
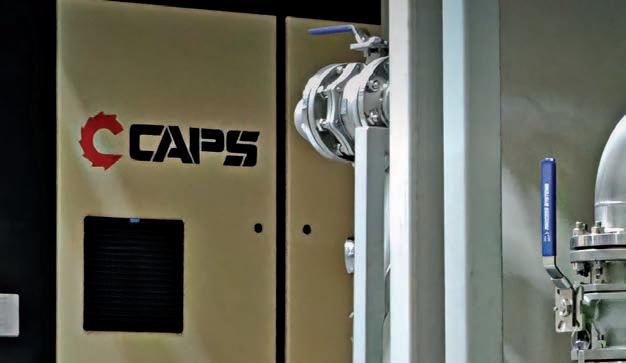
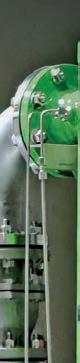
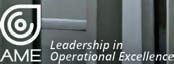
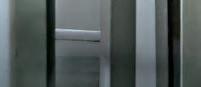
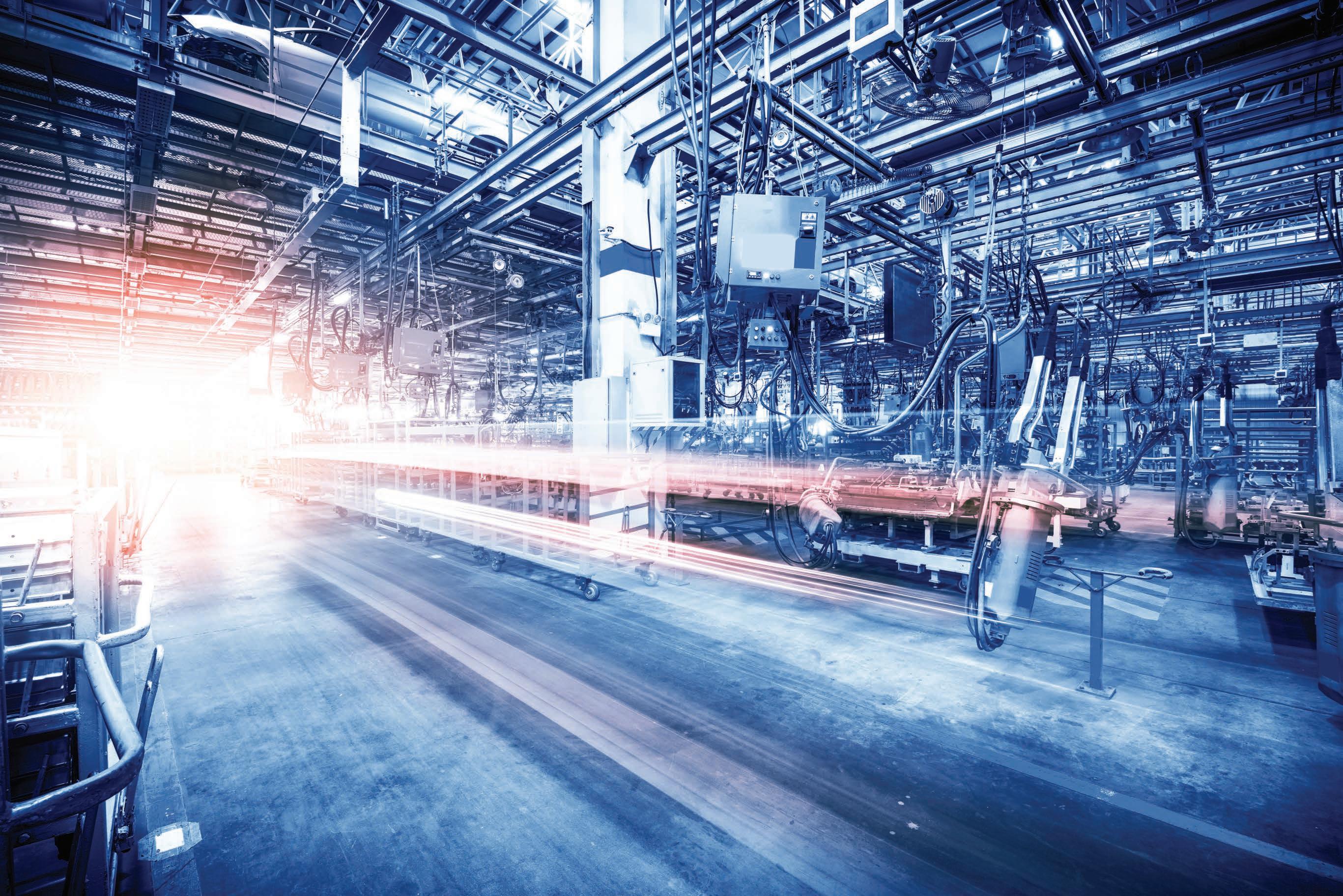



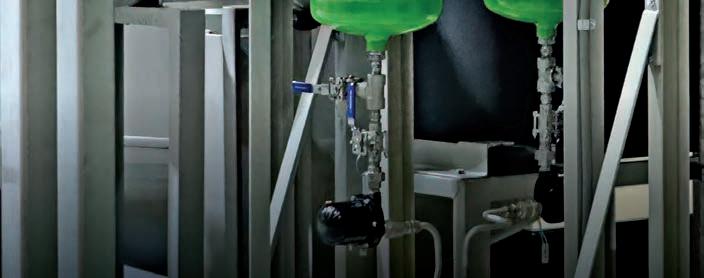
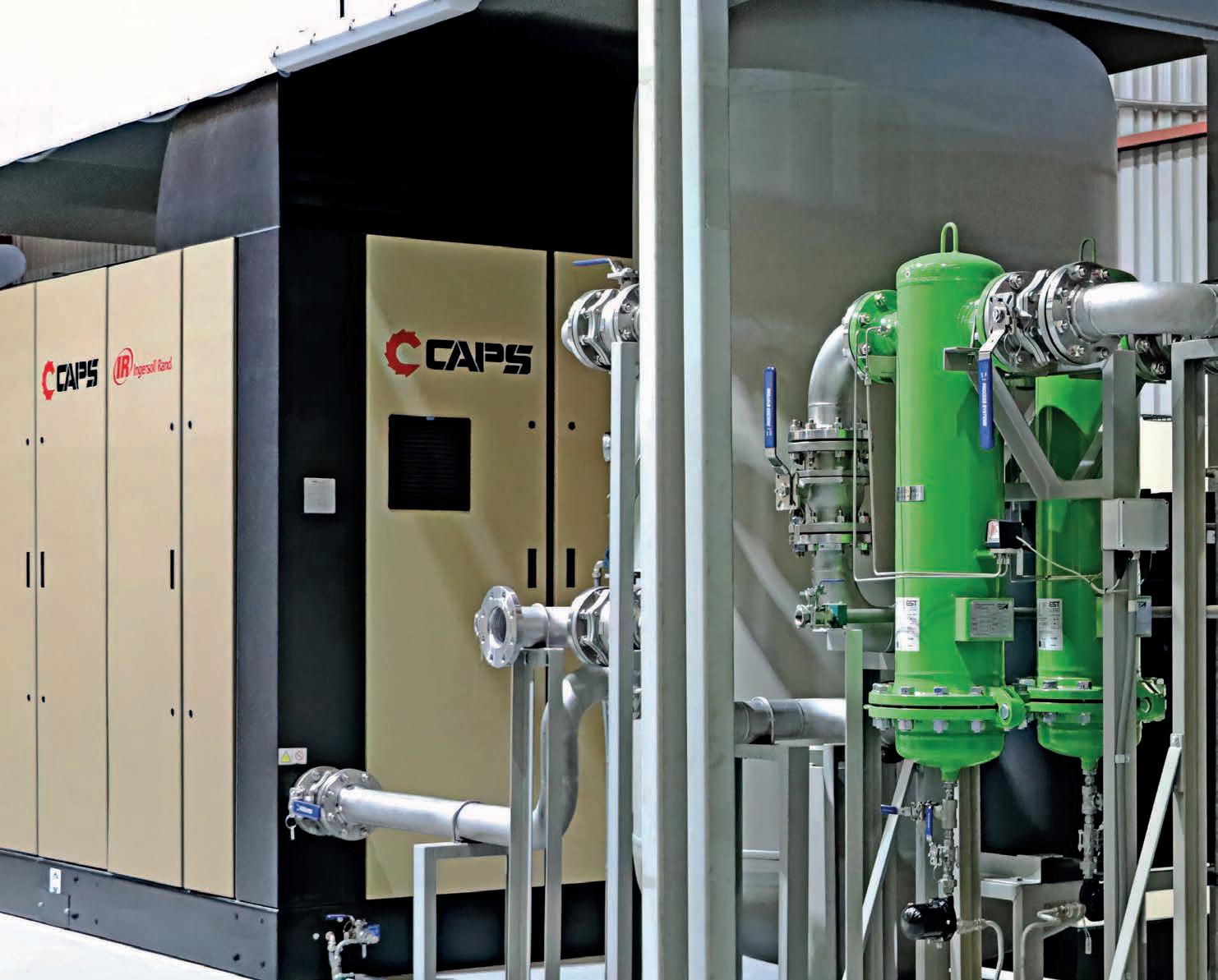
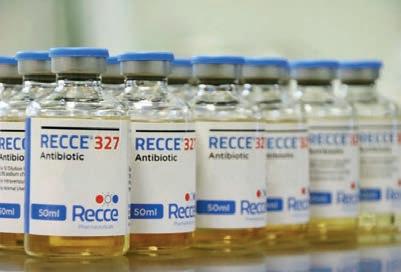

CEO: John Murphy
Chief Operating Officer: Christine Clancy
Managing Editor: Mike Wheeler
Assistant Editor: Jack Lloyd jack.lloyd@primecreative.com.au
Head of Design: Blake Storey
Design: Alejandro Molano
Sales/Advertising: Emily Gorgievska Ph: 0432 083 392 emily.gorgievska@primecreative.com.au
Subscriptions
Published 11 times a year
Subscriptions $140.00 per annum (inc GST) Overseas prices apply Ph: (03) 9690 8766
Copyright Manufacturers’ Monthly is owned by Prime Creative Media and published by John Murphy.
All material in Manufacturers’ Monthly is copyright and no part may be reproduced or copied in any form or by any means (graphic, electronic or mechanical including information and retrieval systems) without written permission of the publisher. The Editor welcomes contributions but reserves the right to accept or reject any material. While every effort has been made to ensure the accuracy of information, Prime Creative Media will not accept responsibility for errors or omissions or for any consequences arising from reliance on information published.
The opinions expressed in Manufacturers’ Monthly are not necessarily the opinions of, or endorsed by the publisher unless otherwise stated.
© Copyright Prime Creative Media, 2024
Articles
All articles submitted for publication become the property of the publisher. The Editor reserves the right to adjust any article to conform with the magazine format.
Head Office
379 Docklands Drive Docklands VIC 3008
P: +61 3 9690 8766 enquiries@primecreative.com.au www.primecreative.com.au
Sydney Office Suite 11.01, 201 Miller St, North Sydney, NSW 2060
Printed by: The Precision Group
83-89 Freight Drive.
Welcome to the February edition of Manufacturers’ Monthly.
Showcased in this edition’s Cover Story is CAPS’ range of products that provide air and power solutions to ensure industrial efficiency.
For this month’s Manufacturers Focus, we spotlight the Australian origin story of sleep technology manufacturer, ResMed, and how the company continues to change lives one machine at a time. Next is a case study that displays the importance of cybersecurity, as Dragos helps a renowned beverage manufacturer in navigating growing cyber risks.
Also spotlighted are the winners of the 2024 Manufacturers’ Monthly Endeavour Awards, who continue to act as trailblazers of innovation and leadership within the industry.
Rounding out the edition is an Engineering Focus article that follows Recce Pharmaceuticals’ journey to one day stop antibiotic-resistant superbugs.
As we went through late 2024 and broke into the new year, Australian manufacturing continued to ride a positive wave of momentum in sectors such as pharmaceuticals, Defence, skills and critical minerals. In the first Manufacturers’ Monthly edition of 2025, we explore trends and advanced technologies that our sovereign industry can look forward to in the coming 12 months.
The potential prosperity of this year was set up in late 2024 with several announcements that focused on new manufacturing hubs across the country.
This began when Australia’s first mRNA manufacturing facility opened at Monash University’s Clayton campus in Victoria, fostered by a partnership between Moderna and numerous Australian governments. As one of the few end-toend mRNA vaccine production facilities globally, it is set to produce up to 100 million vaccine doses annually, marking a milestone in Australian pharmaceutical manufacturing.
In late December, also announced was a
Federal and NSW Government investment of $47 million to establish the Illawarra Heavy Industry Manufacturing Centre of Excellence. With hopes of opening in 2027, this centre at TAFE NSW Wollongong would offer training programs to equip students with advanced manufacturing and digital technology skills into the future.
Defence manufacturing momentum also continued through the end of 2024 when international defence and aerospace company Babcock opened a $3.5 million International Engineering and Technology Hub in Melbourne. Aimed at enhancing R&D in global defence, the facility is set to host up to 100 highly skilled jobs, focusing on areas like AI, secure communications, and systemsengineering.
This investment into Australia’s Defence manufacturing sector will continue into 2025, as the Federal Government announced the build of 40 new Bushmaster Protected Mobility Vehicles. Thales Australia ultimately secured the $100 million contract that is set to benefit national security and
create more than 250 local jobs in Bendigo. 2025 has also already seen further steps toward a ‘Future Made in Australia.’ These steps came by way of a Federal Government’s $2 billion investment in Australian-made aluminium, helping smelters transitioning to renewable electricity. Going forward, this investment is poised to secure jobs, boost local manufacturing, and position Australia as a leader in clean metals production.
To top off a positive start to 2025, the Federal Government released statistics regarding its $400 million Industry Growth Program, which so far has delivered more than $26 million to 20 businesses. Helping technologies across robotics, medical manufacturing and defence, the program will continue to offer grants of up to $5 million and advisory services to businesses.
Going forward, Australia aims to successfully carry the positive momentum from 2024 marked by strong investment, growth, and partnerships into 2025, further propelling the development of its manufacturing industry.
Weld Australia has announced a partnership with EWI and the Canadian Welding Bureau, aiming to provide Australian manufacturers with further access to automation technologies and solutions.
The Australian welding and manufacturing sectors are at a pivotal moment. Rapid advancements in technology, coupled with growing demand in critical industries like renewable energy and Defence, present opportunities to modernise and lead globally.
Weld Australia has announced a transformative partnership with EWI (previously known as the Edison Welding Institute) and the Canadian Welding Bureau (CWB), to provide Australian manufacturers with direct access to cutting-edge automation solutions and world-class research and development (R&D).
Weld Australia’s collaboration with EWI and CWB will focus on Industry 4.0 technologies such as cobots, automated welding systems, and collaborative automation. These technologies are designed to:
• Boost productivity: Streamline welding and manufacturing processes.
• Address labour shortages: Fill skills gaps with reliable, automated solutions.
• Enhance safety: Minimise risks in hazardous processes.
• Reduce costs: Improve efficiency without compromising quality.
Australia’s manufacturing future hinges on embracing innovation. By partnering with EWI and the CWB, Weld Australia is ensuring our members have access to the best automation technologies and R&D solutions. This isn’t just about staying competitive; it’s about leading the way in critical industries like renewable energy and Defence.
For example, EWI’s advanced technologies can enhance the production of wind turbines, solar infrastructure, and Defence components, ensuring precision, quality, and cost-effectiveness.
In the welding industry, productivity is imperative
to driving innovation and growth. Welding businesses that maximise efficiency and optimise operations benefit directly from cost savings and better use of resources. Labour, equipment and materials can be more effectively allocated to minimise waste and energy consumption. Productivity gains lead to faster project completion times – enabling companies to exceed client expectations and secure repeat business.
A clear pathway to productivity is through technology. When companies are focused on improving their processes, they naturally innovate – implementing the latest technologies in a bid to streamline operations. However, Australian companies generally lag their global competitors in digital adoption and unfortunately the welding sector is no exception. Uptake of advanced welding technology remains slow, and this lack of tech adoption is impeding our ability to navigate the current challenges facing the industry.
For instance, the majority of welding businesses are still not leveraging robots or cobots. These technologies work safely alongside humans, designed to take on mundane and repetitive tasks, freeing up workers to take on highvalue tasks.
By leveraging the benefits of cobot welding, businesses can increase their productivity and reduce labour costs, while improving the quality of their welds. Given that the major barriers to productivity are materials handling and a lack of skilled staff, there is an opportunity for welding businesses to harness the capabilities of advanced welding technologies to overcome these issues.
One of the outcomes of this partnership is a direct pathway to EWI’s R&D capabilities. This will ensure Australian manufacturers gain access to automation systems designed to meet the unique demands of local industries, including solutions
that support ambitious national goals in clean energy and Defence.
In addition to delivering advanced technology, we’re committed to upskilling the workforce. Automation training programs, offered through EWI and CWB, will help businesses seamlessly integrate new systems while empowering workers to adapt to evolving roles.
The future of welding in Australia depends on both cutting-edge technology and a highly skilled workforce.
Through this partnership, we’re not only modernising manufacturing but also empowering workers to take on new and exciting roles in industries that are shaping the nation’s future.
This partnership reflects Weld Australia’s mission to drive innovation, enhance competitiveness, and future-proof the Australian manufacturing sector.
This collaboration is more than a partnership – it’s an investment in Australia’s future. By combining EWI and CWB’s global expertise
with our local industry insight, we’re equipping our industry to meet ambitious national targets in clean energy, Defence, and beyond. Together, we’re building a more sustainable, competitive, efficient and secure future for Australian manufacturing.
These partnerships will bring proven automation solutions to key Australian sectors, including renewable energy and Defence.
In renewable energy, EWI developed automated welding systems to enhance the precision and efficiency of wind turbine construction, reducing production time by 30 per cent. Telewelding technology allows remote operation of welding systems, enabling real-time oversight and adjustments from anywhere in the world. This innovation is critical for addressing labour shortages and supporting large-scale projects in remote or hazardous environments, such as offshore energy and Defence installations. Next to wind turbines, solar panels can be
benefitted by advanced laser welding techniques that improve durability and efficiency in photovoltaic module manufacturing, critical for scaling Australia’s renewable energy infrastructure.
EWI also brings benefits in energy storage with its joining technologies for large-scale battery systems supporting reliable and cost-effective energy storage solutions.
In Defence, EWI’s automated welding solutions streamline production for naval ships, enhancing quality and reducing costs – essential for Australia’s naval Defence initiatives.
Additionally, advanced welding technologies for high-strength materials improve durability and compliance with military standards for armoured vehicles.
Also, precision welding for lightweight aerospace parts supports cost-effective and high-quality Defence manufacturing.
Aside from Defence, the partnership will be beneficial to training and workforce development. Through CWB, EWI offers tailored automation training, including cobot programming, welding system integration, and safety protocols.
These programs will help prepare Australian manufacturers to adopt advanced technologies while addressing labour shortages.
The CWB Group is an industry-supported private sector organisation providing welding certification, management systems registration and training services to more than 7,600 companies.
Headquartered in Ontario, Canada, with staff and offices across the country, CWB is recognised as one of the largest and most innovative welding organisations in the world.
EWI (previously known as Edison Welding Institute) is a not-for-profit engineering and technology organisation dedicated to developing, testing, and implementing advanced manufacturing technologies for industry. Headquartered in Ohio in the US, EWI has a team of more than 150 people, offering applied research, manufacturing support, and strategic services to leading manufacturers in the aerospace, automotive, defense, energy, government, heavy manufacturing, medical and electronics sectors.
From modest origins in Sydney, ResMed has grown into a company that specialises in non-invasive technology solutions that improve sleep health worldwide. Jack Lloyd writes.
Founded 35 years ago in Sydney, ResMed is a technology manufacturer focused on improving sleep health and reducing the effects of respiratory disorders such as obstructive sleep apnoea (OSA) and COPD. The company’s products are designed to encourage ventilation by advancing diagnosis, treatment, and management of sleepdisordered breathing.
“ResMed’s cloud-connected devices and digital health solutions transform care to help people stay out of hospitals and live better lives in the comfort of the home,” said global manufacturing principal automation engineer at ResMed, Brock Dominish.
For the last 13 years, Dominish has witnessed the company evolve its capabilities to deliver solutions in over 140 countries.
“ResMed currently operates in over 140 countries globally with manufacturing centres in Australia, Singapore, Malaysia, the USA, China and France,” said Dominish.
Yet, the company was not always wide-reaching, with ResMed’s initial product being created in 1981 when professor Colin Sullivan developed the first Continuous Positive Airway Pressure Device (CPAP) at the University of Sydney. Sullivan then took the system – which targeted OSA specifically – to Dr.
Peter Farrell, who, in 1989, would acquire and commercialise a CPAP prototype in Sydney.
“Dr. Peter Farrell founded the company to bring the life-changing technology developed by Dr. Colin Sullivan at the University of Sydney to the world,” said Dominish.
“Together, they turned groundbreaking research into a thriving industry. From humble beginnings, ResMed has grown into a company that impacts millions of lives worldwide.”
Now, ResMed is thriving globally by producing CPAP masks, machines and in-home life support ventilators that offer a safer treatment than surgery, which comes with inherent risks.
“Sleep health and people’s well-being are at the very core of our mission and the products we create,” said Dominish.
ResMed’s main offering remains the CPAP products that target the treatment of the OSA. This sleep disorder is experienced by over one billion people globally, according to the National Centre of Biotechnology Information in the US.
“It occurs when the upper airway becomes blocked
during sleep, essentially suffocating the sufferer and causing them to wake up throughout the night,” he said.
Dominish said that ResMed’s CPAP machines, masks and anti-snoring mouthpieces function by generating gentle air pressure delivered to the patient through a tube.
“This positive pressure prevents the upper airway from collapsing during sleep, enabling steady breathing, restful sleep, and can lead to a better quality of life,” said Dominish.
These systems have consistently evolved since their creation in 1989, including the addition of software compatibility to provide a holistic approach to care.
“Our devices are paired with software that helps both clinicians and patients monitor sleep health,” said Dominish.
ResMed’s latest CPAP device is the company’s most innovative to date, as the AirSense 11 can sync with a virtual Personal Therapy Assistant and make wireless upgrades.
“The ResMed AirSense 11 AutoSet is designed to enhance user experience and therapy adherence,” said Dominish.
Dominish also made note of ResMed’s AirTouch N30i, a CPAP nasal mask that offers a design that “feels as gentle and cozy as your favourite pyjamas”.
“The company’s first nasal mask features our new ComfiSoft cushion to help provide a comfortable CPAP experience,” he said.
ResMed also manufactures one of the smallest CPAP devices in the world – the ResMed AirMini –which is suitable for travelling or spending nights away from home.
“Whether you’re camping in the Australian outback or flying home after a work trip, this compact machine offers therapy, waterless humidification and convenient control,” said Dominish.
The response to these products from both the medical community and consumers is something of which Dominish and ResMed are proud.
“Healthcare professionals recognise our solutions as transformative,” he said.
“From consumers, we hear incredible stories about how our products have significantly
improved their quality of life. Whether it is better sleep, increased energy, or the ability to live more independently.”
Despite a global presence, ResMed continues to manufacture many products in its 30-acre innovation and manufacturing centre in Bella Vista, Sydney. The facility is supported by around 600 manufacturing staff – including operators, engineers, technicians, and administrative personnel – and 700 design staff.
“Our Australian manufacturing capability includes the assembly, testing and packing of CPAP devices as well as life-support ventilators,” said Dominish. “Fifteen to 20 40-foot containers are shipped weekly to export markets, alongside dozens of trucks for local distribution.”
The company also operates the largest medicalgrade liquid silicone rubber moulding facility in the Southern Hemisphere and runs an advanced machining facility to create custom moulding tools for medical devices.
Dominish said within these facilities, ResMed is fortunate to utilise the latest high-tech manufacturing equipment from around the world.
“Our operations include a robust fleet of robotics and automation systems that handle a wide variety of tasks like component testing, part handling, demoulding, inspection, screw driving, assembly, and printing,” he said.
The company complements these automated systems with traditional hand-operated assembly jigs and production lines.
“Combining automation with skilled manual processes ensures efficiency and quality across manufacturing operations,” said Dominish.
This balanced approach continues through ResMed’s quality control protocols that are also maintained by a balance of personnel and automated systems.
“Quality is embedded in every step of the process
including design, procurement, incoming parts, production lines and distribution,” said Dominish.
“These measures are integrated into our systems, ensuring that every step is performed, recorded, and traceable.”
Aside from controlling the quality of its products, ResMed has prioritised reducing its environmental footprint across production and the supply chain.
“Guided by our Environmental Management System, we work to reduce our ecological footprint through resource efficiency, waste reduction, and energy management,” said Dominish.
Despite a global and streamlined manufacturing capability, ResMed still had to overcome challenges. Dominish noted one of these struggles was responding to the global demand for ventilators during the COVID-19 pandemic, which forced ResMed to ramp up production to 3.5 times its usual capacity.
“This was achieved through agile thinking, leveraging cross-functional teams, mobilising our supply chain, and innovating rapidly to scale production. All while maintaining safety,” said Dominish.
ResMed’s AirTouch N30i is a CPAP nasal mask that is designed to optimise performance and comfort.
The challenge however continues for the company, who is still constantly evolving to meet the growing demand for its products. Dominish said that to achieve this output, ResMed has standardised its equipment infrastructure across its global manufacturing sites.
“Standardisation allows engineers, technicians, and integrators to seamlessly support and maintain equipment regardless of location,” he said.
This adaptation to market dynamics will continue, as the company starts to embrace digitisation technologies across factories.
“Artificial intelligence (AI) is being integrated into our production processes, with technologies like machine learning and computer vision being explored to optimise operations, predict maintenance needs, and enhance product quality,” he said.
This emphasis on innovation is just one small part of a 2030 ResMed strategy that is centred on growing and differentiating the business; expanding into near and adjacent areas; and leveraging leadership in digital health.
“By 2030, ResMed envisions being at the forefront of personalised and digital healthcare,” said Dominish.
“ResMed’s eventual goal is to empower 500 million lives in 2030.”
CAPS continue to provide compressed air and power solutions that deliver the required performance outcomes to avoid any inefficiency or downtime in operations.
Choosing the right compressed air or power solution is more than just delivering the required performance outcomes that an operation needs, it ensures a client has the necessary service and support available to keep things performing at theiroptimum.
Because any inefficiency or downtime has a costly impact on businesses and industry leaders, CAPS Australia offers multiple ways to achieve successful operational outcomes.
Delivering compressed air and power generation
solutions across Australia, CAPS has a range of products and brands to provide air and power solutions that are suitable for local operating requirements. World-renowned partner brands such as Ingersoll Rand, AIRMAN, Mitsubishi Heavy Industries, Sauer, Pedro Gil, Next Turbo Technologies and many more feature in the CAPS designed solutions.
Whether clients are looking for a reciprocating, rotary screw, oil-free rotary screw, portable diesel or centrifugal air compressor, CAPS’ solutions
are engineered around clients’ needs, with a commitment to delivering low-cost industrial air compressors that are engineered to last.
CAPS’ Centrifugal Compressors national product manager, Juan Kotze, said the varied demands of manufacturing industries generally requires systems that are designed and configured to the end-user application.
“Our name demonstrates our commitment to delivering the complete air and power solutions (CAPS) that our customers need, backed by the
skills, service and national footprint that provides local support,” said Kotze.
The manufacturing, food and pharmaceutical sectors require a range of specialised ‘Class Zero’ air quality compressors that meet standards according to ISO 8753-1:2010.
CAPS’ compressed air solutions supply clean, dry air to comply with safety, quality and hygiene standards. The ideal approach to achieving and maintaining this air purity is to minimise the risk of contamination in the first place by using oilfree compressors.
Though they can come with a higher initial capital cost, oil-free compressors offer long-term benefits associated with less ancillary equipment and servicing, as well as a reduction of risk, often making them a more valuable investment.
CAPS Australia meets this requirement with its range of ISO Class 0 oil-free compressors, guaranteeing 100 per cent oil free air for industrial applications.
For larger scale applications, CAPS has a full
range of oil-free centrifugal compressors as well as rotary screw compressors from 37kW to 355kW in either fixed or variable speed. These machines are versatile and tailor-made, so there are many factors to weigh up when choosing the right compressor. Elements such as size, speed control, continuous or intermittent usage, portability, and site operating conditions including altitude and ambient temperature, can all impact which system will suit a client’s needs. CAPS also offer experts that can help people assess their requirements to find them the perfect match.
On a smaller scale, CAPS can offer scroll compressors in an all-in-one solution with a dryer, storage tank and compressor in a single unit, keeping the real estate of the system as compact as possible. This smaller footprint translates to higher efficiency, a key component when choosing the right compressed air system, particularly as energy prices continue to climb across the country. Offered as a single phase from 1.5kW –2.2 kW or three phase from 3.7kW to 7.5kW, CAPS suggests this integrated solution as suitable for smaller applications requiring oil-free air. Setups
can be configured to support an array of end process needs.
Due to their lower initial costs, many manufacturers opt instead to use oil-lubricated compressors with air treatment processesdownstream.
From 5kW through to 315kW, there are many technologies and brands to choose from, meaning it can be quite challenging to evaluate different compressors and select the best technology for a system. CAPS offers a suite of compressed air solutions and has the expertise to help clients choose the right equipment to suit their needs. The company understands that every application is unique, which is why it offers customised solutions and provides ongoing support to ensure optimal performance.
“Our teams are local, meaning our customers interact directly with experienced product managers who have years of compressed air industry expertise, to ensure we understand their requirements, something that other OEMs struggle to provide because their technical support is overseas,” said Kotze.
“We work to understand the specific operational requirements, offering recommendations, providing technically sound advice and ultimately delivering customers the solutions they need.”
Air dryers are essential in meeting the air quality requirements that are critical throughout the manufacturing sector.
Air dryers help to remove moisture from compressed air systems, decreasing the humidity and preventing bacteria from growing, as well as warding off rust and extending the life of the machine. Desiccant air dryers are popular for industrial applications and processes that require extremely dry air between -40˚ C to -70˚ C, where a desiccant material such as silica gel, molecular sieve or activated alumina is housed in a chamber through where the compressed air passes, absorbing the moisture.
Now dry, the air must also be cleaned before it can be compliant with relevant standards. Specialised filters use a variety of technologies – including coalescing and adsorption – to remove dust, oil, and other contaminants from compressed air systems. Reliable and customisable, they are available in various sizes and configurations to meet your specific needs.
The at-scale generation of nitrogen to support operational needs is a challenge for which CAPS Australia has solutions. Experienced in delivering
engineered nitrogen (N2) generation systems, CAPS can configure the equipment needed to support on-site demands. Producing dependable and economical supplies of nitrogen, the systems allow users to generate the quantity and purity of nitrogen necessary for any application on site.
CAPS Australia has been entrusted to provide reliable power for a range of applications such as manufacturing, healthcare, data centres, water treatment, landfills and independent power stations, underpinned by high performance and fuelefficient equipment.
As an Australian supplier of AIRMAN products, and the official Australian distributor for the Mitsubishi Generator Series (MGS), CAPS can deliver the power generation solution needed to underpin operations.
Whether it is worksite power, farming activities, mobile or remote operations, the AIRMAN range of industrial diesel-powered generators are the smart choice for a reliable source of energy.
AIRMAN diesel compressors and generators are designed, engineered and manufactured in Japan and are renowned for their precision engineering, reliability and fuel efficiency.
Partnering with Mitsubishi Heavy Industries Engine System Asia (MHIES-A), the Mitsubishi Generator Series (MGS) delivers reliable and excellent
performance, supplying power during emergencies and acting as a backup for critical operations.
CAPS delivers complete solutions, designed and developed by its in-house engineering team and supported through its Australian ISO9001accredited manufacturing facility. The custom-built systems are matched to clients’ requirements. This expertise also enables CAPS, where possible, to integrate new technology into existing installations, enhancing the operational performance and life of equipment and infrastructure.
The CAPS Engineering team manages the total design, development and manufacturing of specialised one-off compressor, generator and blower packages. This unique capability includes calibration, testing, monitoring and recording of critical data for a range of plants and equipment. The in-house capabilities help fast-track site installation so users can simply plug and play.
Founded in Western Australia in 1980, CAPS joined the Ingersoll Rand family in 2024, expanding its access to Ingersoll Rand’s global offering of innovative and mission-critical air, fluid, energy and medical technologies that enhance industrial productivity and efficiency.
With 10 branches nationwide, the dedicated CAPS team delivers great service, expert advice, support and spare parts. The team’s 24/7 maintenance and breakdown service ensure customers’ operations run smoothly and reliably.
The national footprint means CAPS has experienced and skilled teams working in the same time zones as its clients, enhancing their support to customers through the entire process – from understanding their requirements, offering suggestions and providing advice, to delivering the solutions they need.
Their knowledge is continually updated, and they have the model-by-model understanding to fix a generator first time, every time. Whether it is one generator or a complex system with multiple pieces of equipment, CAPS’ technicians will give the advice needed to ensure continuous operation.
The support continues throughout the equipment’s operational life, with CAPS CARE providing clients with ongoing warranty, parts and service plans, ensuring the greatest value for managing assets. Scheduled air compressor maintenance, as well as using predictive analytics, helps prevent unexpected interruptions in production. CAPS CARE maximises equipment uptime and takes any hassle out of equipmentmaintenance.
Safety is a core value of CAPS and its goal is to never put people, plants or the environment at risk. From design to manufacture, installation and maintenance the company’s equipment and technicians will enhance any necessary safety requirements.
CAPS can also get clients operational without big capital costs by delivering its competitively priced, turnkey rental solutions. Keeping operations running smoothly all year round, CAPS offers short- and long-term rental of
compressors and generators across Australia. They are suitable for special projects, seasonal peak demand requirements and covering any operational breakdowns, renting provides flexibility to suit a client’s needs.
With experience in renting equipment, CAPS has a fleet of units ready for immediate dispatch from local hubs that satisfy a range of applications, including mining, all while ensuring top quality equipment and high standards of customer service.
Utilising quality products with proven reliability, CAPS’ range of industrial equipment provide customers with access to the best technologies in:
•Rotary screw and centrifugal air compressors.
•Portable diesel air compressors.
• Power generators.
• Industrialfiltration.
•Air blowers.
•Gas generators (oxygen and nitrogen).
• Air treatment equipment including custom built heavily engineered vessels.
• Engineered packages to suit customer’s needs and location.
• Parts and accessories.
CAPS delivers global technology, suited to Australian conditions, backed by local service.
Get in touch with the CAPS team on 1800 800 878 or check out www.caps.com.au
The varied demands of manufacturing industries require systems that are designed for specific applications.
Australia’s largest Defence maritime event returns to provide industry updates and engagement.
With a flurry of announcements in the last half of 2024, industry and government are continuing to define the frontline capability and support systems that will underpin Australia’s move to a joint Australian Defence Force (ADF), as laid out in the 2023 Defence Strategic Review.
As one of the world’s largest island nations, it should be no surprise that many of the announcements have a salty tang, regardless of which arm of the ADF will operate the capability. Alongside the headline AUKUS submarine project and Hunter Frigate acquisition, a myriad of other projects are changing the way the ADF will operate in, on and above the sea.
Recent announcements have included:
• The acquisition of eight Landing Craft Heavy vessels, to be built by Austal in Western Australia and operated by Army.
• The first launch of a Tomahawk cruise missile from an Australian Hobart-class destroyer vessel, as part of efforts to equip the Royal Australian Navy with a long-range strike capability.
• A $200 million investment in training infrastructure to grow Australia’s future submariner workforce.
• Anduril Australia’s announcement of an Australian factory to manufacture its Ghost Shark autonomous underwater vehicle for Australia and the region.
• Down-selection of two shipbuilders, Mitsubishi Heavy Industries (MHI) and Thyssenkrupp Marine Systems (TKMS), to progress designs for Australia’s future general-purpose frigates.
• Increased maritime defence exercise participation with regional partners such as India andJapan.
• Successful firing of the Blast Test Vehicle (BTV) from the first Australian-manufactured Naval Strike Missile (NSM) launcher.
• Announcement of a second Army Long Range Fires Regiment, to be equipped with landbased maritime strike missiles (a first for the Australian Army).
In November, industry, government and defence will come together for updates on programs, discussion of challenges and opportunities, and engagement on how Australian industry can provide maritime capability of all kinds for the Australian Defence Force.
The 2025 Indo Pacific International Maritime Exposition, set for Sydney’s International Convention Centre in Darling Harbour from November 4-6, 2025, will host the Royal Australian Navy’s own Sea Power Conference, around 90 maritime conferences, symposia and presentations and more than 800 industry exhibitors from more than 20 nations.
In a packed three-day program, the event will address everything from advances in ship design and maintenance to small-boat operations, helicopters
and autonomous air and sea vehicles, and the thousands of technologies that allow Defence to train, operate and support its equipment and personnel at sea and on land.
Held every two years since 2000, Indo Pacific has become Australia’s largest and most effective platform for engagement between industry, government, academia and navy. More than an exhibition, it is a meeting of the international civil and defence maritime community.
Indo Pacific 2023 saw 176 industry, defence and academic delegations from 46 nations, with 48 chiefs of Navy, counterparts or representatives.
In addition to its Sea Power Conference, the Royal Australian Navy uses Indo Pacific as both a recruitment and industry engagement tool.
“What I really like about Indo Pacific 2023 is the opportunity to talk to our industry partners, to introduce them to the men and women of the Royal Australian Navy and to find opportunities to strengthen our Navy’s capability, which ultimately means we’ve got a stronger Navy and a much stronger nation,” said chief of Navy Australia, Vice Admiral Mark Hammond, during the 2023 event.
But it’s not all about the Navy. Indo Pacific is also the regular home of the IMC International Maritime Conference, organised by The Royal Institution of Naval Architects, The Institute of Marine Engineering, Science and Technology, and Engineers Australia.
The International Maritime Conference involves
delegates in discussion of the latest developments in naval architecture, marine engineering and maritime technology, for both defence and commercial applications. It will cover subjects from maritime safety and environmental protection to cyber security, shipbuilding and sustainment.
For industry, Indo Pacific 2025 is a chance to spend three days surrounded by the key players in the region’s maritime community, and to take advantage of an event crafted to help them promote their products and services.
The combination of Navy, Defence, industry and civil programs attracts and engages personnel at all levels, from chief of Navy and chief executive officers of prime contractors to ministers, government agency personnel, uniformed and civil technical specialists, acquisition program personnel, those who conceive and build today’s cutting-edge technologies, and those who may one day operate them. It has proven the drawcard that brings defence, industry, government and
academia together as a community of knowledgesharing agencies, in the national interest.
The Indo Pacific International Maritime Exposition is designed and structured to enable and encourage engagement between participants at all levels, through the industry exhibition, specialist conferences, networking events or through the sheer concentration of the maritime community on one site.
The Indo Pacific region, perhaps more than any other part of the world, is dependent on sea lanes for trade and transport and is home to some of the world’s largest shipbuilding nations and busiest ports.
Perfectly positioned, commercially disciplined and internationally focused, Australia is the ideal conduit for promoting into the dynamic maritime markets of Asia and the Indo Pacific. For more information see www.indopacificexpo.com.au
By investing in VSD technology, companies can save costs and contribute to a more sustainable future.
Manufacturers’ Monthly explores how Atlas Copco’s Variable Speed Drive (VSD) range enhances the efficiency of compressed air installation to meet the rising demand for these essential systems.
With demand for compressed air fluctuating in 88 per cent of all compressed air installations, there is an opportunity to improve productivity by making air compressors run efficiently.
Seventy per cent of industrial electrical consumption is for electric motors, 20 per cent of industrial electrical capacity is consumed by air compressors, and around 70 per cent of the total life cycle cost of a standard air compressor is electricity. Addressing this demand is where Variable Speed Drive (VSD) technology comes into play. VSD compressors are designed to optimise energy use by adjusting the compressor’s motor speed to match the real-time demand for compressed air. This not only reduces the overall load on the power grid but also minimises sudden spikes in demand, leading to energy savings.
Atlas Copco VSD Heritage
In 1994, Atlas Copco was one of the first compressor companies to fully integrate a VSD compressor. The company’s VSD technology and evolution across 30 years showcases the vision and innovation of the ‘Atlas Copco way’ of providing sustainable solutions, even before the present trend of energy savings and carbon reductions started.
VSD compressors are designed to optimise energy use by adjusting the compressor’s motor speed to match the real-time demand for compressed air.
The evolution has not stopped at integrating VSD into compressors, as Atlas Copco developed its own NEOS Drive in 2014.
This in-house technology is built exclusively for compressors, unlike other VSDs, which are built for various applications. This makes the NEOS Drive a dedicated compressor VSD.
The GA FLX dual-speed compressor is a suitable entry point into the world of variable speed drive technology. The solution is for those not only seeking energy savings but who are not ready for a full VSD system. When ready, the GA FLX can be switched to a VSD machine.
The GA FLX represents a departure from having to choose between fixed-speed air compressors and VSD compressors. It offers a third option.
The system operates at two motor speeds: one for maximum capacity, and a minimum speed for reduced energy consumption when air demand is lower. This positions the GA FLX between a fixedspeed GA compressor and a GA VSD compressor.
Aside from the GA FLX’s option as an entry point, the GA VSD model is the classic among compressors with a variable speed drive. Compared to a fixedspeed compressor, a GA VSD model can reduce energy consumption and costs by up to 35 per cent. Due to their reliability, these compressors remain an option for operations with a variable air demand.
The GA VSD compressors offer other benefits, including energy efficiency, by adjusting the motor speed to match air demand, which reduces energy wastage and lowers electricity bills. Their operational flexibility allows the systems to handle varying air
demands efficiently, making them suitable for a range of industrial applications.
Additionally, the ability to operate at lower speeds reduces mechanical stress on the compressor components, extending the lifespan of the equipment and reducing maintenance costs.
VSD+: Premium efficiency
Moreover, Atlas Copco’s GA VSD+ range is a marvel of engineering that features an interior Permanent Magnet (iPM) motor that boosts the efficiency of VSD compressors. Compared to fixed compressors, this can mean energy savings of up to five per cent. While the initial investment can be greater than traditional compressors, the energy savings can quickly make up for that. Ultimately, the low operating expenses result in a much lower total cost of ownership for GA VSD+ models. The entire drive train of these compressors is a closed circuit, where both motor and elements are cooled with oil, providing additional energy savings.
Another benefit of VSD+ compressors is their flexible installation. Their vertical design has reduced the footprint of these compressors by 60 per cent, allowing them to fit in more places.
Additionally, because there are no couplings or gears between the motor and the screw element, VSD+ compressors are quiet, enabling installation outside the compressor room, at the point of use.
VSDs: Next-generation
These compressors raise the bar in terms of efficiency, reliability, connectivity, and sustainability. This range combines decades of experience with the latest technologies, resulting in a smart, adaptable compressor that benefits operations, the bottom line, and the environment.
The new Neos Next inverter designed specifically for compressor applications – combined with the new drive train –reduces energy usage by up to 60 per cent compared to conventional fixed compressors.
The efficiency of the GA VSDs series is further boosted by its Smart Temperature Control (STC) oil cooling system that combines multiple parameters such as motor speed, ambient temperature, and humidity to ensure the compressor runs at the optimal temperature. This eliminates the risk of condensation.
The STC system makes the VSDs unique as it is the only compressor that can measure ambient conditions and adapt its operation accordingly.
The capability is further extended by Boost Flow mode, which is a standout feature among the rest of the VSD family. Boost flow mode comes to the rescue when more air is required, delivering five per cent more FAD for a certain time. This helps production with the required boost as and when required, without compromising on production costs and quality.
Atlas Copco’s range of VSD compressors provides a solution for industries looking to reduce their energy consumption and improve operational efficiency.
By investing in VSD technology – from the GA FLX dual-speed compressor as a step into variable speed, to the GA VSD, which reduced energy usage by 35 per cent, to the GA VSD+ offering an average of 50 per cent energy savings, and the GA VSDs delivering up to 60 per cent energy savings –companies can achieve cost savings and contribute to a more sustainable future.
With the growing adoption of automation, interconnected devices, and digital technologies in manufacturing, the risk of cyber threats has become a pressing concern.
For Boston Beer, the increasing complexity of its systems and the expansion into operational technology (OT) environments have added new layers of vulnerability. Struggling to keep pace with the resource demands of maintaining and securing these systems, Boston Beer identified the need for the modernisation of its corporate IT and OT security strategies to stay ahead of evolving threats.
Founded in 1984 by Jim Koch, The Boston Beer Company – the maker of brands like Samuel Adams, Dogfish Head, Truly, Twisted Tea, and Angry Orchard – began with a lager recipe passed down from his great-great-grandfather.
Forty years later, Boston Beer has produced 111 million cases of beer, welcomed almost two million visitors to Boston Beer properties, and continues to redefine how the world experiences high-quality beer and seltzer.
When Brandon Catalan joined Boston Beer in 2021 as chief information security officer (CISO), the company had invested in IT cybersecurity programs,
but it struggled to keep up with the resource demands required to maintain its systems, let alone focus on expanding into its OT environment.
As a result, corporate IT security and OT security at the company’s breweries and its overall operational infrastructure were key targets for modernisation.
“We’re not just a beer company; we’re a manufacturing company. If we lose the ability to brew, bottle, and can, then we’re out of business,” said Catalan.
The manufacturing sector is vulnerable to operational risks due to the nature of cyber threats targeting operations technology systems. These risks threaten the integrity of IT systems and pose dangers to OT environments, potentially leading to physical damage, production downtime, financial losses, and safety hazards.
The shift towards greater IT-OT integration and remote access has amplified these risks, exposing critical infrastructure to advanced cyberattacks by actors, including ransomware gangs, criminal organisations, and state-sponsored entities. These actors evolve their tactics to exploit vulnerabilities and native functionality, highlighting the need for cybersecurity measures.
The interconnectedness of the global supply
Boston Beer has modernised IT and OT cybersecurity using Dragos systems, achieving 100 per cent ROI in year one amid growing cyber risks.
chain introduces additional risk and exposure, with a single compromised component potentially impacting countless devices and systems across multiple manufacturers.
The most recent Dragos Year in Review underscores the severity of the situation, noting a nearly 50 per cent increase in ransomware attacks targeting the manufacturing sector in 2023 alone. High-profile cases underscore the extensive financial and operational impacts of such incidents. The findings emphasise the importance of implementing strict network segmentation, enhancing security protocols, and fostering a collaborative approach to cybersecurity across the supply chain to mitigate these pervasive and evolving threats.
Understanding OT risk and prioritising the security of these environments was the first step for Boston Beer.
The next step was for Catalan to align the perspectives and resources of the company’s leadership and board.
Tabletop ransomware simulation
Boston Beer leadership tasked Catalan with building a robust IT and OT cybersecurity program from the ground up. Catalan began by running a
strategic tabletop exercise with the C-suite and the Board that simulated a ransomware scenario on the manufacturing side of the house.
The exercise covered the effects of an attack on every aspect of the business, from the cost of losing three days of production to reputation management to legal and HR implications. The impact was dramatic.
“The tabletop exercise demonstrated how vulnerable we were and got us executive backing and buy-in,” said Catalan.
“After that, whenever the CISO asked for assistance, it became the top priority.”
The exercise also prompted a search for the right OT cybersecurity platform for Boston Beer Co.
Catalan evaluated several vendors but ultimately chose Dragos, citing their ability to “talk the talk and walk the walk.”
“The executive team asked me what I needed, and I pointed to Dragos and said, ‘I need this.’ When you want to make a difference, and you’re not willing to gamble, you go with the Cadillac. That is Dragos,” he said.
Early detection of threats: Using industry-leading threat inputs, including proprietary threat intelligence, OT Watch proactively hunts for sophisticated threats that bypass traditional security measures, reducing potential adversary dwell time in customer environments and mitigating impact of attempted attacks.
Improve response time: OT Watch prioritises suspicious detections within the Dragos Platform and provides the human expertise to escalate high impact threats promptly with actionable guidance.
Identifying misconfigurations: While hunting operations, OT Watch often finds network, system and application misconfigurations, thus optimising security posture and limiting attack exposure.
Proactive risk mitigation: Proactive threat hunting enables a focused response to high probability threats to reduce risk to thebusiness.
Collective power: Customers benefit from the shared insights across the OT Watch client base and enhance their security posture by leveraging expert industrial threat hunters to augment their team.
Health and tuning for the Dragos platform: With OT Watch Premium, customers gain regular platform health support and asset, zone, and alert tuning of the Dragos Platform to maintain peak performance.
Compressed air specialist ELGi Equipment has found success focussing on advanced manufacturing, innovation, and customers.
Compressed air specialist ELGi’s facilities run on precision engineering, innovation, and sustainability with automated assembly lines, advanced quality control, and eco-friendly practices that ensure every part and product meets quality and efficiency standards.
Pioneering a new era in compressed air solutions
ELGi’s innovation and reliability in the compressed air industry continues to address challenges with precision-engineered solutions and a customerfirst approach.
From reducing lifecycle costs with sustainable compressed air solutions, to leveraging performance analytics to drive predictive maintenance, ELGi understands and addresses the challenges faced by customers.
What sets ELGi apart is its commitment to excellence. By investing in advanced manufacturing techniques and vocational training programs, it strengthens the industry with skilled talent and elevates standards for quality and efficiency.
The ELGi foundry was set up in 2013 to produce special castings for its airends while addressing all the challenges of quality, cost, and delivery requirements. The ELGi foundry is Pressure Equipment Directive (PED) and ISO-9001 certified. They are one of the rare compressor manufacturers who make their own airends.
It has an installed capacity of 9,000 metric tonnes to make high-precision ductile and grey iron castings annually.
The foundry uses a fast-loop, automated, no-bake chemical bonding system and employs the Furan and Amine Cold Box techniques for making 10 moulds per hour.
With complex internal capacities and solid shapes, more than 200 variants are developed to cater to ELGi’s air compressor manufacturing needs.
ELGi’s precision machining has been a defining factor in the company’s reaching of standards.
with a few critical machines built by the ELGi machine-building team. The facility is also installed with mixed model conveyorised assembly lines, a vertical storage and retrieval system, a metrology laboratory, and testing equipment, ensuring high accuracy and reliability.
The pressure vessel is one of the critical components of an air compressor package. The pressure vessel division (PVD) was established in 2007 to enhance product quality and support the needs of ELGi air compressor packages.
This integrated manufacturing setup includes designing and manufacturing air-oil separators and air receivers for ELGi air compressors. The air-oil separator vessels are used to separate the air-oil mixture in screw air compressors, whereas air receivers are used to store compressed air for direct applications.
Over the past 30 years, ELGi built its knowledge of “know-how” and “know-why” of compressors to become one of the five companies in the world with the capability to design and manufacture its own airends. “ ”
In 2011-12, ELGi’s Air Compressor Plant was established on over 100 acres, equipped with highprecision grinding, milling, and turning machinery, alongside critical machines constructed by the ELGi machine-building team.
The state-of-the-art plant is equipped with highprecision grinding, milling, and turning machinery,
The ELGi pressure vessel division has a manufacturing capacity of 2400 vessels per month, operating with 100+ people and accredited with sound quality systems and processes in place. The pressure vessels manufactured are compliant with the ASME U Stamp or AS1210.
The assembly process and parts are critical to the performance of an air compressor. The implementation of total quality management processes in the assembly plant has led to delivering products with no defects and high performance.
ELGi has won the 2019 Deming Prize for the sustained application and leverage of TQM (Total Quality Management) across the organisation.
ELGi is the first globally established, industrial air compressor manufacturer, outside of Japan, to win the prestigious award in more than 60 years.
The manufacturing processes and flow lines are designed to capture the quality parameters and assure adherence at every stage before passing on to the next stage. Auto-guided vehicles and digitalised feedback-based measurement systems are deployed to ensure quality in each stage.
Every ELGi manufactured unit delivers compressed air solutions of quality and best-in-class efficiency at competitive pricing to customers across various
industrial verticals worldwide.
ELGi products have ISO 9001:2015, ISO 14001:2015, ISO 45001 : 2018, Green Product certification, ISO 22000:2018.
ELGi has refined its processes to meet the need for high-precision rotors needed to make screw air compressors and machines working at close tolerances.
ELGi began custom designing and building its own rotor milling machines to meet this demand. A machine-building division was established in 2007 to develop complex in-house machines critical to the process.
By effectively deploying in-house engineering talent and capability, ELGi built these cost-effective machines to ensure the highest quality standards, thereby reducing production costs
Every component of ELGi equipment, from airends to enclosures, undergo rigorous testing and inspection. This maximises operational reliability and reduces the risk for the customer. ELGi offers a warranty of up to 10 years on its oil-lubricated air compressors.
It covers manufacturing defects and faulty parts. It ensures lower lifecycle costs by reducing the need for replacements and repairs. The warranty program reflects ELGi’s confidence in the quality of their compressors
Aside from the quality of its products and warranty, the team at ELGi found it challenging to find technically skilled talent to replace its older, skilled workforce.
To overcome this challenge, ELGi’s invested and developed a vocational training program. This initiative addresses the scarcity of skilled talent by offering technical training in engineering and advanced production technologies. The ELGi Vocational Training School (EVTS) has trained people to work on key assembly lines.
Since August 2023, trainees have attended the B.Voc program in Production Technology in partnership with the Community College of the Central University of Tamil Nadu, India. Graduates are assured employment at ELGi, highlighting the company’s dedication to workforce development and industry excellence. For manufacturers, ELGi isn’t just a supplier, but a trusted partner in productivity, sustainability, and growth.
BAB Aluminium’s long-standing relationship with Capral has been instrumental in its production of sustainable seating solutions that highlight Australian-made quality.
Since its foundation, BAB Aluminium has transformed into an Australian-made manufacturer of diverse seating solutions operating out of Ingleburn, NSW.
Having rebranded the company to BAB Aluminium after purchasing it, CEO Brian Blowes has witnessed many iterations of the aluminium manufacturer. The company initially focused on custom fabrication, producing items such as remote-control gates, pool fences, and aluminium components.
Yet, as the sector evolved, Blowes and BAB Aluminium would adapt to customers that – instead of wanting custom made solutions – just wanted a finished product.
“Seating got bigger to where now it’s almost all we do,” he said.
This venture into seating has been successful, establishing BAB as a trusted name in community infrastructure across Australia. The company’s range has branched out to now include portable grandstands, tables, and benches.
“We have people buy them for their backyards and we have the local council, to schools or universities, sporting groups, to the State and Federal Governments. Everybody is a customer,” said Blowes.
The greatest source of revenue out of these offerings is the grandstand, something Blowes realised after producing his first for an on-seller in Gladesville, NSW. Now, Grandstands Australia produces over one hundred GS1 model grandstands a year as its own brand under the BAB proprietary limited umbrella.
“Grandstands Australia has become a third of our business now. It may well outgrow BAB,” said Blowes.
Grandstands Australia now produces five models – GS1 through to GS5 – with an array of products catered to different settings. Where GS1, GS2 and GS3 are more budget-friendly offerings, Blowes said the company’s GS4 and GS5 models target a large hole in the market between the small movable grandstands and larger stadiums.
“Both start at six metres and four tiers, expandable to 30 metres and eight tiers. A GS4 or GS5 at 30metres and 8 tiers accommodates up to 500 people,” he said.
“There is no one else in the market making a product that sits 500 people.
“We’ve probably produced over $1 million worth of GS4 and GS5 in the last couple of years.”
Aside from grandstands, BAB produces five different table settings and has delved into the schooling sector by establishing the ‘Buddy Bench.’ Originating from America, the Buddy Bench targets bullying and depression by creating a safe place for struggling students toreside.
“If the child’s isolated or anxious, they can go sit there and someone would see that. Whether that be a teacher, peer, parent,” said Blowes.
“It’s a conduit for mental health and antibullying.”
Despite an obvious focus, BAB still manufactures other items including engine parts boxes for the Australian Navy’s ANZAC class frigates.
These BAB products are now making their way around the nation in locations like Rio Tinto mines, where the company’s tables and seats feature in some of the villages and outdoor rest areas. The company also has an international footprint.
“We’ve got seats on a boat on the Thames River in London, and in the US Embassy, Singapore, Thailand, New Zealand and Christmas Island,” he said.
Despite the international reach, Blowes insisted that BAB Aluminium remains an Australian business that produces quality products.
“I grew up on a farm in Crookwell, New South Wales. I am fiercely proud that we’re 100 per cent Australian made and use 100 per cent Australian supply chains,” he said.
Blowes said that this sovereign manufacturing allows the company to produce a high-quality product that is safe and backed by a 20yearwarranty.
“Everything we make here’s got a Structural Certificate and a Cyclone Rating to say that it’s safe and fit for purpose,” he said.
“With the 20-year warranty, if something is wrong with it, I’ll either replace it or I’ll give you a brand new one. In saying that, I have not had a warranty claim in the past 40 years.”
A large part of this emphasis on product safety is the target audience of BAB, which is predominantly schools sporting clubs.
“I make stuff for other people’s kids, so safety
is paramount. We file the edges and go to a lot of trouble to make the best product,” said Blowes.
At the heart of BAB’s products is reliability, which is a key element. Blowes said that there are multiple reasons why aluminium is a more beneficial material compared to others like steel.
“It does not rust and it’s not heavy. The lightness, for transportation and frankly the labour content, is probably half that of working with steel, so there’s cost benefits,” he said.
“The life expectancy on most of this stuff is probably 50-plus years.”
Last year, BAB went through 140 tonnes of aluminium in the development of its various products. When the entirety of a business’s product portfolio and throughput relies on an irreplaceable material, a trustworthy and highquality supplier must be involved.
Capral Aluminium – supplier of high-quality aluminium extrusions, plates, sheet, and coils –has been this supplier for BAB since 1980. This relationship dates to a time where Capral was still operating under its past name.
“We started building the seat supports for Capral, then known as Alcan, around 1991,” said Blowes.
Blowes described his relationship with Capral after 44 years as “like family and symbiotic”.
BAB receives Capral’s aluminium in either an extrusion, or in a sheet, which is then produced into their synonymous products. Above all, Blowes said the quality of Capral’s aluminium stands out amongst the crowd.
“That is why I have never gone offshore. If I am putting a 20-year warranty on something, I need to know the material is good,” he said.
The supply chain between both companies is
stronger than ever, as they schedule aluminium supplies two to three months in advance.
A future of sustainable aluminium
Not only has Capral helped evolve product quality, but it has taken BAB’s sustainable footprint to the next level. When approached by Capral’s Sales Rep Mary-Anne Inguanez in relation to Capral’s locally extruded, lower-carbon aluminium, Super Lo-CAL, Blowes could notresist.
“We’d be crazy if we did not do this. It is a no brainer,” he said.
“The idea of the carbon footprint growing is everywhere. Everything that is in here is now supplied with a super green billet that reduces carbon per kilo of aluminium from 12 to fourkilos.
“BAB’s carbon savings last year would have been 58,000tonnes.”
While the use of Super Lo-CAL has also led BAB’s products to being 100 per cent recyclable at end of life, the company’s sustainability initiatives don’t end there. BAB also practices recycling the many off-cuts that appear after an annual throughput.
“From what we do a year, three tonnes of it becomes off-cuts. We just sell that, and it gets recycled and turned back into an aluminium coke or beer cans,” said Blowes.
The company also prioritises the re-usability of its products such as extrusion packaging and timber and is active in stewardship programs alongside Capral.
“We reuse everything. We are very conscious of our green credentials,” said Blowes.
In a business that has evolved so much in 44 years, Blowes said he is still motivated by the pursuit of a supreme product. Not only is he motivated by a product that he has spent more than half of his life perfecting, but he is driven by the relationships he has forged within his team and across the supply chain.
“It’s a good place. I’ve got good staff. It’s where I live when I’m not living at home,” said Blowes.
“Two of our suppliers are more than 40 years on this with us.
“These are the people that keep me in business. Without those on the supply chain having our backs, we wouldn’t be anywhere.”
One of these supply chain relationships is Capral, which has been an essential part of the company’s success. By working with Capral, BAB Aluminium has expanded its offerings and embraced sustainable materials in a journey to set an example of quality Australian manufacturing.
Atlas Copco introduced the rst VSD compressor, which adjusts motor speed based on air demand, reducing energy consumption.
Advancements in VSD technology led to more efficient compressors with better motor control and enhanced energy savings.
2013
The VSD+ series launch marked a leap forward with a compact design, integrated drive, and improved energy efficiency.
2021
Atlas Copco’s VSDs series features harmonic ltering and energy conversion, pushing compressor technology further.
2023
GA FLX compressor smartly regulates to your air demands by operating efficiently at dual speeds to minimise energy consumption and reduced transient losses
Specialty Doors has embraced innovation, sustainable practices, and craftsmanship to manufacture doors in traditional, commercial and acoustic markets.
After 30 years of producing joinery and flush doors, Specialty Doors has expanded into new markets under the leadership of director, Marcus Bastiaan. Acquiring the company over four years ago, Bastiaan navigated early challenges to transform a struggling product into a profitable one.
“In the first year, branching out was difficult in the static marketplace,” he said.
Despite challenges, Bastiaan was determined to find “the sweet spot in Australian manufacturing”. This led Bastiaan to discover the value in producing custom door products that are quality, scalable and priced in the mid to high value.
“We have found our niche in the custom, hard-tofind and hard-to-make doors,” he said.
“These include entry doors, custom joinery and oversized doors as well as commercial products like fire doors, acoustic doors and lead line doors.”
Approximately 60 per cent of these doors go to reseller markets like hardware and trade yards, with 40 per cent supplied to top tier construction companies for a mix of government and private projects.
Specialty Doors has also broken into the luxury door market with its own flush panel doors, batten entry doors and oversized pivot doors.
“These are your grand entrance pieces on luxury build projects,” said Bastiaan.
Bastiaan said this market – that has grown due to a change in home builder and architect preferences –is currently one of the most profitable and interesting for the company.
“In Australia, they want something unique, breathtaking and spectacular. There are interesting residential and commercial design projects we’re getting involved in,” said Bastiaan.
After identifying a viable product range, the company has grown its production output around 1,000 doors per week, increased its presence in Victoria and even expanded into Queensland, with a team of more than 50 in total.
“Queensland’s a very interesting market and it’s grown. We went up at the start of this year and have had a lot of demand for our specialised doors,” said Bastiaan.
Aside from a key target market, the quality and affordability of Specialty Doors’ products have been drivers in its growth, especially within its luxury door offering.
“We like to focus on providing a high-quality product that’s worth investing in. It’s the statement to your home, so it’s an investment well made.”
To uphold this quality, Specialty Doors implements quality control measures that begin well before
production and continue throughout manufacturing.
“We have long running relationships with certified suppliers and we scrutinise how products are made, pressed, cut, finished and dispatched,” said Bastiaan.
This value on quality extends to the company’s implementation of Australian timber into its products.
“We use Australian hardwoods across our product range including Tasmanian Oak, Blackbutt and Spotted Gum. However, the Victorian Government’s move to ban the supply of Victorian Ash has meant we need to increase the amount of imported hardwood from 20 per cent of our overall use to 80 per cent,” said Bastiaan.
Bastiaan hopes to one day return Specialty Doors’ use of Australian timber to 80 per cent of products as a part of a nationwide push to celebrate its sovereign timber.
“What we have in this country is unique, beautiful and entirely our own,” said Bastiaan.
In addition to maintaining product quality
and sovereignty, Specialty Doors implements sustainability initiatives across processes and materials sourcing. Bastiaan said while a renewed effort around green star rating and responsible sourcing of materials is positive, the company sees the most within its new componentry product offering.
The offering makes use of excess material to reduce the timber going to landfill.
“We use excess timber to create door handles and profile pieces,” said Bastiaan.
“We’d like to change the conversation around hardwood through the door handles, which even for the most environmentally conscious person, is a guilt-free indulgence.”
The success of Specialty Doors has seen Bastiaan spin off into two additional businesses that target alternative niche markets.
energy and timber.
“Specialty Doors is the main show, and then we have two auxiliary businesses that supply our customers with a suite of products,” said Bastiaan.
One of these companies – Specialty Commercial – is a timber extrusions company that produces mouldings, lining, boards and custom timber componentry. The company is the primary beneficiary of the Specialty Doors’ sustainability initiatives that help it save 95 per cent of both
“The new range of handles and hardware that we’re going to be releasing to the market in this year is exciting,” he said.
The second spin off from Specialty Doors is Specialty Acoustics, a company that produces acoustic products for commercial and residential construction projects.
“This brand is a specialised, technical, scientific, and data-driven approach to acoustics, performance
and installation,” said Bastiaan.
Specialty Acoustics manufactures its products to qualified standards and – in collaboration with Acoustic Doors Australia – offers installation services for commercial projects.
Going forward, Bastiaan expects, what is now referred to as The Specialty Group, to further grow into new areas and markets. This growth includes introducing new products into the NSW and South Australian markets.
One of BDO Australia’s key advisory offerings is designed to help businesses navigate the complexities of digital transformation and unlock revenue opportunities.
BDO is an adviser to clients seeking audit, tax, advisory and business services across 164 countries and networks. An advantageous offering for manufacturers is the company’s advisory services that guide clients through challenges, changes, and opportunities.
BDO Digital Partner, Kamal Prasad, said this advisory is crucial in a business’s digital transformation.
“During COVID, everyone was preserving capital. Now, we have seen a lot more demand and discussions happening in the market,” he said.
Working to grow the company’s digital advisory offering, Prasad is one part of the team that helps enhance a business’ digital presence to reach objectives.
“We help clients understand what digital transformation entails and partner with them to drive these changes,” said Prasad.
“It’s about making sure that the business understands what is holding them back.”
This service was born in response to a context where industries, like manufacturing, rely on intangibles to succeed.
“Supply and the customer base are becoming global. Connectedness to what’s happening overseas is a big part of what’s making manufacturers successful,” he said.
Considering the importance of connectivity, along with data requirements, regulations, and cyber security threats, Prasad said manufacturers often lack the guidance needed to keep up with technology, resulting in wasted investments.
“When you have a static setup, and everything else around you is changing, the only thing that you can do is put on expensive band aids,” said Prasad.
To ensure manufacturers avoid wasted investment, BDO’s Digital Advisory Services target digitisation across five pillars.
BDO’s most evident advisory pillar is its digital strategy consulting, which offers businesses a roadmap that is critical to remaining competitive. This strategy includes planning and executing
projects involving data, insights, prototyping, learning, and refinement.
“We discuss what’s happening in the marketplace, where you are, where you want to go, what investment is required, what options are available, and what value – such as revenue, cost optimisation, or risk minimisation – can be generated,” said Prasad.
This planning leads to a board discussion for the approval of BDO’s next pillar, technology modernisation. This focuses on consolidating a business’s technology capabilities, addressing its technology gaps and prioritising suitable solutions.
“The technologies can do whatever you want them to do, but BDO ensures clients make the right choices on prioritisation and configuration,” said Prasad.
This technology-focused pillar connects to the company’s next offering that uses AI to turn data and analytics into insights that reveal market and business trends.
“With tech modernisation, you collect good data,” said Prasad.
An example of this is BDO’s partnership with Microsoft, which has proven beneficial for many clients.
“Microsoft opens the whole new world of analytics that leverage all the AI co-pilot type capabilities to unlock insights,” said Prasad.
BDO also provides business technology solutions
that tailor each system to meet clients’ specific needs and drive efficiency.
“When a packaged solution doesn’t make sense for a client, we build a custom solution,” said Prasad.
Aside from technology advisory, BDO offers cyber security services to identify vulnerabilities and provide protection for digital assets.
“We make sure we secure the technology. It’s a lifecycle of support, from strategy to execution,” said Prasad.
Putting these five pillars together, BDO successfully helped a pharmaceutical company that was focused on investing “as late as possible”.
“We helped the company, which grew from $5 million to around $40 or $50 million,” said Prasad.
Due to this success, the company has extended beyond BDO’s digital strategy guidance, to leverage its expertise in technology modernisation and solutions.
“In aiming to reach $100 million in the next three years, they realised that their systems will hold them down,” said Prasad.
“We are in the process of identifying the right technology for them and vendors to enable it.”
BDO has also serviced a $2 billion global manufacturing organisation working out of Australia using its analytics expertise.
“We started looking for anomalies within their order patterns of the last three years,” said Prasad.
By looking at this data, Prasad and his team were able to increase the forecast accuracy leading to efficient inventory planning, less supply chain wastage and better customer service.
Moving into the future, Prasad said BDO will continue to diversify its offerings to offer an end-to-end service.
“I think what we are doing now to support the clients through the whole journey is helping them implement technology,” he said.
In finishing, Prasad acknowledged that none of these transformations are in one straight line, however BDO’s support can help turn a complex situation into a successful one.
Power Equipment’s generator partnership with Eniquest highlights the company’s ongoing commitment to delivering power solutions for the marine and industrial sectors.
Established in 1990, Power Equipment is a family-owned distributor and supplier of power technology solutions for the industrial and marine sectors.
“The focus of Power Equipment is to provide the best power solutions to suit the market’s needs,” said National Power Products sales manager, Dean Whitford.
More than 30 years ago, Power Equipment’s founder and chairman Allan Foster sparked a close partnership with Yanmar, a renowned engine manufacturer that played a pivotal role in the establishment and growth of Power Equipment.
“Allan took on the distribution, and steadily grew Power Equipment into the existing Yanmar portfolio,” said Whitford.
Building on this initial partnership, Foster steered Power Equipment into new markets, leveraging the company’s unique position as one of Australia’s few independent engine distributors.
“That flexibility to package and deliver exactly what the customer needs as a result of the access to various products has been a key to success,” said Whitford.
This has seen the company partner with a stable of recognisable brands, positioning the company as one of the largest independent distributors of marine and industrial power solutions across Australia, New Zealand, and the South Pacific.
“Quality is what has built the company and made it dominant in its own market,” said Whitford.
These brands – that include John Deere, Cox Marine, Smartgyro, Torqeedo, OXE Diesel, PSS Shaft Seals, Gori Propeller, Hundested Propeller, and Mase Generators – are now distributed by a network of more than 400 sales and service dealers across Australia and New Zealand.
“The company spent a lot of time in establishing a very comprehensive dealer network,” said Whitford.
Generating the future of power solutions
One of the company’s newest partnerships came in the form of an exclusive distributor agreement
with Eniquest, an Australian-made diesel generator manufacturer. In a relationship that dates back decades, the agreement was reflective of Power Equipments trust in Eniquest as a brand that advances quality generators across industries like marine, military, mining, and renewable energy.
While previously focused on supplying units for government, military, and private contracts worldwide, this agreement saw Power Equipment bringing Eniquest’s locally designed generators to a commercial market.
“We had the distribution, sales and marketing to effectively help them sell more of the great product they’ve developed,” said Whitford.
After signing the agreement, Eniquest was able to expand its product range and reach new markets.
“You need to be able to have the options that people are looking for. It’s been big for us to offer options that we previously didn’t have access to,” said Whitford.
Eniquest’s diesel generators come in three ranges that offer different features based on customer needs and workplace environment.
Despite its small size, the Husky is Eniquest’s reliable generator that excels in a range of applications, including pumps and irrigators. The Ranger, however, is Eniquest’s low noise offering for residential and back of the truck type of applications. Finally, Eniquest’s mid-size extension of the Ranger, the Stockman, is suitable for all power requirements and comes in an enclosed or semi-enclosed variants.
These generators have proven essential in
various applications, including powering site vans manufactured for rental companies.
“Within those vans, there’s generally a kitchen, microwave, TV, and air conditioners. Because they’re remote, they need to ensure that they’ve got power that’s reliable. There’s not necessarily someone around to fix a problem if there is one,” said Whitford.
“Our answer is we just supply something that doesn’t have a problem.”
In what has been a fruitful partnership so far, Whitford said that the company has now moved to expand its range with John Deere systems.
“Being able to introduce the John Deere product to Eniquest has expanded their horizons. They’re now building much larger units to accommodate those units,” said Whitford.
“We’ve already started with the first unit, which is the Stockman 850 powered unit with a John Deere 4045 engine.”
Aside from its agreement with Eniquest, Power Equipment is continually scouting different global brands to further add to its reputation as a top Australian distributor.
“We will continue to follow a very clear direction to make sure that we’re getting the best of every product that we have, while also ensuring new products integrate seamlessly and complement our existing range,” said Whitford.
Following the acquisition of INMATEC by the BOGE Group, BOGE Compressors Australia has been supporting the Oceania region through its partner network for on-site gas generation projects since August 2023.
With more than 9,000 systems installed worldwide, INMATEC stands for innovative technology from 30 years of research and development “Made in Germany.”
Maximum-purity nitrogen is required as a process alongside inert gas in not only the chemical industry but also in other sectors such as food and beverage. Companies have the choice to procure the gas from third parties or to generate it themselves. The benefits of generating it independently are obvious: the quantity, purity and pressure can be easily controlled and adapted to requirements. This also avoids costs for delivery and storage, and means the gas is available when needed. Purity is monitored continuously – another advantage of onsite generation.
The two elements of an ingenious concept
Combining a modified PN nitrogen generator (PNK) and an H2KAT hydrogen converter, INMATEC, which is part of the BOGE Group,
offers an efficient system for the independent generation of maximum-purity nitrogen (0.001 per cent O2 [degree of purity 5.0]).
The compressed air is filtered and dried before the nitrogen is separated from the ambient air using PSA technology and a high-quality carbon molecular sieve.
The generated nitrogen, which has a purity of 0.1 per cent O2 (degree of purity 3.0), is first stored in a buffer receiver, then enriched with tiny quantities of hydrogen in the H2KAT. Residual oxygen molecules are removed from the nitrogen and bound with hydrogen to produce water vapour. The nitrogen then has a purity of 0.001 per cent O2 (degree of purity 5.0).
The H2KAT is available in eight versions with free air delivery of up to 300 Nm³/h. To match these, there are eight PNK models with their technology being adapted to the relevant H2KAT.
The advantage of this two-stage process for nitrogen generation is a reduction in compressed
air consumption by about 40 to 50 per cent compared with the traditional generation of nitrogen with a purity of 0.001 per cent O2 (degree of purity 5.0).
The generator has been designed for a fixed purity of 0.01 per cent O2 (degree of purity 3.0). The required quantity of compressed air can therefore be reduced by almost half. This has an impact on investment costs because compressed air stations, treatment components and the generator can be much smaller. By reducing the quantity of compressed air provided, energy costs can also be saved, as well as CO2 emissions lowered.
Another advantage is that customers will receive the entire system consisting of compressor, compressed air treatment, nitrogen generator and hydrogen converter from one source.
Due to the combination of INMATEC technology and BOGE compressors, customers are provided with a reliable system that guarantees a continuous and particularly efficient nitrogen supply.
•Nitrogen at any time and at any place.
•Air factor from 2.9.
• Lower compressed air requirement and power savings of up to 50 per cent.
•Cost-effective through low operating costs.
•Sophisticated and reliable technology.
•Exact purity for every application.
• No rental commitments as with bottles/ bundles and tank systems.
•No CO2 pollution for the environment.
Using extensive knowledge of electronics servo drives, Datafactory offers services for a complex industrial environment.
With theoretical and practical knowledge of electronics servo drives, Datafactory offers unique services in what is a complex industrial environment.
Established in 1986, Datafactory has experts that excel in the repair of electronic variable speed drives and power converters.
The company has a well-equipped lab where drives – like AC drives, vector drives, DC Drives, servo drivers – can be both repaired down to a component level and power tested.
The company repairs, re-programs, upgrades and replaces all types of electronic variable drives, including old models that are no longer supported by their manufacturers.
Chartered professional engineer and member
of Institute of Engineers Australia, Darius Kowalewski, heads up Datafactory with years of industry experience including a long career in the R&D service and commissioning of power electronic systems.
Kowalewski also brings to the table university qualifications, completing a Bachelor’s Degree in Electrical Engineering and a Master’s Degree in Digital communication Protocols.
Kowalewski and his team of like-minded individuals make Datafactory the go-to service when consumers need professional advice for a hi-tech gear breakdown.
Recently, labels manufacturer, Pack Creations, experienced one of these technology issues. Datafactory was contacted to repair two
Baumuller servo drive units that were a mainstay of an industrial production line.
Despite being a mainstay, the units are obsolete, which means no one wants to service them.
Datafactory’s repair offerings were vital in this and many other cases.
Despite being described as ‘sophisticated’ and ‘challenging,’ the company would repair two of these drives and begin work on a third.
Chicago Pneumatic continues to adapt to an evolving landscape of machinery with its CPVS 75-120 oil-injected screw compressor.
Chicago Pneumatic has responded to the evolving landscape of industrial machinery with its latest innovation – the CPVS 75-120 oil-injected screw compressor.
This compressor, ranging from 55 kW to 90 kW, is the result of investment in research and development, as well as in-house developed key components. At the heart of the CPVS range lies an in-house designed compression element, paired with an IE4 efficiency motor. This combination not only enhances performance but also ensures lower compression temperatures and reliability. These compressors are designed to thrive in environments with ambient temperatures of up to 46°C due to the to component design.
For units across the entire industrial range equipped with an integrated dryer, an internal water separator is also integrated in the air cooler to ensure optimal performance and efficiency.
The new generation compression element, crafted in Belgium, provides improved performance and capabilities. With increased volumetric efficiency and reduced pressure losses, the CPVS 75 - 120 delivers up to 4 per cent more free air while consuming up to 3 per cent less power.
The Interior Permanent Magnet (iPM) motor, another feature of in-house Belgian engineering,
exceeds IE4 efficiency levels. This oil-cooled motor provides optimal cooling at all speeds, making it eco-friendly and efficient. Its IP66 rating further underscores its robustness and suitability for highspeed operations.
Noise reduction is a critical factor in industrial settings, and the CPVS 75-120 addresses this with its silencing baffle. The filter mats pre-filter incoming air, ensuring good air quality and low noise levels, making it suitable for operations close to the point-of-use.
The separate oil and air coolers are designed for high-quality cooling and extended lifespan. With a 5°C reduction in element outlet temperature and easy access for cleaning and maintenance, these coolers exemplify thoughtfulengineering.
The in-house designed inlet valve optimises the flow to the screw element, offering maintenancefree operation and a low total cost of ownership. Similarly, the in-house casted oil separator vessel
with an integrated minimum pressure valve (MPV) ensures optimal oil separation and minimal oil carryover, eliminating leakage risks.
Control and connectivity are at the forefront with the next-generation ES4000T touchscreen controller. This user-friendly, full-colour graphical display with touchscreen functionality, coupled with integrated connectivity through ICONS, helps optimise operations and achieve energy savings. Finally, the in-house designed inverter, featuring Imperium – Variable Speed Technology, is tailormade for screw compressor applications. Its industrial design, complete with IP5X protection, ensures durability and reliability.
The CPVS75 – 120 oil-injected screw compressor is a blend of innovation, efficiency, and reliability. Chicago Pneumatic has demonstrated its prowess in delivering solutions that meet the needs of modern industrial environments, all while enhancing energy savings.
Quality components ensures reliable technology
Smooth regulation
Easy operation, always in control
Low energy and maintenance cost
Manufacturers’ Monthly spoke with BlueRock Digital director, Thomas Adams, to explore how the company advises businesses to drive growth, reduce costs, and streamline supply chains.
Founded in 2008, Australian advisory firm BlueRock has expanded rapidly, evolving from a focus on accounting advisory to servicing a range of business and wealth solutions.
“BlueRock wanted to provide services to help other high-growth companies to scale, mature and develop,” said company digital director Thomas Adams.
Among its offerings is BlueRock Digital, an advisory service designed to help business owners tackle the complexities of the everchanging digital and technology landscape.
“Having advisors like us that can speak to you, understand your business and identify opportunities gives a foundation for a business to grow,” said Adams.
A key offering of BlueRock’s Digital advisory is its implementation of inventory management software, a tool designed to enhance business efficiency and growth.
“It’s a platform that is very expansive and powerful in nature,” said Adams.
By replacing manual methods of inventory management – like spreadsheets and data entry – with automated solutions, Adams said the software can help businesses improve operational visibility and supply chain efficiency.
“We can help businesses understand their tech stack. We create a roadmap for the coming years and how inventory management software can help achieve it,” said Adams.
To provide the best version of the software to its customers, BlueRock is the implementation partner for software Cin7: Inventory Solutions, and other systems such as MRPeasy.
“We work with providers that offer solutions that are fit for our clients. We’ve got a large client base
in the manufacturing and inventory warehousing sector that benefit from Cin7’s functionalities,” said Thomas.
benefits
Adams explained that a key reason BlueRock advises businesses to utilise inventory management software is its ability to reduce costs and recover lost revenue for businesses.
“We’re able to add value to these businesses by providing guidance for them to reduce costs and recoup lost revenue,” said Adams.
Adams explained that the automated platform offers stock insights, enabling cost optimisation, accurate forecasting, and error reduction.
“These systems can optimise stock levels, so businesses are not holding too much or too little. They can also forecast demand and reduce storage costs,” said Adams.
Adams said another benefit of the automated platform is how it reduces the human error associated with manual processes.
“When you reduce manual errors, you get efficiency through your whole manufacturing line. There’s less delays and no downtime for machines,” said Adams.
These manual processes are also laborious and time consuming, something which Adams believes the software can eliminate.
“You can get cost savings on the human resource side by freeing workers up to be doing the manufacturing itself,” said Adams.
Another key benefit of the platform is its ability to minimise errors caused by rushed work or cutting corners.
“When you’re running a skeleton crew, you can reduce the number of hats that individuals wear. You’re less likely to get fatigued and make mistakes.
This is relevant in manufacturing, where there is risk in operating machines,” said Adams.
In addition to its efficiency, Adams highlighted a valuable benefit of the platform in its ability to create a cleaner manufacturing process.
“You reduce the waste of excess products,” he said.
Aside from benefits to the business, Adams said that these systems can ensure a purchasing experience where a customer has full visibility of stock, backorder and shipping information.
Not only can BlueRock Digital advise the use of inventory systems, but the company has also demonstrated its ability to customise them to client needs through a butchery case study. Unlike inventory systems that track items per unit, butcheries deal with products sold by weight, which presents challenges.
“If you order a pair of shoes online, your warehouse staff can pick one pair of shoes, but they can never pick 1.1 pairs of shoes,” said Adams. Standard systems often block orders with mismatched weights, requiring manual adjustments to sales orders – a time-consuming process that involves voiding and recreating orders to match weights. To address this, BlueRock developed a solution that automates these processes, improving efficiency and ROI.
“We built an application that acts as a wrapper over their Cin7 system and allows that process to happen in the background,” said Adams.
“They run the application on a tablet, scan the meat, it comes at 1.1 and then they click that it’s picked at 1.1, and it sends it through.”
Looking ahead, Adams noted that technologies like AI, IoT, and machine learning will drive future inventory innovations, enabling small businesses to adopt advanced tools like those used by industry leaders like Amazon.
“I envisage us working through more solutions and doing more in the machine learning, algorithms and analytics space to help businesses run efficiently,” he said.
The Manufacturers’ Monthly Endeavour Awards 2024 was a great night for those who gathered to celebrate Australian manufacturing.
Held in Melbourne this past November, the Manufacturers’ Monthly Endeavour Awards provided an opportunity for those in attendance to celebrate the recent successes of theindustry.
The evening culminated in the announcement of the 2024 ‘Manufacturer of the Year’ award, which was claimed by data solutions innovator MEQ. Known for the application of its technologies towards the red meat industry, MEQ earned a double victory. In addition to the top accolade, the company’s MEQ Live solution won the 2024 ‘Technology Application’ award.
The presentation was also a time to recognise pioneers of the industry. In line with this, the 2024 ‘Leader of the Year’ award went to Geoff Crittenden for his 30 years of industry experience at Weld Australia.
The winners were evaluated by a distinguished panel of judges made up of manufacturing figureheads, production experts, and industry associations.
“In Australia there is a national commentary about the decline of manufacturing, which isn’t accurate or useful. There are many segments of manufacturing that are innovative and pioneering, and these should be celebrated,” said judge and CSIRO group leader of Electromagnetic Systems and Devices, Dr Scott Martin.
“The awards perform the valuable purpose of inspiring and encouraging other firms to take the plunge and embrace innovation themselves.”
Within the following pages, you’ll gain insights about each company honoured with an award in each category.
Weld Australia’s Geoff Crittenden, a chartered engineer with more than 30 years of experience, has made contributions across multiple industries, including engineering, consulting, healthcare, and not-forprofit sectors.
His career spans leadership roles in some of Australia’s top organisations, and he is known for his ability to lead multidisciplinary teams through complex environments. As a strategic thinker, Crittenden has driven growth and success with longterm business strategies that have left a lasting impact.
Starting his career as an engineer in the British Army, Crittenden served there for more than 15 years. Following his decision to immigrate to Australia, Geoff took on his first civilian role as CEO of the Association of Consulting Engineers.
He later held senior positions with Transfield Worley, Cynergy Group, and the Risk Management Institute. Since 2014, Geoff has served as CEO and executive director of Weld Australia, further cementing his reputation in the engineering industry.
Established in 1925, Weld Australia is a not-for-profit, membership-based organisation that represents the welding profession in Australia.
“Our members, ranging from individual welding professionals to companies of all sizes, play a vital role in almost every facet of Australian industry,” saidCrittenden.
Weld Australia’s team is engaged in several initiatives, such as the implementation of new resources for the MEM training package, the Advanced Manufacturing Schools Outreach Program, upskilling opportunities for Indigenous Australians and prisoners, and the Women in Welding project.
“I’m particularly proud of Weld Australia’s advocacy for domestic renewable energy manufacturing,” added Crittenden.
“Working closely with federal and state governments, we’re ensuring projects are made locally, supporting jobs and quality standards. As cheaper imports threaten Australian manufacturing, our efforts are focused on securing a sustainable future, with renewable energy solutions made by Australians, for Australians, and strengthening our manufacturing sector for generations to come.”
Weld Australia remains dedicated to advocating for its members and is focused on strengthening and expanding key initiatives. The organisation aims to see its Advanced Manufacturing Schools Outreach Program, Indigenous Welding School, and MEM learning resources adopted nationwide.
Weld Australia’s plans focus on revitalising Australia’s manufacturing sector. The goal is to restore manufacturing to its former scale when it accounted for more than 10 per cent of Australia’s GDP.
“With key sectors like defence shipbuilding, renewable energy, and critical minerals growing, Australia needs a robust manufacturing sector to meet these emerging demands,” saidCrittenden.
“We aim to strengthen local industry and reverse the trend of offshoring, creating a resilient, domestically driven manufacturing landscape that will support Australia’s future.”
Crittenden attributed his 2024 Endeavour Awards to the collective effort of his team at Weld Australia, emphasising the importance of collaboration and the role played by his colleagues in achieving success.
“This win highlights our commitment to promoting the critical role that welding plays in building and maintaining the highest standards of excellence in manufacturing,” he said.
“Over the past 50 years, I’ve learned one crucial lesson: it’s not about you; it’s about the people who work with you.”
The
Australian germicidal light manufacturer, Lindo, has had a rapid evolution since its transition from the Gangi Germicidal Systems in 2022. The company was founded to develop products that utilise UV-C and antimicrobial blue light to disinfect and neutralise up to 99.99 per cent of pathogens on surfaces and in the air.
Lindo services an array of industries including healthcare, transport, and defence, and is committed to sustainability processing using no harsh chemicals. The company has supplied industries with offerings that include the Lindo Chamber for product disinfection and the Lindo Light for surface disinfection. Lindo has also seen an array of its innovations supported by research partnerships with institutions like Swinburne University and Eurofins.
Founder and CEO Robert Gangi said these applications of the company’s technology weren’t enough. This shift in mentality left Lindo committed to doing more.
“We started as a company installing our lighting systems into facilities, including aged care homes. We quickly realised that we could do a lot more with our antimicrobial blue light,” said Gangi. Gangi said this transition required Lindo to problem solve by searching for more potential applications of the company’s antimicrobial blue light.
“We searched healthcare to see what the major issues were and whether or not our tech could assist,” he said.
This dissection of the healthcare industry led Gangi and his colleagues to the serious medical issue of ventilator associated pneumonia (VAP). VAP is a potentially fatal infection that develops within the lung of a patient that has been on a mechanical ventilator for at least 48 hours.
Responding to this issue, Lindo created Lindo Tube, a system targeted at reducing the mortality and morbidity associated with the condition.
“We worked out the cause of the problem and came up with a fairly simple design,” said Gangi.
In what Gangi referred to as his “proudest project of the year,” the solution involves an endotracheal tube that has been engineered together with an antimicrobial blue light. After developing the design, Lindo successfully approached the market this year by signing a milestone agreement with Mayo Clinic in the US to co-develop the device.
“The ability to collaborate with Mayo Clinic has provided our team with a great platform for success,” said Gangi.
This innovation, adaptability and unwillingness to remain comfortable earned Lindo the ‘Outstanding Start-up Award’ at the 2024 Endeavour Awards.
As the audiences’ focus shifted to the companies driving the country’s innovation, Gangi took to
the stage to accept the award on the behalf of his team.
“It’s a great recognition for not only myself, but the entire team, including our lead engineer Urbain, and the product design team, Lloyd and Troy. It’s a great reward for effort. The team and I are excited,” said Gangi.
“If my wife was here not looking after my wonderful children, I couldn’t thank her enough. She’s been amazing.”
Unwavering in its commitment to innovation such as that shown by Lindo is BlueRock, the sponsor of the award and a driver of emerging talent in manufacturing. As a purpose-driven advisory firm, the company supports start-ups on their journey to making an impact.
Moving into next year, while Gangi remains focused on Lindo Tube, he said that the company is searching for other potential applications for the antimicrobial blue light. One of these applications surrounds the development of a prolonged field care system for the defence industry.
“We call it the Hudson Bioelectric Bandage. It’s a light emitting pad that can not only reduce infection rates within wounds but also read vitals from a patient,” said Gangi.
Lindo’s rapid evolution and commitment to innovation has positioned the company as a leader in antimicrobial solutions with the potential to transform healthcare and beyond.
The 2024 ‘Technology Application of the Year’ award was presented to MEQ Live, a real-time data solution designed for feedlots and producers.
W“Our genesis was driven by two things, the lack of digitisation across Australia’s $17.6 billion red meat industry and the creation of new technology to accurately and objectively measure the eating quality of meat,” said Carbone.
Since its foundation, MEQ has been dedicated to building a digital future for the red meat industry, one device and solution at a time. The company designs, develops and manufactures its products in Australia, aiming to transform efficiency, quality, nutritional value, and environmental sustainability for feedlots and producers.
“We started with just one device, the MEQ Probe, which uses spectral analysis and AI to evaluate beef and lamb – and now offer a connected suite of products,” said Carbone.
This suite includes MEQ Live, which was designed to enhance animal performance insights with yield and marbling data collected from live animals. The platform was recognised at the 2024 Endeavour Awards with the ‘Technology Application Award.’ The technology can identify the performance of
Aside from increased visibility and operational efficiency, Carbone highlighted a case study that displayed the sustainability benefits of MEQ Live.
“It showed that a MEQ Live device could yield a reduction of over 2.3 million tonnes of carbon dioxide equivalent emissions,” he said.
“When considering direct emissions and indirect value chain reductions, this translates to a 44 per cent decrease in carbon emissions.
“MEQ products help the entire red meat supply chain – from farmers to retailers – make smart decisions based on accurate data on quality, nutrition and environmental impacts.”
This year, MEQ also added an insights platform to support and enhance its hardware suite. Carbone said the rollout of this insights platform was a proud moment in a breakout year for the company.
“This is transformational for the industry, and we hope it will bring about important changes across the supply chain,” he said.
“Our new platform can include insights into a client’s population across time, sorting by any trait,
grader comparison, and any carcass can be reviewed
“We’re a big believer in the importance of high-tech manufacturing to Australia’s future, and the power of technology to transform industries. It’s humbling to be alongside some outstanding fellow finalists,” he said.
Sponsors of the award, Weld Australia, were proud to present and support an award that aligns with its values to promote industry standards and safety.
Presenting the honour was CEO of Weld Australia and fellow award-winner, Geoff Crittenden.
“As advocates for excellence and innovation within the manufacturing sector, Weld Australia is proud to sponsor the Technology Application Award at the 2024 Manufacturers’ Monthly Endeavour Awards,” saidCrittenden.
“Our commitment to enhancing industry standards and promoting safety aligns perfectly with the goals of these awards.”
MEQ’s innovative approach to digitising the red meat industry is set to boost operational efficiency and sustainability going forward, setting the stage for a transformation across the entire supply chain.
Many industries worldwide, including structural buildings, bridges, mining equipment, marine applications, and more, now require welding to comply with the AWS D1.1 code. Achieving this certification ensures fabrication and inspection meet stringent quality standards, helping companies reduce rework, minimise costs, and deliver projects on time.
Cristian Zanfir joined the CWB Group in 2004. Over the years, Cristian has held several key positions within the organisation, including Procedure Verification Engineer, Supervisor of Ontario Operations, Supervisor of Procedure Verification Engineers, and in the Electrodes Certification Department. Today, Cristian serves as the Manager of Standards in the CWB Group's Office of Public Safety. In this role, he plays a pivotal part in the development of standards, actively contributing to numerous committees within AWS, ASME, CSA, and ISO.With a Bachelor of Engineering in Welding and a Level 2 Visual Welding Inspector certification, Cristian brings a wealth of expertise and dedication to advancing welding standards and practices globally.
This comprehensive course explores the requirements for AWS D1.1 compliance, covering key topics such as:
Certification for welding contractors, inspectors, and procedures
Visual welding inspection techniques
Pre-qualification and qualification of welding procedures
By adhering to AWS D1.1 standards, companies ensure the reliability of steel structures and machinery, improve weld quality, and uphold the integrity of quality control. From managers and engineers to welders and inspectors, all personnel gain valuable knowledge on weld imperfections, preventive measures, and achieving excellence in welding processes.
Scan the QR code to register now.
For further information contact Michelle Tagliapietra on 0437 106 726 or m.tagliapietra@weldaustralia.com.au
The 2024 Towpreg is an impregnated carbon fibre
The world-first Towpreg system developed by Sydney-based firm CST Composites, took home this year’s ‘Project of the Year,’ at the 2024 Endeavour Awards. The CST Towpreg is an impregnated carbon fibre tow that was used for the masts of the ILCA6, ILCA7, 49er, and 49erFX-class sailing boats featured at the 2024 Paris Olympics.
“It is a tremendous honour. It highlights our commitment to excellence and innovation within the Australian manufacturing industry,” said finance executive at CST, Glenn MacPherson.
“We are particularly proud of developing a worldfirst Towpreg production system with live closedloop feedback.
“This lifted the quality of our tubes to be bestin-class worldwide and enabled us to supply more than 50 per cent of all the sailing masts used at the 2024 Paris Olympics.”
This project is the latest in an almost 30year history of CST innovations that have been manufactured at two facilities in Sydney. It was undertaken to develop the world’s first sailing masts with a performance variation of less than 2 per cent, down from an average of 15 per cent, without increasing costs. The target for these new masts being the Paris Olympics.
Alongside evening the playing field for sailors,
Towpreg quickens winding speeds while facilitating the use of multi-spindle winding machines. Not only does this translate to productivity, but also a reduced manufacturingtime.
The Towpreg sees consistency of resin impregnation across the fibres, which improves product quality and performance, ensuring the reliability of the final product.
The Towpreg also allows greater control for manufacturers over resin and fibre volume and allows them to monitor and control the fibre bandwidth during production. This enables precise customisation of material properties and tighter design tolerances, which can lead to potential savings.
Additionally, the system can create a safer work environment by minimising exposure to hazardous fumes and chemicals and can open opportunities for automation and robotics in filament winding operations.
“CST has seen a dramatic improvement in quality with three times less rejects, nine times less non-conforming parts and 20-30 per cent improvement in productivity,” said managing director, CST, Clive Watts.
“We can now supply high-quality towpreg to other filament winding companies in Australia and overseas to improve the quality of composite products in the industry,” he said.
Looking ahead, MacPherson said the company has a plan to become the first Australian producer of composite over-wrapped pressure vessels.
“Our in-house Towpreg gives us the competitive advantage to compete worldwide,” he said.
CST Composites’ development of the Towpreg system exemplifies the company’s dedication to innovation, quality, and global competitiveness in the composites manufacturing industry.
BDO Australia, known for its sector expertise, backed the ‘Project of the Year’ category in 2024 as the sponsor of the award.
Amiga Engineering, founded in 1988 by Michael Bourchier and his brother Dale, has built a legacy of innovation in advanced machining, fabrication, and custom manufacturing.
With a clear vision to enhance Australian industry, Amiga has always been ahead of the curve, recognising early on that Australia sometimes lags in adopting cutting-edge technologies. This foresight has driven the company to make bold investments in modern manufacturing techniques, ensuring that the Australian industry remains competitive on the global stage.
Notably, Amiga has pioneered developments such as 3D-printed metal ballistic titanium armour. For more than three decades the company has continually embraced technological advancements and taken leaps forward, bridging the gap between Australia and global innovation.
At the core of Amiga Engineering are the values of innovation, precision, and collaboration.
“Our mission is to provide engineering and manufacturing solutions that empower ideas and drive technological advancement,” said managing director Bourchier.
“What makes our journey truly special is that, for decades, Amiga Engineering has been the world’s best-kept secret. As a small family business, we’ve worked tirelessly to develop capabilities that rival the largest players in the industry.”
With a history of innovation in advanced machining and manufacturing, this year Amiga earnt the ‘Most Innovative Manufacturer of the Year’ award at the 2024 Endeavour Awards.
“Amiga Engineering is honoured to win the ‘Most Innovative Manufacturer of the Year’ award,” saidBourchier.
“This recognition highlights the hard work and dedication of the team, as well as the groundbreaking innovation they have brought to the manufacturing sector.”
SEW-EURODRIVE, a specialist in mechanical power transmission, sponsored the award.
“As a long-time sponsor of the Endeavour Awards, SEW-EURODRIVE sees the value in inspiring and recognising those in the industry who have made advances in their field,” said marketing coordinator, SEW-EURODRIVE, Katrina Dalgleish.
“As a market leader in drive technology used across the manufacturing sector, big or small, SEW-EURODRIVE sees our involvement in the awards as paramount in building and maintaining important relationships that foster growth and ingenuity throughout the sector.”
Amiga’s development of 3D-printed metal ballistic titanium armour has advanced the possibilities in defence and protective applications. This accolade validates Amiga Engineering’s commitment to pioneering
Amiga’s metal 3D-printed ballistic titanium armour has been a achievement for defence and protective applications.
advanced manufacturing techniques that provide practical solutions.
This innovation also demonstrates the company’s ability to produce complex, high-strength, and lightweight solutions using additive manufacturing techniques
“From humble beginnings, we’ve built a reputation for excellence, supporting industries like medical, food, mining, and agriculture. It’s rewarding to see the world recognise our hard work, and we’re excited to keep serving global industries while staying true to our family values,” said Bourchier.
The company plans to continue expanding its capabilities in advanced manufacturing, particularly in Defence and Aerospace.
The company is actively working on new applications for materials like Scalmalloy and tungsten, both of which have high potential in aerospace and hypersonic technologies.
Amiga Engineering also aims to expand its presence in international markets, further establishing itself as a key player in metal 3D printing.
“Our goal is to remain at the forefront of innovation, continuously pushing the boundaries of what’s possible in engineering and manufacturing,” concluded Bourchier.
“We also have an exciting new product and project in the works, which we look forward to sharing in time.”
Proud sponsor of the Endeavour Awards
Our extensive range of products and services ensures we deliver quality solutions for a wide variety of motion applications.
Industries include but not limited to:
• Food and Beverage
• Manufacturing
• Logistics
• Wastewater
• Agricultural
• Mining
Products and Services include:
• Gearmotors and Gear Units
• Motors
• Decentralised
• Mechanical Variable Speed Drives
• Heavy Industrial Solutions
• Product Life Cycle Services
• Online Support
• Custom Engineered Drive Solutions
• ...and many more!
After taking home the 2024 ‘Technology Application of the Year’ award, MEQ also secured the Endeavour Awards’ top honour. In what proved to be a successful evening for the company, MEQ was presented the prestigious ‘Manufacturer of the Year’ award.
With a history of recognising industry leaders, the award is not only a testament to the work of MEQ co-founder Remo Carbone, but to other team members within the company.
Representing MEQ at the awards night was the company’s chief technology officer, Jordan Yeomans. In his acceptance speech, he mentioned those who have helped the company grow since its infancy stages as a PhD project.
“We were a startup that was the genesis of a couple of PhD programs, and since then, we’ve built our team from one person to 35 people,” saidYeomans.
“We’ve got two of my colleagues here, Thomas Pemberton and Ray McMahon. I’m very proud to have them here with us today.”
Echoing the excitement of those in attendance, Carbone was thrilled to be taking home the Endeavour Awards’ “top gong.” He expressed his gratitude for the opportunity to proudly fly the flag for Australian manufacturing startups working in the agricultural sector.
“Winning the Manufacturer of the Year Award is
a milestone for MEQ,” he said.
“MEQ is still a relatively young business, so this recognition is all the sweeter. Agtech is a huge opportunity for the country, and we hope to see more of our peers appear in the awards in future.
“Thanks to Manufacturers’ Monthly for running the Endeavour Awards, we’re humbled to be joining a great group of winners.”
In line with the evident growth of the company, Carbone has seen MEQ’s clientele evolve from a handful of Australian processors to some of the largest agricultural players in the world.
“The devices we build are used in the US, the UK, Europe and New Zealand as well as here in Australia,” said Carbone.
Carbone said that an element of this success can also be attributed to the company’s commitment to never stray away from its mission to help the entire red meat supplychain.
“Our mission is to build the data-driven digital future for the global red meat industry to radically transform efficiency, quality, nutritional value, and environmental impact,” he said.
Yet, Carbone said MEQ’s rise to prominence wasn’t without its challenges. From the delayed development of its first Probe, to having to build manufacturing capabilities from scratch, he said the challenges were overcome due to an incredible team.
“It’s not easy to start a high-tech hardware business,” he said.
“Our success is possible due to our team of engineers, developers and technicians, and of course to our clients.”
Moving forward, Carbone said the company’s growth in the past two years is only scratching the surface of what is possible in terms of capability and market presence.
“Last year we entered a partnership with global technology business Siemens, and we are seeing more interest in international markets. We’re just getting started,” he said.
“It’s important that Australia takes advantage of its engineering ingenuity and technical research leadership. We believe that high-tech startups have a role to play in transforming manufacturing across subsectors.”
MEQ’s recognition at the 2024 Endeavour Awards highlights the company’s innovation and dedicated team. With ambitious plans in the pipeline, MEQ is poised to drive transformation in the agtech and manufacturing sectors.
The award this year was sponsored by Bestech Australia, who themselves are trailblazers in supplying sensors, instrumentation, and teaching equipment for sectors like manufacturing, the military, mining, and research laboratories.
Our inline plasterboard measurement system comprises two high-precision laser profile scanners, offering both online and motorised offline caliper systems for measurement of edge angle, edge width, recess width, depth and board thickness. Place this system anywhere on the forming belt and you can monitor the profile from anywhere.
Contact our engineers or visit www.bestech.com.au for more information.
Email: enquiry@bestech.com.au
Recce Pharmaceuticals has entered global clinical trials with a product that could be a game changer for the medical industry.
Sydney-based Recce Pharmaceuticals has developed a new class of anti-infectives capable of protecting against the growing threat of antibiotic-resistant bacteria. What started as a vial within the garage of founder Dr Graham Melrose, has been taken international by Graham’s grandson, James.
The company, which was formed and concentrates wholly on the manufacture of these compounds, is now conducting clinical studies in Australia, and will soon conduct clinical studies in Indonesia.
These studies aim to form a product capable of addressing Antimicrobial Resistance (AMR), a global health threat according to the World Health Organization (WHO).
“Antibiotic resistance is occurring before us. There hasn’t been a new class of antibiotics in nearly 40 years,” said CEO and managing director of Recce Pharmaceuticals, JamesGraham.
Graham believes because of AMR; the world has been exposed to the “challenges of antibiotics”.
“The reason they’re doubling the dose and extending the time of consumption is that ten years ago bacteria was treatable. Ten years later, it’s evolved to survive,” he said.
As a result, Graham said the world is on the potential horizon of a pandemic where pharmaceuticals wouldn’t work due to a dry pipeline ofinnovation.
This emerging issue is already showing its impact, with an Antimicrobial Resistance Collaborators report stating that AMR directly caused 1.27 million deaths globally in 2019, and nearly 5 million deaths were associated with drug-resistant infections. WHO warns that if no action is taken, AMR could cause 10 million deaths per year by 2050. A Lancet study estimates that 1.91 million deaths per year will be directly due to AMR, and 8.22 million deaths will be associated with AMR.
Humble beginnings to global breakthroughs
Recce’s Pharmaceuticals was founded in 2007. The company’s foundation surrounds Melrose, who only discovered the compound that would form the basis of Recce Pharmaceuticals when he retired.
“He goes into the garage, pulls out a vial, and says, ‘I think this thing’s got antibiotic properties.’ At that
time, I was a grandson supporting him in getting out of a garage and into a laboratory,” said Graham.
As a co-investor, Graham used his commercial expertise to transform the idea into a reality. Now serving as managing director and CEO, he has spent the past two and a half years guiding a product designed to deliver results.
Short for reconnaissance, Recce’s products currently being clinically trialled are aimed at getting behind enemy lines and eliminating the target undetected. According to The Pew Charitable Trusts, the company produces the most clinically advanced new class of antibiotic or anti-infective in the world.
“We’re the only clinical stage, synthetic compound in the world, to my knowledge. We’ve got the only qualified infectious disease designation awarded by the FDA for sepsis,” said Graham.
At present, Recce’s portfolio of products now includes three anti-infective products: RECCE 327, a rapid-action, broad-spectrum antibiotic targeting resistant bacteria; RECCE 435, a broad-spectrum synthetic polymer antibiotic for oral use; and RECCE 529, a synthetic polymer anti-infective for viral applications.
These products have been synthetically manufactured with a chosen mechanism of action (MoA), meaning there is an array of advantages not otherwise seen among antibiotics. These include being low cost, having broad applicability, working irreversibly and rapidly, and breaking downeasily.
“If you have a product that’s synthetically manufactured, you have a product that’s got a 100
per cent yield, low cost of manufacture, and broad applicability across multiple infectious disease categories. Ours work so quickly, it works irreversibly, and it breaks down quickly,” said Graham.
Graham said Recce’s products eliminate the guesswork at the clinical level due to the broad applications of the compounds.
“Whether it’s an infection from a diabetic foot ulcer, cat scratch, dog bite, burn wound, puncture, bone, toenail, post operative wound and sinusitis. We don’t care what type of bacteria or virus it is,” he said.
“There’s been gangrene, flesh-eating bacteria, staph, Escherichia coli and even the most frightening and deadliest among all, Pseudomonas aeruginosa.” Graham emphasised that the compounds also work consistently and within a matter of minutes unlike existing antibiotics.
“If you have a product that works and keeps on working, it’s valuable,” he said.
“All antibiotics really work by method of saturation over a long period of time. We work in a matter of minutes, not hours or days.
“Once applied, the compound enters the cell membrane to shut down what is the beating heart of the bacteria.
“It binds to the proteinaceous layer of the bacterial cell; it enters the cell wall in actively growing cells and stagnant non-growing cells,” said Graham.
The anti-infective also has what is referred to as a Z ring complex MoA, which was identified by a professor at the University of San Diego, Dr Joe Pogliano.
“The Z ring complex is basically how the cells divide and multiply,” said Graham.
“You put our stuff in there, and the bacteria dies, allowing the eukaryotic [ally cell] to grow and multiply.”
Next to theoretical validation, Recce’s compounds were validated in a heavy medical setting through a clinician in Sydney, who cured a patient’s foot ulcer overnight. After the results of this case, he then decided to put the compounds to use with more serious patients.
“He put it on this diabetic’s foot. He said to the guy, ‘I can amputate your foot today, or I can rub this gel on it and see how it goes.’ It worked,” said Graham.
“There was one where a femur bone had maggots coming out of it. The clinician put this compound on, and it cured the patient.”
For a product that addresses a potentially fatal bacteria, Graham noted five key control parameters of regulatory practice that need to be adhered.
‘Supplier Management’ ensures that material suppliers use quality systems, while ‘Material Controls’ verify raw materials meet standards.
‘Manufacturing Controls’ use validated equipment and processes for product consistencies and ‘QC & Stability Testing’ ensures the finished product meets specifications at manufacture. Finally, ‘Tracking and Trending’ monitors batches throughout the developmentlifecycle.
“We have had a process where our pH probe wasn’t working and our QC system notified us,” said Graham.
Past ensuring a safe product for consumers, Graham said it is also a priority of Recce to “take poisonous, hazardous and dangerous materials from the environment”. To practice this, the company takes an ingredient called acrolein from petrochemical businesses.
“We convert the unsustainable practice of burning acrolein off, into what has proven to be a healthy medical compound for our studies,” said Graham.
The compound’s high yield also enhances environmental benefits, with little material going towaste.
“All existing antibiotics get like 50 per cent yield, and it goes into the environment. We get 99.9 per cent yield, nothing goes into the environment,” said Graham.
To be able to one day make these anti-infectives widely available, Recce Pharmaceuticals has continued to grow its manufacturing capabilities. Located in Sydney’s Macquarie Park, Recce’s automated manufacturing facility processes 500
Australia, Recce’s international testing phases are also progressing with Phase-3 trials in Indonesia and the seeking of approval to commence Phase-3 trials in the US.
“We got a $3 million grant from the US Department of Defence. We work in Europe, in Asia – we really do have a global activity,” said Graham.
Recce Pharmaceuticals is actively trying to overcome the challenge of commercialisation.
doses per hour and up to 5000 per week under Good Manufacturing Practices (GMP). This robust production complies with stringent regulatory guidelines, including those set by the U.S. Food and Drug Administration (FDA). With about 26 staff and several external contractors and suppliers, this growth comes from a large investment in time and money.
“The journey to go from that manual process in a beaker to an automated process with off-the-shelf equipment customised to our requirements took 12 months,” saidGraham.
“We spent maybe $500,000 on the equipment. I think it was one of the greatest investments of our life to own and control that process.”
This growth has seen the company further establish its national and global presence. As one of the few companies that receives 43 and a half cents in every dollar spent globally from Australia’s R&D rebate, Recce has grown in areas all over the globe.
“This week alone, we’ve announced a registrational phase three study in Indonesia for diabetic foot ulcer infections. The Australian Government, or the taxpayer, pays 43 and a half cents of every dollar we expend in that clinical study there,” said Graham.
Because of the rebate, Recce’s studies are progressing well. Alongside Phase-2 trials in
Graham noted that while eventually possible, transitioning from a clinical stage with a defined number of vials to stage 3 testing, and then to commercial production, involves a large scale-up.
“You go from producing low thousands for that study, to some hundreds of thousands. If you’re approved in Indonesia, you probably need to provide 200,000-500,000 doses in the first year,” he said.
Graham said despite this scale being unachievable for at least 18 months, he is working out the logistics behind effective growth.
“We have three different ways of doing that. We can do it ourselves, we can partner with a pharmaceutical company, or we can outsource, which is a hybrid,” he said.
As a part of this constant evolution, Graham said that Recce’s expansion globally will continue in a “two-pronged attack” in Asia, North America, South America, and Europe.
“We’re going through Indonesia to access the ASEAN (Association of Southeast Asian Nations) region, which creates a near term revenue opportunity. If you have that, you pretty well own Asia. Then, if you’re approved in the ASEAN region, you can then pull across to the Middle East,” said Graham.
Reflecting on this, Graham concluded that Recce Pharmaceuticals’ global reach today is a testament to the enduring legacy of his grandfather, Melrose.
“He’s the most driven person I’ve ever come across. He’s passionate and believes that this compound should be available to the masses, and that it should have been done yesterday,” he said.
Becoming a Weld Australia member allows you to surround yourself with people that are passionate about welding and improving the future of all industrial sectors across Australia.
Weld Australia can help you to enhance your career prospects, improve the profitability of your business, and boost your success. Start the year strong – become part of a network that shapes the future of welding in Australia.
Joining Weld Australia offers numerous benefits to professionals and companies within the welding and manufacturing industry.
Weld Australia provides a platform for networking with industry peers, experts, and thought leaders. Members gain access to exclusive events, workshops, and seminars, facilitating connections that can lead to collaborative opportunities, knowledge exchange, and professional growth.
Continuous learning is crucial in the evolving welding sector. Weld Australia offers a range of professional development programs, including training courses, certification programs, and educational resources, all designed to enhance skills and knowledge in line with the latest industry standards and innovations.
Members receive guidance and support in achieving and maintaining compliance with industry standards. Weld Australia plays a key role in setting
welding standards and provides certifications that are recognised both nationally and internationally, enhancing the credibility and reputation of its members.
Access to technical resources and expert support is another benefit. Weld Australia provides technical advice, updates on best practices, and solutions to complex technical challenges, enabling members to stay ahead in technology and processes.
Weld Australia acts as a voice for the welding community, advocating on behalf of its members on regulatory and policy issues that impact the industry. This ensures that the interests of members are well-represented in discussions that shape industry regulations and futuredirectives.
Membership enhances visibility in the industry through listings in member directories, features in newsletters, and opportunities to participate in and sponsor industry events. This increased exposure can lead to new business opportunities and strengthens brand recognition.
Members can participate in research initiatives and innovation projects led by Weld Australia. These projects often focus on pioneering advancements in welding technology and methodologies, positioning members at the forefront of industry innovation.
Being part of Weld Australia allows members to contribute to a community that shares a commitment to excellence and quality in welding. This community support system provides a framework for mutual support, sharing of best practices, and collective problem-solving.
Members receive subscriptions to industry publications that provide insights into market trends, new technologies, and industry news. These publications are invaluable for staying informed and making data-driven decisions in business and practice.
Membership offers financial benefits such as discounts on training, certifications, event registrations, and access to exclusive deals with industry suppliers. These cost savings can be significant, making membership a wise investment for both individuals and companies. Joining Weld Australia not only enhances professional capabilities but also contributes to the strength and advancement of the entire welding industry. Whether you’re looking to expand your professional network, stay ahead of technological advancements, or influence industry standards, Weld Australia is your gateway to achieving these goals.
For more information and to join, visit: https://weldaustralia.com.au/membership/
For manufacturing executives, safeguarding operational technology (OT) is not just a priority—it's a necessity. This comprehensive Executive Guide on OT Cybersecurity summarizes the unique challenges of securing manufacturing environments and offers actionable steps to improve your security posture.