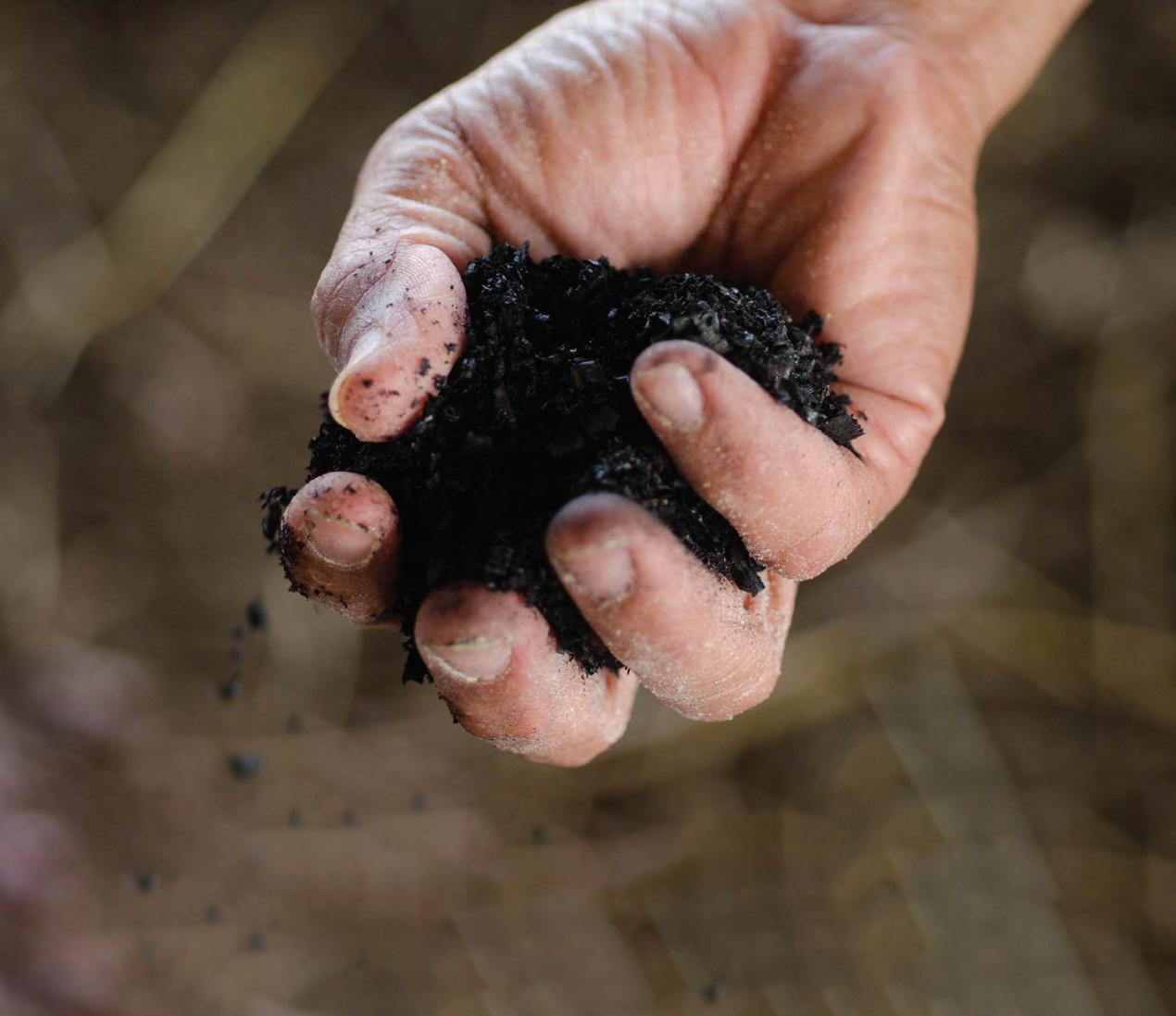
84 minute read
Residual waste
Biochar has been around for almost 2,000 years, according to Shah.
NO matter how many times you try and recycle plastic, one day it will reach end of life. As a waste stream it is problematic – landfills don’t want it, while environmentalists believe burning it, no matter how ‘clean’ the technology, is unacceptable. Those who champion zero waste would rather researchers, and those that produce plastic, work on ways of making it more biodegradable, or give it properties that greatly reduce its endof-life impact on the environment.
However, turning such a useful product – and it is useful in many ways – into something that is more environmentally friendly is not as easy as it sounds; not without heavy investment and costs that a lot of companies are not willing to spend.
Researchers at RMIT University have claimed to come up with a cleaner, cost-effective way to upcycle used plastic, transforming it into nanomaterials and high-quality fuel.
Lead researcher, associate professor Kalpit Shah from the university’s School of Engineering, said that globally, about 20 per cent of waste plastics are recycled. He said boosting that figure remains a challenge as recycling plastic cleanly can be expensive and usually produces lower-value products, often making it financially unviable.
He said the new method his department is working on produces high-value products from plastic – carbon nanotubes and clean liquid fuel – while simultaneously upcycling agricultural and organic waste.
The team’s two-step process, revealed in the Journal of Environmental Management, converts organic waste into a carbon-rich and high-value form of charcoal, then uses this as a catalyst to upcycle the plastic.
“Our method is clean, cost-effective and readily scalable,” Shah said. “It’s a smart solution for transforming both used plastic and organic waste – whether it’s tonnes of biomass from a farm, or food waste and garden clippings from household green bins. We hope this technology could be used in future by local councils and municipal governments to help turn this waste into genuine revenue streams. It’s vital that we explore sustainable and cost-efficient alternatives beyond recycling. Upcycling plastic with home-grown tech would enable us to draw the greatest possible value out of our limited resources and bring us closer towards a true circular economy.”
The new plastic upcycling approach offers a sustainable alternative for the production of carbon nanotubes (CNTs). These hollow, cylindrical structures have electronic and mechanical properties, with applications across a range of sectors including hydrogen storage, composite materials, electronics, fuel cells and biomedical technologies.
Carbon nanotubes are in growing demand, particularly in aerospace and defence, where they can facilitate the design of lightweight parts. The global market for CNTs has been projected to reach $5.8 billion by 2027.
The new method starts with converting agricultural or organic waste to biochar – a carbon-rich form of charcoal often used for improving soil health. The biochar is used to eliminate toxic contaminants – such as Poly-cyclic Aromatic Hydrocarbons, known as PAHs – as the waste plastic is broken down into its components of gas and oil.
The process eliminates those contaminants and convert plastics into liquid fuel. At the same time,
the carbon in the plastic is converted into carbon nanotubes, which coat the biochar. These nanotubes can be exfoliated for use by various industries, or the nano-enhanced biochar can be used directly for environmental remediation and boosting agricultural soils.
“We focused on polypropylene as this is widely used in the packaging industry,” Shah said. “While we need to do further research to test different plastics, as the quality of the fuel produced will vary, the method we’ve developed is generally suitable for upcycling any polymers – the base ingredients for all plastic.”
The experimental study conducted at lab scale can also be replicated in a new type of hyper-efficient reactor that has been developed and patented by RMIT. The reactor is based on fluidised bed technology and offers improvement in heat and mass transfer, to reduce overall capital and operating costs. The next steps for the upcycling research will involve detailed computer modelling to optimise the methodology, followed by pilot trials in the reactor.
However, some participants on social media disagree with the new technology, with one person posting on Facebook, “There are independent researchers that strongly disagree with this industry perspective. Let’s not forget that pyrolysis technology was created by the coal industry. Biochar is unproven and turning plastic into fuel just exacerbates climate change. This petrochemical industry con is a false solution to the plastic waste crisis. As for nanomaterials, despite the significant health and environmental threat they pose, Australia has no regulatory framework in the industry”.
Shah disagrees on both points.
“Pyrolysis was not created by the coal industry,” he said. “It is a process of decomposing organic waste under oxygen free conditions. If the process is looking at producing only biochar (i.e., charcoal-type material) then it runs at much lower temperatures, unlike combustion, which operates at higher temperatures and has the potential to generate more pollutants. It is reported in the literature that production and consumption of biochar has been known to humans for more than 2,000 years. It was naturally formed, so biochar has a long history. Some people think it came from coal, but that is not correct.
“When you compare pyrolysis to incineration or combustion or What are you going to do with the difficult waste? Ultimately, you will have to break it down. If you put that waste in landfill this will cause land, water and air pollution.
gasification-type processes, pyrolysis has much lower environmental emissions. I’m not saying pyrolysis will have no emissions. But you need to understand, what are you going to do with the difficult waste? Ultimately you will have to break it down. If you put that waste in landfill this will cause land, water and air pollution. If you do it the way we are proposing, there may still be some small negative effect in terms of emissions, but the benefits to the environment are significant.”
Shah reiterates, when it comes to residual waste there is no perfect solution. He is looking at the reality of the situation as it stands. Even if a brand new, totally environmentally friendly plastic was to hit the market tomorrow, there would still be billions of tonnes of plastics, including that of the residual kind, needing to be dealt with over the next few decades.
First and foremost, Shah is an environmentalist. He believes in the mantra of ‘first - reduce, reuse and recycle and if that is not possible then go for resource recovery’. To him, there is wishful thinking in only looking sat reduce, reuse and recycle and not dealing with the reality of the situation. The reality being, how can this problematic waste by-product be disposed of with the least amount of impact on the environment if it can’t be reduced, reused or recycled?
“People talk about burning as always a bad thing, but you really need to consider the context. If you put that plastic in landfill, it might end up in the ocean and cause marine life problems. What do you do with all this residual plastic? What I am targeting are plastics that can’t be recycled and need a different approach,” Shah said.
“Overall, there is a great potential that problematic plastics, if processed through our approach, can have much reduced environmental impact. We have to look at what we can do best to damage the environment the least.” iw
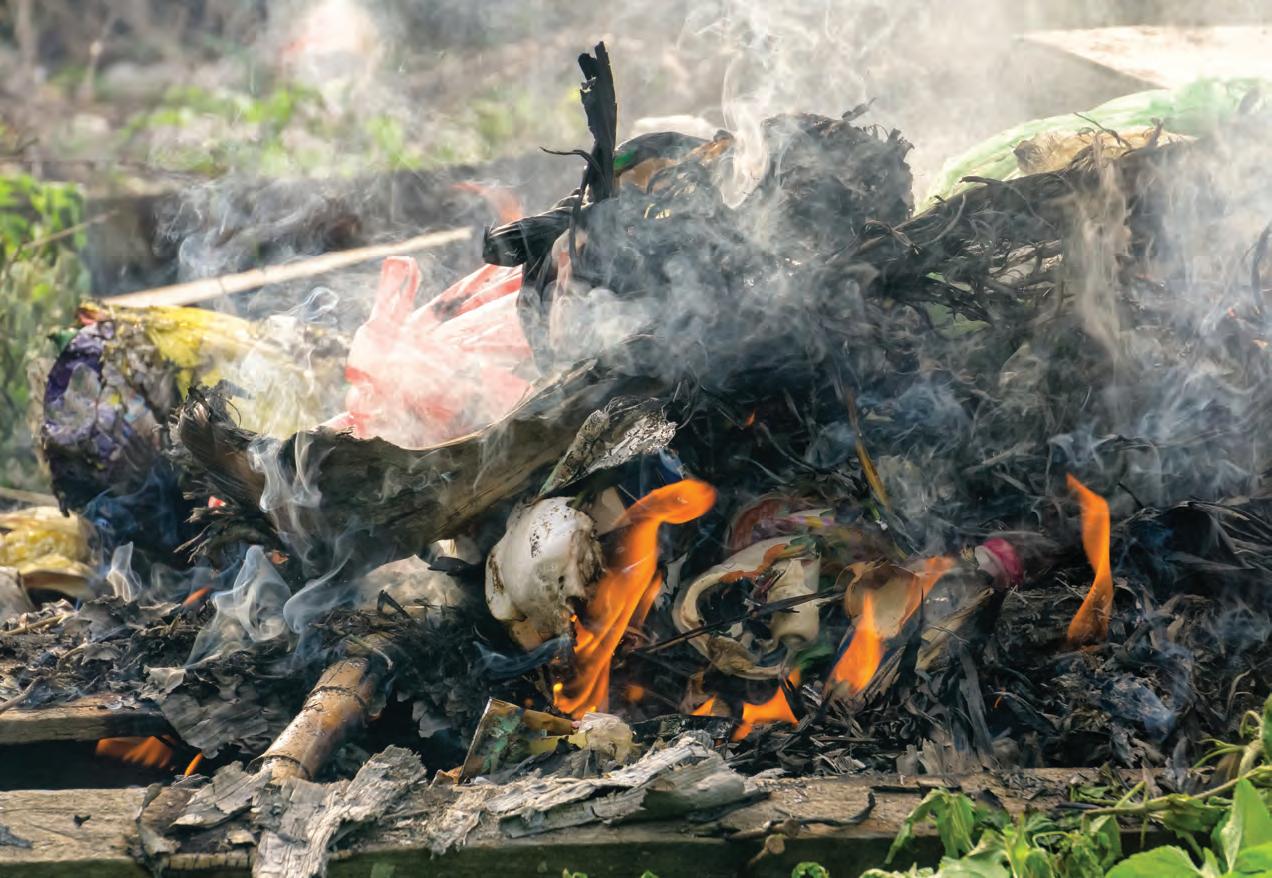
CSIRO testing wastewater from long-haul flights
AUSTRALIA’S national science agency, the CSIRO, has analysed wastewater samples from long haul flights of returning Aussies, which prove signals of the SARS-CoV-2 virus can be detected even before passengers show symptoms.
The research from CSIRO scientists, working with Qantas and The University of Queensland, demonstrates that wastewater surveillance can provide valuable data for public health agencies and help improve confidence in Australia’s safe reopening to the world.
Published in Environment International, the study analysed wastewater samples from lavatories of 37 Australian Government repatriation flights from COVID-hotspots including India, France, UK, South Africa, Canada and Germany landing at Darwin International Airport between December 2020 and March this year.
The research found wastewater samples from 24 of the 37 repatriation flights (65 per cent) showed a positive signal for the virus that causes COVID-19 despite all passengers (except children under age five) testing negative to the virus 48 hours before boarding.
Infected people shed the virus in their faeces about two to five days before showing symptoms. Traces of COVID can also be detected in wastewater from people who were previously infected, still shedding the virus, but are no longer infectious to others (although this is typically a weaker signal).
During 14 days of mandatory quarantine after arriving in Australia, clinical tests identified only 112 cases of COVID-19 among the 6570 passengers (1.7 per cent).
There was 87.5 per cent agreement between the positive detections by surveillance of the wastewater (i.e., detection of SARS-CoV-2 RNA) and the subsequent clinical detections made during the passengers to quarantine.
This was the first official study of wastewater from Australian repatriation flights returning from hot spots and the first time researchers have matched the plane wastewater testing with the follow-up clinical data testing of passengers in quarantine.
For the study, CSIRO undertook the wastewater analyses, and much of the data analysis with input on from University of Notre Dame, USA. Qantas designed the sampling trap with input from The University of Queensland and both organisations were involved in study design and wastewater sampling.
According to the latest paper, surveillance of wastewater from aircraft and cruise ships offers a convenient and cost-effective means of monitoring infectious agents that could be globally scaled to detect and manage the importation of disease. iw
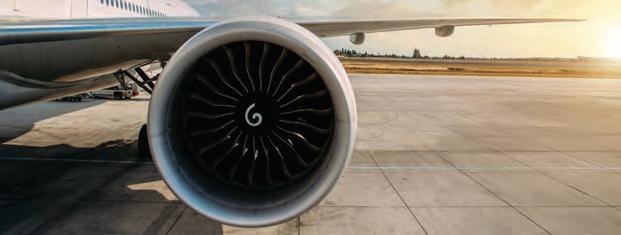
Wastewater had its part to play in detecting COVID-19 on international flights.
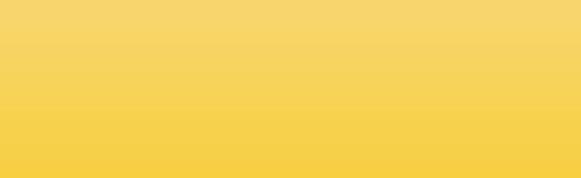
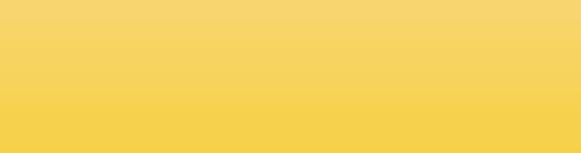
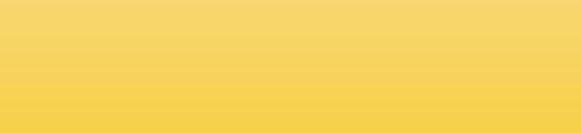
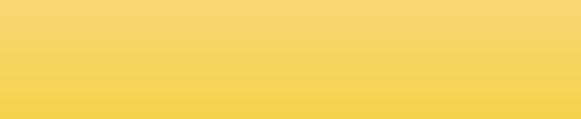



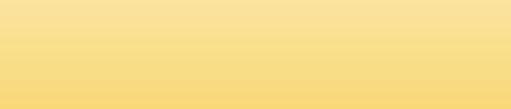


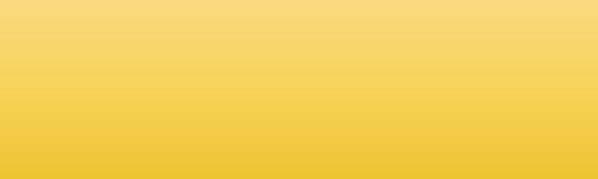
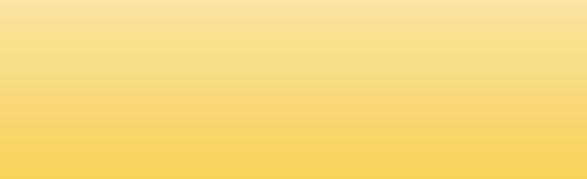
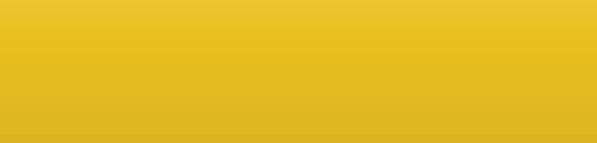
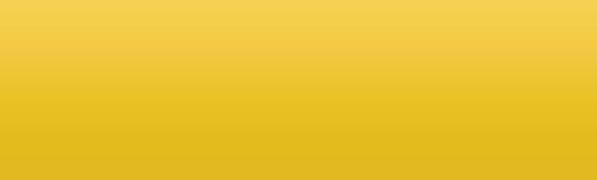
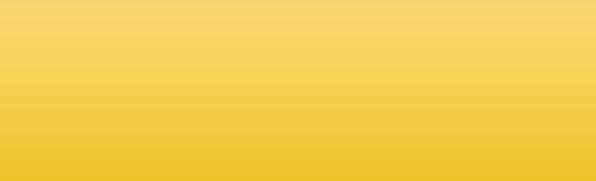
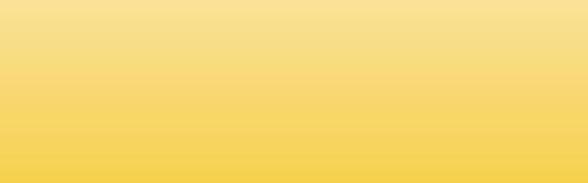

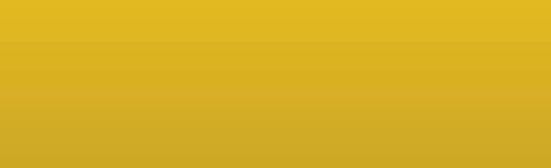
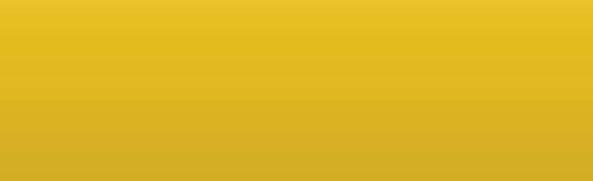
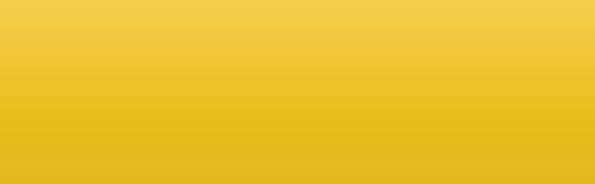
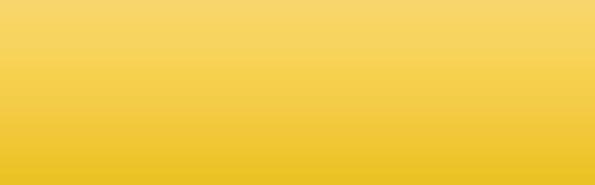
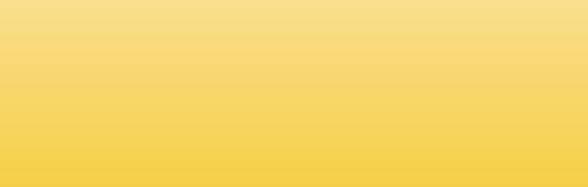
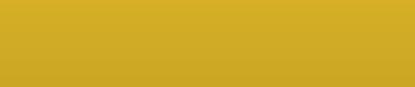
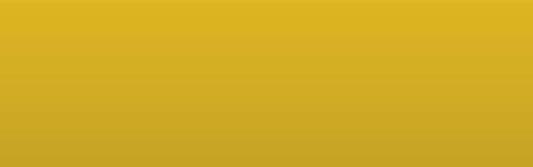
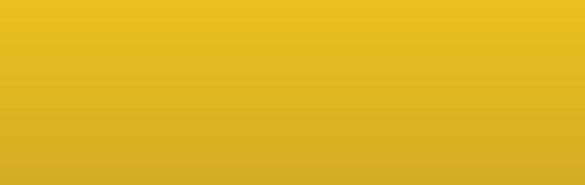
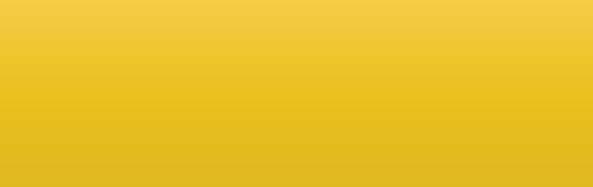
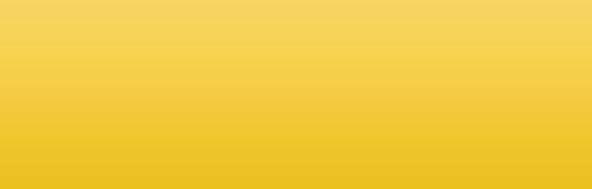
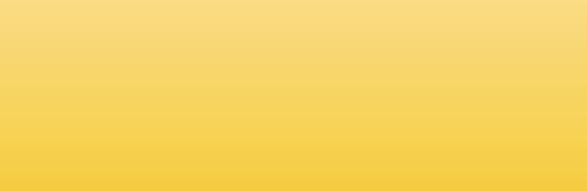

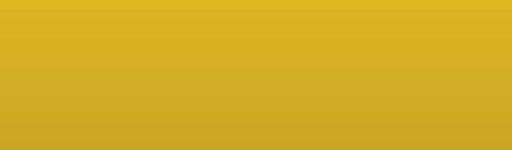

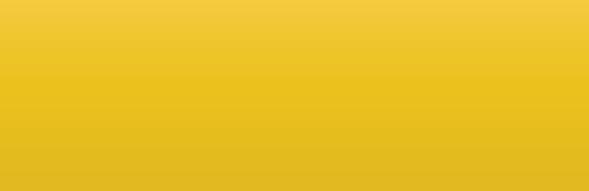
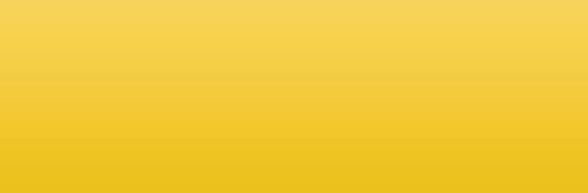
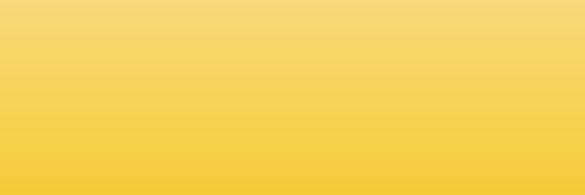

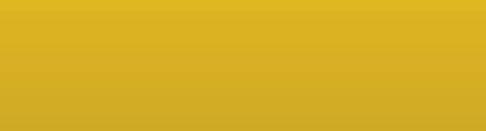
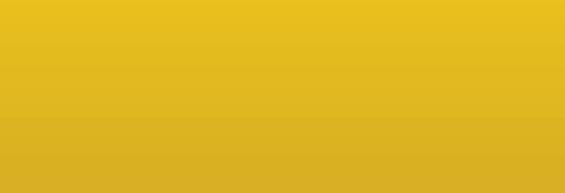
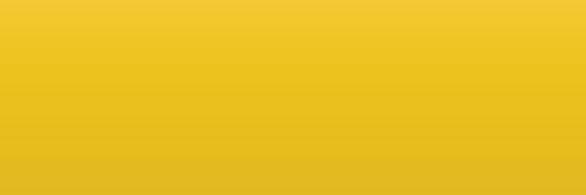
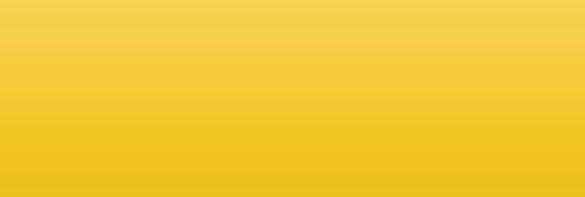

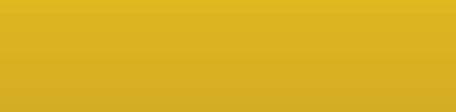
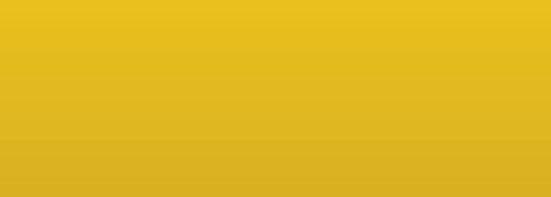
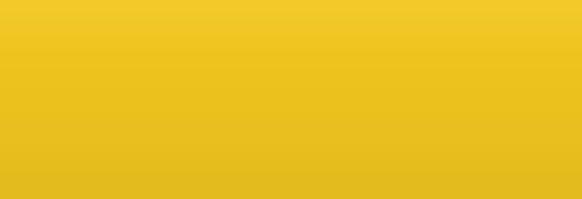
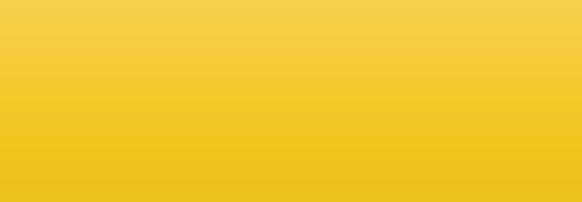
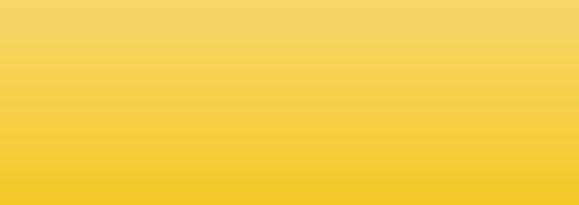
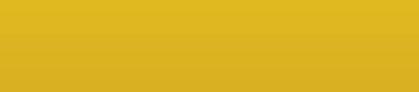
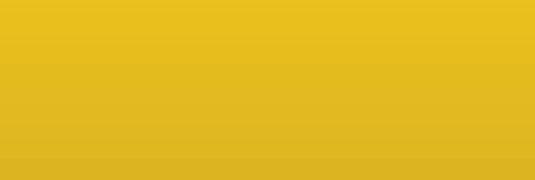
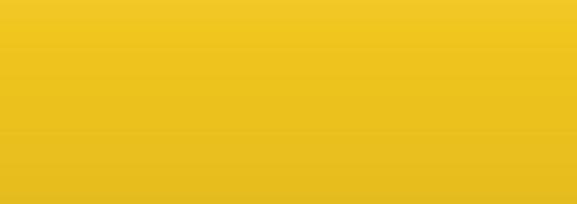
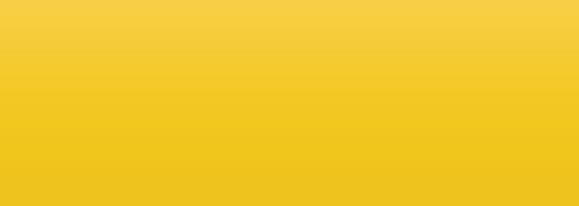
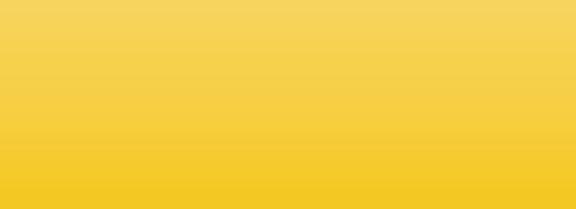
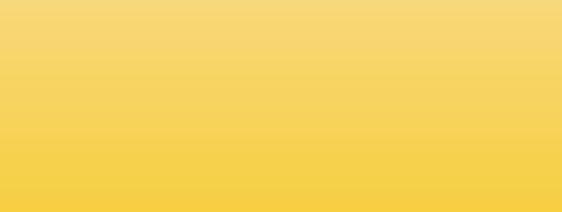

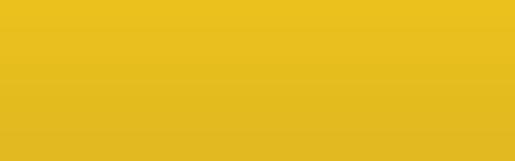
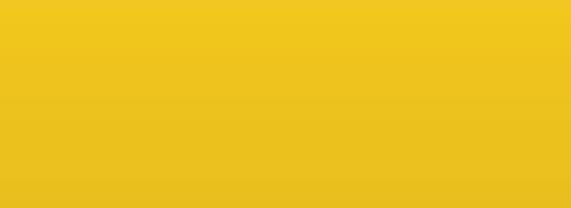
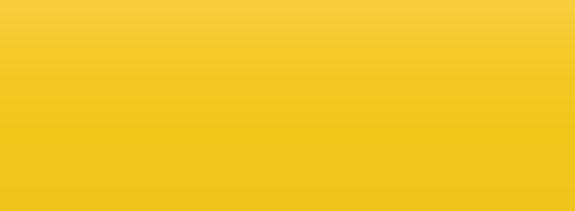
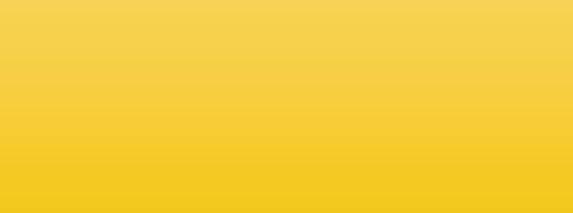
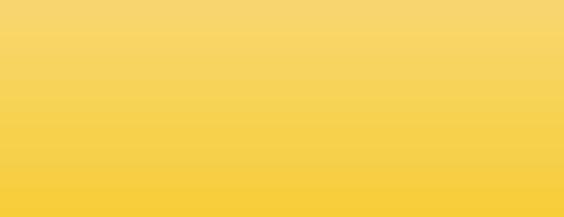

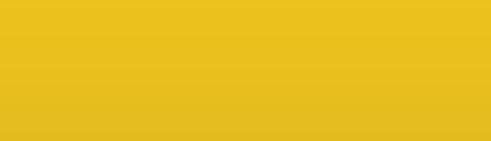
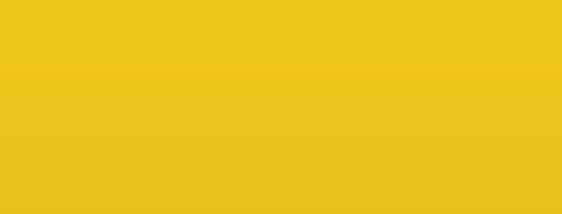
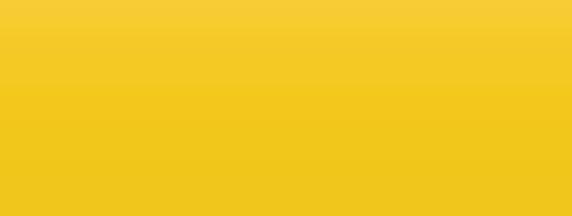
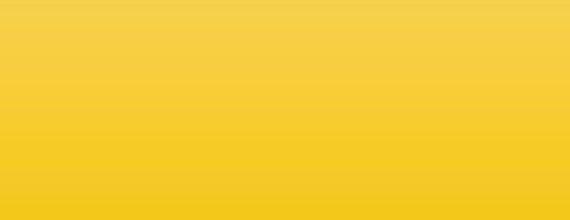
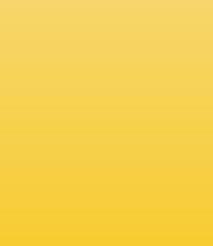
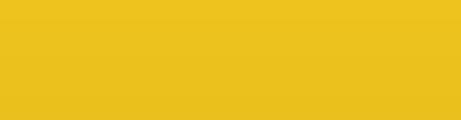
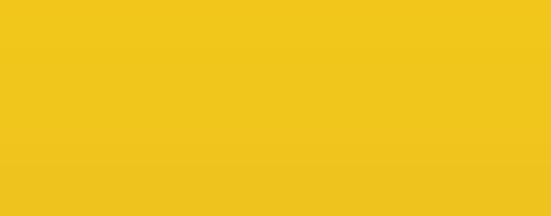
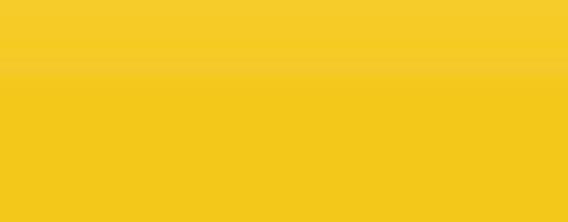
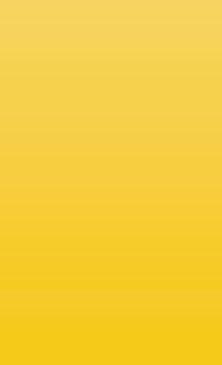
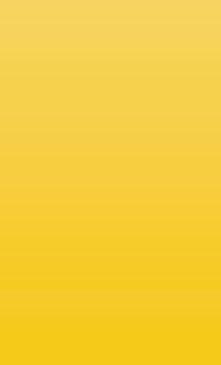
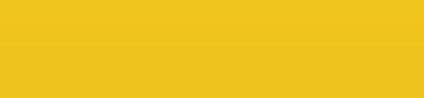
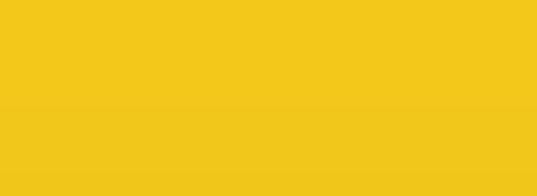
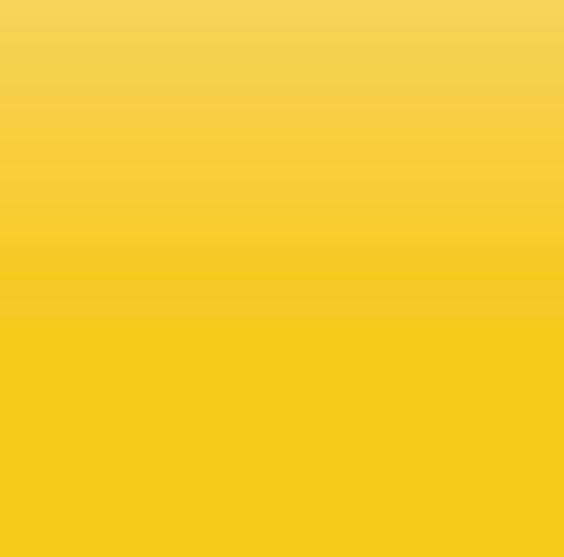
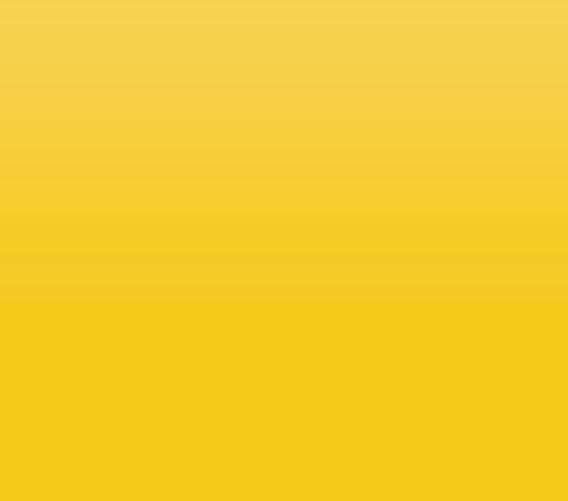
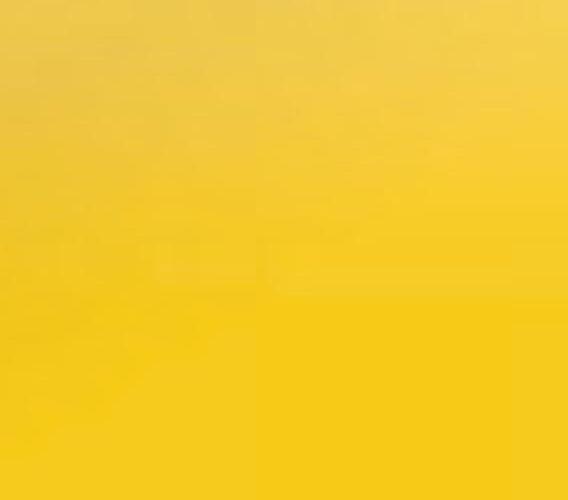
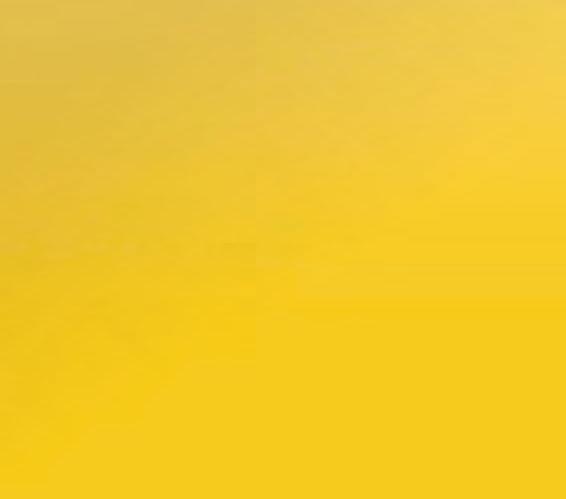
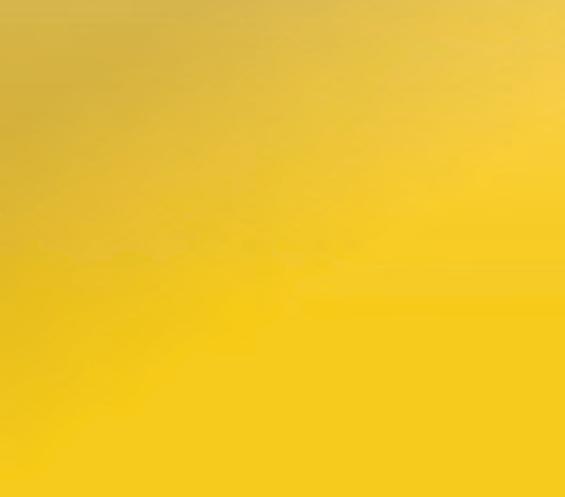
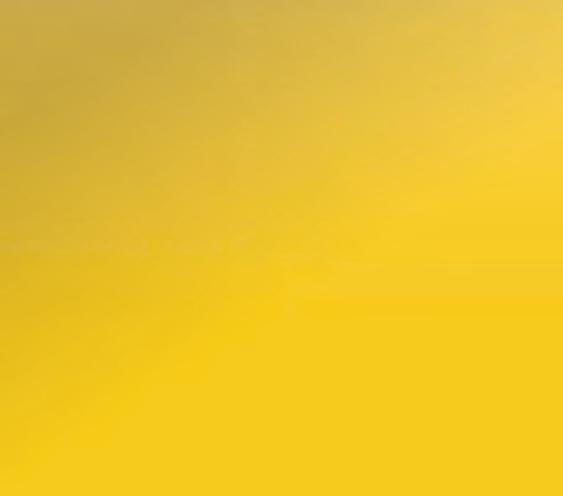
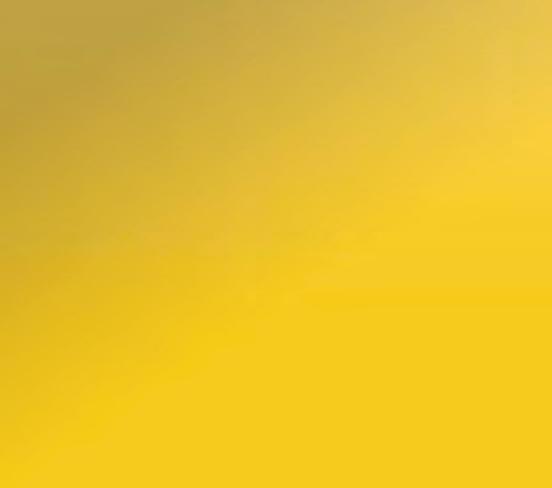
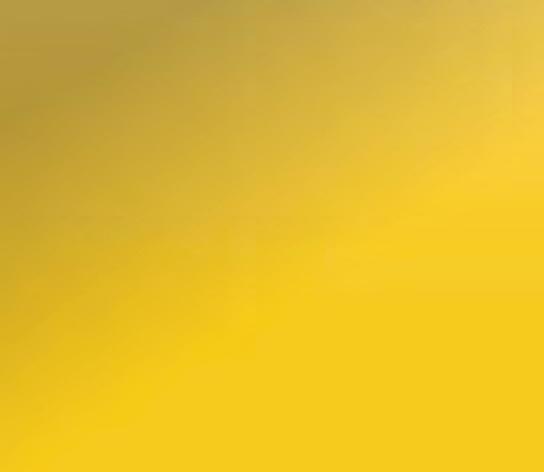
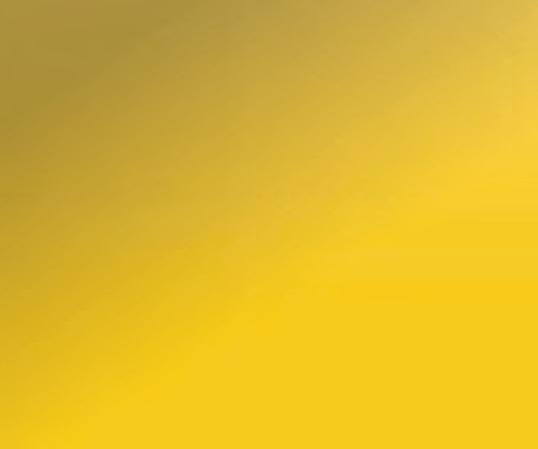
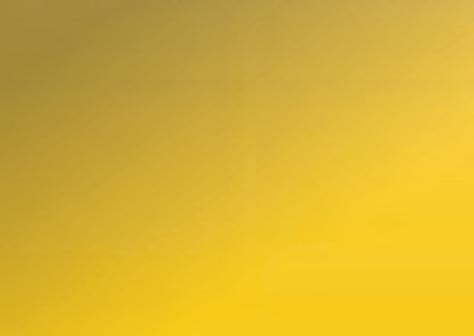
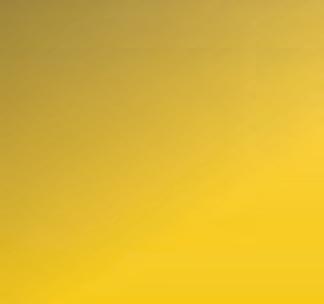
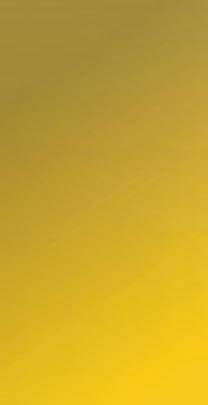
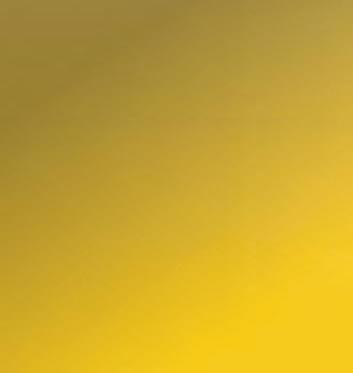

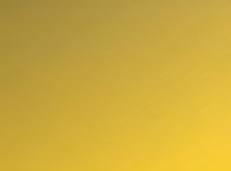
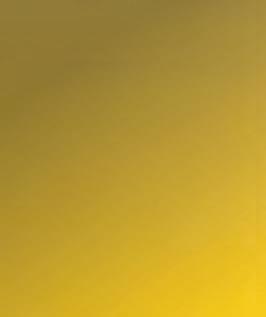
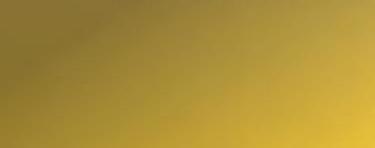
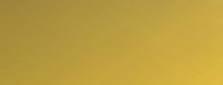
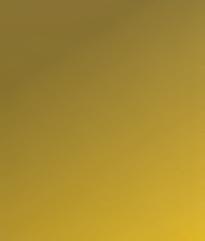
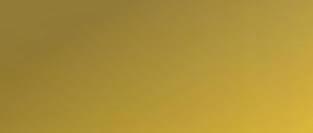
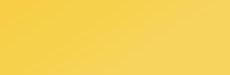
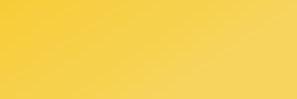
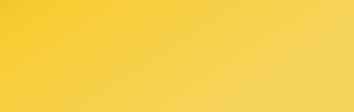
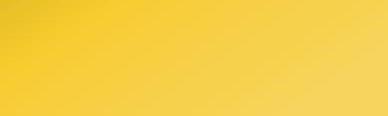
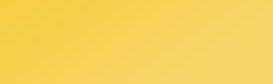
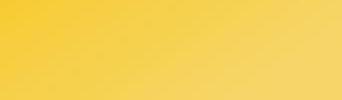
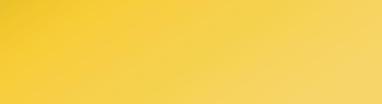
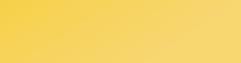
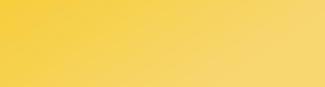
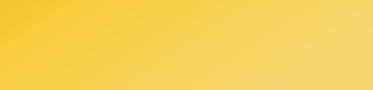
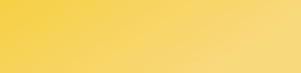
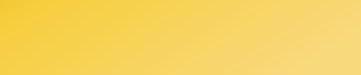




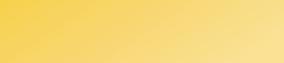
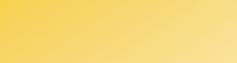
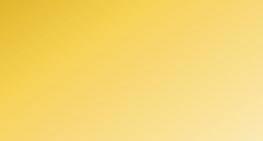
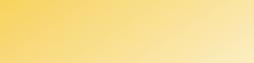
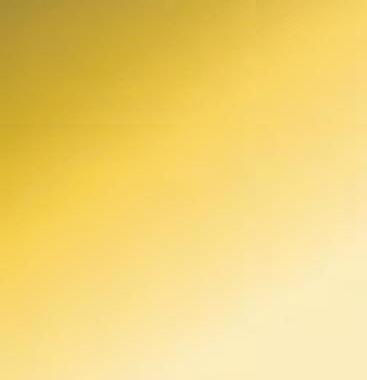
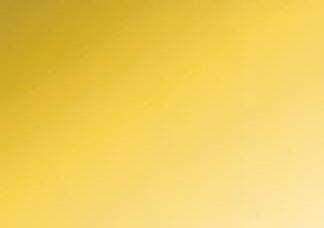
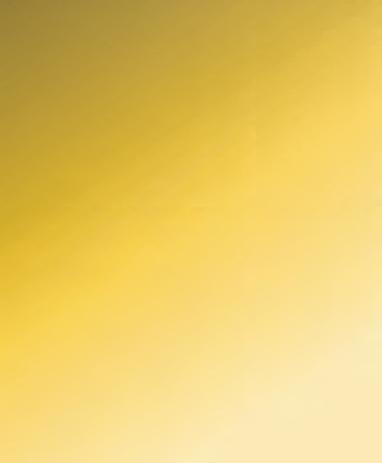
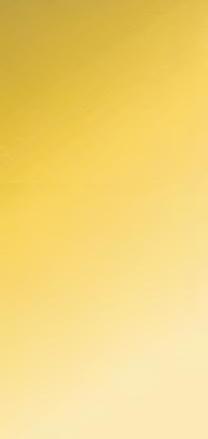
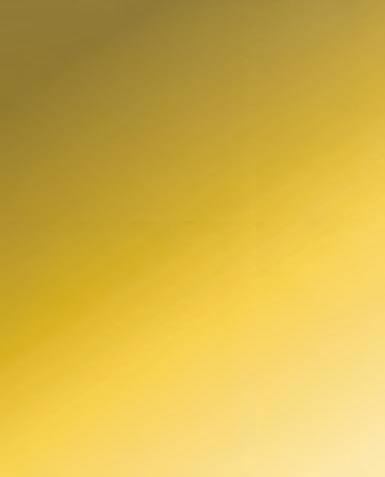
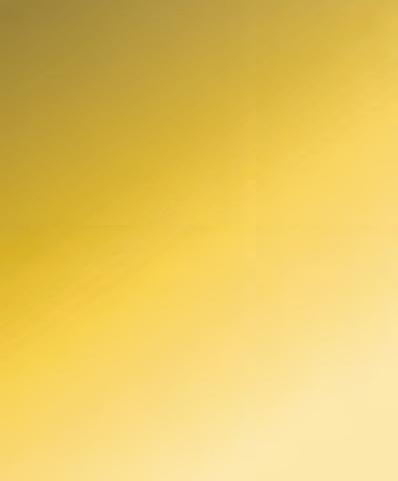
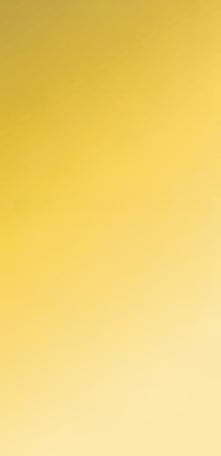


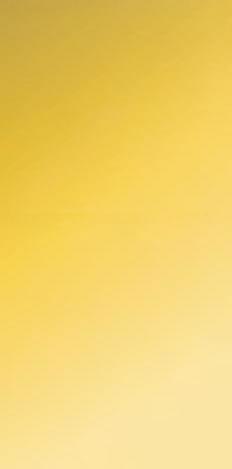
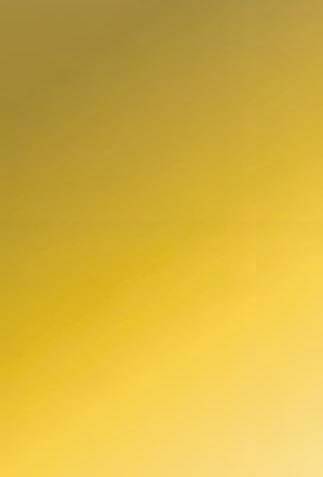
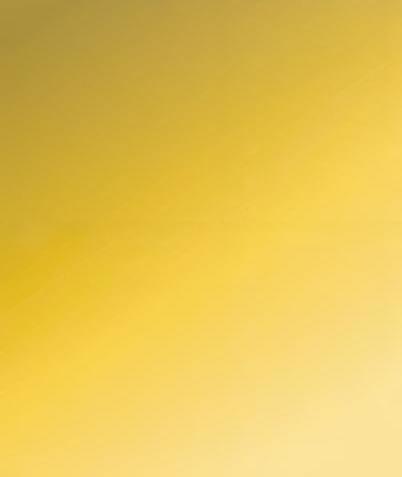
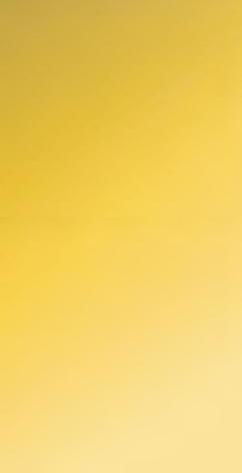
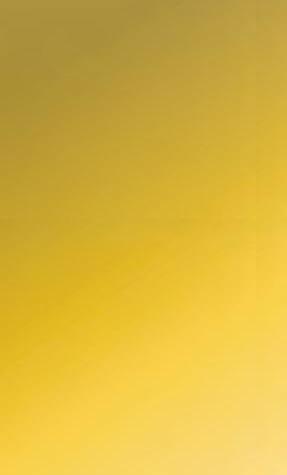
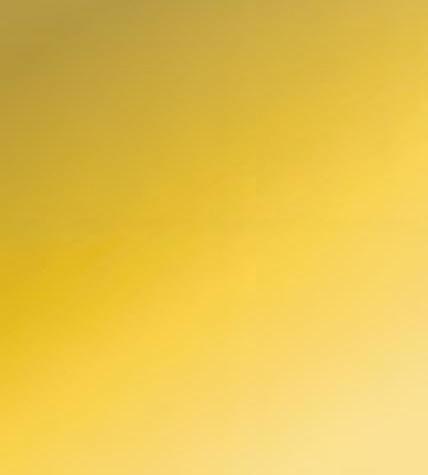
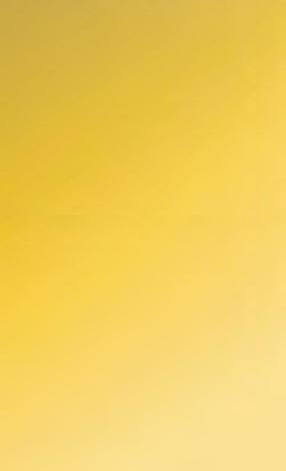
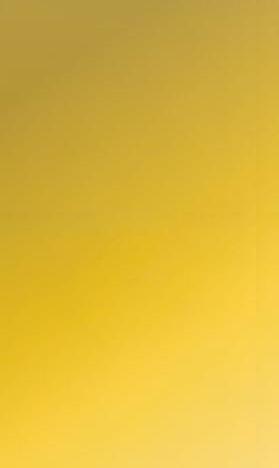
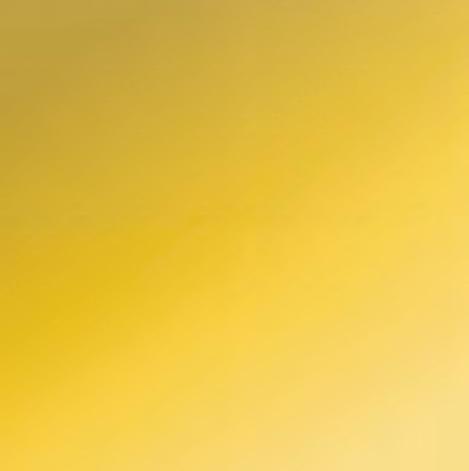
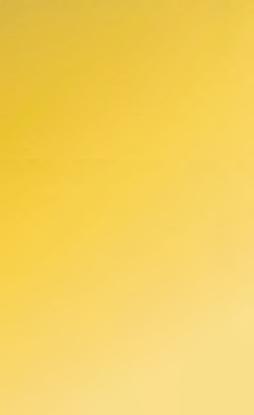
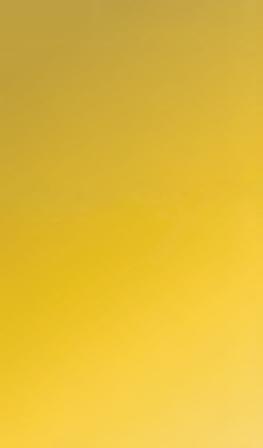
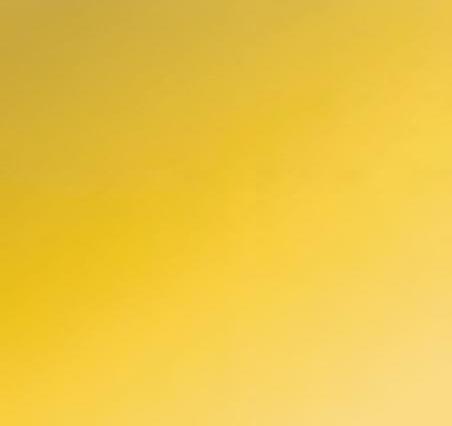
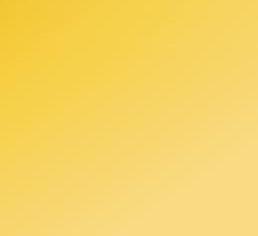
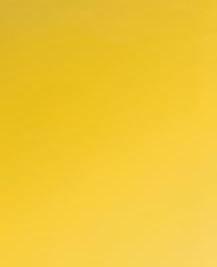
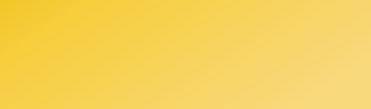
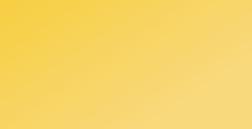
The role of business in reducing plastic pollution
By Paul Cumming
WITH an aim to reduce pollution and confront some of the world’s most challenging environmental problems, a circular economy uses a multitude of approaches. Whether through design, sharing, repair, recycling or behavioural change, a circular economy fully accounts for the products and materials we use. But underpinning the numerous aspects of how a circular economy reduces waste is a single factor: accountability.
Accountability key to stopping plastic pollution
Accountability is key in waste reduction, and especially key in the movement to stem the tide of plastic pollution choking our oceans and waterways. Plastic use in Australia is projected to double by 2040, with 130,000 tonnes already making its way into the marine environment. And as we’re now finding, this is just the tip of the polystyrene iceberg. Last year, CSIRO suggested there might be up to 14 million tonnes of microplastics (plastic of 5mm diameter or less) in the deep ocean – an amount that as it decays, will spread even further. Yet despite its globally significant and ever-growing impact, plastic production and use has been normalised to the point of being almost unconscious.
With inconsistent legislation state-to-state around single-use plastic in Australia, there is a growing consensus that businesses
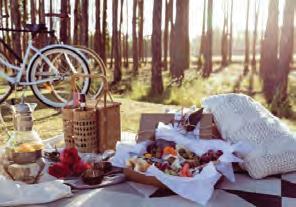
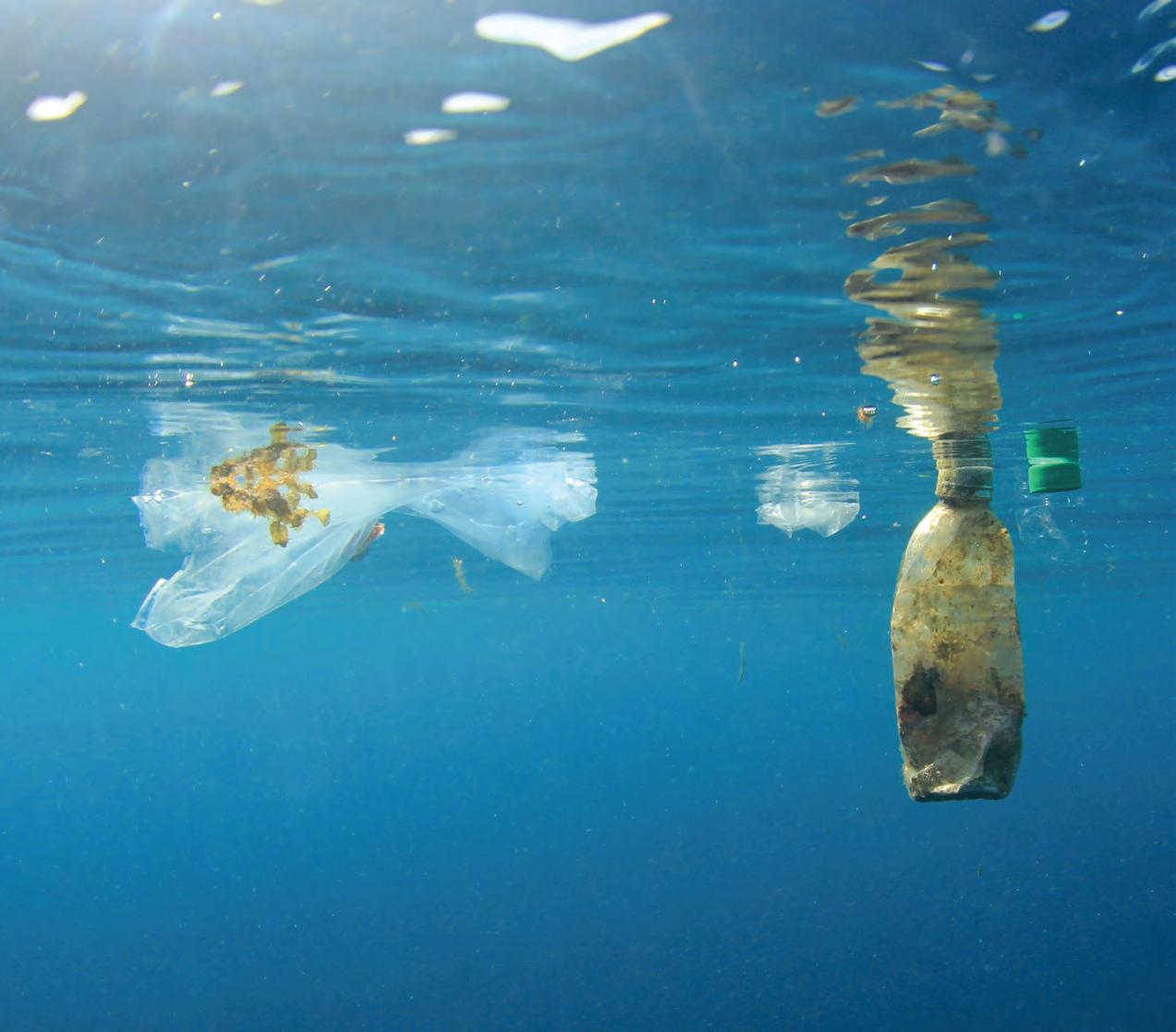
need to start leading the way. Plastic Oceans Australasia (POA) has been prioritising industry collaboration to educate and drive change. As well as partnerships with organisations such as workplace recycling company Ecobin, during the past year, POA has been both host and guest on a variety of digital media, including podcasts and webinars. These have featured not just research and advocacy experts, but businesses that are changing the current plastic-use paradigm, such as The Great Wrap, makers of the Australianmade compostable cling wrap, and Replas, an Australian business that transforms soft plastics into a range of products, from play equipment to playground equipment.
However, the solution doesn’t just lie with businesses that have plastic reduction baked into their business model. The solution lies with the way we all do business. Work is where a large portion of our time is spent as adults. The behaviours and ideas that are cultivated in the workplace are normalised and carried into everyday life. This idea is central to some of the work POA has been doing in a range of different businesses, instituting plastic reduction and recycling programs and inviting employees at all levels to examine how their organisation can reduce their plastic footprint.
An EPIC solution
POA’s work with Australian businesses to reduce the plastic pollution in their value chains is called the Engagement for Plastic-free Innovation and Change – or EPIC – Program. The EPIC program has brought plastic consumption into full-focus in the workplace this year, with 1,870 staff in a variety of organisations undertaking the campaign. These are not small wins. Targeting workplaces not only creates tangible organisational change but increases awareness around singleuse plastic that will continue to drive change into the future.
POA’s EPIC program is solutionsbased – looking at the full lifecycle of plastic within an organisation, from procurement to use, as well as reflecting on the effectiveness of measures implemented during the life of the EPIC program. Through plastic habit surveys, workshops, audits and guides to identifying barriers to behaviour change, EPIC doesn’t dwell on the simple identification of the problem. Instead, it focuses on empowering individual decisionmaking and eliminating barriers to change.
A wave of change
Of course, accountability can’t rest with business alone. With half of the global population living within 100 kilometres of a coastline, our individual choices around plastic make a difference. The Port Phillip Eco Centre’s Baykeeper report cites fragments of hard plastic, often crushed or decayed plastic bottles, as the main pollutant found in both major rivers feeding into Melbourne’s Port Phillip Bay, with the remainder led by other recognisable consumer items – polystyrene and soft plastics.
The data clearly links this with our activity choices: the data peaking in summer and spiking close to key recreation events, such as the Flemington Racecourse during spring racing. This need for an individual behavioural shift has been instructive in the delivery of education programs to more than 17,500 students during 2020-21, as well as the landmark Picnics Unwrapped campaign. Launched on World Picnic Day on June 18 this year and continuing to November 15, Picnics Unwrapped spreads awareness about single-use plastic by encouraging people to host their own plastic-free picnic. With campaign ambassadors ranging from artists and chief executives to marine scientists, Picnics Unwrapped was a fun, positive way to spread the word about plastic use, and highlight the need for more accountability in how we consume.
The growing popularity of the circular economic model is proof that both businesses and individuals are beginning to account for, and address, their respective attitudes towards consumption. And with plastic pollution causing what the UN has called “severe environmental consequences”– in addition to single-use plastic still being on the rise – there is no better time to be a part of the move towards a cleaner, healthier, plastic-free future.
Plastic Oceans Australasia is a Not-for-profit organisation addressing the root cause of single-use plastic consumption. iw
Inside Waste News & Networking twitter.com/InsideWaste

NOW AVAILABLE TO VIEW ON
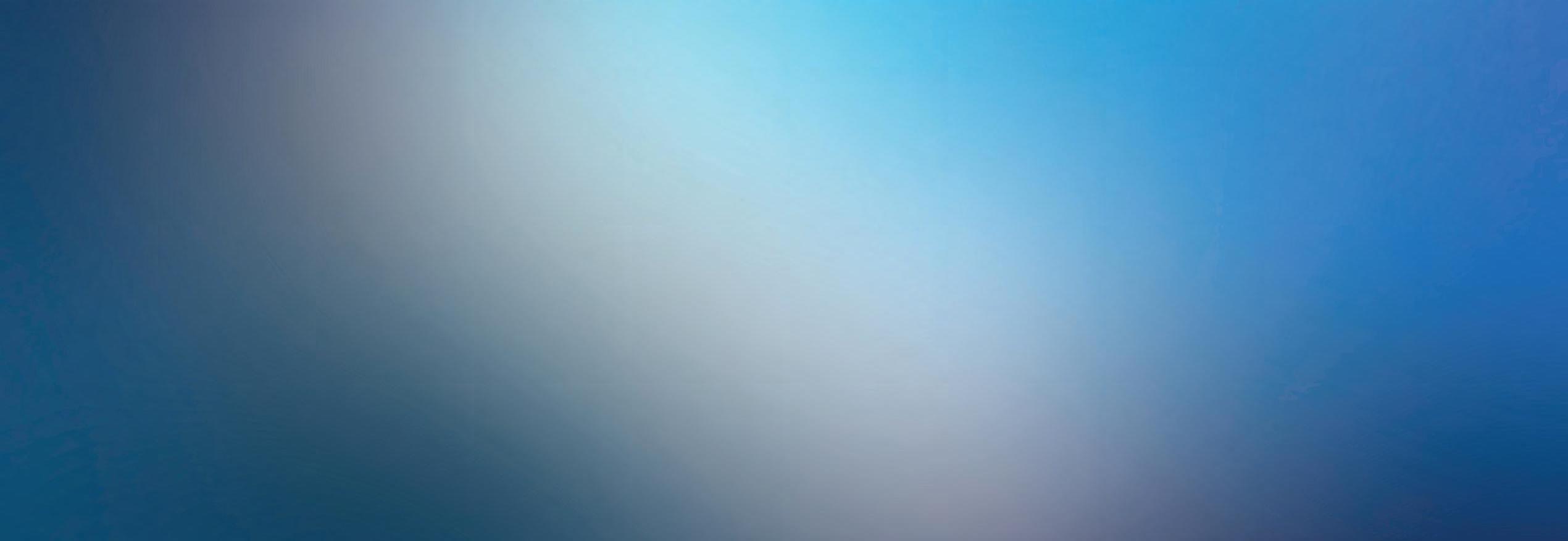
www.insidewaste.com.au
ISSUE 101 | APR/MAY 2021
ISSUE 100 | FEB/MAR 2021 INSIDE
www.insidewaste.com.au
INSIDE 26 AWRE Conference 40 Wastewater 43 Young Professional 30 Landfill 37 What circular economy?42 Truck feature
ON DECEMBER 8, 2020, the Recycling and Waste Reduction Bill was passed in the Senate without amendment. Despite a senate inquiry into the Bill and attempts by the Greens and Labor, the amendments to the Bill that would address plastic pollution and support the recycling sector did not pass. This has resulted in concern within the WARR industry that the government’s commitment to the massive problem of plastic pollution remains fragile despite its assurances and organisation of the first National Plastic Summit in Canberra, prior to COVID-19.Much of the frustration around the failure of the amendment has been focused on the continual reliance on the packaging industry to self-regulate. Despite this industry’s best efforts to address this issue (Inside Waste covered the Australian Institute of Packaging’s Virtual Conference and the APCO initiatives in depth during 2020), the needle on the decrease of plastic waste fails to move by any significant degree. WMRR CEO, Gayle Sloan is one WARR leader who has consistently pointed to the ineffectiveness of the efforts by the packaging industry to manage the issue. She told Inside Waste that the strong support for the amendment to the Bill was an indication of a desire within the Australian community to deal with the packaging problem.“While it is disappointing that the amendment fell through on a single vote, it is heartening to see growing consensus that we need to do more to tackle the packaging that we consume and dispose of. “What we have seen to-date is strong community support for action. Real action to be taken to tackle packaging and create jobs in Australia. “The message is clear,” Sloan said. “The business-as-usual approach is not acceptable anymore. Australians deserve more than a continuation of a voluntary, packaging industry-led scheme that has made little, if any, progress.” Senate didn’t understand Sloan pointed to the “real opportunities to close the loop domestically”. She said that this could be achieved by building local businesses, driving new industries, job creation, and environmental protection. “It is disappointing that some in the Senate did not understand that. However, it is extremely encouraging to see the level of support for change.” However, Sloan is not without suggestions on how to move forward. “With the export bans coming in shortly, and the need to meet national targets, WMRR is urging all governments to think about how we can tackle packaging with the limited and voluntary tools that we’ve been given. “WMRR proposes that it’s time to set up a genuinely independent body truly representative of all stakeholders in the supply chain, including but not limited to the packaging industry, to find productive ways in which we can work together to genuinely close the loop on packaging in Australia by using Australian recycled products. “This is key if we are serious about making real progress while being hamstrung by the lack of regulation on the packaging industry,” she added. (Continued on page 22)
PP: 100024538 ISSN 1837-5618
How Indonesia plans to be plastic-free by Plastic problem is not business as usual All industry stakeholders need to work together to genuinely close the loop on packaging in Australia by using Australian recycled products. WHILE INDONESIA is one of the biggest contributors to the plastic pollution in the ocean, this situation became exacerbated after China banned waste imports and the country emerged as a major portal for global plastic waste. Now its landfills are running out of space with Indonesia’s largest landfill, Bantar Gebang (the only one serving Jakarta) predicted to run out of space this year, according to government officials.Coordinating Minister for Maritime Affairs and Investment, Coordinating Ministry for Maritime Affairs of Indonesia Luhut B. Pandjaitan told the World Economic Forum, “In our cities, our waterways and our coastlines, the accumulation of toxic plastic waste is harming our food systems and the health of our people. “Our booming fishing industry, the second-largest in the world, is under threat from rising levels of marine plastic debris. By 2025, the amount of plastic waste leaking into our oceans could increase to 800,000 tonnes – if no action is taken,” he said. Despite this gloomy scenario, the country has developed a strategy which was presented at the World Economic Forum’s Annual Meeting in Davos last year. Here the world took a first look at Indonesia’s plan, with a radical target to cut marine plastic debris by 70 per cent within the next five years. (Continued on page 24) 2040
Think your waste is unshreddable? Think again! Meet the XR... Low wear. Low maintenance. Low running costs. Maximum performance. Request a free waste audit: info@focusenviro.com.au
THE leading report on waste management and recycling data in Australia shows that Australians are reducing their waste and increasing their recycling.Blue Environment’s National Waste Report 2020, commissioned by the Federal Government’s Department of Agriculture, Waste and the Environment, was released in December last year. The report is the authoritative compilation of national data on waste and resource recovery and the mechanism for measuring progress against national waste policy targets. Issued every two years, the 2020 edition focuses on the status of waste and recycling in 2018-19, with data analysed on a per capita basis as well as on state and territory levels. Findings cover waste generation, source streams, material categories and fates, together with trends measured back to 2006. While the data precedes the significant investments in recycling and resource recovery the Federal Government has made since the 2019 election, its revised 2016-17 data set (first published in the National Waste
Report 2018) will be used as baseline data to measure Australia’s progress against the National Waste Policy Action Plan’s 2030 targets. “The release of the leading report on waste management and recycling data in Australia, shows that Australians are reducing their waste and increasing their recycling,” Assistant Waste Reduction and Environmental Management Minister Trevor Evans said.“This is a great outcome. We can all be proud that our efforts are paying off, to take care of our own waste and to do the right thing by sorting our recycling and diverting more waste away from landfill.” Evans highlighted that Australia created 3.3 per cent less waste in 2018-19 compared to 200607, the foundation year of the national data set. “In effect, we each produced waste that weighed the same as 40 full kegs of beer and we each sent the equivalent weight of 24 full kegs to be recycled,” he said. “However, our growing population means that the overall amount of
waste Australia is generating continues to increase, up five million tonnes since 2016-17.“We need to continue to work hard to reduce the amount of waste we create, and to recycle more of it, if we are to achieve Australia’s ambitious national target of recovering 80 per cent of our waste by 2030.”Evans explained that this was the driver behind “unprecedented” action by the government to turbocharge the waste and recycling industries, so that waste is treated as a resource which can be recycled and remanufactured into valuable new products. He said that this protects the environment, creates jobs and keeps waste out of landfill. “Our billion-dollar investment in new recycling infrastructure is changing the face of the waste and recycling industries in Australia,” Evans said. “We are also the first country in the world to ban the export of its unprocessed waste plastic, paper, glass and tyres overseas thanks to our new national recycling legislation.” (Continued on page 22)
DURING the recent Australian Circular Economy Conference (ACEC), one of the webinars delved into Food and the Circular Economy in Australia and China. One of the speakers was Alana Mann, associated professor for the Faculty of Arts and Social Sciences (FASS) at the University of Sydney. Mann noted that one outcome of the COVID-19 pandemic was that a lot of countries, like China and Australia, were taking a fresh look at how their food systems operated, both in terms of supply chain and food wastage. Mann said it was pleasing to see how both countries, and the world at large, had risen to the challenge of feeding the world’s population during a trying time, but it had also exposed some of the intrinsic weaknesses within some of the systems. “Circular economies and other models of food provisioning including community supported agriculture and cooperatives, are all coming to the fore,” she said. “China is a leader in these areas along with recycling waste and the development of smart technologies for ecommerce. How we connect with consumers and users ensures the supply chains to address food insecurity and also manage issues around waste are addressed, which is an important piece of the circular economy model.” (Continued on page 24) Waste needs to be treated as a resource – report
WEBINAR: Profitable one-step alternative fuel production 13th May 2021 10:00 | Register for your FREE place today: focusenviro.com.au/event
Glass achieved a recycling rate of 59 per cent. Just-in-time model not working
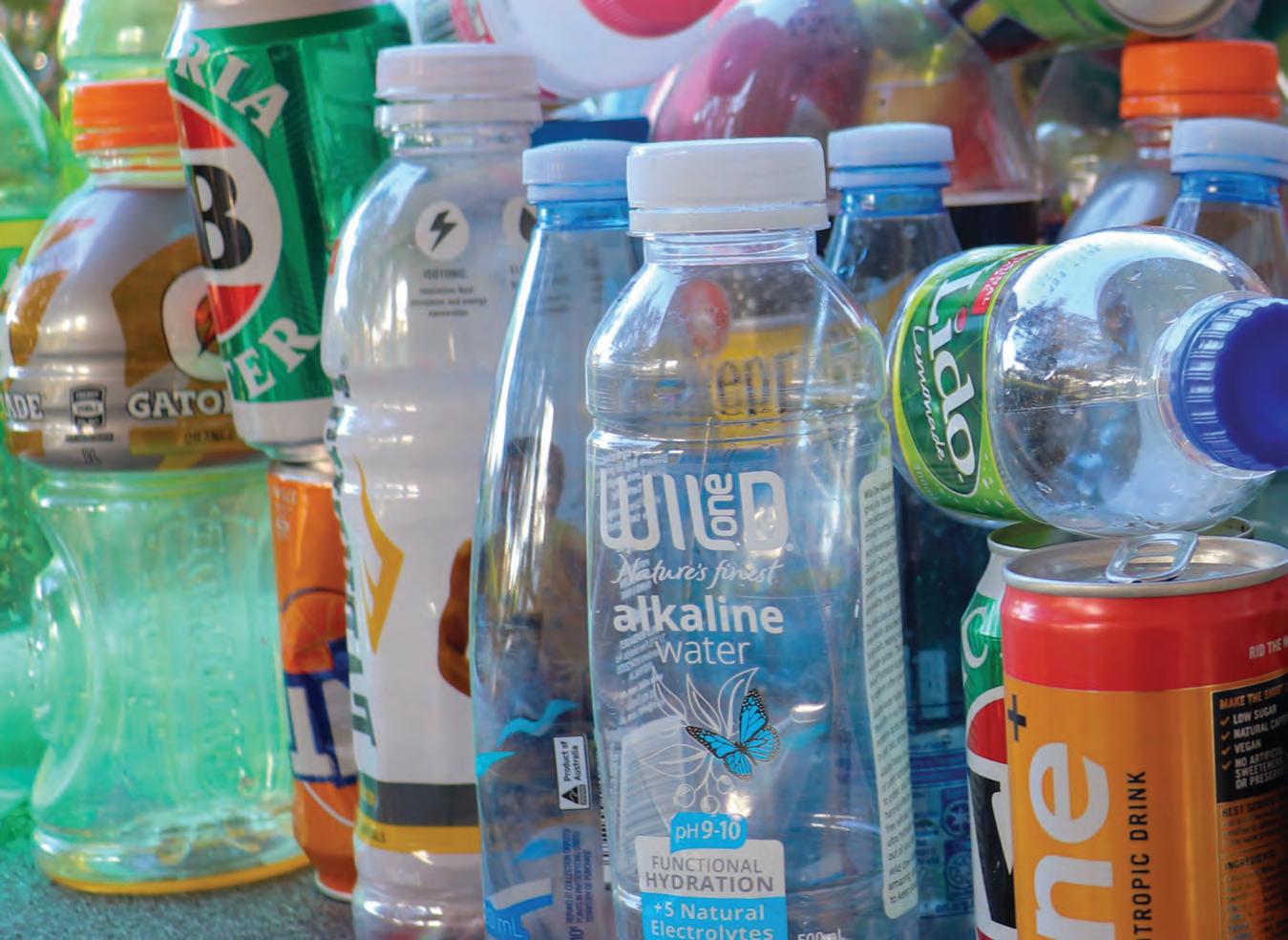
South Australia’s CDS reform needs direction
By Robert Kelman
AT 77 per cent recycling, South Australia’s container deposit scheme (CDS) is in the bottom third in terms of global performance. Most European (and a couple of US) schemes recover well over 90 per cent and Germany sits at 98 per cent. Assuming return rates are the arbiter of a scheme’s success, the recent SA draft CDS reform paper is welcome, providing a comprehensive assessment of the state’s CDS.
However, notably absent from the paper is exactly what the overall goal of the Government’s reform agenda is. Setting a direction, say a return rate target of 95 per cent by 2025, would be useful for stakeholders and the industry. I believe the SA Government needs to then lock in the changes required to reach it. What we do know is that the SA Government is seeking to build on the state’s circular economy (CE) agenda by achieving higher rates of recycling from the state’s CDS. The government recently released a reform paper that outlines what could be done and includes: • shifting some portion of eligible containers out of the kerbside system; • adding to the scope of eligible CDS containers; and • increasing consumer engagement in the scheme.
It’s progressive thinking to posit shifting material out of the kerbside bin. This mass of variable materials has been a problematic repository and a way for beverage producers to avoid the costs of recovery and recycling. For instance, most of the glass isn’t worth much except to be used as road base, and markets are generally wanting cleaner streams of material.
Adding wine and spirits to the list of eligible containers, as floated in the SA paper, would serve to remove decent quantities of this material out of the kerbside bin (and landfill), into the cleaner and more valuable CDS system for bottle-to-bottle CE outcomes.
Similarly, SA is looking to increase the volume thresholds for products such as alternate and flavoured milks (e.g. soy and almond milks etc). At present, the scheme effectively only covers 600ml LPB containers as the criteria is up to 1litre – so one litre and above is exempt, which accounts for the majority of this material.
The existing SA collection network is well utilised and important, and it needs augmenting if SA is to achieve its policy objectives of growing the success of its CDS. The 130 or so depots across the state have served the scheme well and the CDS helps underpin the economics of many of these sites that also collect other household recyclables such as
The existing SA collection network needs augmenting if the state is to achieve its policy objectives.
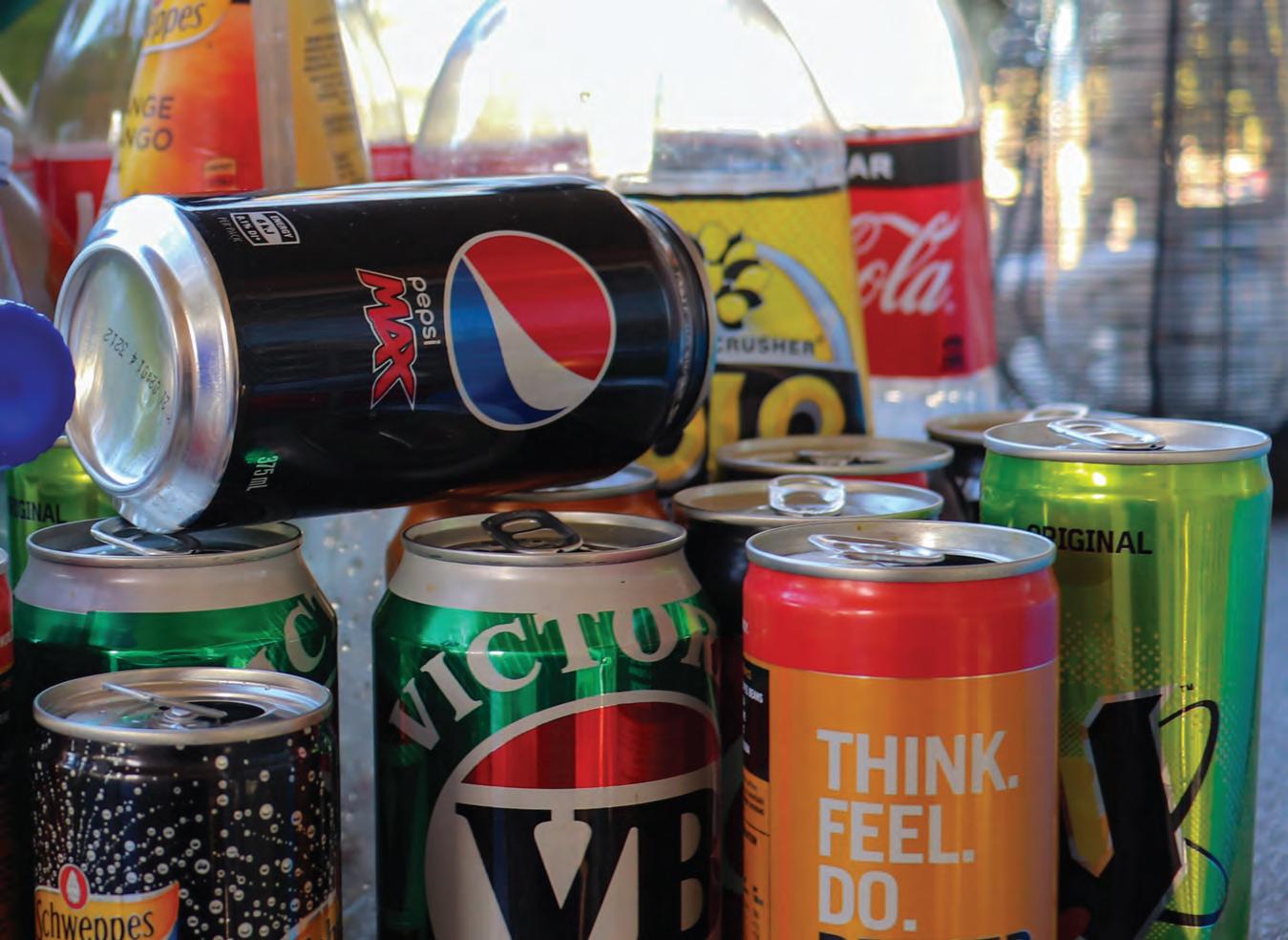
computers, gas bottles, batteries etc.
Ensuring the viability of this network is important, and giving disengaged consumers access to some additional collection points to capture an extra possible 15-20 per cent of containers would lift SA into the world rankings of scheme performance.
There are two principal features of successful CDSs around the world; ease of consumer access or convenience of the collection network, and the value of the refund. Both of these consumer engagement mechanisms need improving in SA and elsewhere in the country.
The SA paper outlines there is just one collection point per 13,400 people. Across Europe this ratio ranges around one collection point per 1,000 people. SA and all other Australian states and territories need much higher numbers of these facilities.
But it’s not just a numbers game. Convenience means collection points that are open when and where people naturally spend time rather than special trips to remote corners of a city. The paper outlines that SA consumers tend to sit on their containers for long periods – returning on average 210 containers every 2-3 months. Redeeming containers is therefore a periodic and specific task rather than a week-to-week activity incorporated into existing shopping habits. It should be made easier.
Beverage industry control of Australia’s CDSs is now at the core of the policy debates across all states and the SA paper begins examining mechanisms to loosen this grip on their scheme. As a reminder: For every 10 per cent less recycling in Victoria’s CDS, drink producers would have saved around $50 million per annum through avoided refunds and recycling fees. This is big-coin, and significant enough motivator for producers to try and control a state’s CDS to keep return rates suppressed.
By only allowing a relatively inconvenient network of collection points to be established or maintained, and/or advocating to keep the refund value low, big beverage producers achieve lower rates of consumer engagement and therefore return rates than would otherwise be the case.
NSW, the ACT and soon Victoria and Tasmania have dealt with this obvious conflict of interest by directly contracting the recycling industry for collection networks inherently motivated to maximise return rates, as they get paid per container collected.
The paper goes into some detail on possible governance changes to the SA CDS. As an example of producer control over SA’s CDS, it’s the beverage-owned ‘super collectors’ that decide who gets a ‘waste management agreement’ (WMA). These allow a collection point operator to get paid for their containers. Super collectors have then used control of these WMAs to block new entrants to the collection network in SA. Perhaps the EPA should licence and approve these WMAs instead and allow for the growth in size and convenience of SA’s collection network?
Finally, Australia’s 10 cent refund on CDS containers is losing its ‘value’ by the day and must be raised if we are to expect return rates above 80 per cent in any state. While we have a similar GDP per capita to Germany and much of northern Europe, our refund value is three to four times lower. SA’s leadership nationally on this issue is about pushing this value up. With a clear forward schedule of refund value increasing over the coming years to deal with inflation, this would be valuable.
Reforming SA’s CDS is overdue, though timely. This agenda offers SA an opportunity to build on its heritage, offer consumers better scheme access and engagement, an opportunity to implement its CE agenda, and also help guide other states in getting all Australian schemes up and out of the lower rankings. iw
Paving the way with toner waste
By Inside Waste
COMPANIES who want to know how they can help with the circular economy in terms of reusing, repurposing, recycling and reducing their waste footprint, should look to the collaboration between Close the Loop, Downer and CPB Contractors. The trio has come together to turn plastic powder from toner cartridges and waste soft plastics into a valued commodity.
It hasn’t been an easy road. The final product – TonerPlas, which is used in road construction – took Downer and Close the Loop (CtL) the best part of 10 years to realise. But it’s been worth it.
Toner cartridges and its residue powder had been destined for landfill as there didn’t seem to be any way they could be recycled into anything useful.
However, when Downer and CtL joined forces they discovered by adding soft plastics to asphalt, you get a product that ticks several boxes on the road construction front, and thus TonerPlas was born.
“It’s great at increasing stiffness and increasing the service life of an asphalt road,” said CtL’s founder Steve Morriss. “We started years ago by surveying some roads that had been laid that included toner powder as an additive in Texas in the US.
“That project was abandoned because of safety and health issues, but I had three different sections of that road surveyed and realised that it was adding significant value to reduce cracking and rutting in asphalt.
“Fast forward a few years and we had partnered with Downer by this stage. We started to think ‘how could we make the asphalt additive more elastic?’ That is when we moved to the mixed soft plastics and the REDcycle program.
“We are now the largest user of this particular waste stream from all Coles and Woolworths stores throughout Australia.”
At its most basic, TonerPlas is a polymer. Graham Henderson, who is the manager of precontracts and development at Downer, said the journey to getting the new material in asphalt started a while ago with another CtL product, which was used with an additive that Downer had developed.
“CtL first created a product called TonerPave, which was predominantly a toner-based additive that had some performance-enhancing characteristics about it,” said Henderson.
“Through the journey with them we started talking about ‘what’s next in asphalt?’ and looked for something new that would help solve the problems around waste.
“It was the same for all of our customers when it came to waste plastics that generally didn’t have any recycling avenues.
“CtL went off and did some research. We had input on what an additive needed to be working with our asphalt plant, and what sort of form the additive would need to be to get into our mixes. After a collaborative journey of a couple of years, we developed the product.”
So where is TonerPlas being used? Raphael Touzel is a project director for CPB Contractors, a company that specialises in infrastructure projects including roads. It too was looking for sustainable products to be used as an additive to asphalt on some of its projects, including an upgrade on the M80 Ring Road in Melbourne, Victoria.
The company works closely with Victoria’s Department of Transportation (DOT), a state government entity that has stringent rules on what it allows in its roading aggregate.
“The DOT is really strict with their pavement designs,” said Touzel. “They own the pavement design, which is pretty robust, and they want it to last for a number of years for future increased traffic loadings. Once you build a new pavement, and you’ve got traffic running on it – especially a freeway – you don’t want to be going back to improve it. They’ve got a design that is fairly conservative and that is what we had to work with.”
What are some of the properties of TonerPlas that make it suitable for roading? According to Morriss it has improved resistance to rutting, and improved fatigue life, making it longer lasting with a lower carbon footprint. This has been independently tested by the Australian Road Research Board
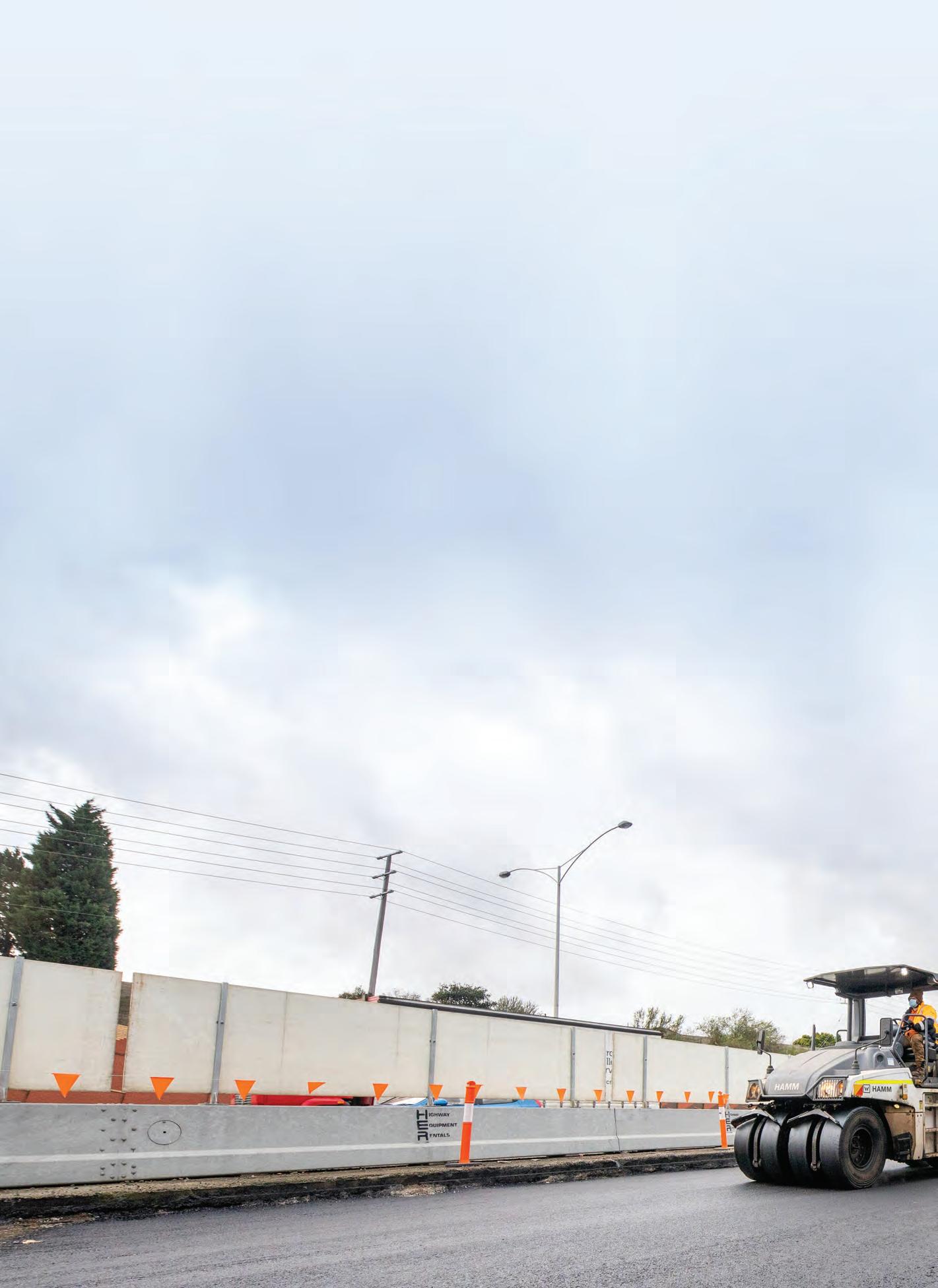
(ARRB), which is how the company got it approved for use by the Victorian DOT on the M80 Ring Road.
Tests carried out by the ARRB show that under the wheel tracking test – the Victorian DOT standard for this particular mix design has to be less than 11mm – the TonerPlas version came in at 2mm and the baseline standard asphalt was 9mm.
“We’re talking significant improvements [in fatigue life],” said Morriss.
“What that means is it increases the longevity of the asset. That correlates to about 15 per cent improvement of the life of the road, which in turn correlates to about a 15 per cent improvement in whole of life cost of the asset. It is a lowcarbon option.
“If you spread the carbon footprint over 23 years instead of 20 years, you have a significant improvement in the impact of that road.”
The sorting of the waste is key to making sure it meets the specifications to be used.
“We do a manual sort/ decontamination,” said Morriss. “We shred the mixed soft plastics then put it through automated cleaning systems, such as rare earth magnets, eddy current separators, and air density separators. They then go into a series of sophisticated mixing machines. These mixers are compounding the plastics and homogenising these plastics into a dough.
“This is where we add the toner powder. Out comes the product, which are small pellets. They end up in bulk bags and can be added as a dry mix additive at an asphalt plant.”
“We’ve done a lot of testing on it in terms of its wear capabilities,” said Henderson. “We had to in order for it to get acceptance from road authorities around the country. We’ve done a lot of performance testing. Our philosophy is that the product has to perform at least as well, and ultimately better, than the standard product.”
As well as meeting the standards of the Victorian DOT, it had to meet the standards set out by the state’s Environment Protection Authority (EPA). This was because there could have been issues with microplastics being put into the atmosphere as the road wears.
“We knew the way that we developed it, and how we incorporated it into the mix that we wouldn’t have a microplastics problem in our end asphalt product,” said Henderson.
“It was very pleasing to have gone through rigorous testing with designing it, in conjunction with the NSW EPA, because they had the most stringent requirements to get it through. That was a process of almost 18 months; sending samples over to Europe. It was a great thing to go through and get the validation at the time. It proved we didn’t have a microplastic issue compared to any other standard asphalt in the market.”
For Touzel, the M80 project has always been about using recycled pavement materials.
“When you demolish buildings, bridges, pavements or other concrete structures, it gets crushed up and turned into a road base instead of going into a landfill,” he said.
“All our pavements we have built are built out of recycled products – brick, concrete, old road base, recycled glass.
“It used to be that virgin aggregates would be needed, which would come out of different quarries to meet specification. Now it’s all recycled and blended mixes which can still meet the requirements.”
Then there is the asphalt layer, which is where TonerPlas comes into play.
“Downer’s tech expertise mixed with Steve’s knowledge got this across the line on our project,” said Touzel.
“It also helps to have a client who has a recycle-first policy. We believe in a recycle-first narrative, so we brought all that stuff together and thought ‘let’s give it a go’.”
However, is there enough toner powder and cartridges to continue making TonerPlas to do the job?
With a lot of companies going paperless, or at least vastly reducing their printing needs, will there be enough product available in the future? Morriss is confident there will be. Even if there isn’t, he’s not panicking about finding another source.
“There is scope to increase the amount we can produce,” he said. “We are never going to run out of toner powder.
“If we ever did in Australia, then we can call on the toner powder from our US or European business as a resource.
“It is a polymer. There are many sources of waste polymer that meet our spec.” iw
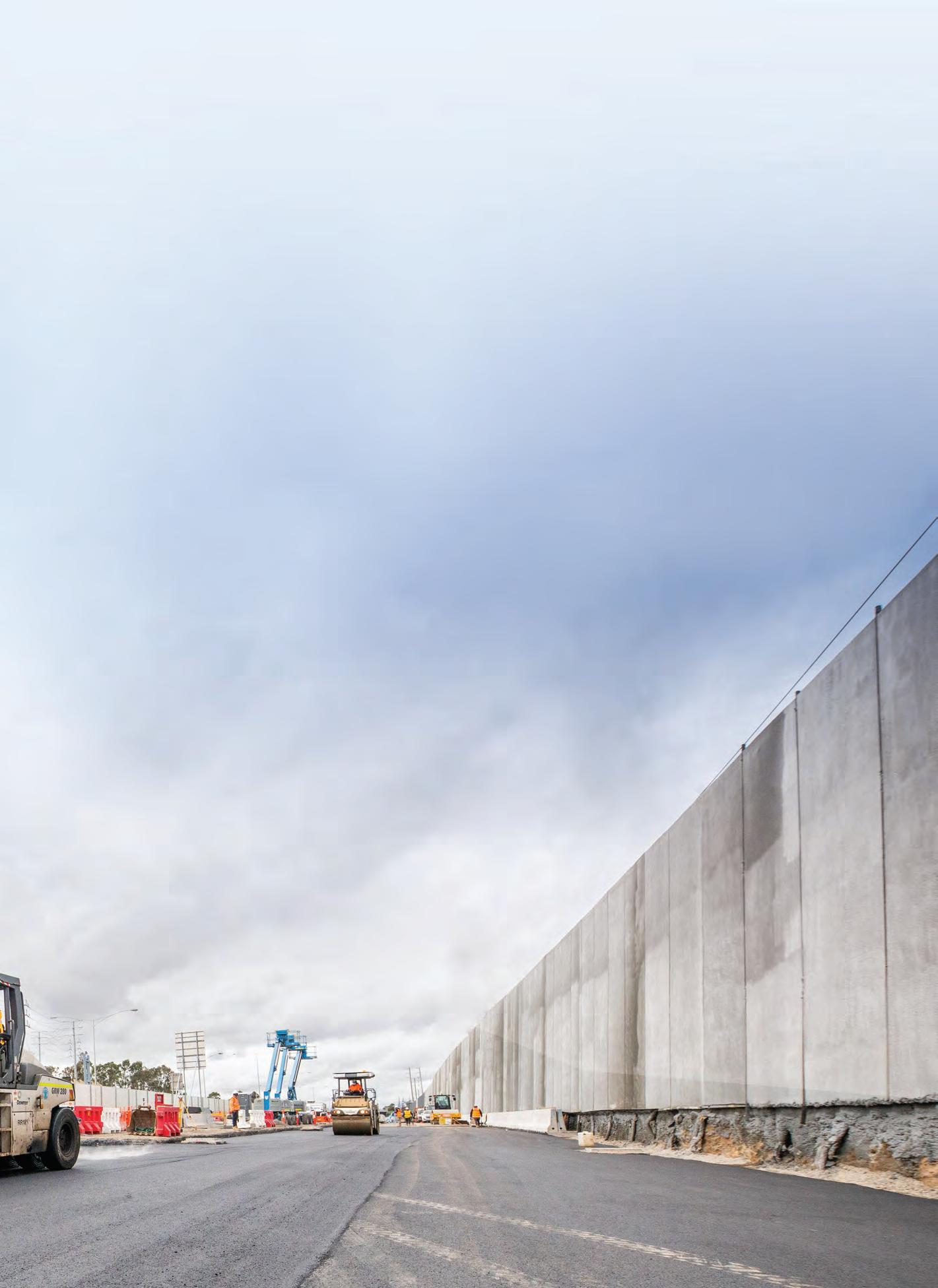
“Through the journey with Close the Loop, we started talking about what the possibilities were of, ‘what’s next in asphalt?’ and looked for something new that would help solve the problems around waste. It was the same for all of our customers when it comes to waste plastics that generally didn’t have any recycling avenues.”
CSS Recycling Equipment Solutions
Company Overview:
With 20 years of experience in our unique Australian and New Zealand region, CSS Recycling Equipment customises waste, organics, and scrap metal processing solutions, by taking a collaborative and consultative approach with their clients.
From the provision of ad hoc machinery and technology to fit an existing processing line, up to complete plant and materials handling solutions, CSS Recycling Equipment designs each solution specific to client’s requirements.
CSS Recycling Equipment takes a comprehensive approach, starting with on site reviews of existing processes, machinery and capability, analysis of client objectives, challenges, and end materials. By working closely with clients and with exclusive global suppliers to curate the best possible solutions, CSS becomes a trusted strategic partner, integrating technology, improving processes and bottom line results.
The technologies represented by CSS Recycling Equipment Solutions are sourced from around the world, are proven and reliable and have been tried and tested in our region. CSS Recycling Equipment specialises in processing all types of materials from C&D to C&I, from MSW to FOGO, Biomass and Wood, Compost and to hard to process waste.
Products and Services:
Specialising in all aspects of reduction, separation and recycling technology: • Complete consultative and collaborative plant design and delivery • Fuel Preparation Technology • Shredding • Screening • Air Separation • Baling and Shear Baling • Plastics Washing and Preparation • FOGO • Waste to Energy technology
Brands:
• 3Tek Scrap Metal technologies (USA) • Beier Machinery (China) • Ecostar Dynamic Screens (Italy) • Ecohog Air Separation Technologies (Northern Ireland) • Hammel Recyclingtechnik (Germany) • Jono Enviro (China) • Lindner Recyclingtech (Austria) • Vezzani (Italy)
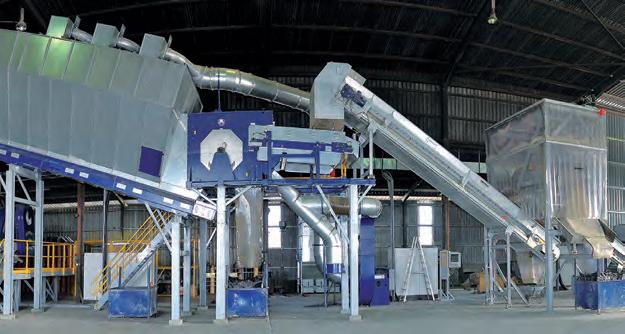
Core Capabilities:
Collaborate, consult, design, deliver and the supply of high quality equipment and plant solutions for C&D, C&I, Biomass, Organics, Wood Waste, FOGO, MSW, Scrap Metal industries.
Source innovative and strategic solutions both within and outside of our stable of equipment solutions, always with the client’s outcome as our focus.
Utilise our global relationships and local knowledge to deliver positive business outcomes for our clients and continually improving environmental solutions for Australia and New Zealand.
Specialists in: • hard to process waste • mobile and static processing solutions • manufacture of custom components • high quality and on budget projects
Contact Details:
CSS Recycling Solutions PO Box 359, Dee Why NSW 2099 Phone: 1800 644 978 Email: info@cssequipment.com.au Web: www.cssequipment.com.au
Komptech CEA
Company Overview:
Komptech CEA is the Australasian distributor of Komptech machinery and systems for the treatment and processing of solid waste and organics waste materials for recovery and recycling. Our product range includes over 30 different types of both mobile and stationary machines that cover all key processes in modern waste processing including: • Single-shaft and dual-shaft industrial shredders • Compost windrow turners for commercial operations • Star screen and trommel screen machines • Material separation equipment including windsifters, ballistic separators and stone contaminant separators • Stationary recycling system solutions including shredders, separators and screening machines
Brands:
• Rowan • Komptech
Core Capabilities:
With a specialized product portfolio that includes over thirty different types of machines covering all key processes in modern waste handling, a consultative guiding approach to solution development for customers, and full service aftersales support and parts, Komptech CEA has become a leading supplier to the recycling and waste processing industry.
Providing customer value is our focus as we strive to be the industry’s technological leader through continual innovation. Komptech CEA is dedicated to working with you to help you solve your waste problems and identify opportunities with comprehensive, detailed solutions driven by world-class technology.
Contact Details:
Sydney
6 Skyline Crescent Horningsea Park, NSW 2171 1300 788 757 www.komptechcea.com.au
Melbourne
109 Merola Way Campbellfield, VIC 3061 1300 788 757 www.komptechcea.com.au
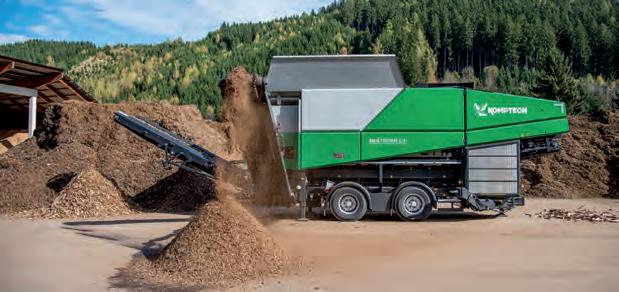
Brisbane
11 Kiln St, Darra 4076 1300 788 757 www.komptechcea.com.au
Adelaide
260 Cormack Rd Wingfield, SA 5013 1300 788 757 www.komptechcea.com.au 1300 788 757 www.komptechcea.com.au
Auckland
96 Gavin Street Mt Wellington 1060 1300 788 757 www.komptechcea.com.au
Key Contacts:
Craig Cosgrove
Product Manager 0417 320 082 c.cosgrove@cea.net.au
Simon Humphris
Product Manager 0478 196 263 s.humphris@cea.net.au
Davis Earthmoving & Quarrying Pty Ltd
Davis is a leader in mobile waste processing in NSW. Established in 1975, we are proudly Australian, family-owned and operated, contracting state-wide in NSW. We offer services in Green Waste Recycling, Glass & Concrete Recycling, C&D Shredding, Land Clearing, Mulching, Trommel Screening, Haulage, Recycled Products & Landscape Supplies. We process over a quarter of a million tonnes of material per annum. For over 45 years, Davis has successfully completed tens of thousands of government, civil and commercial projects, and are regular contractors for Councils in NSW. We have a diverse range of 100 pieces of Plant & Equipment in our privately owned fleet for hire or contract, all equipment is available in-house. We operate our own service centre for scheduled maintenance and field repairs, this guarantees safety, quality and maximum efficiency. For many years we have been proudly delivering high rates of resource recovery. We process, supply and deliver quality materials to the community, using innovative and environmentally responsible solutions. CEO Eric Davis has in-depth knowledge and experience in sustainable recycling. If we all manage the worlds resources better and recover materials from waste to be repurposed, we can conserve our world’s natural resources, and do our bit to transform the way the world values waste.
Products and Services:
• Green Waste Recycling • Forest Mulching, Timber & Stump
Grinding • Land Clearing, Road Widening &
Forestry • Crushing & Concrete Recycling • Screening • Low Speed, High Speed, C&D
Shredding • Glass Recycling • Quality Recycled Landscaping Supplies • Plant & Equipment Hire • Bulk & Heavy Haulage
For hire:
• Low Speed Shredders; Komptech • Horizontal Grinders; Diamond Z,
Peterson • Mobile Crushers; Rubblemaster, Metso • Soil & Trommel Screens; Pronar, Metso • Picking Stations; Kiverco • Forestry Mulchers; FAE • Excavators 1.8 to 46 tonne; CAT,
Komatsu • Dozers • Rollers, Compactors & Drotts • Wheel & Track Loaders
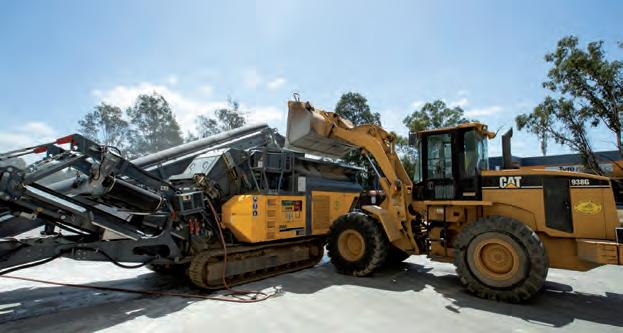
Core Capabilities:
Davis Earthmoving offers reliable, high-powered, mobile waste processing equipment for hire or contract in NSW. We deliver high-volume production to meet client’s varied needs and specifications. Our Low Speed Shredder processes heavy C&D, logs, palms, carpet, tyres, mattresses. We have equipment available for forestry mulching, subdivisions, road constructions, grubbing, firebreaks. Horizontal Grinders process green waste, C&D, timber, stumps, logs. Mobile and Trommel Screens process soil, timber, green waste. Our Crushers recycle concrete, brick, rock and glass. Our aim is to efficiently recover environmentally sustainable and quality recycled products for beneficial reuse in a circular economy.
Contact Details:
Davis Earthmoving & Quarrying Pty Ltd PO BOX 19 TERREY HILLS NSW 2084 Phone: (02) 9450 2288 Email: davisem@davisem.com.au Web: davisem.com.au
Hitachi Zosen Inova
Company Overview:
Hitachi Zosen Inova (HZI) is a global leader in energy from waste (EfW), anaerobic digestion (AD) and Powerto-Gas, acting as an engineering, procurement and construction (EPC) contractor delivering complete turnkey plants and system solutions for energy recovery from waste.
Since 2015, HZI Australia, a 100% subsidiary of HZI, is developing new projects in Australia, New Zealand, and the South Pacific. Its first project, the 300,000 tpy East Rockingham WtE is now in construction and will start commercial operation in Dec 2022.
Products/Services:
• Thermal treatment of residual waste, energy recovery, flue gas treatment, and residue recycling • Dry anaerobic digestion of food & green resources, renewable power production, biogas upgrading to biomethane and bio-CNG • Power-to-Gas for volatile electricity into renewable synthetic gas for a
carbon-neutral economy • Development, Design, Build,
Finance, Own, Operation &
Maintenance
Brands:
• Hitachi Zosen • Aquaroll, DYNOR, Kompogas, • HZI Etogas, HZI DryMining
Core Capabilities:
Energy from Waste, Renewable Gas, Project Development, EPC, O&M, Asset Management
Recent Projects/Installations:
DUBAI ENERGY FROM WASTE (EFW) – START OF OPERATIONS IN 2024 Warsan, Dubai, United Arab Emirates
The world’s largest EfW processing up to 1,89 mill tpy of non-recyclable municipal solid waste from the Dubai area and producing 171MW of electricity. To be designed, built and commissioned by a JV partnership between HZI and BESIX Group with a minimum of 30 years’ operation and inclusive of minority ownership. Visit https://www.hz-inova.com/projects/ dubai-uae/
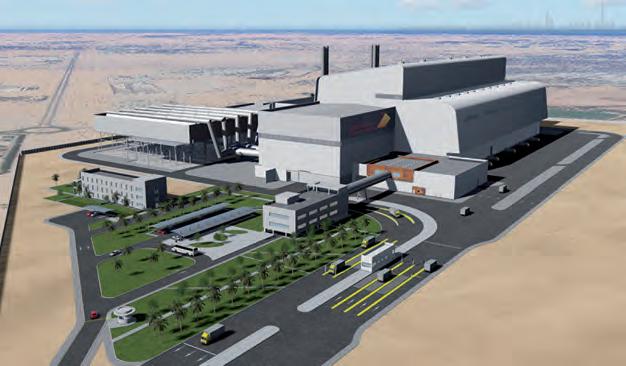
ZUFFENHAUSEN ANAEROBIC DIGESTION PLANT – START OF OPERATIONS IN 2023 Baden-Württemberg, Germany
A dry anaerobic digestion plant using HZI’s Kompogas® technology to process 35,000 tpy of source-separated organic waste from the Stuttgart urban area into biogas, high-grade liquid fertilizer and compost. The bulk of the biogas will be used at the manufacturing plant of a well-known automaker to produce electricity and heat for direct use on site. Visit https://www.hz-inova.com/ kompogas-for-the-future/
Contact Details:
Hitachi Zosen Inova Australia Pty Ltd
Level 17, 40 Mount Street North Sydney, NSW 2060 Phone: 02-8003 4110 Email: info@hz-inova.com Web site: www.inova.com
Key Contacts:
Merlo Group
Company Overview:
Merlo is an Italian-based industrial group that designs, manufactures and markets its products under the Merlo and Treemme brands, both synonymous with quality the world over, with a commitment to respecting the environment.
All the products in the Merlo range have the largest cabin and operator space available to the Australian market, which is characterised by innovation, technology and reliability. They are distinctive characteristics of the Merlo Group that have earned the trust of the world telehandler markets.
Since its origins, the Merlo Group has always had an international approach in terms of product and business; this global vision of the market today generates the export of more than 90% of production. Today the Merlo Group’s worldwide presence is guaranteed by a direct organisation of six branches (France, Germany, England, Spain, Poland and Australia), by a distribution network of over 50 importers and 800 dealers, offering widespread coverage in terms of sales, service and spare parts. The Merlo Group’s international approach continues to increase its global presence, guaranteeing proximity to customers and opening up new markets by introducing hightech products with superior safety standards.
The Merlo Group’s products are created from the deep experience gained in over 50 years of history; they satisfy every market and customer need.
AUSTRALIA
Products & Services:
The Merlo brand has always been synonymous with cuttingedge technology in the field of telehandlers, operating machines and telescopic boom tractors.
Core Capabilities:
Merlo’s advanced technology has become the driving force behind a development that has made it possible to look beyond daily business. Safety, comfort, performance are the key words. As a result, every machine rises the bar and sets a new standard in terms of design, power, care for man and the environment. This winning attitude translates into high integration into production processes, modern construction systems, process automation, revolutionary integrated electronic systems, in robotised processes and much more.
Our commitment to maintaining an ever-closer relationship with our customers is reflected in our ongoing training and updating of programmes, our technical support services, and the trusted relationship with our extended dealer network. The results of all this are compact machines, with ease of operation, that ensures the unrivalled operating features of, comfort, efficiency and above all, unparalleled safety. This is the strength of the Merlo product. Merlo Group Australia - TRUSTED
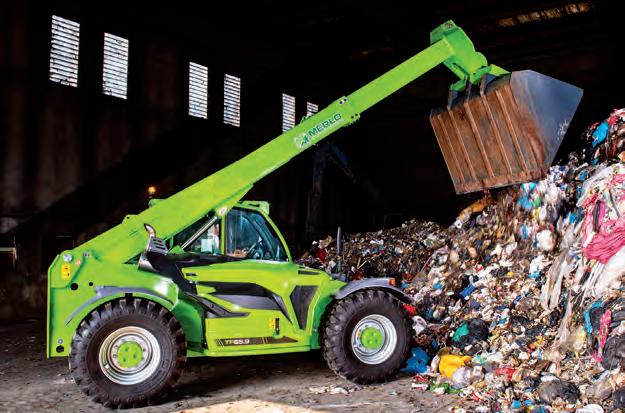
Contact Details:
Merlo Group Australia Pty Ltd
120-124 Toongabbie Rd, Girraween NSW 2145 Phone: 1300 657 325 Email: sales@merloaustralia.com.au Web: https://www.merlo.com
STEINERT
Company Overview:
STEINERT is a manufacturer of superior magnetic separation and state-ofthe-art sensor sorting equipment. Headquartered in Cologne, Germany with subsidiaries in Australia, USA, Brazil, STEINERT supplies the waste, metal recycling and mining industry globally. With over 130 years of history STEINERT is at the forefront of technology and innovation with a focus on quality, reliability and continuous research.
STEINERT’s presence in Australia encompasses a manufacturing facility in Melbourne, Victoria where the Australian designed and made magnets originate. STEINERT’s Test Facility in Perth, Western Australia provides customers with the opportunity to test small and large samples under conditions that very closely match real life scenarios. Customers benefit from the very latest findings and technological advancements in a tried and tested environment, utilising the latest STEINERT sensor-based combination sorting solutions.
STEINERT’s Service Technicians are based on both the east coast and west coast of Australia and have the capability to support your service requirements around the country, both on-site and remotely.
This strong presence ensures best support of the magnetic and sensor sorting equipment for the customers in Australia.
Products & Services:
• Overhead suspension magnets, electric and permanent • Magnetic drums, electric and permanent • Eddy current separators • Near Infrared sorters • Optical sorters • Induction sensor sorters • X-ray transmission/fluorescence sensor sorters • Combination sensor sorters • Service & maintenance
Brands:
• STEINERT MAGV/MAGX suspension electromagnet • STEINERT MAGP permanent suspension magnet • STEINERT MTE electric drum • STEINERT EddyC eddy current separator • STEINERT ISS induction sensor sorting system • STEINERT KSS combination sensor sorting system • UniSort PR EVO 5.0 NIR sensor sorting system
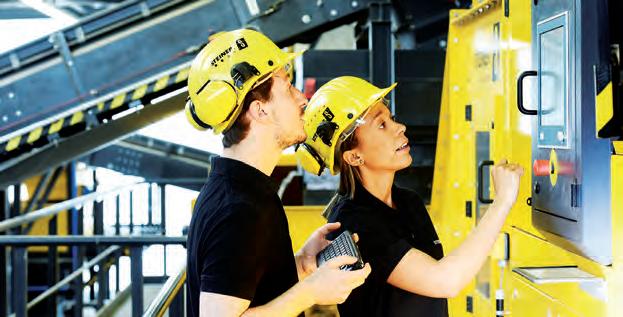
Core Capabilities:
We support customers from the project design stage with application knowledge, material testing in our test facilities, process consultation, supply of equipment, on-site commissioning to continuous service support, maintenance and repairs from our Australian team.
Our manufacturing facility in Melbourne enables us to hold critical spare parts for our equipment and perform full repairs and refurbishments in local response times. Together with our team of service technicians we are able to provide a high standard of after-care for our equipment.
Contact Details:
STEINERT Australia Pty Ltd
14 Longstaff Road, Bayswater VIC 3153 P: +61 3 8720 0800 E: sales@steinert.com.au W: www.steinert.com.au
Key Contacts:
Applied Machinery
Contact Details:
55-61 Nissan Drive Dandenong VIC 3175 Phone: 03 9706 8066 Email: sales@appliedmachinery.com.au Web: www.appliedmachinery.com.au
Company Overview:
Applied Machinery is one of Australia’s largest suppliers of quality recycling machinery. Over 30 years industry experience enables us to deliver turnkey solutions for all manner of recycling applications across Australia.
Products and Services:
• Shredders and granulators • Plastic washing, tyre, and e-waste recycling plants • Repelletising systems/screen changers • Polystyrene recycling machines
Brands:
• Genox • Polystar • Fimic • Greenmax
Core Capabilities:
Applied Machinery has the capability to service the smallest single machine requirement, through to the largest of multi-site, staged installations and complete recycling line, turn-key projects. We supply some of Australia’s largest recycling organisations. A wide range of shredders and granulators are always in stock for quick delivery.
Recent Projects/Installations:
PORT PLASTICS Port Macquarie
Polystar Repelletising system and Genox large format shredder to drive recycling operations in the Port Macquarie region and reduce the need for transport of recyclables to metropolitan centres.
Australasian Specialty Coatings
that allows for bespoke designs for your particular needs.
Contact Details:
ASC Head Office
1/14 Chicago Avenue Blacktown, NSW 2148 Phone: 02 8840 8888 Email: enquiries@acoatings.com.au Web: http://ascoatings.com.au
Company Overview:
ASC is a team of experienced coating and flooring professionals. We specialise in repairing and coating concrete and steel surfaces in harsh environments – waste handling, tipping sheds, chemical storage and high traffic surfaces.
We are fully certified to ISO 9001, ISO 14001, and AS 4801 Standards.
When you call in ASC you get a professional, reliable team dedicated to solving your problems and delivering the best outcome, on time. We have a solutions-oriented approach
Products/Services:
• Tipping Shed Floor Resurfacing • Chemical Bund Coating & Lining • Concrete Repair & Remediation • Corrosion Prevention Coatings • High Traffic Surfaces • Leachate Resistant Materials • High Grip & Anti-Slip Coatings • Waterproof Membranes • Tank Lining • Acid Resistant Coatings • Expansion Joint Rebuilding & Sealing • Water Treatment Plant Coatings
Recent Projects/Installations:
TIPPING SHED FLOOR RESURFACING Banksmeadow, NSW
Remediation of Eroded Concrete Slab 1500m² Leachate-Resistant Floor Surface
CHEMICAL STORAGE AND PUMPING BUND Lidcombe, NSW
Acid & Chemical Resistant Bund Re-lining Full Remediation of Bund Internal Surfaces
Company Overview:
Diverseco
• Truck wheel washes for EPA and road safety compliance. • Automated waste sortation systems: comprehensive and completely automated robotic sortation systems for MRFs.
As one of Australia’s leading measurement and automation solutions providers, we at Diverseco pride ourselves on the sheer scope of our problem-solving expertise and supply of industry leading innovative technologies. We are heavily involved across a wide range of industries, with a comprehensive solutions portfolio specific for the waste management industry that includes both driver-specific solutions and robotic automation solutions for material recovery facilities.
Products and Services: Brands:
• Waste Robotics • BinWeigh
Core Capabilities:
At Diverseco, our core capabilities reside in our ongoing ability to meet and exceed customer requirements through our extensive problem-solving resources: we are ideal partners for any organisation looking to turn their operational problems into new, profitable capabilities.
• Waste vehicle on-board payload optimisation and overload monitoring (Chain of Responsibility and legal-fortrade operations). • Weighbridges and portable truck scales for accurate vehicle weighing and accountability.
Contact Details:
3309 Logan Road Underwood, QLD, 4119 M: 1300 069 970 E: onboardsolutions@diverseco.com.au W: diverseco.com.au
Spartel Pty Ltd
FABCOM® Organics Under Control©
www.FAB-COM.com.au
Contact Details:
aspects organic waste processing from waste generation to soil beneficiation products, technology, process data processing and control, odour prevention and control
Harrie - 0414 37 66 99 E: info@spartel.com.au W: www.FAB-COM.com.au
Company Overview:
Spartel Pty Ltd was founded in 1995 by Dr Harrie Hofstede, specialist waste management scientist in waste composting and pollution control. The company has a consulting arm, Hofstede & Associates, and waste technology R&D programme under the umbrella. The R&D has resulted in six patents in international markets. We have designed and developed two main large-scale composting systems under the FABCOM® Brand. FABCOM® Tunnels and the FABCOM® MAF system.
Core Capabilities: Products and Services:
• FABCOM® Tunnel compost plants • FABCOM® MAF composting system • Wireless data transmission and processing over a 2 km radius • Aeration controlled by process data • Remote access process control • Design and construct of compost plants • Development and optimisation of compost process and products • ODOROV™ effective odour control agent for organic waste • High nitrogen composts (4% N)
Recent Projects/Installations: :
FABCOM® MAF SUEZ Newcastle
Raymond Terrace NSW Dedicated FABCOM® MAF aeration system for post Bedminster compost maturation & drying; Capacity 10,000 tpa
ResourceCo
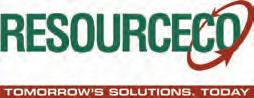
Contact Details:
ResourceCo Head Office
Level 1, 162 Fullarton Road Rose Park, SA 5067 Phone: (08) 8406 0300 Email: enquiries@resourceco.com.au Web: www.resourceco.com.au
Company Overview:
ResourceCo (RC) is a global leader in the recovery and re-manufacture of primary resources, extracting maximum value from materials otherwise destined for landfill.
Recent Projects/Installations:
ESKINE PARK PLANT
Operations commenced at Tyrecycle’s (RC’s tyre recycling division) new multi-million-dollar plant at Erskine Park in Sydney , producing in excess of 10,000 tonnes of rubber crumb for the construction industry, generating 40,000 tonnes of TDF, and providing a local circular economy solution to rubber waste.
Products and Services:
• C&D & C&I Recycling • Disposal, Treatment & Management of Contaminated Soils • Renewable Energy & Alternative
Fuels • Tyre & Waste Rubber Recycling • Recycled Construction Material
Brands:
• ResourceCo Pty Ltd • Southern Waste ResourceCo • Cleanaway-ResourceCo • SUEZ-ResourceCo • Tyrecycle Pty Ltd
Contact Details:
Hyva Pacific
A fleet of service vehicles offers on-site solutions for all hydraulic, fabrication, electrical, air-conditioning and engineering requirements.
Products and Services:
72 Glenwood Drive Thornton, NSW, 2322 Phone: 02 4966 3777 Email: hyvapacific@hyva.com Web: www.hyva.com
Company Overview:
Hyva Pacific is a leading provider of innovative and highly efficient transport solutions for the commercial vehicle and environmental service industries. Its products are used worldwide across a range of sectors including transport, construction, mining, materials handling and environmental services providers.
HSR Southern Cross is the HYVA distributor for NSW and the exclusive Australian HYVA PRESS Waste Handling Equipment distributor. HSRSX is strategically located in Western Sydney. • Waste Handling Equipment (Rear loaders / Compactors) • Hookloaders • Skiploaders • Vehicle Loading Cranes
Core Capabilities:
Hyva /HSRSX is the ‘one stop shop’ for the commercial vehicle and waste handling industry, providing a wide range of high-quality equipment including installation, engineering, service and repair in our workshops or onsite.
Contact Details:
35 Holbeche Rd, Arndell Park NSW 2148 Phone: 02 9725 3347 Email: admin@hsrsx.com.au Web: www.hsrsx.com.au
Komatsu Forest
Company Overview:
Komatsu Forest is one of the world’s largest manufacturers of forest machines. We are represented on six world continents by a network of dealers and our own sales companies.
Komatsu Forest’s head office is in Umeå, Sweden, and we have two manufacturing units, in Sweden and the USA. Our own sales companies are located in Sweden, Norway, Finland, Germany, Austria, France, United Kingdom, Russia, USA, Australia and Brazil, and our network of dealers represent us on all other important forestry markets.
Our extensive service organisation takes care of the machines, ensuring that they perform their best throughout their service lives. We have workshops throughout the world, service vehicles for quick assistance, in-house machine and methodology instructors to help maximise productivity, and support functions for everything related to our machines and services.
Products and Services:
increase productivity while simplifying the working day for you as a machine owner.
We combine all our services under our Customer Care concept. This is our promise that you will enjoy the benefits of Komatsu Forest’s investments in research, development, servicing, support, logistics and innovative services. These combined resources are at the very heart of Komatsu Forest’s offer.
Our goal is to make your working day as safe, problem-free and profitable as possible, no matter where in the world you operate. Let us show you that by choosing Komatsu, peace of mind and accessibility can become a natural part of your working day.
Brands
• Komatsu • Peterson • TimberPro
Core Capabilities:
Our world-wide network of highly trained service professionals is ready for you.
We know how important it is to be close to service and maintenance when help is needed. Therefore, we have a market-wide network of highly trained service professionals that knows your Komatsu, Peterson & Timberpro machine in every detail. They are, in turn, in constant contact with the Komatsu Forest head office so your voice or needs are never more than a call away from our collective expertise. Furthermore, we are constantly developing new services that will help you in your everyday work.
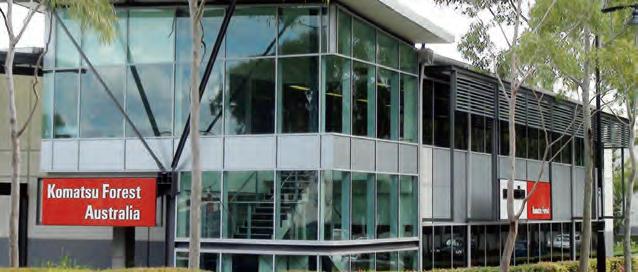
We offer:
• Workshops and field services throughout Australia & New Zealand • Well qualified personnel with expert knowledge of Komatsu & affiliated machines • Field Service that enables us to remain close to you and your
machine • Support and maintenance throughout your machine’s service life • Maintenance agreements with fixed maintenance prices and other benefits
Contact Details:
AUSTRALIA
Komatsu Forest Pty Ltd 4/11 Ave of Americas Newington, NSW 2127 T : +61 2 9647 3600 E : info.au@komatsuforest.com
NEW ZEALAND
Komatsu Forest Pty Ltd 15C Hyland Cres Rotorua, New Zealand M: John Kosar + 64 274 865 844 M: Paul Roche + 64 21 350 747
How Macpresse MAC112 extends landfill life
A landfill’s life can be extended using the Macpresse MAC112.
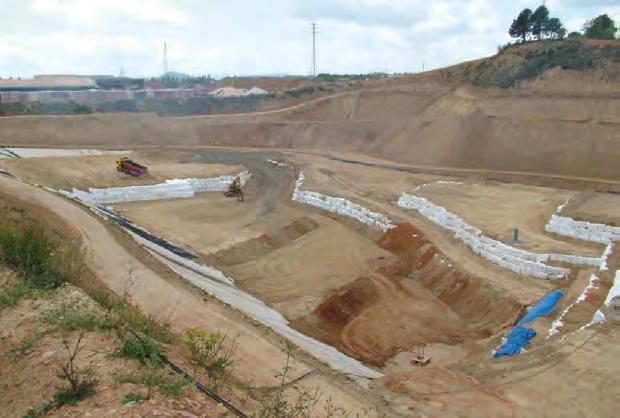
By Inside Waste
EVERY solid waste entity deals with the same problems; litter control, vermin, rising operational expenses and ever diminishing space in landfills. Not every facility meets those challenges in the same way and the solid waste division of St Lucie County, Florida, was determined to find a long-term costeffective solution.
The fundamental answer to many of the problems it faced was baling of solid waste, a trend that is gaining significant traction within the industry.
Leo Cordeiro, solid waste manager at St Lucie Solid Waste Authority, investigated whether to consider baling garbage, and it didn’t take very long to come up with just the opposite question “why aren’t people doing it?”.
“When you look at the benefits, it was so obvious that what we’re doing is just so defunct, there’s no comparison, no reason not to do it,” he said.
“We have 1100 pounds of garbage in every cubic yard of air space (656 kg to every 1 m3).
“And when we look at baling it, we can do close to double the volume and reduce cover, litter and leaching. You’ve got to ask yourself why am I not doing it?”
A new Solid Waste Facility was designed with separate unloading and baling areas, establishing an effective and controllable workflow.
The power behind the St Lucie facility, were dual Macpresse MAC 112 balers.
The MAC 112 has been calculated to increase productivity, reduce operation costs with much lower kilowatts per hour, yet producing up to 70 tonnes of baled material per hour depending upon moisture content as well as the infeed density.
How are these production numbers achieved? The difference is in the design. The overall layout is the product of 50 years of Macpresse experience.
The efficient material flow path and the horizontal baler orientation increase production speed and make bale sizing easy to change.
Solid waste is delivered by the staged conveyor belt system. The conveyor in the pit transports the material to the inclined conveyor, which travels at a slightly higher speed. This delivery technique spreads out the material more evenly, thereby increasing system production. Supplied in Australia by Cemec Techonologies, the 112 incorporates a single ram continuous feed design, bringing efficiency and producing high hourly production rates.
Powering the strong compaction ram is a high-pressure hydraulic system designed around Rexroth variable flow piston pumps and high efficiency electric motors, allowing one or both motors to operate independently.
Delivering the hydraulic energy to the baler is the patented hydraulic manifold block, which reduces hydraulic shock and is designed to keep oil temperatures consistently low to enhance the hydraulic functions. Hydraulic and mechanical forces applied to the material in the chamber produce dense square bales.
During compression, leachate is gathered by conveyor systems, dust is mediated by the filtration system, and both are reintroduced into the waste stream.
Once sized, the bales are cut with the two-stage serrated shear.
This design eliminates shear shock and the need for a pre-press flap apparatus.
The compressed material is then tied by the five-wire mechanism, which positively feeds each wire into the twister assembly preventing missed wires and wire ties. All five wires are tied simultaneously to reduce tying time.
This entire system is controlled from an electrical control panel. All functions of the MAC 112 are easily executed using Programmable Logic Control (PLC) technology which also offers an optional Supervisor system that provides real time diagnostic functions with data exported into excel for cost analysis.
Maintenance considerations are an integral part of the design of the MAC 112, with motor and pump areas that can be exposed, and panels opening wide for maintenance issues. Safety was not sacrificed in the interest of speed or flexibility.
Has the Macpresse total solution design been effective? In 1989 it was predicted that in the year 2002 the St Lucie landfill would be full.
Through good management and the implementation of baling, the landfill now has life expectancy to 2050 and capacity of 13,886,728 cubic yards.
“Here at St Lucie County the baling process is going to save us over ¼ million dollars a year in operation costs by eliminating compactors scheduled every three years, operator salary, and diesel fuel at 60 gallons per day (273 ltrs),” said plant superintendent Ron Roberts.
“The biggest saving is in daily cover material.
“Operators from the waste companies are in the landfill 80 per cent less time, residents don’t see numerous birds or blowing litter – all that has been solved with baling.”
“In the research we did, there were two balers to choose from,” said Cordeiro. “After we looked at Macpresse they told us, ‘we’ll deliver the machine, it’s not your machine until we have it running, and we will guarantee density’. As well as being $250,000 cheaper – you’ve got to be foolish not to look at it.”
“Through the whole design process and construction of our facility, Macpresse were there 100 per cent of the way, working with us not against us.
“Giving us the best, we were looking for and trying to achieve the best design in the US of a baling facility,” said Roberts. iw
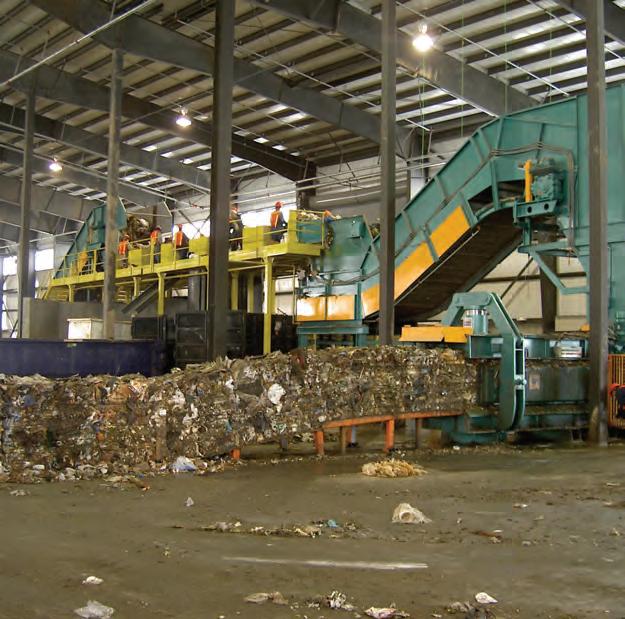
Specialist doors for Energy from Waste plants
By Inside Waste
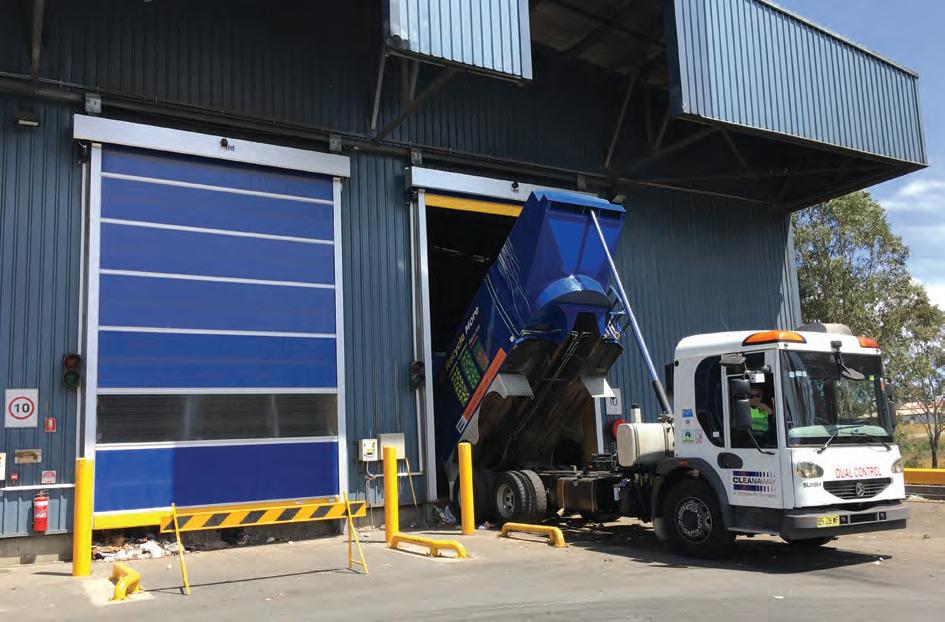
THE Energy from Waste (EfW) industry is growing in Australia, as are waste recycling plants and FOGO processing. These plants are becoming more sophisticated with the processing, and the containment of noise and air pollution is important. With large doorways for ingress of trucks and other vehicles, pollutants can be a challenge to contain.
DMF International supplies specialist high-speed doors that are designed for high frequency of use and are efficient in sealing the doorway against dust, noise and odours.
An additional challenge for these plants can be the need for big opening doorways, and exposure to wind forces, and/or to corrosive contaminants.
There are a number of elements that need to be incorporated when choosing the right door. Designers and operators need to consider the following attributes: • What are the key features to be controlled, such as traffic flow, dust, noise, odour, draft etc? • What type of traffic uses the doorway and therefore what are the appropriate forms of activation for the doors? • How many times per day is the door opened and closed, and what is the desired door speed? • Is the door exposed to corrosive substances? • What is the anticipated wind loading on the door? • Is the doorway size suitable for the applicable traffic types and does the
building structure accommodate the installation of a specialist door? • Does the door need to provide a level of security? • How serviceable are the doors, and can the supplier react quickly to service and repair requirements?
DMF can provide custommanufactured doors to suit a variety of applications. Over the past few years, it has installed doors into a variety of heavy industrial applications, including waste and recycling plants.
“There are a number of door types that we can supply, depending on the application,” said DMF director Stephen Fell. “We carefully consider all aspects of the application, and may not present the cheapest solution, but one that we know will work well for a long time.”
All DMF doors are custom made to size and specification, either in the Sydney factory, or from one of its long-term partners in Europe, including Efaflex Gmbh, a Germanbased company that specialises in the design and manufacture of high-speed doors.
The door blades can be made from durable reinforced flexible PVC in single or dual skin design, through to 100mm-thick, insulated sections provide a high level of noise insulation.
Door speeds can range from 0.5m/ sec up to 2m/sec, depending on the model and door size. Wind speed capacity is also critical for large doorways, and some door models can accommodate more than 150km/h wind force, while retaining full operation.
These doors are designed to perform hundreds of cycles per day, and there are many forms of activation sensors that can be offered, depending on the traffic types and flow. From magnetic induction floor loops to infra-red motion sensors, or manual control from a plant room or traffic management system, the doors need to be well automated to open and close to maximise the effectiveness of sealing the doorway.
The safety features of these doors are paramount. All doors come with the required safety sensors to ensure that not only operators are kept safe, but that the door, being critical to the plant’s operation, is well protected. Various forms of other safety sensors may include photo-electric lights beams, full light beam curtains, infrared or laser sensing, all which prevent the door from closing on an object. iw
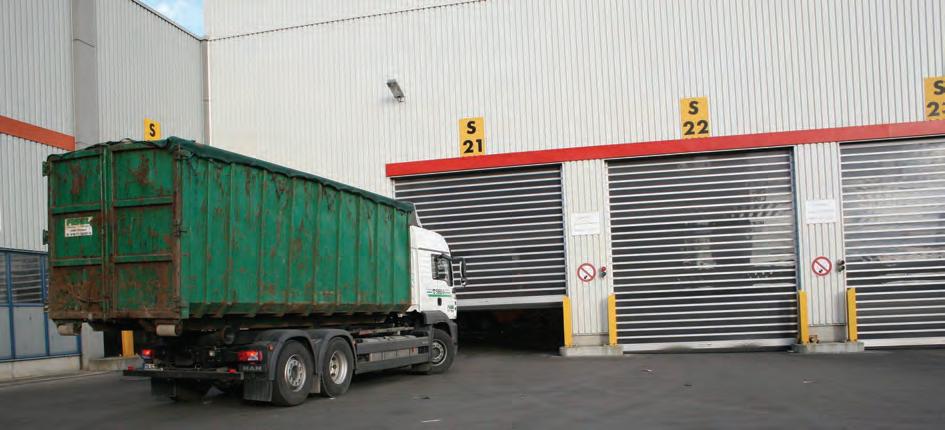
The size of a doorway is important when unloading waste inside a facility. Wind can be an issue when unloading and loading waste in MRFs.
Circularity – Integra’s progressive approach to recycled waste bins
Failure not an option for Energy from Waste sector
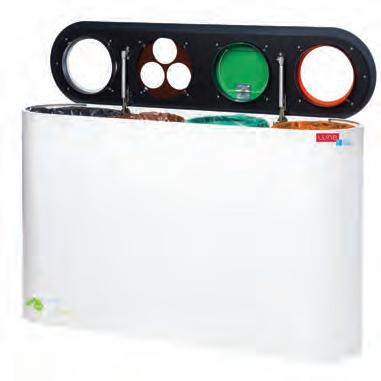
By Inside Waste
THE Lune Split and Paxa waste removal systems combine the principles of a circular economy – a cradle-to-cradle philosophy where all elements of a product are reused, recycled, or redeployed – to create sustainable recycle waste bins. These systems are designed by Lune, a subsidiary of Dutch manufacturer Brink Industrial, and manufactured by award-winning Australian advanced manufacturer and industrial designer Integra Systems under a digital licensing arrangement.
The bins help facilitate the separation of waste by doing more than just the standard three-type waste removal system commonly seen in Australia. With Split and Paxa, waste can be further separated into the categories of general waste, recycling, paper, cups, and organic waste. This ensures less waste goes to landfill and, consequently, more materials can be repurposed.
The Split range comes in four options – the Split 2, Split 3, Split 4 and Split 5 – depending on the number of waste streams required by any given organisation. All bin options are made from high-quality, powder-coated steel. They also feature gas springs in the lid for ergonomic, hygienic cleaning and emptying, and a modular, future-proof design to accommodate interchangeable waste stream inserts.
The Paxa range comes in a small option (23-litre capacity) and a large option (65-litre capacity). The lid types include sustainable sourced bamboo or 100 per cent recycled materials, and there is the option for a loose or dampened lid. Individual bins come linked by magnets, which means the bins can be easily rearranged or clustered as desired.
Every aspect of this partnership between Integra Systems and Lune, established late 2020, encompasses the principles of circularity. This means following a closed-loop system where materials are used and reused as efficiently as possible, and then recovered and regenerated into new products at their end-of-life. It also means manufacturing products in Australia for the Australian market to remove carbon emissions produced via international transport.
Circularity is reflected in the manufacturing of the Split and Paxa range through the use of sustainable and recycled materials, and the modular, future-proof design of the bins. This means that parts can be replaced or changed as needed, such as swapping out the inserts as the requirements of the organisation develop.
The bins can be refurbished if parts get damaged or have an issue. A new part is sent out to replace the old one, and the old one is then recycled and incorporated back into the making of a new product. This cradle-to-cradle cycle, as opposed to cradle-to-grave, eliminates the need for parts to go into landfill, allowing constant rejuvenation of old parts into new products. iw
If a part needs replacing a new one is sent, while the old part is then recycled.
By Inside Waste
THE main purpose for an emergency back-up system is to restore power during a grid failure. The Energy from Waste industry (EfW) demands reliable back-up energy solutions such as a diesel generator.
There are multiple processes critical to waste management and electricity generation. These processes could be adversely affected if there are any prolonged interruption due to an unscheduled grid failure.
Critical factors when selecting a back-up system are costs, minimising noise, and keeping the real estate footprint of the system as compact as possible.
Delivering a back-up diesel generator, especially for the EfW segment, involves several challenges, such as real estate constraints, rapid start-up along with performance and emissions issues.
This is why CAPS Australia has teamed up with KOHLER to deliver a custom Australian built system. The KOHLER brand, with 100 years’ experience in the power generation segment, delivers product where reliability together with performance and quality is a suitable solution for industries such as EfW.
The KD series, combined with local expertise and in-house engineering, and with the selection of innovative smart technologies exhibited in ancillary selection, such as patent air cooler design, CAPS Australia can deliver a solution for an upcoming facility where real estate versus scope requirement is a challenge.
Rapid start-ups with load acceptances in seconds involves a specialised locally built control system to manage the Engine Control Unit (ECU), together with a high pressurised fuel system that results in a smooth energy transition against a G3 performance class.
System reliability is further improved via the incorporation of redundant, dedicated battery systems to support starting and control logic. These are some of features locally engineered as an additional assurance to the segment.
A topic sometimes of less focus, due the diesel generator being termed as a back-up, is noise and flue emissions, which are also important for the EfW segment.
Where efficient cooling, together with acoustic design and elevated performance limits, the KD series delivers a compact system that meets acceptable industry levels.
Offering customised, competitive premium solution is important for CAPS Australia with product availability nearing 4600kVA. This is the highest in the market.
It also has sustainable energy such as battery storage, which is renewable or hybrid.
CAPS’ trained technician’s knowledge is continually updated, and they have the model-by-model knowledge to service or fix equipment.
Whether a customer has one generator or a complex system, the CAPS’ technicians will give the advice needed to ensure that there is continuous operation.
CAPS Australia also has a national network of more than 60 service technicians covering Australia who are available 24-hours a day, seven days a week. iw
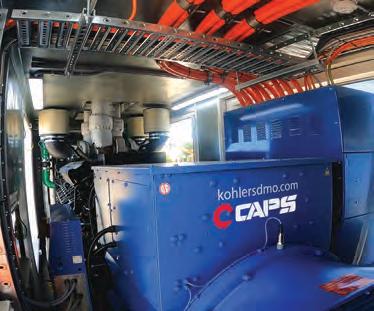
Two worlds collide for positive outcome
“I was very interested in the geological time scale and how we have entered ‘Anthropocene’, which is a new epoch shaped by the negative impacts on the planet caused by human activity which is thought to have started during the industrial revolution. That is a very big concern for me. That is why I am in the line of work I am in now, which is resource management.”
Priya Murthy knows what she wants in life and being involved in the waste sector ticks quite a few boxes – not in terms of working just to make a living, but also how it fits into her own philosophy in life.
Murthy has been with waste specialist Cleanaway for just over twoand-a-half years and during that time has been a resource recovery officer in the company’s solid waste services division.
Graduating with a double degree – a Bachelor of Science in Geology and Geophysics, and a Bachelor of Arts Philosophy – Murthy has found that both degrees are intertwined and complement one another in her chosen field. Something that is not obvious at first glance.
“People can be perplexed when I tell them I have two degrees that don’t seem that related,” she said. “They usually don’t see an immediate connection between the arts and the sciences. Notable ancient Greek philosophers were also prominent figures in the sciences such as mathematics and physics. I think philosophy is extremely important and the evolution of philosophical thought and theories over time have endowed us with a foundation of theories for modern day and futuristic thinking. I believe it should be implemented at any workplace and school, and at any level as idea generating and broadening perspectives will pave the way to open-mindedness and creativity.”
As for Murthy’s everyday work, it is varied and interesting. As a resource recovery officer, she is responsible for consulting with SMEs and helping them with their best practice waste management plans, which is designed to help them increase diversion of waste from landfill. Murthy says the goals don’t have to be overly ambitious, initially, but it doesn’t take clients long to realise that recycling can help keep their general waste costs down if done correctly.
As well as conducting site assessments, Murthy has been involved in several tasks, such as the EPA’s Bin Trim program. She has also been a project manager for several clients including one who is setting resource recovery goals. She has also worked with government on circular economy
projects and is currently working on a contamination management strategy project for another client.
Since beginning in the role, one issue that has become clear – and is ongoing and been mentioned by most sectors of the industry – is the lack of public knowledge about recycling and reuse of products. Murthy said this lack of knowledge can be anything from what is supposed to go in each bin at the kerbside, through to what a MRF is supposed to do and why contamination is such an issue at those refuse stations.
“There is a lack of knowledge in the general public, which is the fundamental baseline that we need to get right first,” she said. “And when it comes to these large infrastructure projects that can help boost the circular economy, the challenges are that we need more sponsorship and engagement, which also ties in with awareness and education. I think it
is an intertwined relationship. People don’t understand why contamination is a big issue in both the C&I and municipal sectors. It is a major issue and Cleanaway provides a lot of transparency in that regard.”
Where her interest in geology and geophysics has really come into play is her openness to use new technologies. Especially when it comes to end-of-life residual plastic waste.
“One of the things that stands out for me is the CAT-HTR processing facilities,” she said. “These convert end-of-life plastic back into the crude oil it was created from. This is of particular interest to me because of my background in the geosciences. This technology allows us to promote a closed-loop process for problematic plastics and minimises the requirement of extracting finite resources from underground.
“These kinds of facilities are a great option for plastics that have reached their end of life. I would love to see more infrastructure like this being built to be tied in with more product stewardship programs. Overall, the goal would be to get to the point where we could transition into using the term ‘resource’ instead of ‘waste’ and that comes from a successful circular economy model.
“Ambitious and all-encompassing sustainability goals are great to have, and are something to be worked towards, but they can’t be achieved without maintaining socio-ecological resilience. For that, we need to raise awareness about the technology out there and to also educate the general public.”
When it comes to working at Cleanaway, Murthy sees a bright future. She is interested in the commercial and industrial side of the company, mainly because she likes the challenge of working with multiple stakeholders. She finds this type of work challenging and rewarding.
“It is rewarding for me to help the customer – and all the stakeholders involved – implement solutions which will benefit the environment in their operations. That is what led me to this particular role.”
Murthy started her career at Cleanaway’s NSW Centre for Sustainability, which ticked all her boxes in terms of being a nurturing environment for graduates keen to learn and that independence of getting out in the field to site assessments on their own. It helps graduates become confident in project management and development, said Murthy. Cleanaway has helped Murthy grow her skill-set in the industry, which has furthered her passion, and this is why she is starting a master’s in environmental engineering in 2022.
“Cleanaway’s an innovative and progressive company and aligns with a lot of the values and ideas of where I want our country and our planet to head in the future,” she said. iw
Murthy has a particular interest in CAT-HTR processing facilities.
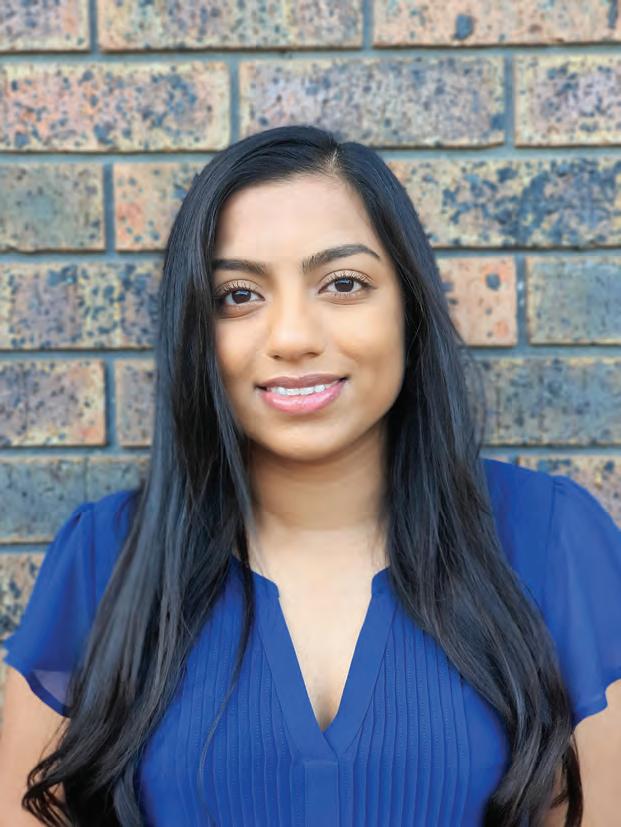
Pact Group SULO 2-Wheeled Mobile Garbage Bins
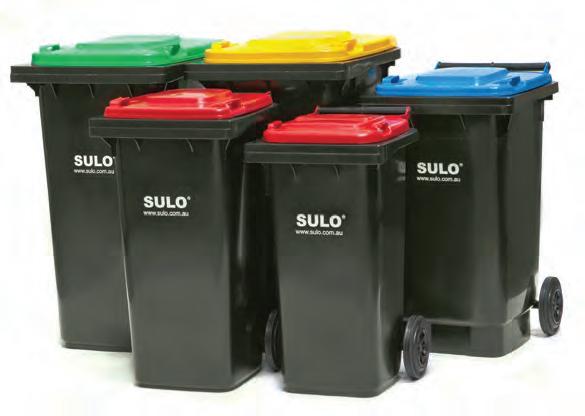
Source Separation Systems SULO 4-Wheeled Garbage Bins
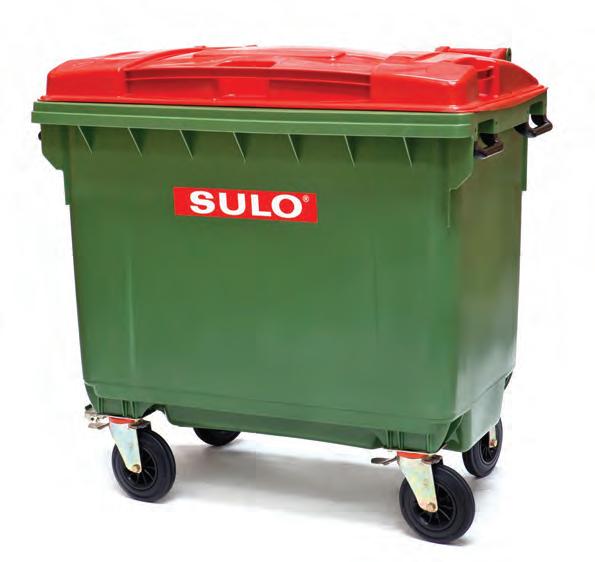
Kitchen Caddy
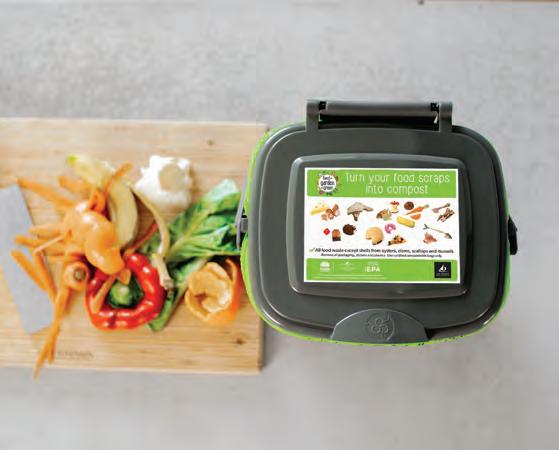
Overview: Made from up to 80% recycled content, SULO Mobile Garbage bins are manufactured in Australia in accordance with AS4123 & EN840 standards and can be customised to suit local government requirements. Weight(kg): 6.19 – 17 Capacity (Litres): 60 / 80 / 120 / 240 / 360 Options/Extras: Available in multiple colour and lid combinations and custom hot-foil printing and branding available. Price: Contact for Quote
Phone Number: 1300 364 388 Webpage: sulo.com.au Email: sulosales@pactgroup.com
Overview: With ergonomic easy-grip handles to optimise manoeuvrability our 4-wheeled bins have been engineered with safety in mind, allowing for easy handling and increased safety. Unit Dimensions(mm): 1070 x 1240 x 1330 (LxWxH) Weight(kg): 65 Capacity (Litres): 1100 Options/Extras: Available in multiple colour and lid combinations and custom hot-foil printing and branding available. Price: Contact for Quote
Phone Number: 1300 364 388 Webpage: sulo.com.au Email: sulosales@pactgroup.com
Unit Dimensions: Height 235mm Width 225mm Depth 225mm Weight: Approx 1 kg Capacity (in weight): Designed to hold approx. 7 Litres of Organic waste No. of units in range: Designed with a full colour Educational Inmould Label, this Kitchen Caddy is customised for each FO+GO Program. Several in stock standard educational graphics are also available. Finished product size: NA Options/Extras: Available with Australian Certified Compost-A-Pak compostable liners, and a range of external household collection bins. Price: Prices vary based on selections and quantities. More: Units are made in Australia from up to 100% Post-Consumer Recycled Content commonly collected from Roadside Council Bins.
Name: Melanie Barstow Phone Number: 02 49 537 644 Webpage: https://www.sourceseparationsystems.com.au/product/ kitchen-caddy Email: info@sourceseparationsystems.com.au
Paxa Waste Removal Systems
Unit Dimensions: Small (24 x 24 x 45cm) or Large (30 x 30 x 72cm) Capacity: Small (23L) or Large (65L) Weight: Small (6kg) or Large (10kg) No. of units in range: Two - Small or Large Finished product size: Small (25 x 25 x 46cm) or Large (31 x 31 x 73cm)
Options/Extras:
• Waste compartment options: general waste, recycling, paper, cups and organic waste • Lid type: made from durable bamboo or 100% recycled plastics • Lid options: loose lid, dampened lid or front door Price: RRP ex. GST - Small: $245 or Large: $325
More:
• Waste bins linked by magnets: can be rearranged, clustered or placed as single units • Designed and manufactured with the priciples of circular economy • Designed in the Netherlands, made in Australia
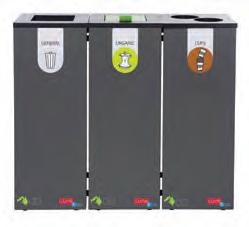
Name: Andrew Steed Phone Number: +61 3 9359 3133 Webpage: www.integratransform.com.au Email: integratransform@integrasystems.com.au
MGB’s 80-1100 Litre Capacity
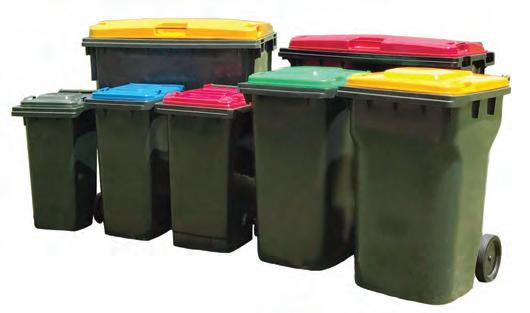
Lune by Integra Systems
Split Waste Removal Systems
Unit Dimensions: Split 2 (71 x 30 x 71 cm), Split 3 (98 x 30 x 71cm), Split 4 (120 x 30 x 71cm) or Split 5 (150 x 30 x 71cm) Capacity: Split 2 (2 x 30L = 60L), Split 3 (3 x 30L = 90L), Split 4 (4 x 30L = 120L) or Split 5 (5 x 30L = 150L) Weight: Split 2 (20kg), Split 3 (30kg), Split 4 (38kg) or Split 5 (48kg) No. of units in range: Four units - Split 2, Split 3, Split 4 and Split 5
Finished product size:
Split 2: 72 x 31 x 72cm; Split 3: 100 x 31 x 72cm; Split 4: 121 x 31 x 72cm; Split 5: 150 x 31 x 72cm Options/Extras: Waste options: general waste, recycling, paper, cups and organic waste Price: RRP ex. GST - Split 2: $980; Split 3: $1325; Split 4: $1620; Split 5: $2290
More:
• Made from high-quality powder coated steel • Can be upgraded, refurbished & repaired • Soft close lid for ergonomic cleaning and ease of emptying • Modular design with interchangeable waste stream inserts • Designed and manufactured with the priciples of circular economy • Designed in the Netherlands, made in Australia
Name: Andrew Steed Phone Number: +61 3 9359 3133 Webpage: www.integratransform.com.au Email: integratransform@integrasystems.com.au
Product/model name: MGB’s 80 litre to 1100 litre as well as Kitchen caddy’s Unit Dimensions: Various subject to applicable bin size Weight: Various subject to applicable bin size Capacity (in weight): 80, 120, 140, 240, 660 and 1100 litre. No. of units in range: 6 Finished product size: Various subject to applicable bin size Options/Extras: Bins can be customised to suit application Price: Various subject to applicable bin size More: Trident are the only company in Australia that have had the above bin capacities certified to AS 4123. This is the only way to ensure you receive a quality bin.
Name: Gary Silby Phone Number: 0413 031 165 Webpage: www.tridentaustralia.com Email: gary.silby@tridentaustralia.com
MultiSort Recycling Bins
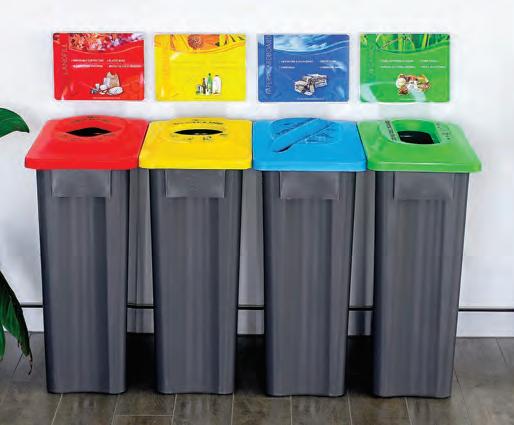
Unit Dimensions: Popular 60 Litre option. Height 654mm Width 290mm Depth 606mm. Weight: Approx 3 kg Capacity (in weight): Range of options from 40 Litres to 90 Litres per stream. No. of units in range: Extensive range mirroring popular waste streams, including Landfill, Organics, Recycling, Soft Plastics, Glass Only and 10c Refundables. Finished product size: Capacity can be customised depending on waste streams selected. Options/Extras: Available with Australian Compost-A-Pak compostable liners, an internal bag holder and trolley options. Price: Prices vary based on sizes and streams selected. More: 60 Litre Base is made in Australia from up to 100 per cent post-consumer recycled content commonly collected from Roadside Council Bins.
Name: Melanie Barstow Phone Number: 02 49 537 644 Webpage: https://www.sourceseparationsystems.com.au/product/multisort Email: info@sourceseparationsystems.com.au
Burning rubber and all that
MORNING Sir,
GREETINGS from the burning rubber capital of Oceania – and no, I’m not talking about doing doughnuts in the Aston Martin around the MCG after a few glasses of champers or martinis. No, I’m talking stockpiles of tyres – those oil-derived must-haves that keep the wheels of cars, industry, just about everything, turning.
Antipodean governments take this kind of thing very seriously. Back in the day when Britannia ruled the waves it was a case of sending off the used rubber to the nearest third-world country willing to take it in. Didn’t really matter where it ended up, as long as it wasn’t in our backyard.
Anyway, along came social responsibility and now those plans have been blown to smithereens. I don’t blame those countries for not wanting our rubbish anymore. Not only are they sick of us kicking the can (or tyre) down the road, but I think the guilt was building up for your average Ocker, too.
What does this mean for those in the industry, you ask? What indeed. Tyres can be a messy business at the best of times. They’re an ugly commodity, with an ugly history. Those running the show down here – Tyre Stewardship Australia, the Australian Tyre Recycling Association and the federal government, championed by the popular and effervescent Trevor Evans – all seem to be on the same page.
But like Whitechapel back in the day there is an undercurrent of scallywags and scoundrels who want to make a dollar or two on the sly – sort of like sly grogging, but instead of dodgy 90 proof gin that’d blow the socks off a welloiled booze-hound, they’re looking at literally burning rubber and damn the torpedoes, or most correctly, the environment.
Already discovered a plot by ne’er-do-wells scamming retailers out of their used spares, sticking them in a warehouse and then scarpering. How is this possible in the digital age, you ask, sir? In a time of CCTV cameras on what seems like every street corner, every citizen with a mini video recorder in their back pocket, and track and trace software, you think it would be easy to find out who these scoundrels are. Well, they’re smart. They use shell companies and cash. Yes, cash – something I haven’t used in a long time. Last time I visited my bank in the Cayman Islands they had a fit of laughter when I asked for 10 $100 bills. Wanted to hand them out to those in need on Barefoot Beach. Made me reminisce for the good old days when Oddjob and I had a run in at Fort Knox – good solid, hard, moolah. Mind you we are talking gold back then.
I certainly look forward to seeing how the industry will handle the new normal.
Yours
JB
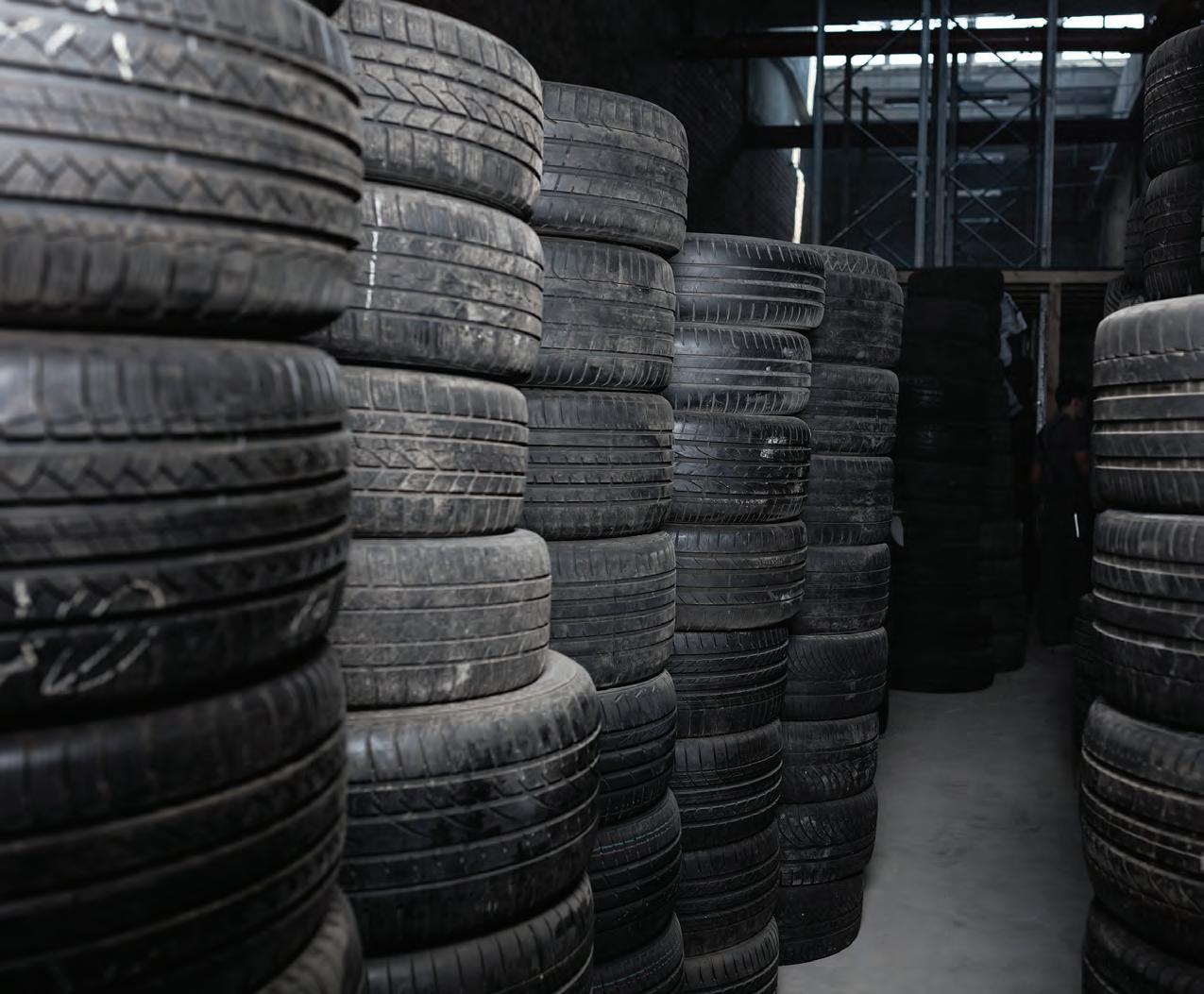