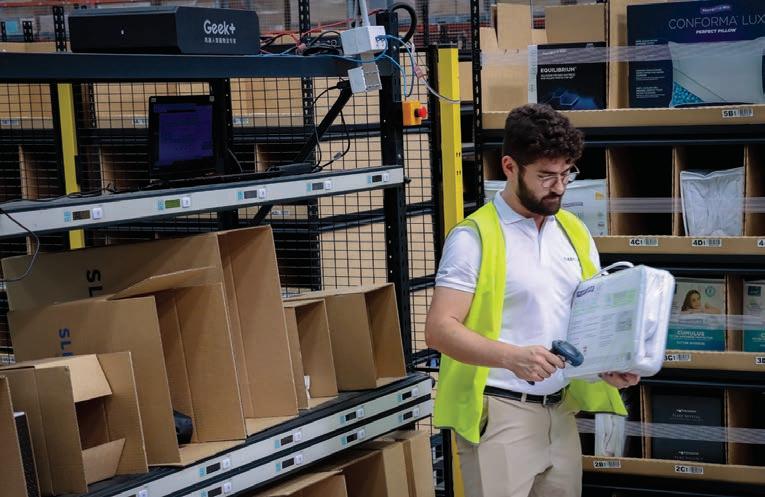
7 minute read
Fuzzy LogX transforms Aussie
from MHD Apr 2022
by Prime Group
LEADING AUSSIE MANUFACTURER MEETS WAREHOUSE WIZARDS
Sleep Corp is an iconic Australian brand manufacturing the best in mattress protectors and associated sleeping products. Having decided to overhaul its manufacturing and warehousing operations, it turned to Fuzzy LogX’s team of warehouse design experts to help turbocharge its operations as it enters a new and exciting future.
Ryland Joyce, Operations Manager at Sleep Corp, says that the company’s history stretches back 45 years to the owner and founder’s initial creation of a waterproof mattress protector. Since then, the company has expanded into new markets and products, although along the way the current iteration of the brand, Sleep Corp, elected to double down on the Australian market and focus on being an Australian manufacturer and distributor of mattress protectors and related products.
“One of the core goals of our business since then – and especially in the last 10 years – is focusing on ‘Australian Made’,” Ryland says. “50 per cent of our products have been Australian made for the last decade.”
But roughly four years ago, Ryland says Sleep Corp decided to set its sights on the future.
“We recognise that we own the market when it comes to mattress protectors,” he says. “We invented the product and are the leader in that space. But there are a lot more opportunities in the sleep space where we know we can add value in offering extraordinary products and brands. We’ve been around for 45 years, so what does the next 50 look like?”
Ryland says that there were two major projects that had to be undertaken to position Sleep Corp for a strong future – one was updating its manufacturing processes, and the other its warehousing and distribution capabilities.
“For the manufacturing side, it was about automation and everything that came with it,” he says. “Now we’ve got the equipment and machinery, as well as the systems and intelligence supporting it. It’s not just about the robotics, it’s the Industry 4.0 technology, an automated manufacturing execution system that uses AI and intelligent awareness around the product to make it more efficient.”
The upshot of this new manufacturing capability is that with the same number of people working at Sleep Corp, it will be able to double its output of Australian-manufactured products by May of this year.
This is certainly impressive, but as Ryland notes, updated manufacturing must be complemented by advanced warehousing.
“If I have double the number of products being manufactured but my warehouse can still only output the old number, that doesn’t help anyone,” he says. “The demand for our products is there – that is clear. But without a sophisticated and automated warehouse, those products are going nowhere fast.”
And that’s where Fuzzy LogX and its team of ‘Warehouse Wizards’ come in.
“The transformation of our warehousing has taken us from Industry 1.0 to Industry 4.0 and beyond,” Ryland says. “Previously, we had MHE and systems that were literally 30 or 40 years old. We weren’t even scanning barcodes three years ago. So, we had a lot of catching up to do – and looked to experts to help us take that next step.”
Ryland Joyce, Operatios Manager at Sleep Corp.
ENTER FUZZY LOGX
Ryland says that choosing Fuzzy LogX started off as simply as Googling for solutions providers. He was taken in by Fuzzy LogX’s website and style, and reached out to Jeffrey Triantafilo, Fuzzy LogX’s
Director of Systems and DC Design.
“Anyone who has met Jeff knows instantly that he knows what he’s talking about, that he is genuinely interested in building a rapport and understanding your needs,” Ryland says. “I knew this was a person I could trust. At that point we weren’t even thinking about automation – and he wasn’t trying to sell us on anything. He just wanted to understand our situation. We knew we were going to be moving manufacturing and warehousing into a new facility, but beyond that we were looking for guidance.”
The partnership started out with a basic audit of the warehouse – so Fuzzy LogX and Sleep Corp could work together to figure out basic things like warehouse layout and the kinds of system that would best match Sleep Corp’s unique needs and future ambitions.
Recalling the whole process, Jeff is both excited and proud with what Fuzzy LogX and Sleep Corp achieved together. He says it all started off with a simple conversation in a room, where both sides discussed the potential for Sleep Corp’s development.
“We then conducted an audit – or a ‘Process Excellence Review’ as we call it,” says Jeff. “Essentially, we capture the operation. We ensure we properly understand it, we ask all the silly questions, we immerse ourselves in it, and then only after we’re satisfied with our own understanding do we start thinking about the future.
“The next stage was to ask the question: ‘What are you guys thinking about growth – your ambitions and your potential?’ We had that conversation and identified five different channels in the business and how we might help them grow. With that picture in place, we then moved onto a more in-depth discussion. We created concepts for what a future DC might look like in terms of size, ensuring it would fit within the walls of their new building, then explored different automation systems, and then went out to market to find the right solution and the right partner.”
Deciding the best automation fit for Sleep Corp was a team effort using Fuzzy LogX’s proven systems design framework. Supporting the implementation and delivery of the final solution fell to Marina Longbottom, Intralogistics Consultant at Fuzzy LogX, and its first ‘Warehouse Wizard’ located permanently in Melbourne.
As Marina says, traditional ASRS systems were designed primarily for the FCMG industry – Coles, Woolworths, Big W, and the like – and require a large infrastructure to implement, as well as being quite costly and timeconsuming to install.
“By contrast, Sleep Corp must navigate a multi-channel customer environment, often producing highly individualised products for clients which bring with them their own unique requirements,” Marina says. “The handling, scanning, packing, labelling, and distribution processes are quite various – so we needed an automation solution that was flexible enough to deal with this degree of variation.”
It is for this reason that Marina believes that Körber AMRs were the perfect fit for Sleep Corp. “They’re highly customisable, can serve different purposes, and don’t have to be built into the surrounding environment like an ASRS system. On top of that, Körber’s team is highly responsive and just a phone call away should an awkward challenge arise. We’ve
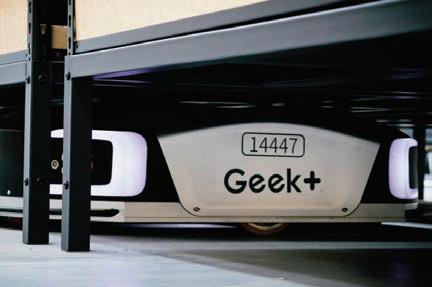
The end result of the Fuzzy LogX-Sleep Corp collaboration is an integrated manufacturing and warehousing operation – in one location. Körber AMRs were introduced at Sleep Corp.
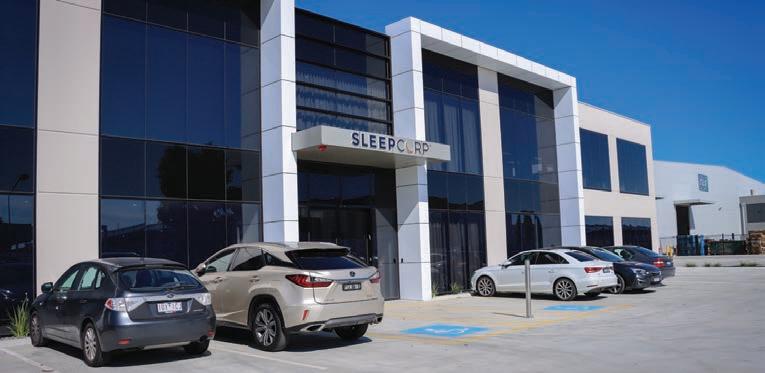
modified our warehouse blueprints a few times along the way, and Körber has never said to us that something can’t be done. Fuzzy LogX and Sleep Corp are collaborative in spirit – and we appreciate that Körber has worked with us in like manner.”
MISSION ACCOMPLISHED
The end result of the Fuzzy LogX-Sleep Corp collaboration is an integrated manufacturing and warehousing operation – in one location.
Ryland says that the Sleep Corp experience shows the way to a renaissance in homegrown, sophisticated Australian manufacturing.
“We didn’t suffer like others did in COVID because our stock was made here in Australia, we hold our materials here, and we distribute from here,” he notes. “Our problem was the opposite of many others – we didn’t have the capacity to meet demand. Now that’s changed, with our new, automated, future-directed manufacturing and warehousing operations sitting side by side. The fact that I can walk from our manufacturing plant to our warehousing operation – and watch how everything flows through from order to despatch – provides a level of transparency and certainty that no one else can match. It’s an advantage that other Australian manufacturers could learn something from.”
‘Transparency’ is a keyword for both Ryland and Fuzzy LogX.
“Transparency and trust are absolutely vital for us at Fuzzy LogX,” Jeff says. “This project is one we’re all very proud of at Fuzzy LogX. Ryland and I can look each other in the eye and know for certain we’ve each gotten the best out of each other. It all comes down to relationships – that’s what we’re about.” ■