
8 minute read
FACTORY TOUR
TO ACTION A CALL
AS THE WORLD’S TOP TRAILER BUILDER IN TERMS OF COMBINED VEHICLE OUTPUT, CIMC VEHICLES IS TURNING TO INTELLIGENT MANUFACTURING TO TRANSITION AWAY FROM THE ‘MADE IN CHINA’ STIGMA ASSOCIATED WITH ITS MASS PRODUCTION ACHIEVEMENTS. O utdated production lines and obsolete organisational structures are impacting CIMC Vehicles’ current operations, yet without these challenges, the Chinese industrial powerhouse would find no momentum for transformation, according to CEO and President, David Li.
He explains that even though CIMC Vehicles implemented automated production processes as early as 2014, at the time it identified the need to upgrade its manufacturing infrastructure as well as reshape the organisation from the ground up. This would take for the form of restructured management and a directive to standardise the CIMC product range to be in-line with market trends and demands.
Recognising the benefits of utilising its global network, CIMC now begins the production process of each of its trailers in the digitalised factory called the ‘Light Tower’ factories, which is one of four new purpose-built built semiautomated production facilities in China. Key components are then sourced from all around the world. The business has moved from the traditional labourintensive manufacturing model to a technology-intensive manufacturing model; abiding by the principles of cross-ocean manufacturing, local engineering and global supply chain.
Li confirms that CIMC’s ‘intelligent upgrade’ of its production lines introduces advanced equipment for processes such as automated cutting, loading and unloading of materials and welding. This manufacturing hardware has the capability to receive and carry out requests, comprising Product Lifecycle Management Systems (PLM), Manufacturing Execution Systems (WEMS), Warehouse Management Systems (WEMS), and Enterprise Resource Planning Systems (ERP).
The sequence for developing these sub-systems is important, Li says, because the ERP will not work if the production lines are not connected and the data is not available.
After two years of planning and construction, mass production eventually started at the first lighthouse plant in Dongguan City of Guangdong Province in the middle of 2016. Currently, three plants under CIMC Vehicles are about to be upgraded as lighthouse plants with the automated IoT equipment in the final phase of debugging and optimisation.
CIMC Vehicles claims to be ahead of its peers regarding the development of smart technologies, too. For instance, the OEM equips its semi-trailers with multiple sensors at critical locations to transmit the collected data to a terminal so that the client can monitor the entire process. When a semi-trailer is transporting temperature-sensitive cargo such as food, it is necessary to CIMC Vehicles President and CEO, David Li.
Dongguan Light Tower factory.
install sensors that are capable of measuring the temperature and sending data in fiveminute intervals to ensure effective control and whole-process monitoring.
To maintain its world-leading position in the trailer building market, Li says a smart business ecosystem must exist, which for CIMC Vehicles comes in the form of digital solutions – namely, Big Data.
“This is the most important commercial value of installing the sensors,” he says. “CIMC Vehicles has just made the first step for this and there is still a long way to go. However, it is always our goal to create value for the customers and offer them premium services.”
With the upgrade to lighthouse plants on track, CIMC Vehicles is set to transform its organisational structure and management under the force of various digital application technologies and automated manufacturing technologies since the original organisation model is no longer suitable for the current situation.
Li says CIMC Vehicles has established a dedicated technical team for digital manufacturing, including a digital model design centre, an automated production technology centre and a digital management centre as well as an office in the company’s headquarters.
The one-office-with-three-centres structure is the norm in the organisation of the lighthouse plant and an integral part

of the digital plant that CIMC Vehicles will build in the future. Li explains that proper classification and segmentation during digital transformation is absolutely critical.
CIMC Vehicles has also instigated a dedicated ‘coach regiment’ to execute the lighthouse plant program. According to Li, there are about three to five members in the coach regiment with the commander designated by the headquarters. The commander, as the person in charge, must be an interdisciplinary person with excellent leadership. Then, the commander will choose members of the ‘regimental cabinet’ and battalions will be created under the regiment with outstanding persons in the areas of digital model design, automated production lines and digital management recruited.
“Similar to the one-office-with-three-centres structure of the lighthouse plant, this is a ‘one regiment with three battalions’ structure,” Li says. “Take the lighthouse plant in Yangzhou City as an example. The coach regiment of this plant consists of one commander and one assistant commander, both having doctorates, and another three technical personnel in certain areas from the headquarters. They have been sent to Yangzhou to establish the digital design team, the automated manufacturing team, and the digital management team for the plant.”
In October 2016, this coach regiment had built the production line and developed the system and the applications for designing digital models step by step. By mid 2017, the primary plan for the lighthouse plant was made by the team under this coach regiment. In 2018, trial production started in this plant.
“The name ‘coach regiment’ sounds quite military since developing a lighthouse plant is just like fighting a dubious battle,” said Li.
With a severe shortage of persons on digital technologies, it is imperative for the company to turn its employees into someone it actually needs and seek for technical persons aligned with the corporate development. To this end, CIMC Vehicles adopted an approach with “internal training” and “external recruitment” running side by side.
“We will first choose among our employees and encourage them to compete for related positions,” Li says. “If there is still any position left after internal selection, the external recruitment will be executed. Whether it is for technical personnel or the management, anyone who has the qualification and a strong
Advanced production line.

desire for the position can be a candidate. However, if an employee is not suitable for any position in the new organization, he/she will be assigned to a position for services such as the after-sales service, customer services, and repair. We will make such reposition more frequently. In fact, we have employees who have been working as service personnel for several decades. Therefore, they are perfectly suitable and enjoy certain advantages for such positions.”
Li believes that the greatest difficulty in transforming employees into management personnel lies not their skills but their perspectives.
“For a digital plant, the employees have to shift from the recurrence thinking to recursive thinking and from direct thinking to reverse thinking,” he says. “For this, CIMC Vehicles has adopted a course training method to accelerate the transformation of our people’s way of thinking.”
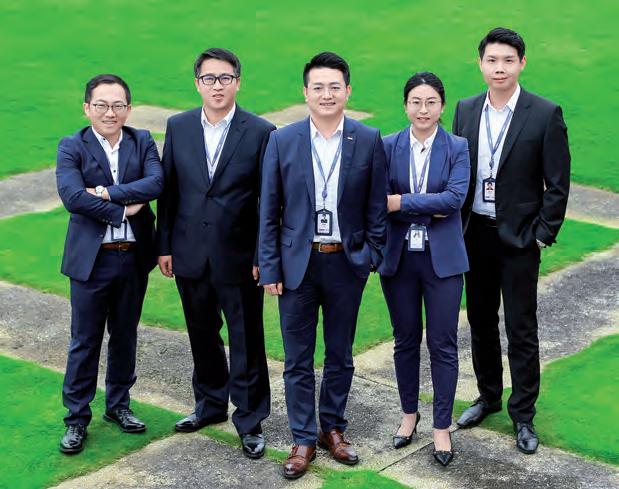
R&D Team Leaders of CIMC Vehicles.
Once a new project is rolled out, the company will choose specialists to build the coach regiment. Team members under the regiment will try to reach different goals surrounding certain tasks. For example, the team for automated production must complete the detailed renovation and upgrade of the engineering regarding the production line, including the graphic design, core equipment and so on.
Before such renovation and upgrade, however, the boundary of the production line has to be defined by the team on digital models – specifically, which products can be made. Once that is resolved, a digital system will be developed for the production line.
“An automated production line is not as flexible as the manpower,” Li says. “The larger the product mix is, the more complicated the equipment must be and the investment cost will be greater accordingly.”
More recently, CIMC Vehicles has signed cooperation agreements with Antai College of Economics and Management (ACEM), Shanghai Jiao Tong University, and MIT (USA) to recruit suitable persons externally. The OEM has also officially become a partner in the MBA program of the “China Leaders for Global Operations (CLGO)” initiative.
This program is initiated jointly by Antai College of Economics and Management (ACEM), Shanghai Jiao Tong University, and MIT (USA) with the aim of nurturing interdisciplinary persons in an era of intelligent manufacturing. As a partner in this program, CIMC Vehicles, as the assessor, can interview MBA students who have great potential, address its shortage of related personnel by attracting the students to the company for internships, and recruit outstanding students.
“I hope that all plants of CIMC Vehicles would be transformed to lighthouse plants and the number of dedicated teams on digital manufacturing would increase from four currently to 14 by 2025,” Li says. “Technical personnel in certain areas will increase to 400 to 500 as scheduled to lend support to our 25 manufacturers across the globe.” www.cimc.com
VANTRAAX ® / ULTRAA-K ® Trailer Air Slider Suspension Systems North America

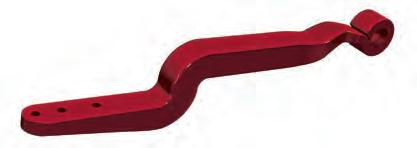
MONOLEAF AIRLINK Europe
INTRAAX ® Integrated Trailer Air Suspension System North America / Asia Pacific



TRLAXLE ® / HTA ® / HCA ® Non-Integrated Trailer Axles North America / South America / China / India / Asia Pacific

HSDS ® Severe-Duty Trailer Air Suspension System North America / South America / China / India / Asia Pacific
Hendrickson Trailer North America / South America 2070 Industrial Place SE Canton, OH 44707-2641 USA +1.866.743.3247 +1.330.489.0045 Fax +1.800.696.4416
Hendrickson Trailer China No.1668 North Section of Chunbo Road, East New Dist of Jinan High Tech Industrial Development Zone, Jinan, 250104 Shandong, China +86 21 5876 5710 Fax +86 21 5876 1577
Hendrickson Trailer Asia Pacific 32-44 Lecton Drive Dandenong South, Victoria, 3175 Australia +61 3 8792 3600 Fax +61 3 8792 3699
Hendrickson is a leading global manufacturer and supplier of mediumand heavy-duty mechanical, elastomeric and air suspensions; integrated and non-integrated axle and brake systems; tire pressure control systems; auxiliary lift axles systems; parabolic and multi-leaf springs; stabilizers; bumpers; and components to the global commercial transportation industry.
Hendrickson Trailer India Plot No. 4 & 5, Gat. No. 679/2 Behind Hotel Gandharva Alandi Kuruli Road, Kuruli (Chakan) Taluka Khed, Pune 410501, India +91 2135 662600
Hendrickson Trailer Europe Gussstahlwerkstraße 21 A-8750 Judenburg, Austria +43 3572 44011 400