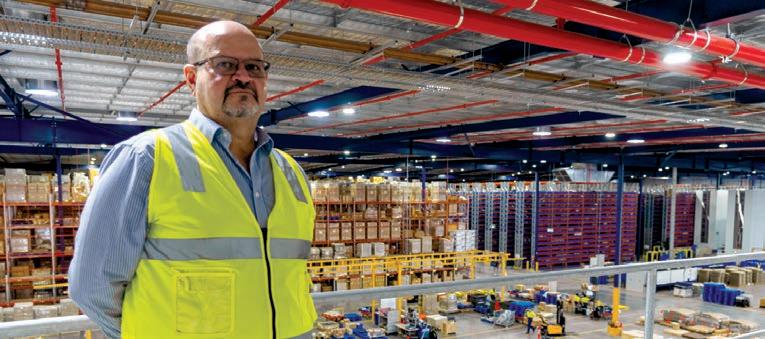
3 minute read
BHD’s storage and racking
from MHD Apr 2022
by Prime Group
STATE-OF-THE-ART STORAGE
Global earthmoving and mining equipment manufacturer Komatsu recently built a new DC in Queensland, with BHD Storage Solutions playing an essential role in the project’s success. MHD finds out more.
Komatsu is an internationally renowned global manufacturer and distributor of earthmoving and mining equipment. Naturally, given the importance of Australia’s mining sector – and Queensland’s in particular – it made sense for Komatsu Australia to build a new distribution centre (DC) that could cater to the evolving needs of local industry, in keeping with one of Komatsu’s core company values: collaboration.
A vital component of the new DC is the storage solution implemented by BHD Storage Solutions. But before we get there, it’s important to explore why this new DC is so important.
Recently, MHD spoke with Hennie Van Der Merwe, Komatsu’s General Manager of Warehousing at the new state-ofthe-art 17,000m2 warehouse and DC in Wacol, Brisbane.
Hennie was responsible for the delivery of the new DC – from conception to its completion as a fully integrated operating facility. As such, he is well placed to provide an overview of the new centre’s capabilities.
“The $50 million Distribution Centre is a strong demonstration of Komatsu’s commitment to supporting and servicing their customers’ growth in Queensland, the Northern Territory, and northern New South Wales,” Hennie says.
“With the wide range of machines in the mining industry comes a wide range of components,” he says. “This warehouse houses 55,000 SKUs at 80,000 locations. Parts are available ranging from O rings – that are half the size of a $2 coin – up to 25-tonne ring gears for electric dump trucks. The warehouse processes 45,000 lines per month, either being despatched or received as stock. This facility forms part of Komatsu’s global network of manufacturing and supply chain warehouses.”
Hennie says that the omnichannel management order process is integrated
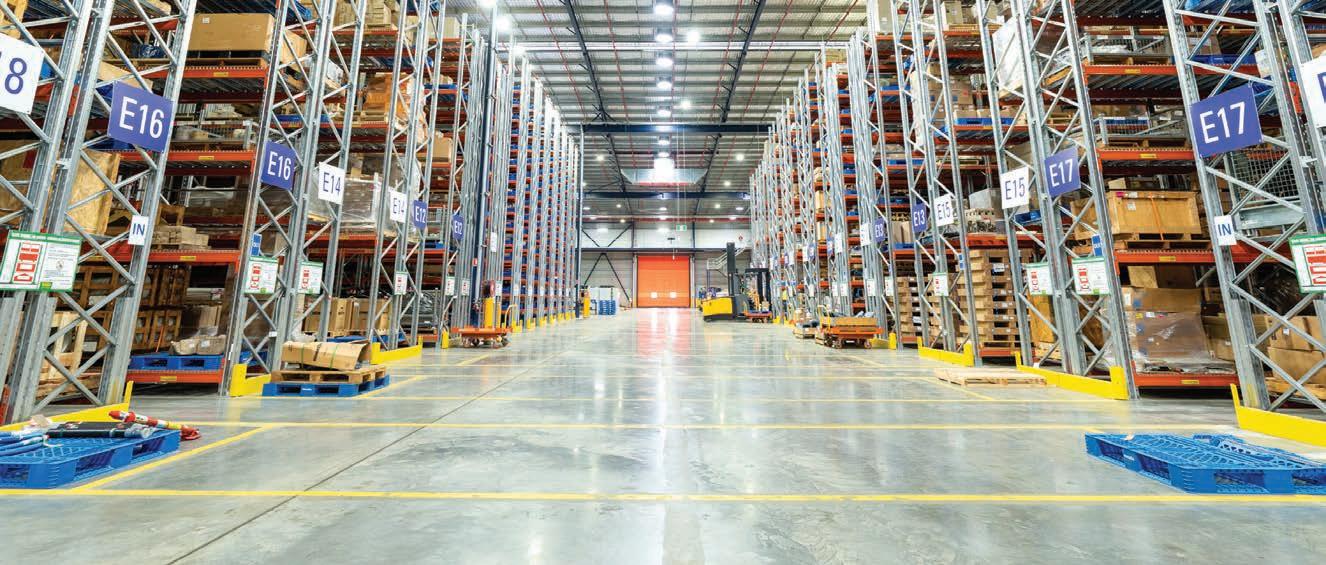
with an ERP system, which allows walkins, online orders, phone orders, onsite visits for customers, and business-tobusiness orders.
“Komatsu’s philosophy is to meet the customer’s requirements – from the smallest machine operator to multinational mining companies,” he adds.
With 55,000 SKUs, storage requirements vary greatly in terms of size, weight, and loading points. With such range, depth, and variety of SKUs, it was essential for Komatsu to have the perfect racking and storage solutions for the job.
To that end, Komatsu partnered with David Seale from BHD Storage Solutions to provide customised and manufactured racking required for all these lines. This resulted in 15 different rack designs.
“Pallet racks from BHD ranged in capacity from 52,000 kg, 30,000 kg, 28,000 kg, 27,000 kg, and 10,000 kg per bay – with heights up to 10 metres,” says David. “Super heavy-duty racks with ten PFC beams per level that can carry up to 8000 kg per level. Long bulky products, such as hydraulic hoses, can be carried on nine metres cantilever racks. For the sorting and despatch of smaller orders, long span and CLS roller racks are used.”
The use of mobile racks, which can store motors and large oversize components of up to 5000 kilograms has improved the density of required warehouse floor space by approximately 70 per cent for the same area, David notes. Thus, it is possible to retrieve these parts in a very efficient
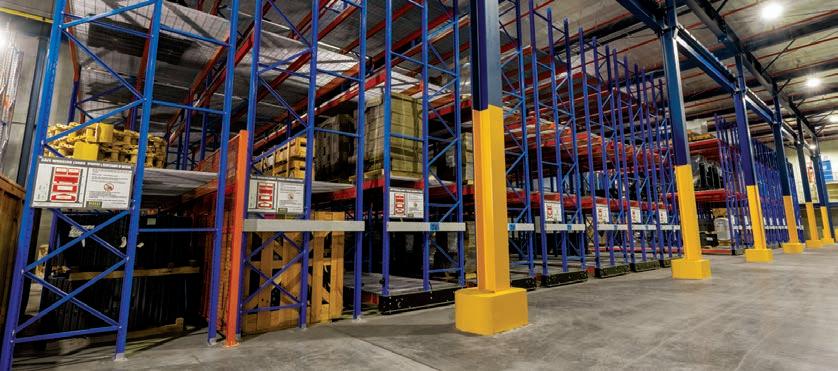
Komatsu partnered with BHD Storage Solutions to provide customised racking.
manner. As a result, the engines and components can be despatched the same day to the client.
Hennie is justifiably impressed with the results of BHD’s work.
“In order to support our customers for many years to come, all Komatsu’s small to multinational clients will rely upon the benefits provided by this investment in an integrated global warehousing and logistics centre. And BHD’s racking and storage is an indispensable part of this project.” ■
Cubiscans & DWS Systems
Supercharge your Warehouse Management System with accurate SKU dimensional master data
Cubiscans
Automate the capture and export to your host WMS, TMS, or FMS precise SKU, partcel, or pallet cubic and weight in real time. Systems Integration is a standard value offer from Diverseco.
In-Motion Dimension-Weigh-Scan (DWS) Systems
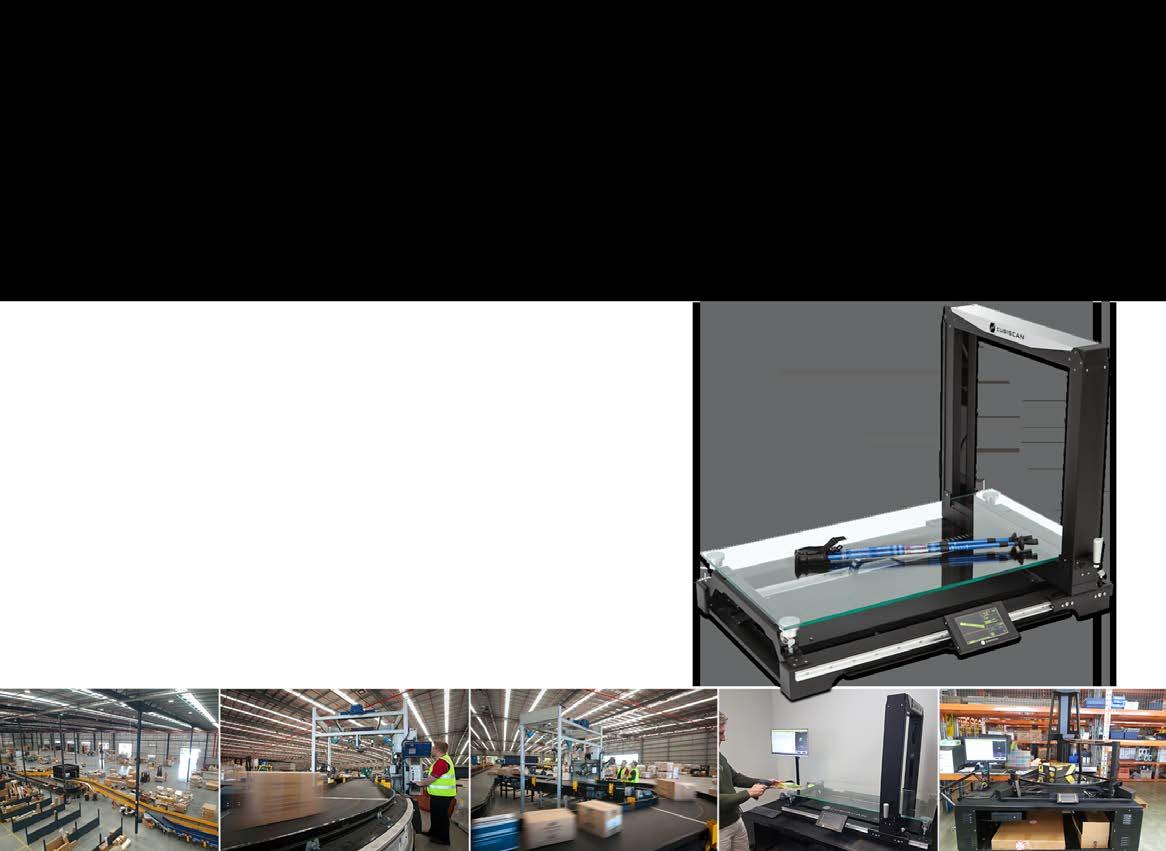
Capture legal-for-trade weight and dimensions of outbound parcels in a DC or express freight facility.
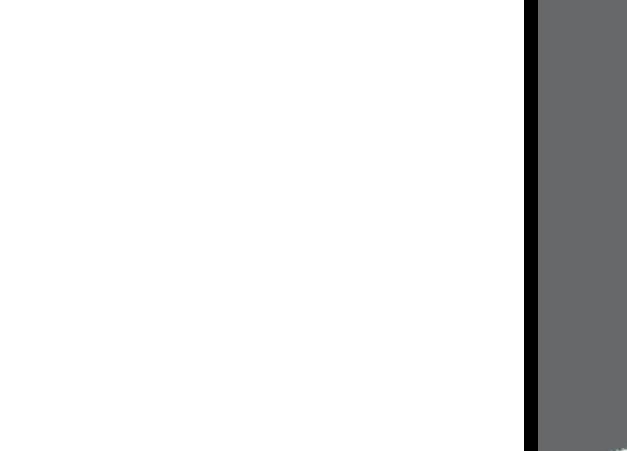
Dimensioning Automation
For scanning items into custody and determining sortation lane destinations from information embedded in parcel item barcode data.