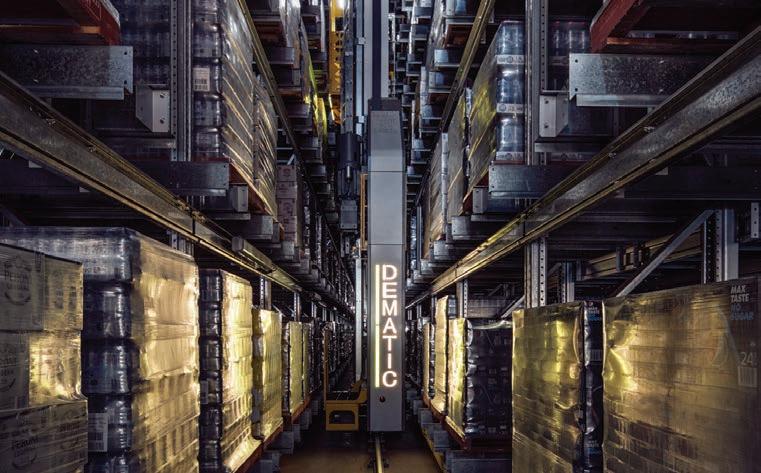
6 minute read
Dematic on automation for
from MHD Apr 2022
by Prime Group
DISRUPTION IS THE NEW NORMAL – HOW AUTOMATION BUILDS BUSINESS RESILIENCE
Dematic’s Pas Tomasiello – Senior Regional Director Sales & Solutions Development, and Philip Makowski – Director Marketing APAC, explain how in times of disruption automation is key to building business resilience.
We are constantly being reminded that we are living through one of the greatest periods of disruption in history. Working and shopping patterns have changed and images of empty shelves in the supermarket, along with announcements of buying restrictions for essential groceries, have practically become commonplace throughout the pandemic.
However, for residents in Western Australia and the Northern Territory, it was not COVID-19 that was the cause of recent food shortage issues, but rather a mass flooding event that temporarily cut rail supply lines, leading to a scarcity of imported goods. Likewise, the catastrophic impact of the recent floods in southeast Queensland, Sydney and the NSW Northern Rivers is still being determined, but what we can expect is that supply chains will be seriously impacted, either as much as or even more than the previous major floods in the same region in 2011.
The fact that these unexpected supply chain interruptions occurred during a period of wider disruption for businesses has underlined that the pandemic isn’t the only unforeseen challenge or crisis impacting supply chains. Those organisations that view the current period of challenging operating conditions as being temporary, with improving circumstances leading to a ‘new normal’ in the near future are being overly optimistic, if not unrealistic. What is far more likely is that disruptions are now the norm, not the exception, whether it be from a new variant of a global virus, natural disasters, or geopolitical or economic events.
So, how can companies and their supply chain organisations manage their businesses under such challenging operating conditions? How can they utilise new technologies to build resilience and agility into their supply chains to meet customer and business demands?
TECHNOLOGY SOLUTIONS FOR THE NEW NORMAL
The current pandemic has shown that businesses who have invested in automation are more resilient to unforeseen disruptions. In turn, automation has enabled these businesses to maintain and manage operations during testing circumstances, and deliver customer orders with limited staff, while also facilitating social distancing. Automation has also equipped these businesses with the capacity, flexibility, and responsiveness to handle spikes in order volumes and changes to order profiles, such as an influx of online orders.
Of these pioneering retailers choosing to automate operations, many stated that their highly automated order fulfilment system ideally positioned them to maintain high customer service levels, with rapid, error-free order fulfilment, as online orders spiked at the start of the pandemic. This has
allowed these retailers to gain not only a greater market share, but also customer loyalty, providing them with a stronger foundation for future growth. Likewise, other large retailers with both automated distribution centres and manual warehouses in their extensive supply chain network reported a significant decrease in operational disruptions, allowing them to effectively maintain store replenishment activities and avoid undue stockouts.
These stark experiences have underlined that businesses need to consider automation technology throughout their end-to-end supply chains to ensure the capacity and flexibility to navigate unexpected events and manage periods of disruption as best as possible. Even before the pandemic, grocers and food and beverage manufacturers were struggling to optimise order fulfilment to make it both sustainable and profitable in an industry with notoriously tight profit margins. Now, with unprecedented pressures on global supply chains, those issues have only been amplified.
INTELLIGENT SOFTWARE: THE FOUNDATION FOR RESILIENCE AND AGILITY
Logistics software integrated across sites can also provide a holistic, endto-end view of an entire supply chain. Retailers, as well as manufacturers, can utilise connected data, smart algorithms, and data-driven intelligence and decision support tools to optimise operations and make more effective decisions based on a wide variety of factors including consumer behaviours — such as panic buying — to determine inventory needs, address major peaks in demand, and manage unexpected supply chain interruptions.
HEDGING AGAINST THE UNEXPECTED
Given the ongoing global supply chain issues, many manufacturers and retailers are looking to increase inventory levels as a hedge against future disruption. However, this is leading to new challenges entirely, due to the shortage of commercial warehouse and industrial space in key fulfilment areas. Even prepandemic, rent for warehouse space in Australia had increased by 25 per cent in the previous three years, and the availability of commercial land in a city such as Sydney has reduced by 35 per cent in the last five years. This shortage of readily available facilities is leading many retailers and logistics companies to rethink their approach to commercial warehouse space.
In this environment, businesses are increasingly investing in solutions like Automated Storage and Retrieval Systems for pallets and Multishuttle and Autostore systems for cartons, cases and totes to maximise storage capacity in a smaller footprint, while providing them with optimal inventory management and tracking along with increased system reliability.
These space savings allow for the better utilisation of existing facilities beyond warehousing, and some customers have used this newly created space to expand manufacturing capacity or add special areas for value-adding tasks such as kitting or custom build areas.
MANAGING STAFF SHORTAGES
Finding and retaining labour is a key issue facing many supply chain operations today. Indeed, the need to attract and retain staff is creating real business pressures due to a shrinking pool to hire from, as well as rising staff costs.
Automated systems can help reduce a business’s reliance on manual labour, while also enhancing health and safety protocols for workers in the warehouse. Innovations such as Automated Guided Vehicles, for example, provide fully automated unit transport between subsystems, as well as automated storage for block stacking and rack storage.
Moreover, Automated Storage and Retrieval systems (AS/RS), such as the Dematic Multishuttle and AutoStore systems, work to not only expand storage capacity but reduce a reliance on labour. As the storage engines for goods-toperson systems – where product cases or items are delivered automatically to pickers at ergonomically optimised high-rate pick stations – work to optimise fulfilment operations, they also streamline efficiency levels with accelerated order responsiveness, be it for single item or case picking. With productivity gains of up to 500 per cent over manual systems, goods-to-person systems significantly reduce the reliance on labour, and as stations are physically separated, they also support social distancing protocols for operators.
Likewise, because all these automated systems are separated from employee working areas, workplace accidents are far less likely to occur. Automation enables businesses to continue operations during a period of massive disruption where labour is scarce or worker density limits are enforced, while maintaining employee safety protocols.
OPTIMISING THE ‘LAST MILE’ OF E-COMMERCE FULFILMENT
With the ever-increasing growth in online orders and a downturn in business for physical stores, many retailers and even some food producers are now adopting micro-fulfilment solutions to implement online order fulfilment operations close to customers, addressing the challenge of last-mile deliveries.
Micro-fulfilment solutions are highly compact Multishuttle or AutoStorebased goods-to-person systems for e-commerce order fulfilment that can be installed either in the back of existing store locations, in nearby distribution centres, or even dedicated online fulfilment dark stores to serve nearby consumers. Micro-fulfilment solutions are highly flexible and can serve in-store fulfilment, click-and-collect, and support other stores nearby.
AUTOMATION IS THE FUTURE
Businesses should now be considering logistics automation technology and supply chain software to support operations with the resilience and agility needed to handle unanticipated demand surges and abrupt disruptions.
All in all, retail, wholesale, and manufacturing businesses should be evaluating automation technology and software to provide their supply chains with the flexibility to be able to adapt quicker and more proactively to any changes in the market, ensuring long-term resilience and agility to any anticipated and unanticipated disruptions – and there’s never been a better time than now to start this transition into future-proof business operations. ■