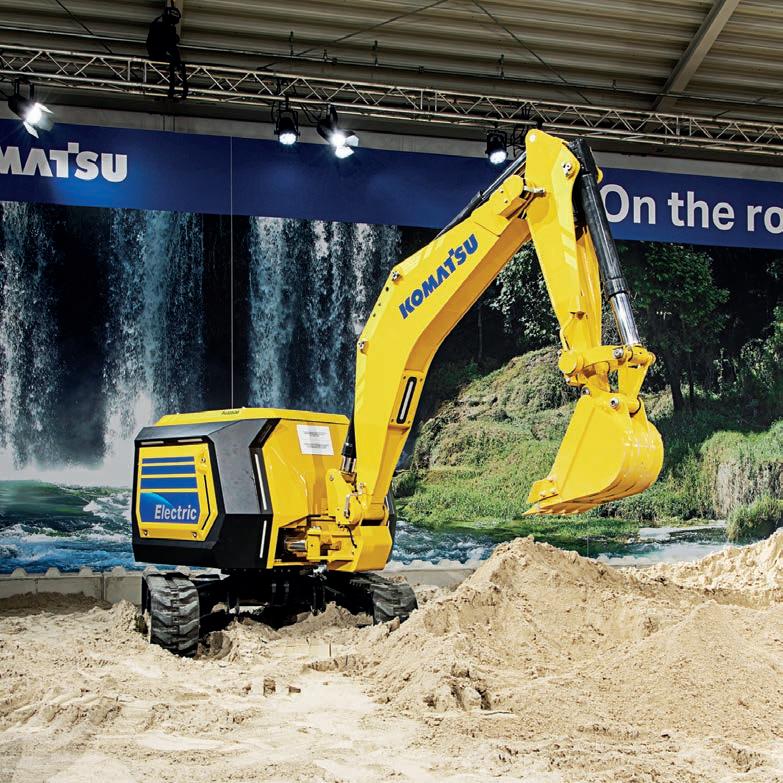
3 minute read
FOCUS Electrification
marking the beginning of extensive growth in the company’s electrification venture.
Komatsu more recently launched the PC01E-1 in Japan last year – its first electric micro excavator powered by portable and swappable mobile batteries. At bauma 2022 trade fair held late last year, Komatsu proudly displayed the machine along with a concept model of its new 3-ton Full Electric Remote Controlled Mini Excavator boasting six electric motors. Prototypes of the 3-ton PC30 Electric Mini Excavator and 20-ton PC210 Electric Hydraulic Excavator were also on display at the event, with both machines set to be introduced to the market in 2023.
“These prototypes are a great indicator of where the company is taking electrification, and once launched, you’ll see these models grow in exposure over the next couple of years,” says Gaedtke.
Following the successful launch of the prototypes, Gaedtke says customers are now asking questions around the challenges of purchasing and utilising electrified machines. “The big question is obviously price,” he says. “Yes, the customer will use no fuel, but there is an initial higher cost for an electrified machine.”
“Most people understand the impact of carbon in our environment and want to do the right thing – but of course our customers need a favourable Return on Investment (ROI) from the technology.”
Gaedtke says another concern for customers is around the infrastructure and technology needed to recharge the machines on a construction site. Customers are asking how long the machine lasts before it needs to be recharged, and what is needed and how long it takes to recharge it.
“The technology has come a long way, but there’s still some way to go,” says Gaedtke. “All of these site challenges that have been brought to our attention we have, or are working towards, solutions.”
But he says the benefits far outweigh the challenges. First and foremost, electric machines produce zero emissions in alignment with Komatsu’s commitment to achieving a sustainable society.
In developing safe, productive, smart and clean workplaces for a brighter future, Komatsu’s electric machines have quieter motors producing less noise and vibration. This means the machines can continue to operate on noise restricted sites and operators are more comfortable, resulting in less impact on the body.
Electrified machines don’t require engine oil, so immediately they remove the risk for a hazardous fluid on site that could potentially leak, creating a contamination problem.
There’s also a huge benefit in the reduced maintenance requirements and operating cost of electric machines. Fewer moving parts and fluids result in significant maintenance cost and time savings; and all electric components of the machines require little to no regular maintenance.
When it comes to efficiency, Gaedtke says, “As you combine our electric machines with our semi-autonomous technology, operators are able to dig and grade more accurately, in turn improving efficiency.”
On top of their recently released prototypes, Gaedtke says there’s a lot happening in the design areas of the business, and customers can expect more electric machines and technologies to be released in the coming years.
“We’re excited about the impending launch of Komatsu’s Electric 3-ton Mini Excavator and the Electric 20-ton Excavator,” he says. “You’ll also see advancements from Komatsu’s mining technology that we will adopt to develop construction technology.”
“We have released Intelligent Machine Control (iMC) machines that can cut to grade the first time with no errors, and our equipment will continue to be developed to be even smarter over the next few years.
“At a time when we’re seeing skill and resource shortages, Komatsu’s electrified machines in the pipeline will make operators’ lives easier.”
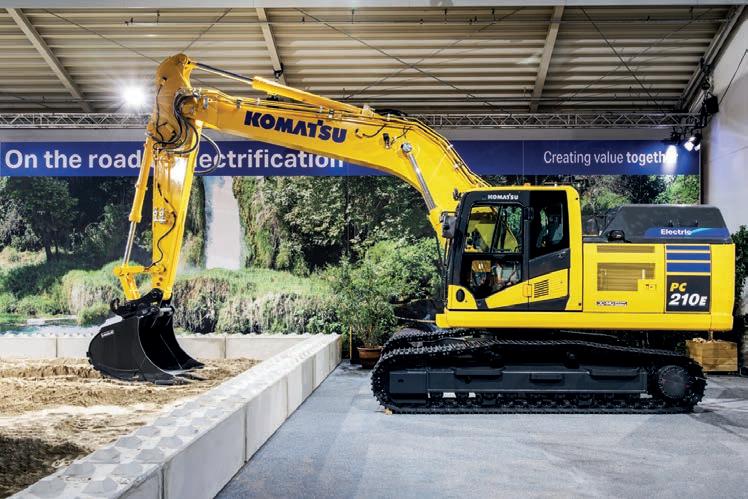
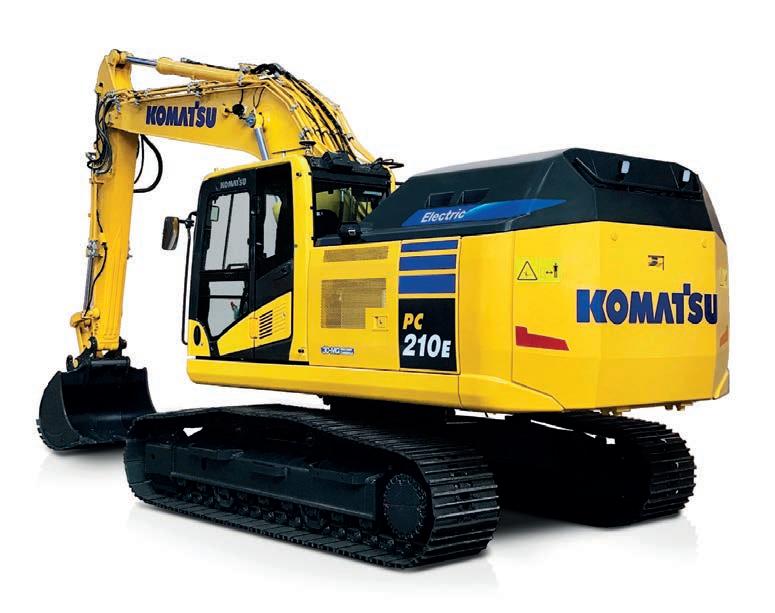
The level of innovation at Komatsu is increasing rapidly and spearheading a prosperous future for the industry. The engineers and graduates joining the company are able to work with the latest in technology, from autonomous and semi-autonomous machinery to threedimensional digital control and the software smarts that run in the background of Komatsu’s equipment.
Speaking of the internal response from Komatsu employees, Gaedtke says team members new and old are excited by the innovative machines and equipment being launched by the company. “They’re contributing some fantastic ideas in the electrification and 3D Control space, which is exciting for us to see,” he adds.
Further to electrification, Komatsu has continued to showcase its commitment to developing products designed to mitigate environmental impact. Electrification is one large piece of the puzzle towards carbon neutrality, explains Gaedtke, along with the further advancement of hybrid and diesel electric equipment, and adopting new technologies for solutions such as hydrogen fuel cells.
Declaring in 2021 it will become carbon neutral by 2050, Komatsu’s ongoing efforts towards net zero carbon emissions includes three scopes. Scope One and Two involves extending the company’s efforts of reducing CO2 emissions in its supply chain and factories, while also working to cut down CO2 emissions at its business sites; and Scope Three will see the company reduce CO2 emissions from the use of its products, which will all combine to benefit its customers’ total workplace operations.
“This strategy focuses on the supply chain, production and the end of use of our machines,” says Gaedtke. “Electrification is an important detail of Scope Three in how we build our machines and how they operate in terms of sustainability.”
“We have factories around the world harnessing a mix of solar and geothermal power to operate more sustainably and we also use biomass for our power generation.
“Komatsu has been on a journey to net zero for some time and our three scope strategies for carbon combat are committed to this goal.”