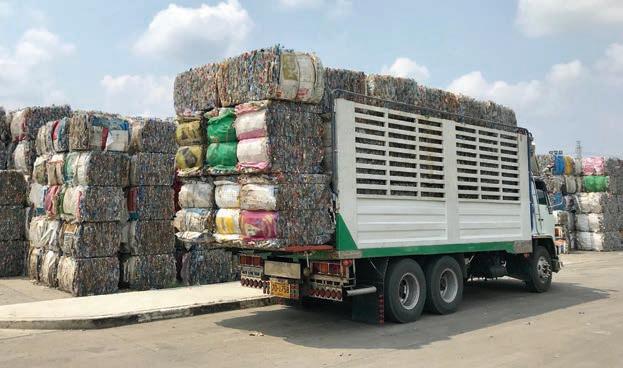
101 minute read
Waste Innovation
Those who innovate first will get a competitive advantage
By Dr Karl Baltpurvins
THE Federal Government has enacted elements of the Recycling and Waste Reduction Act 2020 (the Act) ensuring Australia takes responsibility for its waste for generations to come. The Act provides a national framework to manage waste and recycling across Australia. It has been developed to align with seven key goals of the Australian Waste Management Plan: • Ban the export of waste plastic, paper, glass and tyres. • Reduce total waste generated in
Australia by 10 per cent per person by 2030. • An 80 per cent average recovery rate from all waste streams by 2030. • Increase the use of recycled content by governments and industry. • Phase out problematic and unnecessary plastics by 2025. • Halve the amount of organic waste sent to landfill by 2030. • Make comprehensive, economy-wide and timely data publicly available to support better consumer, investment and policy decisions.
It is hoped that the reforms introduced in the Act will lead to increased recycling and remanufacturing of waste materials, which will transform our industry and boost jobs. To illustrate this point, the waste export ban is expected to see the Australian economy generate $1.5 billion in additional economic activity over the next 20 years.
If Australia is to have a hope to achieve these goals, some other critical areas require support including: • diversion of landfill levies to support investment in the recycling sector; • continued local, state and federal funding; • development of reliable markets for waste-derived products; • acceptance of waste-to-energy as part of Australia’s arsenal of landfill diversion technologies; • improvement in environmental planning process to facilitate the development of new resource recovery operations; • expansion of product stewardship schemes; • implementation of risk-based frameworks to facilitate the beneficial reuse of waste; • increased investment in research
and development and most notably commercialisation to realise tangible innovation; and • active development of infrastructure to cater for emerging waste types and contaminants.
I have no doubt the key to success lies in Australia’s ability to reinvent the sector through tangible innovation. This means we will have to not just invest in research and development programs to drive innovation, but carefully support innovation through all stages of commercialisation. I often see good innovative technologies fail at the point of commercialisation.
Fundamentally, the goal of innovation is to provide organisations with a competitive advantage within the market in which they operate. In the waste management and resource recovery sectors, this is typically focussed on cost reduction. However, other areas such as sustainability and the customer experience can also provide differentiation. The key is to understand what your customers want and also what factors drive the market (e.g., landfill levies). For the waste industry, the market is going through unparalleled change, particularly driven by the export bans, which has upset the recycling equilibria around the world. In this context, the goal of innovation in the waste management sector should logically be focussed on developing domestic resource recovery solutions. Ultimately, the organisations that innovate will obtain a competitive advantage by reducing their costs but also achieving a sustainable future.
Innovation in the waste management and resource recovery sector requires the sector to consider not only the future drivers of waste generation in Australia, but the world. Most importantly, we need to consider the drivers in the economy and what impact these will have in the future state. For example, if you consider the rapid adoption of technology, whether it be an iPhone or flat screen TV, it is fairly predictable that the volume of these wastes will generate in line with the market expansion.
Now what about emerging wastes? One excellent example is the adoption of electric vehicles. These vehicles all need reliable energy storage in the form of batteries such as Lithium-Ion Batteries. Batteries all have a lifetime where they lose efficiency and need to be safely recycled. Although Australia has recently approved a product stewardship scheme for batteries, this doesn’t include those generated from electric vehicles as there is a train of thought that business will solve that problem through R&D and innovation. This may well prove to be the case, but at present there is only a handful of brave and innovative SMEs paving the way with limited support. Given the potential of this sector, one would think that the support would be more focussed in this regard.
The other consideration for the sector is the prevalence of emerging contaminants. An example are per- and polyfluoroalkyl substances (PFAS). These chemicals are persistent in the environment and in the human body – meaning they don’t break down and they can accumulate over time. Emerging contaminants such as PFAS are starting to raise the heads through the waste management and resource recovery sector. We need to ensure that our sector is robust and can accommodate for the rapidly changing landscape, or we jeopardise achieving the above-mentioned goals, particularly the 80 per cent landfill diversion target by 2030.
The key to innovation is to invest at the right time. If you invest too early you run the risk of not obtaining a reasonable return on your investment; too late and you simply fall behind your competitors. As a country, we need to have long-term vision and an investment horizon (often 10 + years) that supports us in realising this vision. There is also a significant need for government, at all levels, to support innovation in the sector. This can include providing innovation funding, product stewardship schemes, landfill levies (and bans), as well as ensuring that the planning process supports rather than hinders investment. It is clear that the Australian population expects the industry and government to uphold environmental and sustainability standards. Whether it be the illegal export of e-waste to the developing world, or banning single-use plastic bags in our supermarkets, the community is driving social change.
The waste sector has always shown itself to be adaptable to change with the constant evolution of the market. However, there is no doubt that the current challenges we face in Australia will require more intensive investment in innovation, infrastructure and technology. This type of investment requires strong government policy making, so that the industry has confidence that the investment will provide a reasonable return on capital over the lifetime of the investment. For this to occur, there needs to be a strong alignment with the waste management industry and policy makers so that the investment risks are specifically addressed.
Executed well, Australia will join other leading nations in developing a sustainable future including the development of a robust circular economy. Executed poorly, and we will see major stockpiles of waste and a deterioration in social sentiment towards recycling.
Australia needs to develop domestic resource recovery solutions to its waste issues.
Education important in moving ahead with reusing materials
“GROWING up we put everything in a garbage bin, garbos came, and took it away into landfill. Life was simple back then. The only recycling I did was crawl around a few new construction sites as a kid and pick up some coke and Fanta bottles and get my 5 cents or 10 cents and buy some lollies with it. That was how life was then.”
Cleanaway’s COO Brendan Gill also remembers going to the local tip with his father and throwing all their rubbish into the local landfill at no cost – nothing was sorted, everything went in the one place. Then there was the backyard incinerator that was the staple of many Australian urban and rural households. It was a quick way to get rid of rubbish – he even remembers the funny colours plastic made as it melted under the assault of heat from the fire.
Those days are long gone but Gill also believes that we are still a long way from where we want to be. Gill was due to speak at the Australian Waste Recycling Expo (AWRE) event in July but it was cancelled due to COVID-19. He was to talk about the challenges faced by FOGO, plastics and textiles in the circular economy. However, he doesn’t need an audience to get across his message – and passion – about where Australia, and more importantly its inhabitants, need to be in order to keep up with Europe in terms of getting a sustainable circular economy up and running.
“Society’s resources are finite, yet we are a disposable society,” he said. “When I think about everything that goes into a landfill nowadays, pretty much everything can have a better use than burying it in the ground. If that happens it will just decompose, and depending on the nature of the material, it will produce methane. As most people in the industry know, methane is about 30 times more potent in terms of being a greenhouse gas, than carbon dioxide.
“We’ve made some improvements but there is still a lot of stuff in those garbage bins that can be recycled and reused that is going to landfill. What does it take to fix? I think it starts with households and businesses to take ownership and stewardship of their waste. That means sorting it. There are no technologies that can sort every possible waste stream.”
He believes the country needs the generators of waste to do some of the sorting into green and food organics.
“We can put them into one bin and turn them into valuable composts. We generally have lousy soil in Australia, so we can renew soils,” he said. “The challenge with FOGO is to get it in markets. While we collect a lot of green material and we have to clean it all up, not everybody runs a reasonable household like you and I. There is all sorts of stuff in those bins. I was at a processing facility recently and I asked one of the workers what was the most interesting thing they’d found in the past month. It was a sheep’s head.”
One of the biggest challenges is education, he said. Some people are
ignorant of what it takes to make sure that the different wastes are put in the correct streams. Then there is the impression from the public that maybe it isn’t their job to make sure waste is sorted into the various bins.
“I saw a comment on a social media site recently where the poster said, ‘why should we have to do all the recycling at our homes and in our bins? It’s the waste company’s job to do that. I pay rates, why should I have to go and sort the bins out for these people? All you are doing is the waste company’s jobs for them’,” said Gill. “I think that is a small-minded mentality. If they didn’t do it, and you still want it sorted, then the companies will have to pay people to do it. That means rates are going to go up.”
And the landscape is changing all the time. Most people remember when recycling first started, there was your general waste bin, plus a 20-litre container bin. Today, most councils have a minimum of three bins, with a fourth on the horizon, and there might even more happening si milar to some countries in Europe. However, it is not only the number of bins that might be changing. Councils are realising that all waste is not created equal.
“We have just been told that our general waste bin will no longer be collected weekly,” said Gill. “We have been given a year’s notice that it will be collected fortnightly. Our FOGO bin will be collected weekly. That’s because the biggest component of household waste, by type, is food.”
On the bureaucracy front, Gill
believes both the federal and state governments need to step up to the plate more in terms of assisting waste companies find markets for recycled products. Cleanaway, along with other waste management enterprises, is proactive, however a little bit of help would be good.
“We need to have end markets for these recycled materials. It is a priority,” he said. “Government needs to show leadership to companies. I’m involved in a lot in plastics at the moment. We have a joint venture with Asahi Beverages and Pact Group with a plant being built in Albury. It will take about 1 billion bottles. Coke has joined us for another plant we will probably build in Victoria. That plant will process about 1 billion bottles, too, but we need an end market. We need end consumers wanting to buy water bottles made out of recycled material.”
And while Gill is glad that the joint venture will do a lot to get the number of empties out of the waterways, playgrounds and parks, he believes that still more needs to be done.
“One billion bottles are drop in the ocean,” he said. “About 10 per cent of them. It all helps in terms of collecting it. It’s a resource. To replace that plastic – it is an oil-based product – you eventually have to drill more oil wells. If you have it, why not use it? If you have absolutely no better user for something, and it has some calorific value, then burn it.”
But isn’t burning it just as bad? Not if you use energy-from-waste (EfW) technology, said Gill. To the uninitiated, an energy-from-waste plant doesn’t sound too appealing in terms of negative impacts on the environment. EfW plants don’t come cheap. Those within the industry know how they work, but again, to Gill it is all about educating the naysayers. Not only are energy-from-waste plants a good idea, they have many strings to their bow.
“They’re not what you might think they are in terms of being like an incinerator – nothing could be further from the truth,” he said. “They are hi-tech plants. We are proposing one for Sydney out at Eastern Creek. It will cost about $700 million to build but the emissions out of that would be lower than the lowest European emissions today. A colleague said to me that the amount of emissions and nasty stuff is the equivalent of six prime movers running down the freeway for the day.
“You get more emissions than that taking waste down to landfills, but with this method you also get power out of the deal.”
Also, there are certain things that can’t be recycled or burned, but if they go through the EfW process, they will eventually have another use. “If you put a broken plate in your rubbish bin, it won’t burn. It can’t be recycled,” said Gill. “However, if you put it through the EfW plant it’ll end up as bottom ash, which you can then put into pavers, roads, bricks and whatever else. At the end of the day the principles are all the same – try and reuse if you can. Don’t go and buy more than you need.” iw
The backyard incinerator is from a time when all rubbish was thrown away or burned.
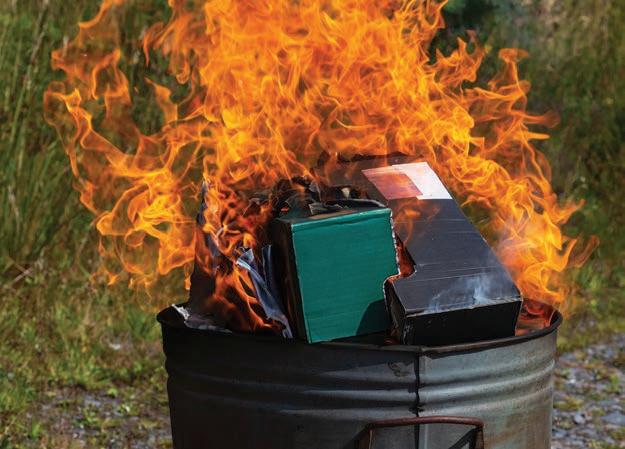
New Victorian EPA rules to come down hard on soil contamination
By Dale Smith
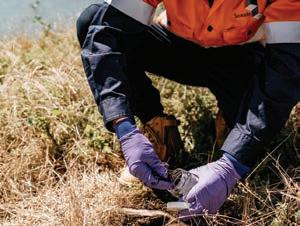
NEW environmental legislation in Victoria has significantly shifted the regime of risk associated with soil containing asbestos, PFAS and other chemicals on major property and infrastructure projects, which could see developers and contractors fined and slapped with multi-million-dollar clean-up bills.
Amendments to the Environment Protection Act (2017) that came into effect on 1 July 2021 have replaced the old system that governed liability for polluted soil and given the Victorian Environmental Protection Agency (EPA) new powers to enforce compliance across the sector.
As a result, landholders, property developers, contractors, subcontractors and third parties can be held to significantly higher levels of accountability for actions that are harmful to the environment or community. On top of that, their liability now extends for decades beyond their direct involvement with the project in question.
Rather than the end-user being saddled with rectification costs, the new regime transfers the lion’s share of liability to parties involved in the delivery of new residential communities, apartments and townhouse developments, commercial and industrial sites, as well as major road, rail and other governmenttendered infrastructure projects.
Further, this liability extends well beyond the design, construction and commissioning of these assets, with the new legislation granting the EPA powers to impose multi-million-dollar fines on individuals and organisations responsible for environmentally destructive practices, such as soil contamination.
The environmental watchdog still carries the historical legacy of multimillion-dollar clean-up bills from decades of chemical contamination of soil across Greater Melbourne. However, the agency’s ultimate focus remains the proactive protection of the environment and human health.
These regulatory changes make it essential that all parties active in land-based development undertake appropriate due diligence to identify risk as related to the presence of contaminated soil.
Understanding the extent of the contamination, if any, is the first step toward the implementation of appropriate, proactive soil remediation systems on site prior to the commencement of works.
For many of these operators, acting early could be the difference between a healthy business balance sheet and extensive post-construction remediation costs, including relocation and cartage of contaminated soil, legal fees, reputational damage and a seven-figure fine. For many operators, these unforeseen additional costs could prove fatal.
Importantly, the reforms are expected to create better economic, environmental and community outcomes for Melbourne and Victoria as the city and state continue to grow. However, a lack of general understanding and public resources around the complex issue of soil contamination means calling in the professionals to advise and assist is ideal.
The rules offer greater clarity around the apportionment of responsibility for environmentally harmful actions during the delivery of major projects and, while they are still in their infancy and yet to be tested in the courts, should give developers and contractors the push they need to engage qualified environmental consultants early in the life of the project.
Given the changes, developers and contractors with active projects on land of which they are unsure of contamination levels should seek expert advice. Ideally, engagement should occur at the commencement of scoping and design works. If possible, developers should engage expert advice prior to the appointment of the project delivery team and contractors should ensure engagement has taken place prior to the release of tenders for government-funded infrastructure projects.
However, even on projects that are well into the design phase, or have commenced construction, it’s never too late to act.
Early involvement of soil contamination experts will identify any additional costs associated with remediation works and, for the majority of projects, this cost can be built into the overall cost of the project during the tendering process, meaning no surprises and no court battles, legal fees or project delays. Greater clarity and a well-defined framework for shared risk also lays the footings for a more collaborative approach to infrastructure delivery between governments and infrastructure providers, helping maximise value for clients, contractors and communities.
Getting on the front foot and getting help setting out a clear plan is the best way to tackle uncertainty and risk. In most cases, only simple and relatively inexpensive works are required to solve the problem. It’s important to remember that any additional layer of cost identified during soil testing isn’t necessarily due today or tomorrow: the earlier businesses understand the situation, the more scope they have to allocate budget and amortise costs over the short, medium and long-term.
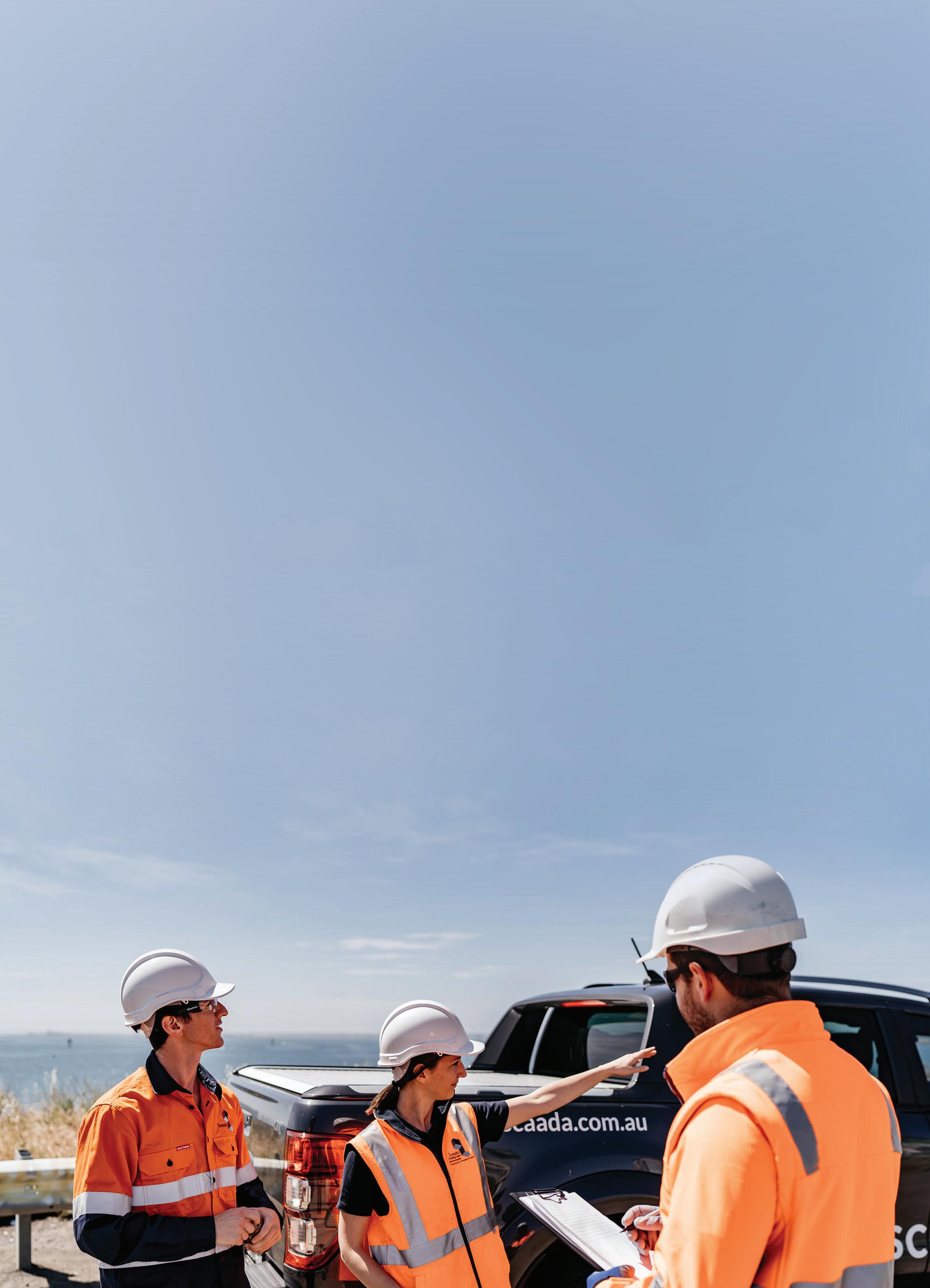
The EPA is proactive of protecting human health.
Dale Smith is the managing director of SCAADA Group iw
Composting facilities complement biogas facilities for organics recycling
By Charlie Emery
THE circular economy is about designing out waste and pollution and keeping resources in use at their highest value, while regenerating natural systems. There’s a lot of organics to be diverted away from landfills in Australia. Sending organics to landfill releases greenhouse gases, primarily methane which contributes to climate change. The impact of methane on climate change is around 25 times greater than carbon dioxide.
Nutrient-rich organic waste resources can be used to produce biogas for electricity as well as soil health products. Soil health and renewable energy are both central to a closed-loop carbon cycle and a circular economy.
In the EU and USA, you’ll find biogas and composting facilities working side by side to create renewable energy and organic soil improvers. Co-locating these technologies significantly reduces environmental footprints. Then there is the anaerobic digestion (AD) process, which creates biogas and digestate. Combining biogas and composting technologies means the composting facility can take the digestate as a liquid or as a solid.
Organic waste delivered to an AD plant can produce high-quality biofertiliser via wet or dry systems. The end by-product of the AD process is mixed with other organic materials and composted.
Bringing together these different technologies means you can aggregate the inputs into one receiver and send it to the appropriate technology on the same site.
There are multiple benefits to colocating an AD system with an aerobic In Vessel Composting (IVC) process: • It captures methane from organics first to produce biogas for electricity. • Outputs from the biogas plant can be used to create organic soil improvers. This avoids sending waste resources to multiple locations. • It reduces the number of transport
movements to and from facilities • It offers economies of scale for administration and site infrastructure. • Composting facilities have direct access to more renewable electricity for processing.
A successful example of co-locating composting and AD is at Richgro’s facility in Jandakot, WA. The facility processes food waste to produce a high-quality biofertiliser and green energy to operate the site’s plant and equipment. Excess electricity from the plant is then fed back into the grid, powering homes in the City of Cockburn.
EarthPower Technologies was one of the first food waste AD facilities in Australia. Located in the Sydney suburb of Camellia, the facility processes food wastes to produce green electricity and soil fertiliser. Food scraps from more than 14,000 households in the City of Sydney council are being sent to the facility. This saves the council on waste disposal costs, creates green energy, and produces an organic fertiliser for local agriculture businesses.
Success for the Richgro and Earthpower facilities has come via commercial persistence and minimal regulatory support. Overseas, there are good incentives to supply renewable energy to the grid for community use. The following plans are in place in the UK to encourage AD plants: 1. The Green Gas Levy is placed on licensed gas suppliers who are required to make quarterly payments to fund the Green Gas
Support Scheme. This scheme provides financial incentives for
AD biomethane plants and aims to increase the proportion of green gas in the natural gas pipeline network. 2. The Domestic Renewable Heat
Incentive Scheme provides financial assistance to promote heat from renewable sources, including biomass boilers. 3. Renewable Obligation Certificates are Green Certificates generated per megawatt hour (MWh) of energy generated from a renewable energy source, which can be then traded in the market to generate revenue.
This scheme is similar to the
Large-Scale Generation Certificates (LGCs) created in Australia under the Federal Government’s
Renewable Energy Target. An LGC is created for every MWh of green energy generated.
The recently released NSW Waste and Sustainable Materials Strategy includes AD, in-vessel composting and more advancement of the waste-toenergy conversation.
Byron Shire Council’s proposed bioenergy facility will be the first of its kind in Australia. Dry AD uses oxygen-free (anaerobic) conditions to break down organic matter inside a contained facility. The resulting biogas
is converted into 24/7 dispatchable and controllable renewable energy 365 days a year. The proposal will provide enough renewable energy to power the facility itself and the Byron Bay Sewage Treatment Plant with any excess available going back into the grid.
The Australian Government recently announced $196.9 million in new funding over four years to implement the National Soil Strategy. This includes the Food Waste for Healthy Soils Fund, worth $67 million to enhance organic waste facilities and support community education to reduce food waste going to landfill. This funding will bring together governments, industry, researchers, farmers and other stakeholders to sustainably manage our soil.
The guiding principles of collaboration, science and innovation, knowledge sharing, and future soil security, inspired the National Soil Strategy. Its vision is to value soil as a key national asset that is better understood and sustainably managed to benefit the environment, economy, food, infrastructure, health, biodiversity and communities.
Compost is key to soil health because it increases water retention, reduces compaction and erosion, improves drought tolerance and maintains biodiversity. Aerated composting infrastructure equipped with specialised air and water
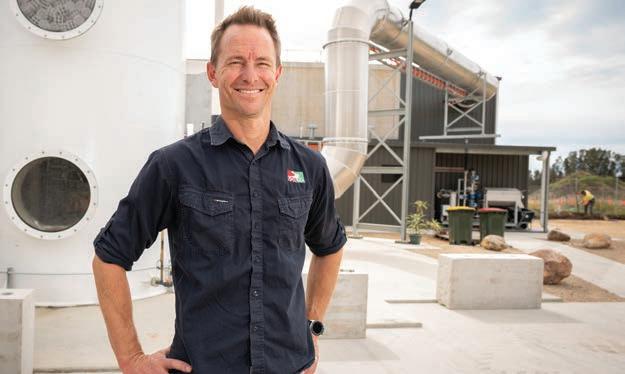
management systems can maximise outputs and minimise costs. This technology provides investment and jobs that lead to huge environmental benefits in water use, soil health and regeneration.
Creating a closed-loop carbon cycle gives organic matter back to soil, increasing its ability to sequester carbon. Drawing down carbon from the atmosphere reduces greenhouse gas emissions and mitigates climate change. Introducing mechanisms to assist with establishing AD, supplying renewable energy to produce soil health products or power our homes should make sense.
AORA NSW ’s chair Charlie Emery is a champion of biogas being used to produce electricity.
Nowra has been chosen as the new site for the biogas facility
Biogas plant to be built at Nowra site
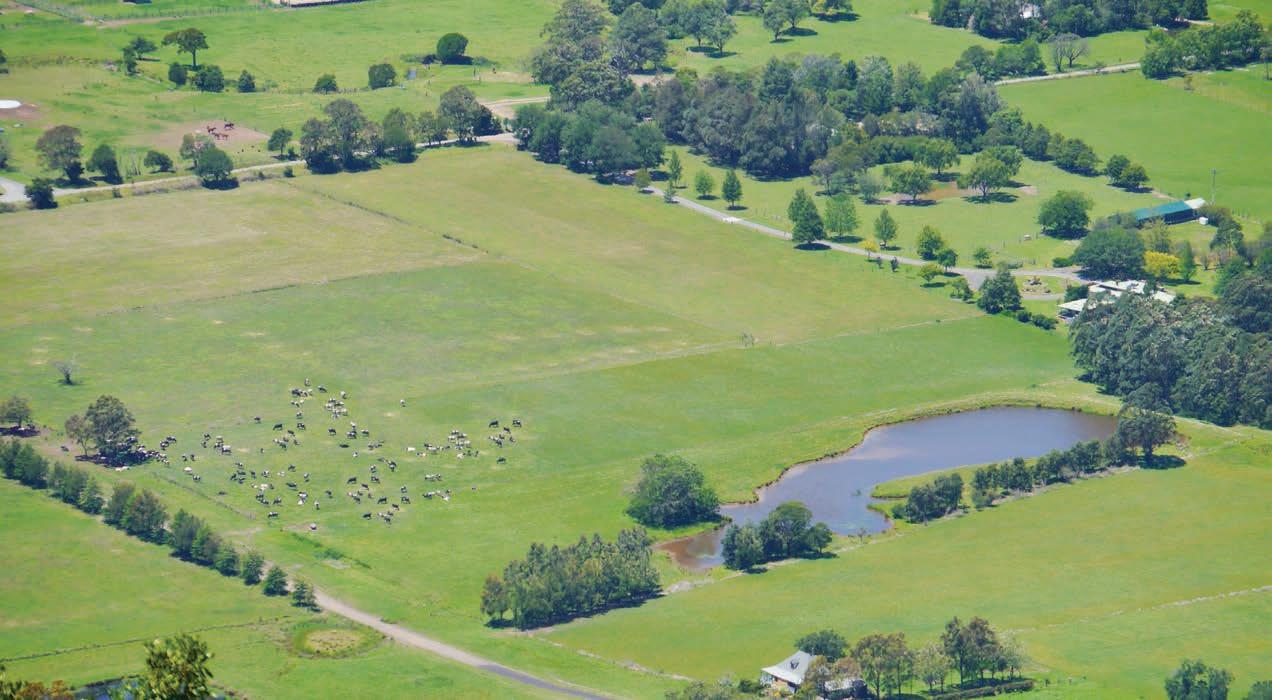
NOWRA is to become home to a large-scale waste to energy biogas plant. The upcoming project is a joint venture between Innovating Energy, Botres Global and biogas tank manufacturer Schumann Tanks.
“Nowra will be the first of a number of renewable waste to energy projects to be developed by the Joint Venture throughout Australia and New Zealand, which will be fuelled by cow manure and other organic wastes,” said Innovating Energy’s managing director, David Ryan. “The project will improve the dairy farming environment by cleaning up waterways and contributing to reducing CO2 emissions for the dairy farms who are constantly striving for solutions to reduce farm pollution.”
Several dairy farmers in the region have already signed on to the project.
The biogas plant is to be built on the Terara Sewage Treatment Plant site owned by Shoalhaven Water & Shoalhaven Council and is unique in that the manure from each dairy farm in the group will be aggregated to feed and operate the plant and the electricity produced will be shared between the group of dairies and Shoalhaven Council with the excess being sold to retail customers.
The group of local dairy farmers are the project’s biggest supporters and have said that the Biogas Plant will provide cost benefits and energy savings for their dairies and will assist in helping to deal with manure management on each farm. Rising energy costs are a consideration in operating dairy farms, particularly the costs associated with keeping milk chilled at the required temperature prior to pick up by processors, so generating electricity from their own farms will be a benefit.
The Innovating Energy Biogas plant will be built over a 12-14 month period with completion expected in early 2022. It will feature the very latest in Biogas technology provided by Botres Global and Schumann Tanks producing clean, green energy 24/7 with zero emissions. iw
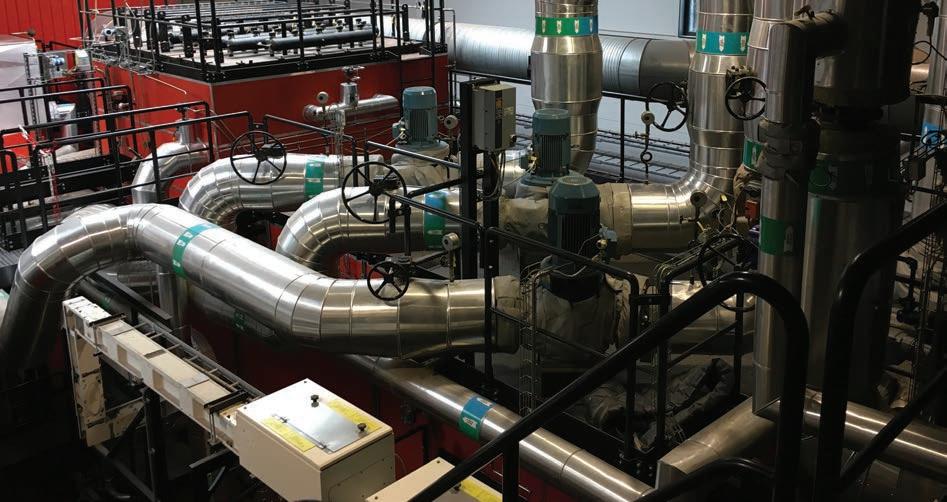
Calculating how much fuel tax credits a company is entitled to can be time consuming.
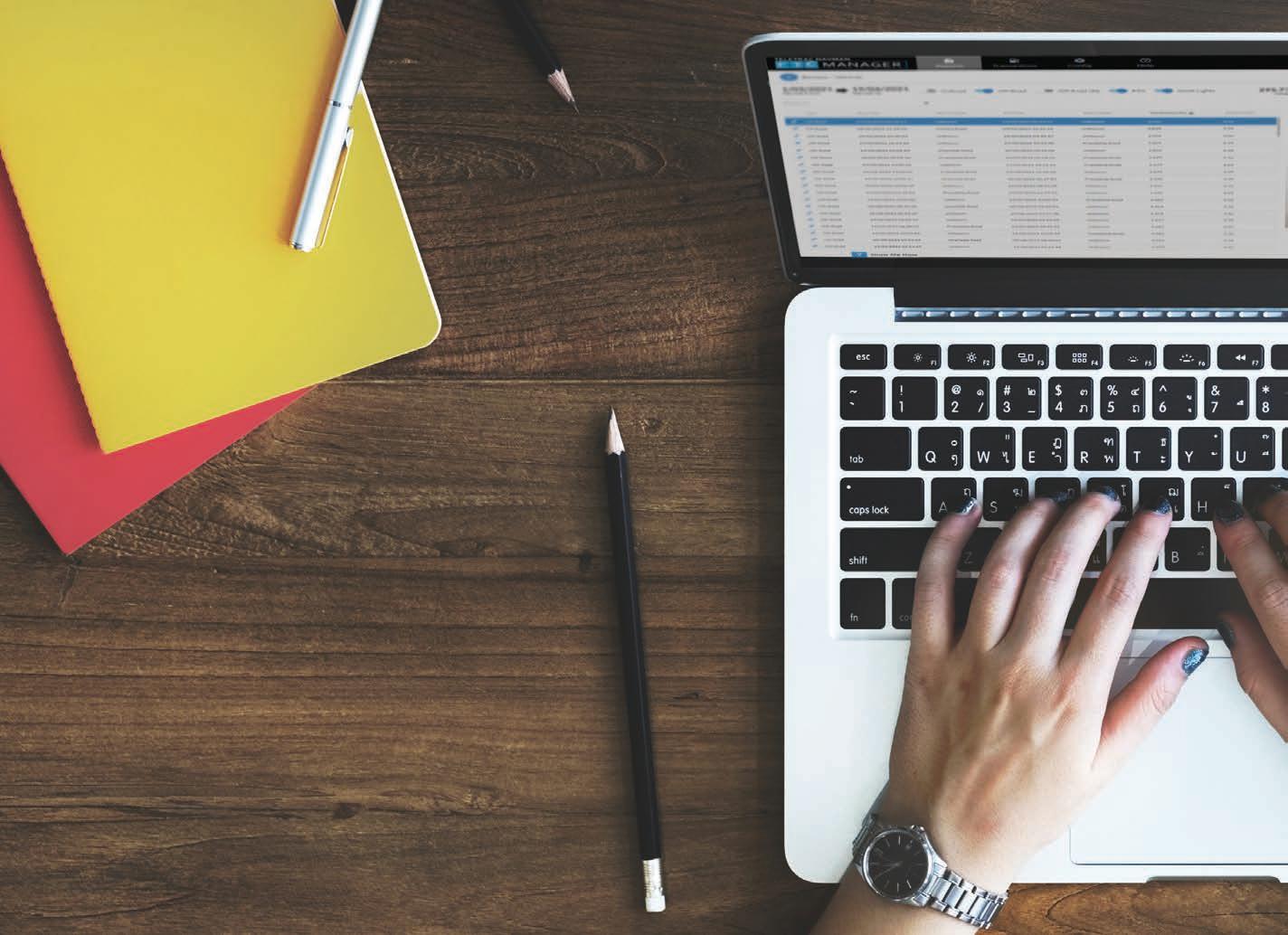
Fuel tax credits: how much money can you get back?
WHETHER your contracts are for the inner city, suburbia or regional Australia, keeping a fleet of garbage trucks on the go is a costly exercise. And being a vehicle that takes its toll on the road, these trucks pay their fair share of road tax via the excise on fuel. Yet, these vehicles spend plenty of time off-road – at landfills and MRFs – offloading the contents of their bins.
This means that during the time, they are not aiding in the deterioration of roads so therefore are not subject to the fuel tax. However, figuring out how much tax you should be getting back in the form of a tax credit can be confusing – What constitutes offroad? Does the ATO have a formula? Are there programs that can help you figure it all out? The answers are: depends, not really and yes.
Peter Perich is a director of PPM Tax Group, who specialise in getting monies back for businesses that use truck fleets, and especially like those in the waste sector that spend a fair amount of time off road. How does a business go about getting fuel tax credits and how does the government charge for the tax in the first place?
“Fuel tax credits are about recovering excise tax on fuel. When you go to the servo at the moment you are paying about 0.43 cents a litre in tax for fuel,” said Perich. “If you are a business using it in certain activities, you can either recover the full amount or a partial amount. It has been given a number of names in the past. If you use that fuel for a business purpose that is not travelling on a public road you can get all your excise back. This covers such industries as mining, farming and construction.
“However, if you are a heavy vehicle about 4.5 tonne GVM – such as garbage trucks – then you have to take out a road user charge that drops you back to 16.9 cents per litre. The road user charge is the government’s way of recovering costs for the additional wear and tear on public roads by heavy vehicles. Historically, what has happening in the past was people would say ‘I have a vehicle that is 4.5 tonne GVM I can claim road transport rate. If I have off-road machinery and equipment I can claim that rate. If I have a light vehicle, I can’t claim it’.
“However, the argument from the ‘Linfox Case’ – which was ultimately successful in the Administrative Appeals Tribunal was that – ‘well, it’s not the whole of the fuel. You can apportion the fuel you have used between activities, including to operate auxiliary equipment on heavy vehicles.”
There are three activities that a truck can exercise its right to get fuel tax credits when not on a public road and therefore do not have to pay the road user charge. These are: • Places where they don’t travel on a public roads. • The extent to which they idle in those places – when they are burning fuel and not travelling on a public road. • The operation of auxiliary equipment,
The last point is a big one for the waste industry, according to Perich. It is essentially any moving parts on a vehicle that are driven by the main engine, i.e. using the fuel to operate. It is allowable to apportion some of the fuel use towards operating that equipment. This includes anything that is driven by a PTO (Power Take Off unit), which converts the power
from the engine into a form that can be used by different types of machinery that is mounted on the vehicle. This would include the bin-lifting mechanism on a garbage truck. It does not matter if the vehicle is on or off a public road when using this equipment.
And what type of monies can be returned to the business? Depends on the size of the business and what they have claimed, said Perich.
“In the past decade I have done about 500 reviews for all sorts of companies around the country – the largest being in the millions in terms of refunds, but usually it can be anything from a couple of grand to hundreds of thousands of dollars. It depends on the business, how they are currently claiming, and what their vehicles are doing,” he said.
Perich uses a system called FTC Manager, which helps calculate the tax credits. One of the key issues when deciding on tax credits is what is off-road and what isn’t. Supported by ATO Product and Class Rulings, the system uses mapping technology, among other things, to make sure claims about the amount of time spent off-road are correct.
The mapping system is two layered. There is the base layer, which is called the centreline geo-tunnel, which is in blue. This is put 30m from the centre line either side of every public road in Australia. Anything within that area is on-road, everything outside that area is off-road. That is the starting point. However, the ATO does acknowledge there is no universally available map sets that are always 100 per cent accurate, said Perich.
“People are drawing new sites; new roads are being constructed and that sort of thing is happening,” he said. “So, we have a second map, or layer, we can override that base line of mapping by drawing specific geofences around certain locations. For example, the first map indicating on-road areas, might encroach over areas that are definitely off road. If you don’t have a geofence that isolates that part of the grid, it will be considered on road. The geofences override that first layer and we can go right up to the edge of the road and maximise the off-road entitlement there. Every metre travelled in that area, or every second idled in that area, will be recorded as off-road travel or idle. It does it automatically, allowing customers to support a higher level of FTC claim.”
Currently, the system has about 35,000 geofences loaded. Every geofence is individually approved by PPM’s team of FTC advisors and once they are approved, they go into FTC Manager’s universal database so all customers can use them.
“If you can think about it conceptually – if I am driving along the highway and I’ve got a GPS unit that pings off the satellite every three or five minutes, you can connect the dots and figure out what it is doing by following the road,” he said. “But, if that vehicle goes off a public road, into private property, and drives around and you’re pinging every five minutes, you’ve got no way of figuring out what it has actually been doing. Our system only works with second-by-second data attained from high-definition telemetry so we do not need to rely on ‘algorithms; to estimate what happens between satellite pings.”
And just to be sure, the manufacturers of the system got a product and class ruling from the ATO.
“The product ruling says that the apportionment methods used by system are fair and reasonable for the purposes of the fuel tax law, and the class ruling says that we can use the raw data as support for making a claim. The product ruling took 10 months of negotiations with the ATO and was approved earlier this year,” said Perich.
Perich acknowledges that some fleets are bigger than others, and that there can be differing amounts saved. However, he has seen a lot of money saved by many companies. He has completed about 310 FTC Manager reviews and has seen an average increase of claim of about $63 per vehicle per month, with some industries such as mining and agriculture tending to have much higher returns.
“Bear in mind the cost of using the system is up to $15 a month, so the net average saving is at least $48 per vehicle,” he said. “There is no one size fits all, especially in the waste industry where you have different vehicles. What I will say about the waste industry is that they tend to have high off-road usage because of the nature of what they are doing. Not a lot of people understand the full extent of what they are entitled to claim. The more supporting data they have to evidence their fuel use during different activities, the more they can potentially recover and get refunds.” iw
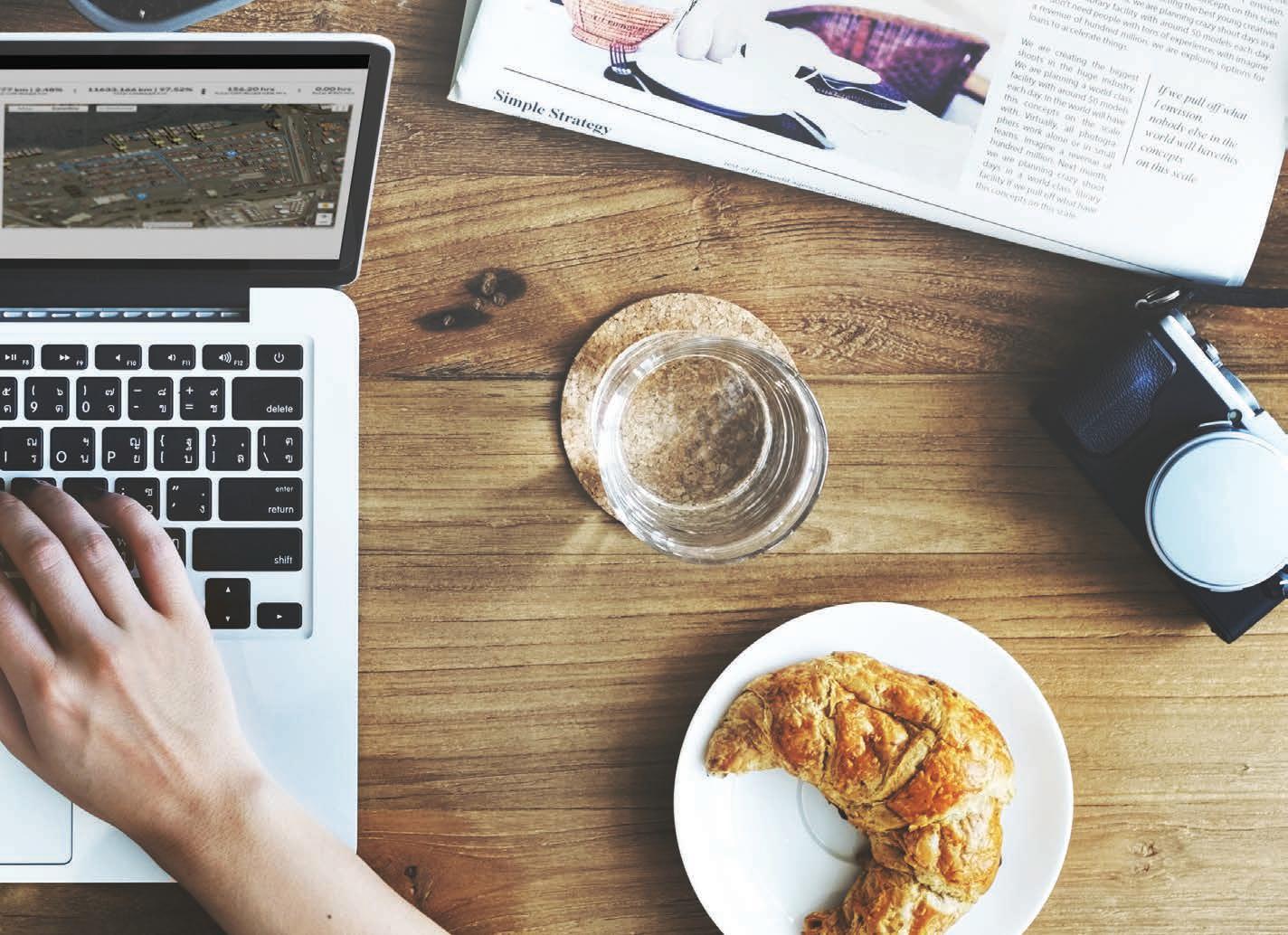
Difficult year, but waste shines through
IT has been an interesting year in the waste space, with a lot going on in terms of trying to make sure the industry navigates its way through an array of changes that are occurring. From COVID-19 though to singleuse plastic bags being banned, as well as the diversion of waste from landfill targets being met, most of these challenges have been met head-on by the industry. It is keen to embrace these changes because it sees the long-term goals as essential for Australia in terms of meeting its circular economy and sustainability ambitions. Then there is the issue of energy-from-waste and what it means for the landscape. And what about new infrastructure, and more importantly, who is going to pay for it?
While these issues are at the forefront of industry, 2021 has also been a year where a lot of organisations and individuals have stepped up to lead the way, take on difficult propositions, and say what has to be said in order for the industry to move forward and provide the products and services the country and states want and deserve.
With that in mind the Waste Innovation & Recycling Awards have been developed to recognise those that are leading the way in of making sure targets are being met, creating innovative and new ways of dealing with waste, and dealing with the government bureaucracy and red tape in order to get these ideas off the ground.
What is heartening about going through the different nominations (all listed on Page 48 and 49 of this issue), is the number of people excited to be in the industry, and companies that are taking the message on board in terms of community expectation. In some cases, they are using their own initiative without the big stick of local, state or federal government legislation waving in the background.
Overall, there is an impressive array of nominations, and it would not be prudent to single any out. The judges have a difficult task ahead when trying to choose a standout in each category.
Unfortunately due to the COVID epidemic, the hope of holding the awards in conjunction with the Waste Expo Australia event is now not possible as the Expo has been moved to an online platform event. The good news is that, all going well and COVID doesn’t rear its head in another form, the awards will be held as a live event on March 31, 2022 at the Showtime Events Centre in Melbourne.
As usual, sponsors are a key component to any successful awards night, and the Waste Innovation & Recycling Awards are no exception. We would like to thank ResourceCo, Daimler and the MWRRG for their sponsorship of the award’s program. Here’s hoping that next year, all sectors of the industry will start to see the benefits of the groundwork laid out by many companies, government bodies and individuals in 2021 in moving the industry forward. iw
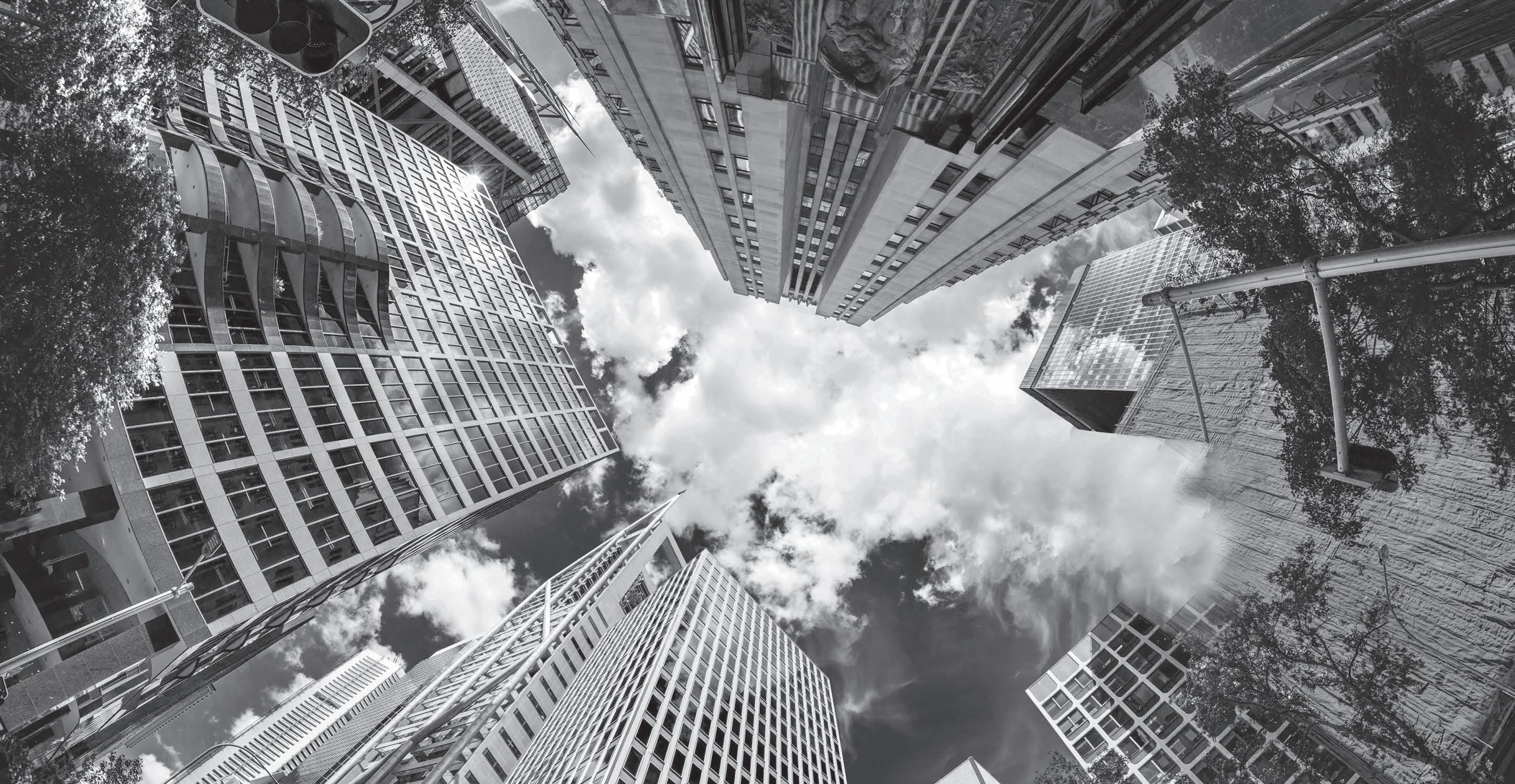
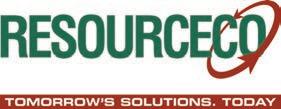
GLOBAL leader in the recovery and re-manufacturing of primary resources, ResourceCo, has been announced as the sponsor for the coveted Innovation Award at the Waste Innovation and Recycling Awards, which will be held in early 2022.
The Innovation Award recognises the evolution, invention and improvement that must always occur in the waste management and resource recovery sector, in order for a strong circular economy to grow.
ResourceCo CEO of Waste & Recycling, Brad Lemmon, said the company is proud to support an Award that is focussed on innovation to build a sustainable future and make a positive difference.
“We’ve been at the forefront of established and emerging markets for recovered materials for 30 years and have a strong understanding that to build a sustainable future, you need to accelerate growth through innovations and investments,” Lemmon said.
“Earlier this year, we pioneered a domestic-led solution to waste glass, using over 8.5 tonnes of repurposed glass as an alternative base to sand in the construction of South Australian roads.
“After successfully trialling the technology with the South Australian Department for Infrastructure and Transport, we further backed this latest innovation, by investing in a new glass processing plant north of Adelaide.
“This investment is capable of transforming the way we use recycled materials on our roads, as we could ultimately see 30,000 tonnes of waste glass repurposed into construction materials each year.
“At the end of the day, it’s about backing progressive solutions in sustainability and building environmentally conscious partnerships across industries.”
ResourceCo is also leading the way in the rubber remanufacturing industry, with its award-winning tyre recycling business, Tyrecycle, investing more than $10 million in the development of a new dedicated tyre processing plant in Sydney’s Erskine Park and a further $30 million in facilities all around Australia.
Tyrecycle CEO Jim Fairweather said the facility will be outfitted with cutting-edge technology and world class equipment that will expand the business’ production capacity and capability for tyre-derived-fuel (TDF) and rubber crumb products.
“It is only through investments in innovative new technologies, and a steadfast commitment to environmental security and improving current supply chains, that we can achieve meaningful and sustained progress towards a circular economy.
“We’re delighted to back this Award, which demonstrates a real confidence

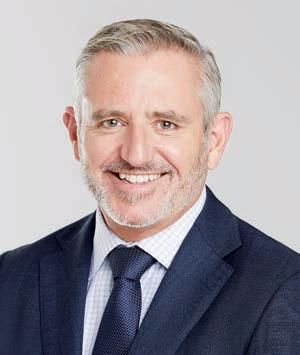
Tyrecycle CEO Jim Fairweather.
in the innovation of the resource recovery sector and its commitment to driving sustainable solutions to longstanding waste management issues.”
The winner will be announced at the ceremony, with the Award going to a company or individual who has endeavoured to close the loop and achieve circularity by introducing new technologies, processes, or facilities to their operations.
ResourceCo is also hoping that the Award will encourage others to continue finding new ways of progressing waste management and resource recovery across Australian markets. iw
Once-in-a-generation step change
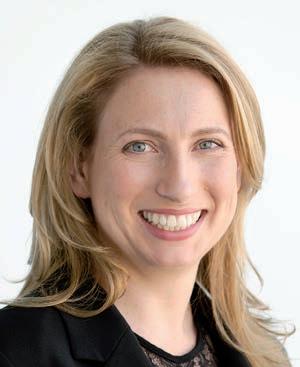
Leadership starts at the top
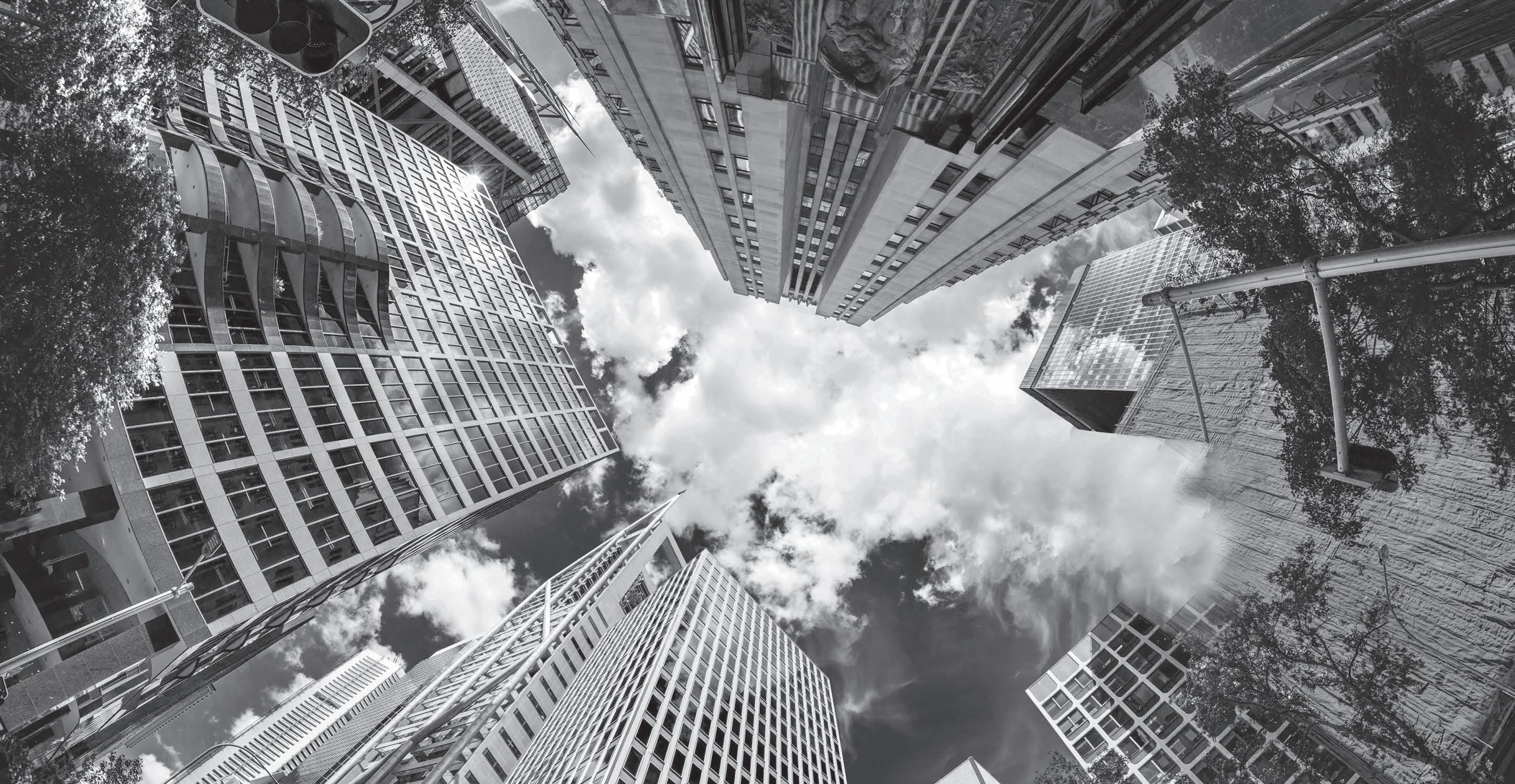
THE Metropolitan Waste and Resource Recovery Group (MWRRG), more commonly known as Metro, based in Victoria is one of the sponsors of the Waste Innovation and Recycling Awards.
The government entity will be sponsoring the Women in Waste Award, one that CEO Jill Riseley, believes is important not just for the industry but Australia as a whole.
“Celebrating women in our sector is critical. We need the benefits and insights achieved through diversity to address the challenges of reducing waste and increasing resource recovery as we all are move towards a circular economy,” she said. “Women are going to be critical not only in terms of being part of that change that we are seeing in the industry, but also their ideas and innovations. I think at a really basic level, one thing I am keen to highlight, is that across the board, not just in our industry, we know there is more work to be done in improving gender diversity in Australia. We know that diversity improves outcomes and is good for the bottom line. We continue to see the improvements in gender diversity, and continue to see representation in our industry. Recognising and encouraging the contribution of women is a critical part of that. This award recognises this, and we are pleased to be able to support it.”
As an entity, Metro helps to support and transform change by interacting with the many councils within its purview. Delivering the Recycling Victoria policy at Metro is key as it continues to work with councils. More broadly, at a national level, the implementation of the national waste policy and the ban on the export of plastics in June this year, and tyres at the end of the year, are also focusses.
“For Metro, we’re playing a role in supporting industry and councils to adopt a adjust to these changes,” said Riseley. “The ongoing development of end markets is something that we think requires continued attention and
MWRRG CEO Jill Riseley.
investment. That is critical in creating that lasting and circular reform.
“These things, when you put them together, are a once-in-a-generation step change in how we approach recycling and waste. It is a really exciting time and keeping us all out of trouble. We are very busy.”
As Riseley points out, dealing with 79 councils sometimes means there are 79 views on policies. However, one great thing about working in such an environment is that everybody wants similar outcomes.
“I’ve found all the council’s incredibility receptive and accommodating to what we are trying to achieve,” she said. “They all have different appetites for change, and they all have different capacities to introduce a change in form depending on their municipalities. Some municipalities have got challenges that others don’t. Whether that be in regional, rural or metropolitan setting. Some of our Metro councils see community and behaviour change as really critical things that need to be invested into in order to deliver reform. Other councils are at different points in their journey. To answer the question broadly, councils have been really enthusiastic and supportive partners.
“We are a state government entity and report to a board. I am in awe of CEOs of councils. They do an amazing job. Councils do an amazing job. You look at the touch points, particularly waste – every household having recycling or FOGO, or organics or waste collected every week, every fortnight. There are very few industries that go house to house on such a regular basis. It is really impressive that the service that councils deliver, and deliver it really efficiently and really well.” iw
MERCEDES-BENZ Trucks is proud to be recognising individuals in the waste industry who have shown strength in leadership over the past year.
Leadership within an industry is an important value to be recognised. Leaders push boundaries, challenge the norm, and make changes to drive progress. Such leadership leads to products like The Econic truck from Mercedes-Benz Trucks being developed, which is a leader in the field of refuse collection. The Econic is powerful and efficient, while also delivering great safety for all road users. It delivers sustainable solutions to the growing emissions burden in urban areas, and provides an ideal working condition for the refuse collection driver and crew.
Leadership in the area of safety.
Providing trucks that are safe for not only the driver and the goods they are transporting, but the wider community at large, is an ongoing endeavour for Mercedes-Benz Trucks.
The low-entry concept means that there are only two steps up into the cab, making getting in and out easy and safer. On a busy working day, that means less climbing up and down in the Econic compared with other trucks. Also good for the back and the joints is the full air suspension with raising and lowering function on all axles.
The walk-through cab allows the driver to enter and exit the cab from the traffic-free side of the road using the inward-opening folding door. That’s not just practical, it prevents accidents.
Optimum vision of the road, and reducing blind sports, is an important strategy to ensure all road users are kept safe.
The Econic allows drivers to see other road users, such as pedestrians and cyclists, at eye level. The low seating position of the driver, the glazed cab and the additional safety assistance systems make for a great view of the road and pavements in all directions – and compared with regular trucks, that’s an advantage in busy inner cities and complex situations. This provides drivers with optimal support and ensures greater safety on the road.
The Econic can be equipped with as many as 10 safety assistance systems with the aid of cameras, sensors and additional lighting systems, designed for urban operations.
These assistance systems range from Sideguard Assist, pre-installation for Reversing Assist, Active Brake Assist, Adaptive Cruise Control, and the blind spot camera.
260kW (354hp) at 2,200rpm, minimise the particulate emissions and nitrous oxides produced from traditional Euro V engines, as well as fuel and AdBlue consumption.
Ideal working conditions
The Econic’s spacious cab offers great freedom of movement, and its wellengineered design delivers the ideal working conditions. Depending on the field of operation, there is room for up to three passengers. When pulling away, the folding door on the passenger side closes automatically.
Depending on the field of operation, a hinged door can also be installed. Furthermore, you can choose between a high and a low cab height.
With the Econic, Mercedes-Benz Trucks leads the waste industry in the field of providing safer, more efficient and comfortable trucks.
Mercedes-Benz Trucks is proud to recognise individuals who demonstrate the same leadership values in order to drive progress for our Australian waste and recycling industry. iw
Waste Innovation & Recycling Awards 2021
Outstanding Facility Award ReProcess Tas - Spectran Group
ReProcess Tas is a 12-acre state-ofthe-art construction and demolition waste reprocessing facility in Southern Tasmania. The facility is the first of its kind in the state.
Commercial Pilot Facility - Bardee
Bardee transforms food waste into protein and fertiliser with insects. Every tonne of protein offsets 50 tonnes of CO2e carbon emissions and uses no additional water.
Central Waste Facility – Bega Valley Shire Council
The construction of an emergency landfill cell and resource recovery area were a direct response to the 2019-2020 Black Summer Bushfires that hit the area. Taking a basic concept and turning it into a landfill cell and associated infrastructure happened over a 14week period and demonstrated the commitment from Bega Valley Shire Council to help get its community back on its feet.
Perth Material Recovery Facility – Cleanaway
Cleanaway reopened the Perth MRF located in South Guildford after a fire. The $26 million facility has the capacity to process over half of commingled recycling from residents and customers across Western Australia delivering up to 90 per cent recovery of reusable products.
Leader of the Year Award sponsored by Daimler
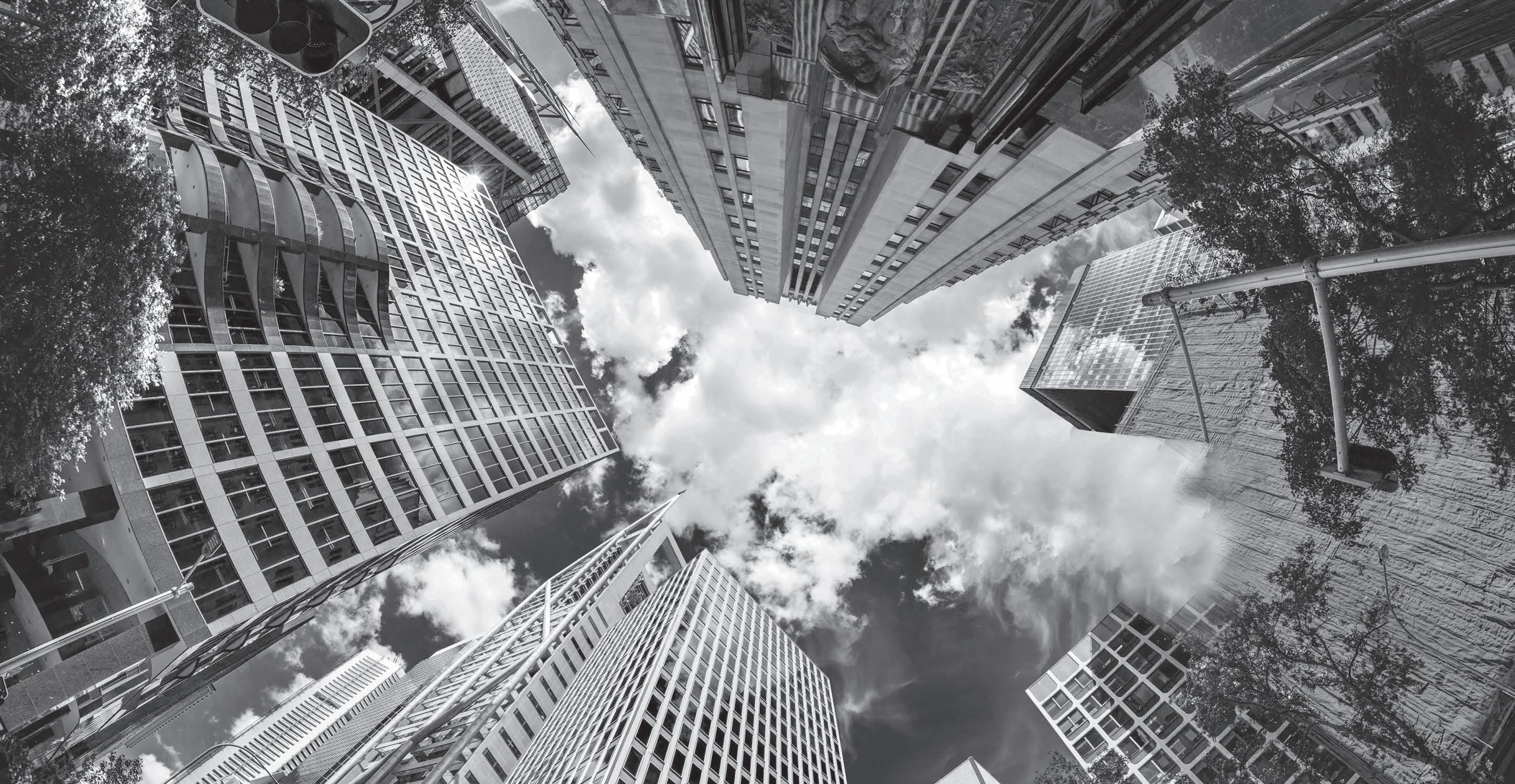
Harry Wilson
Harry Wilson is an industry icon, with a career spanning 50 years in the waste and resource recovery sector. His working career has included both small, private companies, and large Australian blue-chip corporates and leading and developing his own business. Over the years, he has lead innovation, conducted research and shared results leading to best practice.
Julian Grasso
Julian is co-founder and owner of both 30XY Group and Reclaim Waste. He founded 30XY Group approximately 10 years ago and established Reclaim Waste in 2021. Julian sits on a number of committees within the waste industry and has a real passion to do better for the industry.
Larissa Rose
Larissa has mentored more than 32 students over the past 4.5 years. She has curated an ‘Internship and Mentoring Program through her company, Glowing Green Australia. She has played a pivotal role in building the leaders of the future, which is her methodology and duty of care she believes is necessary for true leadership.
Women of Waste Award – Sponsored by Metropolitan Waste and Resource Recovery Group Sabina Wills
Sabina has driven change and innovation, including developing cleaner production solutions in the wine industry, the first Buy Recycled Conference and statistical analysis of landfill audits.
Susie McBurney
Susie has more than 20 years’ experience in the waste industry, spanning a number of senior management positions at both Remondis and Cleanaway. She has managed complex situations in many areas of the industry.
Ninna Larsen
Ninna started Reground, a model that exists to turn ground coffee waste into a resource in the community.
Larissa Rose
Larissa has demonstrated leadership in mentoring young women to achieve personal and professional success. Key to this success has been her Internship and Mentoring Program.
WARR Workplace of the Year Award Handybin Waste Services
Handybin is committed to the philosophy of seeking maximum recovery of recyclables and of achieving the highest economic value for all its products. It has successfully introduced glass, polystyrene and textiles recycling to the communities it services.
Remondis Australia
Remondis Australia has operated Mugga Lane Landfill, Mugga Lane Transfer Station, Mitchell Transfer Station and ACT’s Recycling Drop-Off Centres. It has also operated the Mugga 2 Quarry site since 2019. Over time, the facilities have transitioned from disposal to resource recovery operations.
Bega Valley Shire Council
The council’s construction of an emergency landfill cell and resource recovery area were a direct response to the 2019-2020 Black Summer Bushfires. Taking a concept and turning it into a landfill cell and infrastructure demonstrated the commitment from Council to help get its community back on its feet.
Glowing Green Australia
Larissa Rose has mentored more than 32 students over the last 4.5 years. She has curated an Internship and Mentoring Program and has played a pivotal role in building the leaders of the future, which is her methodology of teaching future trailblazers the necessary steps to become a leader of an organisation.
Community Engagement Success of the Year Award WasteSorted Talking My Language - City of Wanneroo
This program is a multilingual learning resource developed to overcome barriers experienced by culturally and linguistically diverse (CaLD) demographics when accessing waste education messaging.
TerraCycle School Recycling Program - TerraCycle
TerraCycle is empowering teachers and parents to raise the next generation with sustainable practices and values, by incorporating hands-on learning about recycling through activities in the classroom.
Our Future Waste community engagement - Sunshine Coast Council
Sunshine Coast Council sought assistance from Engagement Plus to assist it to better understand community views on options to extend the collection and processing of organic waste.
Waste Wednesday - Forbes Shire Council
The Forbes Shire Council engaged with the community and spread awareness about the ongoing resource recovery facilities available, statistics related to the waste surveys/audits carried out by the Council, innovations and additions to the existing resource recovery programs and more.
Young Professional of the Year Award Stacey Ward
Stacey Ward is an integral member of the Waste Futures team at the City of Port Phillip. She led several projects critical to the success of the ‘Don’t Waste It!’ Waste Management Strategy, including the Council’s first ever food and garden organics trial, which is now an ongoing service.
Samuel Lawson
When Samuel was young, he followed his Grandma around as she pointed to plants and told him of their everyday uses. Her influence led him to study analytical and environmental chemistry, which connected him to Keep Victoria Beautiful (KVB). Samuel is a research and project coordinator at KVB, specialising in litter/illegal dumping from a land manager perspective.
Matthew Day
Matthew is a technical engineer with Remondis Australia. Having completed his bachelor’s degree in Mechanical Engineering and Archaeology, Matthew joined Remondis as a part of its 2019 Graduate Program. His responsibilities include assisting business development, providing technical advice and support, and the management of projects from initiation to full operation.
Tara Osborne
Tara has been at BINGO for over four years and has seen the company through its IPO and large acquisitions. At the age of 28, Tara took on the challenge of being a general manager at BINGO. The company has provided many opportunities and challenges for Tara, which she has risen to every time she has been asked.
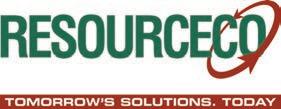
Innovation Award sponsored by ResourceCo Handybin multi-stream recycling services - Handybin Waste Services
Handybin seeks the maximum recovery of recyclables and achieving the highest economic value for all its products. Since building the plant in 2012, and further upgrading in 2015, and in addition to the traditional MRF operations, the company has successfully introduced glass, polystyrene and textile recycling to the communities it services.
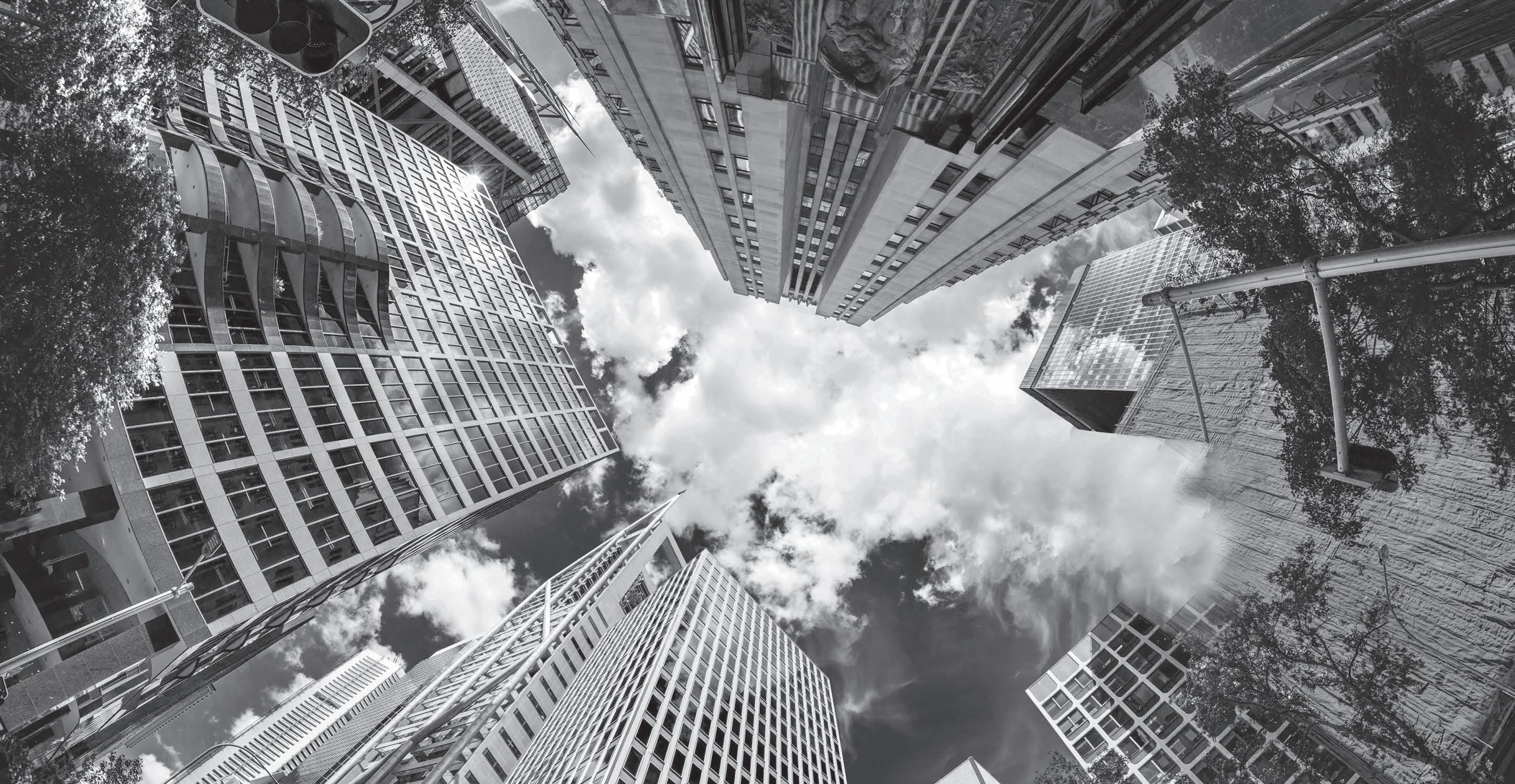
The Reground Coffee Recycling Service - Reground
Reground is a certified social enterprise turning waste into a resource to create a circular economy.
Operational Excellence Award Remondis Operational Excellence in the ACT
Remondis Australia has operated Mugga Lane Landfill, Mugga Lane Transfer Station, Mitchell Transfer Station and ACT’s Recycling Drop Off Centres since it acquired Thiess Services in 2011. Remondis has also operated the Mugga 2 Quarry site since 2019. Over time, the facilities have transitioned from disposal to resource recovery operations with the Remondis ACT team using their operational expertise to assist the region to achieve their ambitious objectives under the ACT Waste Management Strategy 2011-2025.
Waste enforcement training - Keep Victoria Beautiful
The Litter Enforcement Officer Network run by Keep Victoria Beautiful has designed and delivered the only training for authorised officers on the new Environment Protection Act. The Regulating Litter and Other Waste The Reground Coffee Recycling Service: A Model for Circular Practices was established in 2016 as Australia’s first coffee collection system, and has since seen the diversion of over 700,000kgs of ground coffee from landfill.
Recycled Plastics RMP Noisewalls - Pact Group
In a world first innovation, Pact has transformed 600 tonnes of hard to recycle plastic waste into a recycled noisewall panels spanning 32,000 square metres of the Mordialloc Freeway. Each panel comprises 75 per cent recycled materials.
Polyrok - Replas
Polyrok concrete is the latest innovation from Replas. It is a sustainable recycled plastic aggregate alternative to mineral aggregate in concrete for pathways, kerbs and channels that finds a home for one of the most problematic waste streams, soft plastic.
Training Course has been reviewed and endorsed by EPA Victoria and is being rolled out to officers all around the state.
ReProcess Tas - Spectran Group
ReProcess Tas is a 12-acre state-ofthe-art construction and demolition waste reprocessing facility in Southern Tasmania. The facility is the first of its kind in the state and at full operation, allows up to 95 per cent reduction in construction waste entering landfill.
Optimising waste collection initiative - Brimbank City Council
Brimbank’s Asset Services Team introduced digital mapping for waste collection to replace its outdated paper-based system. The all-in-one digital solution wasn’t just about replacing paper-based mapping and procedures with GPS-like mapping, event log and digital forms. It was about using technology to improve driver safety among a range of other features.
Outstanding WARR Project Award – Regional Kleinton Waste Management Facility - Toowoomba Regional Council
The Kleinton Waste Management Facility and is based on a the nearby GTWMF facility, including a Reviva Tip Shop. The Kleinton Tip Shop has demonstrated diversion of around 15 tonnes per month since opening. In addition, mattress processing has been implemented at both sites. Since commencing in November 2020, it has processed over 5100 mattresses, which has saved 1900m3 of landfill space and produced over 60 tonnes of steel.
Waste enforcement training – Keep Victoria Beautiful
To date this training course has been delivered in various formats and at a range of costs. Over 60 officers have been trained and increases in their understanding of the new Act have been seen. It has delivered the course to metropolitan councils in person and online, to regional councils in person and online, and has released a seminar recording to ensure all councils have access to the training.
McMullin Building Demolition - Drumderg Services
The demolition of the McMullin Building proved to be a benchmark project for the University of Newcastle, Drumderg and TSA Management in establishing complementary protocols for planning, achieving and exceeding best practice environmental, recycling, HAZMAT removal and safety across all phases of the demolition project.
FOGO deep dive education project – Forbes Shire Council
The objective of the project is to recover FOGO materials ending up in the landfill. A three-month long education and awareness campaign focusing on diversion of FOGO materials from red lid garbage bins to green lid FOGO bins was delivered.
Outstanding WARR Project Award – Metro Paving the Way - SSROC
Paving the Way has created a local closed-loop market for approximately one-third of participating councils’ domestic glass collections. It has reduced greenhouse gases, and driven essential infrastructure development and job creation.
Creating Change with Containers in WA – Remondis
Remondis Australia currently operates the collection and processing of non-glass products for WA’s Container Deposit Scheme (CDS) for the Perth, Peel and Wheatbelt regions. Containers are sorted at drop-off points by material type and is then collected and processed.
Berwick Reconophalt project – Stockland Minta
Reconophalt is a road surfacing material that contains recycled content derived from waste streams (soft plastics, toner, glass and reclaimed road) that would otherwise be bound for landfill. It is a type of asphalt that does not cause any harm to the environment or exude harmful fumes.
Recycled Organics and medical equipment trial - Epworth HealthCare Centre
Epworth HealthCare has recycled almost 30-tonnes of food waste, medical PVC and employee uniforms, turning these items into electricity, garden hose and stuffing for exercise equipment. iw
CAPS Australia
Company Overview:
CAPS Australia is a privately owned and proud Australian company intent on remaining at the forefront of compressed air, critical power generation solutions. CAPS offers capital sales, rental equipment, engineering & manufacturing, service and parts.
CAPS has over 40 years of experience in the Australian market with nine branches across Australia and over 170 employees, including 60 service technicians covering the full national footprint with a 24/7 service offering. CAPS is an independent company with the flexibility to search globally for the best products and technologies that best serve the Australian market’s needs and unique conditions.
CAPS has world-renowned partner brands such as Ingersoll-Rand, KOHLER/ SDMO, AIRMAN, Sauer, Pedro Gil and many more.
CAPS has in-house engineering capabilities, able to customer engineer any equipment to your needs and specifications. Back this with our Australian ISO 9001 accredited manufacturing facilities, CAPS can provide the complete end-to-end solution.
Products & Services:
• Power Generators • Air Compressors • Dryers • Blowers • Spare Parts • 24/7 Servicing • Engineering services • Rental / Hire
Products & Services:
• KOHLER/SDMO • AIRMAN • INGERSOLL-RAND • TEKSAN • SAUER • BEKO • DEEPSEA
Core Capabilities:
CAPS Diesel Generators; together with KOHLER are tailored designed to meet onsite limited real estate; featuring superior transient performance; maximum reliability; low specific fuel consumption & market leader with high power density for various segments.
Our portfolio covers high speed diesel generators up to 4600kVA (50 Hz); available with different voltage configurations; packaged either in a purpose-built acoustic enclosure or plant room install.
Standby Diesel Generators guarantee energy security for waste to energy facilities; to prevent critical process sudden shutdowns; which are termed detrimental to both equipment & revenue generation.
The CAPS Diesel Generators are engineered; tailored built to deliver superior performance but also meet stringent requirements related to real estate; load acceptance & noise performance; together with in-house engineering & local partners.
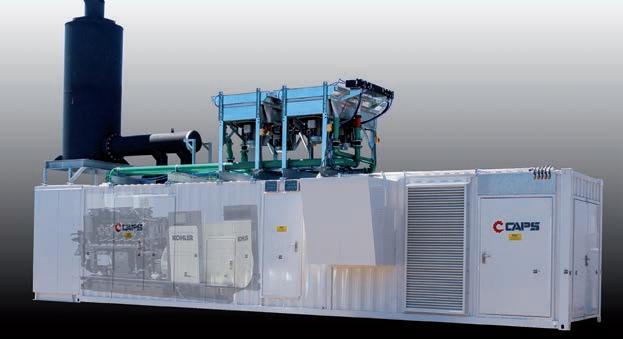
Contact Details:
CAPS Australia
185 Planet Street Welshpool WA 6106 Phone: 1800 800 878 Email: info@caps.com.au Website: www.caps.com.au
Key Contacts:
Nestor DeNiese
National Sales Manager – Power Generation Number: +61 8 6250 9871 Email: nestor.deniese@caps.com.au
CSS Recycling Equipment Solutions
Company Overview:
With 20 years of experience in our unique Australian and New Zealand region, CSS Recycling Equipment customises waste, organics, and scrap metal processing solutions, by taking a collaborative and consultative approach with their clients.
From the provision of ad hoc machinery and technology to fit an existing processing line, up to complete plant and materials handling solutions, CSS Recycling Equipment designs each solution specific to client’s requirements.
CSS Recycling Equipment takes a comprehensive approach, starting with on site reviews of existing processes, machinery and capability, analysis of client objectives, challenges, and end materials. By working closely with clients and with exclusive global suppliers to curate the best possible solutions, CSS becomes a trusted strategic partner, integrating technology, improving processes and bottom line results.
The technologies represented by CSS Recycling Equipment Solutions are sourced from around the world, are proven and reliable and have been tried and tested in our region. CSS Recycling Equipment specialises in processing all types of materials from C&D to C&I, from MSW to FOGO, Biomass and Wood, Compost and to hard to process waste.
Products and Services:
Specialising in all aspects of reduction, separation and recycling technology: • Complete consultative and collaborative plant design and delivery • Fuel Preparation Technology • Shredding • Screening • Air Separation • Baling and Shear Baling • Plastics Washing and Preparation • FOGO • Waste to Energy technology
Brands:
• Ecostar Dynamic Screens (Italy) • Ecohog Air Separation Technologies (Northern Ireland) • Hammel Recyclingtechnik (Germany) • Jono Enviro (China) • Lindner Recyclingtech (Austria) • Vezzani (Italy)
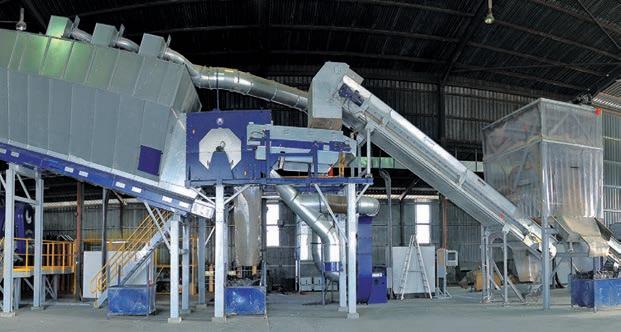
Core Capabilities:
Collaborate, consult, design, deliver and the supply of high quality equipment and plant solutions for C&D, C&I, Biomass, Organics, Wood Waste, FOGO, MSW, Scrap Metal industries.
Source innovative and strategic solutions both within and outside of our stable of equipment solutions, always with the client’s outcome as our focus.
Utilise our global relationships and local knowledge to deliver positive business outcomes for our clients and continually improving environmental solutions for Australia and New Zealand.
Specialists in: • hard to process waste • mobile and static processing solutions • manufacture of custom components • high quality and on budget projects
Contact Details:
CSS Recycling Solutions PO Box 359, Dee Why NSW 2099 Phone: 1800 644 978 Email: info@cssequipment.com.au Web: www.cssequipment.com.au
Davis Earthmoving & Quarrying Pty Ltd
Davis Earthmoving & Quarrying is a leader in mobile waste processing in NSW. For over 45 years, Davis has successfully completed tens of thousands of diverse projects for councils, government, civil and commercial sectors. Established in 1975, Davis Earthmoving is an Australian, family-owned company offering Green Waste Recycling, Concrete Recycling, Glass Recycling, C&D Shredding, Crushing, Screening, Mulching, Land Clearing, Haulage and Supply of Recycled Products. We process over a quarter of a million tonnes of material per annum. Davis has 100 pieces of diverse Plant & Equipment in its privately owned fleet for hire or contract, all equipment is available in-house. We operate our own service centre for scheduled maintenance and service trucks for field repairs. This guarantees safety, quality assurance and maximum efficiency. Our warehouse of spare parts minimises delay waiting for suppliers or imported parts – meaning little delay for clients. A key goal is client satisfaction. We’re here to help our customers by offering economical and efficient waste management solutions. We’re a trusted Contractor known for our reliability – we always deliver. We’re on time, every time. CEO Eric Davis has in-depth experience in recycling and mobile waste processing. Davis Earthmoving has demonstrated stability, whilst also being progressive in an ever-evolving industry.
Products and Services:
• Green Waste Recycling • Forest Mulching, Timber & Stump
Grinding • Land Clearing, Road Widening &
Forestry • Crushing & Concrete Recycling • Screening • Low Speed, High Speed, C&D
Shredding • Glass Recycling • Quality Recycled Landscaping Supplies • Plant & Equipment Hire • Bulk & Heavy Haulage
For hire:
• Low Speed Shredders; Komptech • Horizontal Grinders; Diamond Z,
Peterson • Picking Stations; Kiverco • Mobile Crushers; Rubblemaster, Metso • Soil & Trommel Screens; Pronar, Metso • Forestry Mulchers; FAE • Feller Bunchers; Tigercat • Excavators 1.8 to 46 tonne; CAT,
Komatsu • Dozers, Rollers, Compactors & Drotts • Wheel & Track Loaders
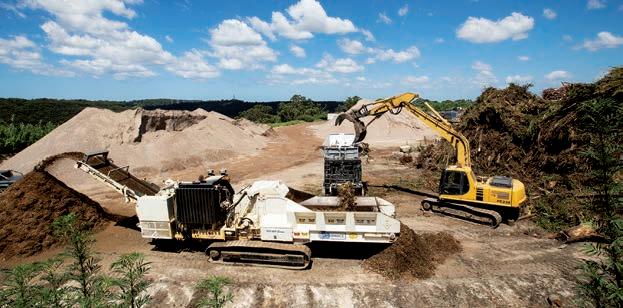
Core Capabilities:
Davis Earthmoving offers reliable, high-powered, mobile waste processing equipment for hire or contract in NSW. We deliver high-volume production to meet client’s varied needs and specifications. Our Low Speed Shredder processes heavy C&D, logs, palms, carpet, tires, mattresses. We have equipment available for forestry mulching, tree felling, subdivisions, road constructions, grubbing, firebreaks. Horizontal Grinders process green waste, C&D, timber, stumps, logs. Mobile and Trommel Screens process soil, timber, green waste. Our Crushers recycle concrete, brick, rock and glass. Our aim is to efficiently recover environmentally sustainable and quality recycled products for beneficial reuse in a circular economy.
Contact Details:
Davis Earthmoving & Quarrying Pty Ltd PO BOX 19 TERREY HILLS NSW 2084 Phone: (02) 9450 2288 Email: davisem@davisem.com.au Web: davisem.com.au
Komptech CEA
Company Overview:
Komptech CEA is the Australasian distributor of Komptech machinery and systems for the treatment and processing of solid waste and organics waste materials for recovery and recycling. Our product range includes over 30 different types of both mobile and stationary machines that cover all key processes in modern waste processing including: • Single-shaft and dual-shaft industrial shredders • Compost windrow turners for commercial operations • Star screen and trommel screen machines • Material separation equipment including windsifters, ballistic separators and stone contaminant separators • Stationary recycling system solutions including shredders, separators and screening machines
Brands:
• Rowan • Komptech
Core Capabilities:
With a specialized product portfolio that includes over thirty different types of machines covering all key processes in modern waste handling, a consultative guiding approach to solution development for customers, and full service aftersales support and parts, Komptech CEA has become a leading supplier to the recycling and waste processing industry.
Providing customer value is our focus as we strive to be the industry’s technological leader through continual innovation. Komptech CEA is dedicated to working with you to help you solve your waste problems and identify opportunities with comprehensive, detailed solutions driven by world-class technology.
Contact Details:
Sydney
6 Skyline Crescent Horningsea Park, NSW 2171 1300 352 378 www.komptechcea.com.au
Melbourne
109 Merola Way Campbellfield, VIC 3061 1300 352 378 www.komptechcea.com.au

Brisbane
103 Axis Place Larapinta, QLD 4110 1300 352 378 www.komptechcea.com.au
Adelaide
260 Cormack Rd Wingfield, SA 5013 1300 352 378 www.komptechcea.com.au 1300 352 378 www.komptechcea.com.au
Auckland
96 Gavin Street Mt Wellington 1060 0800 435 269 www.komptechcea.com.au
Key Contacts:
Craig Cosgrove
Product Manager 0417 320 082 c.cosgrove@cea.net.au
Simon Humphris
Product Manager 0478 196 263 s.humphris@cea.net.au
Hitachi Zosen Inova
Company Overview:
Hitachi Zosen Inova (HZI) is a global leader in energy from waste (EfW), anaerobic digestion (AD) and Powerto-Gas, acting as an engineering, procurement and construction (EPC) contractor delivering complete turnkey plants and system solutions for energy recovery from waste.
Since 2015, HZI Australia, a 100% subsidiary of HZI, is developing new projects in Australia, New Zealand, and the South Pacific. Its first project, the 300,000 tpy East Rockingham WtE is now in construction and will start commercial operation in Dec 2022.
Products/Services:
• Thermal treatment of residual waste, energy recovery, flue gas treatment, and residue recycling • Dry anaerobic digestion of food & green resources, renewable power production, biogas upgrading to biomethane and bio-CNG • Power-to-Gas for volatile electricity into renewable synthetic gas for a
carbon-neutral economy • Development, Design, Build,
Finance, Own, Operation &
Maintenance
Brands:
• Hitachi Zosen • Aquaroll, DYNOR, Kompogas, • HZI Etogas, HZI DryMining
Core Capabilities:
Energy from Waste, Renewable Gas, Project Development, EPC, O&M, Asset Management
Recent Projects/Installations:
DUBAI ENERGY FROM WASTE (EFW) – START OF OPERATIONS IN 2024 Warsan, Dubai, United Arab Emirates
The world’s largest EfW processing up to 1,89 mill tpy of non-recyclable municipal solid waste from the Dubai area and producing 171MW of electricity. To be designed, built and commissioned by a JV partnership between HZI and BESIX Group with a minimum of 30 years’ operation and inclusive of minority ownership. Visit https://www.hz-inova.com/projects/ dubai-uae/
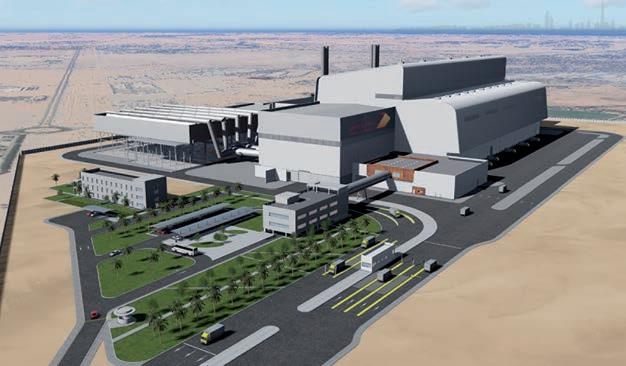
ZUFFENHAUSEN ANAEROBIC DIGESTION PLANT – START OF OPERATIONS IN 2023 Baden-Württemberg, Germany
A dry anaerobic digestion plant using HZI’s Kompogas® technology to process 35,000 tpy of source-separated organic waste from the Stuttgart urban area into biogas, high-grade liquid fertilizer and compost. The bulk of the biogas will be used at the manufacturing plant of a well-known automaker to produce electricity and heat for direct use on site. Visit https://www.hz-inova.com/ kompogas-for-the-future/
Contact Details:
Hitachi Zosen Inova Australia Pty Ltd
Level 17, 40 Mount Street North Sydney, NSW 2060 Phone: 02-8003 4110 Email: info@hz-inova.com Web site: www.inova.com
Key Contacts:
Dr Marc Stammbach
02 – 8003 4110 info@hz-inova.com
Komatsu Forest
Company Overview:
Komatsu Forest is one of the world’s largest manufacturers of forest machines. We are represented on six world continents by a network of dealers and our own sales companies.
Komatsu Forest’s head office is in Umeå, Sweden, and we have two manufacturing units, in Sweden and the USA. Our own sales companies are located in Sweden, Norway, Finland, Germany, Austria, France, United Kingdom, Russia, USA, Australia and Brazil, and our network of dealers represent us on all other important forestry markets.
Our extensive service organisation takes care of the machines, ensuring that they perform their best throughout their service lives. We have workshops throughout the world, service vehicles for quick assistance, in-house machine and methodology instructors to help maximise productivity, and support functions for everything related to our machines and services. increase productivity while simplifying the working day for you as a machine owner.
We combine all our services under our Customer Care concept. This is our promise that you will enjoy the benefits of Komatsu Forest’s investments in research, development, servicing, support, logistics and innovative services. These combined resources are at the very heart of Komatsu Forest’s offer.
Our goal is to make your working day as safe, problem-free and profitable as possible, no matter where in the world you operate. Let us show you that by choosing Komatsu, peace of mind and accessibility can become a natural part of your working day.
Brands
• Komatsu • Peterson • TimberPro
Core Capabilities:
close to service and maintenance when help is needed. Therefore, we have a market-wide network of highly trained service professionals that knows your Komatsu, Peterson & Timberpro machine in every detail. They are, in turn, in constant contact with the Komatsu Forest head office so your voice or needs are never more than a call away from our collective expertise. Furthermore, we are constantly developing new services that will help you in your everyday work.
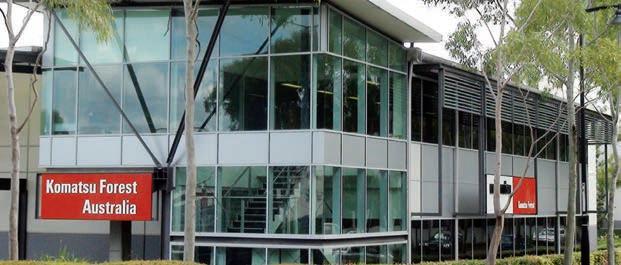
We offer:
• Workshops and field services throughout Australia & New Zealand • Well qualified personnel with expert knowledge of Komatsu & affiliated machines • Field Service that enables us to remain close to you and your
machine • Support and maintenance throughout your machine’s service life • Maintenance agreements with fixed maintenance prices and other benefits
Contact Details:
AUSTRALIA
Komatsu Forest Pty Ltd 4/11 Ave of Americas Newington, NSW 2127 T : +61 2 9647 3600 E : info.au@komatsuforest.com
NEW ZEALAND
Komatsu Forest Pty Ltd 15C Hyland Cres Rotorua, New Zealand M: John Kosar + 64 274 865 844 M: Paul Roche + 64 21 350 747
Merlo Group
Company Overview:
Merlo is an Italian-based industrial group that designs, manufactures and markets its products under the Merlo and Treemme brands, both synonymous with quality the world over, with a commitment to respecting the environment.
All the products in the Merlo range have the largest cabin and operator space available to the Australian market, which is characterised by innovation, technology and reliability. They are distinctive characteristics of the Merlo Group that have earned the trust of the world telehandler markets.
Since its origins, the Merlo Group has always had an international approach in terms of product and business; this global vision of the market today generates the export of more than 90% of production. Today the Merlo Group’s worldwide presence is guaranteed by a direct organisation of six branches (France, Germany, England, Spain, Poland and Australia), by a distribution network of over 50 importers and 800 dealers, offering widespread coverage in terms of sales, service and spare parts. The Merlo Group’s international approach continues to increase its global presence, guaranteeing proximity to customers and opening up new markets by introducing hightech products with superior safety standards.
The Merlo Group’s products are created from the deep experience gained in over 50 years of history; they satisfy every market and customer need.
AUSTRALIA
Products & Services:
The Merlo brand has always been synonymous with cuttingedge technology in the field of telehandlers, operating machines and telescopic boom tractors.
Core Capabilities:
Merlo’s advanced technology has become the driving force behind a development that has made it possible to look beyond daily business. Safety, comfort, performance are the key words. As a result, every machine rises the bar and sets a new standard in terms of design, power, care for man and the environment. This winning attitude translates into high integration into production processes, modern construction systems, process automation, revolutionary integrated electronic systems, in robotised processes and much more.
Our commitment to maintaining an ever-closer relationship with our customers is reflected in our ongoing training and updating of programmes, our technical support services, and the trusted relationship with our extended dealer network. The results of all this are compact machines, with ease of operation, that ensures the unrivalled operating features of, comfort, efficiency and above all, unparalleled safety. This is the strength of the Merlo product. Merlo Group Australia - TRUSTED
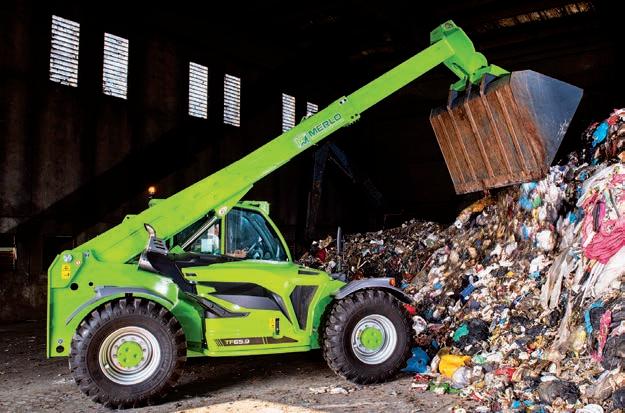
Contact Details:
Merlo Group Australia Pty Ltd
120-124 Toongabbie Rd, Girraween NSW 2145 Phone: 1300 657 325 Email: sales@merloaustralia.com.au Web: https://www.merlo.com
STEINERT
Company Overview:
STEINERT is a manufacturer of superior magnetic separation and state-ofthe-art sensor sorting equipment. Headquartered in Cologne, Germany with subsidiaries in Australia, USA, Brazil, STEINERT supplies the waste, metal recycling and mining industry globally. With over 130 years of history STEINERT is at the forefront of technology and innovation with a focus on quality, reliability and continuous research.
STEINERT’s presence in Australia encompasses a manufacturing facility in Melbourne, Victoria where the Australian designed and made magnets originate. STEINERT’s Test Facility in Perth, Western Australia provides customers with the opportunity to test small and large samples under conditions that very closely match real life scenarios. Customers benefit from the very latest findings and technological advancements in a tried and tested environment, utilising the latest STEINERT sensor-based combination sorting solutions.
STEINERT’s Service Technicians are based on both the east coast and west coast of Australia and have the capability to support your service requirements around the country, both on-site and remotely.
This strong presence ensures best support of the magnetic and sensor sorting equipment for the customers in Australia.
Products & Services:
• Overhead suspension magnets, electric and permanent • Magnetic drums, electric and permanent • Eddy current separators • Near Infrared sorters • Optical sorters • Induction sensor sorters • X-ray transmission/fluorescence sensor sorters • Combination sensor sorters • Service & maintenance
Brands:
• STEINERT MAGV/MAGX suspension electromagnet • STEINERT MAGP permanent suspension magnet • STEINERT MTE electric drum • STEINERT EddyC eddy current separator • STEINERT ISS induction sensor sorting system • STEINERT KSS combination sensor sorting system • UniSort PR EVO 5.0 NIR sensor sorting system
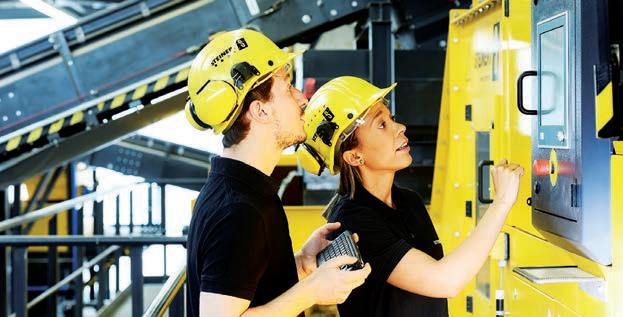
Core Capabilities:
We support customers from the project design stage with application knowledge, material testing in our test facilities, process consultation, supply of equipment, on-site commissioning to continuous service support, maintenance and repairs from our Australian team.
Our manufacturing facility in Melbourne enables us to hold critical spare parts for our equipment and perform full repairs and refurbishments in local response times. Together with our team of service technicians we are able to provide a high standard of after-care for our equipment.
Contact Details:
STEINERT Australia Pty Ltd
14 Longstaff Road, Bayswater VIC 3153 P: +61 3 8720 0800 E: sales@steinert.com.au W: www.steinert.com.au
Key Contacts:
Applied Machinery
Contact Details:
55-61 Nissan Drive Dandenong VIC 3175 Phone: 03 9706 8066 Email: sales@appliedmachinery.com.au Web: www.appliedmachinery.com.au
Company Overview:
Applied Machinery is one of Australia’s largest suppliers of quality recycling machinery. Over 30 years industry experience enables us to deliver turnkey solutions for all manner of recycling applications across Australia.
Products and Services:
• Shredders and granulators • Plastic washing, tyre, and e-waste recycling plants • Repelletising systems/screen changers • Polystyrene recycling machines
Brands:
• Genox • Polystar • Fimic • Greenmax
Core Capabilities:
Applied Machinery has the capability to service the smallest single machine requirement, through to the largest of multi-site, staged installations and complete recycling line, turn-key projects. We supply some of Australia’s largest recycling organisations. A wide range of shredders and granulators are always in stock for quick delivery.
Recent Projects/Installations:
PORT PLASTICS Port Macquarie
Polystar Repelletising system and Genox large format shredder to drive recycling operations in the Port Macquarie region and reduce the need for transport of recyclables to metropolitan centres.
Australasian Specialty Coatings
that allows for bespoke designs for your particular needs.
Contact Details:
ASC Head Office
1/14 Chicago Avenue Blacktown, NSW 2148 Phone: 02 8840 8888 Email: enquiries@acoatings.com.au Web: http://ascoatings.com.au
Company Overview:
ASC is a team of experienced coating and flooring professionals. We specialise in repairing and coating concrete and steel surfaces in harsh environments – waste handling, tipping sheds, chemical storage and high traffic surfaces.
We are fully certified to ISO 9001, ISO 14001, and AS 4801 Standards.
When you call in ASC you get a professional, reliable team dedicated to solving your problems and delivering the best outcome, on time. We have a solutions-oriented approach
Products/Services:
• Tipping Shed Floor Resurfacing • Chemical Bund Coating & Lining • Concrete Repair & Remediation • Corrosion Prevention Coatings • High Traffic Surfaces • Leachate Resistant Materials • High Grip & Anti-Slip Coatings • Waterproof Membranes • Tank Lining • Acid Resistant Coatings • Expansion Joint Rebuilding & Sealing • Water Treatment Plant Coatings
Recent Projects/Installations:
TIPPING SHED FLOOR RESURFACING Banksmeadow, NSW
Remediation of Eroded Concrete Slab 1500m² Leachate-Resistant Floor Surface
CHEMICAL STORAGE AND PUMPING BUND Lidcombe, NSW
Acid & Chemical Resistant Bund Re-lining Full Remediation of Bund Internal Surfaces
Company Overview:
Diverseco
• Truck wheel washes for EPA and road safety compliance. • Automated waste sortation systems: comprehensive and completely automated robotic sortation systems for MRFs.
As one of Australia’s leading measurement and automation solutions providers, we at Diverseco pride ourselves on the sheer scope of our problem-solving expertise and supply of industry leading innovative technologies. We are heavily involved across a wide range of industries, with a comprehensive solutions portfolio specific for the waste management industry that includes both driver-specific solutions and robotic automation solutions for material recovery facilities.
Products and Services: Brands:
• Waste Robotics • BinWeigh
Core Capabilities:
At Diverseco, our core capabilities reside in our ongoing ability to meet and exceed customer requirements through our extensive problem-solving resources: we are ideal partners for any organisation looking to turn their operational problems into new, profitable capabilities.
• Waste vehicle on-board payload optimisation and overload monitoring (Chain of Responsibility and legal-fortrade operations). • Weighbridges and portable truck scales for accurate vehicle weighing and accountability.
Contact Details:
3309 Logan Road Underwood, QLD, 4119 M: 1300 069 970 E: onboardsolutions@diverseco.com.au W: diverseco.com.au
Contact Details:
Hyva Pacific
A fleet of service vehicles offers on-site solutions for all hydraulic, fabrication, electrical, air-conditioning and engineering requirements.
Products and Services:
72 Glenwood Drive Thornton, NSW, 2322 Phone: 02 4966 3777 Email: hyvapacific@hyva.com Web: www.hyva.com
Company Overview:
Hyva Pacific is a leading provider of innovative and highly efficient transport solutions for the commercial vehicle and environmental service industries. Its products are used worldwide across a range of sectors including transport, construction, mining, materials handling and environmental services providers.
HSR Southern Cross is the HYVA distributor for NSW and the exclusive Australian HYVA PRESS Waste Handling Equipment distributor. HSRSX is strategically located in Western Sydney. • Waste Handling Equipment (Rear loaders / Compactors) • Hookloaders • Skiploaders • Vehicle Loading Cranes
Core Capabilities:
Hyva /HSRSX is the ‘one stop shop’ for the commercial vehicle and waste handling industry, providing a wide range of high-quality equipment including installation, engineering, service and repair in our workshops or onsite.
Contact Details:
35 Holbeche Rd, Arndell Park NSW 2148 Phone: 02 9725 3347 Email: admin@hsrsx.com.au Web: www.hsrsx.com.au
ResourceCo

Contact Details:
ResourceCo Head Office
Level 1, 162 Fullarton Road Rose Park, SA 5067 Phone: (08) 8406 0300 Email: enquiries@resourceco.com.au Web: www.resourceco.com.au
Company Overview:
ResourceCo (RC) is a global leader in the recovery and re-manufacture of primary resources, extracting maximum value from materials otherwise destined for landfill.
Recent Projects/Installations:
ESKINE PARK PLANT
Operations commenced at Tyrecycle’s (RC’s tyre recycling division) new multi-million-dollar plant at Erskine Park in Sydney in June 2021, producing in excess of 9000 tonnes of rubber crumb for the construction industry and providing a local circular economy solution to rubber waste. Additional new plants are also planned for Perth and the Pilbara in WA later this year.
Products and Services:
• C&D & C&I Recycling • Disposal, Treatment & Management of
Contaminated Soils • Renewable Energy & Alternative Fuels • Tyre & Waste Rubber Recycling • Recycled Construction Material
Brands:
• ResourceCo Pty Ltd • ResourceCo Material Solutions • Southern Waste ResourceCo • Cleanaway-ResourceCo • SUEZ-ResourceCo • ResourceCo Property • Tyrecycle Pty Ltd • Kariyarra Tyrecycle
Spartel Pty Ltd
FABCOM® Organics Under Control©
www.FAB-COM.com.au
Contact Details:
aspects organic waste processing from waste generation to soil beneficiation products, technology, process data processing and control, odour prevention and control
Harrie - 0414 37 66 99 E: info@spartel.com.au W: www.FAB-COM.com.au
Company Overview:
Spartel Pty Ltd was founded in 1995 by Dr Harrie Hofstede, specialist waste management scientist in waste composting and pollution control. The company has a consulting arm, Hofstede & Associates, and waste technology R&D programme under the umbrella. The R&D has resulted in six patents in international markets. We have designed and developed two main large-scale composting systems under the FABCOM® Brand. FABCOM® Tunnels and the FABCOM® MAF system.
Core Capabilities:
The overall core capability is all
Products and Services:
• FABCOM® Tunnel compost plants • FABCOM® MAF composting system • Wireless data transmission and processing over a 2 km radius • Aeration controlled by process data • Remote access process control • Design and construct of compost plants • Development and optimisation of compost process and products • ODOROV™ effective odour control agent for organic waste • High nitrogen composts (4% N)
Recent Projects/Installations: :
FABCOM® MAF SUEZ Newcastle
Raymond Terrace NSW Dedicated FABCOM® MAF aeration system for post Bedminster compost maturation & drying; Capacity 10,000 tpa
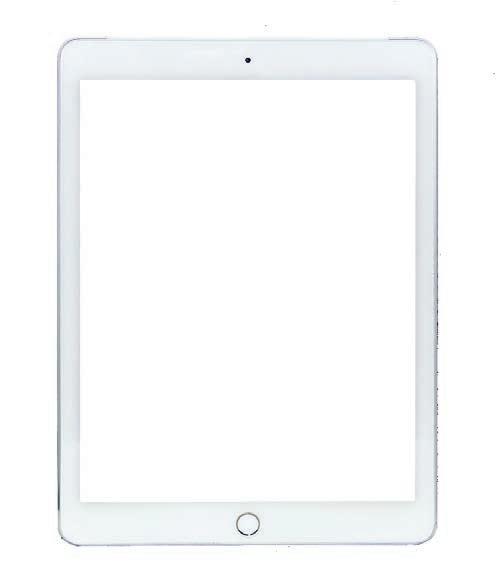
NOW AVAILABLE TO VIEW ON
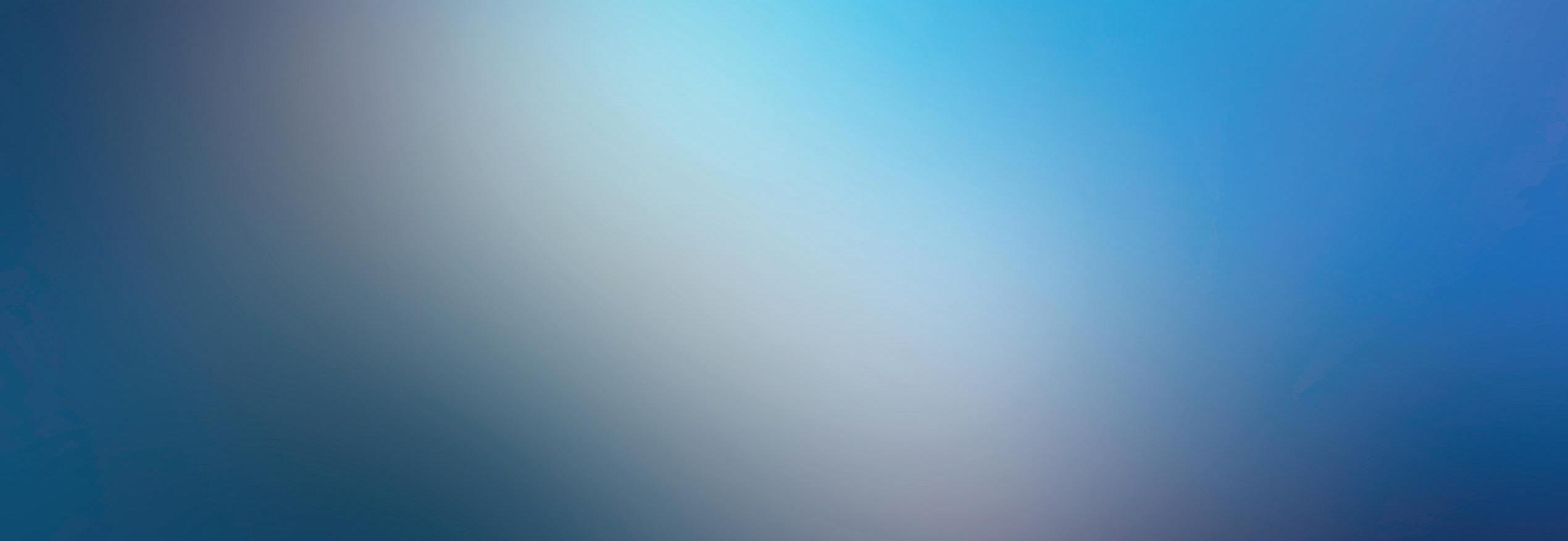
www.insidewaste.com.au
ISSUE 101 | APR/MAY 2021
ISSUE 100 | FEB/MAR 2021 INSIDE
www.insidewaste.com.au
INSIDE 26 AWRE Conference 40 Wastewater 43 Young Professional 30 Landfill 37 What circular economy?42 Truck feature
ON DECEMBER 8, 2020, the Recycling and Waste Reduction Bill was passed in the Senate without amendment. Despite a senate inquiry into the Bill and attempts by the Greens and Labor, the amendments to the Bill that would address plastic pollution and support the recycling sector did not pass. This has resulted in concern within the WARR industry that the government’s commitment to the massive problem of plastic pollution remains fragile despite its assurances and organisation of the first National Plastic Summit in Canberra, prior to COVID-19.Much of the frustration around the failure of the amendment has been focused on the continual reliance on the packaging industry to self-regulate. Despite this industry’s best efforts to address this issue (Inside Waste covered the Australian Institute of Packaging’s Virtual Conference and the APCO initiatives in depth during 2020), the needle on the decrease of plastic waste fails to move by any significant degree. WMRR CEO, Gayle Sloan is one WARR leader who has consistently pointed to the ineffectiveness of the efforts by the packaging industry to manage the issue. She told Inside Waste that the strong support for the amendment to the Bill was an indication of a desire within the Australian community to deal with the packaging problem.“While it is disappointing that the amendment fell through on a single vote, it is heartening to see growing consensus that we need to do more to tackle the packaging that we consume and dispose of. “What we have seen to-date is strong community support for action. Real action to be taken to tackle packaging and create jobs in Australia. “The message is clear,” Sloan said. “The business-as-usual approach is not acceptable anymore. Australians deserve more than a continuation of a voluntary, packaging industry-led scheme that has made little, if any, progress.” Senate didn’t understand Sloan pointed to the “real opportunities to close the loop domestically”. She said that this could be achieved by building local businesses, driving new industries, job creation, and environmental protection. “It is disappointing that some in the Senate did not understand that. However, it is extremely encouraging to see the level of support for change.” However, Sloan is not without suggestions on how to move forward. “With the export bans coming in shortly, and the need to meet national targets, WMRR is urging all governments to think about how we can tackle packaging with the limited and voluntary tools that we’ve been given. “WMRR proposes that it’s time to set up a genuinely independent body truly representative of all stakeholders in the supply chain, including but not limited to the packaging industry, to find productive ways in which we can work together to genuinely close the loop on packaging in Australia by using Australian recycled products. “This is key if we are serious about making real progress while being hamstrung by the lack of regulation on the packaging industry,” she added. (Continued on page 22)
PP: 100024538 ISSN 1837-5618
How Indonesia plans to be plastic-free by Plastic problem is not business as usual All industry stakeholders need to work together to genuinely close the loop on packaging in Australia by using Australian recycled products. WHILE INDONESIA is one of the biggest contributors to the plastic pollution in the ocean, this situation became exacerbated after China banned waste imports and the country emerged as a major portal for global plastic waste. Now its landfills are running out of space with Indonesia’s largest landfill, Bantar Gebang (the only one serving Jakarta) predicted to run out of space this year, according to government officials.Coordinating Minister for Maritime Affairs and Investment, Coordinating Ministry for Maritime Affairs of Indonesia Luhut B. Pandjaitan told the World Economic Forum, “In our cities, our waterways and our coastlines, the accumulation of toxic plastic waste is harming our food systems and the health of our people. “Our booming fishing industry, the second-largest in the world, is under threat from rising levels of marine plastic debris. By 2025, the amount of plastic waste leaking into our oceans could increase to 800,000 tonnes – if no action is taken,” he said. Despite this gloomy scenario, the country has developed a strategy which was presented at the World Economic Forum’s Annual Meeting in Davos last year. Here the world took a first look at Indonesia’s plan, with a radical target to cut marine plastic debris by 70 per cent within the next five years. (Continued on page 24) 2040
Think your waste is unshreddable? Think again! Meet the XR... Low wear. Low maintenance. Low running costs. Maximum performance. Request a free waste audit: info@focusenviro.com.au
THE leading report on waste management and recycling data in Australia shows that Australians are reducing their waste and increasing their recycling.Blue Environment’s National Waste Report 2020, commissioned by the Federal Government’s Department of Agriculture, Waste and the Environment, was released in December last year. The report is the authoritative compilation of national data on waste and resource recovery and the mechanism for measuring progress against national waste policy targets. Issued every two years, the 2020 edition focuses on the status of waste and recycling in 2018-19, with data analysed on a per capita basis as well as on state and territory levels. Findings cover waste generation, source streams, material categories and fates, together with trends measured back to 2006. While the data precedes the significant investments in recycling and resource recovery the Federal Government has made since the 2019 election, its revised 2016-17 data set (first published in the National Waste
Report 2018) will be used as baseline data to measure Australia’s progress against the National Waste Policy Action Plan’s 2030 targets. “The release of the leading report on waste management and recycling data in Australia, shows that Australians are reducing their waste and increasing their recycling,” Assistant Waste Reduction and Environmental Management Minister Trevor Evans said.“This is a great outcome. We can all be proud that our efforts are paying off, to take care of our own waste and to do the right thing by sorting our recycling and diverting more waste away from landfill.” Evans highlighted that Australia created 3.3 per cent less waste in 2018-19 compared to 200607, the foundation year of the national data set. “In effect, we each produced waste that weighed the same as 40 full kegs of beer and we each sent the equivalent weight of 24 full kegs to be recycled,” he said. “However, our growing population means that the overall amount of
waste Australia is generating continues to increase, up five million tonnes since 2016-17.“We need to continue to work hard to reduce the amount of waste we create, and to recycle more of it, if we are to achieve Australia’s ambitious national target of recovering 80 per cent of our waste by 2030.”Evans explained that this was the driver behind “unprecedented” action by the government to turbocharge the waste and recycling industries, so that waste is treated as a resource which can be recycled and remanufactured into valuable new products. He said that this protects the environment, creates jobs and keeps waste out of landfill. “Our billion-dollar investment in new recycling infrastructure is changing the face of the waste and recycling industries in Australia,” Evans said. “We are also the first country in the world to ban the export of its unprocessed waste plastic, paper, glass and tyres overseas thanks to our new national recycling legislation.” (Continued on page 22)
DURING the recent Australian Circular Economy Conference (ACEC), one of the webinars delved into Food and the Circular Economy in Australia and China. One of the speakers was Alana Mann, associated professor for the Faculty of Arts and Social Sciences (FASS) at the University of Sydney. Mann noted that one outcome of the COVID-19 pandemic was that a lot of countries, like China and Australia, were taking a fresh look at how their food systems operated, both in terms of supply chain and food wastage. Mann said it was pleasing to see how both countries, and the world at large, had risen to the challenge of feeding the world’s population during a trying time, but it had also exposed some of the intrinsic weaknesses within some of the systems. “Circular economies and other models of food provisioning including community supported agriculture and cooperatives, are all coming to the fore,” she said. “China is a leader in these areas along with recycling waste and the development of smart technologies for ecommerce. How we connect with consumers and users ensures the supply chains to address food insecurity and also manage issues around waste are addressed, which is an important piece of the circular economy model.” (Continued on page 24) Waste needs to be treated as a resource – report
WEBINAR: Profitable one-step alternative fuel production 13th May 2021 10:00 | Register for your FREE place today: focusenviro.com.au/event
Glass achieved a recycling rate of 59 per cent. Just-in-time model not working
Taking a load off – you can’t manage what you can’t measure

By Inside Waste
MAKING sure loads are the correct weight is key when collecting waste and taking it to landfills. Not only because landfills charge levies by weight, but because overloaded trucks are a danger to other road users and increase wear and tear on roadways and impair vehicle safety.
Stuart Knight is the product manager for onboard weighing systems for Diverseco, a company that specialises in onboard vehicle weighing systems: from overload suspension systems to high accuracy underbody loadcells systems and trade-approved, charge-byweight systems.
He has said that over the past few years he has seen charge-by-weight becoming dominant in the commercial waste sector, which is why Diverseco has invested in products that can help companies make sure they are complying with standards and legislation.
“We introduced the first tradeapproved “BinWeigh” system into Australia, which utilises Swiss technology and measures the weight of each loaded bin, providing net bin weights,” he said. “This information maximises charge-by-weight operations with highly accurate weight data and is appropriate for most front, rear, and side-lift loaders.”
Tim Francis is Diverseco’s general manager for automation. He said it is also about making sure efficiencies are being met.
“It would be fair to say of the onboard product, it’s not so specific to this segment within the waste sector but rather the waste collection component of it,” he said. “It is an advantageous tool to those companies that hold that contracts for waste collection so that they can monitor efficiencies. They can monitor load runs to make sure they have maximum payload, but not too much - you don’t want to be running around with a half-empty truck. That is not good business sense. The scales are great, but ultimately it is the data that these systems yield that is empowering for the owner.
Importantly, said Francis, the systems come with a crucial feature in that it helps clients achieve compliance under chain of responsibility legislation.
“When you think about it, you’re going around in a truck and you’re picking up waste bins, and you’re throwing the content into the back of your truck,” he said. “If you don’t weigh that, you have no idea how heavy your truck is becoming or how heavy it currently is. It could be full of milk bottles, in which case it could be light, or it could be full of house bricks, in which case you are probably overloaded.”
Looking ahead with automation, Francis sees a big future for the technology in the industry. He thinks it will be a mixture of robotics and AI, however, there is still a lot of work to be carried out with the technology.
“Robotic sortation will be entering more into industry as the artificial intelligence technology improves. To be fair, it is still very much in the developmental phase at the moment,” he said. “Most people in that space are looking for a partner where they grow that technology to a space where it is commercially viable because in reality there can be a significant ramp-up and learning time for the artificial
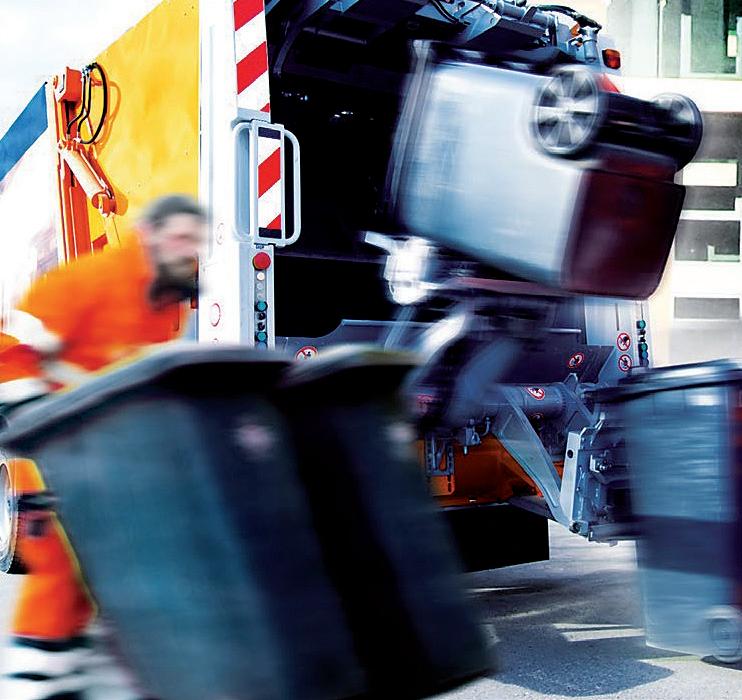
intelligence to become effective.
Waste is one of the most unstructured environments you will find; you never know what the next piece of gear is coming down the waste line on the conveyor. That is quite the puzzle for artificial intelligence to cope with. When you start looking at general waste or recyclables, I’m not sure how many robots you would need and I’m not sure how big the computer would be in order to handle the AI required to deal with all those things concurrently in the one environment”
At the foundation of Francis’ point is data. Like a lot of industries – especially manufacturing and other industries – data is not only important in terms of the information it provides, but it can start to influence the bottom line in terms of identifying inefficiencies to be rectified. Waste is no different.
“From the data perspective, people are using it for payment, which is absolutely crucial and paramount for the business,” he said. “Generally speaking, waste can be measured from a cubic volume perspective as well as from weight, and these measurements are often linked to customer, levy, and other payments. The method of measurement is often mandated by government or regulatory authorities. The higher the volume, the greater the likelihood that a legal-for-trade weighing instrument will be required for measurement.
“Modern day compliance standards, particularly when considering the EPA, requires record-keeping and traceability throughout the life cycle of the item, from cradle to grave – from point of manufacture to point of disposal. Weighing devices can be beneficial in automating and systemising the collection of this data to assist in meeting those compliance requirements.“
While people of a certain age remember how things used to be – no waste levies to tip your waste at the local landfill (it was covered by council rates), and there were incinerators in our back yard – the waste landscape has changed significantly since then, according to Francis.
“One of the problems with waste in the past was that there was not enough money in it for people to do the right thing. Now there is. That situation has changed over time. As the prosperity has improved, so too have the penalties for not meeting requirements,” he said. “The governments and waste collectors themselves are really gearing up to take it to the next level and identifying the waste source, and fairly soon we’ll start to see the introduction of RFID tags on domestic bins. When a company comes and picks up your bin and throws it into the back of the truck, they will know that it is yours. They’ll have cameras on there. They’ll record what waste was yours, and how much of it was it was yours. Even down to what was in the bin.”
Knight said the company is working closely with councils and is seeing many changes within the industry when it comes to new technologies.
“We work closely alongside vehicle suppliers and body builders for a variety of applications, providing engineering support, with our national service team providing support for end users in the field. Chain of responsibility laws have drastically increased the need for overload protection systems, with major increases in uptake among local councils operating with small and large tippers, which can be easily overloaded.” iw
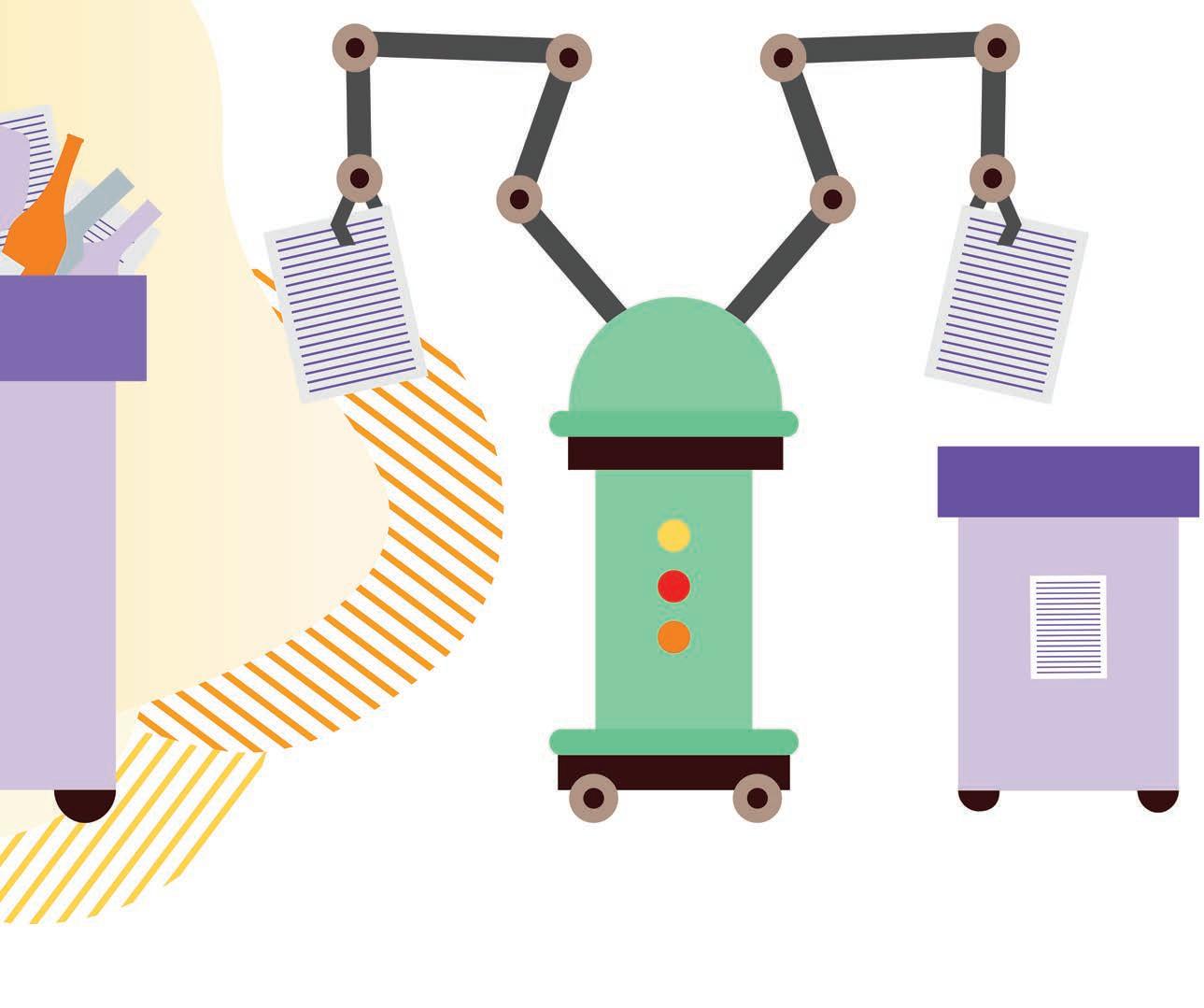
In the future, robotics and AI will be used in the industry, but there is still a lot of work to be done.
By Inside Waste

THE KATflow 200 is a portable instrument that is a lightweight flowmeter that is easy to use and can be operated one-handed, which makes it a suitable tool for use in confined spaces or when working at height. The KATflow 200 flowmeter offers measurement performance normally associated with more complex devices and is complemented by the quality and robustness of the Katronic transducers.
The hand-held KATflow 200 has an array of features that make this versatile instrument unique for a meter of its size.
It is available with a choice of robust stainless-steel transducers to cover many temperature ranges between -30 °C to +250 °C and provides an autonomy of 24 hours using the convenience of NiMH AA batteries.
It can be supplied with three different transport case options to suit customer requirements, has a large internatal data logger and an optional wall thickness gauge.
The KATflow 200 has many application is various industries, building services, pharmaceuticals, food production, water and waste water, power generation and general industries. iw
The flowmeter is suitable for confined spaces.
Macpresse MAC/2 baler series
By Inside Waste
FOLLOWING the launch of its MAC/1 baling press machines series in 2001, Macpresse launched its new MAC/2 multi-material baler series in 2016.
The MAC/2 supersedes the previous MAC/1 baler’s performance with better efficiency, as well as improved volume reduction to optimise waste transport and management costs. The new series is designed for recycling, biomass and refuse derived fuels industries.
Jakob Becker, is a German company the specialises in the secondary raw materials treatment, and at the time had been a Macpresse customer for four years.
A pioneer in waste treatment that, with more than 100 years of business experience, ranks as one of the first German companies of the sector in terms of turnover.
In 2012, Jakob Becker discovered Macpresse and has been using the equipment since that time.
First, it purchased a MAC 111/1 baling press machine, then a MAC 107/1 and after that a MAC 110/1.
In 2016, Jakob Becker, chose a baling press machine from the latest MAC/2 series
“MAC baling press machines have a simple design, they are strong, easy to manage and reliable,” said Thomas Becker, owner and CEO of Jakob Becker. “Over four years of business experience, management costs have always been low, and machines have never stopped working. When Macpresse presented its new /2 series, we had no doubts and chose a MAC 110/2 with a conveyor belt for our most important plant.”
Jakob Becker’s faith is repaid by a top-quality machine, designed to meet the requirements of a developing market.
“You just need to replace the blades to bale different materials with the same machine: plastic, paper, biomass and refuse derived fuel (RDF),” said Becker.
“This allows us to optimise bale processing and makes the new baling press machines ideal to treat different types of waste.”
MAC/2 balers have large load dimensions to assist entry of very voluminous materials.
Another feature is the XL channel: longer extrusion channel (+1.5 m) for better bale density.
Macpresse has always designed solutions able to reduce management, energy and transport costs.
The new series was designed to further enhance these feature with: • Volume optimisation due to bale format – the bale format obtained with the MAC/2 baling press machines makes the best use of space in the ordinary means of transport, such as trucks, thus reducing transport and storage costs. • Easy maintenance – the baling press machines of the new series are safer and easier to clean for operators. • More efficient tying system – the
MAC/2 baling press machine is equipped with a new and highefficiency electromechanical tying system that allows to reach +50% tying speed (cycle) and to tie bales both with plastic and iron wire. • Reduced energy costs – the cutting system has been redesigned for better bale integrity and lower energy consumption. Also, the hydraulic system has been renewed and is equipped with a highefficiency IE3 motor allowing a 30 per cent increase in energy savings as compared to traditional motors • Reduced labour costs – the new baling press machine presents higher levels of automation than the previous series, therefore requiring fewer operators to manage and service the baler
“MAC/2 is the result of 15 years of dialogue, research and collaboration among Macpresse, its customers and international agents,” said Giuliano Scotuzzi, Macpresse export sales manager,
“Our work was aimed at a steady improvement in order to meet the needs of a dramatically changing market.
“The result is a series with even more performance than the previous version and 10 per cent stronger.”
The MAC/2 series comes in three models specifically conceived to meet the constantly changing waste treatment market demands.
Furthermore, MAC 107/2 is designed for companies pursuing medium production while simultaneously striving for high production standards at a low cost.
The new series is suitable for recycling, biomass and refuse derived fuels industries because, using the same baling press, you can bale everything. iw
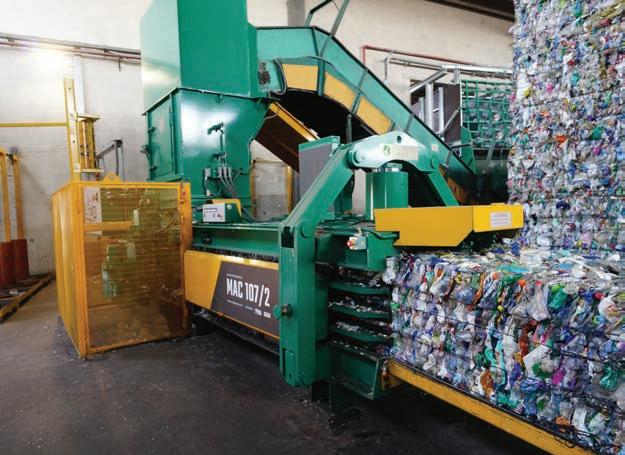
Shocking introduction leads to great career choice
AS with a lot of people, having a job in the waste industry wasn’t originally in Maya Deacock’s plans when setting out her career path. Graduating with a Bachelor of Science (Hons) degree from the University of New South Wales, Deacock said that even though as a kid she had an ecological bent, the waste industry wasn’t really on her radar.
Like a lot of young graduates, once university was finished, Deacock went over to the UK for a couple of years. When she arrived back in the country she caught up with a friend who was working at waste management specialist consulting company, MRA Consulting. After a three-month internship, she had a full time job and hasn’t looked back.
“I had never really thought about working in the waste industry to be honest, apart from putting my bins out on the street,” she said. “My grandfather was very big into conservation, so I was always leaning towards that. Before I reconnected with my friend, I was applying for ecology-type scientific roles all across Sydney. When I ran into him he said, ‘we have a waste audit coming up, if you’re interested, you are welcome to come along and try your hand’.
“It was a very shocking introduction into waste because it was pretty gross. You are rummaging through tonnes of rubbish, and while it’s not very nice it certainly is an eye opener as to what people are throwing out. It is amazing the number of things that end up in a recycling bin that shouldn’t be there. Before doing that I had never really thought about what was in my bin. I started working for MRA and I loved it. MRA are committed to a more sustainable economy and that sits well with my values.”
Part of her job is with the planning team, who help developers, landowners, and lease holders to get the relevant approvals they need to move forward on a project. This is particularly important when it comes to waste management plans – whereby the team assists with waste strategies and planning for a building, as well as help them get the best outcome in terms of waste management and sustainability. It is a fulfilling job.
“I like that I can help out people in a concrete way,” she said. “You can see the impact you are having on people. You drive down the street and you see one of the developments you worked on a DA for, and you know exactly what their waste strategy is like, such as getting everyone up to date with Green Star and all these industry standards. Even helping councils with their development control plans is an interesting aspect of the job. It is basically bringing everyone up to this great standard.”
Deacock finds that councils are generally onside when it comes to making the best of the environment. She said that they especially hold themselves to a high standard when it comes to making sure compliance is being adhered to by the various stakeholders. However, there is always room for improvement, especially when it comes to legislation and policy clarity.
“Councils always have that attitude of looking forward – ‘what is the next big environmental standard that we can reach?’,” she said. “It is important to have clear wording around policy to ensure there is no confusion about things.
“For example, we were having this conversation in the office about the energy-from-waste policy and what does and doesn’t apply and how some of it seems ambiguous. State governments need to be much clearer about what they want from councils and residents in terms of creating a sustainable or circular economy.”
On the other end of the spectrum there are people – such as some developers – without even being prompted, are trying to find the best environmental outcomes for their sites. Gone are the days of developers looking for the easiest and cheapest way to get from point A to point B on a project.
“You see it all in this line of work. For the most part, everyone is generally very compliant. They might even have their own internal standards. ESD (Environmentally Sustainable Development) is very big, and it is growing. Especially as climate change reports are coming out and it is getting a lot more focus,” said Deacock.
Does Deacock find it a fulfilling career considering she never really thought about it until that fateful runin with a friend?
“Absolutely,” she said. “I fell into waste by chance, but I think I will be definitely staying in it as a career. I don’t see it going anywhere in terms of this industry declining or petering out. It is an essential service. Even five, 10, 15 years down the track there are going to be continual challenges coming up.”
Any advice for those that are thinking of coming into the industry? Deacock recommends getting an internship first, like she did. Doing so will give a person an excellent perspective on how the industry works. She also believes that an important part of starting out is sitting back and listening to what is being said.
“Go to as many meetings as you can and sit there and take notes,” said Deacock. “I was very lucky to attend a very early business development meeting with my boss when I was still an intern. And we are still working with that client three years later. I came into the industry with a blank slate and didn’t know anything about waste. I had the environmental background but that was it. As well as attending as many meetings as you can, go to online seminars and listen to what is being said. Don’t be afraid to ask questions. There is no such thing as a silly question, and nobody will think any less of you for asking one.
“Also, try out things. For example, I didn’t know about financial modelling before starting at MRA and you get chucked in the deep end – writing business cases and things like that. In a small company you get to work on many diverse different projects. I’ve flown to Alice Springs to help them start up a composting program. You get to put your hand up and say, ‘I’m interested, can I help out, and what can I do?’
“There is a lot to know. I am now getting to the stage where I am feeling confident about my background knowledge in waste, but it takes time.” iw
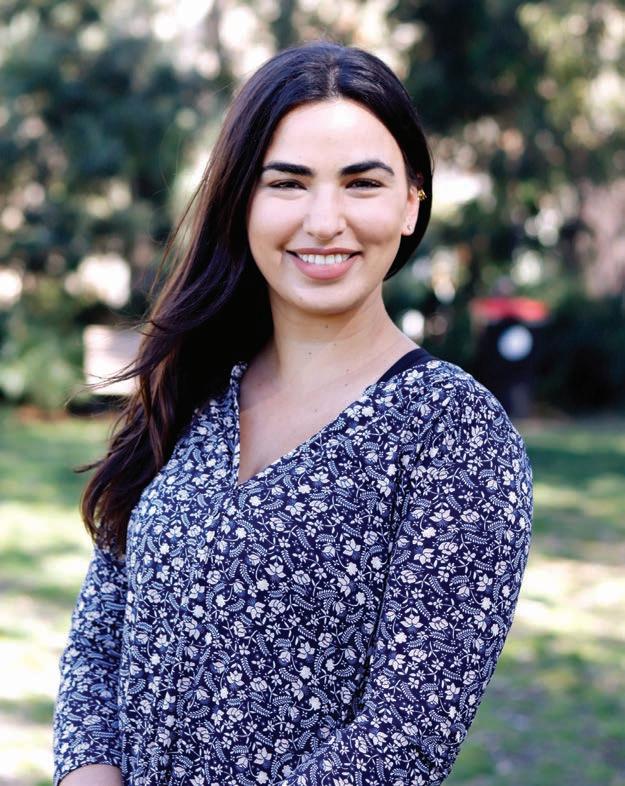
Deacock said there needs to be more clarity around what state governments want from local councils..
Hammel RED GIANT VB950DK
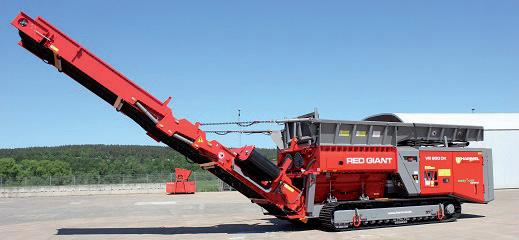
Company: Hammel Recyclingtechnik (CSS Equipment) Product name: VB Primary Shredder Speed (slow/high): Twin Shaft – Slow Speed Throughput: 200tph+ Suitable material: All Waste Types Drive type: Diesel or Electric No. shafts/speed: Twin Shaft/Slow Speed up to 40rpm Hopper Size: Up to 16 cubic metres Unit Dimensions: TBC Weight (tonnes): Up to 66 tonnes No. of units in range: 6 Models Base price: $250,000 + GST For more info: www.cssequipment.com.au or 1800 644 978
Cemec Technologies Pty Ltd Ecostar Hexact Screens
Company: Ecostar (CSS Equipment) Product name: Hextra Model Unit dimensions: 4 to 7 Metres long. Weight: 17 - 22 tonnes on crawler tracks Motor: Diesel/Electric
Screens material this size:
Various (double or triple fractions) Screen type: Dynamic (Hardox Discs) Designed for (material): All Waste Materials Throughput: Up to 200tph+ Base price: Contact CSS Equipment For more info: www. cssequipment.com.au or 1800 644 978

Macpresse Baler 108/2
Unit Dimensions:
14385 mm x 5900 mm x 3722 mm Weight: 4045,000 kg Drive Type: Main Motors Power Motor: 2 x 75kw
Rotor diameter/ lengths/speed:
170 tonne cutting and thrust power
Speed (slow/
high): 2 x 100 HP
Suitable material:
PET, OCC, RDF, Mix Paper No. of units in range: 2 Throughput: PET 10t/h, OCC 18t/h, RDF 33t/h, Mix Paper 30t/h Designed for (material): Baling PET, OCC, RDF, Mix Paper Price: POA More: www.cemactech.com, 03 84006066 or info@cemactech.com

HYVA
CSS Equipment EHSR RC0914 Hard Waste Rear Loading Compactor

Company: HSR Southern Cross
Model name: HSR RC0914 Hard
Waste Rear Loading Compactor. Unit Dimensions: 4,818mm Long, 2,245mm Wide, 1,951mm Heigh (above chassis) Weight: 4,520kg Drive Type: Hydraulicly Driven via PTO Motor: N/A Rotor diameter/lengths/speed: N/A Speed (slow/high): Compaction Cycle Time 20 Seconds Suitable material: All Domestic and Commercial Waste Streams, Hard Waste Clean-up. No. of units in range: 6 Throughput: N/A Finished product size: 24m3 Options/Extras: Available upon request Price: TBA More: HSR RC0914 Hard Waste Specification Body with 14m³ capacity body, plus tailgate, with upgraded sweep and packer panels and HARDOX 450 lined hopper bowl and side walls. These units are by far the most heavy-duty rear load compaction units on the market. The overall Tailgate volume is 2.14m³ with a hopper swept volume of 1.5m³ water Level capacity. The HSR strength configurations will achieve both domestic collections, as well as handle the most destructive curb side collections of waste with ease. Inspection of our Sydney (Arndell Park) manufacturing and installation facility is offered at any time convenient to inspect how these truly unique compaction units are manufactured. Price: From $220,000 More: www.hsrsx.com.au, Ph: 0499 944 969
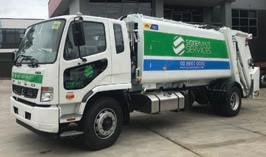
Ecohog Mobile Windshifter
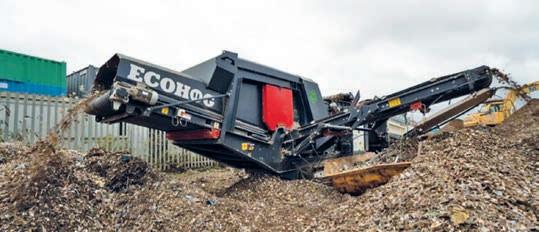
Model name: EH-1500 TWS (Mobile Windshifter) Unit Dimensions: Contact CSS Equipment Weight: From 8.5 tonnes Drive Type: Genset (CAT) Motor: CAT 100KvA Suitable material: Light and Heavy Waste Materials No. of units in range: 2 Models (Static & Mobile) Throughput: Dependant on Material Type & Density Designed for (material): Separating Light Materials from Heavy Materials. Options/Extras: Static or Mobile, with Metal Separation. Price: From $220,000.00 AUD More: CSS Equipment Pty Ltd Info@cssequipment.com.au / 1800 644 978
Giving (certain) states a break
MORNING Sir,
I hope all is well up in our green and fair land. Well, the numbers keep coming out, and I’m beginning to wonder if some states will see it through. While 80 per cent seems like a tall target, surely if we all pull together and see it through, we can hit that milestone, necessary for the future of this country to move forward.
Of course, I’m talking about the 80 per cent land fill diversion target that the federal government set a while back. Should be easy to get reach, right? Well, not necessarily. While some of the states seem to be doing okay, there are some recidivist offenders that might not make it?
Currently, the two struggling the most are WA and Queensland. Their current rates are hovering around the 30 per cent mark (a bit like 006’s assessment at the shooting range I hear – I told him to stay off the G&T’s the night before, but you can take the man out of Knightsbridge, but not Knightsbridge out of the man it seems). That means they will have to triple their recovery rates at the same time that the likes of NSW only need to bump their current 65 per cent by 15 per cent. A hard task for even the most determined WA/ Queensland premier.
At the risk of sounding condescending, I can’t help but wonder if the governments of those two states are their own worst enemies. In the case of Queensland, well, they certainly are the masters of the own downfall. Former premier Campbell Newman decided to scrap the landfill levy all together. Made sense at the time of course – Queensland has more holes to fill than a 9/11 conspiracy theory due to the amount of mining that has gone on in the state. Why not encourage them to be filled? Very logical. Of course, the next government to come in decided to reinstate the levy, but still at a hugely discounted rate compared to its southern neighbour.
Yet, this is the real kicker – instead of using the levy as a stick to try and encourage landfill diversion, the state government decided to use it as a carrot instead. They pay councils 105 per cent of the value that they spend sending stuff to landfill. Yeah, a real disincentive, not!
That is the power of rate payers, Sir. Governments – both state and local – are too scared to make the right call. Not too sure who the brain surgeon was who decided that little nugget was a good idea. That’s akin to asking our old Soviet friends to introduce just a little capitalism into their economy – would kind of undermine the whole point of their system.
But here is another idea. All things are not created equal. Maybe the Federal Government should give those lagging behind a little more time to catch up. Not much, mind you. Maybe another one to two years? Just to make sure they do it properly. Sure, there’ll be the odd whinging and whining from the states who have got their houses in order, but that’s nothing new either. We know WA and Queensland are a bit like the Gloucestershire of country cricket, not that successful but they do try hard.
Anyway, that’s all from me this time around, Sir. Time for high-tea at the MCG – precursor to the cricket season kicking off down here. iw
JB
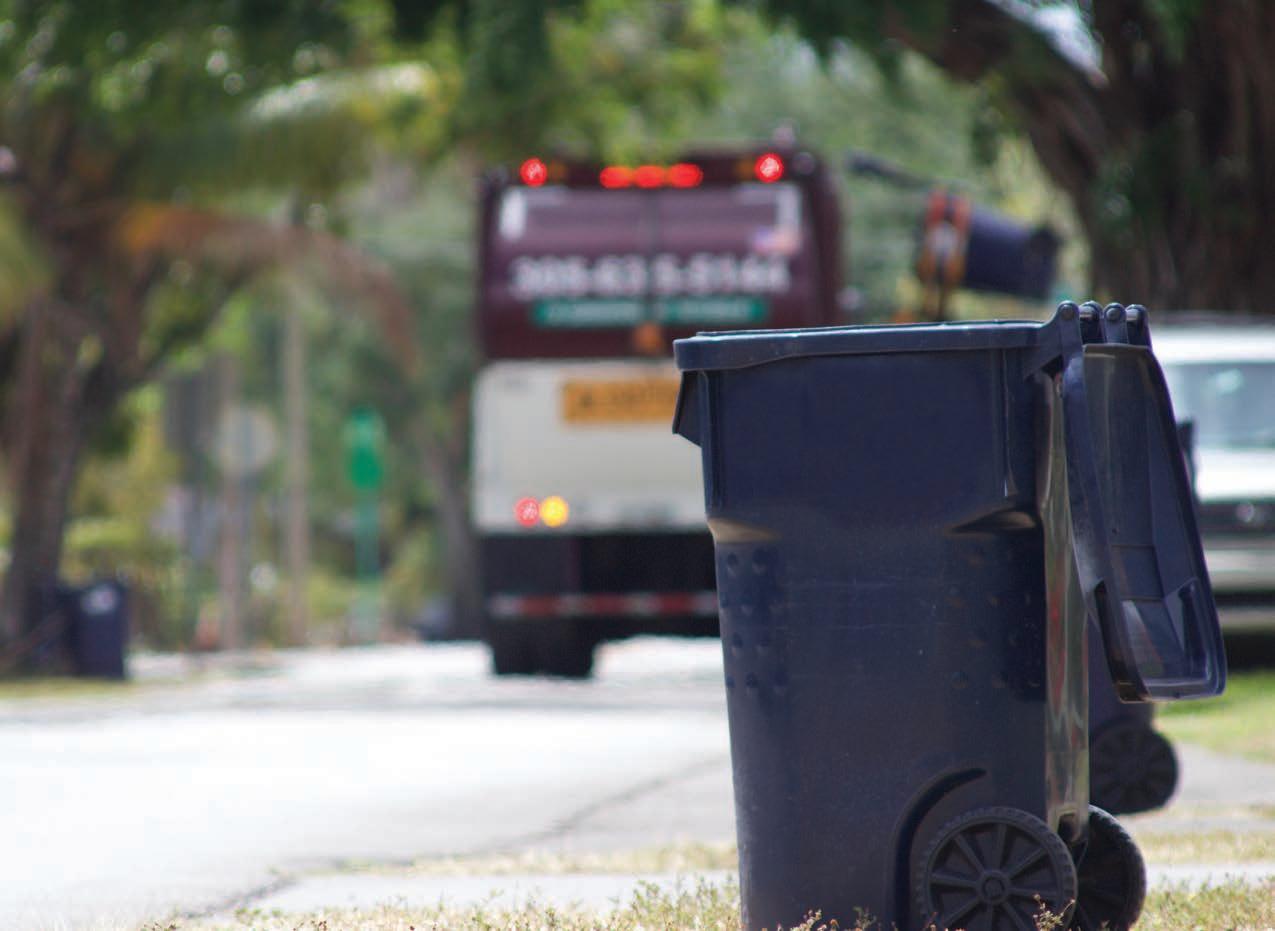