It’s notoriously tough and easily handles large loads being dumped on it. Another benefit is that it doesn’t wear, like plate off teel, allowing the machine to look smarter for longer. The rear floor is 15mm thick and the cross-conveyor floor is 12mm.
It’s all much thicker, more flexible, and less prone to banging, vibration, and fatigue in comparison to steel.
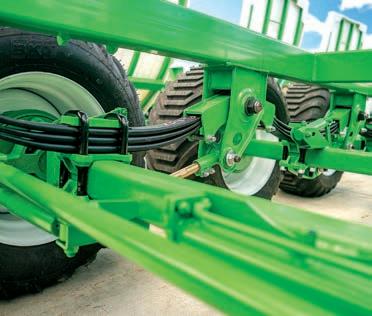
LOADING AND HAULING
As mentioned, the low loading height is a real sales point of the RX. Another handy feature when loading are the snazzy MiNT edition white mudguards. These are now sloped so that mud and acidic forage don’t sit on the mudguards causing them to prematurely rust out.
The ground clearance has been increased (particularly the side elevator), proving great for over humps and hollows in paddocks, as well as making it a lot easier getting into gateways and over races with a large crown on them.
A significant proportion of the large RXs are used on multiple blocks where carting silage (and a lot of it) on the road is one of the main prerequisites in the job description. To cater for this, the tridem axles on the RX218 are all sprung, braked, and with a rear steering axle.
The RX218 is shod on 500/45 R22.5 wide, low profile tyres, which are great for reduced ground compaction in the wet, as well as added safety on hills and smooth riding on the road.
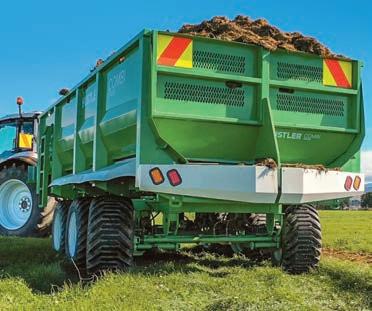
A The FeedLink (scales) allows accurate weighing regardless of whether the machine is on a tractor or the jack stand
B The tilting elevator allows for easy feeding, even over a temporary fence C Feeding into troughs is straightforward and accurate
D Tridem springs are on the RX218 model, with a walking beam tandem on the RX148 and 178 models
E
The tridem axle travelled exceptionally well on and off the roa
SCALES AND FEEDLINK
All RX models come ‘scale ready’. The load cells themselves on these machines are 120,000kg rated, nearly two-and-a-half times stronger than on its predecessor. This combined with the integrated positioning of the scales means you can get away with fewer load cells but still achieve accurate weighing.
The RX218 comes standard with four scales on the main bin (as it runs a twin chassis for the sprung axles), and two up the front on top of the drawbar – delivering accurate weight whether the machine is on a tractor or the jack stand.
B
C
D
E
Pluses
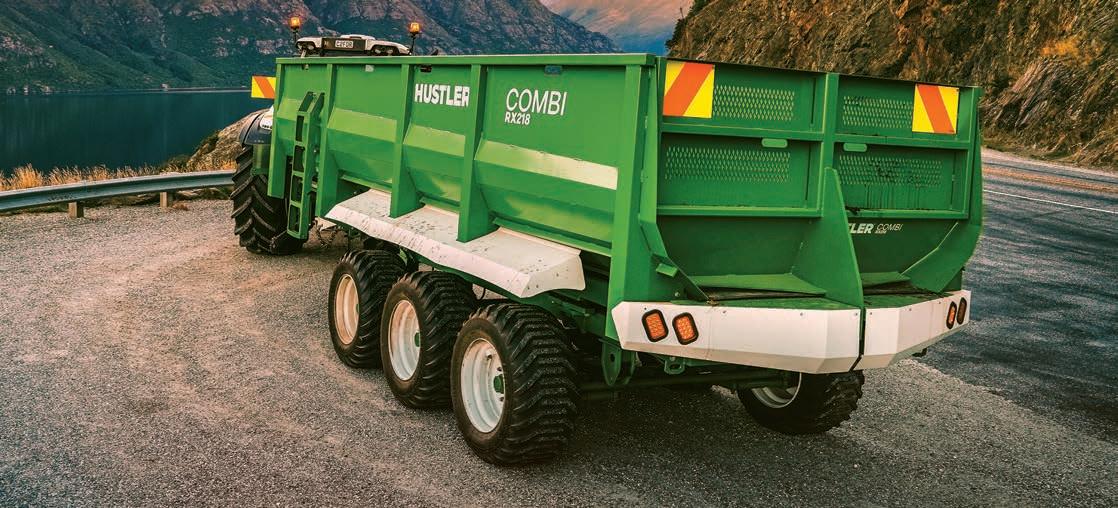
The rear pusher is a game changer for root crops such as fodder beet. The soil and stones simply get pushed, so no more chains and sprockets getting a hiding Rear steering makes it very manoeuvrable for a large machine
Spung axles mean it follows contours and travels well on the road
Large load capacity Smart looking, well-built machine Feedlink is practical but also gives great flexibility Two-mode joystick with a pause button is awesome Front mesh and low loading height allow from the tractor cab excellent visibility of exactly what’s going on inside the wagon Level floor means feed transitions onto the cross floor well

Puck board floor is durable and easy to replace if need be Minuses
I’m impatient and I think the rear pusher should move faster. Having said that because you can move the pusher back (but can’t take the feed with it), you don’t want to get too greedy In certain situations on feedpads where the elevator can’t be tilted right down, a little bit of feed dropped off the elevator bars. On other pads, it performed flawlessly
Hustler Combi RX218
Round bales 10 per layer Medium square bales 10–14 Large square bales (8ft long) 10–14 Loose silage (load level) 21.4 cubic metres
Loose silage (heaped load) 26 cubic metres Maximum load 17,000kg Overall width 3,035mm Overall length 9,180mm Overall height 2,650mm Standard tyres 500/45R22.5 flotation grip tread
Axle Tridem steering suspension axle
Brakes Six-wheel braking Weigh scales Feedlink weighing and feed management system Floors (bed floor/cross floor) 15mm HD Puck board/12mm HD Puck board
Chains (bed/cross floor/ elevator)
Feed bars (bed/ cross floor/ elevator) Twin 12,000lb roller chains
Twin hydraulic rams/ 65 x 35 RHS/40 x 40 RHS
Joystick In-cab electric control w/ Bale and Silage modes Hydraulics required Three pair double-acting plus brake coupling Elevator 1,645mm-wide chain/slat Jack 80mm two-speed screw, with quick adjustment, designed to be used as quick hitch stand Rear steering makes for a highly manoeuvrable machine
Neatly stowed above the drawbar is the ‘brains of the operation’ – connecting to the tech-savvy Feedlink. This app-based system is compatible with Apple iPhones and iPads. Feedlink gives a live reading of how much is in the wagon, and it also allows for herd feed management.
As an example: say you had 10 tonnes in the wagon, and you want to feed this out to three different mobs. Mob one in paddock 6 gets four tonnes. Mob two in paddock 17 gets 3.5 tonnes, and Mob three gets 2.5 tonnes in paddock 54. This system is great, as it allows the driver to know exactly what to feed.
An audible alarm will sound and the weight flashes red once the target is hit. Once in Wi-Fi or hotspot range, this can be sent for traceability back to management. It also runs a cumulative total, which allows you to see how much forage has been to each mob over a period (a month, or a season, etc).
IN-CAB OPERATION
The feed controller (separate from Feedlink) has also been upgraded with a new in-cab monitor. This has a switch at the bottom for either Bale mode or Silage mode. Bale mode allows you to control everything independently. The elevator needs to be engaged through one of the spools on the tractor, and this needs to be constantly pumping. You can then move the rear pusher door backwards or forward, and move the cross floor left or ight.
My favourite feature of the whole wagon is a button on the end of the joystick, which pauses everything. This is outstanding for feeding bales. As bales tend to behave badly when being fed out (on any machine), the ability to let the core roll back into the wagon is epic.
Alternatively, if you can see a large lump going over the elevator, you can pause it, let some drop; then let the pause button out for a second so a little bit more drops and so on. This is also handy when feeding on a feed pad for the same reason.
Silage mode is more automated. The rear pusher is still operated manually (and the pause button can still be used), but the cross feed and the elevator work in unison based on clever load sensing valves.
SUMMARY
In general, I think the majority of people were staggered when Hustler announced that it was going to drive a Valtra T174 and theRX218 wagon all the way from Invercargill to Whangarei. To put it bluntly, they thought we were crazy.
As the man behind the wheel, the driving wasn’t that bad; the stops meant you saw a different part of the country every day. The scenery was amazing, thanks to sitting higher and going slower than a car, and it allowed plenty of opportunities to take in the views. The people we met along the way were topnotch Kiwis, and overall, the farmers were impressed.
The RX performed flawlessly and so I guess that deems the whole venture a success. I was certainly impressed at the variety of feed we used and how well the machine handled it. It truly is the ultimate all-rounder.
10 silage bales are a doddle. 15 per load is easily achievable